第一章 泵二次修改.docx
《第一章 泵二次修改.docx》由会员分享,可在线阅读,更多相关《第一章 泵二次修改.docx(117页珍藏版)》请在冰豆网上搜索。
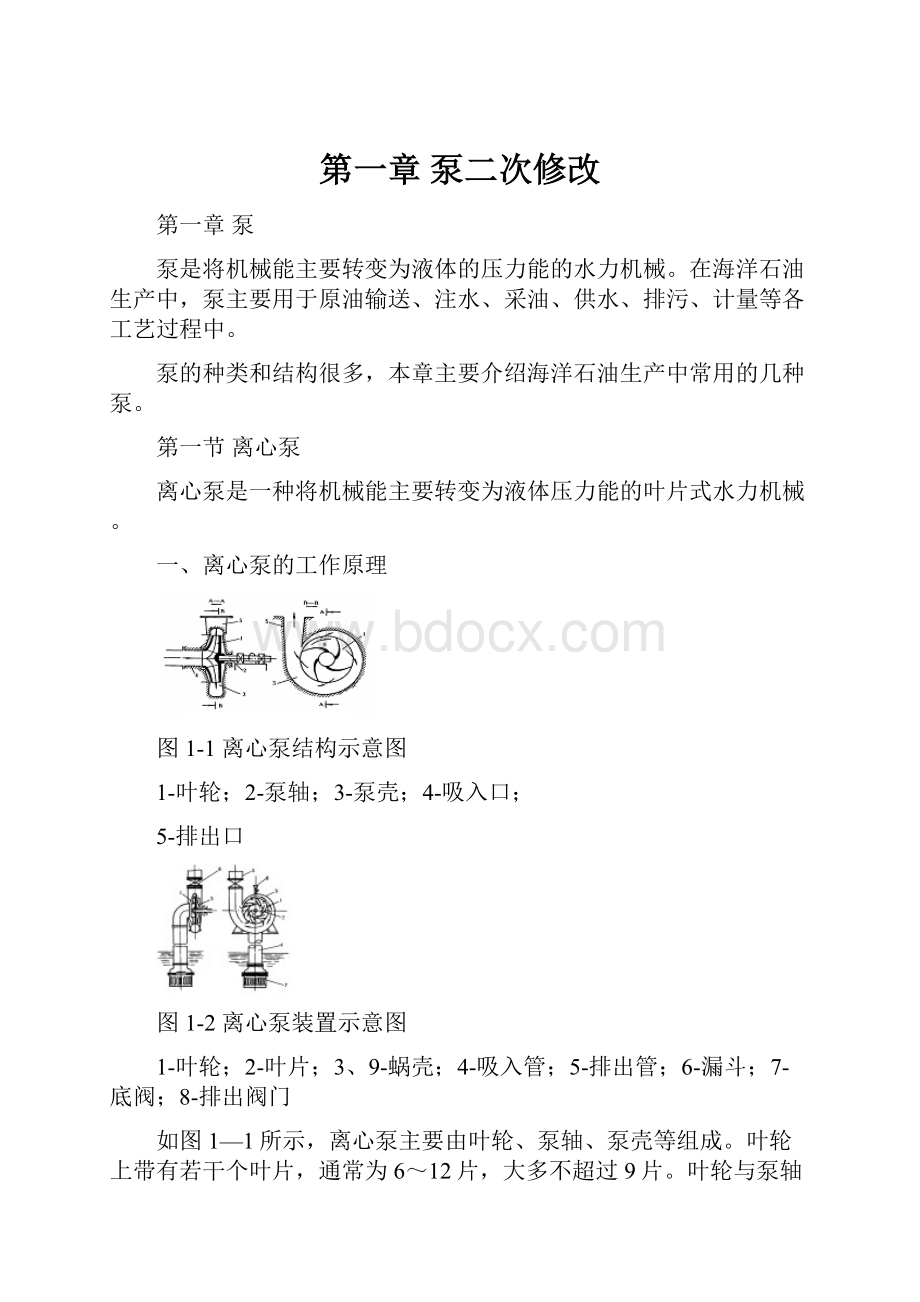
第一章泵二次修改
第一章泵
泵是将机械能主要转变为液体的压力能的水力机械。
在海洋石油生产中,泵主要用于原油输送、注水、采油、供水、排污、计量等各工艺过程中。
泵的种类和结构很多,本章主要介绍海洋石油生产中常用的几种泵。
第一节离心泵
离心泵是一种将机械能主要转变为液体压力能的叶片式水力机械。
一、离心泵的工作原理
图1-1离心泵结构示意图
1-叶轮;2-泵轴;3-泵壳;4-吸入口;
5-排出口
图1-2离心泵装置示意图
1-叶轮;2-叶片;3、9-蜗壳;4-吸入管;5-排出管;6-漏斗;7-底阀;8-排出阀门
如图1—1所示,离心泵主要由叶轮、泵轴、泵壳等组成。
叶轮上带有若干个叶片,通常为6~12片,大多不超过9片。
叶轮与泵轴固装在一起,动力机通过联轴器带动泵轴旋转,从而带动叶轮一起旋转。
其工作原理是:
液体首先被灌满泵壳和叶轮内,动力机通过泵轴带动叶轮旋转时,叶片就带动叶片间流道中的液体作圆周运动,液体在离心力的作用下,以较大的速度和较高的压力,沿着叶片间的流道,从叶轮中心向外缘运动,并通过蜗壳和扩散管流向排出管。
由于液体不断被排出,在泵壳内叶轮中心和吸入管内形成真空,吸入池中的液体在大气压或液罐内压力的作用下,源源不断地流进吸入管和叶轮中心,然后又在离心力的作用下被甩出,从而使泵形成连续的吸入和排出过程,不断地排出高能量的液体。
蜗壳则收集从叶轮中高速流出并具有一定压力的液体,并引向扩散管和排出管;扩散管的过流断面是逐渐增大的,起着降低液体流速和进一步增加液体压力的作用。
要使离心泵正常工作,必须将离心泵与吸入管汇和排出管汇等共同组成如图1—2所示的泵装置。
吸入管的下部安装有滤网和底阀,对液体起过滤作用,并防止管中液体倒流进吸入池。
排出口处安装有阀门,用于调节流量。
蜗壳的顶部一般有灌注口,用于在启动泵之前向泵内灌液以排除泵腔内的气体,或由专用的真空泵抽吸泵腔内的气体。
启动泵之前要关闭排出阀门,启动后再逐渐打开。
二、离心泵的类型
(一)离心泵的种类
离心泵的种类很多,有各种分类方法。
1.按泵轴布置方式分主要有:
(1)卧式泵泵轴为水平布置。
(2)立式泵泵轴为垂直布置。
2.按吸入方式分有:
(1)单吸泵叶轮从一个方向吸入液体。
(2)双吸泵叶轮从两个方向吸入液体。
3.按叶轮级数分可分为:
(1)单级泵泵轮上只安装一个叶轮。
(2)多级泵泵轴上安装两个或两个以上的叶轮。
4.按泵体的形式分可分为:
(1)蜗壳泵叶轮排出一侧具有蜗形室的壳体。
(2)透平泵带导叶的多级泵。
5.按壳体剖分方式分可分为:
(1)分段式泵泵的壳体按照与泵轴垂直的平面剖分
(2)中剖式泵壳体在通过轴心线的平面上分开。
6.按用途分可分为:
清水泵、油泵、污水泵、砂泵、酸泵、碱泵等。
此外,离心泵还可以按叶片安装方式、压力大小及比转数等进行分类。
(二)离心泵的名称代号
型号代号通常有首、中、尾三部分。
首部是数字,表示泵的主要尺寸规格,一般为泵的吸入口直径,单位为mm或in;中部则用汉语拼音字母表示泵的型式或特征;尾部一般用数字表示泵的参数。
对于具体的泵,往往根据其主要的特点,按照汉语拼音字母等编制型号代号。
国内离心泵的型号表示方法不完全统一,但都包括表示型式的字母及表示有关尺寸和参数的数字两部分。
1.字母表示泵的型式。
部分表示泵型的字母的含义介绍如下:
(1)BA单吸、单级悬臂式泵。
(2)SH单级双吸泵。
(3)DA单吸、多级、低速分段式泵。
(4)DE单吸、多级、分段式泵。
(5)D分段、多级、高转速泵。
(6)DG分段、多级、高压泵。
(7)GC锅炉给水泵。
(8)FDJ单吸、多级油泵。
(9)FDR单吸、多级热油泵。
(10)Y单吸油泵。
(11)GY高压多级油泵。
(12)FSR双吸、多级热油泵。
(13)YS双吸油泵。
(14)J单级常温油泵。
(15)DR单级热油泵。
2.数字主要有以下几种组合方式。
(1)吸入口的直径—比转数×级数如4BA—6,10Sh—19,8DA—8×9等离心泵,字母前的数字是吸入口直径(mm)除以25所得的数值,其单位为英寸;字母后第一组数表示泵的比转数除以10所得的数值;第二组数表示泵的级数,即叶轮数,无数字为单级泵。
(2)吸入口直径—扬程×级数如150D—170×11,100Y-120×2等泵,字母前的数字为泵吸入口直径(mm);字母后第一组数为单级叶轮的扬程(mm),第二组数为泵的叶轮级数。
如;
(3)流量—扬程X级数如D250—150×11,DG270—140×10泵等,字母后面第一组数字表n<泵的流量(m3/h);第二组数字表示单级叶轮的扬程(m);第三组数字为叶轮的级数。
(4)吸入口的直径—泵的流量—压力如6D80—120,6D100—150和4D50—200泵等,字母前的数字为吸入口直径(mm)除以25所得的商;字母后第一组数字为泵的流量(m3/h);第二组数字为泵的压力(0.1MPa),亦即泵的扬程(m)除以10所得的商。
由于离心泵的种类很多,其代号亦未完全统一,表示方法亦不尽相同。
因此,对于具体的泵应具体分析。
三、离心泵的应用
离心泵在海洋石油生产中的应用见表1-1。
表1-1绥中36-1油田A平台所用离心泵
离心泵的名称及型号
用途
开排泵WYPR40-125
将开式排放罐收集的液体打到闭式排放罐中。
闭排泵1½DCH-5×7
将存于闭式排放罐内的含油液体打进工艺流程。
热介质循环泵R454
将贮存罐内的可重复使用的热介质油,泵入到膨胀罐内,不能使用的打入甲板上的排放罐。
淡水泵CISR50-200A
将贮存在淡水罐内的淡水输至各个用户。
海水提升泵QJH
将海水提升至平台,为公用系统供应杂用水。
原油外输泵411DA-10tage
将含水原油增压后通过海底管线输往陆上终端。
油污泵ILWY40-125
将生产污水增压后送入核桃壳过滤器。
反冲洗泵
将净水缓冲罐中的水送入反冲洗水缓冲罐中。
反冲洗水返回泵
将反冲洗水缓冲罐中的水打回生产污水处理系统。
注水泵DH118-122X10
向井底注水。
四、典型离心泵的整体结构和零部件
(一)离心泵的主要零部件
离心泵的主要零部件有叶轮、泵壳、泵轴、密封装置、轴承等。
1234
图1-3离心泵叶轮形式
1-闭式叶轮;2-半开式叶轮;3-开式叶轮;4-双吸叶轮
1.叶轮
离心泵的叶轮是使液体产生离心力并获得能量的主要部件。
如图1—3所示,叶轮形式有闭式、半开式、开式和双吸叶轮四种,通常为铸造件。
闭式叶轮由前盖板、后盖板、叶片及轮毂等组成;液体一般从内孔直径较大的一端,沿轴向吸入,从内孔直径较小的一端,沿径向排出。
半开式叶轮无前盖板,开式叶轮无前、后盖板。
双吸叶轮相当于两个闭式叶轮叠加在一起,液体可从两个方向吸入。
有两叶轮中的叶片有圆柱形(单向弯曲)和扭曲形(双向弯曲)之分。
闭式叶轮的平面投影如图1—4所示。
叶轮流道面积要求变化均匀,流道中心是内切圆心的连线。
图1-4闭式叶轮平面图
图1-5多级离心泵转子装配图
2.泵轴
泵轴是传递功率和力矩的主要零件。
悬臂泵的泵轴的一端安装叶轮,另一端安装用轴承安装在托架上;中小型多级泵一般采用光轴,各级叶轮滑配在轴上,用短键传力,大型多级泵一般采用阶梯轴,各级叶轮用热套法安装在轴上。
泵轴与叶轮等组装在一起后,用锁紧螺母固定,成为高速旋转的转子,在泵总装前要进行小装即部件装配,并检查转子各部位的径向跳动,如果跳动过大,泵在运行中容易产生振动和偏磨,应该设法消除。
对于分段式多级泵,需要对转子部件作小装检查;对于悬臂泵,需要对托架部件作小装检查.图1—5和图1—6
图1-6悬臂泵转子装配图
是泵轴小装的装配图。
3.泵壳
泵壳是离心泵中收集液体并把液体导出的零件,铸造而成。
泵壳一般有涡壳形和圆柱形两种结构形式。
泵壳一般由有吸入管、吸入室、壳体、压出室、排出管等部分组成。
吸入室的作用是将吸入管中的液体均匀地吸入叶轮,力求流动损失最少。
吸入室有3种:
锥形吸入室、环形吸入室和螺旋形吸入室。
(1)锥形吸入室如图1—7所示。
其末端圆滑地过渡到叶轮入口直径处,锥度70~180。
它能在叶轮入口前产生不大的液流加速度,使叶轮前流速均匀,流动损失很小。
小型单吸单级悬臂式离心泵多采用此种结构。
(2)环形吸入室如图1—8所示。
其吸入流道过流面积逐渐缩小,圆环液流速度略小于叶轮入口速度,以保证液流进入叶轮时有一个不大的加速度。
这种吸入室的结构简单,轴向尺寸短,但液体进入叶轮时有冲击和漩流损失,常用在单吸分段式多级离心泵中。
(3)螺旋形吸入室如图1—9所示。
其优点是液体进入叶轮时流动情况较好,速度比较均匀,但液体进入叶轮前有预旋,对比转数较大的泵,扬程损失比较明显。
双吸单级泵和水平中剖式多级泵,一般采用此种结构。
图1-7锥形吸入室图1-8圆柱形吸入室图1-9螺旋形吸入定室
压出室的作用是以最小的损失将从叶轮中流出的高速液体收集起来,引向出口,同时将一部分液体的动能转变为压能。
有两种形式:
(1)环形压出室如图1—10所示。
流道各处有相等的横断面积,主要用于分段式多级离心泵的排出段(后段),或输送杂质的泵(如砂泵、泥浆泵、灰渣泵、注水泵等)。
焊接结构的泵体通常也采用环形压出室,以便简化工艺。
由于各处断面积相等,环形室中的流速并不相等,故存在冲击损失,使泵的效率降低。
(2)螺旋形压出室(蜗壳)如图1—11所示。
一般用于单级双吸泵或水平中剖式多级泵中。
主要优点是制造比较方便,泵性能曲线的高效区域比较宽广,缺点是在非设计工况下运转时,产生不平衡的径向力。
设计螺旋蜗室时,通常以液体在蜗室中作等速运动,并从叶轮中均匀流出为基本条件。
螺旋形压出室中的蜗室只起收集液体的作用,在扩散管中才将液体的部分动能转化为液体的压能。
图1-12径向导叶
图1-10环形压出室图1-11螺旋形压出室
1-导叶片;2-叶轮;3-导叶;4-泄水管
4.导叶
图1-13叶轮与泵体间的间隙
分段式多级离心泵都安装有导叶,其作用是收集由叶轮流出的高速液流,将一部分液动能转换成液压能,并引导液流均匀地进入下一个叶轮或压出室。
导叶有流道式和径向式两种,分段式多级离心泵多采用径向导叶,其结构如图1—12所示。
导叶由正导叶、环形导叶过渡区和反导叶组成。
正导叶(A—B段)内螺旋线部分用于保证液体作自由等速运动,扩散部分(B—C段)则用于将大部分动能转换成压能,过渡区(C—D段)用于变换液流方向,反导叶(D—E段)的作用是消除速度环量,把液体均匀地引向下一级叶轮。
实际上,导叶相当于安排在叶轮周围的几个蜗室,兼具吸入室和压出室的作用,也可将蜗室看作只有一个叶片的导叶。
目前,有些离心泵中,采用流道式导叶,目的是减小径向尺寸。
5、离心泵的密封
离心泵工作时,由于转子部分高速旋转,并输送具有一定压力的液体,因而在转动部分与固定部分之间,主要是叶轮与泵体间的口环处和泵轴与泵体间,存在液体的漏失。
通常把叶轮与泵体间的漏失称为内漏或内窜,泵轴与泵体间的漏失称为外漏,其中,内漏是主要的。
为了尽可能减少液体的漏失,离心泵中必须有良好的密封装置。
1)叶轮密封
离心泵工作时,叶轮在泵体中旋转,叶轮与泵体间必须保持一定的间隙,如图1—13所示。
就叶轮入口处而言,如果其外环与泵体间的间隙过大,就会导致泵的容积效率显著降低。
因此,应该选择合适的密封断面和形状,增加液体流动阻力,使得由高压腔到吸入口的漏失量最小,同时又能保证较高的寿命。
这类密封称作叶轮密封或口环密封。
叶轮密封的结构型式很多,如图1—14所示。
(1)平口环密封结构简单,但漏失量大,且漏失液会冲向吸入口,造成液流漩涡,降低水力效率,一般只在低扬程泵中使用。
1234556
图1-14叶轮密封的结构型式
1-平口式;2-直角式;3、4、5-迷宫式;6-阶梯式;7-螺旋沟式
(2)直角式密封漏失量少,主要是漏失液流从径向间隙流入轴向间隙时,由于轴向间隙显著增大,使流速下降,因而造成的液流漩涡较小。
(3)迷宫密封对液流的阻力最大,泄漏量小,但结构复杂,容易引起转子自振,不宜用于高压或超高压水泵中。
(4)阶梯形密封在环形密封间增设一个小室,实际是增加了一个出口损失和一个进口损失,使流动阻力增加,减小泄漏量,优点是工作平稳,在高压泵中广泛应用。
图1-15填料密封结构
1-填料套;2-填料盒;3-填料;4-填料压盖;5-轴套;6-填料环
(5)螺旋沟槽密封在动表面上开出螺旋槽,其螺旋方向与叶轮转动方向一致,当叶轮转动时,由于液体的惯性和粘性作用,阻碍液体向泄漏方向流动,适用于输送粘性液体,缺点是制造较复杂,也容易磨损。
为了保护泵体和叶轮,密封大多做成可拆式的环,磨损后换去密封环,泵体和叶轮可照常使用。
2)轴封结构
旋转的泵轴与固定的泵体间的密封结构简称轴封。
轴封的作用是防止高压液体从泵内漏出和外部空气进入泵内。
对于高压或输送含沙、易燃及有毒液体的离心泵,轴封是否可靠,是决定使用安全和寿命的关键所在。
离心泵常用的轴封结构有:
填料密封、有骨架的橡胶密封、机械密封和浮动密封等。
(1)填料密封填料密封是一般离心泵常用的密封结构,如图1—15所示。
由填料盒、填料环、填料、填料压盖等组成,靠填料和轴或轴套的外圆表面接触实现密封。
轴封的松紧程度通过调节填料压盖来控制。
太紧,容易造成发热、冒烟,甚至烧毁填料和轴套;太松,泄漏量增加,外部空气容易进入泵内,降低泵效,或使泵无法工作。
合理的松紧程度大致是液体从填料盒中呈滴状渗漏,泄漏量约1滴/s左右。
对于有毒、易燃、腐蚀及贵重液体,不能泄漏,不宜采用此种密封。
填料有软填料、半金属填料和金属填料等形式。
①软填料用石棉、橡胶、棉纱等动植物纤维和聚四氟乙烯树脂等合成树脂纤维编织成方形或圆形断面,再根据使用条件,用石墨、黄油等浸透,起润滑和防漏作用。
软填料只适用于输送温度不高的液体。
②半金属填料将石棉等软纤维用铜、铅、铝等金属丝加石墨、树脂等编织或压制成型,适用于输送中温液体,以及轴的转速和液压力较高的场合。
图1-16组合密封结构示意图
1-压力表;2-压缩空气室;3-橡胶薄膜;4-阀门;5-机油室;6-石棉圈;7-J型无骨架橡胶油封;8-隔膜
③金属填料将巴氏合金、铝或铜等金属丝浸渍石墨、矿物油等润滑剂压制成型,一般做成螺旋状,可用于液体温度≤150℃和圆周速度≤30m/s的场合。
(2)橡胶组合密封橡胶组合密封结构简单,体积小,密封效果比较显著,但密封皮碗内孔尺寸容易超差,将轴压得过紧,消耗功率过大,且耐热性和耐腐蚀性都不够理想,寿命较短,故只在小泵上应用较多,大泵则很少采用。
这类密封圈有的带骨架,有的无骨架,已经标准化。
图1—16是150GZ型离心泵所采用的一种新型组合密封结构,主要由一个储能器、3个J型无骨架橡胶密封圈和石棉圈组成。
当静压力压缩气室中的气体推动橡胶薄膜时,机油室中的机油通过阀门和隔圈通孔流向密封圈的唇口和轴表面,阻止泥浆浸入密封腔,同时对唇口和轴提供充分的润滑和冷却条件,形成油膜,避免磨粒磨损。
三道密封圈既可防止泥浆泄漏,又可封住机油,浸油石棉圈可起密封作用,又可阻止空气侵入,确保油封唇口与轴接触区始终保持负压状态,是组合密封的最后一道防线。
(3)机械密封依靠两个经过精密加工的动环与静环的端面,沿轴向紧密接触实现密封的结构。
机械密封又称端面密封。
机械密封的结构型式很多,但原理基本相同,其工作原理如图1-17所示。
该密封装置中,主要密封件(摩擦副)是动环和静环。
动环安装在泵轴上随轴一起转动,静环安装在泵体上为静止件。
动环在液体压力的作用下,紧压在静环上。
动环通过传动座、螺钉、拨叉等克服摩擦力,随轴套和轴一起转动,而静环则由防转销制动。
动环和静环一般用不同的材料制成,一个由硬度较低的石墨或石墨加其他填充材料制成,另一个由钢或表面堆焊硬质合金制成;也可以用同一种材料制成动环和静环,如碳化钨对碳化钨。
由图可以看出,机械密封有4个可能泄漏点:
A处是动环与静环的接触面,由于二者紧密接触,并有油膜形成,可以阻止液体泄漏;B处用“O”形密封圈防止静环与压盖之间泄漏;C处动环与轴或轴套之间也属于静密封,用“O”或“V”形密封圈防止泄漏;D处壳体与压盖之间用“O”型密封圈或垫片防止泄漏。
由此可见,机械密封的特点是将容易泄漏的轴向密封转换为不易泄漏的静密封和端面密封。
其优点是密封可靠,消耗功率少,泄漏少,几乎可以做到无泄漏,因此,广泛用于输送高温、高压和强腐蚀性液体的离心泵。
缺点是对材料、制造和安装精度的要求高,更换困难。
图1-19迷宫密封结构示意图
(a)金属迷宫密封(b)碳精迷宫密封
图1-20叶轮叶轮侧压力分布图
图1-18浮动环密封装置示意图
1-浮动环;2-浮动套;3-支承弹簧;4-泄压环;5-轴套;6-泄压孔
图1-17机械密封结构示意图
1-静环;2-动环;3-压盖;4-弹簧;5-传动销;6-螺钉;7、8-密封圈;9-防转销
(4)浮动环密封在200~400℃高温和10~20MPa高压条件下工作的离心泵,采用机械密封比较困难,目前多用如图1—18所示的浮动环密封结构。
它实际是机械密封和迷宫密封的一种结合形式。
其径向密封依靠浮动环与浮动套的端面接触来实现,轴向密封依靠轴套外圆表面与浮动环内圆表面形成狭窄缝隙产生节流作用来实现。
浮动环密封具有自动调心的优点,径向间隙可以很小。
泄漏量的大小取决于浮动环与轴套间的间隙及长度,且一定存在泄漏。
(5)迷宫密封迷宫密封主要应用在大容量水泵、汽轮机、压气机及鼓风机等机械中。
其结构种类很多,常用的有金属迷宫和碳精迷宫两种。
迷宫密封的原理是在密封片与轴间形成微小间隙,流体通过间隙时由于节流作用使压力逐渐降低,从而大大减小泄漏量。
优点是不存在任何机械摩擦件,功率消耗少,结构简单。
最简单的迷宫密封如图1—19(a)所示,由一系列铜基合金片与转轴组成微小的间隙。
图1—19(b)是碳精迷宫密封,轴套表面加工出密封片,密封片与方形螺纹相似,碳精环则安装在密封室中;为便于组装,将碳精环分成若干个弧段,分别用螺旋压簧定位,并用止动销防止转动。
6.离心泵轴向力的平衡
由于叶轮受力的非对称性而产生的轴向力,只靠轴向止推轴承难以完全承受,必须安装轴向力平衡装置。
1)轴向力的产生
图1—20是单吸叶轮两侧压力的分布图。
从叶轮打出的高压液体有一部分回流到前、后盖板的外侧。
一般认为叶轮与泵体之间的液体压力按抛物线形状分布。
在密封环直径Dw以外,叶轮两侧的压力p2是对称的,无轴向力。
但在Dw以内,作用在叶轮左侧的压力是入口压力P1,作用在叶轮右侧的压力是出口压力P2,且p1两侧压力差与相应面积的乘积,就是作用在叶轮上的轴向力。
所以,离心泵的轴向力总是指向叶轮的吸入口方向,大小为:
F=△p·s=(p2一p1)·π2Dw2/4
对于单吸多级泵,每级叶轮都产生轴向力,其值可能很大,仅靠轴向止推轴承平衡会使轴承无法承受,将严重降低其使用寿命。
2)轴向力的平衡方法
从长期的生产实践中总结出许多平衡轴向力的方法,如利用叶轮的对称性、对叶轮结构进行改造、增设专门的平衡装置等,在应用中都收到了良好的效果。
(1)利用叶轮的对称性平衡轴向力
对于单级泵,利用双吸叶轮,使叶轮两侧盖板上的压力相互抵消,可以很有效地平衡轴向力。
图1-21叶轮对称排列平衡轴向力
对于多级泵,利用对称排列方式,即将总级数为偶数的叶轮,如图1—21所示背靠背或面对面地串联在一根轴上。
这种方法不能完全消除轴向力,一般还应安装止推轴承。
水平中剖式多级泵和立式多级泵,常采用此法。
(2)改造叶轮结构平衡轴向力
对于单吸离心泵,可以适当改变叶轮结构,消除或减少轴向力。
主要的有三种方法:
①平衡孔法即在如图1—22(a)所示的叶轮后盖板上开一圈小孔,称作平衡孔孟,使后盖板密封环内的压力与前盖板密封环内的压力基本相等。
由于前、后盖板密封环直径相同,故大部分轴向力可以被平衡。
②平衡管法如图1—22(b)所示,在前、后盖板上都安装有直径相同的密封环,并自后盖板泵腔处接一根平衡管,使叶轮背后的压力液与泵的吸入口接通,以消除大部分轴向力。
图1-22改变叶轮结构结构平衡轴向力
(a)平衡孔法(b)平衡管法(c)平衡叶片法
③在叶轮背面加平衡叶片法叶轮旋转时,平衡叶片强迫叶轮后面的液体加速旋转,使压力下降,从而达到减小轴向力的目的。
带平衡叶片的叶轮如图1—22(c)所示。
(3)安装专用的平衡装置
对于单吸多级泵,特别是分段式多级泵,一般依靠平衡装置平衡轴向力。
主要有:
图1-23平衡盘装置
①自动平衡盘平衡轴向力自动平衡盘多用于多级离心泵,安装在末级叶轮之后,随转子一起旋转,如图1—23所示。
该平衡装置有两个间隙,一个是轮毂或轴套与泵体间的径向间隙b≈0.2~0.4mm;另一个是平衡盘端面与泵体上平衡圈间的轴向间隙bo≈1.0~0.2mm;平衡盘后面的平衡室用连通管与泵的吸入口连通,压力接近吸入口压力p0。
液体在径向间隙前的压力是末级叶轮后盖板下面的压力p,通过径向间隙后下降为p’,压力降△pl=p一p’;液体再流经轴向间隙后,压力降为p0,轴向间隙两边的压力差△p2=p’一p0;平衡盘两边的压力差△p=△pl+△p2=(p一p’)+(p’一p0)=p一p0。
由于平衡盘两边有压力差△p2,液体在平衡盘上有向右的作用力p,称平衡力;其值与向左的轴向力F大小相等,方向相反;当F=p=0时,轴向力被完全平衡。
这种装置中的径向间隙和轴向间隙各有其作用,又互相联系,可以自动平衡轴向力。
当工况改变,轴向力F与平衡力p不相等时,转子就会轴向窜动。
若F>P,转子就向左边的吸入方向移动,轴向间隙b0减小,液体流动损失增加,漏失量减少,平衡盘前面的压力p’增加。
在总液压差△p不变的情况下,因泄漏量减少,△p1下降,因而压差△p2增大,平衡力p随之增大,转子开始向右边的出口方向移动,直至与轴向力平衡为止。
若轴向力F
由于泵的工况不断变化,以及转子惯性力的作用,转子不会总停留在一个位置,而是在某一位置左右作轴向窜动,因此,平衡盘的平衡是动态的。
鉴于此,采用平衡装置时,一般不安装轴向止推轴承。
轴向间隙b0很小,当转子窜向左边时,平衡盘与平衡圈间可能产生严重的磨损。
为了增加耐磨性,平衡圈一般采用不锈钢,平衡盘采用磷锡青铜等材料制成。
目前油田上使用的5D100—150注水泵,驱动功率800kW,当扬程为1500m时,产生的轴向力大约12000N,就是靠采用平衡盘方案平衡轴向力的。
在该泵中,当转子部件上安装平衡盘后,平衡盘与平衡圈间的轴向间隙b≈1.5~2.0mm;径向间隙A与输送介质有关,输送原油为0.45~0.5mm,污水为0.4~0.45mm,清水为0.38~0.43mm。
图1-24平衡鼓装置
②平衡鼓平衡轴向力图1—24是平衡鼓装置,它是安装在末级叶轮后面与叶轮同轴的鼓形轮盘,其外圆表面与泵体上的平衡圈间有0.2~0.3mm很小的间隙。
平衡鼓左侧压力接近叶轮出口压力为P2;平衡鼓后面的连通管与泵吸入口连通,平衡鼓右侧的压力接近泵的吸入压力p;平衡鼓两侧产生压差△p=p2一p