化工安全课程设计概述doc 4+页优秀免费下载版.docx
《化工安全课程设计概述doc 4+页优秀免费下载版.docx》由会员分享,可在线阅读,更多相关《化工安全课程设计概述doc 4+页优秀免费下载版.docx(58页珍藏版)》请在冰豆网上搜索。
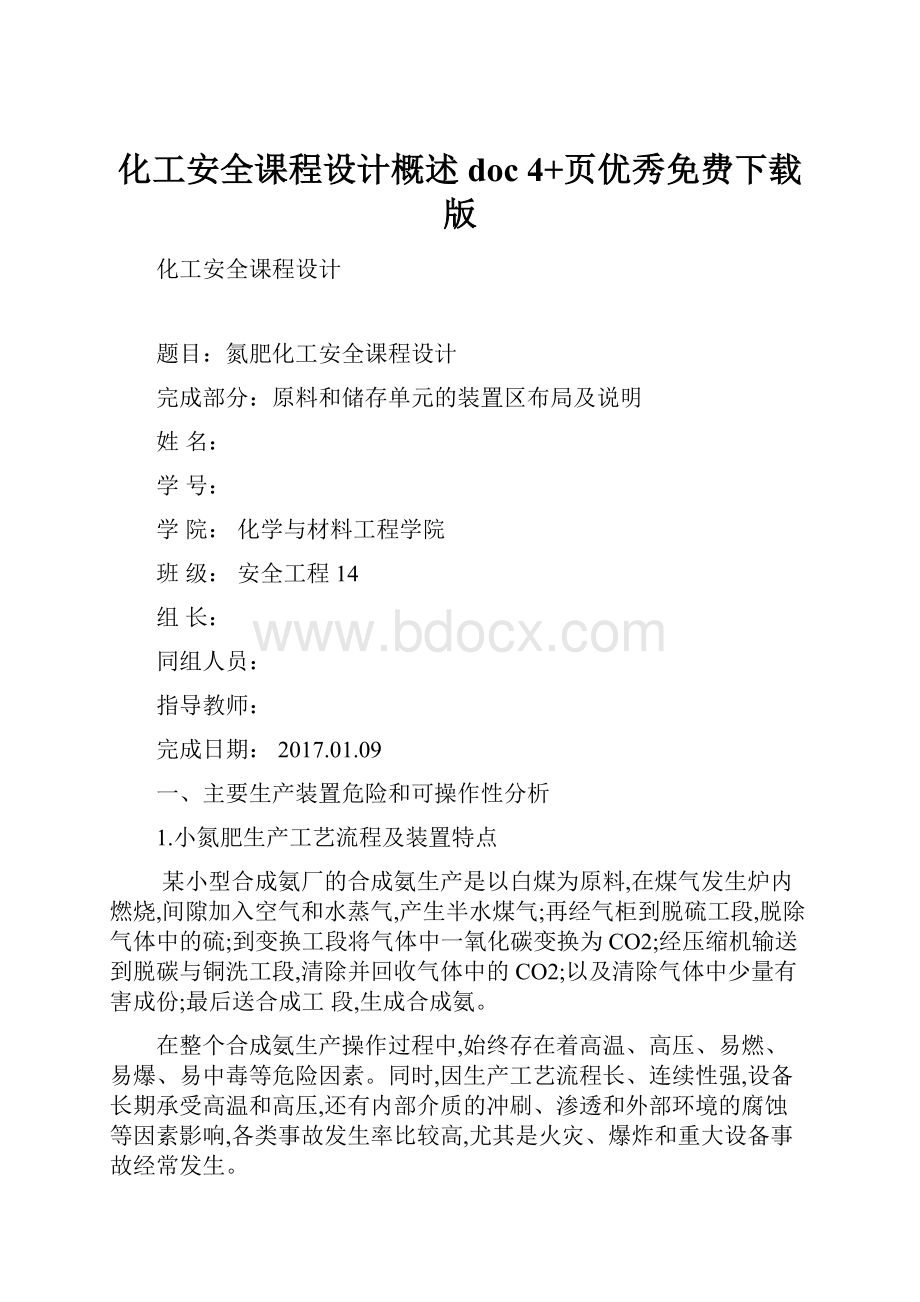
化工安全课程设计概述doc4+页优秀免费下载版
化工安全课程设计
题目:
氮肥化工安全课程设计
完成部分:
原料和储存单元的装置区布局及说明
姓名:
学号:
学院:
化学与材料工程学院
班级:
安全工程14
组长:
同组人员:
指导教师:
完成日期:
2017.01.09
一、主要生产装置危险和可操作性分析
1.小氮肥生产工艺流程及装置特点
某小型合成氨厂的合成氨生产是以白煤为原料,在煤气发生炉内燃烧,间隙加入空气和水蒸气,产生半水煤气;再经气柜到脱硫工段,脱除气体中的硫;到变换工段将气体中一氧化碳变换为CO2;经压缩机输送到脱碳与铜洗工段,清除并回收气体中的CO2;以及清除气体中少量有害成份;最后送合成工段,生成合成氨。
在整个合成氨生产操作过程中,始终存在着高温、高压、易燃、易爆、易中毒等危险因素。
同时,因生产工艺流程长、连续性强,设备长期承受高温和高压,还有内部介质的冲刷、渗透和外部环境的腐蚀等因素影响,各类事故发生率比较高,尤其是火灾、爆炸和重大设备事故经常发生。
2.小氮肥生产中的火灾爆炸因素分析
2.1造气工段
造气工段主要制造半水煤气,其主要成分如下:
H2,CO,CO2,N2及极少量的CH4,O2和微量的H2S[8]。
H2,CO、CH4极易爆炸。
在生产过程中,一旦空气进入煤气柜、洗气塔、煤气总管,H2,CO和CH4等与空气混合形成爆炸性混合气体,遇到明火或获得发生爆炸的最小能量,即可发生爆炸。
氧含量是煤气生产过程中一个重要的控制指标,要求控制在0.5%(体积比)以下。
氧含量的增高,意味着火灾、爆炸危险性的增加。
另外,在进行停车作业检修过程中,对于设备、管道、阀门等,如果没有进行置换或置换不干净,在用火作业前没有进行动火分析,确定的取样分析部位不对而导致分析结果失真,或者进行作业时,没有采取可靠的隔绝措施,导致易燃易爆气体进入动火作业区域,均可导致火灾、爆炸事故。
2.2脱硫工段
半水煤气中的H2,CO,CH4和H2S等都是易燃易爆的气体。
在脱硫工段,常因设备或管道泄漏造成火灾、爆炸;也会因操作不慎、设备缺陷等原因,导致罗茨鼓风机抽负压,使得空气进入系统,与半水煤气混合,形成可爆炸性气体,引起爆炸事故。
在生产系统的设备和管道表面,由于H2S气体的作用,常会生成一层疏松的铁的硫化物(FeS与Fe2S),该硫化物遇到空气中的氧,极易引起氧化反应,放出大量的热,很快使自身温度升高并达到其燃点而引起自燃。
同时,在检修时,设备管道敞开后,也常会因其内部表面铁的硫化物和煤焦油与进入的空气迅速发生氧化反应而引起自燃着火的现象。
2.3变换工段
变换工段是在一定的温度和压力下进行的,既存在物理爆炸的危险性,又存在化学爆炸的危险性。
在生产过程中,由于设备和管道在制造、检维修中本身存在缺陷或者气体的长期冲刷,设备、管道会因腐蚀等造成壁厚减薄、疲劳,进而产生裂纹等缺陷,如果不能及时发现,及时消除,极易因设备、管道因为承受不了正常工作压力而发生物理爆炸,其后果又可能引发次生火灾及化学爆炸。
半水煤气转换为变换气后,气体中的H2含量显著增加,高温气体一旦泄漏出来,遇空气易形成爆炸性混合物,遇火或高热很容易引起火灾、爆炸事故;如果设备或生产系统形成负压,空气被吸入与煤气混合,形成爆炸性混合物,在高温、摩擦、静电等作用下,也会引起化学爆炸;如果生产系统半水煤气中氧含量超过工艺指标,会引起过氧爆炸,违章动火,违章检修,也会引起化学爆炸。
2.4压缩工段
易燃、易爆气体经压缩机加压后,其压力和温度都得到提高,可燃气体的爆炸范围随温度高、压力大而扩大。
若高压气体泄漏到空间,即使有少量的也容易形成爆炸性混合物,同时高温、高压气体泄漏时,气流冲击产生静电火花,极易引起火灾、爆炸事故。
2.5脱碳与铜洗工段
铜洗工段的压力及H2浓度很高。
同时,高、低压连通部位多,容易发生高压串到低压部分,导致发生物理爆炸、化学爆炸和火灾危险。
2.6合成工段在小氮肥生产中,合成工段属于高温、高压工段,且高压、低压并存,这决定了对生产合成氨的设备、管道必须有更高要求。
如果因为材质本身的缺陷,制造质量不过关,维修质量不合格,外界压力超过设备、管道的承受压力,便会发生物理爆炸,同时也会引发化学爆炸。
在高温高压下,H2对碳钢有着较强的渗透能力,形成氢腐蚀,使钢材脱碳而变脆(即氢脆);N2也会对设备发生渗氮作用,从而减弱其机械性能;材料自身在高温高压下会发生持续的塑性变形,改变其金相组织,从而引起材料强度、延伸等机械性能下降,使材料产生拉伸、起泡、变裂和裂纹而破坏。
氢脆、氮蚀、塑性变形的发生,也可引起爆炸事故的发生。
合成工段主要使用H2为原料,反应生成了氨。
H2和NH3是易燃易爆气体,而且其爆炸极限在高温高压下将扩大,一旦发生泄漏而与空气混合,极易发生爆炸。
二、装置区布局及说明
1、装置区布局的大体设计要求
1)重量大的设备设置在地基最好的地方。
2)换热器尽量设在地上。
3)按照流程图,对设备周围的配管、阀门仪表等的安装位置进行研究,留出充分的空间,以免互相碰撞。
4)施工所需要的道路及安装所需要的空间。
5)为了将来扩建,预留适当的空间,另外还要考虑与原有危险性大的设备保持安全距离。
6)因为在运转或维修时可能会有化学危险物等流出,所以泵、换热器、塔、槽等设备的周围地面应进行铺装,并用高于15cm的围堰围住。
7)设备与设备之间以及这些设备与其他设备之间所铺设的通道的宽度应为0.8m以上。
8)装置内的道路两个方向都是通路,不能有死路,以便在发生火灾时消防车的进出。
9)装置内的设施均应通风良好,不能有滞留气体的地方。
10)装置平面布置设计应满足工艺流程要求,按物流顺序布置设备。
11)装置平面布置设计应满设备的间距、建筑物、构筑物的防火间距要求,符合安全生产和环境保护要求。
12)装置平面布置设计应考虑管道安装经济合理和整齐美观,节省用地和减少能耗,便于施工、操作和维修。
13)装置平面布置设计应满足全厂总体规划的要求;装置主管廊和设备的布置应根据装置在工厂总平面图上的位置以及有关装置、罐区、系统管廊、道路等的相对位置确定,并以相邻装置的布置相协调。
14)装置平面布置设计应根据全年最小风频率风向确定设备、设施与建筑物的相对位置。
15)设备应按工艺流程顺序和同类设备适当集中相结合的原则进行布置。
在管廊两侧按流程顺序布置设备、减少占地面积、节省投资。
处理腐蚀性、有毒、粘稠物料的设备宜按物性分别布置。
16)设备、建筑物、构筑物应按生产过程的特点和火灾危险性类别分区布置。
为防止结焦、堵塞、控制温降、压降,避免发生副反应等有工艺要求相关的设备,可靠近布置。
17)工艺设备的竖向布置,应按下列原则考虑:
工艺设计不要求架高的设备,尤其是重设备,应落地布置;由泵抽吸的设备和容器以及真空、重力流、固体卸料等设备,应满足工艺流程的要求,布置在合适的高层位置;当装置的面积受限制或经济上更为合理时,可将设备布置在构架上。
18)在确定设备和构筑物的位置时,应使其地下部分的基础不超出装置边界线。
附:
装置内通道的最小净宽和最小净高单位:
m
1
主要车行道路
4
4.5
2
消防、检修道路
4
4.5
3
大型装置区块之间的道路
6
4.5
4
泵区检修通道
2
3.2
5
操作、连接通道
0.8
2.2
2.氮肥生产流程
氮肥生产流程可概括为以下四个步骤:
(1)造气—将原料制备成主要含有氢、氮气体的原料气。
(2)精制—将原料气中氢、氮以外的杂质去除,使原料气得到精纯。
(3)压缩与合成—将较为纯净的氮、氢比例为1:
3的氮氢混合气体压缩到高压状态,在催化剂和高温的作用下合成为氨。
(4)氨加工—将氨经进一步加工得氮肥。
前三步常称为氨的合成。
经进一步加工制得的成品如硝酸铵、尿素等都是化肥。
合成氨流程图
2.1造气工段
造气实质上是碳与氧气和蒸汽的反应,主要过程为吹风和制气。
具体分为吹风、上吹、下吹、二次上吹和空气吹净五个阶段。
原料煤间歇送入固定层煤气发生炉内,先鼓入空气,提高炉温,然后加入水蒸气与加氮空气进行制气。
所制的半水煤气进入洗涤塔进行除尘降温,最后送入半水煤气气柜。
2.2脱硫工段
煤中的硫在造气过程中大多以H2S的形式进入气相,它不仅会腐蚀工艺管道和设备,而且会使变换催化剂和合成催化剂中毒,因此脱硫工段的主要目的就是利用DDS脱硫剂脱出气体中的硫。
气柜中的半水煤气经过静电除焦、罗茨风机增压冷却降温后进入半水煤气脱硫塔,脱除硫化氢后经过二次除焦、清洗降温送往压缩机一段入口。
脱硫液再生后循环使用。
2.3变换工段
变换工段的主要任务是将半水煤气中的CO在催化剂的作用下与水蒸气发生放热反应,生成CO2和H2。
经过两段压缩后的半水煤气进入饱和塔升温增湿,并补充蒸汽后,经水分离器、预腐蚀器、热交换器升温后进入中变炉回收热量并降温后,进入低变炉,反应后的工艺气体经回收热量和冷却降温后作为变换气送往压缩机三段入口。
2.4变换气脱硫与脱碳
经变换后,气体中的有机硫转化为H2S,需要进行二次脱硫,使气体中的硫含量在25mg/m3。
脱碳的主要任务是将变换气中的CO2脱除,对气体进行净化,采用变压吸附脱碳工艺。
来自变换工段压力约为1.3MPa左右的变换气,进入水分离器,分离出来的水排到地沟。
变换气进入吸附塔进行吸附,吸附后送往精脱硫工段。
被吸附剂吸附的杂质和少量氢氮气在减压和抽真空的状态下,将从吸附塔下端释放出来,这部分气体称为解析气,解析气分两步减压脱附,其中压力较高的部分在顺放阶段经管道进入气柜回收,低于常压的解吸气经阻火器排入大气。
2.5碳化工段
2.5.1气体流程
来自变换工段的变换气,依次由塔底进入碳化主塔、碳化付塔,变换气中的二氧化碳分别在主塔和付塔内与碳化液和浓氨水进行反应而被吸收。
反应热由冷却水箱内的冷却水移走。
气体从付塔顶出来,进入尾气洗涤塔下部回收段,气体中的少量二氧化碳和微量的硫化氢被无硫氨水继续吸收,再进入上部清洗段。
气体中微量二氧化碳被软水进一步吸收,最后达到工艺指标经水分离后,送往精脱硫塔进一步脱硫后,送往压缩机三段进口。
2.5.2液体流程
浓氨水由浓氨水泵从吸氨岗位浓氨水槽打入付塔,一方面溶解塔内的结疤,另一方面吸收主塔尾气中的剩余二氧化碳,逐步提高浓氨水的碳化度。
然后,付塔的溶液由碳化泵从底部抽出,打入主塔,在主塔内进一步吸收变换气中的二氧化碳,生成含碳酸氢铵结晶的悬浮液,再由底部取出管压入分离岗位进行分离。
回收塔回收段中的无硫氨水来自合成或铜洗工段使用过的无硫氨水和回收段的稀氨水压入稀氨水压入吸氨岗位母液槽和稀氨水槽或送脱硫岗位使用,从回收段出来的水直接排污水沟。
2.6甲醇合成工段
联醇是将经变换、脱碳后的净化气中的CO:
1-5%、CO2<0.5%(其含量可根据生产所要求的醇氨比调节)与气体中的H2经压缩机加压到15MP后,依次经过洗氨塔、油分、预热器、废热锅炉进入合成塔,在催化剂的作用下合成为甲醇,同时起到气体净化的作用。
醇后气中CO<0.5%、CO2<0.2%。
出塔气体经水冷却到40℃左右,将气体中的甲醇冷凝,使气体中的甲醇含量小于0.5%,经醇分离器分离出甲醇后,一部分气体经甲醇循环机返回甲醇合成塔,大部分气体进入精炼工段。
2.7精炼工段
醇后工艺气中还含有少量的CO和CO2。
但即使微量的CO和CO2也能使氨催化剂中毒,因此在去氨合成工序前,必须进一步将CO和CO2脱除。
醇后气体由铜洗塔底部进入,与塔顶喷淋的醋酸铜氨液逆流接触,将工艺气中的CO和CO2脱除到25ppm以下,经分离器将吸收液分离后送往压缩机六段进口。
铜氨液从铜洗塔经减压还原、加热、再生后,补充总铜、水冷却、过滤、氨冷后经铜氨液循环泵加压循环使用。
2.8压缩工段
压缩工段的压缩机为六段压缩。
由于合成氨生产过程中,变换、脱碳、粗醇与氨合成分别在0.87MPa、3.7MPa、15MPa、27MPa条件下进行,压缩工段的任务就是提高工艺气体压力,为各个生产工段提供其所需的压力条件。
2.9氨合成工段
氨合成工段的主要任务是将铜洗后制得的合格N2、H2、混合气,在催化剂的存在下合成为氨。
压缩机六段来的压力为27MPa的新鲜补充气,与循环气混合后进入氨冷器、氨分离器、冷交换器,经循环机升压并经过油分离器除油后进入氨合成塔的内件与外筒的环隙,冷却塔壁,出来后经预热器升温后进入氨合成塔内件,完成反应后离开反应器,分别进入废热锅炉、预热器、软水加热器回收热量,最后经水冷器、冷交换器、氨冷器降温冷却,将合成的氨液化分离出系统,未反应的氮氢气循环使用。
2.10冷冻工段
由于氨合成工段需要通过液氨气化来产生低温生产条件,因此冷冻工段的任务就是把气态的氨重新液化。
由氨蒸发器蒸发的气氨经气氨总管进入冰机前分离器,分离出液氨后进入氨压缩机加压,加压后的气氨经油分离器后进入水冷器,在此气氨冷凝为液氨并回到冰机液氨贮槽,由支出阀送给氨蒸发器循环使用或氨库。
3.主要设备布置规范
3.1泵
(1)各类分离器和泵之间间距在4.5m左右
(2)泵类于换热器间距保持在4.5m左右
(3)各类液罐的间距保持在2到4m之间
(4)泵基础对齐
(5)前方的操作检修通道不应该小于1.25m。
标高设置在0.3m
3.2加热炉的布置
(1)传递管线最短
(2)明火加热炉宜集中布置在装置的边缘并靠近消防通道,且位于可燃气体、液化烃、甲B、乙A类设备的全年最小频率风向的下风侧。
(3)加热炉可按炉子中心线对齐,并成排布置。
加热炉炉体之间的净距不宜小于3m。
(4)采用机动吊装机具吊装炉管时,应有机动吊装机具通行的通道和检修场地。
对于水平布置炉管的加热炉,加热炉的一侧应有炉管抽出的检修场地,检修场地的长度应不小于炉管长度加2m。
加热炉外壁与检修道路边缘的间距不应小于3m。
3.3塔的布置:
(1)塔的布置要求:
塔与进料加热器、非明火加热的重沸器、塔顶冷凝冷却器、回流罐和塔底抽出泵等宜按工艺流程顺序,在不违反“防火规范”的条件下尽可能靠近布置,便于操作管理。
应在塔和管廊之间布置管道,在背向管廊的一侧设置检修通道或场地。
塔的人孔、手孔应朝向检修区一侧。
塔和管廊立柱之间没有布置泵时,塔外壁与管廊立柱之间的距离一般为3到5m,不宜小于3m。
(2)塔和管廊立柱之间布置泵时,泵的基础与塔外壁的间距应按泵的操作、检修和配管要求确定,一般不宜小于2.5 m。
(3)两塔之间净距不宜小于2.5 m,以便敷设管道和设置平台。
3.4管廊的布置:
(1)管廊的长度:
由设备的平面布置决定。
设备的数量和尺寸是其主要影响因素。
(2)管廊的高度:
横穿道路时≥4.5m;下方布置泵时≥3.5m;下方布置换热器时,适当增加标高,可为5.5m。
(3)管廊的宽度:
由管子数和管径决定,并加一定余量,一般≤9m,特殊情况≤12m。
管廊的管道布置原则:
大直径管道应靠近管廊柱子布置;小直径、气体管道、公用工程管道布置在管廊中间;工艺管道宜布置在与管廊相连接的设备一侧;工艺管道视其两端所连接的设备管口标高可以布置在上层或下层;需设置“Ⅱ”型补偿器的高温管道,应布置在靠近柱子处,且‘Ⅱ”型补偿器宜集中设置;低温介质管道和液化烃管道,不应靠近热管道布置;也不要布置在热管道的正上方;对于双层管廊,气体管道、热管道、公用工程管道、泄压总管、火炬干管、仪表和电气电缆糟架等宜布置在上层;一般工艺管道、腐蚀性介质管道、低温管道等直布置在下层;管廊上管道设计时,应留10%-20%裕量。
三、原料和产品储存单元说布局及说明
1.氮肥原料
1.1氮肥原料种类
1.1.1铵态氮肥
铵态氮肥包括碳酸氢铵(NH4HCO3)、硫酸铵{(NH4)2SO4}、氯化铵(NH4Cl)、氨水(NH3.H2O)、液氨(NH3)等。
铵态氮肥的共同特性:
1、铵态氮肥易被土壤胶体吸附,部分进入粘土矿物晶层。
2、铵态氮易氧化变成硝酸盐。
3、在碱性环境中氨易挥发损失。
4、高浓度铵态氮对作物容易产生毒害。
5、作物吸收过量铵态氮对钙、镁、钾的吸收有一定的抑制作用。
1.1.2硝态氮肥
硝态氮肥包括硝酸钠(NaNO3)、硝酸钙{Ca(NO3)2}、硝酸铵(NH4NO3)等。
硝态氮的共同特性:
1、易溶于水,在土壤中移动较快。
2、NO3—吸收为主吸收,作物容易吸收硝酸盐。
3、硝酸盐肥料对作物吸收钙、镁、钾等养分无抑制作用。
4、硝酸盐是带负电荷的阴离子,不能被土壤胶体所吸附。
5、硝酸盐容易通过反硝化作用还原成气体状态(NO、N2O、N2),从土壤中逸失。
1.1.3铵态硝态氮肥
铵态硝态氮肥包括硝酸铵、硝酸铵钙、硫硝酸铵。
1.1.4酰胺态氮肥
酰胺态氮肥——尿素{CO(NH2)2},含N46.7%,是固体氮中含氮最高的肥料。
1.2氮肥原料生产
天然气、煤炭、石油是生产化肥的三大原料,通常被称为气头、煤头、油头三类,由于石油和煤炭价格的升幅远大于天然气,故按成本优势排列为气头、煤头、油头。
我国现阶段生产合成氨的原料中煤占65%、天然气占28%、重油占7%。
合成氨生产所用的煤主要是无烟煤,只有少数几个企业采用德士古法、鲁奇法、恩德炉法和灰熔聚法生产合成氨,不用无烟煤。
现将用于生产合成氨的主要原料分述如下。
1.2.1煤和焦炭
截至2005年底,我国已探明无烟煤的储量达1130亿吨,占全国已探明煤炭储量的U%。
同年我国无烟煤产量为3.04亿吨,占全国煤炭产量的18%,其中用于化肥工业造气的无烟煤大约在4000万吨。
产地主要集中在山西晋城、宁夏石炭井、河南焦作、永城,其中晋城无烟煤质量最好。
合成氨生产采用的固定层常压气化炉对无烟煤的要求是:
固定碳(于基)≥70%;灰分(干基)<20%;挥发分(干基)<8%;含硫(干基)1250。
C;机械强度>70%;粒度25~75ram。
此外为解决无烟煤来源不足或节约成本,有些企业还利用无烟煤粉制成块状(煤饼、煤棒)来代替无烟块煤。
用鲁奇法气化时,也可使用粒度较小(2~4mm)、机械强度和热稳定性较差的煤。
德士古水煤浆气化和壳牌干煤粉气化使用煤种比较广泛。
1.2.2天然气
目前中国探明天然气可采资源量为14万亿立方米左右,截至2003年底,我国天然气探明地质储量3.86万亿立方米,天然气探明可采储量2.47万亿立方米(不含油田溶解气可采储量3807亿立方米),目前我国天然气探明程度为17.6%。
全国有5个天然气富集区,主要分布在东部地区的渤海湾和松辽平原;陕甘宁地区的中部、中东部;川渝地区的东部、中部、西北部;青海的冷湖、南八仙、涩北;新疆自治区的塔里木、吐哈。
天然气可分为“干气”和“湿气”。
“干气”所含成分几乎全是甲烷,纯度较高,乙烷以上的烷烃气较少。
“湿气”则含有10%左右乙烷以上烷烃的混合气,中国“湿气”多为油田伴生气。
据统计,世界上天然气主要用作民用燃料和发电,化工利用的比例较低,仅占天然气消费量的10%~12%,而且主要用于合成氨和甲醇的生产。
天然气是清洁能源,热值高、易燃烧、污染少,是优质的民用和工业燃料,也是生产合成气的理想原料。
1.2.3重油
用于生产合成氨原料气的燃料油通常为重油和渣油。
炼油厂常压蒸馏所得馏出点在350℃以上的塔底产品称为重油,重油再经减压蒸馏所得的520℃以上的馏分称为渣油。
习惯上把各种深度加工方法所得到的重质油通称为重油。
重油是由碳、氢、氧、氮、硫及灰分组成,~般含氢10%~13%,碳85%~88%,氧和氮都不超过1%,硫0.1%~1.5%,构成灰分的有钠、镁、钒、镍、铁和硅等元素,总量不超过0.3%。
制合成氨原料气的主要成分是碳和氢,它们的比例用C/H表示,C/H较低的油密度小,热值较高。
热值较高的油耗氧少,而得到的有效气较多。
重油中氧和氮元素大部分以中型胶质或沥青质化合物存在,这些物质在重油预热时易析出碳,以致沉淀并堵塞滤网和较细的管道。
重油中的硫、硫化物、硫醚、噻酚等化合物是合成氨生产中的有害物质,必须清除。
1.3氮肥原料处理
整个生产过程可以分为造气、脱硫、压缩、变换、脱碳、合成、甲醇、尿素等主要单元(工段)。
上述各单元(工段)的操作在工艺上密切联系,但在地域上分散、在控制上相对独立。
1.3.1造气
造气一般是以块煤为原料,采用间歇式固定层常压气化法,在高温和程控机油传动控制下,交替与空气和过热蒸汽反应。
反应方程式:
吹风C+O2→CO2+Q
CO2+C→2CO-Q
上、下吹C+H2O(g)→CO+H2-Q
A、吹风阶段
吹风阶段的主要作用是产生热量,提高燃料温度。
B、上吹(加氮)阶段
上吹阶段的主要作用是置换炉底空气,吸收热量、制造半水煤气,同时加入部分氮气。
C、下吹阶段
下吹阶段作用是制取半水煤气,吸收热量,使上吹后上移的气化层下移。
D、二上吹阶段
二上吹的主要作用是将炉底及进风管道中煤气吹净并回收,确保生产安全。
E、吹净阶段
吹净的主要作用是回收造气炉上层空间的煤气及补充适量的氮气,以满足合成氨生产对氮氢比的要求。
1.3.2变换
工艺简介
经过压缩有一定压力的半水煤气先经过油水分离器,除去煤气中的油物。
然后进入饱和塔的下部与热水进行交换后升至一定温度,经过气水分离器分离出煤气中的水份。
去除水分的煤气进入预热交换器,与中变炉出口的高温煤气进行两次热交换后,进入中变炉,在触媒的催化作用下,煤气中的一氧化碳发生反应,生成二氧化碳,中变炉的炉体内有三层反应区,在正常的工艺状况下,第一层的反应温度控制在450℃左右,第二层反应温度控制在400℃左右,第三层的反应温度控制在380℃左右。
反应后出中变炉的变换气进入与入口水煤气进行热交换的两级热交换器后,再进入低变炉使变换气中的一氧化碳进一步变换,经过两次变换的水煤气成为合格的变换气后,经热水塔,冷却塔之后送入下一工段进行后续处理。
1.3.3脱碳
工艺简介
含有一定浓度(CO2)的变换气进入吸收塔内。
气体中CO2被逆流流下的碳酸丙烯酯所吸收。
净化CO2气脱至所要求的浓度由塔顶排出,成为可供用户使用的工艺气。
吸收CO2后的碳酸丙烯酯富液经涡轮机回收能量后,在高压闪蒸槽内闪蒸。
高压闪蒸液再到减压槽进行减压闪蒸。
减压闪蒸汽相含浓度较高的CO2,可供用户使用。
减压闪蒸液在气提塔内经空气气提再生,再生后的碳酸丙烯酯贫液经循环液泵送回吸收塔循环使用。
气提空气由通风机从气提塔塔底送入。
高压闪蒸汽中含CO2及部分工艺气。
高压闪蒸汽可全部或部分返回压缩与原料气汇合,以回收氮气和氢气。
脱碳过程中,入脱碳塔贫液的流量,将直接影响二氧化碳在脱碳塔中的溶解度。
流量过小,原料气中的CO2不能被充分吸收;流量过大,能耗增加。
闪蒸槽的液位和压力,对于原料气的回收再利用有重要作用,它不仅可以回收闪蒸汽里的氮气和氢气,还可以减少碳酸丙烯酯的损失。
脱碳后煤气送入下一个工段进行进一步处理。
1.3.4合成
工艺简介
目前国内大多数中小氮肥企业均采用中压法氨合成工艺,其合成压力为31.4MPa。
合成塔的直径一般为Ф800~Ф1200mm。
将压缩送来的合格精炼气在适当的温度、压力和触媒存在的条件下合成为氨,所得气氨经冷却水及液氨冷却,冷凝为液氨,并将液氨从氢氮气中分离出来,未合成的氢氮气补充部分新鲜气继续在合成系统内循环合成。
1.3.5甲醇
工艺简介
甲醇是重要的有机化工原料,又是优良的能源载体。
近代工业甲醇生产主要以天然气、煤