1000m3高炉在经济产能下指标的优化与提升.docx
《1000m3高炉在经济产能下指标的优化与提升.docx》由会员分享,可在线阅读,更多相关《1000m3高炉在经济产能下指标的优化与提升.docx(11页珍藏版)》请在冰豆网上搜索。
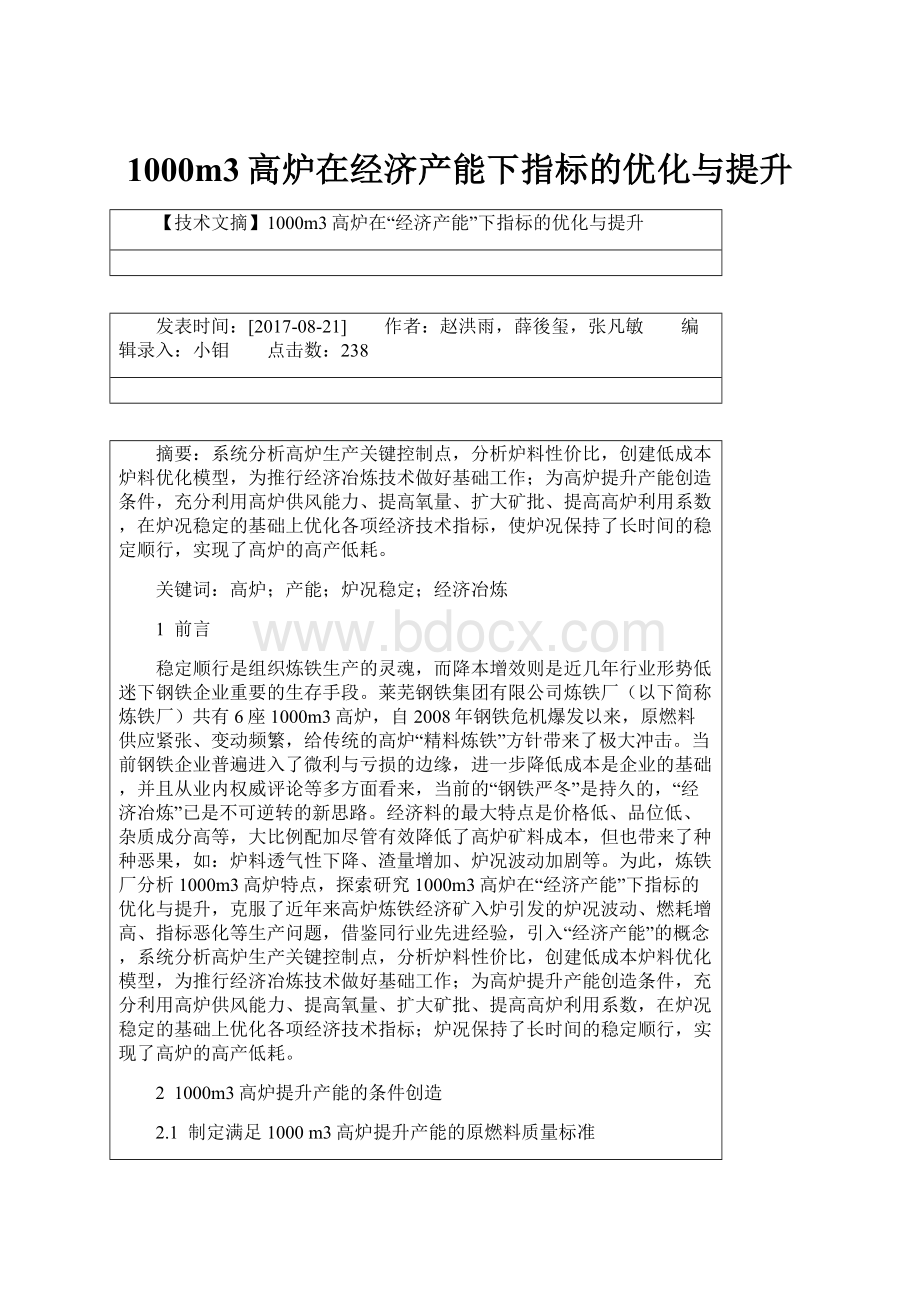
1000m3高炉在经济产能下指标的优化与提升
【技术文摘】1000m3高炉在“经济产能”下指标的优化与提升
发表时间:
[2017-08-21] 作者:
赵洪雨,薛後玺,张凡敏 编辑录入:
小钼 点击数:
238
摘要:
系统分析高炉生产关键控制点,分析炉料性价比,创建低成本炉料优化模型,为推行经济冶炼技术做好基础工作;为高炉提升产能创造条件,充分利用高炉供风能力、提高氧量、扩大矿批、提高高炉利用系数,在炉况稳定的基础上优化各项经济技术指标,使炉况保持了长时间的稳定顺行,实现了高炉的高产低耗。
关键词:
高炉;产能;炉况稳定;经济冶炼
1 前言
稳定顺行是组织炼铁生产的灵魂,而降本增效则是近几年行业形势低迷下钢铁企业重要的生存手段。
莱芜钢铁集团有限公司炼铁厂(以下简称炼铁厂)共有6座1000m3高炉,自2008年钢铁危机爆发以来,原燃料供应紧张、变动频繁,给传统的高炉“精料炼铁”方针带来了极大冲击。
当前钢铁企业普遍进入了微利与亏损的边缘,进一步降低成本是企业的基础,并且从业内权威评论等多方面看来,当前的“钢铁严冬”是持久的,“经济冶炼”已是不可逆转的新思路。
经济料的最大特点是价格低、品位低、杂质成分高等,大比例配加尽管有效降低了高炉矿料成本,但也带来了种种恶果,如:
炉料透气性下降、渣量增加、炉况波动加剧等。
为此,炼铁厂分析1000m3高炉特点,探索研究1000m3高炉在“经济产能”下指标的优化与提升,克服了近年来高炉炼铁经济矿入炉引发的炉况波动、燃耗增高、指标恶化等生产问题,借鉴同行业先进经验,引入“经济产能”的概念,系统分析高炉生产关键控制点,分析炉料性价比,创建低成本炉料优化模型,为推行经济冶炼技术做好基础工作;为高炉提升产能创造条件,充分利用高炉供风能力、提高氧量、扩大矿批、提高高炉利用系数,在炉况稳定的基础上优化各项经济技术指标;炉况保持了长时间的稳定顺行,实现了高炉的高产低耗。
2 1000m3高炉提升产能的条件创造
2.1 制定满足1000m3高炉提升产能的原燃料质量标准
2.1.1 高炉提升产能所需的烧结矿
(1)影响高炉提升产能的主要因素
炼铁厂老区烧结矿产能与高炉需求量存在不匹配的现状,存在较大的烧结矿缺口,需要用外厂烧结矿进行补充,由于无法实现均匀配加造成了炉渣碱度的波动,多次倒运又造成了烧结矿的粉末增加,入炉粉末增加后恶化了高炉的透气性,影响高炉的生产稳定。
为降低生产成本烧结工序炼铁厂配加了高铝的塞拉利昂粗粉,由于塞矿粒度较大,10mm以上的组份在50%左右,直接影响了烧结矿成品质量。
(2)提升产能对自产烧结矿的质量要求
烧结矿品位TFe≥58.5%,Al2O3≤2.0%,铁分波动≤0.5%,碱度R=2.0波动≤0.05,FeO波动≤0.75%,转鼓指数≥80%,还原粉化率(RDI)~35%,粒度5~50mm,其中大于50mm≤5%,小于5mm≤5%,5-10mm≤20%。
2.1.2 高炉提升产能所需的球团矿
(1)影响高炉提升产能的主要因素
炼铁厂使用的球团矿品种较多,老区以自产二车间球团矿为主,不足部分以外购莱矿球、鲁南球、矿建球补充,二区高炉全部配加自产一车间球团矿。
由于设备老旧,二车间球团矿粉末量和转股等指标波动较大。
外购球则存在阶段性粉末多的情况,难以筛分,经常性糊筛子,造成入炉粉末多影响了料柱的透气性。
(2)提升产能对球团矿的质量要求
球团矿TFe≥63.5%,FeO〈0.7%,转鼓指数≥91%,常温抗压强度200kg/球,膨胀率<15%。
自产球-5mm≤2%,外购球-5mm≤5%。
2.1.3 高炉提升产能所需的生矿
(1)影响高炉提升产能的主要因素
炼铁厂的生矿均储存在露天一次料场,当天气变化时对生矿质量影响较大,生矿水分变大时,附着的粉末基本无法被筛下,全部进入了高炉,雨天时高炉经常被迫减少生矿配加量以避免炉况波动。
(2)提升产能对生矿的质量要求
生矿粒度:
5~25mm,-5mm≤7%。
2.1.4 高炉提升产能所需的焦炭
(1)影响高炉提升产能的主要因素
炼铁厂所使用的焦炭比较复杂,外购焦全部存放在露天料场,下雨天水分过高时,焦粉会粘附在焦炭上无法筛下,造成入炉粉末量增加,这是一个重要的影响生产因素。
炼铁厂老区高炉使用的焦炭为自产水熄焦加上自产干熄焦(实际干熄率在80%~90%),不足的部分补充外购焦,但老区配加外购焦时只能从自产焦皮带上加料,实际生产中自产干熄焦中的水熄焦混加比例不均匀,外购焦水分与成分和自产焦有差异,对炉况影响比较大。
自产焦为了降低成本配加了大量的高硫煤,焦炭中的S始终在1.1%左右,导致高炉S负荷升高,燃耗升高。
二区高炉全部配加的外购焦,雨天生产时焦炭水分基本饱和,对炉况影响较大。
(2)提升产能对焦碳的质量要求
自产水熄焦:
灰份≤12%,S≤1.1%,M40≥80%,M10≤7%。
反应后强度≥60%,反应性≤30%
自产干熄焦:
灰份≤12%,S≤1.1%,M40≥82%,M10≤5%。
反应后强度≥62%,反应性≤28%
外购焦:
灰份≤12%,S≤0.6%,M40≥80%,M10≤7%。
反应后强度≥62%,反应性≤28%
2.1.5 高炉提升产能所需的煤粉
(1)影响高炉提升产能的主要因素
炼铁厂老区高炉的受喷煤制粉能力的影响,煤比提升后,制粉量不足,需要频繁倒用旧系统,倒罐频率高,使用旧系统时高炉风压上升较多,对高炉炉况稳定顺行存在不利影响。
(2)提升产能对入炉煤粉的质量要求
灰份≤10%,挥发份≤10%,固定碳≥76%,S≤0.6%,水份≤1%,-200网目≥60%。
2.2 加强原料管理,提升精料技术
从高炉原燃料稳定上下大功夫,及时与原料部、焦化厂、公司部门沟通,建立起实时、真实的原燃料预警机制。
同时,自身不断加强精料技术研究与管理,及时优化烧结矿混匀料、炼焦配煤结构,加强原燃料检测,改造外围设备等,既保证了原燃料优质优量供给高炉,又实时掌控原燃料质量波动,为判断炉况发展趋势和保证高炉长期稳定奠定了基础。
为了适应在高产量下的操作,保证炉况稳定顺行,采取了以下措施:
(1)加强入炉焦炭质量管理。
一是加强与调度联系,尽量使自产焦与外购焦分仓供应,保证有序上料;二是在板报上记录不同入炉焦炭所占百分比,为本班和下一班提供焦炭负荷参考;三是要求工长和上料工每小时看一次焦炭料车料位,及时检查水分变化并及时适量调剂负荷,减少因其波动对炉况的影响。
(2)及时掌握原燃料变化情况,防止粉料入仓;每两小时检查入炉原燃料实物质量。
(3)加强槽下筛分,减少粉料入炉。
槽下对矿石、焦炭的过筛效果,是精料工作的很重要环节。
<5mm的粉末人炉数量增加,高炉的透气性很快恶化,导致顺行被破坏,产量降低、焦比升高,甚至炉墙结厚等恶性事故发生,所以加强检查、测定、定时清筛等管理工作是必要的。
一般情况下.要求每个矿筛振料时间不低于100s;对于焦炭,要求振料时间大于120s。
发现振料时间少于规定时间时要及时调整。
(4)加强槽位管理。
高炉料仓槽位受多方面因素影响,如槽位过低,加剧矿石和焦炭摔打,使小粒级和粉末大量增加,同时仓壁附着的粉末也随之而下,必然恶化高炉透气性,破坏高炉顺行。
一旦顺行被破坏,即使槽位恢复正常,高炉也吃不下去。
随之生产平衡被打破,影响前道工序正常生产,形成恶性循环,所以必须要主动控制。
为减少矿石、焦炭小粒级和粉末入炉,规定正常烧结矿槽位≥1/2,焦炭槽位≥1/2。
2.3 创建低成本炉料优化模型
建立日核算制度,建立高炉成本控制模型,分析炉料性价比,通过适当调整优化炉料结构,降低生产成本。
受市场价格影响,各种矿料单品位成本变化大,供应情况也不稳定,在密切关注市场供应情况的同时,只有通过日核算、勤调整,才能及时按照精确性价比排出次序。
但稳定运行,又是高炉高效生产的前提和基础。
因此,需分析炉料性价比,模糊控制与精确控制相结合,创建低成本炉料优化模型,不断优化炉料结构,为推行经济冶炼技术做好基础工作。
主要实施步骤如下:
2.3.1 建立日核算制度
根据每月和每周的炉料性价比,每周对炉料进行一次排序,并结合高炉实际运行情况,每日一核算精确性价比、生产成本,并根据公司的炉料结构进行适当优化、调整。
经计算,进口块矿始终是单品位成本最低的炉料,应安排各高炉优先配加,并要求达到5%~10%的比例。
为避免出现经济矿料配比过高影响冶炼指标的情况,以首先满足高炉炉况稳定顺行为原则,累积、比较日核算数据,探索最佳配比,在高炉炉况出现波动情况下,及时调整配比,经过反复优化调整,在满足高炉炉况稳定顺行需要和降本增效之间,找到了最佳交叉点,高炉炉况稳定性提高,同时生铁成本也显著降低。
2.3.2 建立高炉成本控制模型
经过系列性价比分析,确定宏观炉料性价排序分别为块矿、外购球团矿、烧结矿、自产球团矿,并以此作为高炉炉料结构调整的依据,特别是块矿使用。
在宏观性价比排序的基础上,建立宏观性高炉成本控制模型如下:
(1)矿石性价比:
烧结矿<球团矿<生矿
选择65%+ 15% + 10%
(2)矿石性价比:
烧结矿=球团矿<生矿
选择75% + 15% +10%
(3)矿石性价比:
烧结矿<球团矿=生矿
选择:
65% +30% +5%
(4)矿石性价比:
烧结矿>球团矿=生矿
选择:
75%+20%+5%
另外,为全面降低炉料成本,还应注意:
(1)根据矿料库存及供应情况,调整配比,计算出每种矿料的单品位成本及冶炼性能,然后根据经济性及冶炼性能进行排队,优先使用单品位成本最低的矿料,最大限度降低烧结矿成本。
(2)采取多种措施,稳定原燃料质量,如:
根据焦炭加减价的管理制度,根据国家标准改变焦炭取样地点,将焦炭取样地点由焦化厂改为,焦化厂与炼铁厂皮带交接处,确保了焦炭成分的真实性和代表性。
从2014年1月份开始两区高炉大幅度增加块矿配比,最高达到16%,宏观性价比排序降本效果明显,截止到12月份,炉料结构优化与2013年相比,剔除价格因素,老区降低5.06元/t.Fe,二区降低4.93元/t.Fe,实施效果显著。
2.4 操作制度优化
2.4.1 大批重
批重对炉料在炉喉分布影响很大。
批重太小布料不均,小到一定程度,将使边缘和中心无矿石。
批重增大,相对加重中心而疏松边缘,而且软熔带气窗增大,料柱界面效应减少,有利于改善料柱透气性。
客观上来讲,每座高炉都有一个临界批重,当批重大于临界值时,高炉顺行难以得到保障,当批重小于临界值时,高炉指标难以得到优化。
5号、6号高炉在实验时通过对批重28~36t进行反复尝试总结,最终确定35t/批适合高炉目前状况。
这一批重,一是可以兼顾中心、疏松气流,改善煤气利用;二是随着焦批的增大,焦窗增大,软熔带透气性增加,有利于改善料柱透气性;三是比较适用于5号、6号高炉的上料设备,每小时6.5批料就可以保证3.3t/(m3·d)的利用系数。
2.4.2 提高风温、富氧,增加喷煤量
提高风温水平,能显著提高理论燃烧温度,提高渣铁物理热,改善渣铁流动性。
由于炼铁厂经济料中Al2O3普遍较高,如果渣铁物理热不充足,炉缸热贮备相应减少,高炉炉腰、炉腹、炉缸等高热流强度区域的热量储备处于较低水平,一旦高炉风量偏少,操作稍有不慎,极易造成炉身粘结,导致炉况失常。
高风温的使用,在降低焦比的同时,会使炉内压差升高,这主要是因为焦比降低,焦炭在料柱中所占体积减少,料柱骨架作用减弱,使料柱透气性变差。
为了创造高炉接受高风温的条件,5号、6号高炉做了以下工作:
1)提高矿石和焦炭强度,特别是热强度,尽量筛除原料中小于5mm的粉末,改善料柱透气性;2)提高炉顶压力,利用高压操作对还原和降低炉内煤气压差的有利因素来消除高风温对高炉还原和顺行的不利影响;3)增加喷吹量,利用喷煤降低风口前理论燃烧温度的特性来抵消高风温提高风口前理论燃烧温度的影响,以获得合理的理论燃烧温度。
通过以上措施,5号、6号高炉在提高风温使用水平、降低焦比的同时,高炉顺行一直保持良好、稳定。
高富氧大喷吹是提高产量、降低焦比和成本的重要手段。
由于两者对冶炼过程的影响大部分是相反的,两者有机结合,可相辅相成,互为补充;一是可增加焦炭燃烧强度,大幅增产;二是促使喷吹燃料气化,在不降低理论燃烧温度的情况下扩大喷吹量,进一步降低焦比。
6号高炉2013年富氧率基本稳定在4%左右。
高富氧大喷吹必然会对高炉的顺行状况产生一些影响,主要表现在:
富氧增加后风量下降、压差升高,边缘煤气流发展,同时喷吹量的增加使焦炭负荷加重,料柱骨架作用减弱,透气性变差,影响炉况顺行。
针对以上变化,5号、6号高炉通过调整布料矩阵和用料结构、扩大批重、精料等措施,较好地克服了以上不足。
2.4.3 确定风口布局,提高鼓风动能
高炉风口布局直接关系到初始煤气流的分布和鼓风动能的大小以及风口回旋区的大小和形状。
5号、6号高炉各有20个风口,风口长度465mm,16个直径120mm风口、4个直径115mm风口,全开风口送风面积为0.2224m2。
风口呈对称型分布,以保证初始煤气流分布均匀。
但在实际生产过程中,由于风口面积偏大,导致鼓风动能小,经常造成中心气流不足,进而炉况抗波动能力差。
为此对风口尺寸进行了优化,全部使用直径115mm风口,风口面积缩小到0.2076m2。
又采取“大风量,高动能活跃炉缸”的送风制度,保持炉缸工作的均匀活跃。
根据与永锋、鲁丽、石横、东阿、长治等厂家同类型高炉的对标统计,1000m3高炉的鼓风动能最高达到10000kg.m/s以上,日产最高达到3800吨左右。
通过与这几个厂家的对比,炼铁厂1000m3高炉存在的主要问题是炉缸的活跃程度不够,造成了高炉对外界的条件过分依赖,也就是抗波动能力不强。
为此,炼铁厂以产能提升为契机,以对标参数为依据,走大风量提高鼓风动能,活跃炉缸。
从5号、6号高炉的送风参数发生了较大变化。
入炉风量显著提高,5号高炉由2200m3/min提高到2500m3/min,6号高炉由2200m3/min提高到2400m3/min,5号高炉鼓风动能提高了500kg.m/s左右,6号高炉提高了1000kg.m/s左右。
二区高炉的炉缸活跃程度显著提高,迅速遏制了频繁损坏风口的状态。
其中,5号高炉送风参数变化情况见下表1、表2:
适当疏松边缘,稳定煤气流,冷却壁温度趋于稳定,水温差降低,高炉抗波动能力增强。
在增加入炉风量以后,随着中心气流的发展,在布料参数上进行了适应性的调整,通过适当疏松边缘,达到了中心畅通,边缘稳定的目的。
高炉使用的布料矩阵见下表3:
从布料矩阵上看,5号炉采取边缘增加一圈焦炭,6号炉采取边缘大一度,增加一圈焦炭,这都是疏松边缘的装料制度。
二区两座高炉的调整和我们对标的几家同类型高炉是相符的,在产能提高后,随着风量的增加,动能的提高,要通过采取大矿批、大角差、轻边缘等措施来稳定煤气流。
3 条件具备后高炉进行产能提升
在基础条件创造完成后,高炉产能逐步提高,产量提升见图1。
注:
2月2号高炉停炉,7月份4号高炉开炉
4 高炉在“经济产能”下对指标进行优化
4.1 提高炉顶压力和压差水平
一般来说,提高炉顶压力能增加入炉风量,延长煤气在炉内停留时间,改善煤气利用,促进间接还原,降低煤气流速,有利于高炉的稳定顺行。
研究表明,炉顶压力每提高0.01MPa,可提高冶炼强度2%左右,降低焦比0.5%。
5号、6号高炉经过4个月的设备磨合,为了强化冶炼,最终将顶压提到0.195MPa。
根据炼铁长期生产实践经验估算,在其他条件不变的情况下,仅此一项,即增产生铁150~200t,降低焦比3~5kg/t,冶炼效果显著。
压差是高炉热风压力与炉顶压力的差值,其实质是料柱对煤气流的阻力损失。
当料柱透气性一定时,风量越大,煤气流速越高,料柱对煤气流的阻力损失越大,压差也就越高。
反过来说,当料柱透气性一定时,提高压差水平,也就是增加了入炉风量。
风量增加一方面提高了风速和鼓风动能,有利于活跃炉缸,促进高炉稳定顺行;另一方面也有利于煤气流在炉内的合理分布,保持合适的操作炉型,防止炉墙粘结;同时,还可吹出较多的粉末,改善料柱的透气性,反过来又可促进风量的进一步增加,从而形成了高炉操作中的良性循环。
但是,过高的压差水平会使料柱浮力增加,造成料难行,所以提高压差水平对料柱透气性和高炉操作水平提出了更高的要求。
5号高炉在通过精料入炉和加强工长操作的同时,将压差提高到现在0.180MPa,不仅炉况顺行得到保障,而且增加了风量,提高了产量。
4.2 实施低硅冶炼
生铁含硅量每降低0.1%,可降低焦比4~5kg/t,增加产量1%~1.5%,是促进高炉生产实现高效低耗的一项重要措施。
随着原燃料条件改善和高顶压、高风温、富氧喷煤等技术的综合应用,高炉中心气流旺盛,炉缸活跃,热量充沛,适于低硅冶炼,所以我们在热制度方面进行了大胆尝试,把[Si]做到了0.3%-0.4%。
5号高炉的低硅冶炼顺利推进,2013年4月[Si]为0.36%,已经达到了良好的水平。
[Si]降低后,不但因燃料比降低使产量相应提高,更主要的是由于[Si]降低后,实际煤气体积减小、上升浮力降低。
为加风创造了条件,有利于进一步提高冶炼强度,增加产量。
同时物理热仍能保证1470~l500℃的水平,能够满足生产要求。
在低硅和强化冶炼情况下,稳定炉温显得尤为重要。
高炉要求工长每小时看一次风口,提前预测炉温变化趋势,提前进行调剂,做到早调微调.煤粉调剂上下不超2t,避免风量大幅度波动;每天接班分析上一班的具体操作,并写出本班的操作思路,以保证炉况的稳定交接;从稳定冶炼强度来稳定炉温,要求每班争取上限料批,正常情况每四小时波动少于—批。
炉温的稳定,有利于保证强化冶炼,提高产量。
同时,随着原燃料价格的不断攀升,原燃料质量下降,有害元素增多。
在生产实践中,铁水含硅量控制较低时,一旦炉况发生波动,炉墙极易掉渣皮。
渣皮中富集的有害元素进入炉缸,吸收大量热量,渣铁流动性变差,不利于高炉生产的顺利进行;而且,渣中Al2O3也呈上升趋势,尽管在配矿中也相应增加了MgO的配比,但难以避免Al2O3突发增高的现象。
因此,为了确保渣铁流动性良好,以及避免炉凉等生产事故的发生,实现炉况长周期的稳定顺行,日常生产中适当提高了铁水含硅量的控制上限,将其控制在0.35%~0.50%。
4.3 强化冶炼
通过总结摸索得到适合1000m3级高炉的上部装料制度,下部制度调整过程中选择好和上部制度相匹配的风速、鼓风动能,维持一定的风口回旋区长度,逐步活跃炉缸,达到上稳下活状态。
高风温不但为高炉带入了宝贵的物理热,而且可以快速加热煤粉,促进煤粉提前着火,有利于煤粉化学能的充分利用。
高风温是实现高煤比和强化燃烧的基础,使用高风温也是提高热风炉利用效率的必然要求。
所以,高炉生产中一方面要努力提高热风炉的操作水平;另一方面在高炉正常生产时,一定要坚持全风温操作。
为了保证充足的炉缸物理热和煤粉燃烧率,通过上下部调剂,1000m3级高炉风温最高用1226℃。
随着负荷加重、煤比提高,压差进一步提高,会威胁到炉况顺行,煤气不稳,甚至有气流管道发生。
如何在高压差条件下,保持炉况稳定顺行,实现高煤气利用率至关重要。
高炉压差高时,接受炉腹煤气量能力较低,为了减少炉腹煤气量,降低煤气阻力,送风制度上不过分追求高风量,采取了提高富氧和炉顶压力的措施,达到了改善煤气利用、降低压差、提高产量的效果。
同时,注重外围设备稳定性,避免由于设备问题给高炉稳定造成隐患,从设备上保证了高炉长期的稳定顺行。
4.4 优化煤焦结构,降低高炉燃料比
高炉通过加强原料质量的管理,完善各项操作制度,加强炉前出铁管理,使高炉冶炼技术进一步提高,随着风量的提高,高炉顶压的提高,利用高顶压稳定气流的效果收到成效,二区高炉在煤粉、焦炭质量变化不大的情况下,燃耗水平显著降低(见图2)。
从统计分析来看,产能提升后,二个区高炉产能水平显著提升,12月份全厂高炉燃料比降低到了524kg/t。
5 实施效果
项目实施后,莱芜钢铁集团有限公司炼铁厂高炉炉况稳定运行,在经济料大幅增加的基础上,产质量得以稳步提升,燃料比由2015年的544kg/t.Fe降低到了2016年的533kg/t.Fe。
炼铁生产成本大幅降低,高炉各项技术指标也得到了保证,确保了高炉长期高效率、安全、低消耗运行,提高了高炉运行的稳定性。
6 结论
炼铁厂分析1000m3高炉特点,探索研究1000m3高炉在“经济产能”下指标的优化与提升,克服了近年来高炉炼铁经济矿入炉引发的炉况波动、燃耗增高、指标恶化等生产问题,借鉴同行业先进经验,引入“经济产能”的概念,系统分析高炉生产关键控制点,分析炉料性价比,创建低成本炉料优化模型,为推行经济冶炼技术做好基础工作;为高炉提升产能创造条件,充分利用高炉供风能力,提高氧量,扩大矿批,提高高炉利用系数,在炉况稳定的基础上优化各项经济技术指标;炉况保持了长时间的稳定顺行,实现了高炉的高产低耗。