风烟道阻力及均匀性优化专题.docx
《风烟道阻力及均匀性优化专题.docx》由会员分享,可在线阅读,更多相关《风烟道阻力及均匀性优化专题.docx(15页珍藏版)》请在冰豆网上搜索。
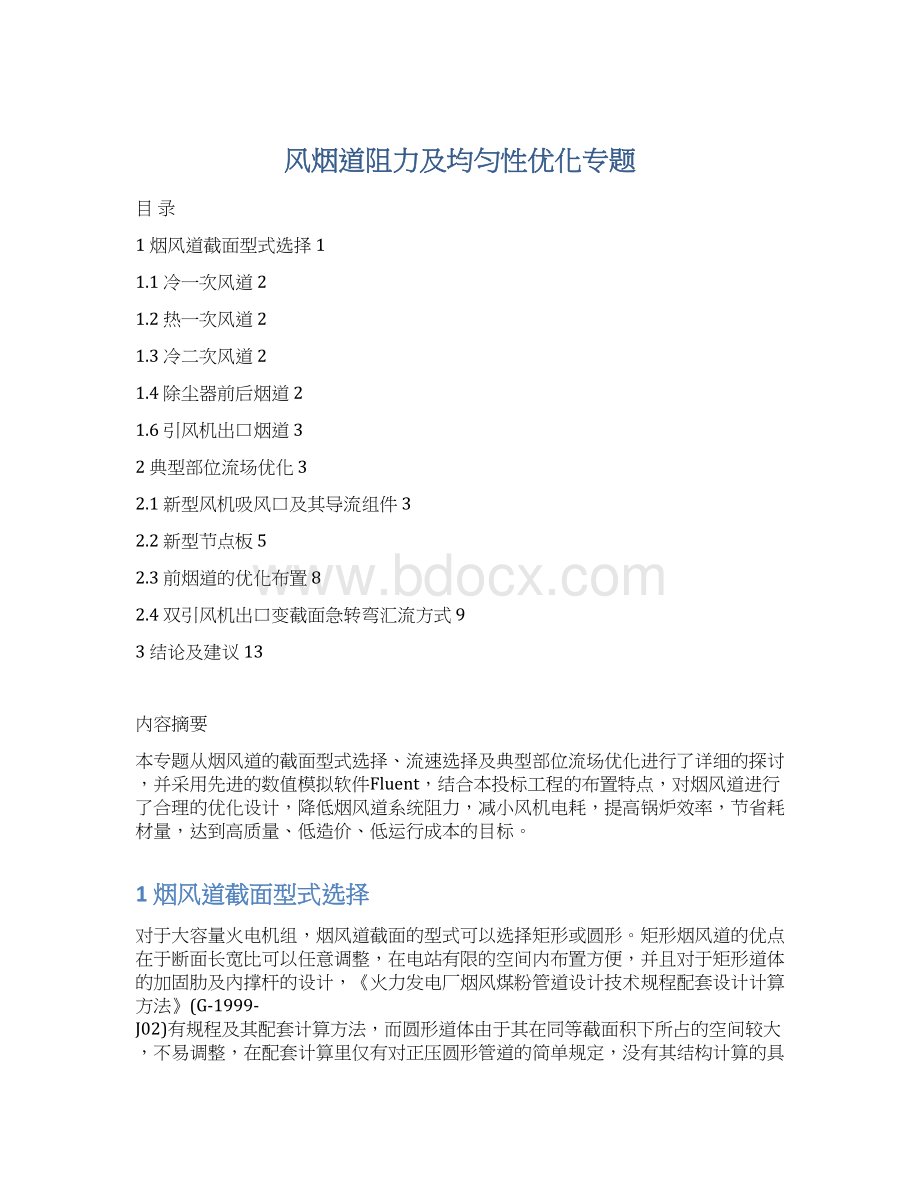
风烟道阻力及均匀性优化专题
目录
1烟风道截面型式选择1
1.1冷一次风道2
1.2热一次风道2
1.3冷二次风道2
1.4除尘器前后烟道2
1.6引风机出口烟道3
2典型部位流场优化3
2.1新型风机吸风口及其导流组件3
2.2新型节点板5
2.3前烟道的优化布置8
2.4双引风机出口变截面急转弯汇流方式9
3结论及建议13
内容摘要
本专题从烟风道的截面型式选择、流速选择及典型部位流场优化进行了详细的探讨,并采用先进的数值模拟软件Fluent,结合本投标工程的布置特点,对烟风道进行了合理的优化设计,降低烟风道系统阻力,减小风机电耗,提高锅炉效率,节省耗材量,达到高质量、低造价、低运行成本的目标。
1烟风道截面型式选择
对于大容量火电机组,烟风道截面的型式可以选择矩形或圆形。
矩形烟风道的优点在于断面长宽比可以任意调整,在电站有限的空间内布置方便,并且对于矩形道体的加固肋及內撑杆的设计,《火力发电厂烟风煤粉管道设计技术规程配套设计计算方法》(G-1999-J02)有规程及其配套计算方法,而圆形道体由于其在同等截面积下所占的空间较大,不易调整,在配套计算里仅有对正压圆形管道的简单规定,没有其结构计算的具体公式及方法,故长期以来电站的烟风道,采用矩形道体居多。
圆形和矩形烟风道的主要技术特点对比如下表所示。
表1-1圆形与矩形烟风道的主要技术特点对比
圆形
矩形
烟风道布置
由于道体外形不能改变,布置局限性较大
道体高宽比可以改变,布置局限性较小
流动阻力分析
1)无内支撑,直段部分内部流场相对较好
2)由于采用焊接弯头,当弯曲半径与矩形相同时,其阻力偏高
有内撑,由于支撑的存在,会有一定的阻力消耗,但由于支撑所占截面较小,对阻力的影响较小。
道体及支吊架加工制作
1)道体及加固肋等设计耗材量较少,但由于圆形烟风道对钢板原料尺寸的要求较高,故其加工裕量较大,一般为5-10%,尤其是方圆节,加工裕量一般为10%以上;
2)焊缝少,焊接工作量有所降低;
3)支吊架加工精度要求较高,加工工作量较大;
4)支吊架材料耗量较多;
5)因为烟风道壁面较薄,板面及加固肋的卷制较为困难,尤其是方圆节工作量较大,至少是矩形大小头工作量的5倍以上;
6)由于道体相对较轻,而施工单价按照重量报价,故每t的加工成本会高于矩形烟道。
1)道体及加固肋等设计耗材量较多,但对钢板原料尺寸的要求较低,故其加工裕量较小,一般为3%左右;
2)焊缝数量较多,焊接工作量相对较大;
3)支吊架加工精度要求相对较低,加工工作量较小;
4)支吊架材料量耗用较少。
道体吊装
烟风道整体刚度较差,零件加工完成后对于放置角度要求较高,并经常需要增设临时内支撑,现场吊装较为困难
烟风道整体刚度较好,现场吊装简单
1.1冷一次风道
冷一次风道主要指一次风机吸入口及一次风机出口至空预器入口部分的风道。
由于一次风机入口为方形接口,故消音器至风机入口之间的大小头可以选择采用矩形截面,或者方圆节(对应消音器为圆形截面)。
当进出口尺寸相当时,方圆节耗用材料量更多,并且现场加工工作量大,加工精度更难保证,故一次风机入口应选择矩形大小头。
由于一次风机出口为圆形接口,空预器冷一次风道入口为方形接口,故一次风机与空预器之间的冷一次风道可以选用矩形或圆形。
当选用矩形截面时,风道的截面尺寸为2000×2100×4,风机出口设置方圆节;当选用圆形截面时,风道的截面尺寸可以选择Φ2320×4,空预器入口设置方圆节。
对一次风机出口至空预器入口之间的风道,采用圆形截面的综合成本低于矩形截面,且阻力降低,故在布置允许的情况下推荐选用圆形风道。
1.2热一次风道
热一次风道是指空预器出口至磨煤机入口之间的风道。
空预器至煤仓间前管道及母管常规选用圆管的,本次优化不做讨论,选用Φ1820×5圆形管道。
对于磨煤机入口支管部分,因为一般按照防爆压力0.35MPa设计,采用矩形管道的结构和强度设计较难满足要求。
如选用矩形截面,风道的截面尺寸为1100×1200×8;当选用圆形截面时,风道的截面尺寸可以选择Φ1320×5。
本工程磨煤机入口支管部分选用圆形Φ1320×5管道。
1.3冷二次风道
冷二次风道主要指送风机吸入口及送风机出口至空预器入口部分的风道。
由于送风机入口为方形接口,故消音器至风机入口之间的大小头可以选择采用矩形截面,或者方圆节(对应消音器为圆形截面)。
当进出口尺寸相当时,方圆节耗用材料量更多,并且现场加工工作量较大,加工精度更难保证,故送风机入口应选择矩形大小头。
送风机出口至空预器入口部分的风道,当选用矩形截面时,风道的截面尺寸为3600×3200×4,风机出口设置方圆节;当选用圆形截面时,为Φ3920×4,空预器入口设置方圆节。
本工程送风机出口至空预器入口部分的风道选用圆形Φ3920×4管道。
1.4除尘器前后烟道
除尘器前烟道指空预器出口至除尘器入口部分的烟道,除尘器后烟道主要指除尘器出口至引风机入口部分烟道。
。
当选用矩形截面时,截面尺寸为3200×3000×5;当选用圆形截面时为Φ3220×5,并在空预器出口、除尘器进出口均设置方圆节。
除尘器前烟道若采用矩形截面,则空预器出口部位一般采用联箱结构作为除尘器3个通道的分流装置,该结构具有易积灰、流场混乱的缺点。
烟道采用圆形管道的综合成本明显低于矩形管道,故在布置允许的情况下除尘器前后烟道应优先选用圆形截面。
除尘器前后烟道采用圆形烟道后,结合引风机的布置方式,选择圆形截面通过调整能使得除尘器出口的每根支管长度相近,弯头数量及阻力也能保持均衡,从而确保更好的流场效果和结构强度。
除尘器两室的气流均布、阻力偏差均得到很好的解决。
1.6引风机出口烟道
引风机出口烟道主要指引风机出口至吸收塔入口部分的烟道。
当选用矩形截面时,引风机出口设置有方圆节;当选用圆形截面时,通过两个方圆节变径。
采用圆形和矩形方案的弯头数量完全相同,但由于圆形烟道取消了内撑杆,其内部流场分布较好,整体阻力较低。
采用圆形截面的材料综合成本也明显低于矩形截面,故宜优先推荐圆形烟道。
2典型部位流场优化
2.1新型风机吸风口及其导流组件
风机吸风口通常采用的型式主要有两类,一种是采用直通道吸风,如图2-1,一种是采用90°弯头吸风,并且配套设置楼板或防雨罩来对风机进行防护。
这种做法的缺点在于:
防护设施往往采用平板面等常规的结构型式,不能与风机吸入口的气流分布相协调,从而使得风机吸风口气流紊乱,不但增加风机运行阻力和功耗,而且会引起风机及风道系统振动,产生噪音污染。
目前常用的减小噪音的做法是在风机吸风口设置消音器,而消音器的设置不但会进一步增加系统的运行功耗,并且因其优化气流分布的作用有限,也不能取得很好的降噪作用。
基于此,我院结合数值模拟软件对吸风口及其防雨罩进行了优化设计,详见图2-2所示,主要有如下特点:
1)对应于确定的风机和风量需求下,采用新型吸风口可以有效的组织气流分布,降低风道和风机振动,并且可以减少烟风流动阻力,降低能耗和噪音,实现节能;
2)采用新型吸风口及其导流组件不但可以有效的组织气流分布,并且可以很好的保护风机,防止杂物和雨水进入。
3)新型吸风口弧度及导流装置形状完全根据数值模拟和物模实验确定,对于气流分布的控制更精准,可以视情况取消风机入口的消音器,从而进一步降低阻力和能耗。
图2-1传统型吸入口图2-2新型吸风口及其导流组件
该方案的数值模拟采取非结构网格模型。
主要是因为结构中由薄壁结构,在遮雨板曲线优化中,由尖角产生,因此采用非结构网格能够很好的保证最后网格划分的质量。
经过模拟计算的风道三维流线分布图如图2-3所示。
吸入口剖面总压分布图如图2-4所示。
通过数值模拟结果可以看出,采用新型的吸风口及其导流组件使得进入风机的气流分布更均匀,有利于风机及出口风道的气流均布,降低风机及风道运行阻力。
2-3流场分布总图
2-4吸入口剖面总压分布图
2.2新型节点板
烟风道作为一种建筑构件,当烟风道尺寸大于一定值后,烟风道的外壁上需设置加固肋,在实际施工过程中,为了施工安全和减少加固肋的使用,或者当超过频率控制极限跨度和需要减小加固肋规格时,在烟风道内增设内支撑是必要的措施,内支撑多采用圆管或型钢,即首先在烟风道内壁上设置数个加强板,后在每一组相对设置的加强板上横向设置一根内支撑,此时内支撑对准每道横向加固肋设置,为减少内支撑的现场施工工作量并提高施工的精度,相互交叉连接的内支撑之间或者内支撑与烟风道内壁之间的连接一般采用节点板。
如图2-5所示,是现有烟风道内支撑B型节点形式,两个内支撑形成“十字形”交叉结构,并于交叉部位通过节点板连接,对于B型节点,《火力发电厂烟风煤粉管道设计技术规程》(以下简称规程)中推荐使用的节点板安装方式是:
节点板为两块板体1、2,两块板体1、2分别焊接在其中一个内支撑3的两侧,另一个内支撑4分为两段,每段与节点板的连接端面上开有沿该端面径向贯穿的卡槽7,两块板体1、2分别卡接固定于卡槽7内,此时,节点板的板面与烟风道内烟风的流向基本垂直,即节点板的板面迎向烟风;如图2-6所示,是现有烟风道的内支撑C、D、F型节点形式,该节点是通过内支撑与烟风道连接形成,对于此种节点,《规程》中推荐的节点板安装方式是:
在烟风道10的外壁上设有加固肋11,加强板5设置在烟风道10的内壁上,在加强板5上以与其垂直方向设置节点板6,内支撑8与节点板6的连接端面上分别开有沿该端面径向贯穿的卡槽9,节点板6卡接固定在卡槽9内,此时,节点板的板面与烟风道内烟风的流向基本垂直,即节点板的板面迎向烟风。
2-5原B型节点示意图
2-6原C、D、F型节点示意图
以上节点板安装方式的缺陷在于:
⑴随着烟风道尺寸的增大,内支撑的规格也会增大,而节点板的尺寸也会相应加大,使得节点板占烟风道通流面积的百分比增加,由于节点板的板面迎向烟风,烟风流通的截面积减小,会增大烟风道的阻力,增加烟风道运行能耗,不利于节能降耗;⑵烟风流过节点板,容易产生涡流,引起烟风道的振动,产生较大的噪音;⑶在烟风流量确定的情况下,现有节点板的设置使得烟风道的截面积尺寸较大,因此增加了耗材,提高了投资成本;⑷当烟风道的内支撑沿烟风流动方向排列有多个时,为了实现组织气流分布的良好效果需增设导流板,如此会增加施工成本。
新型节点板的板面与烟风道内的烟风流动方向平行,增加了烟风实际利用的流通截面积,从而降低了烟风流速,减少烟风流动阻力,降低能耗,实现节能;由于烟风流过节点板后不易形成涡流,因此减少了烟风道的振动,使得由于振动而产生的噪音也大幅度降低;新型节点板具有导流板的作用,因此当烟风道的内支撑沿烟风流动方向排列有多个时,不必另设导流板,也可以实现组织气流分布的良好效果,从而降低了施工成本;在烟风流量确定的情况下,设计烟风道截面尺寸时,采用新型节点板可以在满足规程推荐的烟风流速前提下,降低烟风道的截面尺寸,从而减少材料耗量,降低施工成本。
新型节点板应用于内支撑B型节点:
节点板为板面开有中心安装孔的板体,第一内支撑分为两段,每段的其中一端分别固定在烟风道的内壁上,而每段用于与节点板连接的端面上开有沿该端面径向贯穿的卡槽,所述节点板的两边侧卡接固定在相对应的卡槽中;所述中心安装孔的孔径与第二内支撑的径向截面尺寸相适应,第二内支撑穿过所述中心安装孔后两端均固定在烟风道的内壁上。
在满足相同受力情况下,节点板与内支撑焊接连接时,焊缝的长度缩短为现有节点板焊接连接形成焊缝的一半,而且本发明节点板为一块,因此可降低施工人员切割和焊接的工作量,从而加快施工进度。
应用于内支撑C型节点:
所述节点板为两个,每个内支撑用于与节点板连接的端面上开有沿该端面径向贯穿的