第二代余热发电的废气温度及热量分布图.docx
《第二代余热发电的废气温度及热量分布图.docx》由会员分享,可在线阅读,更多相关《第二代余热发电的废气温度及热量分布图.docx(17页珍藏版)》请在冰豆网上搜索。
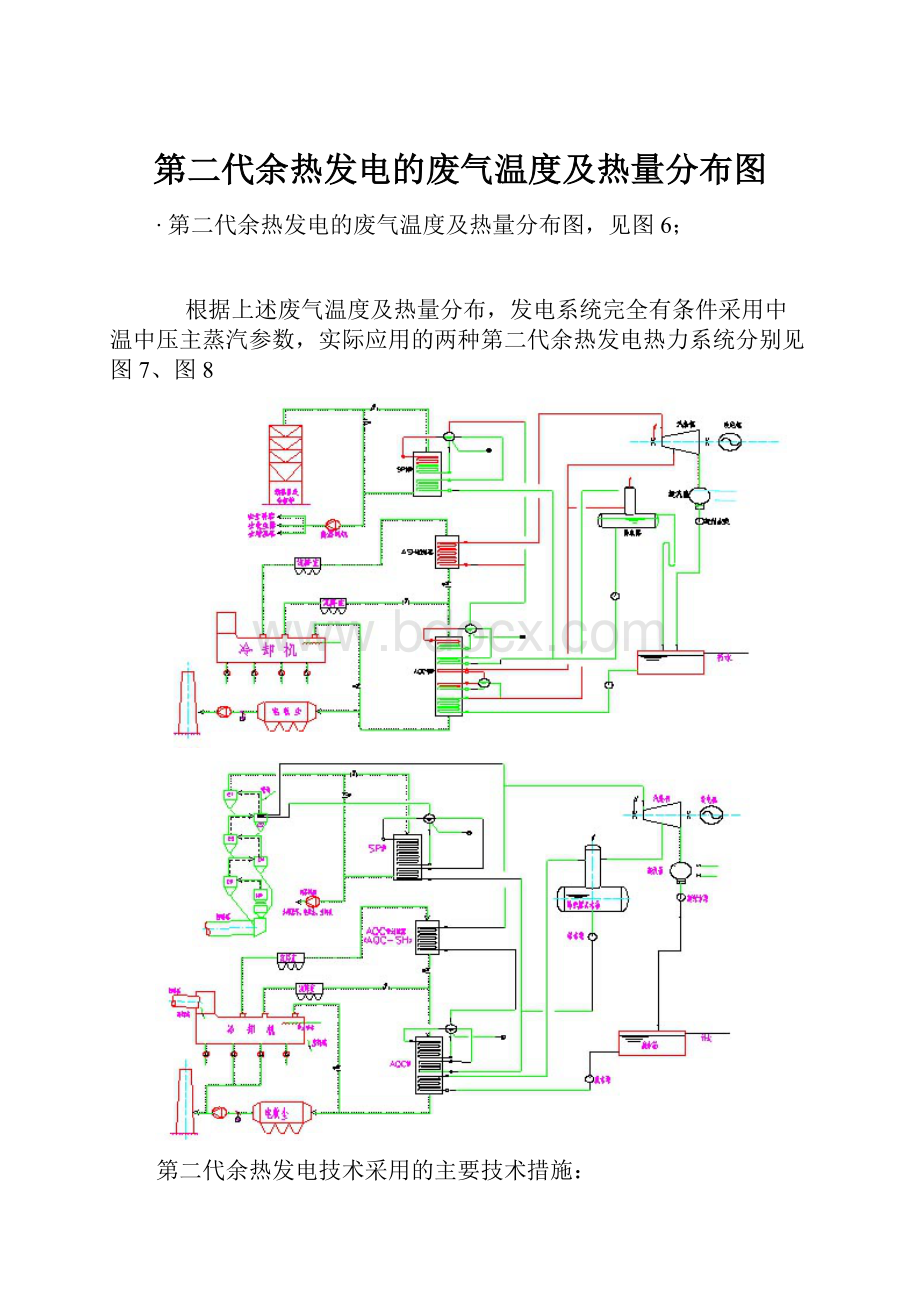
第二代余热发电的废气温度及热量分布图
∙第二代余热发电的废气温度及热量分布图,见图6;
根据上述废气温度及热量分布,发电系统完全有条件采用中温中压主蒸汽参数,实际应用的两种第二代余热发电热力系统分别见图7、图8
第二代余热发电技术采用的主要技术措施:
(1)改变抽取窑头熟料冷却机废气方式,即在靠冷却机进料端(热端)设置一抽取400~600℃废气的抽废气口,同时在冷却机中部设置抽取260~360℃废气的抽废气口。
根据废气温度,利用400~600℃抽废气口抽出的废气设置ASH蒸汽过热器,用于调整控制汽轮机进汽温度;利用260~360℃抽废气口抽出的废气设置AQC炉生产1.57~3.82Mpa次中压或中压饱和蒸汽并同时生产0.1~0.5Mpa饱和温度至180℃的低压低温蒸汽、85~200℃热水。
(2)在利用窑尾预热器系统最终(C1级旋风筒出口)排出的300~350℃废气的同时,利用C2级旋风筒内筒至C1级旋风筒入口的450~600℃废气设置蒸汽过热器。
这样:
一方面C1级旋风筒入口的450~600℃废气温度仅降低20~25℃,是水泥生产所允许的同时不会增加熟料热耗;另一方面,通过设置的C2级旋风筒内筒过热器使SP炉可生产1.57~3.82Mpa次中压或中压饱和温度至450℃的过热蒸汽,见图8。
目前这项技术已在1600t/d窑3000kw纯低温余热电站系统顺利通过实验考核运行。
(3)为了提高窑头熟料冷却机废气余热回收率以提高窑头AQC炉进口废气温度从而进一步提高发电量,窑头熟料冷却机冷却风采用循环风方式,即将AQC炉出口废气部分或全部返回冷却机。
目前这项技术也已在1600t/d窑3000kw纯低温余热电站系统顺利通过实验考核运行。
对于第二代余热发电技术的上述
(2)、(3)项措施,根据工程实际情况,即可以同时采用,也可以采用其中的某一项,也可以两项都不采用。
是否采用上述
(2)、(3)项措施,对余热电站实际发电能力有10~15%的影响。
目前国内预分解水泥窑采用纯低温余热发电的主机设备配置主要为:
1窑头采用余热锅炉(或热交换器),简称为AQC炉,国内都为立式;国外也是。
2窑尾采用余热锅炉(或热交换器),简称为SP炉,国内都为立式;国外为卧式。
3汽轮机,国内采用补汽凝汽式汽轮机;国外为混压式汽轮机。
4发电机,国内采用空冷式发电机;国外也是。
5水处理设备。
6循环冷却设备。
7DCS控制设备。
余热锅炉设备国内制造地主要有哈尔滨、辽宁鞍山、杭州、无锡、盐城和河南洛阳;汽轮机设备国内制造地主要有杭州、南京、青岛、洛阳等。
对于余热锅炉如何适应废气的低温和含尘的高浓度是设备之关键。
因为废气温度低就要增加换热面积;废气的含尘浓度高会带来传热性能降低,并加快设备磨损,尤其是窑头余热锅炉的磨损。
对于汽轮机设备面对的是中、低品位的混压进汽,混压进汽式汽轮机的开发成功,填补了国内汽轮机制造业的空白。
因此可以认为预分解水泥窑纯低温余热发电设备的逐渐成熟正处于应用初始阶段。
一、余热锅炉类
(1)哈尔滨锅炉厂
(2)杭州锅炉集团
(3)南通万达锅炉公司
(4)鞍山锅炉厂
(5)无锡华光锅炉股份公司
(6)中信重型机械公司
(7)盐城锅炉公司
(8)东方锅炉设备制造公司
(9)鞍山锅炉厂
(10)郑州锅炉厂
二、汽轮发电机类
(1)杭州中能汽轮动力公司
(2)南京汽轮机厂
(3)青岛汽轮机厂
(4)中信重型机械公司
(5)杭州发电设备厂
(6)济南发电设备厂
3 主要设备及系统配置
3.1 余热锅炉
余热锅炉按布置形式可分为立式和卧式两种,按循环方式又可分为强制循环和自然循环。
在中低温纯余热发电系统中,一般设置2台余热锅炉,1台为窑尾锅炉通常称SP炉,1台为窑头锅炉通常称AQC炉。
SP炉设置在最后一级预热器和窑尾主排风机之间。
废气温度一般在300~400℃之间,含尘量高,一般为标准状况下50~80g/m3,废气的负压较大。
要求锅炉的换热原件不易积灰,受热面布置便于清灰,且锅炉的密封性能要好。
采取的布置形式一般根据工厂的场地、粉尘的堆积特性等条件确定。
宁国水泥厂的SP炉就选用的卧式锅炉。
卧式锅炉的特点是烟气在炉中水平流动,受热面是蛇形光管,竖直布置上端固定在构架上,下端为自由端,并焊有振打装置之连杆,特殊设计的振打装置对受热面定期振打,加之蛇形管为竖直悬吊在构架上,可使受热面保持干净无灰,从而保证了很高的传热效果。
由于工作介质在蛇形管内上下流动,无法利用其重度差进行自然循环,所以采用强制循环。
锅炉下部用一内置式拉链机将灰输送至锅炉的一端经一锁风喂料机输出。
又如台湾的花莲水泥厂的SP炉则采用的立式锅炉。
立式锅炉的特点是烟气在炉中垂直流动,受热面也采用蛇形光管,但水平布置,分组采用特殊的挂件悬挂在构架上,分组设置振打装置,从上至下逐组振打,也能满足清灰的要求,但这种布置方式比起竖管的清灰干净程度略差,所以在受热面的设置上要考虑上述因素。
以确保锅炉的高效率。
但立式锅炉占地面积小,布置方便。
冷却机的废气虽然含尘量不大,标准状况下约10~20g/m3,但磨蚀性大。
所以AQC炉的设置分前置式和后置式两种。
前置式即AQC设在冷却机与电收尘器之间,这种设置一般还需加预收尘装置以减轻粉尘对AQC炉内的换热管磨蚀,因此系统阻力增加较多,但可以利用图3、图4流程。
后置式即AQC设在电收尘和窑头排风机之间,粉尘对换热管磨耗小,且系统阻力增加不大,但电收尘必须密封性能好,漏风量小,热损失小。
窑头粉尘为熟料颗粒,粘附性不强,所以AQC炉的结灰不严重,一般均选为立式锅炉。
由于窑头的废气温度低,气量大,且对锅炉的排气无特殊要求,应尽可能地回收余热。
为了增大换热面积,强化换热效果,AQC炉的换热管应采用螺旋翅片管或蟹形针管等能显著增加换热面积而又耐磨蚀的管形。
3.2 汽轮发电机
用于余热利用的汽轮发电机其特点是以汽定电,所以要求带负荷的能力可在较大范围内波动,尤其是发电机的选型要考虑能超过设计发电量的15%左右。
目前市场上可用于中低温纯余热发电系统的汽轮发电机有两种。
一种为单压系统的低参数凝汽式汽轮机。
特点是系统简单,适合3000kW左右的小机组。
另一种为混压系统,汽机除主蒸汽进口外还有一至两个补汽口,并辅助采用了热水闪蒸技术,用闪蒸的饱和蒸汽混入汽轮机做功。
特点是系统较复杂,但系统热效率较高,适合6000kW以上机组。
3.3 热力系统
在热力系统的设计上一般是根据废气温度及废气量经过合理配置来确定蒸汽参数和蒸汽量,一般选用的汽轮机的参数比较低。
在余热锅炉设置上,对SP炉来说因出炉的废气还要用于原料的烘干,所以一般SP炉带汽包仅设置过热器和蒸发器。
AQC炉的排烟无特殊要求,主要设置省煤器,也可带汽包设置蒸发器,有可能的情况下也可适当的设置过热器例如窑头采用图3、图4流程。
余热锅炉的受热面的配置,最终是根据余热资源及最大产气量配置的。
由于系统用于水泥厂的余热发电,所以汽机必须带有前压调节装置,当机组在正常运行时,以汽机的进口压力作为主要控制参数,来调节机组输出功率以保证压力基本稳定,这种方式可适应废气余热参数
5)水泥连接系统优化
与杭州锅炉厂合作,设置两台不同参数余热锅炉,保证能够充分利用余热资源。
由于水泥线工艺布置较紧凑,现场空地不多,而窑尾SP锅炉又采用立式锅炉,综合以上因素考虑,将窑尾SP炉布置在窑尾预热器后的高温风机之上。
由于出冷却机的余气温度大约300℃左右,为提高主蒸汽品质,需对冷却机进行改造,可从冷却机中部(原煤磨抽风处)引出管道,抽出350℃左右的废气送至沉降室,滤去大颗粒粉尘后再由管道分别引向AQC锅炉和煤磨。
原余风管路系统可做为锅炉的旁通烟道,当锅炉故障或水泥生产不正常时可关闭去AQC锅炉的阀门,气流可不经锅炉而由此旁路系统直接排至窑头收尘器。
在冷却机原余风管路上、新设的去锅炉管路上和出锅炉管路上均增设电动百叶阀门,以实现对气流的控制和切换。
2双压纯低温余热发电技术介绍
双压余热发电技术就是按照能量梯级利用的原理,在同一台余热锅炉中设置2个不同压力等级的汽水系统,分别进行汽水循环,产生高压和低压两种过热蒸汽;高压过热蒸汽作为主蒸汽、低压过热蒸汽作为补汽分别进入补汽凝汽式汽轮机,推动汽轮机做功发电,双压余热发电系统使能量得到合理利用,热回收效率高。
余热资源参数不同,余热锅炉的低压受热面与高压受热面有不同的布置方式。
根据辽源金刚水泥厂窑头(AQC)和窑尾(SP)的余热特点和工艺要求,经过余热利用后,要使AQC余热锅炉排烟温度降到100℃左右。
使窑尾SP余热锅炉排烟温度降低到220℃左右后进入原料磨烘干原料,其设置的双压余热发电系统简图如图1。
双压余热发电系统与常规余热发电系统不同之处在于其窑头(AQC)余热锅炉增设了低压汽水系统,其汽轮机组在第四压力级之后增加了补汽口,并适当增大补汽口以后汽轮机通流部分面积。
采用双压系统的主要目的是为了提高系统循环效率。
使低品位的热源充分利用,获得最大限度的发电功率,降低窑头(AQC)双压余热锅炉的排气温度;其次是双压系统的低压蒸汽是过热的,进入汽轮机后能保证汽轮机内的蒸汽最大湿度控制在14%以下,使汽轮机叶片工作在安全范围内,并提高机组的效率;同时低压蒸汽还可用于供热等其它需要热源的地方,提高运行灵活性。
双压余热发电系统简单灵活、成本低、热利用率高。
由于在余热锅炉上增设了低压省煤器、低压蒸发器,并且增设了低压过热器,能够把更多的低温余热吸收利用,比单压系统多发电10%左右,并且必要时能够解列,维持单压系统正常运行。
而对于能够增加发电量的闪蒸系统来说,需要增加闪蒸器、汽水分离器等设备;闪蒸器产生的是饱和蒸汽,在进入汽轮机做功后,易使汽轮机排汽干度不能满足汽轮机的要求。
3.2设计特点
3.2.1电站工艺系统特点
根据辽源金刚水泥厂的余热条件,结合朗肯循环原理,对能量进行梯级利用,采用双压工艺热力系统,可使相对高温热源(210~350℃烟气)产生较高参数的蒸汽,使相对低温热源(100~210℃烟气)产生较低参数的蒸汽,使能量分布优化,提高热力系统循环效率。
在窑尾预热器废气出口设置SP余热锅炉。
从预热器出来的350℃左右的烟气从顶部进入SP余热锅炉,由于其烟气粉尘浓度高为80-100g/Nm3、粉尘颗粒细、粉尘比电阻高、粉尘硬度低等特点,对锅炉受热面的磨损不严重、但容易积灰,因此在SP余热锅炉内设置振打除灰装置。
烟气在锅炉内经过能量交换后,温度为220℃左右,进入原水泥系统。
在窑头冷却机废气出口设置AQC余热锅炉,采用双压技术。
由于窑头烟气带着磨损性较强的熟料微粒,含尘浓度为20-30g/Nm3左右,具有干燥,粉尘粒径粗、磨损性大、粘附性不强等特点;为减轻锅炉磨损,提高锅炉的使用寿命,在AQC锅炉前设置沉降室。
350℃左右的烟气从篦冷机中部抽出后进入沉降室,在沉降室内约有60%的灰尘沉降下来,灰尘通过拉链机送到水泥熟料系统,烟气再从顶部进入AQC余热锅炉,在锅炉内经过能量交换成为温度为100℃左右的烟气,进入水泥系统的窑头电收尘器。
余热发电汽水系统流程为:
给水经高压给水泵进入AQC余热锅炉公共省煤器后,被加热成为饱和水后,分成二路分别进入AQC锅炉高压系统和SP锅炉。
另一路低压给水经低压给水泵进入低压省煤器后,进入AQC锅炉低压系统。
进入AQC高压系统和SP锅炉的水经过锅炉内部循环被加热成过热蒸汽;进入AQC低压系统的水被加热成低压补汽,两台锅炉的过热蒸汽混合后和低压补汽分别进入汽轮机前端高压进汽口和中
部低压补汽口做功发电。
为了保证电站事故时不影响水泥窑生产顺利进行,余热锅炉均设有旁通废气管道,一旦余热锅炉或电站发生事故时,可以将余热锅炉从水泥生产系统中解列,不影响水泥生产的正常运行。
以上电站工艺系统特点,可以使电站运行方式灵活、可靠,很好地与水泥生产配合,并最大限度地利用余热。
3.2.2余热发电系统的接入
由于水泥线工艺布置较紧凑,现场空地不多,而窑尾SP锅炉又采用立式锅炉,所以将窑尾SP炉布置在窑尾预热器后的高温风机之上。
在每条线最上一级(C1级)预热器至窑尾高温风机的下行管道上引出废气管道与SP锅炉相连。
锅炉出口烟气温度在220℃左右,送到窑尾高温风机进风口的管道上,以满足下道工序烘干原料和煤的需要。
烘干原料和煤后的废气由原废气处理系统的收尘器净化后排入大气。
控制锅炉的烟气阻力≤1000Pa,使系统的阻力在窑尾高温风机的能力允许范围之内。
在原预热器出口至高温风机的烟道引出管道、原下行管道以及锅炉出口管道上均增设电动百叶阀门,对气流进行控制和切换,原下行管道可做为锅炉的旁通烟道。
当需要提高烘干原料和煤的烟气温度时,可适当调节下行烟道调节阀,让锅炉出口的低温烟气和C1级出口直接下行的高温烟气混合,提高进窑尾风机(原料磨)的烟温,其调节范围从220℃或更低直至C1级出口温度(即烟气一点不通过SP锅炉),而且SP炉的进口烟道阀和旁路烟道阀,正常设计在窑控制室操作,窑操可随时根据具体情况调整,既满足了水泥生产的稳定运行,又保证了SP炉的安全。
通过旁通烟道的调节作用还可使水泥生产及余热锅炉的运行均达到理想的运行工况。
在熟料冷却机与窑头收尘器之间设一台AQC锅炉,由废气管道连接。
为保证锅炉正常产汽量,需对冷却机进行改造,从冷却机中部(原煤磨抽风处)引出管道,抽出350℃左右的废气送至沉降室,滤去大颗粒粉尘后再由管道引向AQC锅炉。
从冷却机中部抽风的目的是提高进入AQC余热锅炉的废气温度,提高整个系统的循环效率。
每条线出AQC锅炉的废气进入原有的窑头收尘器收尘后,由原有窑头排风机排放,冷却机剩余的低温余风仍由原管路进窑头收尘器。
原余风管路系统可做为锅炉的旁通烟道,当锅炉故障或水泥生产不正常时可关闭去AQC锅炉的阀门,气流可不经锅炉而由此旁路系统直接排至窑头收尘器。
在冷却机原余风管路上、新设的去锅炉管路上和出锅炉管路上均增设电动百叶阀门,以实现对气流的控制和切换。
锅炉和沉降室的烟气总阻力控制小于1000Pa,使改造后的气体流量和压力在窑头排风机的能力允许范围之内。
3.2.3废灰处理
窑尾SP余热锅炉管束上的积灰经过振打装置振下后通过螺旋输送机送到原水泥系统增湿塔下面的链式输送机,与增湿塔下来的料混合后,温度降低,对系统设备不会造成影响,再通过链式输送机送到原料库;AQC余热锅炉及沉降室的积灰量清下后通过拉链机送到熟料输送机,再由熟料输送机送到熟料库。
3.2.4循环冷却水系统
循环冷却水系统包括循环冷却水泵站、冷却构筑物、循环水池及循环水管网。
运行时,循环冷却水泵自循环水池抽水送至各生产车间供生产设备冷却用水,冷却过设备的水(循环回水)利用循环水泵的余压送至冷却构筑物,冷却后的水流至循环水池,供循环水泵继续循环使用。
为确保该系统良好、稳定的运行,系统中设置了加药和旁滤设备。
加药系统采用两套自动加药装置定期加入阻垢剂与杀菌剂,分别投加HEDP和ClO2。
HEDP除去水中的Ca2+,Mg2+等金属离子,降低水的硬度,防止设备、管道结垢;ClO2防止水中滋生藻类,同时可以杀菌作用。
3.2.5化学水处理系统
为了保证锅炉给水水质,提高供水安全可靠性考虑,建设一条一级反渗透+一级混床除盐的除盐水系统。
考虑采用一级反渗透+混床水处理系统的原因为:
①用一级反渗透+混床制除盐水,与用软化水相比较:
可降低锅炉排污率,从而降低热量的损失,提高了余热的利用效率。
用一级反渗透+混床制除盐水的排污率为0.4%,用软化水的排污率为7.5%。
可大大提高了补给水水质,解决了中低压锅炉中常用软化水作补给水而引起的硅酸盐结垢的问题。
有利于锅炉的长期稳定运行,延长了锅炉的使用寿命。
由于纯低温余热发电利用废烟气,温差波动较大,造成锅炉负荷变化大,因此蒸汽中携带的盐分较多,在过热器及汽轮机中造成盐类的积聚,引起过热器堵塞及汽轮机故障,选用纯度较高的除盐水,能在负荷不稳的情况下保证蒸汽的品质,提高系统运行的可靠性。
②用一级反渗透+混床制除盐水与用一级除盐水相比较,
可降低酸碱耗量,一级反渗透+混床的再生酸碱耗量为一级除盐水的5%,从而减少了酸碱废水的排放量,有利于环境保护。
减少了系统的频繁再生操作,使系统的运行操作更简单,
系统的出水水质更易得到保证,且大大提高了出水水质。
采用一级反渗透+混床水处理系统符合系统及现场的条件,有利于系统的稳定运行。
3.2.6除氧系统
为控制锅炉给水的含氧量,减少溶解氧对热力系统设备的腐蚀,根据余热发电工艺要求,进入锅炉的给水含氧量必须≤0.05mg/l。
采用化学药剂除氧,在给水中加入化学还原药剂联氨(N2H4),使其与氧反应生成无腐蚀的稳定化合物,将水中的溶解氧除去。
其反应方程式如下:
N2H4+O2=N2↑+2H2O
其反应产物N2和H2O对热力系统没有任何害处,在200℃以上的高温水中,N2H4还可以将Fe2O3还原成Fe3O4、FeO以及Fe。
联氨的这些性质对防止锅炉内的铁垢有一定的作用。
被广泛地应用于中、高压锅炉给水的化学除氧处理。
采用化学除氧的原因:
常用的除氧方法有热力除氧、真空除氧、化学除氧(包括药剂除氧和钢屑除氧)、解析除氧等。
热力除氧不符合工艺要求(给水水温55℃,锅炉排烟温度95℃左右),如果改变工艺,则造成系统的复杂;
采用真空除氧造成操作及系统复杂,由于在真空状态下,被除氧的水温度对除氧效果有着直接关系,除盐水温度应高出除氧器运行的真空度所对应的饱和温度3-5℃,水喷射真空泵工作的循环水温应低于该饱和温度3-5℃。
两者温差为6-10℃,只有控制好这一温差,除氧效果才能好,在实际运行中,由于运行条件的变化及四季的变换,这一温差不好控制、操作困难,除氧不很可靠。
采用化学除氧的铁屑除氧在运行时需要反洗,要经常更换滤芯,维护费用较大。
采用解析除氧要消耗燃料,工艺复杂。
采用化学除氧的药剂除氧。
可以简化全厂的热力系统并保证除氧效果。
综合考虑,采用化学药剂除氧系统。
3.2.7保温
由于本工程地处东北严寒地区,需对室外的仪表等设备进行伴热保温。
电气设备各测点的导压管、变送器设置自限温伴热带,同时设置保温箱以确保仪表灵敏、准确工作;对于室外液位计、现场控制箱等需防冻的设备,设置保温箱进行保护。
3.3主要设备
3.3.1窑头(AQC)双压余热锅炉
其型号为:
QC180/350-14(4)-1.6(0.35)/330(165)。
是为满足5000t/d水泥熟料生产线的窑头冷却机的余热回收而设计的。
锅炉规范及主要参数为:
1、锅炉额定蒸发量:
14(4)t/h
2、额定蒸汽压力:
1.6(0.35)MPa(g)
3、额定蒸汽温度:
330(165)℃
4、给水温度:
55℃
5、余热烟气量:
180000Nm3/h
6、余热烟气进口温度:
350℃
7、设计烟气出口温度:
95℃
8、烟气含尘量:
30g/Nm3
AQC余热锅炉采用双压结构,高压段出口额定蒸汽压力为1.6MPa(g),低压段出口额定蒸汽压力为0.35MPa(g)。
AQC锅炉整体采用管箱式结构,自上而下有高压过热器管箱、两级高压蒸发器管箱、高压省煤器管箱、低压过热器管箱、低压蒸发器管箱,高低压省煤器管箱。
管箱采用左右对称结构共14只管箱,这些管箱均通过底座型钢将自身重量传递到钢架的横梁上。
采用这种管箱式结构,可将锅炉漏风降至最低,提高锅炉效率,减少现场安装的工作量。
3.3.2窑尾(SP)余热锅炉
其型号为:
QC340/350-24-1.6/320。
是为满足5000t/d水泥熟料生产线的窑尾预热器(SP)的余热回收而设计的。
锅炉规范及主要参数为:
1锅炉额定蒸发量:
24t/h
2额定蒸汽压力:
1.6MPa(g)
3额定蒸汽温度:
320℃
4给水温度:
134℃
5余热烟气量:
340000Nm3/h
6余热烟气进口温度:
350℃
7设计烟气出口温度:
220℃
SP余热锅炉采用单锅筒自然循环方式、露天立式布置,结构紧凑、占地小。
烟气从上向下分别横向冲刷过热器、五级蒸发器、省煤器,气流方向与粉尘沉降方向一致。
图2和图3是AQC余热锅炉和SP余热锅炉T-Q图
3.3.3补汽凝汽式汽轮机
其型号为:
BN6.5-1.5/0.35。
是为满足水泥行业5000t/d熟料生产线双压余热发电而设计的低参数汽轮机,适合水泥厂及其它具有中低温废热资源单位使用。
其主要参数为:
装机功率:
6.5MW
额定转速:
3000r/min
进汽压力:
1.5Mpa(a)
进汽温度:
300℃
进汽量:
38t/h
补汽压力:
0.35Mpa(a)
补汽温度:
155℃
补汽量:
?
4t/h
排汽压力:
0.007Mpa(a)
排汽温度:
39.02℃
汽轮机补汽缸采用渐缩蜗壳式结构,保证低压蒸汽能均匀补进汽轮机,补进后能与主蒸汽均匀混合;末级叶片采用扭叶片,提高汽轮机后缸热力性能和汽轮机的效率。
对于补汽式汽轮机,在主蒸汽及补汽参数确定后,补汽点的选取和补汽结构的设计是关键。
补汽点位置选取不当会造成蒸汽补不进去或补汽损失太大,在经过详细的汽轮机通流部分计算,兼顾额定工况、最大工况和变工况以及汽轮机的实际结构后,确定补汽点为第四压力级后。
汽轮机高压主蒸汽参数的确定:
高压主蒸汽压力增加使蒸汽焓降有所增加,但同时压力增加使进汽比容减小,由于高压级叶片较短,损失增加;压力增加也使排汽湿度增加,对末级叶片的安全性及经济性不利。
而且压力增加也使系统耗功增加,所以汽轮机进汽压力并非越高越好,经过优化后取汽轮机进汽压力为1.5MPa(a)。
机组出力随主蒸汽温度的提高而明显地增加,但它受余热烟气温度的限制。
考虑锅炉投资同增加出力的关系取热端温差为25℃。
同时考虑到沿途散热及损失的影响,进汽轮机的主蒸汽温度定为300℃。
汽轮机低压补汽参数的确定:
低压补汽参数的选取从三个方面来考虑:
(1)最佳的经济性,补汽压力的确定要使汽轮机出力最大。
(2)补汽温度同主流温度要匹配,补汽与主蒸汽温差不宜太大,这是为了降低补汽口处缸体的热应力。
(3)补汽过热度要求,补入蒸汽带有湿度不利于机组安全运行,设计要求在任何工况下补汽的过热度大于11℃。
综合以上情况选取补汽压力为0.35MPa(a),补汽温度为155℃,过热度为16℃。
2设计范围
本工程机务部分的设计范围包括烟风系统,6Mw汽轮发电机组范围内的主辅机选
型,设备布置及安装图设计,工艺管道安装图设计等内容。
3主要设备技术规范
(1)余热锅炉
窑头锅炉(AQc锅炉):
型号:
QCl30/360—9.5—1.8/330
烟气进余热锅炉:
流量为130000Nm3/h,温度为360℃
烟气出余热锅炉:
流量为l30000Nm3/h,温度为约100℃
过热蒸汽参数:
压力:
1.8MPa
温度:
330℃
流量:
9.5t/h
为立式布置,自然循环方式
窑头粉尘预处理器:
处理烟气量:
140000Nm3/h
烟气温度:
390℃
阻力:
≤1000Pa
窑尾锅炉(SP锅炉):
型号:
QC240/360—22.5一1.65/330
烟气进余热锅炉:
流量240000Nm3/h,温度为360℃
烟气出余热锅炉:
流量240000Nm3/h,温度为220℃
过热蒸汽参数
压力:
1.