模具培训教材中级.docx
《模具培训教材中级.docx》由会员分享,可在线阅读,更多相关《模具培训教材中级.docx(16页珍藏版)》请在冰豆网上搜索。
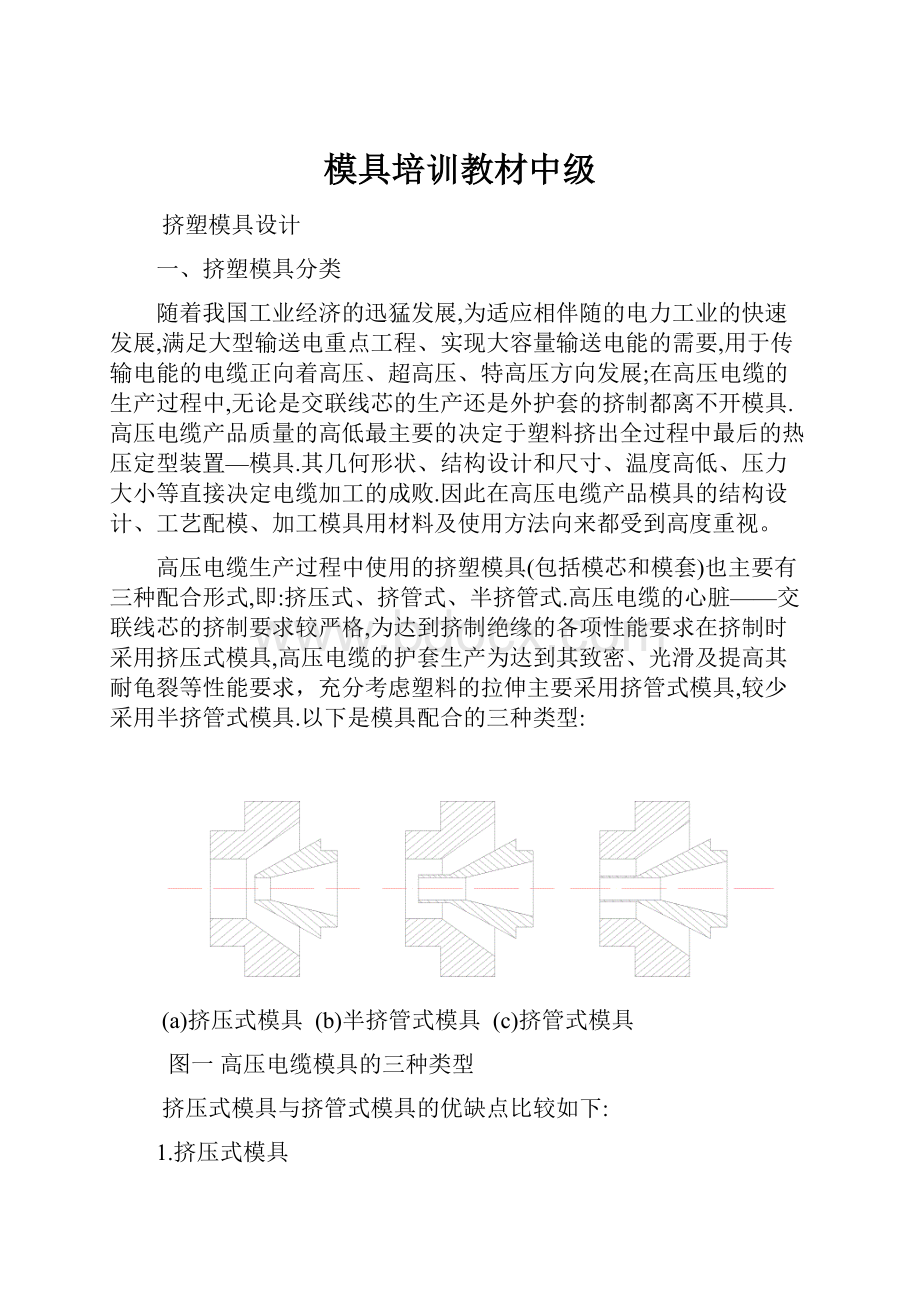
模具培训教材中级
挤塑模具设计
一、挤塑模具分类
随着我国工业经济的迅猛发展,为适应相伴随的电力工业的快速发展,满足大型输送电重点工程、实现大容量输送电能的需要,用于传输电能的电缆正向着高压、超高压、特高压方向发展;在高压电缆的生产过程中,无论是交联线芯的生产还是外护套的挤制都离不开模具.高压电缆产品质量的高低最主要的决定于塑料挤出全过程中最后的热压定型装置—模具.其几何形状、结构设计和尺寸、温度高低、压力大小等直接决定电缆加工的成败.因此在高压电缆产品模具的结构设计、工艺配模、加工模具用材料及使用方法向来都受到高度重视。
高压电缆生产过程中使用的挤塑模具(包括模芯和模套)也主要有三种配合形式,即:
挤压式、挤管式、半挤管式.高压电缆的心脏——交联线芯的挤制要求较严格,为达到挤制绝缘的各项性能要求在挤制时采用挤压式模具,高压电缆的护套生产为达到其致密、光滑及提高其耐龟裂等性能要求,充分考虑塑料的拉伸主要采用挤管式模具,较少采用半挤管式模具.以下是模具配合的三种类型:
(a)挤压式模具(b)半挤管式模具(c)挤管式模具
图一高压电缆模具的三种类型
挤压式模具与挤管式模具的优缺点比较如下:
1.挤压式模具
优点:
挤压式模具的模芯无管状承线径,装配时缩在模套承径后面,塑料是靠挤出压力来实现最后定型的,所以,其挤出的塑料层结构紧密,外表较光滑圆整.主要用于交联线芯导体屏蔽、绝缘、绝缘屏蔽的挤制.
缺点:
模具设计要求较严格,模芯与模套间的角度差大小、结构尺寸、及其表面光洁度都决定着交联线芯的结构尺寸和表面质量;在生产时偏心调节较困难,绝缘厚度不易控制,高压交联线芯必须借助测偏仪来校正达到要求;再一个因是靠压力挤出,在模口处产生较大反作用力,出胶量较低因而车速慢产量较低.
2.挤管式模具
优点:
(1)挤出速度快,挤管式模具充分利用塑料可拉伸的特性,线速度可根据塑料拉伸比的不同而有所提高,从而可提高产量。
(2)偏心调节容易,生产时操作简单不大会产生偏心,不会因芯线任何形式的弯曲而使塑料层产生大的偏心。
(3)模芯的使用寿命较长,因模芯内孔与芯线间的间隙较大,使磨损减小。
(4)工艺配模较方便,因模芯内孔与芯线间的间隙范围较大,模芯的通用性较大,同一套挤管式模具可通过调整塑料拉伸比的办法来挤制不同芯线直径和不同厚度要求的护套。
(5)护套厚薄容易控制,可通过调整牵引速度来调整拉伸比,从而改变并控制护套厚度。
(6)提高结晶性高聚物(聚乙烯)护套耐龟裂性能,因塑料经拉伸发生”定向”作用,结果使塑料的机械强度提高,能有效地提高电缆护套拉伸方向的强度。
缺点
(1)塑料层的致密性较差,塑料是沿着模芯外承线径挤出随着线芯的牵引拉伸包附在芯线表面上,压实力较小,可通过适当增加拉伸比或采用抽真空的方法来克服。
(2)表面圆整度远不如挤压式模具,芯线的不均匀性常在护套表面显露出来,通过适当增大模芯与模套间的夹角来改善。
二、高压电缆模具的设计
(一)模具的设计原则
因模具的质量好坏直接影响交联线芯与电缆外护套的质量,所以对模具的设计及加工要求较严格,总的具体要求如下:
1.凡是与塑料接触的模具表面应光滑、光洁度要高,一般要求在0.8(用去除材料方法表示)或抛光处理;尤其是模套的承径区更应光洁必须要抛光处理,以保证塑料成型的表面光洁度要求。
2.熔融塑料的流动的道路要流畅,所有料流道路上应无突变、无突起等阻碍,也不能有死角;在机头及模具中一切造成料流停滞、涡流的地方都应避免。
3.塑料在模具内流动须具有一定压力,必须要求模套内锥角大于模芯的外锥角,这个角度必须要存在,否则会造成料流压力减小,出胶量不稳且致密性太差,严重者会造成塑料层脱节,严重影响塑料的表面质量。
4.模具的端部尺寸要与机头分流器衔接吻合,不得出现前台阶或后台阶,镶嵌式模芯的外锥角要与芯座的外锥角相一致,防止塑料出现突变或滞留。
5.在设计时要充分考虑模芯座与模套座端面间距离,以准确定位模芯与模套的前后位置关系,在设计时才能做到有的放矢,准确无误。
6.模具要具有互换性,应考虑各部位的尺寸公差要求;且模具的寿命要长,合理选用模芯及模套材料并进行热处理提高其强度和耐磨性。
(二)高压交联线芯模具的设计
目前高压交联线芯为满足其绝缘交联度、偏心度等要求,生产设备采用的是瑞士VCV(立塔全干式交联及冷却工艺)生产线,此生产线控制系统先进性在国内也是一流的,导体屏蔽、绝缘、绝缘屏蔽采用三层共挤方式一次性挤出,为保证线芯绝缘的致密性及线芯表面光滑与圆整度模具必须采用挤压式模具,因是三层共挤模式,生产一种规格高压交联线芯的一组模具包含
芯、
芯、中模(机头结构自带)与模套,以下是三种(除中模外)模具的设计思路:
1.模芯
的设计
挤压式模芯
的结构见图二
在材料确定后,以工艺的合理性,兼顾加工的可能性恰当设计各部分尺寸,应注意的设计要点如下:
(1)Φds:
模芯
的内径
这是对挤出质量影响最大的结构尺寸之一,根据线芯结构特性及其尺寸设计。
既不能太大,也不能太小。
因为过大了,一则形成线芯的摆动而造成挤出偏芯,再则会出现倒料,既有害挤包层质量,又有可能造成断线。
而过小,会造成绝缘线芯呈现竹节状且易刮伤线芯甚至断线,同时模具的磨损加大使模具寿命降低。
一般的工艺配模尺寸为Φds=d+ed为线芯导体直径(包括半导电绕包带);e为增大间隙余量,一般d≦20mme=0.8-1.0随线芯直径的增大而增大;d>20mme=1.0-1.2同样随线芯直径的增大而增大;220Kv1x2000mm2、1x2500mm2的导体线芯e量可增加到1.5mm。
图二模芯
结构图
(2)Φdu:
模芯
外径
Φdu实际上是决定模芯出线端口厚度的尺寸,端口厚度△=1/2(Φdu-Φds)不能太薄,否则影响使用寿命;也不宜太厚,否则塑料熔体流道发生突变,并且形成涡流区,引发挤出压力的波动,而且易形成死角,影响塑料层质量,一般模芯
出线端口的壁厚控制在0.5mm为宜。
(3)Φ1:
外锥角
根据机头结构和塑料流动特性设计,φ
角小时推力大而压力小,此时挤出的速度快、产量高,但塑料表面不很光滑且包的不紧密;反之φ
角大时推力小而压力大,此时挤出速度慢、产量低,但塑料表面光滑、包的紧密。
通常模芯
的外锥角要小于模芯
的内锥角。
一般Φ1锥角控制在45°以下,其角度的大小往往根据机头内部结果特点决定,在此Φ1=40°。
(4)L1:
内承线径
L
决定线芯通过模芯的稳定性,但也不能设计的太长,否则将造成加工困难,工艺上的必要性也不大,一般L
=(0.5~1.5)d
,且模芯孔径d
较大时选下限,否则,反之。
(5)Φ2:
内锥角
在Φds确定后,Φ2随L1的变化而修正,原则上来说只要模具强度足够Φ2角愈大愈好,便于穿线。
(6)L:
模芯
总长度
由上图可知L=L2+(d1-du)/2tg(Φ1/2),所以L可以依据上述决定的尺寸确定,经计算确定L的长度,如果太长或太短,与机头内部结构配合不当,可回过头来修正锥角φ
,然后再计算L直至合适。
(7)Φd1、L2、Φd2、M等尺寸是与机头模芯
座相吻合,不得出现前台阶或后台阶的现象,否则会出现塑料流动受阻或滞留,容易产生焦糊料挤出后会形成内屏蔽突起,引起绝缘局部放电现象,这在高压交联线芯中是绝对不允许的。
在设计时注意。
2.模芯
的设计
挤压式模芯
的结构见图三;同样要在材料确定后,以工艺的合理性,兼顾加工的可能性恰当设计各部分尺寸,应注意的设计要点如下:
图三模芯
结构图
(1)Φds:
模芯
内径
Φds是模芯
的关键尺寸之一,其决定了导体屏蔽的厚度;Φds的大小是依据导体屏蔽厚度来决定的,既不能太大也不能太小,要符合工艺要求。
一般工艺配模方法为当导体线芯为紧压圆结构时Φds=d(导体线芯直径)+2△(导体屏蔽厚度);当导体线芯为分割导体结构时Φds=d(导体线芯直径)+2△(导体屏蔽厚度)+e,e值是考虑到分割导体结构存在的分割块成缆间隙,虽有半导电带的包扎但在挤制时仍存在屏蔽料轻微嵌入,e值大小一般为0.1—0.2mm。
(2)Φdu:
模芯
外径
Φdu也是决定模芯出线端口厚度的尺寸,端口厚度△=1/2(Φdu-Φds)不能太薄,否则影响使用寿命;也不宜太厚,否则塑料熔体流道发生突变,并且形成涡流区,引发挤出压力的波动,而且易形成死角,影响塑料层质量,考虑塑料溶体发生突变的因素较多,一般模芯
出线端口的壁厚控制在0.5mm为宜。
(3)φ
:
模芯
外锥角
φ
的大小对绝缘的挤出影响很大,通常根据机头结构和塑料流动特性设计,由生产工艺要求必须保证绝缘表面光滑、且包的紧密。
通常模芯
的外锥角也必须要小于中模(机头结构中自带)的内锥角。
它们的角度差也在3°—10°之间,其角度的大小往往根据机头内部结果特点决定,在此Φ1=56°。
(4)φ2:
模芯
内锥角
φ2的大小由与模芯
外锥角的配合及机头结构和塑料流动特性来决定,与模芯
外锥角的角度差也符合3°—10°的区间,在此φ2=45°。
(5)δ:
模芯
的修正角度
δ的存在意义非常重要,在Φds较小时也即Φdu较小时,为保证模芯
端面与模芯
端面间合理间隙(约为5-8mm),且还要保证塑料的良好流动特性,必须对模芯
内锥角进行修正,此处修正的角度在Φdu﹤50mm时δ=8°;在Φdu≥50mm时δ=1°。
δ的值在设计时可根据具体情况进行调整。
(6)L2:
模芯
内承线径
为保证导体屏蔽光滑致密与圆整,模芯
必须留有一定长度的内承线径,但不能太长若太长了在线芯稍微偏心的情况下容易造成导体屏蔽脱节,并且导体屏蔽料过度摩擦温升过快易造成烧焦,从而形成内屏蔽突起伸入绝缘层,将来交联线芯运行后会造成局部放电现象,大大降低高压电缆的运行寿命。
一般L2值在2-3mm左右。
(7)L:
模芯
总长度
由上图可知L=L1+(d1-du)/2tg(Φ1/2),所以L可以依据上述决定的尺寸确定,经计算确定L的长度,如果太长或太短,与机头内部结构配合不当,可回过头来修正锥角φ
,然后再计算L直至合适。
(8)Φd1、L1、Φd2、M等尺寸是与机头模芯
座相吻合,不得出现前台阶或后台阶的现象,否则会出现塑料流动受阻或滞留,容易产生焦糊料挤出后会形成绝缘杂质的存在,引起绝缘局部放电或绝缘击穿现象,这在高压交联线芯中是绝对不允许的。
在设计时注意。
3.模套的设计
以下是高压交联线芯挤压式模套的结构示意图四,同样要在材料确定后,以工艺的合理性,兼顾加工的可能性恰当设计各部分尺寸,应注意的设计要点如下:
图四挤压式模套结构图
(1)Фd:
模套内径
因挤压式模具是靠压力来实现塑料定型的,这也是与挤管式模具最大的区别;Фd的大小直接决定了线芯的外径大小和挤出表面质量,这是模套设计的精密尺寸之一。
要根据产品直径、各挤出工艺参数及挤制塑料特性来严格设计。
考虑到塑料出模口后,解除压力后的膨胀和冷却后的收缩,一般d=导体线芯直径+2x内屏蔽标称厚度+2x绝缘标称厚度x1.06+2x外屏蔽厚度,1.06是绝缘的热缩系数。
(2)L1:
模套承线径
模套承线径的长度对机头料流的压力、偏心度控制的难易、挤包表面的光洁度及交联线芯外径的均匀性都有很大的关系。
太长,虽然交联线芯外径均匀、表面光滑,但料流阻力大、机头内料流压力高,塑料不易流出,线速度慢生产效率低;太短熔融塑料流动阻力小,机头内料流压力小容易挤出生产速度快;但塑料挤包压力不够,交联线芯外径不均匀、表面也不光洁。
一般生产高压交联线芯L1=3x(绝缘厚度+绝缘屏蔽厚度);另外,为了更好地实现熔融塑料压力在挤出过程中逐步增大且均匀稳定,达到交联线芯外径均匀圆整、绝缘层致密的效果,在承线径L1上留有β=2°的过渡角。
(3)α°:
模套内锥角
α的大小由与中模外锥角的配合及机头结构和塑料流动特性来决定,角α同样也必须大于中模外锥角3~10°,若没有这个角度差,便保证不了挤出压力,为保证交联线芯表面光滑、致密且圆整,角度差可以稍大一点,此处α=66°。
(4)L:
模套的总长度
由上图可知L=L1+(d1-d)/2tg(α/2),所以L可以依据上述决定的尺寸确定,经计算确定L的长度,如果太长或太短,与机头内部结构配合不当,可回过头来修正锥角α,然后再计算L直至合适。
(5)D、d1、d2尺寸大小与绝缘屏蔽分流器内部结构相吻合,同样不能出现前台阶与后台阶,要保证熔融塑料的畅通无阻,从而避免绝缘屏蔽层出现焦糊粒子等缺陷致使绝缘层击穿的现象。
4.高压交联线芯工艺配模举例
请列举出生产型号规格为YJLW03-Z127/220KV1X1000mm2的高压交联线芯用模具的尺寸?
解答:
(1)根据以上产品型号规格的工艺质量计划可知道:
所用导体线芯为分割导体结构;导体线芯标称外径为d=39.0mm;绕包两层半导电带后直径为d1=39.8mm;挤制+绕包厚度Δ1=2.5mm;绝缘层厚度Δ2=24mm;绝缘屏蔽层厚度Δ3=1.0mm。
(2)根据以上所述的各模具设计中配模公式计算如下:
模芯
内径:
D1=d1+e(因是分割导体可取1.0mm)=39.8+1.0=40.8mm;
模芯
内径:
D2=d+2Δ1+e=39+2x2.5+0.1=44.1mm;
模套的内径:
D3=d+2Δ1+2Δ2x1.06+2Δ3=39+2x2.5+2x24x1.06+2x1.0=96.7mm
(三)高压交联电缆外护套模具的设计
由前言中所述挤管式模具有挤出速度快、偏心调节容易、工艺配模较方便、模芯的使用寿命长、护套厚薄易控制、提高结晶性高聚物耐龟裂性能等优点;根据高压交联电缆产品的结构特点,要挤制护套的线芯一般都是单芯且较圆整,所以高压交联电缆外护套挤制通常采用挤管式模具,对挤包要求包紧力大的护套,为提高挤管式挤包层对线芯的包紧程度,可通过采用抽真空或适当提高牵引速度的方式来实现。
一组挤管式模具包括一件模芯和一件模套,以下是两种模具的设计思路:
1.挤管式模芯
挤管式模芯的结构见图五:
在材料确定后,以工艺的合理性,兼顾加工的可能性恰当设计各部分尺寸,其结构设计除定径区部分之外,其余外形尺寸与挤压式模芯设计基本相同,现仅对挤管式模芯定径部分的尺寸设计作一简述,应注意的设计要点如下:
图五挤管式模芯结构图
(1)Φd1:
模芯定径区内径
又叫模芯孔径,该尺寸依据选用模芯材料的耐磨性、线芯尺寸大小及其材质与外径规整程度等设计,因为高压线芯尺寸较大且规则,一般根据经验设计为d1=d(线芯外径)+6~10mm,因为挤管式模具通用性很大,配模时若较大线芯余量可放大到10mm;具体设计时为了模具系列化,通常将模芯孔径加工成整数尺寸。
(2)Φd2:
模芯定径区外径
从上图可看出d2决定于尺寸d1及其壁厚δ,即d2=d1+2δ。
壁厚的设计既要考虑模芯的寿命,又要考虑塑料的拉伸特性及电线电缆塑料层的挤包紧密程度,这个数值不能太大,否则拉伸比就大,塑料层拉伸后强度提高,而延伸率下降,影响电线电缆的弯曲性能;但也不能太小,太小因过薄使其使用寿命降低。
一般高压交联电缆设计为d2=d1+2(2~2.5)mm,即模芯嘴壁厚为2~2.5mm。
(3)L1:
模芯定径区外圆柱长度
该尺寸依据模芯尺寸d1并结合模套内承线径的长度和考虑挤出塑料成型特性设计,首先要满足与模套装配后模芯的外锥角与其外圆柱的过渡点,与模套内锥角和其内承线径的过渡点间距离Δ=5~10mm(见图六);再结合塑料本身的特性一般设计为L1=(0.5~1.0)d1,d1值大取下限,d1值小取上限。
(4)L2:
模芯定径区内圆柱(承线)长度
定径区内圆柱(承线)长度L2:
该尺寸由加工条件,线芯结构特性决定。
考虑到线芯的稳定性长一点较好,但加工较困难;无论如何L2必须比L1长度大5~6mm,这是确保模芯强度的必需。
2.挤管式模套
挤管式模套的结构见图六:
挤管式模套的结构型式与挤压式模套基本相同,所不同之处是其结构尺寸中的模套定径区的直径及其长度,必须按与其配合的挤管式模芯来设计;在此仅对挤管式模套定径部分的尺寸设计作一简述,应注意的设计要点如下:
图六挤管式模芯、模套装配图
(1)L:
挤管式模套内承线径
一般挤管式模芯与模套口端面是持平的,L往往根据塑料的成型特性并结合模芯定径区外圆柱(模芯嘴)的长度L1而定。
一般设计为L=(0.3~1.0)D,D值大取下限,D值小取上限;再结合塑料本身的特性,阻燃料及熔融粘度高的塑料L要求短一些。
但首先必须保证Δ=5~10mm即L1-L=5~10mm。
(2)ФD:
挤管式模套内径
该尺寸根据线芯外径d、挤管式模芯嘴外圆直径d2、护套厚度及塑料的拉伸特性等设计。
D值的确定有以下两种方法:
a.配模系数K、拉伸比S
配模系数(也称拉伸平衡度):
在挤管式模具的设计中,要求模套内径(D大)与电缆护套外径(d大)之比大于或等于模芯承径部分外径(D小)与电缆线芯外径(d小)之比。
只有满足了拉伸平衡度,才能避免出现护套圆锥撕裂、脱节、针孔、裂缝、松包、等缺陷,才能生产出合格的高压电缆外护套。
令K为配模系数则有:
D大/d大>1紧包
K=——————=1平衡拉伸
D小/d小<1松包
当K>1时,成为不平衡拉伸,若要继续保持平衡拉伸,因为芯线直径d小、模芯承线径外直径D小在挤出过程中都不变,电缆的护套厚度必然增加从而电缆外径增大;若仍要求电缆外径不变,在实际生产过程中可通过提高牵引速度使料流发生层间错位,经过一定的拉伸达到所需要的电缆外径。
因此,K>1则电缆生产速度快,塑料经过一定的拉伸与芯线包的紧密,且机械强度提高,对实际生产具有指导意义。
根据不同塑料K的取值不同,通常取K等于1.05~1.20,高压电缆护套K值一般取1.1。
当K<1时,成为不平衡拉伸,在塑料还未完全包紧芯线的情况下就进入水槽冷却,芯线与冷却塑料之间有空隙就形成松包;若要继续保持平衡拉伸,因为模套内径D大、模芯承线径外直径D小、芯线直径d小在挤出过程中都不变,电缆的护套厚度必然减小从而电缆外径减小,达不到设计要求是不理想的。
在高压电缆护套模具的设计中不采用K小于1的情况。
拉伸比(塑料的拉伸特性):
塑料离开模口时的圆环截面积与冷却后包覆于芯线表面护套的圆环截面积之比称为拉伸比S。
对于不同的塑料,根据其熔融下的粘度、流动特性等其拉伸比是不同的。
高压电缆常用护套料的拉伸比为PVC1.2~5、PE1.5~5。
D大2-D小2
S=——————
d大2-d小2
模套内径D大的确定:
在挤管式模具设计中,首先必须保证的是配模系数K应符合要求,然后再考虑拉伸比S。
一般是已知芯线直径d小、电缆护套外径d大,根据芯线直径先选择模芯的结构尺寸D小,再选定K后通过计算求出模套内径D大。
从而也计算出拉伸比S的大小,比较其拉伸比是否在范围之内。
前面已讲过挤管式模具通用性较大,计算出D大后在现有的模具中找一下有无接近的,若相差太大必须重新设计加工。
D小xd大xK
D大=——————
d小
b.经验公式
有时挤管式模具的设计利用配模系数与拉伸比的计算方法,计算出的模套内径不一定很确切,且较麻烦尤其对初学者来说。
可根据实际生产经验来进行设计。
一般情况下高压电缆护套挤制挤管式模套的内径D大=D小(模芯外径)+2δ(护套厚度)+e(增量),e=8~12mm;e值随线芯的增大(护套厚度也相应增大)而加大。
3.高压交联电缆外护套模具的设计举例
请列举出生产型号规格为YJLW03-Z127/220KV1X1000mm2的高压交联电缆护套用模具的尺寸?
解答:
(1)根据以上产品型号规格的工艺质量计划可知道:
铝护套线芯标称外径为d小=118.0mm;护套标称厚度Δ=5.0mm;电缆标称外径d大=128.5mm。
(2)根据以上所述的各模具设计中配模公式计算如下:
模芯内径:
d=d小+e=118+9=127mm;
模芯外径:
D小=d+2Δ1(壁厚)=127+2x2.5=132mm;
模套的内径:
(按照经验公式设计)
D大=D小+2δ(护套厚度)+e(增量)=132+2x5.0+10=152mm
模套的内径:
(按照配模系数及拉伸比计算)
D小xd大xK132x128.5x1.05
D大’=——————=————————=151mm
d小118
D大2-D小21512-1322
S=——————=——————=2.08
d大2-d小2128.52-1182
因所用护套料是PE料计算S值在其拉伸比范围内。
(四)高压挤塑模具的材料选择
模具材料的选择以资源、成本、寿命要求为基本原则,以及耐热、耐磨、耐腐蚀性要好,易于切削加工、不生锈等。
因挤塑模具是属于热作模具类,所以,其有两方面的特点;一是模腔表层金属受热,所以其性能要求满足具有高温硬度、高温强度和高的热塑变抗力;二是模腔表层金属产生热疲劳(龟裂),所以其还要满足具有高的热疲劳抗力。
常用来做挤塑模具(模芯模套)的材料主要有:
碳素结构钢(例45#钢应用最广);合金结构钢(2Cr13、12CrMo、38CrMoAl等)。
加工完后必须进行热处理(调质加氮化处理)HRC达到45~52。
以提高其耐磨性、耐腐蚀性及耐热性。