刹车盘的加工工艺及夹具设计.docx
《刹车盘的加工工艺及夹具设计.docx》由会员分享,可在线阅读,更多相关《刹车盘的加工工艺及夹具设计.docx(38页珍藏版)》请在冰豆网上搜索。
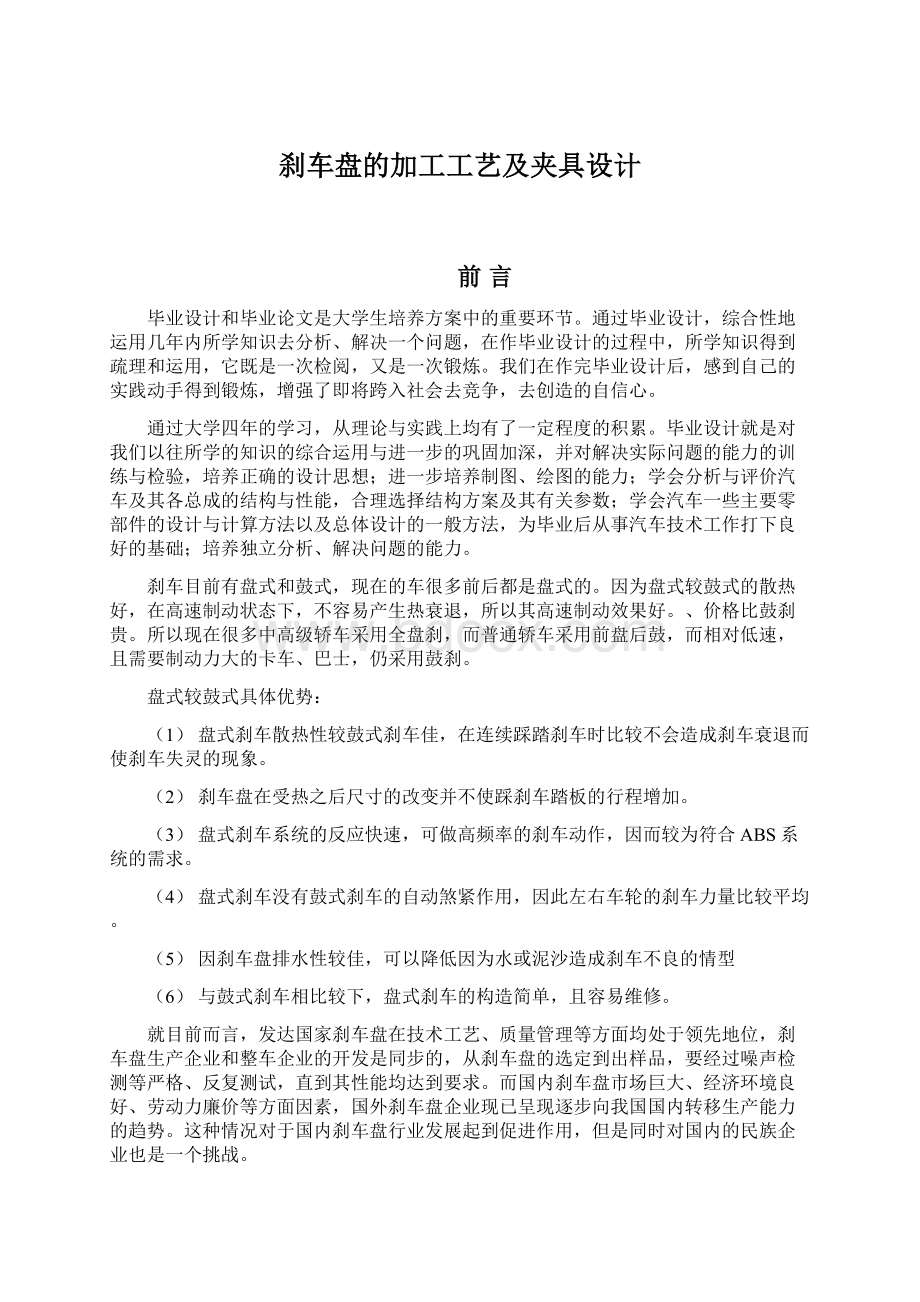
刹车盘的加工工艺及夹具设计
前言
毕业设计和毕业论文是大学生培养方案中的重要环节。
通过毕业设计,综合性地运用几年内所学知识去分析、解决一个问题,在作毕业设计的过程中,所学知识得到疏理和运用,它既是一次检阅,又是一次锻炼。
我们在作完毕业设计后,感到自己的实践动手得到锻炼,增强了即将跨入社会去竞争,去创造的自信心。
通过大学四年的学习,从理论与实践上均有了一定程度的积累。
毕业设计就是对我们以往所学的知识的综合运用与进一步的巩固加深,并对解决实际问题的能力的训练与检验,培养正确的设计思想;进一步培养制图、绘图的能力;学会分析与评价汽车及其各总成的结构与性能,合理选择结构方案及其有关参数;学会汽车一些主要零部件的设计与计算方法以及总体设计的一般方法,为毕业后从事汽车技术工作打下良好的基础;培养独立分析、解决问题的能力。
刹车目前有盘式和鼓式,现在的车很多前后都是盘式的。
因为盘式较鼓式的散热好,在高速制动状态下,不容易产生热衰退,所以其高速制动效果好。
、价格比鼓刹贵。
所以现在很多中高级轿车采用全盘刹,而普通轿车采用前盘后鼓,而相对低速,且需要制动力大的卡车、巴士,仍采用鼓刹。
盘式较鼓式具体优势:
(1)盘式刹车散热性较鼓式刹车佳,在连续踩踏刹车时比较不会造成刹车衰退而使刹车失灵的现象。
(2)刹车盘在受热之后尺寸的改变并不使踩刹车踏板的行程增加。
(3)盘式刹车系统的反应快速,可做高频率的刹车动作,因而较为符合ABS系统的需求。
(4)盘式刹车没有鼓式刹车的自动煞紧作用,因此左右车轮的刹车力量比较平均。
(5)因刹车盘排水性较佳,可以降低因为水或泥沙造成刹车不良的情型
(6)与鼓式刹车相比较下,盘式刹车的构造简单,且容易维修。
就目前而言,发达国家刹车盘在技术工艺、质量管理等方面均处于领先地位,刹车盘生产企业和整车企业的开发是同步的,从刹车盘的选定到出样品,要经过噪声检测等严格、反复测试,直到其性能均达到要求。
而国内刹车盘市场巨大、经济环境良好、劳动力廉价等方面因素,国外刹车盘企业现已呈现逐步向我国国内转移生产能力的趋势。
这种情况对于国内刹车盘行业发展起到促进作用,但是同时对国内的民族企业也是一个挑战。
1零件的分析
1.1零件的作用
该零件作为汽车的制动元件,用于汽车的刹车系统中,是决定刹车效果好坏的重要零件。
刹车盘片肯定是用来制动的,其制动力来源于制动钳。
通常来说一般的制动钳都是固定内侧制动活塞泵所在部分,外侧是一个卡钳式的结构。
内侧制动片固定在活塞泵上,外侧制动片固定在卡钳外部。
活塞通过制动油管过来的压力推动内侧制动片,同时通过反作用力拉动卡钳,使外侧制动片向里。
两者同时压向制动盘,通过制动盘和内外制动片的摩擦产生制动力。
这个过程中,推动活塞是靠制动液,也就是液压油。
1.2零件的工艺分析
该零件是一个形状较为规则的盘类零件,主体部分是回转体,其上主要有凸缘、均布孔等结构,由于壁厚较薄,所以加工起来较为复杂,并且有的加工面对形状位置精度要求较高,因此先通过铸造的形式铸出如以下形状的毛坯。
再对此毛坯进行相应的加工即得所需的零件。
零件的主要技术要求分析如下:
(1)刹车盘毛坯采用铸造的方式进行生产,铸件要求不能有砂眼、疏松等缺陷,以保证零件的强度及刚度。
在外力的作用下,不至于发生意外事故。
(2)刹车盘的大外圆径向尺寸较大,宽度方向相对较小,一侧有层孔,属薄壁盘类零件,所以有的工序在机床卡盘不能满足夹紧的情况下,要考虑专用夹具。
(3)刹车盘的两个刹车面要求精度很高,每个刹面的平面度公差的允许值为0.04,两刹面的平行度公差的允许值为0.08,刹面相对于中孔中心线的跳动公差的允许值为0.10。
因为刹车盘刹车时靠的就是这两个刹面,所以加工时要用数控车精车两刹面,达到其表面粗糙度要求Ra1.6,并且保证一定的形状位置精度。
(4)由于汽车刹车时,刹车盘表面的温度能达到300~500摄氏度,要尽快降低刹车盘的表面温度。
所以两盘面之间留有风道,是通过37个沿圆周均匀分布的筋条连接起来的。
(5)四个直径是13的孔和两个直径是8.5的忽锥孔是比较重要的孔,也是以后装配的主要基准。
因此加工此孔的工序显得尤为重要,要在夹具设计中充分考虑,保证达到此孔的精度及粗糙度的要求。
图1.1刹车盘零件
Fig.1.1Partdrawing
2工艺规程的设计
2.1确定毛坯的制造形式
铸铁上工业上应用最为广泛的一种铸造合金。
铸铁和钢的区别在于,铸铁中的部分碳是以自由状态,即石墨的形式存在,它们有降低强度、塑性和韧性的作用;铸铁不能像钢那样进行轧制和锻造变形。
铸铁的突出优点是具有非常好的铸造性能,铸铁生产的熔化设备简单,工艺操作简便,生产成本低廉。
零件的材料为HT200,灰铸铁的铸造性能优良。
由于熔点低(约为1200℃),铁液的流动性好,所以可以铸造形状复杂的零件,且不易形成集中缩孔,也较少有分散缩孔,仅长度方向有线收缩。
由于铸铁中的石墨可以起断屑作用,并对刀具具有润滑减摩作用,所以灰铸铁有优良的切削加工性能。
综合力学性能低,抗压强度比抗拉强度高约3-4倍。
吸振性好。
弹性模量较低。
结构贴点:
形状可以复杂,结构允许不对称。
2.2定位基准的选择
工件在加工时,用以确定工件对机床及刀具相对位置的表面。
根据零件图纸及零件的使用情况分析,已知四个孔、两个刹面的厚度及各层内孔等均应通过正确的定位才能保证其位置精度,故对基准的选择应予以分析。
2.2.1粗基准的选择
选择粗基准时,首先要考虑两个问题:
一是合理地分配个加工面的加工余量;二是保证加工面与不加工面之间的相互位置要求。
在具体的选择时应参考下列原则。
(1)相互位置原则。
对于同时具有加工表面与未加工表面的工件,为了保证不加工表面与加工表面之间的位置要求,应选择不加工表面作粗基准。
如果零件有多个不加工表面,则应以其中与加工面相互位置要求较高的表面作粗基准。
(2)余量最小原则。
对于具有较多加工表面的工件,选择粗基准时,应考虑合理地分配各表面的加工余量。
为满足各主要加工表面都有足够的余量这个要求,应选择毛坯余量最小的表面作粗基准。
(3)重要表面原则。
(4)不重复使用原则。
粗基准应避免重复使用。
在同一尺寸方向上,粗基准通常只允许使用一次,以免产生较大的定位误差。
(5)便于装夹原则。
选作粗基准的表面应平整,没有浇口、冒口或飞边等缺陷,以便定位可靠。
首先应保证零件加工精度,然后再考虑装夹方便,使用可靠,操作简单。
选择精基准一般应遵循的原则如下。
2.2.2精基准的选择
(1)基准重合原则即直接选择加工表面的设计基准为定位基准。
使用基准重合原则可以避免定位基准与设计基准不重合而引起的定位误差(基准不重合误差)。
(2)基准统一原则即当加工工件时,以某一组精基准定位可以方便地加工其他各表面,实际加工中会优先采用此组精基准定位,这种多数工序所选用的这同一组基准的工艺现象。
(3)自为基准原则。
(4)互为基准原则。
(5)便于装夹原则。
保证工件定位准确、夹紧可靠、操作方便。
同时定位基准应有足够大的接触面积,以承受大的切削力。
应该指出,上述粗基准、精基准的选择原则中,常常不能全部满足,应用时往往会出现相互矛盾的情况,这就要求从实际出发,综合考虑,分清主次,着重解决矛盾。
2.3工艺路线的拟定
制定工艺路线的出发点,应当是使零件的几何形状,尺寸精度及位置精度等技术要求能得到合理的保证。
在生产纲领已确定为大批生产的条件下,可以采用万能机床配以专用夹具,并尽量使工序集中来提高成产率。
除此以外,还应考虑经济效果,以便降低生产成本。
2.3.1工艺路线方案一
毛坯精铸,人工时效处理
(1)粗车大外圆面
(2)粗车小外圆面
(3)粗车中孔小圆顶面及右侧面
(4)粗车左侧面及各内孔
(5)半精车左侧刹面及各层内孔
(6)半精车右侧刹面、小外圆表面、小外圆端面及中孔
(7)精车左右刹车面及小圆端面
(8)钻孔、锪锥孔
(9)去毛刺,吹铁屑。
(10)检验入库
2.3.2工艺路线方案二
毛坯精铸,人工时效处理
(1)粗车大外圆面
(2)粗车中孔
(3)粗车小圆端面、侧面及右侧刹车面
(4)粗车左侧刹车面及各内侧孔
(5)半精车大外圆面、左侧刹车面及各内层孔
(6)半精车小外圆面、端面、中孔及右侧刹车面
(7)精车槽及右侧刹车面
(8)精车左刹车面及小圆端面、精车左侧底层圆面、内孔倒角
(9)钻孔、锪锥孔
(10)去毛刺,吹铁屑。
(11)检验入库
2.3.3两个工艺方案的比较与分析
在以上两个个工艺方案中前3道工序是不尽相同的,接下来的5道工序是相同的。
方案一是通过大外圆粗定位,加工出小外圆面,以此获得基准面,再加工中孔,而后以中孔定位加工刹面,达到基准重合的目的。
方案二是通过大外圆粗定位,先加工出中孔,在以中孔为基准加工小端面外圆,也能得到较好的加工精度。
两个个方案的加工方式是基本相同的,只是在加工获得基准的顺序上不相同。
但是,后面的工序均以孔及小端外圆面定位,所以说是满足基准重合原则的。
两个方案在这点上是相同的。
加工过程中还要充分利用互为基准的原则,才能精确完成加工任务。
此外,选择加工方案时还应考虑到加工单位的具体生产条件如:
生产设备能否满足加工精度,能否自行设计工装夹具,能否借用各种量具等,这都会对加工方案产生影响。
本次设计的加工工艺方案选择方案二。
2.4确定切削用量及毛坯图
2.4.1初步确定毛坯尺寸
根据铸件毛坯最大尺寸和加工表面基本尺寸查表<<铸件的机械加工余量>>(按中间等级2级精度查表)可得出,顶面的的机械加工余量为3.5,底面的机械加工余量为 3.5,侧面加工余量为5.5。
查表<<铸件的尺寸偏差>>可得出,刹车盘的毛坯的尺寸偏差为±1.5。
但由于用查表法所确定的总余量与生产的实际情况有些差距,故还应根据加工工艺编制以及加工过程中情况进行适当的调整。
这里仅仅是初步确定毛坯的基本尺寸。
表2.1毛坯主要尺寸及公差
Tab.2.1Mainroughsizeandtolerance
零件尺寸
总余量
毛坯尺寸
尺寸公差等级
大外圆
258.5
5.5
264
IT12
小外圆
140
4.0
144
IT13
两刹车面
20.6
3.5
24.1
IT14
宽度
41
5
46
IT14
中孔
61
4.0
65
IT5
2.4.2机械加工工艺的编制
零件材料选择灰铸铁HT200,毛坯为精铸件,清理后,人工时效处理,以消除铸造过程中产生内应力,并改善机械切削加工性能。
在毛坯车间进行调整,达到毛坯的技术要求,然后送到机械加工车间加工。
(1)详细加工工序
①粗车大外圆面
②粗车中孔
③粗车小圆端面、侧面及右侧刹车面
④粗车左侧刹车面及各内侧孔
⑤半精车大外圆面、左侧刹车面及各内层孔
⑥半精车小外圆面、端面、中孔及右侧刹车面
⑦精车槽及右侧刹车面
⑧精车左刹车面及小圆端面、精车左侧底层圆面、内孔倒角
⑨钻孔、锪锥孔
⑩去毛刺,吹铁屑。
⑪检验入库
(2)机械加工余量、工序尺寸的确定
工序一:
粗车大外圆面Φ264,选择加工余量3.3mm
工序二:
粗车中孔Φ65,选择加工余量2.3mm
工序三:
粗车小圆端面车平即可
粗车小圆面Φ144,选择加工余量2.5mm
粗车右侧刹车面车平即可
工序四:
粗车左侧刹车面车平即可
粗车左侧次层圆尺寸φ167,加工余量为2.5mm
粗车左侧次层圆尺寸φ144,加工余量为2mm
顺次粗车内圆尺寸φ129,加工余量为2mm
顺次粗车内圆尺寸φ125,加工余量为2mm
顺次粗车内圆尺寸φ121,加工余量为2mm
工序五:
半精车大外圆面φ