粘土湿型砂及其控制管理要点.docx
《粘土湿型砂及其控制管理要点.docx》由会员分享,可在线阅读,更多相关《粘土湿型砂及其控制管理要点.docx(30页珍藏版)》请在冰豆网上搜索。
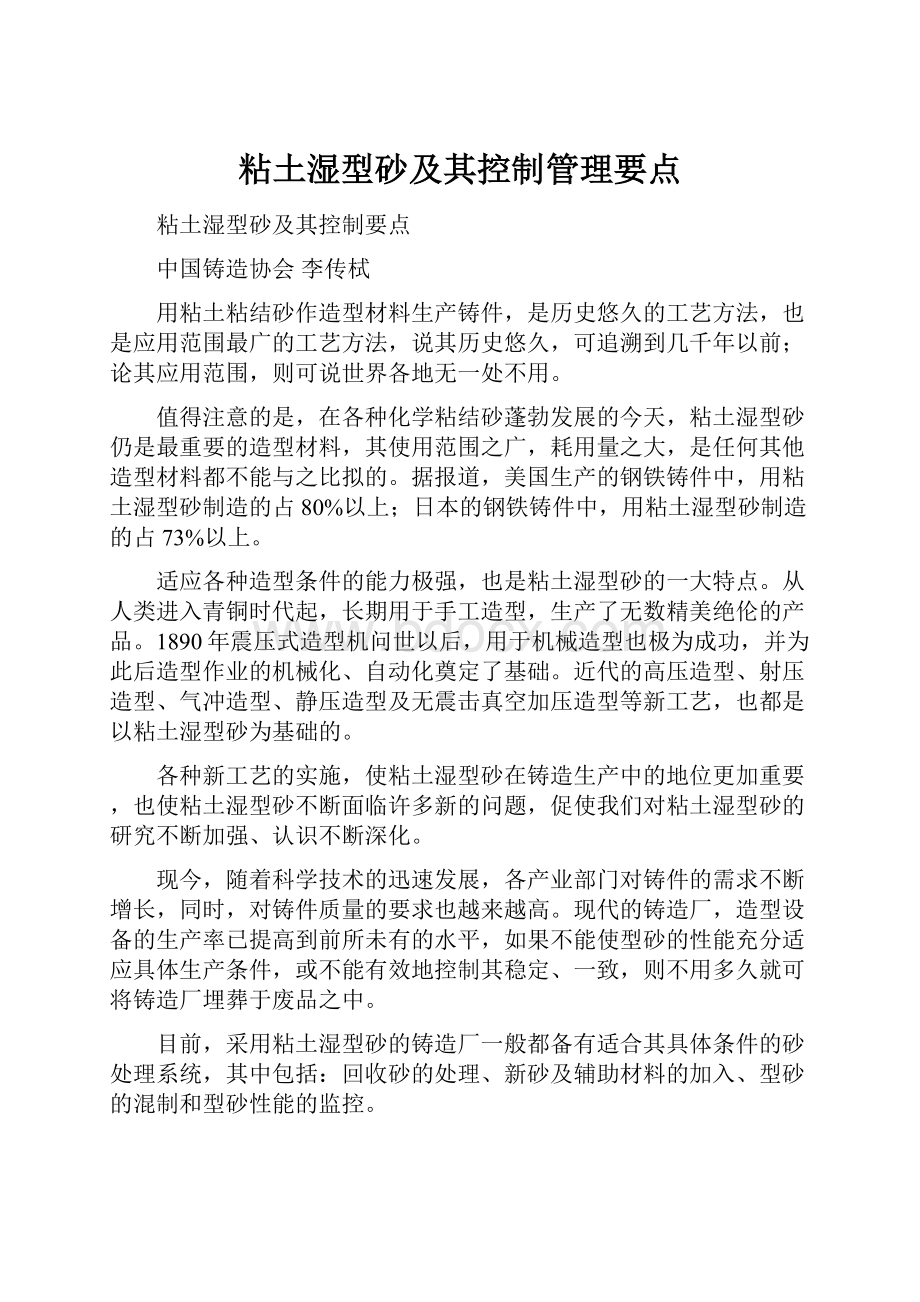
粘土湿型砂及其控制管理要点
粘土湿型砂及其控制要点
中国铸造协会李传栻
用粘土粘结砂作造型材料生产铸件,是历史悠久的工艺方法,也是应用范围最广的工艺方法,说其历史悠久,可追溯到几千年以前;论其应用范围,则可说世界各地无一处不用。
值得注意的是,在各种化学粘结砂蓬勃发展的今天,粘土湿型砂仍是最重要的造型材料,其使用范围之广,耗用量之大,是任何其他造型材料都不能与之比拟的。
据报道,美国生产的钢铁铸件中,用粘土湿型砂制造的占80%以上;日本的钢铁铸件中,用粘土湿型砂制造的占73%以上。
适应各种造型条件的能力极强,也是粘土湿型砂的一大特点。
从人类进入青铜时代起,长期用于手工造型,生产了无数精美绝伦的产品。
1890年震压式造型机问世以后,用于机械造型也极为成功,并为此后造型作业的机械化、自动化奠定了基础。
近代的高压造型、射压造型、气冲造型、静压造型及无震击真空加压造型等新工艺,也都是以粘土湿型砂为基础的。
各种新工艺的实施,使粘土湿型砂在铸造生产中的地位更加重要,也使粘土湿型砂不断面临许多新的问题,促使我们对粘土湿型砂的研究不断加强、认识不断深化。
现今,随着科学技术的迅速发展,各产业部门对铸件的需求不断增长,同时,对铸件质量的要求也越来越高。
现代的铸造厂,造型设备的生产率已提高到前所未有的水平,如果不能使型砂的性能充分适应具体生产条件,或不能有效地控制其稳定、一致,则不用多久就可将铸造厂埋葬于废品之中。
目前,采用粘土湿型砂的铸造厂一般都备有适合其具体条件的砂处理系统,其中包括:
回收砂的处理、新砂及辅助材料的加入、型砂的混制和型砂性能的监控。
粘土湿砂系统中,有许多不断改变的因素。
如某一种或几种关键性能不能保持在控制范围之内,生产中就可能出现问题。
由于各铸造厂砂处理系统的安排不同,选用的设备也不一样,要想拟定一套通用的控制办法是做不到的。
这里,将扼要谈到粘土湿型砂的特性及一些目前已被广泛认同的控制要点。
在理解这些要点基础上,可根据企业自己的具体条件确定可行的控制办法。
而且,还要随着技术的进步和工厂实际能力(包括人员和资金)的增强,不断改进型砂系统。
一、粘土湿型砂的特性
通常都说粘土湿型砂的粘结剂是粘土,实际上这种提法是不太确切的,单用粘土,不能粘结砂粒、使型砂具有强度,粘土湿型砂中的粘结剂是粘土和水按一定比例配合组成的,水是粘结剂中的重要组成部分,只不过水太平常了,所以往往未得到足够的重视。
1、土-水比
如果按活性粘土和水各自在型砂中所占的份额,将活性粘土和水按比例单独混合,得到的是粘稠的膏状体,类似于为制作饺子所和的面团。
按土质学方面对粘土-水系统的稠度划分原则,粘土湿型砂中的土-水混合物属于“半固态”范围,实际上型砂中将砂粒粘结起来是这种膏状体,我们将其称之为“粘土膏”。
目前,粘土湿型砂中所用的粘土都是膨润土,水和膨润土混成的粘土膏,大体上是在土-水比为3:
1左右时强度最高。
采用高压造型工艺时,为得到高强度的铸型,型砂中所含的活性膨润土和水分的质量分数之比,大体都在3:
1左右。
在这种条件下,型砂的可紧实性也最适合高压造型的要求(约在35~45之间)。
粘土膏的水分增多,其粘度随之降低,强度也相应下降。
采用震压式造型机造型时,使型砂流动并将其紧实所需的能量比高压造型小得多,型砂的强度就应该低一些。
因为型砂的强度越高,其抵抗变形的能力越强,造型设备提供的能量不足,就难以使铸型具有必要的紧实程度。
为适合这种条件,型砂中的土-水比就应该高一些,一般以控制在3:
2左右为合适。
2、粘土湿型砂的砂粒结构
砂粒之间的粘结,是靠粘土膏实现的。
理想的情况是:
水和粘土混合得很好,成为均匀的粘土膏,粘土膏又均匀地涂布在每一砂粒的表面上,砂粒之间由其表面的粘土膏彼此相连而形成的粘结桥粘结起来,如图1所示,其间的空隙可使型砂具有必要的透气性。
图1粘土湿型砂理想的砂粒结构
要将粘土和水混成均匀的膏体是很不容易的。
泥塑艺术家和制陶器的技师混制膏体时,要先将其混匀,再放置一段时间使之熟化,然后还要揉搓、摔打。
粘土湿型砂中的粘土膏,质量要求当然没有这样严格,但要使膨润土充分吸水、调混均匀并均匀涂布在每个砂粒表面上也是非常困难的。
在生产条件下,混砂的时间是非常有限的,不仅不可能使粘土和水调配均匀,其在砂粒表面的涂布状态也与图1所示的也相距甚远。
完全用新砂配制粘土湿型砂,混成砂的实际砂粒结构示意图见图2。
反复使用的系统砂,涂土膏在砂粒表面分布的情况要好一些。
图2用新砂配制的粘土湿型砂砂粒结构示意图
3、粘土湿型砂的混砂效率
有鉴于在生产条件下粘土湿型砂中的粘土和水不可能充分混合,美国的C.E.Wenniger提出了“混砂效率”的概念。
粘土湿型砂的混砂效率是指:
型砂中实际上起粘结作用的膨润土量与其中的活性膨润土含量之比,即
这里有两个术语需要特别说明一下:
“活性膨润土”是型砂中所含的具备活性、能吸水膨胀而起粘结作用的膨润土,也就是可以用吸蓝法测定其含量的膨润土。
活性膨润土(activeclay),曾有人将其译为“有效膨润土”,而且在全国广为采用,这是很不妥当的。
因为活性膨润土是能起粘结作用的,是具有活性的,但在型砂中不可能全部都起作用,并不是都是“有效的”,而且也不希望其全部都起作用。
“有效膨润土”(effectiveclay)则是在型砂中发生了有效粘结作用而使型砂具有强度的膨润土。
由于粘土膏属半固态性质,粘度很高,难以混匀,用于混制粘土湿型砂的混砂机,所需的功率比供砂能力相同的树脂砂混砂机大得多,混砂所需的时间也更长。
即使如此,型砂中的粘土和水仍不能充分混匀,用当前高水平的混砂设备,混砂效率也不过是60~70%。
另一方面,从要求型砂适于造型的可紧实性看来,也不应该让所有的活性粘土都充分吸水并混合均匀。
例如,高压造型一般要求型砂的可紧实性数值为35~45,在这种条件下,混砂效率大约仅略高于60%。
如果充分加水,并加以长时间的混制,使混砂效率提高到80%以上,型砂的可紧实性就会远高于60,根本就不能使用,更不用说让型砂中的活性粘土全部都起作用了。
还要特别指出的是:
如果型砂中的活性粘土全部都起作用,都充分吸水了,造好的砂型浇注时,金属/砂型界面处的水向内部迁移,形成水分凝聚层时,由于此处粘土已经充分吸水,不能再吸收水分,水分凝聚层的强度将会非常之低,铸件上就极易于产生膨胀缺陷。
所以,从这方面看来,追求过高的混砂效率也是不可取的,一切事物都是有两面性的。
在正常的混砂条件下,粘土湿型砂的强度决定于其中粘土膏的多少和粘土膏的粘度,所以,强度、活性膨润土含量和水分之间是有相依关系的。
此外,在型砂强度一定的条件下,其可紧实性越高,则其中有效膨润土的含量也越高,三者之间也有相依关系。
在这种认识的基础上,由众多的实验数据,得到了图3所示的线图。
利用图3,可由型砂的湿抗压强度和水分的测定值,得知其中的活性膨润土含量。
但是,活性膨润土含量必须以吸蓝法的测定值为依据,由图3查得的值应经常与之对比,作为日常测定性能时的参考。
同样也可以根据湿抗压强度和可紧实性的测定值,查出型砂中有效膨润土含量,并由此计算出型砂的混砂效率。
图3粘土湿型砂一些主要性能参数之间的关系
例如,某铸造厂粘土湿型砂的湿抗压强度为178kPa,可紧实性为42%,水分为3.5%。
从纵坐标上湿抗压强度为178kPa一点画水平直线,由此直线上水分为3.5的一点,可知型砂中的活性膨润土含量约为7.5%。
再由此水平直线与代表可紧实性的一组斜线的交点,即可求得型砂的有效膨润土含量为4.4%。
随着高压造型技术和各种造型设备的发展,粘土湿型砂砂处理工艺和设备也在不断改善。
由于回收砂的性状对型砂质量的影响很大,很多技术开发的着眼点都在于改善回收砂的处理,主要几点是:
·落砂以后,尽可能早地给回收砂加水,使已干燥的膨润土有时间充分吸水;
·加强回收砂的冷却,使其中的水分稳定;
·增加预混工序,使水和粘土混配更为均匀。
4、造型性能
前面已经提到,粘土湿型砂的一大特点就是能适应各种造型条件,但是,也应同时看到,由于起粘结作用的粘土膏的粘度很高,造型时未经紧实的型砂就具有相当高的强度,流动性很差,因而,造型性能不好,紧实铸型所需的能量很大,造型机的功率一般都相当高,如欲制得高紧实度铸型,造型设备不得不庞大而笨重。
在改善粘土湿型砂造型方面的一项重要发展,就是在向砂箱中填砂之前,先用气流将型砂流态化,使其流动性大幅度改善。
日本新东公司采用此项技术后,使造型机的尺寸缩小,设备重量大幅度减轻,造型的能耗较用传统机型平均减少60%。
不难设想,在改善型砂造型性能方面仍有宽广的发展空间。
二、粘土湿型砂的组成
一般认为,粘土湿型砂是由原砂、膨润土、其他附加材料(如煤粉、淀粉之类)和水组成的。
对于完全用新砂配制的型砂,情况是这样的。
但是,在生产条件下,完全用新砂配制粘土湿型砂的情况是极为罕见的,粘土湿型砂的重要特点之一就是可反复使用。
型砂经造型、浇注、冷却、落砂、磁选、筛分、冷却等复杂的工艺过程之后,再由混砂机混制。
每一铸造厂,型砂都在其特定的系统中循环使用。
混砂时补加新砂、膨润土、附加物和水,是为了弥补工艺过程中的损耗,以保持系统中的砂量不变。
在反复使用的条件下,由于型砂经受多次机械作用和热作用,不仅有部分膨润土变成死粘土、部分煤粉焦化,砂粒的结构也会发生重大的变化。
因此,铸造厂现场使用的粘土湿型砂一般都不是简单的混合物,其组成是相当复杂的。
不同的铸造厂,即使用相同的原材料、相同的型砂配比,其型砂的实际组成却可能很不相同,铸件质量也因而会有很大的差别。
1、型砂在使用过程中的变化
铸型浇注以后,各处型砂受热的条件不同,砂粒表面的状况也会有很大的差别。
靠近铸件的砂粒受高温的作用,表面上由粘土膏形成的粘结膜会完全脱水而成为死粘土,而且还会与其他附加物残留的灰分、附近因受热作用而破碎的砂粒、铸件表面上被氧化而生成的FeO等多种物质烧结在一起,其性质完全不同于浇注前的状态,所以称之为“变质烧结层”。
在以后的砂处理过程中,这些砂粒上的变质烧结层受到各种机械作用,一部分会磨掉,一部分会脱落,但总有相当的一部分与砂粒表面烧结得比较牢固而残留下来。
当然,这样的砂粒量不很多,而且会分散到其他未受热影响的砂粒之中。
离铸件较远的砂粒受影响不大。
煤粉不会焦化,其他附加物不会被烧蚀,只是粘土膏中的水会部分蒸发,这部分型砂经冷却、加水后可以恢复原先的状态,但脱水的粘土膏吸水恢复状态需相当长的时间,不是一加水马上就能实现的。
处于上述两种条件之间的型砂,砂粒表面的粘土膏脱水程度较高,还会有部分膨润土因脱除了结晶水而成为死粘土,也会有少量煤粉因脱除挥发分而焦化。
其中的死粘土当然不能再具有粘结能力,仍具备活性的粘土因脱水程度高,吸水恢复粘结能力也更为困难。
以循环使用的系统砂为基础,补加煤粉和其他附加物,按常规的砂处理系统的作业程序混砂,砂粒表面会有变质烧结层,变质烧结层外面是粘土膏,粘土膏在砂粒表面上涂布的情况比全部用新砂配制的均匀一些。
补加的煤粉和其他附加物大部分都进入粘土膏中,但由于混砂时间太短,也仍然有少量游离存在,有代表性的砂粒结构如图4所示。
图4常规粘土湿型砂砂粒结构示意图
变质烧结层是型砂中的易熔组分,大约在1100℃左右即可开始烧结,是由含铁、铝的复合硅酸盐和灰分、硅砂碎屑等构成的。
厚度适当的变质烧结层能改善砂粒的形貌,且能减轻因硅砂相变膨胀而造成的铸件缺陷,是有益的。
在正常的情况下,以旧砂为主配制的型砂,性能及使用效果都优于全用新砂配制的型砂。
但是,如变质烧结层太厚,就会导致铸件表面粗糙或粘砂。
2、粘土湿型砂的组成
为了在生产条件下控制型砂的组成,F.Hofmann1970年提出了“型砂组成控制纲要”(silicaprogram)。
1975年前后,欧洲和美国就有500家以上的铸造厂据以检查型砂的组成。
现在,该技术已逐步完善,在美国、欧洲和日本都颇受重视。
按“型砂组成控制纲要”,粘土湿型砂中,除水分以外,主要有以下5种组分。
(1)活性粘土
型砂中能吸水膨胀而起粘结作用的膨润土,可用吸蓝法测定其含量。
(2)含碳材料
含碳材料(如煤粉、重油、沥青、聚丙烯、聚乙烯、聚苯乙烯等)是铸铁型砂中的重要组分。
铸钢用的型砂,虽不加煤粉,但也需加入谷物粉或淀粉之类,这些也都是含碳材料。
(3)易熔组分
易熔组分包括砂粒表面上的变质烧结层和粒度小于0.053mm的细粉(270目以下)。
型砂中,上述细粉的来源如下:
·膨润土在高温下(600"C以上)失去结晶水而成的死粘土:
·金属铸型界面上形成的FeO、MnO和硅砂反应生成的硅酸盐细粉:
·硅砂在563℃相变膨胀时碎裂形成的细粉;
·硅砂因机械作用破碎形成的细粉;
·硅砂中所含的长石及其他杂质形成的细粉。
(4)金属细粒
(5)砂粒
在上述5组分的基础上,规定了一项评估型砂质量的指标,即型砂的洁净因素,其定义如下:
3、生产中所用型砂的实际组成及其与铸件质量的关系
美国一些铸造厂所用的粘土湿型砂的组成及简要说明见表1。
表1美国一些铸造厂所用的粘土湿型砂及相关的铸件质量情况
铸造厂编号
型砂类别
型砂中各组分的含量(%)
型砂的洁净因素(%)
铸件质量情况
活性粘土
含碳材料
易熔组分
金属细粒
砂粒
1
灰铸铁件型砂
4.4
4.6
4.8
1.5
84.7
93.1
良好
2
灰铸铁件型砂
4.0
3.5
3.4
4.2
84.9
91.8
良好
3
灰铸铁件型砂
5.4
3.6
11.8
1.0
78.2
85.9
良好
4
灰铸铁件型砂
8.0
8.4
13.2
0.4
70.0
83
尚好(铸件较小)
5
灰铸铁件型砂
6.8
3.2
13.6
1.6
74.8
83.11
尚好
6
灰铸铁件型砂
8.5
9.7
9.8
2.0
70.0
85.5
尚好
7
灰铸铁件型砂
7.9
7.9
14.2
2.0
68.0
80.7
铸件表面粗糙
8
灰铸铁件型砂
11.0
10.9
21.0
4.2
52.9
67.7
表面粘砂
9
灰铸铁件型砂
9.4
10.2
31.0
2.2
47.2
58.7
表面粘砂严重
10
有色合金件型砂
6.4
1.7
9.9
4.8
77.2
84.0
良好
11
铸钢件面砂
5.5
1.6
2.3
1.0
89.6
96.4
良好
日本一些铸造厂所用的粘土湿型砂的组成见表2,其铸件产品质量的情况未见报道。
表2日本一些铸造厂所用的粘土湿型砂的组成
铸造厂及型砂
型砂中各组分的含量(%)
型砂的洁净因素(%)
活性粘土
含碳材料
易熔组分
金属细粒
砂粒
A厂,1号铸铁型砂
2号铸铁型砂
3号铸铁型砂
8.4
5.2
15.3
1.0
70.3
81.2
10.2
4.1
9.9
1.0
74.8
87.3
10.1
3.9
12.9
1.4
71.7
83.0
B厂,铸铁型砂
10.9
3.3
22.0
63.8
74.3
C厂,铸铁型砂
8.3
5.3
41.8
1.8
38.6
46.9
D厂,铸钢型砂l
铸钢型砂2
铸钢型砂3
9.2
1.8
11.4
77.6
87.2
9.2
1.5
12.2
77.1
86.3
9.2
2.3
13.1
0.8
74.6
84.3
表1中,铸造厂8和9,型砂中砂粒含量分别为52.9%和47.2%,易熔组分的含量分别为21.0%和31.0%,铸件表面都有粘砂缺陷,铸造厂9则尤为严重。
铸造厂7所用型砂,砂粒含量68%,易熔组分14.2%,虽无粘砂缺陷,但铸件表面比较粗糙。
铸造厂4,型砂中易熔组分含量13.2%,砂粒含量也只有70%,由于该厂生产小型铸件,故铸件表面品质仍属较好。
目前,生产灰铸铁件、可锻铸铁件或球墨铸铁件的铸造厂,型砂中砂粒含量多在70%到85%之间;易熔组分含量多在5%到15%之间。
各工厂的具体控制目标,可在多次测定的基础上按具体情况确定。
型砂中含砂粒85%以上者,只适用于制造铸钢件。
对于制造铸铁件并不合适,尤不适于用机器造型。
用于制造铸铁件的型砂,以保持洁净因素在83~93%之间为好。
铸钢件用的型砂则应在90%以上。
4、粘土湿型砂各组分的测定方法
上述型砂中的5种组成,可用以下方法测定。
(1)活性膨润土含量
先取工厂所用的原砂和膨润土样品,于110℃烘干一小时后,以不同的配比配成试样,测定各试样的吸蓝量数值,然后绘制反映膨润土含量与吸蓝量之间的关系的标准曲线。
一般用6组试样,见表3。
表3绘制标准曲线所用的试样
试样1
试样2
试样3
试样4
试样5
试样6
膨润土量(g)
0.1
0.2
0.3
0.4
0.5
0.6
新砂量(g)
4.9
4.8
4.7
4.6
4.5
4.4
试样中膨润土含量
2%
4%
6%
8%
10%
12%
用蒸馏水制备两种试剂:
a.含1%焦磷酸钠的水溶液;(焦磷酸钠的规格为化学纯)
b.含0.2%亚甲基蓝的水溶液;(亚甲基蓝的规格为分析纯)
将试样置三角烧瓶中,加蒸馏水50ml,再加焦磷酸钠溶液20ml,摇匀后置垫有石棉网的电炉上加热,煮沸5min后取下,冷却到室温。
用亚甲基蓝溶液滴定:
向装有试样的三角烧瓶中,先加入亚甲基蓝溶液预期用量的2/3左右,摇匀,用玻璃棒站一滴点在滤纸上,如深色圆点之外未现蓝绿色晕环,则再加亚甲基蓝溶液1ml摇匀。
重复操作,直到滴在滤纸上的圆点边缘出现晕环。
记录耗用的溶液总量(ml),即吸蓝量。
所有的试样均按此测定吸蓝量,画出标准曲线。
测定型砂中活性膨润土含量时,取砂样置110℃下烘干1小时。
称砂样5.00g,按前述方法测定吸蓝量。
根据测定的吸蓝量,对照标准曲线,即可求出活性膨润土含量。
(2)含碳材料
先测定型砂的灼烧减量(LOI),再减去其中活性膨润土中的结晶水量,即是型砂中含碳材料的总量。
如果原砂的灼烧减量在1.0%以上,就应该在上述试验结果中再核减原砂的灼减量。
一般情况下,这一项可不考虑。
测定型砂的灼烧减量时,取砂样在110℃下烘干1小时。
然后,称砂样50g,放在由φ100的石英玻璃皿中,在980℃下保持1.5小时,冷却后称重,算出灼烧减量。
活性膨润土中的结晶水,大致可按每1%的活性膨润土为0.09%计。
例如,型砂中活性膨润土为8%时,应减去的晶格水量为0.09×8%,即0.72%
从测定的灼烧减量(%)中,减去0.72%,即是含碳材料的含量。
(3)金属细粒
测定金属细粒含量时,取经烘干的型砂样50g,按常规方法测定含泥量。
保留测含泥量剩下的砂样,烘干。
冷却后用270目筛分离细粉,筛分时间l0min。
分离细粉后的砂样,再在980℃烧1~1.5小时,以去除焦化成颗粒的煤粉。
剩下的砂样称重,记录。
然后用下述两方法之一测定金属细粒。
其一,将砂样分散平铺在光滑的纸上,用强磁铁自下方吸引,使其与砂样分离,分离后称重,即可求出金属细粒含量。
其二,将砂样置600ml的烧杯中,加蒸馏水100ml,再加浓盐酸100ml。
然后用表面皿盖上烧杯,在通风罩下加热,使烧杯内液体接近沸腾但不可沸腾,保持1.5~2小时。
略微冷却后,加水冲淡、清洗,但注意别冲走砂粒。
洗净后,烘干,称重,按酸煮前后的重量差,即可求出金属细粒含量。
(4)砂粒
分离金属细粒后的砂样中,只剩下砂粒和变质烧结层。
用磷酸洗去变质烧结层,就是砂粒。
从砂样中取出10.00g,装在烧杯中,加入200ml85%的磷酸,煮沸至少1小时,直到溶液颜色不再加深,有时需几小时。
变质烧结层完全溶蚀后,冷却15min,倒出大部分酸液,冷却到60℃后用热水稀释,加热水时应缓慢地顺烧杯壁加入,操作者应戴防护眼镜。
多次稀释并按测含泥量法吸出液体后,烘干砂样,称重。
按分离金属细粒后砂样重量,即可算出型砂中砂粒含量。
(5)易熔组分
从100%中减去以上四项的百分数,即是易熔组分含量的百分数。
三、浇注、落砂后回收砂的处理
用粘土湿砂造型工艺时,浇注以后,除粘在铸件上的少量型砂随铸件转移到清理工部脱除,不能循环使用外,大量的型砂都要回收,经处理后循环使用。
配制粘土湿型砂时,回收砂用量一般都在90%以上,如果对回收砂的处理不当,无论怎么样加强混砂,无论添加什么辅助材料,都不可能得到质量良好的型砂。
所以。
对回收砂进行有效的处理,是保证型砂质量的关键。
1、回收砂温度的控制
热砂问题,己被公认为是采用粘士湿型砂铸造工艺时必须面对的最大问题。
型砂温度太高,铸件容易产生夹砂、表面粗糙、冲砂、气孔等缺陷。
热砂对铸件质量的负面影响,主要由于以下几个方面:
◆由于热砂使水分蒸发,混砂时无论怎样注意,也难以控制型砂的性能;
◆将热型砂送往造型机的过程中,由于水分损失,型砂性能改变,
造型时实际上用的型砂,其性能与混砂时测定的有所不同;
◆造型时,热型砂的水分容易在模样表面上凝结,导致型砂粘模;
◆合型后,热砂的水分蒸发,凝结在冷的芯子上,会使芯子的强度降低,铸件也易于产生气孔;
◆如果回用砂要贮存在砂斗中备用,则热砂容易粘附在砂斗壁上。
严重时,砂斗四周堵满了型砂,只剩中间一个孔洞,使系统中的型砂只有一部分循环使用,型砂周转快、温度又会进一步提高,使热砂问题更加严重。
多高温度的砂算是热砂?
判断热砂的温度界限,是看其是否使混砂、造型及铸件质量方面出现问题。
对此,许多研究者从各方面进行了研究:
有人研究了型砂温度对其性能稳定性的影响;有人研究了温度对膨润土-水系统流变性的影响;有人研究了型砂温度与铸件质量的关系。
各方面的研究都得到了一致的结论,即:
为保证型砂的性能稳定,温度应保持在50℃以下。
使型砂冷却,最有效的办法是加水,但是,简单的加水,效果是很差的,一定要吹入大量空气使水分蒸发,才能有效地冷却。
因为水的蒸发热是其比热的540倍。
目前,回收砂冷却装置的品种、规格很多,主要有冷却滚筒、双盘冷却器和沸腾床等。
无论采用何种冷却装置,在回收砂进入冷却装置前先加足够量的水、然后充分鼓风使水分蒸发都是十分重要的。
2、增加回收砂与水分作用的时间
几乎所有的铸造厂都重视混成砂的水分,但是,对于严格控制回收砂水分的重要性,多数铸造厂都缺乏足够的认识。
实际上,如果不严格控制回收砂的水分,就不可能保持型砂的质量稳定。
加水润湿膨润土,其吸水膨胀需要很长的时间,向已经吸收了一部分水的膨润土进一步加水,吸水过程就容易得多,这一点已为许多研究试验所证实。
铸型浇注后,由于浇注金属的热影响,相当一部分砂粒表面上由粘土膏形成的粘结膜已脱水干燥,润湿这种脱水膨润土比润湿粉状膨润土更为困难,因为其表面面积减少了。
如果回收砂以这种状态进入混砂机混制,虽然水分的数值是符合要求了,但所加的水不能使膨润土充分膨胀,发挥更好的作用。
结果导致混砂效率降低,混成砂的质量不佳,而且很不稳定。
近年来,国外很多高水平的铸造厂,都将尽可能早地向落砂后的回收砂中加水作为改善型砂质量的重要措施。
采用较多的方式是:
回收砂送入冷却装置之前,先加入足够的水,使回收砂冷却之后的水分仅略低于混成砂的预期水分。
也有些铸造厂在落砂之后立即向回收砂中加水。
采取这样的措施,大幅度增加了回收砂中已脱水的膨润土与水作用的时间,使水-粘土系统能更好地发挥其粘结作用。
最后,在混砂过程中,只