水泥生产资源综合利用及节能降耗途径最新版.docx
《水泥生产资源综合利用及节能降耗途径最新版.docx》由会员分享,可在线阅读,更多相关《水泥生产资源综合利用及节能降耗途径最新版.docx(7页珍藏版)》请在冰豆网上搜索。
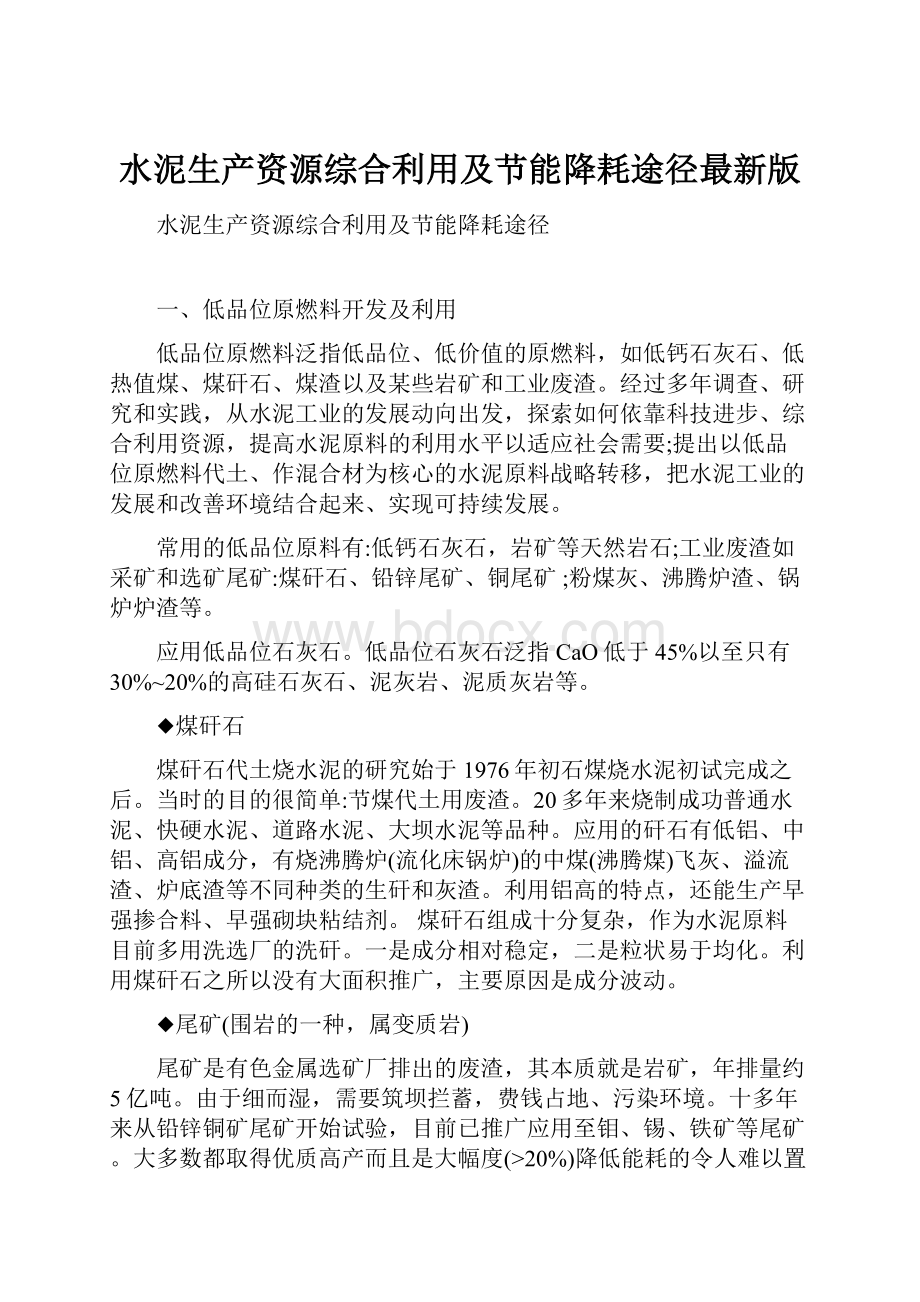
水泥生产资源综合利用及节能降耗途径最新版
水泥生产资源综合利用及节能降耗途径
一、低品位原燃料开发及利用
低品位原燃料泛指低品位、低价值的原燃料,如低钙石灰石、低热值煤、煤矸石、煤渣以及某些岩矿和工业废渣。
经过多年调查、研究和实践,从水泥工业的发展动向出发,探索如何依靠科技进步、综合利用资源,提高水泥原料的利用水平以适应社会需要;提出以低品位原燃料代土、作混合材为核心的水泥原料战略转移,把水泥工业的发展和改善环境结合起来、实现可持续发展。
常用的低品位原料有:
低钙石灰石,岩矿等天然岩石;工业废渣如采矿和选矿尾矿:
煤矸石、铅锌尾矿、铜尾矿;粉煤灰、沸腾炉渣、锅炉炉渣等。
应用低品位石灰石。
低品位石灰石泛指CaO低于45%以至只有30%~20%的高硅石灰石、泥灰岩、泥质灰岩等。
◆煤矸石
煤矸石代土烧水泥的研究始于1976年初石煤烧水泥初试完成之后。
当时的目的很简单:
节煤代土用废渣。
20多年来烧制成功普通水泥、快硬水泥、道路水泥、大坝水泥等品种。
应用的矸石有低铝、中铝、高铝成分,有烧沸腾炉(流化床锅炉)的中煤(沸腾煤)飞灰、溢流渣、炉底渣等不同种类的生矸和灰渣。
利用铝高的特点,还能生产早强掺合料、早强砌块粘结剂。
煤矸石组成十分复杂,作为水泥原料目前多用洗选厂的洗矸。
一是成分相对稳定,二是粒状易于均化。
利用煤矸石之所以没有大面积推广,主要原因是成分波动。
◆尾矿(围岩的一种,属变质岩)
尾矿是有色金属选矿厂排出的废渣,其本质就是岩矿,年排量约5亿吨。
由于细而湿,需要筑坝拦蓄,费钱占地、污染环境。
十多年来从铅锌铜矿尾矿开始试验,目前已推广应用至钼、锡、铁矿等尾矿。
大多数都取得优质高产而且是大幅度(>20%)降低能耗的令人难以置信的技术经济效益。
研究其机理,是其中的许多岩矿组分改变了水泥熟料的煅烧和成矿过程,成为提高等级或多掺混合材降低成本的有效措施,获得比过去推广应用低热值煤(石煤、煤矸石)烧水泥更好的效果。
尾矿的应用成为重新认识熟料烧成机理、煅烧潜力和控制烧成过程的机会。
各地尾矿成分不同,提高强度、降低煤耗的幅度也不一样。
需要因地制宜选择应用。
以节能环保、实用高效为导向,以便实现清洁生产和高效率节约化生产为目标,走可持续发展的道路,是21世纪水泥工业发展的趋势。
在水泥生产材料使用的研究方向主要是减少水泥生产材料在生产中化合后产生的有害气体(cO:
、s02等)的排放,要求在原料的采用上,增加对低品位原燃料、工业废弃资源的使用范围和程度。
二、利用先进的粉磨工艺技术和节能粉磨设备
据有关资料统计,我国水泥厂每生产1吨水泥需要粉磨30种以上各种物料,而粉磨电耗约占水泥生产总电耗的65%~70%,粉磨成本占生产总成本的35%左右,粉磨系统维修量占全厂设备维修量的60%。
因此,粉磨对水泥生产企业的效益影响极大。
粉磨工序能耗主要体现在生料制备、煤粉制备和水泥粉磨的环节,其电量消耗占水泥生产综合电耗的72%(生料粉磨电耗约占水泥综合电耗的24%,水泥粉磨电耗约占水泥综合电耗的38%)。
因此,选择节能粉磨设备和工艺流程显得很重要。
(一)生料辊压机粉磨工艺技术及设备
辊压机水泥生料终粉磨系统广泛应用于水泥生料生产。
其采用先进的辊压粉磨技术,改变了传统的粉磨系统和粉磨原理,电耗大幅度降低,并配备了航空液压系统、自动控制系统和V型选粉机,确保了辊压机运行更加可靠,运转成本更低。
系统综合利用辊压机辊面耐磨技术、辊压机恒缝控制及自动纠偏的液压及自控技术、V型选粉机静态分选技术、XR动态选粉机分选技术等多项自主创新技术,解决了辊压机运行过程中产生振动等技术难题,整个工艺系统投资少、占地面积小,结构简洁,操作简单,维护便利。
辊压机水泥生料终粉磨系统性能指标:
应用辊压机生料终粉磨系统生产出的生料成品:
生料成品:
R0.08mm≤14%,R0.2mm≤2.5%;成品颗粒形状:
呈针状、片状,更易烧结;车间电耗:
约11kWh/t。
与国内外同类技术比较国内常用的生料粉磨设备为管磨机和立磨机,但是管磨机系统车间电耗约为22kWh/t,立磨系统车间电耗也约为18kWh/t。
随着节能降耗观念的深入,辊压机运用于水泥厂生料粉磨系统的趋势已经初现端倪。
成都利君实业股份有限公司开发的辊压机水泥生料终粉磨系统解决了辊压机使用的可靠性,完全解决了生料的粉磨、分选、烘干问题,并以良好的运行情况投入到实际生产中,以其高效、节能、环保的特点,很快得到了市场的认同和用户的好评。
经实际使用,系统单位电耗仅为11kWh/t,相对于常规管磨、立磨系统,能耗分别降低50%和39%,辊压机系统产量提高100-300%。
成都利君实业股份有限公司开发的辊压机水泥生料终粉磨系统采用“辊压机+V型选粉机+热风管道+动态精细选粉机”的工艺路线,从根本上降低生料粉磨电耗,也降低了投资成本。
实现节能降耗、减少投资,维修保养方便。
采用辊压机恒缝控制方法及自动纠偏系统,结合辊压机辊面耐磨技术,提高了辊压机寿命,减少停机时间,提高运转率,维护简便减少了维修保养成本。
采用“V型选粉机+XR选粉机+旋风收尘器+循环风机”选粉系统,既解决了生料的烘干问题、提高了选粉效率,又能保证生料的细度要求。
2000年以来,合肥水泥研究设计院开发的辊压机生料半终粉磨系统被成功应用于内蒙古冀东水泥有限责任公司、湖南兆山新星水泥有限公司的5000t/d熟料生产线及吉林省通化特种水泥集团股份有限公司、山东兖矿集团有限公司水泥厂、浙江诸暨八方水泥有限责任公司等企业的水泥生料系统改造中。
成都利君实业股份有限公司开发出了适用于2500t/d熟料生产线的辊压机生料终粉磨系统(辊压机:
CLFl80-120,电机功率:
2×1250kW),并应用于国内新型干法水泥生产线中。
目前,共有5(台)套分别用于榆次智海、贵州六矿瑞安、常德中材牛力、云浮中材亨达和恩施腾龙的2500t/d熟料生产线上。
辊压机生料终粉磨系统主要特点是:
系统充分利用了辊压机的料床粉碎压力高和挤压后物料全部机械外循环的方式输送,减少了分级系统风机的装机功率,系统电耗较低。
可见,在辊压机生料终粉磨系统选用得当的情况下,其原理决定了比生料立式磨更节能。
但是,选择辊压机用于生料粉磨系统时,需要注意以下问题。
(1)辊压机的工作压力高,被挤压物料易成饼,给烘干增加难度。
此外,水泥原料中的水分受季节影响较大,矿山开采不同阶段中韧性杂质含量的波动等也会对辊压机的有效运行产生较大影响。
(2)辊压机的拉入角比立式磨小得多,且料层的稳定性也不如立式磨。
因此,辊压机的最大入料粒度也比立式磨小得多。
(3)生料粉磨系统直接影响水泥窑的运转率。
立式磨可以在30个小时左右将磨盘、磨辊的磨损件更换完毕,而辊压机则要比这一时间长很多。
因此,在选择辊压机用于生料粉磨系统时,必须备有完整的轴系作备件,并周密安排检修计划和季节,以保证随窑运转率。
(4)辊压机的工作压力高于立式磨,而料层厚度却小于立式磨。
因此,对金属异物的敏感性远高于立式磨,必须严格控制大块金属材料,尤其是高合金钢的非磁性材料。
(二)水泥粉磨工艺技术及设备
1、不同粉磨技术及设备能耗比较
◆球磨机系统
影响球磨机粉磨效率的因素较多,包括研磨体级配、磨机通风、熟料温度和粉磨工艺等。
应优先采用配高效选粉机的圈流球磨工艺,圈流磨利于产品细度和温度的调节和控制,粉磨效率比开流磨高10%~20%,成品越细优势越明显。
◆辊压机预粉磨系统
辊压机与球磨机组成的各种预粉磨系统(包括循环预粉磨、联合粉磨、半终粉磨等)已经成为水泥粉磨的主要方案,这是由于辊压机的粉磨效率约为球磨机的2倍左右,可以大幅度节电。
辊压机系统节电水平取决于辊压机消耗功率的大小,辊压机每消耗1kWh/t,主机电耗(辊压机+球磨机)可降低0.8kWh/t~1kWh/t。
辊压机的功率消耗与投影压力成线性关系,循环预粉磨辊压机投影压力为5500kN/m2~6500kN/m2,联合粉磨投影压力略低,控制在5000kN/m2~6000kN/m2。
辊磨终粉磨系统:
粉磨水泥时辊磨的粉磨效率是球磨机的1.6~1.8倍,系统节电30%以上。
熟料温度、入料粒度、磨损程度等对产量和电耗均有较大影响。
关键是终粉磨水泥性能,要通过调节粉磨压力、挡料圈高度、风速风量,控制出口温度,采用高性能选粉装置等措施优化水泥颗粒级配,保证产品性能。
对于生料磨如分别更替离心式或旋风式选粉机,可增产10%左右或5%左右,降耗1kWh/t左右。
用于生料磨的好处主要是分离清晰,成品中过粗颗粒少,有利于烧成,可适当放宽细度。
但生料细度较水泥粗,粗选粉并不是高效笼式选粉机的长处。
因此其增产节能指标要低于水泥磨。
◆预破碎
“多破少磨”从粉碎机理上来说是合理的。
一方面破碎的单耗远比球磨的单耗低,因此后者的无用功大,粉碎效率低。
另一方面入磨粒度降低以后,球磨机中的钢球可大大变小,小钢球将减少对物料粉碎所造成的能量过剩的浪费。
一般来说,大球的比能耗高,小球的比能耗低。
从以上粉磨系统的不同特点可以看出,各系统均有不同程度的优势和不足,企业选择粉磨系统时,特别是对现有磨机进行改造时,应根据自身的设备、原料、管理水平、资金状况等条件,按可选择方案的性价比选择适合自己企业的方案。
2、水泥粉磨技术的改进措施
2.1正确选择粉磨研磨体及其级配物料在粉磨过程中,一方面需要冲击作用,另一方面需要研磨作用。
不同规格的研磨体配合使用,还可以减少相互之间的空隙率,使其与物料的接触机会多,有利于提高能量利用率;在研磨体装载量一定的情况下,小钢球比大钢球的总表面积大;要将大块物料击碎,就必须钢球具有较大的能量,因此,钢球(段)的尺寸应该较大;需要将物料磨得细一些,就应选择小些的钢球(段)。
因此在粉磨作业时,要正确选择研磨体且必须进行合理的级配。
粉磨研磨体级配基本原则:
(1)入磨物料的平均粒径大,硬度高,或要求产品粗时,钢球的平均径应大些,反之应小些。
磨机直径小,钢球平均球径也应小,一般生料磨比水泥磨的钢球平均球径大些;
(2)开路磨机,前一仓用钢球,后一仓用钢段;
(3)研磨体大小必须按一定比例配合使用,钢球的规格通常用3~5级,钢段一般用2~3级,若相邻两仓用钢球时,则前一仓的最小规格应作为后一仓的最大规格(交叉一级);
(4)各级钢球的比例可按“两头小、中间大”的原则配合,用两种钢段时,各占一半即可。
用三种钢段时,可根据具体情况适当配合;
(5)在满足物料细度要求前提下,平均球径应小些,借以增加接触面积和单位时间的冲击次数,提高粉磨效率。
2.2加强预粉碎技术的应用与采取的配套措施以降低入磨物料粒度为主要手段,使球磨机节能高产的技术称之为预粉碎技术。
它把球磨机第一仓的粉碎工作,部分或全部由其他能量利用率高于球磨机的粉碎设备来完成,让入磨物料粒度降低到5mm以下或更小,可使磨机台时产量提高30%以上、单产电耗降低15%~20%,产品颗粒组成更加合理。
配套措施:
(1)选用振动筛或回转筛,对粉碎后的入磨物料采用检查筛分闭路流程,合格物料入磨,粒度过大的物料重新预粉碎;
(2)入磨粒度缩小后,第一仓研磨体平均球径也要缩小;第一仓长度要缩短,隔仓板前移;
(3)磨内风速要提高,磨机通风量加大;
(4)闭路粉磨系统辅助设备的生产能力要加大,系统循环负荷率要降低,选粉效率要提高。
2.3严格控制入磨物料的水分为了保证磨机正常操作、配料的准确和提高磨机的产、质量。
当物料含水量大时,容易产生糊磨现象,磨内细粉粘附在研磨体和衬板上,使粉磨效率降低,严重时会使隔仓板篦孔堵塞造成磨机通风不良,物料难以通过,产量急剧下降,质量也引起较大的波动。
根据生产实践经验,各种物料的水分可控制在下列范围内:
石灰石<><><><><><><>
2.4加强磨机通风是提高磨机生产能力的主要途径其优点有以下:
(1)减少球磨机内的过粉磨现象。
使磨内微细粉,及时地被气流带走,消除了细粉结团、糊球、糊衬板现象以及对研磨体的缓冲作用;
(2)磨内的水蒸汽能及时的排除,使隔仓板篦缝不易堵塞,减少饱磨、糊磨现象;
(3)能降低磨内温度,防止石膏脱水、出磨水泥假凝,有利于磨机正常运转和保证水泥质量;
(4)有利于车间环保和清洁生产。
三、结束语
除了上述介绍的低品位原燃料开发及利用、利用先进的粉磨工艺技术和节能粉磨设备以外,在新型干法水泥生产制造技术方面,还有孰料冷却技术、两支承短窑技术、预热器节能技术、余热发电等技术值得研究。