机械毕业设计1611硬质合金超声复合电加工设计及试验论文.docx
《机械毕业设计1611硬质合金超声复合电加工设计及试验论文.docx》由会员分享,可在线阅读,更多相关《机械毕业设计1611硬质合金超声复合电加工设计及试验论文.docx(37页珍藏版)》请在冰豆网上搜索。
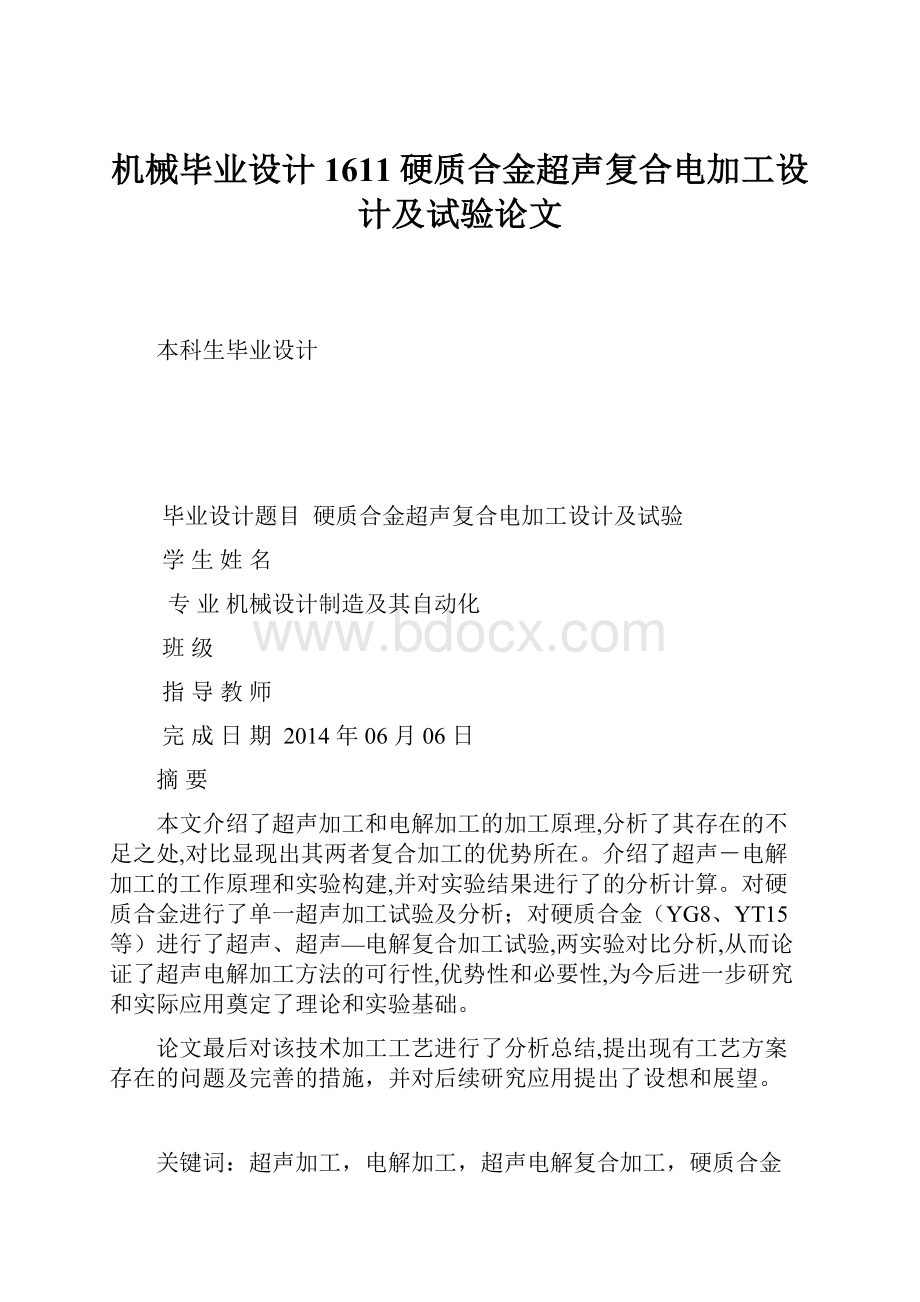
机械毕业设计1611硬质合金超声复合电加工设计及试验论文
本科生毕业设计
毕业设计题目硬质合金超声复合电加工设计及试验
学生姓名
专业机械设计制造及其自动化
班级
指导教师
完成日期2014年06月06日
摘要
本文介绍了超声加工和电解加工的加工原理,分析了其存在的不足之处,对比显现出其两者复合加工的优势所在。
介绍了超声-电解加工的工作原理和实验构建,并对实验结果进行了的分析计算。
对硬质合金进行了单一超声加工试验及分析;对硬质合金(YG8、YT15等)进行了超声、超声—电解复合加工试验,两实验对比分析,从而论证了超声电解加工方法的可行性,优势性和必要性,为今后进一步研究和实际应用奠定了理论和实验基础。
论文最后对该技术加工工艺进行了分析总结,提出现有工艺方案存在的问题及完善的措施,并对后续研究应用提出了设想和展望。
关键词:
超声加工,电解加工,超声电解复合加工,硬质合金
Abstract
Thispaperintroducestheprinciplesofultrasonicmachiningandelectrochemicalmachining.Andanalyzetheexistenceoftheinadequacies,ContrasttothetwotoshowstheadvantagesoftheCompositeprocessing,Focusesontheultrasound-theworkingprincipleofelectrolyticprocessingandlaboratoryequipment.Improvedthecathodeandtheworkpiecebetweenthemicro-pressureregulatordevices,horndesignandproduction,theworkoftheeffectivesupplyofliquidmethodofprecisionmicro-positioningdevicemethods,processesandprocessingparametersdetectionshowthattheaccuracyofmeasurementtechnologylink,inordertotestResearchconditionsprovidethebasis
Finally,Thepaperhascarriedontheanalysissummarytothistechnicalprocessingcraft,proposedthattheexistingcraftplanexistence'squestionandtheconsummationmeasures,andproposedtothefollowingresearchapplicationconceivesandforecasts
Keywords:
Ultrasonicmachining,Electrochemicalmachining,Ultrasound-ECMmachining,Hardmetal
摘要………………………………………………………………………1
Abstract……………………………………………………………………2
目录………………………………………………………………………3
第1章绪论……………………………………………………………5
1.1特种加工技术概述…………………………………………………………5
1.2硬质合金的特性……………………………………………………………6
1.3课题研究目的及内容………………………………………………………6
第二章超声加工和电解加工………………………………………………………7
2.1超声加工原理及特点…………………………………………………72.2电解加工原理及特点……………………………………………………8
2.3超声电解复合加工原理…………………………………………………10
2.4本章小结…………………………………………………………………13
第三章超声电解复合加工试验系统构建………………………………………14
3.1复合加工机理……………………………………………………………14
3.2复合加工技术优势………………………………………………………15
3.3构建实验系统……………………………………………………………16
3.4变幅杆设计与制作………………………………………………………18
3.5极工具头设计……………………………………………………………20
3.6工艺试验…………………………………………………………………22
3.6.1试验材料…………………………………………………………22
3.6.2工具阴极及变幅杆………………………………………………22
3.6.3超声磨料…………………………………………………………22
3.6.4电解液……………………………………………………………23
3.6.5加工电参数……………………………………………………23
3.6.6.超声功率¡¡¡¡…………………………………………23
3.6.7.超声频率……………………………………………………23
3.6.8试验步骤……………………………………………………24
3.6.9硬质合金的单一超声加工…………………………………24
3.6.10硬质合金YT15超声复合电解加工试验¡¡¡¡¡¡¡26
3.6.11硬质合金YG8超声复合电解加工试验¡¡¡¡¡¡¡¡28
3.6.13本章小结¡¡¡¡¡¡¡¡¡¡¡¡¡¡¡¡¡¡¡¡32
第四章总结与展望¡¡¡¡¡¡¡¡¡¡¡¡¡¡¡¡¡¡¡¡33
致谢¡¡¡¡¡¡¡¡¡¡¡¡¡¡¡¡¡¡¡¡¡¡¡¡¡¡¡34
参考文献¡¡¡¡¡¡¡¡¡¡¡¡¡¡¡¡¡¡¡¡¡¡¡¡¡¡¡35
第一章
1.1特种加工技术概述
制造技术历史悠久,是人类生存与发展的基础及社会物质财富的主要来源,对人类的生产和物质文明起着极大的作用。
18世纪70年代,英国发明了蒸汽机,由于当时还不能制造高精度的气缸,而迟迟不能转化为生产力。
直至气缸镗床的出现,这一发明才得以广泛应用,从而导致第一次产业革命。
不言而喻,新产品的研究开发,科学技术和社会经济文化的发展,无不与制造技术息息相关。
然而,以后的近200年,人们一直是采用传统加工方法,并利用机械能和切削力来切除工件金属而达到制造要求的。
起加工实质是“以硬对软”。
本世纪40年代,前苏联曾发明电火花加工。
人们初次脱离了传统加工的旧轨道,利用电能、热能,在不产生切削力的情况下,以低于工件金属硬度的工具去移除工件上多余的部位,成功地获得了“以柔克刚”的技术效果。
自本世纪50年代以来,特别是近一二十年,由于材料科学、高新技术的发展和激烈的市场竞争、发展尖端国防及科学研究的急需,不仅新产品更新换代日益加快,而且产品要求具有很高的强度重量比和性能价格比,并正在朝着高速度、高精度、高可靠性、耐腐蚀、高温高压、大功率、尺寸大小两极分化的方向发展。
为此,各种新材料、新结构、形状复杂的精密机械零件大量涌现、,对机械制造业提出了一系列迫切需要解决的新问题。
例如,各种难切削材料的加工;各种形状复杂、尺寸或微小或特大、精密零件的加工;薄壁、弹性元件等低刚度、特殊零件的加工等。
对此,采用传统的加工方法十分困难,甚至无法加工。
于是,人们一方面通过研究高效加工的刀具和刀具材料、自动优化切削参数、提高刀具可靠性和在线刀具监控系统、开发新型切削液、研制新型自动机床等各种途径,进一步改善切削状态、提高切削加工水平,并解决了一些问题;另一方面,则冲破传统加工方法的束缚,不断地探索寻求心的加工方法,于是一种本质上区别于传统加工的特种加工变应运而生。
后来,由于新颖制造技术的进一步发展,人们从广义上来定义特种加工,即将电磁声光化学等能量或其组合施加在工件的被加工部位上,从而实现材料被去除、变形、改变性能或被镀覆的非传统加工方法统称为特种加工(NTM,Non-TraditionalMachining)。
它是一种涉及多学科、学科交叉融合的先进制造技术,具有才传统加工所无可比拟的特点[1]。
.1.2硬质合金的特性
硬质合金是由硬度很高的难熔金属碳化物(WC、TiC、TaC和NbC等)和金属粘结剂(c0、Ni、Mo)用粉末冶金的方法制成的材料,硬质合金中的碳化物都具有硬度高、熔点高、化学稳定性和热稳定性好等特点。
采取普通的切削加工方法来加工硬质合金材料简直是无法想象的。
有关资料表明,超声加工对于玻璃、陶瓷等非金属脆性材料具有很高的加工精度和加工效率,加工表面的表面质量也很好,但用来加工硬质合金材料,其加工效率较低,加工工具局部损耗较大等缺陷。
所以对于硬质合金材料基本不采用超声加工方法,通常仍以电解加工或电火花加工的方法进行零件或模具加工。
电解加工适合于包括硬质合金的大多数金属材料的成形加工,可获得较高的加工速度,较好的表面粗糙度(Ra=0.16—1.25m),但与超声加工所得到的表面粗糙度(Ra=0.1—1m)相比要差些。
显然,采用超声加工、电解加工的方法来加工硬质合金具有各自的优点和缺点。
将两种加工方法进行适当的结合,即采用超声电解复合加工的方法,既保证电解加工的高效性,得到很高的加工速度,又保持了超声加工的较好加工精度和表面粗糙度。
1.3课题研究目的及内容.
随着科学技术的发展,具有三维型面的难加工材料的应用越来越广泛,普通的机械加工难以满足要求,而超声波加工不仅能加工硬质合金、淬火钢、陶瓷、半导体锗和硅片等硬脆材料,电解加工具有效率高、电极无损耗,表面质量好等优点,特别适用于导电性难加工材料的三维型面加工。
超声加工结合电化学加工,利用超声作用对电解加工过程的改善,可以提高超声加工的效率,减小电极损耗,提高电解加工的精度,具有技术复合综合技术优势。
本课题本课题探讨硬质合金材料超声加工特性,并进行超声加工工具及工艺设计,进行超声参数试验及优化,为其实际应用建立工艺基础。
第二章超声加工和电解加工
2.1超声加工的原理及特点
2.1.1超声加工的基本原理
超声加工是利用工具端面作超声频振动,通过磨料悬浮液加工硬脆材料的一种特种加工方法,超声加工的基本原理如图1-2所示。
超声加工时,在工具1和工件2之间加入水(或油等)和磨料混合的悬浮液3,并使工具以适当的压力F轻轻压在工件上。
超声换能器6产生高达16000Hz以上的超声频率作纵向振动,由于弹性杆(弹性杆使振幅产生一定的放大变化,通常称其为变幅杆)的作用,振幅被放大到0.05~0.1mm左右,驱动工具端面作超声振动,迫使工作液中悬浮磨料的磨粒以很大的速度和加速度不断地撞击、抛磨被加工工件表面,把被加工工件表面的材料粉碎成很细的微小颗粒,从工件上被打击下来。
虽然每一次打击下来的材料很少,但每秒打击的次数高达16000次(与超声频率有关)以上,所以仍有一定的加工速度。
1-工具2—工件3—磨料悬浮液
4、5—变幅杆6—换能器7—超声波发生器
图2.1超声加工原理图
与此同时,工作液受工具端面超声振动作用而产生的高频、交变的液压正负冲击波和“空化”作用,迫使工作液“钻”入被加工材料的微细缝隙处,从而更加剧了机械破坏作用。
所谓“空化”作用,是指当工具端面以很大的加速度离开工件表面时,加工间隙内形成较大的负压和局部真空,使得工作液内瞬间形成很多微空腔,当工具端面以很大的加速度接近工件表面时,空泡又重新闭合,又引起较强的液压冲击波,上述作用迅速地、反复地施加在工具与工件之间微小间隙内的工作液里,可以大大强化加工过程。
此外,正负交变的液压冲击也使悬浮工作液在加工间隙中强迫循环,带动磨料运动,使部分变钝了的磨粒及时得到更新。
由此可见,超声加工是磨粒在超声振动作用下的机械撞击和抛磨作用以及超声空化作用的综合结果,其中,磨粒的机械撞击作用是占主导地位的。
本质上,材料去除的能量是机械能。
由于超声加工基于局部撞击作用,所以当受到撞击作用时,越是硬脆的材料,其受破坏的程度越大,越容易进行超声加工。
相反,脆性和硬度不大的韧性材料,由于它对撞击能量的吸收、缓冲作用而难以实施超声加工,或者说加工效果很不理想。
所以,这一性质常利用在工具材料选择上,要求它既能撞击磨粒,又不至于使自身受到很大的破坏,一般选择塑性较好的材料,通常采用45钢或弹簧钢等材料作为工具材料较合适。
2.1.2超声加工的基本特点
1.超声加工适合于加工各种硬脆材料,特别是不导电的非金属材料,例如玻璃、陶瓷(氧化铝、氮化硅等)、石英、锗、硅、石墨、玛瑙、宝石、金刚石等材料。
在理论上,对于导电的硬脆金属材料如淬火钢、硬质合金等,也能进行加工,但加工效率较低。
2.由于工具的运动轨迹通常为直线,工具可用相对较软的材料制造且可以制成较复杂的形状,可以加工具有异型截面的形状、具有阶梯的通孔、盲孔等;不需要使工具和工件作比较复杂的相对运动,在一般情况下,超声加工机床的结构比较简单,操作、维修都很方便。
3.由于去除加工材料是靠粒度极微小的磨料瞬时、局部的撞击作用以及超声空化作用,所以工件表面的宏观切削力很小,切削应力、切削热很小(即使产生很小的切削热也会被磨料悬浮液及时带走),不会引起变形及烧伤,因而零件的表面粗糙度较好,一般可达Ra(1~0.1)μm,加工精度达到(0.01~0.02)mm,而且可以加工薄壁、窄缝、低刚度的零件[3-4]。
超声加工的局限性:
1超声加工面积较大时,超声加工效率有明显的降低;其次超声加工很难加工韧性较大金属材料(工具钢、硬质合金等);
2超声加工圆柱形孔深度一般以工具直径的5倍为限,对于深径比较大的深小孔加工很困难
3超声加工工具在磨料的抛磨下有损耗,同时,磨粒使工具与工件之间存在间隙,因此,精加工时要考虑工具损耗及磨粒直径大小对加工精度的影响,工具设计中应给予合理补偿。
2.2电解加工原理及特点
2.2.1加工原理
1—直流电源2—工具阴极3—工件阳极
4—电解液泵5—电解液图
图2.3电解加工示意图
电解加工是利用金属在电解液中发生电化学阳极溶解的原理将工件加工成形的一种特种加工方法。
如图2.3所示,加工时,工件接直流电源(一般为10-24V)的正极,工具接负极,两极之间保持较小的间隙(一般在0.1-1mm范围内)。
电解液从极间间隙中流过(6-30m/s),使两极之间形成导电通路,并在电源电压下产生电流,从而形成电化学阳极溶解。
随着工具相对工件不断进给,工件金属不断被电解,电解产物不断被电解液冲走,最终两极间各处的间隙趋于一致,工件表面形成与工具工作面基本相似的形状。
a.加工开始 b.加工过程c.加工终止
图2.4加工示意图
2.2.2加工特点:
(1)加工范围广。
常用于加工硬质合金、高温合金、淬火钢、不锈钢等难加工材料。
(2)生产率高,且加工生产率不直接受加工精度和表面粗糙度的限制。
电解加工能以简单的直线进给运动一次加工出复杂的型腔、型面和型孔,而且加工速度可以和电流密度成比例地增加。
据统计,电解加工的生产率约为电火花加工的5至10倍,在某些情况下,甚至可以超过机械切削加工。
(3)加工质量好。
可获得一定的加工精度和较低的表面粗糙度。
(4)可用于加工薄壁和易变形零件。
电解加工工具和工件不接触,不存在切
削力,不产生残余应力、变形、毛刺。
(5)工具阴极无损耗。
在电解加工过程中工具阴极上仅仅析出氢气,而不发生溶解反应,所以没有损耗。
(6)易与机械加工及其他特种加工方法相结合形成复合加工,如电解磨削、电解抛光、超声电解等。
另外,电解加工也具有一定的局限性,主要表现为:
(1)不容易达到较高的加工精度和加工稳定性。
这一方面是由于阴极的设计、制造和修正都比较困难,阴极本身还存在制造精度问题;另一方面是影响电解加工间隙稳定性的参数很多,控制比较困难。
(2)电解加工的附属设备较多,占地面积较大,机床需要有足够的刚度和防腐蚀性能,造价较高,因此单件小批量生产时的成本比较高。
(3)电解加工产物需要进行妥善处理,否则将污染环境。
综上所述,电解加工工艺具有表面无变质层、无残余应力、表面粗糙度小、加工成本较低、加工效率高等优点,这些特点是其它特种加工方式所不全具备的。
因此电解加工在机理上存在能实现精密加工,甚至是nm级加工的可能性,因此发掘其机理优势,将其应用于MEMS器件微细加工,是很有研究前景的课题。
与传统电解加工相比,电解加工除拥有上述特点外还有自身的工艺特点,如电解液的浓度低、加工电压低、阴阳极间的间隙小、加工零件尺寸小、精度要求高等。
为了克服以上缺陷,复合加工应运而生,显示了其性能优越性和加工稳定性。
2.3.超声—电解复合加工
随着经济的发展,现有的特种加工方法已经不能满足社会发展的要求,复合加工应运而生,在很好的解决常规特种加工方法缺陷的同时很好的确保了其优越性和高效性,同时也扩大了材料加工范围,大大提高了特种加工技术加工效率和加工精度.
复合加工应用多种形式能量的综合作用来实现对工件材料的去除和加工,其中包括传统加工和特种加工的复合、特种加工与特种加工的复合,实现不同加工技术的优势互补,扬长避短,大大提高了加工效率和加工精度。
图2.5复合加工实验设备
2.3.1加工原理
超声电解复合加工的基本构思就是,将超声加工和电解加工两种工艺结合在一起。
复合加工的工作液是采用带有悬浮磨料的钝化性电解液,首先由电解加工在工件待加工表面形成钝化膜,阻止金属继续溶解,继而利用磨粒在超声振动作用下的机械撞击和抛磨,来去除工件表面对应于工具阴极部分的钝化膜,该处裸露的金属层恢复活化,继续溶解,又形成新的钝化膜层。
上述过程周而复始,反复进行,在能够控制加工输入微能量变化的前提下,期望能有效地改善电解的定域性,提高总体加工精度。
超声空化作用还能改善极间状态,加强产物排除。
1.变幅杆2.电极3.电解液4.工件5.电源
图2.6超声—电解复合加工示意图
超声-电解复合加工过程中,工件接直流电源正极,工具接阴极,其加工的原理是,阳极的工件因电解作用,加工表面产生致密的电解产物,从而减小了电解作用,甚至形成钝化膜,阻止电解加工进一步进行。
此时,加工液中的磨粒因超声波的作用而作高频的抛磨作用,破坏加工区域的电解产物,并在超声振动及空化作用下由工作液带走,此时,工件表面金属再次显露出来,电解作用继续进行,两过程交替进行,如此循环,从而完成加工过程。
2.3.2加工特点
相对于单一的超声微细加工及电解微细加工,超声—电解复合微细加工的技术优势主要有以下几个方面:
1.高频振动冲击波及“负压空化”作用能有效、及时地去除加工料去除量以钝化膜层为单位(μm或亚μm级[34]),机理上可保证加工过程中钝化膜产生和去除的协调配合,解决电解微细加工过程难以持续的问题,使其实用成为可能。
2.电解微细加工采用钝化性电解液,如浓度1%—5%的NaNO3,电解钝化膜能控制在局部进行有选择地电解蚀除,提高电解加工的定域性;当电解液浓度降低时,效率曲线(如图2.7所示)将会右移,切断间隙将减小,即只有在很小间隙时,钝化膜才能被破坏,这时的电场、流场变化对加工精度的不良影响将变得很小,杂散腐蚀现象可以完全避免,从而获得所需的形状和尺寸。
3.超声—电解复合微细加工中,超声作用需去除的是电解钝化膜,磨料粒度可以更微细,可使用nm级微粉(甚至无磨料加工),从而可最大限度地减小超声加工工具损耗,大幅度提高微细加工精度,减小粗糙度。
另外低浓度钝化性电解液,不具污染性,且在超声频振动、微电流电解作用时采用“静态”供液即可,无需常规电解加工的电解液循环系统,便于实现低成本及清洁、绿色制造。
图2.7效率曲线
4.超声电解复合微细加工方式的材料去除是以钝化膜层为单位(亚¦Ìm级),电解钝化与超声作用消除交替进行,机理上可保证加工过程中钝化膜产生和去除的协调配合,解决电解微细加工过程难以持续的问题,使其实用成为可能。
因此超声—电解复合微细加工工艺在机理上能够保持两种特种加工方法的优点,可提高加工精度,具有独特的优越性。
超声电解加工在确保加工精度的同时,大副提高了加工速度,有效提高加工精度.然而,但是该项技术仍不成熟,仍然存在一些缺陷等待解决如电流密度较大时加工杂散腐蚀现象(从某外电源漏散电流而引起的金属腐蚀)。
当杂散电流在金属构件的某一表面区域离开金属(电子导体相)而进入介质(离子导体相)时,对于金属构件的这一区域来说,是阳极电流,故加速金属的阳极溶解,造成由杂散电流而引起的“腐蚀”破坏。
)严重,采取超高频脉冲电源、混气加工或复合电解液等措施,虽可得到一定程度改善,但还需要进一步探索。
综上所述,超声—电解复合微细加工可保持电解加工高效率、阴极损耗小的优点,同时超声振动、脉冲电流又可以改善电解加工过程,具有复合技术优势,能够满足微细加工的要求,具有进一步研究和应用的前景。
2.4本章小结
本章分析了超声电解以及超声电解复合加工的原理和特点,探讨超声电解加工可行性与技术优势,为试验系统构建建立了基础。
第三章超声电解复合加工实验构建
微细加工材料需要的去除量微小,加工精度要求很高,为了避免大电流密度的杂散腐蚀作用,电解作用须在低电位、微电流密度下进行,即处于效率曲线的钝化区,并且不能采用活性大但杂散腐蚀严重的NaCl电解液,这样,用单一电解方式加工时,材料开始虽可以电解,但随着加工过程的继续,工件阳极超电位升高,加工进入钝化区,工件表面产生低电流密度难以破坏的钝化膜,阻止电解作用的持续进行,这就使单一电解方式在微细加工中的应用受到限制。
至于超声加工技术,比较适合于加工硬脆材料,特别是陶瓷材料,表面粗糙度较低,尺寸精度较高,并且不存在残余应力,不改变组织结构;但缺点是超声加工工具有损耗,加工效率较低,且在材料面积、韧性较大时,效率显著降低,应用受到限制。
可见,单独使用电解或超声波加工方法加工硬脆材料都不是最好的方法。
初步研究分析证明,将超声频振动加工工艺和脉冲电流电解加工工艺有机复合,扬长避短,可发展成为MEMS各种材料微器件加工的一种全新工艺。
3.1复合加工机理
.
1.换能器2.变幅杆3.电解液和磨料4.工件5.直流电源6.工具7.超声发生器
图3.1超声电解复合加工原理图
超声电解复合微细加工是加工硬脆材料的新工艺,是将超声频振动加工、脉冲电流及电解加工技术等多种工艺有机复合在一起的一种加工方法。
加工原理如图3.1,换能器6将超声波发生器输出的高频电信号转变为机械振动能,通过变幅连接件使工具端面作小振幅超声高频振动,工具头1和工件2分别接脉冲电解电源的负极和正极,加工区充满磨料+电解液组成的复合工作液,在超声和脉冲电解双重作用