01济钢3200高炉主控室工艺技术操作规程讲解.docx
《01济钢3200高炉主控室工艺技术操作规程讲解.docx》由会员分享,可在线阅读,更多相关《01济钢3200高炉主控室工艺技术操作规程讲解.docx(47页珍藏版)》请在冰豆网上搜索。
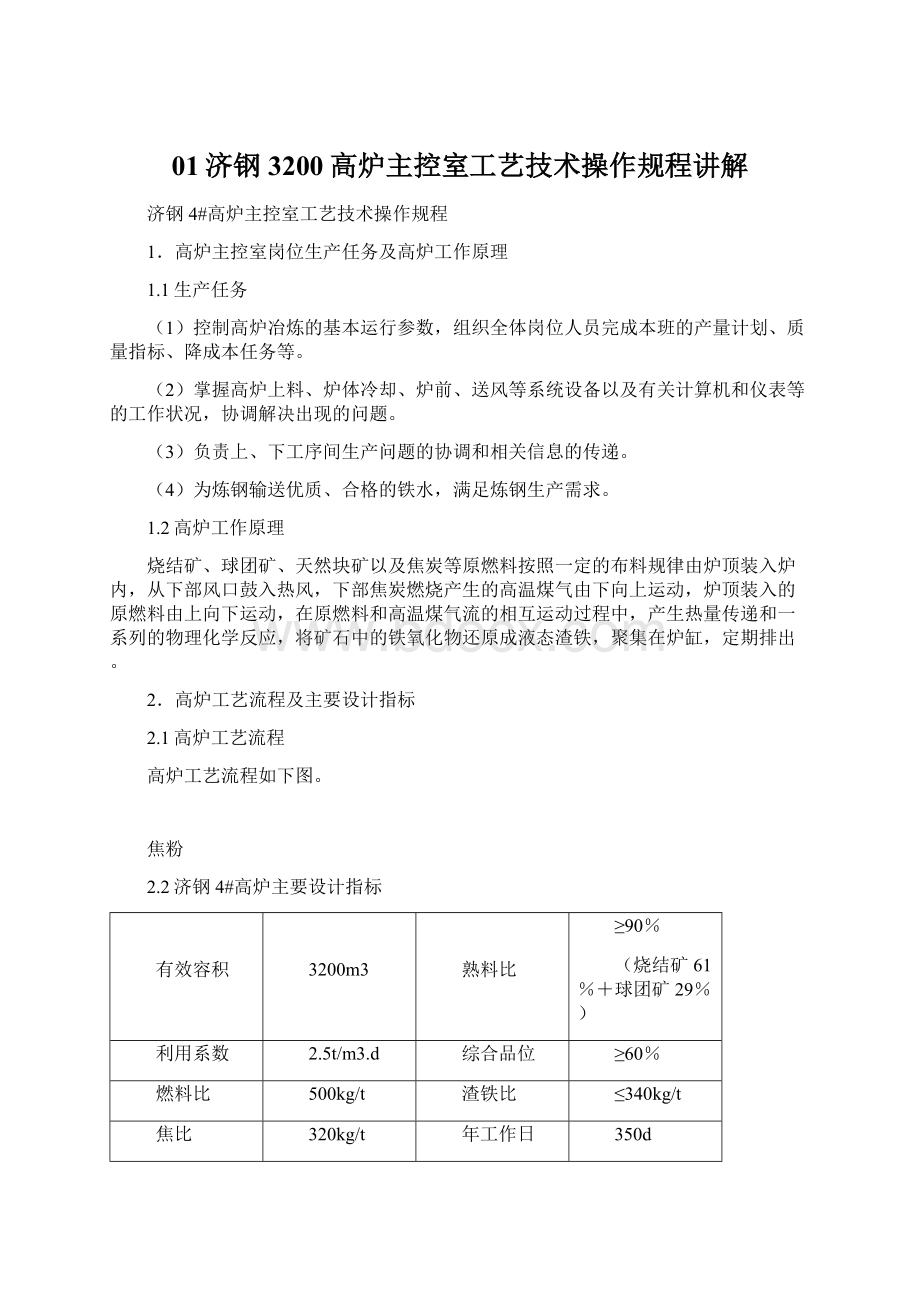
01济钢3200高炉主控室工艺技术操作规程讲解
济钢4#高炉主控室工艺技术操作规程
1.高炉主控室岗位生产任务及高炉工作原理
1.1生产任务
(1)控制高炉冶炼的基本运行参数,组织全体岗位人员完成本班的产量计划、质量指标、降成本任务等。
(2)掌握高炉上料、炉体冷却、炉前、送风等系统设备以及有关计算机和仪表等的工作状况,协调解决出现的问题。
(3)负责上、下工序间生产问题的协调和相关信息的传递。
(4)为炼钢输送优质、合格的铁水,满足炼钢生产需求。
1.2高炉工作原理
烧结矿、球团矿、天然块矿以及焦炭等原燃料按照一定的布料规律由炉顶装入炉内,从下部风口鼓入热风,下部焦炭燃烧产生的高温煤气由下向上运动,炉顶装入的原燃料由上向下运动,在原燃料和高温煤气流的相互运动过程中,产生热量传递和一系列的物理化学反应,将矿石中的铁氧化物还原成液态渣铁,聚集在炉缸,定期排出。
2.高炉工艺流程及主要设计指标
2.1高炉工艺流程
高炉工艺流程如下图。
焦粉
2.2济钢4#高炉主要设计指标
有效容积
3200m3
熟料比
≥90%
(烧结矿61%+球团矿29%)
利用系数
2.5t/m3.d
综合品位
≥60%
燃料比
500kg/t
渣铁比
≤340kg/t
焦比
320kg/t
年工作日
350d
煤比
180kg/t
(设备能力200kg/t)
年产生铁
280×104t
炉顶压力
0.23Mpa
(最大0.25Mpa)
年产水渣
105×104t
热风温度
1200~1250℃
高炉煤气发生量
60.69×104m3/h
(标况)
富氧率
0~3%
高炉一代寿命
≥15a
入炉风量
最大7200m3/min
(标况)
热风炉一代寿命
30a
3.高炉工艺设备及相关技术参数
3.1高炉内型
高炉内型及相关参数如下图。
3.2炉缸电偶布置
炉缸圆周分为24个纵截面,横截面设13层。
每个铁口沿轴线四周埋设8个测温点,4个铁口共32个点。
沿高炉轴线埋入6点;铺底层(封板上找平层)5点,中心一点其余4点均匀布置。
共埋设683个测温点。
4.原燃料管理
4.1原燃料质量管理
4.1.1原燃料质量标准:
(1)精块矿
项目
热爆裂指数
%
全铁量
%
粒度范围
mm
6~30mm
%
-5mm
%
质量标准
<1
>64
6~30
≥85
≤4
(2)烧结矿
项目
TFe
%
CaO
SiO2
FeO
%
Al2O3
%
S
%
TI
%
RDI
%
转鼓指数
(+6.3mm)
+50mm
%
5~10mm
%
-5mm
%
波动范围
质量
标准
±0.5
±0.05
7~9
≤2.0
≤0.01
≥70
≤30
≥79
≤5
≤18
≤5
(3)球团矿
项目
TFe
%
CaO
SiO2
FeO
%
S
%
转鼓指数
(+6.3mm)
常温耐压
强度
N/个
还原率
%
膨胀指数
%
-5mm
%
波动范围
质量
标准
±0.5
±0.05
≤1
≤0.005
≥90
≥3000
≥80
≤16
≤3
(4)焦炭
强度要求
机械强度
热态指标
抗碎强度M40
耐磨强度M10
反应性CRI
反应后强度CSR
≥88
≤6.0
≤23
≥70
成分要求%
水分(MT)
灰分(Ad)
挥发份(Vdaf)
硫分(St.d)
≤0.2
≤12
≤1.0
≤0.6
粒度要求%
平均粒度
mm
<25mm
25~40mm
40~75mm
>75mm
45~55
<10
<10
备注
焦炭的CRI、CSR只做为生产操作的依据,不是考核指标。
(5)无烟煤、烟煤
水分%
挥发份%
灰分
硫份%
固定碳%
无烟煤
≤10
≤12
≤0.7
烟煤
≥23
≤10
≤0.7
混合煤粉
18~22
≤11
≤0.7
备注
烟煤的胶质层厚度≤10mm
4.1.2原燃料的取样与分析要求
原料名称
分析项目
分析频度
采样地点
焦炭
工业分析、转鼓、粒度组成
1/班
焦化厂
反应性(CRI)、反应后强度(CSR)
2/周
灰份全分析
2/周
槽下小焦
粒度组成
2/周
高炉槽下
烧结矿
成分分析、转鼓、粒度组成
2/班
400烧结机
还原度(RI)、低温还原粉化(RDI)
2/周
入炉粒度组成
2/周
高炉槽下
小粒烧
粒度组成
2/周
高炉槽下
球团矿
成分分析、粒度组成、抗压强度、转鼓
1/班
球团厂
还原度(RI)、膨胀指数(RSI)
2/周
富块矿
成分分析、粒度
3/批
料场
锰矿
成分分析、粒度
使用前
料场
熔剂
成分分析、粒度
使用前
料场
喷吹煤粉
固定碳、灰分、挥发份、硫磺、粒度
1/班
喷煤
喷吹原煤
工业分析
2/批
原煤场
4.1.3采用新原燃料品种或原用原燃料发生重大的调整和变化时,必须先进行成分分析、理化及冶金性能的试验,取得试验数据,并经分管厂长批准后方可使用。
4.2卸(存)料管理
4.2.1高炉所使用的各种原燃料,必须按品种卸入规定的料仓,严禁混料。
每个料仓所对应的物料品种计划应由高炉作业区提出,并报调度室同意后,由调度室统筹安排。
4.2.2料仓应作为原燃料进一步混匀与改善的手段,各种原燃料应逆皮带运转方向依次卸入指定料仓。
矿石采用中心卸料法,焦炭采用先边缘后中心卸料法,充分发挥料槽的中和作用,减少偏析和破碎。
4.2.3各料仓的槽存量应保持在料仓有效容积的70%以上,槽内存料低于有效容积40%的警戒料位时,要及时通知高炉主控室。
4.2.4卸料应遵循一槽一品种的原则,严禁混料。
如出现混料,应立即停止使用,并报厂调度室调查后研究处理办法。
4.2.5矿仓改变储存品种时,应先清理矿仓后进行。
4.2.6高炉各料仓的储存能力。
炉料名称
数量(个)
单个容积(m3)
总容积(m3)
贮存时间(h)
焦炭
6
580
3480
13.3
烧结
7
740
5180
21.2
球团
3
410
1230
29
块矿
3
200
600
14.6
杂矿
3
200
600
~28.8
碎焦
1
170
170
9.3
碎矿
1
160
160
9.1
焦丁
1
120
120
10
4.3原燃料的使用管理
4.3.1高炉的正常原料结构,由安全生产技术部依据原料的平衡计划制定方案,并报经生产(或技术)副厂长批准后,高炉作业区遵照执行。
确因事故需临时改变配料比时,值班工长报调度,由值班主任批准执行,短时间不能恢复的,要及时汇报生产(或技术)副厂长。
4.3.2高炉用主要原燃料不能正常供应,总的槽存量低于管理标准时,调度室应迅速查明情况,同时要求高炉做好应急准备,当情况继续恶化时,可参照下述原则进行处理。
(1)总的槽存量低于50%,高炉要高度警戒,做好应急准备;
(2)总的槽存量低于40%,高炉可减风10~30%;
(3)总的槽存量低于30%,高炉可减风50%,并做好休风准备。
4.3.3高炉休复风的配料
(1)24小时以内的计划休风,由高炉中心提出,安全生产技术部审核后,报经技术副厂长批准后执行。
(2)24小时以上的计划休风、停开炉、封炉及降料线等,由安全生产技术部与高炉中心共同提出,并制定详细的方案,会同各工艺主管工程师共同审核后,报经技术副厂长审核、批准后执行。
4.3.4特殊炉况、尤其是高炉的洗炉配料方案,由安全生产技术部和高炉中心共同议定,技术副厂长批准后执行。
4.3.5炉料的校正
高炉所用原燃料的质量及理化指标应力求稳定,但实际的运行过程中难免存在波动,高炉值班工长适应各种变化,及时调整,保证各操作参数的稳定。
4.3.5.1炉料校正的要求
(1)高炉值班工长在正常情况下,对焦炭负荷及炉渣碱度的校验每班不少于两次,每次变料均要依据原燃料成分进行校验后方可执行,并要经常地检查实际装料情况。
(2)当原燃料的理化性能有较大的波动或变化时,值班工长应据此及时调整(或校正)配料,以保证炉况稳定,并报告值班主任。
(3)变料时,值班工长要填写变料单,校对后交布料工进行变料,同时值班工长检查实际的装入情况。
4.3.5.2炉渣碱度的校正
下列因素变化,值班工长应调整配料以保持要求的炉渣碱度:
(1)焦炭和煤粉的灰分有显著变化,其波动值超过±1%时;
(2)入炉原料的SiO2、CaO、MgO、Al2O3有显著变化时;
(3)原燃料中的含硫量变化,引起入炉硫负荷显著变化时;
(4)较大幅度调整焦炭负荷时;
(5)原热制度稳定的情况下,造渣制度不能保证生铁质量时;
(6)炉温较高,短时间不能达到要求值、以及高炉发生崩悬料时,可临时加酸料。
4.3.5.3焦炭负荷的校正
下列因素变动时,值班工长应调剂焦炭负荷:
(1)入炉原料品位的变化,引起入炉综合品位波动超过±1%时;
(2)熟料比变化或不同性能的矿石相互替代时;
(3)原料的理化性能发生明显的变化时;
(4)焦炭和煤粉的灰分有显著变化,其波动值超过±1%时;
(5)焦炭的冷热态强度等理化性能显著变化时;
(6)焦炭的水分明显变化,超出自动补偿范围时;
(7)需变动风温或喷煤量时;
(8)铁水温度偏离正常的管理基准,短时间没有恢复的条件时;
(9)需要调整生铁含硅量时;
(10)采用发展边缘的装料制度或有引起边缘发展的因素时;
(11)冶炼强度(或料速)有较大变动时;
(12)炉顶布料溜槽有故障,被迫维持到休风处理的一段时间要酌情减轻焦炭负荷;
(13)下列情况下允许加净焦:
a.炉凉、发生连续崩料或坐料时;
b.低料线时间过长且料线过深时;
c.炉凉严重,采取其他措施不能迅速恢复到正常炉温时;
d.长期休风前后;
e.临时停止喷吹物时;
f.出现上料错误时。
4.3.5.4净焦的加入方法和权限
(1)通过加净焦指令按钮加,每按一次即可随即加净焦一批;
(2)通过计算机配料程序加,在该程序上输入需要加入的净焦量和起始的批号,即可按要求连续加入;
(3)超过5批净焦的要经技术副厂长同意。
4.4高炉装料管理
4.4.1高炉的基本装料制度由安全生产技术部和高炉中心共同议定,并报技术副厂长批准,且不能轻易改动。
4.4.2值班工长每班到槽下对电子称称量情况检查一次,称量工经常检查核对电子称零点。
各电子称允许的称量误差:
焦炭≯3%,矿石≯3%。
4.4.3原燃料的筛分
(1)筛网规格的设定
槽下所有的筛网尺寸需经安全生产技术部决定,并报生产(或技术)副厂长批准。
(2)装入粉率的管理
管理目标值
管理方法
烧结矿
-5mm<3%
根据取样(1次/天)结果
判断、调整筛网的给料速度
焦炭
-15mm<2%
(3)筛网的t/h值管理
t/h值表示筛网的给料速度。
各班测定一次筛上给矿量、记录在“筛网给矿量管理表”内。
测定要领
称量开始后,测定3~5t的给料时间,称出给矿量。
t/h=