电动的单梁起重机检修规程新.docx
《电动的单梁起重机检修规程新.docx》由会员分享,可在线阅读,更多相关《电动的单梁起重机检修规程新.docx(11页珍藏版)》请在冰豆网上搜索。
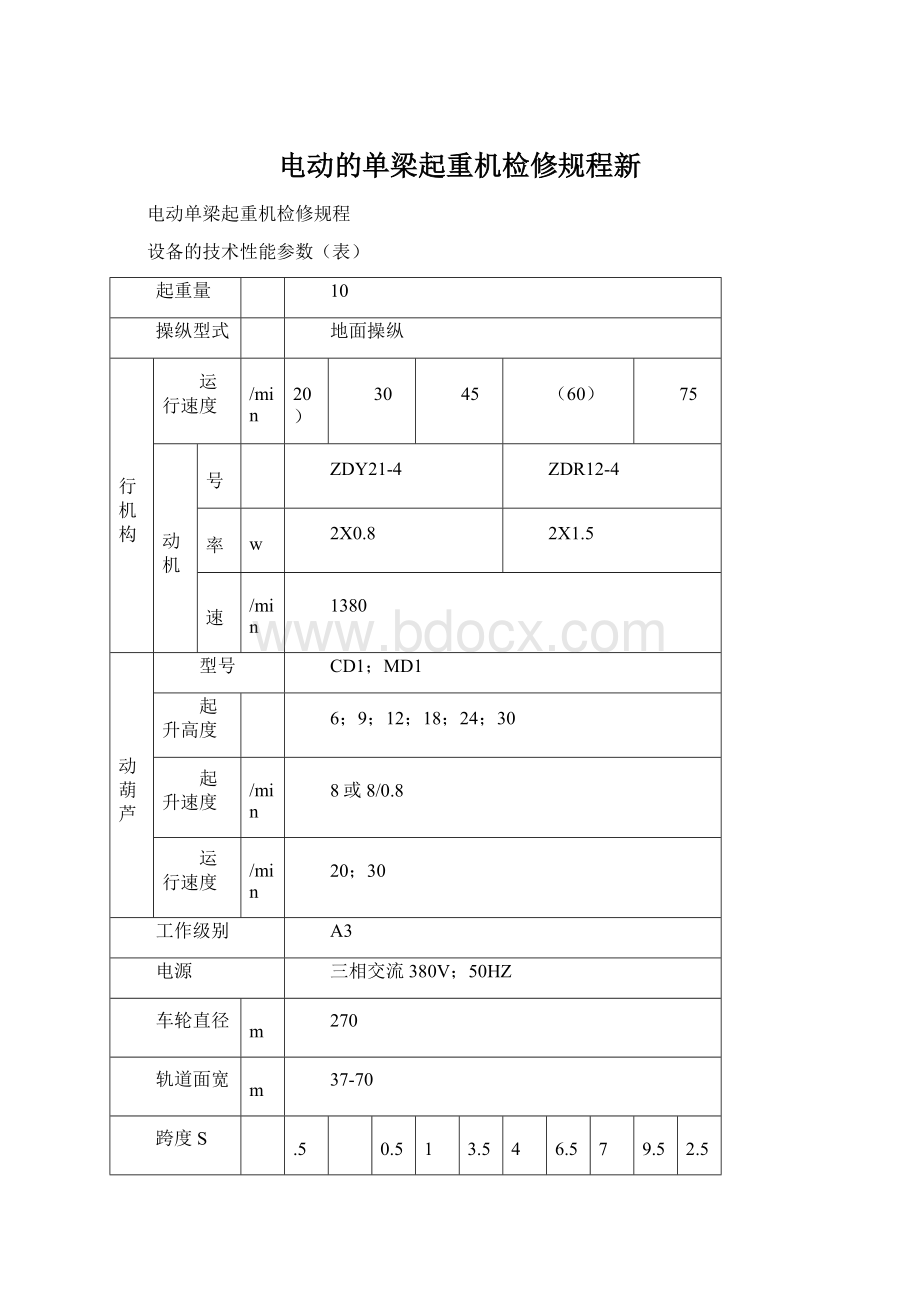
电动的单梁起重机检修规程新
电动单梁起重机检修规程
设备的技术性能参数(表)
起重量
t
10
操纵型式
地面操纵
运
行
机
构
运行速度
m/min
(20)
30
45
(60)
75
电
动
机
型号
ZDY21-4
ZDR12-4
功率
Kw
2X0.8
2X1.5
转速
r/min
1380
电
动
葫
芦
型号
CD1;MD1
起升高度
m
6;9;12;18;24;30
起升速度
m/min
8或8/0.8
运行速度
m/min
20;30
工作级别
A3
电源
三相交流380V;50HZ
车轮直径
mm
270
轨道面宽
mm
37-70
跨度S
m
7.5
8
10.5
11
13.5
14
16.5
17
19.5
22.5
最大轮压
KN
50.98
51.78
54.99
55.93
58.03
58.7
65.9
66.5
64.4
67.1
53.98
54.78
57.99
58.93
61.03
61.7
68.9
69.5
67.4
70.1
总重量
t
3.245
3.329
3.768
4.020
4.493
5.584
5.194
5.298
6.66
7.78
3.645
3.279
4.168
4.420
4.839
5.984
5.594
5.698
7.06
7.18
基
本
尺
寸
H1
mm
720
820
975
865
875
h1
900
1000
1200
1250
1250
h
1500
1600
1640
I1
1293
I2
1893
K
2000
2500
3000
B
2500
3000
3500
一、检修前的准备
1、工具的准备:
根据检修项目,应提前准备好相应的工具:
1.1起吊工具:
天车(吊车)、手动吊具、吊索、专用吊钩。
1.2电动工具:
手枪钻、钻床、砂轮机。
1.3焊具:
电焊机、氧气瓶、乙炔气瓶、气带、焊炬。
1.4电气检测工具:
万能表、摇表。
1.5手动工具:
大锤、撬棍、活动扳手、扭力扳手、梅花扳手(套)、内六角扳手(套)、螺丝刀(套)。
1.6专用工具:
拉拔器(套)。
1.7测量工具:
卷尺、卡尺、塞尺。
2、根据确定的检修项目,拟定设备修理和主要零部件修复工艺;制定检修方案或施工网络图表,落实检修力量和必要的施工工具。
3、使用单位根据下达的检修计划,在指定的时间内,在主管部门主持下与施工单位进行交接。
使用单位应向施工单位交清设备技术状况、主要缺陷和隐患、缺件情况等。
4、施工单位应尽量把需要更换符合质量要求的部件预装成套,并在施工前将备品配件、材料、工具等运到现场。
5、大、中修理时,施工单位向使用单位安全部门提交单项施工安全措施。
二、设备拆、装顺序及方法
2.1、划分装配单元,即从工艺角度出发,将设备分解成可以独立拆装的组件及各级分组件。
2.2、根据先上后下、先外后内、先易后难、先一般后精密、先轻后重大的原则拆卸设备。
2.3、装配设备时,先选取装配基准件,基准件首先进入装配,然后根据具体情况,按照先下后上、先内后外、先难后易、先精密后一般、先重大后轻的原则确定装配顺序。
2.4、装配方法:
互换法、选配法、修配法、调节法。
三、检修工艺及其技术要求
3.1、拆卸工艺
3.1.1、清扫、洗涮。
3.1.2、外观检查。
3.1.3、拆成部件、机组。
3.1.4、拆零。
3.1.5、零、部件清洗。
3.1.6、零、部件检验。
3.1.7、零、部件按“可使用”、“可修复”和“报废”分类,并分别存放。
3.1.8、零、部件修配、入库。
3.2、组装工艺
3.2.1、零、部件运至施工现场。
3.2.2、零、部件清洗。
3.2.3、零、部件及机组检查。
3.2.4、零件组装。
3.2.5、部件机组安装。
3.2.6、调整机组安装。
3.2.7、试车。
3.2.8、设备防腐。
3.3、总拆卸时,按设备拆装顺序及方法的拆顺序进行。
3.4、总装配时,按设备拆装顺序及方法的拆顺序的反向进行
3.5、检修周期及工期见下表
项目
周期
工期
小修
1~3个月
8~16小时
中修
18个月
8~10天
大修
根据技术监督局测定结果(处理大梁下挠)
1O~15天
3.5.1、小修内容:
3.5.1.1、检查更换钢丝绳。
3.5.1.2、更换磨损严重的销轴、螺栓。
3.5.1.3、检查电气系统及拖线电缆。
3.5.1.4、减速机油位检查、加注,漏油处理。
3.5.1.5、更换损坏的吊钩护罩、滑轮。
3.5.1.6、更换缓冲器弹簧。
3.5.1.7、配齐缺损的小零件。
3.5.1.8、调整偏差,消除隐患。
4.5.1.9、焊接修理安全防护装置。
3.5.1.l0、处理松动的轴、套,调整配合并加注润滑油脂。
3.5.1.11、检查确认集中润滑泵工作正常,润滑点无漏油、管路无堵塞
3.5.1.12、调整更换极限、调整变幅摇架的上压轮、下托轮与齿条间隙。
3.5.1.13、检查齿接手磨损情况,更换达到报废标准的零件。
3.5.1.14、各齿接收、车轮、铰链点、滑轮等部位润滑检查并承注润滑油。
3.5.1.15、检查更换电机碳刷、变频器及制动单元接线紧固、限位检查测试。
3.5.1.16、检查紧固电阻箱、控制器接线螺丝。
3.5.1.17、小车拖缆整理,电气线路检查处理。
3.5.1.18、处理日常点巡检中发现的问题。
3.5.2、中修内容:
3.5.2.l、电机抽芯清扫,检查绝缘,轴承清洗、检查换油。
3.5.2.2、传动机组清洗检查、调整、找正,使之达到技术标准。
3.5.2.3、减速机清洗换油,更换磨损严重的齿、轴、轴承。
3.5.2.4、卷筒钢绳更换、卷筒表面清洗探伤检查有无裂痕及其它缺陷,轴承清洗、检查、更换。
3.5.2.5、车轮组解体,轴承清洗、检查、更换。
3.5.2.6、吊钩组及定滑轮轴承清洗、检查、更换。
3.5.2.7、检查更换集中润滑泵,润滑管路局部更换;液压闸润滑油更换。
3.5.2.8、检查端梁螺栓紧固情况。
3.5.2.9、检查更换控制器、电气线路及卷筒电缆。
3.5.2.10、检查更换保护柜、主控屏、电阻箱、控制箱内损坏的元件。
3.5.2.11、检查更换集电器、输电导管、小车拖缆及滑线架等。
3.5.2.12、调整更换大车行走供电滑线。
3.5.2.13、检查金属结构的焊缝,铆接情况,发现裂纹应进行修焊。
3.5.2.14、大、小车轨道检查、调整或更换
3.5.2.15、除锈刷漆。
3.5.2.16、进行全面检查,完成全部小修内容。
3.5.3、大修内容:
3.5.3.l、完成全部中修内容。
3.5.3.2、测量起重机的上拱度,验证主梁是否超过规定变形。
3.5.3.3、测量处理主粱旁弯度。
3.5.3.4、检查处理主梁和端梁连接焊缝。
3.5.3.5、检查对角线,矫验车架平行度。
3.5.3.6、卷筒、吊钩、横梁、轮板、定、动滑轮轴进行探伤检验。
3.5.3.7、更换达到更换标准的成套件,如:
减速机、吊钩组、滑轮组、车轮组、卷筒等。
3.5.3.8、更换磨电道、输电导管。
3.5.3.9、测定大车轨道接地装置的电阻值。
3.5.3.10、进行全面性能试验(静、动负荷试车)。
四、检修技术标准
4.1、20NAT6*19W+FC-1770钢丝绳
4.1.1、凡钢丝绳磨损量达原直径l5%应予更新,要求无整股断裂,无明显的内部腐蚀。
4.1.2、钢丝绳在一个节距中断丝数<7根,钢丝绳在一个节距中有下表情况者,应报废更新:
钢丝绳种类(安全系数在6以下)
6×19+1
6×37+1
6×61+1
逆捻
顺捻
逆捻
顺捻
逆捻
顺捻
钢丝绳断丝数
12
6
22
11
36
18
若是用于吊运烧红的金属,或易燃易爆物品的钢丝绳,应按上述规定断丝根数,减半计算报废。
4.1.3、钢丝绳受冲击负荷而拉长超原长0.5%以上应报废。
4.1.4、钢丝绳在卷简上固定必须可靠,所有压板均应紧固,吊钩降到最低位置时,卷筒上最少留2~3圈钢绳。
4.2、车轮
4.2.1、车轮上不得有裂纹、轮缘上不得有过分磨损,如轮缘磨损超过原厚度的50%应更换,踏面上不许有超过2mm深的凹陷和压痕,踏面上最大磨损量不得超过轮缘厚度的15%。
4.2.2、两主动车轮直径的相对磨损差超过直径的0.1%时,应重新加工成相同的直径,其公差应不低于d6。
4.2.3、车轮端面不铅垂度g≤D/5000(D—轮的名义直径),车轮的上缘应向外倾。
4.2.4、车轮宽度的中心线与轨道中心线应平行,不平行度b≤D/1000(D—轮的名义直径),跨距两端的两车轮的倾斜方向应相反。
4.2.5、同一端梁下的车轮轮宽中心线应在同一直线上,其偏移C<2mm,且应垂直于大车纵向中心线。
4.2.6、同一端梁下车轮轴心,应处在同一水平面上,其高低差e<L/2000,(L—轮距),车轮轴距偏差为:
当轴距小于或等于3.5m时,应少于3mm,当轴距大于3.5m时,应不大于4mm。
4.2.7、车轮装好后,应都与轨道接触,如发现有悬空或啃道现象应设法消除。
4.2.8、小车同一轨上的车轮轴距偏差,一般不应大于2mm。
4.2.9、大车走行轮对角线的长度差不应大于5mm,小车走行轮对角线的长度差不应大于3mm。
4.3、减速机
4.3.1、减速机里面的油面,应始终保持在油针指示的油位上。
4.3.2、地脚螺钉和结合面螺钉不能有任何松动。
4.3.3、不准有漏油现象。
4.3.4、在运行中不准有噪音及撞击声,发现问题必须检查齿轮工作状况,磨损程度及啮合的正确性。
4.3.5、齿轮的接触,沿齿高方向不少于45%,沿齿长方向不少于60%。
4.3.6、在装入一个调整环后,滚动轴承的轴向间隙为0.4~0.2mm。
4.3.7、上、下机壳只能用漆片或密封胶密封,不得用其它代替,当螺栓拧紧后,接触面的局部间隙不得大于0.03mm。
4.3.8齿啮合侧间隙为齿啮合顶隙1-1.2mm,侧隙0.15-0.2mm。
4.3.9、齿轮磨损原齿的15%应报废。
4.4、轨道
4.4.1、大车跨度偏差凸L=±4~6mm,跨距小于19.5m时,为±4mm,跨距大于19.5m时,为±6mm。
4.4.2、大车轨道坡度为1/1000,接头间隙1~2mm,高低差不大于1mm,横向偏移应小于1mm。
4.4.3、大车轨道横向不水平度公差为轨道宽度的1%。
4.4.4、大车两条轨道的相对标高在柱子处小于10mm,其它地方小于15mm。
4.4.5、直线性误差±3mm。
4.4.6、天车轨道梁中心线位置,对设计定位轴线的偏差小于5mm,顶面标高对设计标高的偏差为10~-5mm。
4.4.7、车挡与天车大车缓冲器接触面应在同一水平面,两者定位轴线的距离偏差小于4mm,每跨两端必须安装行程限位器。
4.4.8、轨道检修调整应符合下述要求,否则应调整轨道梁:
4.4.8.1、轨道顶面抬高小于50mm。
4.4.8.2、轨道中心线和轨道梁中心线间距小于2Omm。
4.4.9、用小锤敲击轨道固定螺钉不得有松动现象。
4.4.10、轨道上应清洁,不得有油垢等异物,严禁电焊在轨道上打火。
4.5、滑轮
4.5