铜及铜合金国家标准化学分析方法修订.docx
《铜及铜合金国家标准化学分析方法修订.docx》由会员分享,可在线阅读,更多相关《铜及铜合金国家标准化学分析方法修订.docx(48页珍藏版)》请在冰豆网上搜索。
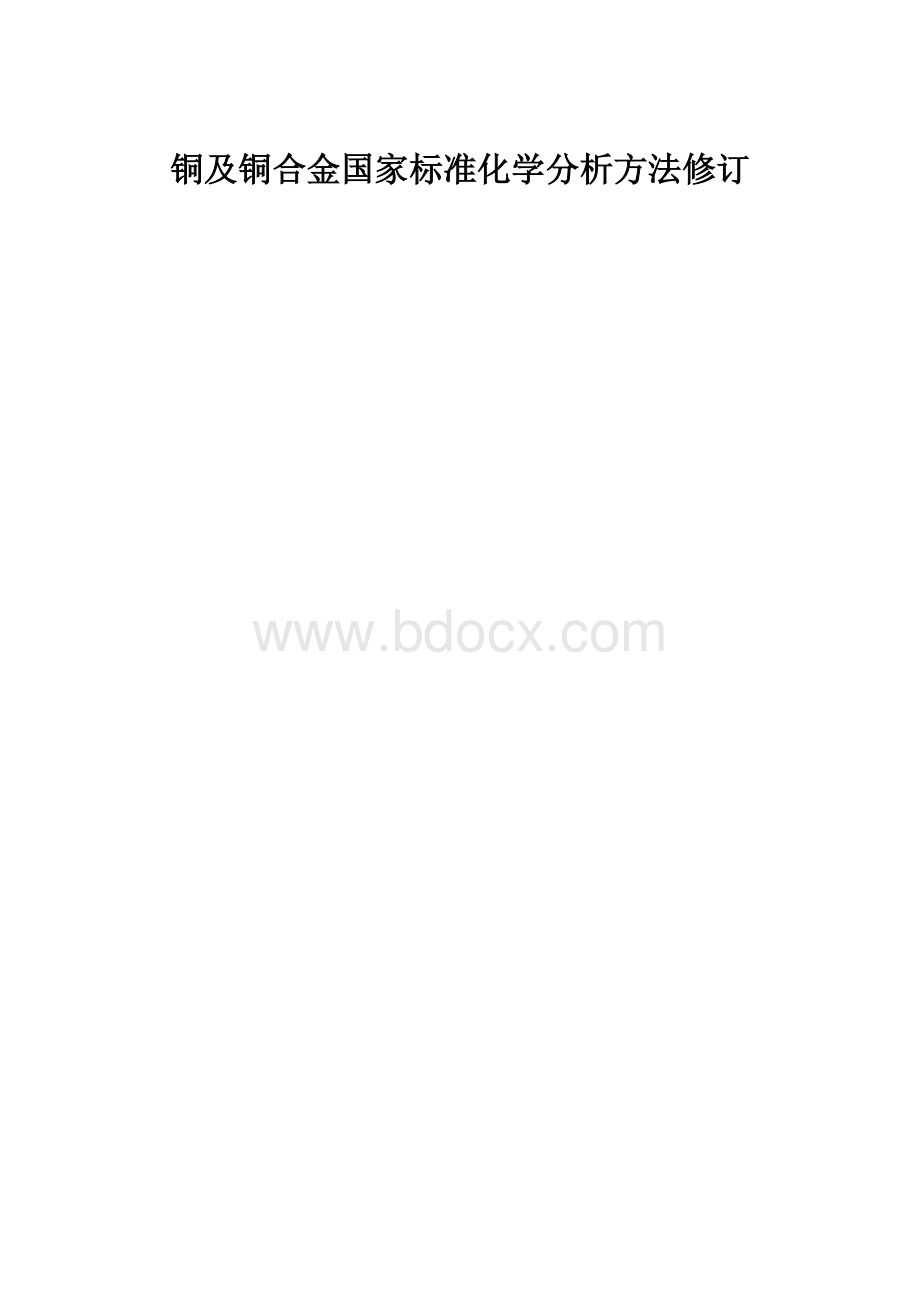
铜及铜合金国家标准化学分析方法修订
铜及铜合金管材内表面碳含量的测定
编制说明
浙江省冶金产品质量检验站有限公司二0一六年七月
《铜及铜合金管材内表面碳含量的测定方法》标准(送审稿)编制说明
1任务来源
根据国标委《国家标准委关于下达<钢铁行业原料场能效评估导则>等135项国家标准制修订计划的通知》(国标委综合〔2015〕59号20152283610)、全国有色金属标准化技术委员会“关于转发2015年第二批有色金属国家、行业标准制(修)订项目计划的通知”(有色标委[2015]29号)及陕西西安有色标准落实会确定《铜及铜合金管材内表面碳含量的测定》(项目编号:
20152283610)由浙江省冶金产品质量检验站有限公司负责起草。
浙江省冶金产品质量检验站有限公司、浙江海亮股份有限公司、中铝洛阳铜业有限公司为主要起草单位。
2工作简况
2.1立项目的和意义
我国是目前世界上最大的铜加工材生产国与消费国。
铜管产量已稳居世界第一,产量占全世界的一半以上,在产品质量、品种及技术水平等方面均已达到世界发达国家水平。
然而我国每年都有大量铜管、铜管件因碳膜引起的电化学腐蚀而报废,造成巨大的经济损失。
制定《铜及铜合金管材内表面碳含量的测定》标准后,有利于铜管生产、消费企业,通过测定铜管、铜管件内表面碳含量,使内表面碳含量过高成为不合格品,不使用到下游产品中去,从而减少应碳膜引起的电化学腐蚀,增加下游产品的使用寿命,降低经济损失。
2.2申报单位简况
浙江省冶金产品质量检验站有限公司是具有独立法人资格的第三方公正检测机构,浙江省政府第一批授权成立的省级质检机构,我省冶金(有色)行业产品质量检测的专业检验机构,浙江省高级人民法院对外委托司法鉴定机构。
公司拥有一支具有丰富经验的专业技术人员队伍,其中高级工程师5名,检测
人员具有较高的专业知识、技术能力和评判能力。
公司以高标准进行实验室建设,装备了具有国际、国内先进水平的仪器设备,拥有德国公司750三基体单火花直读光谱仪、德国6宽视野金相显微镜、日本岛津-6501F原子吸收分光光度计、
日本岛津-160A紫外/可见分光光度计、2000型红外碳硫分析仪、60中型石英摄谱仪、200钢材应力松驰试验机、深圳新三思公司5105电子万能材料试验机、
微机控制600电液伺服万能试验机、1000微机控制万能试验机等一批先进的检
测设备。
公司长期承担各类冶金有色产品理化检验,积累了丰富的检测经验和数据。
同时公司还承担各级政府行政管理部门下达的产品质量定期监督检验、日常监督检验、市场抽查检验、产品质量仲裁检验等指令性任务。
在研究水平方面,公司的研究条件及整体水平处于国内领先,通过承担一系列科研项目,取得了丰硕成果:
已获授权国家发明专利10项,另有13项发明专利已初审通过进入实质审查和公示阶段;负责编制了8891-2013《铜及铜合金散热管》;参与编制了5121.14-1996《铜及铜合金化学分析方法锰量的测定》、670-2008《空调器连接用保温铜管》、26303.1-2010《铜及铜合金加工材外形尺寸检测方法》、759-2011《铜及铜合金铸棒》、247-2011《镉棒》、26290-2010《红色黄铜无缝管》、813-2012《废杂黄铜化学成分分析取制样方法》、3131-2001《锡铅钎料》、200422-2006《无铅焊料》、28770-2012《软钎料试验方法》等多项标准。
2.3主要工作过程
2.3.1标准立项
我国每年都有铜管、铜管件因内表面残碳、潜碳的存在而引起电化学腐蚀,迫使相关设备停产维修,造成巨大的损失。
《铜管或铜管件内表面碳含量的测定燃烧法》标准的制定,有利于铜管、铜管件产品通过测定内表面碳含量,控制内
表面碳含量过高的产品投入使用,减少铜管、铜管件电化学腐蚀情况的发生。
我公司于2014年申请《铜及铜合金管材内表面碳含量的测定》国家标准的制定任
务,国家标准计划项目:
20152283610《铜及铜合金管材内表面碳含量的测定》。
2.3.2项目分工
为了完成《铜及铜合金管材内表面碳含量的测定》标准制定任务,浙江省冶金产品质量检验站有限公司立即成立了由总经理领导的标准编制小组,同时我们也积极的与共同负责起草的浙江海亮股份有限公司、中铝洛阳铜业有限公司进行交流、探讨,并进行了前期的试验,这为该标准全面、系统、有效的制定打下了良好的基础。
之后,编制小组开始了对该标准的起草工作,经过多次讨论及征求
意见,于2016年4月形成了该标准讨论稿。
于2016年5月23日至25日在杭州召开预审会,对讨论稿进行初步评审,经专家评审和修改,于2016年6月形成本标准送审稿。
2.3.3主要起草过程
经过标准编制组及有关人员的共同努力,通过对国内外应用现状及发展趋势的分析,参照国内外,在723-2009《铜及铜合金铜管或铜管件内表面碳含量的测定燃烧法》基础上修改采用制定本标准,同时参照15350-2000《钢铁总碳硫含量的测定高频感应炉燃烧后红外吸收法(常规方法)》、15349-2-1999《非合金钢低碳含量的测定第2部分:
感应炉(经预加热)内燃烧红红外吸收法》、5121.4-2008《铜及铜合金化学分析方法第4部分:
碳、硫含量的测定》,
20975.26-2013《铝及铝合金化学分析方法第26部分:
碳含量的测定红外吸收法》,并结合我国化学分析方法编制的特点,经过大量实验测试,编制小组于2016
年6月起草完成了该标准送审稿。
3编制原则
本标准本着积极采用国际先进标准的原则,在723-2009《铜及铜合金铜管或铜管件内表面碳含量的测定燃烧法》基础上修改采用制定本标准,同时参照
15350-200《0钢铁总碳硫含量的测定高频感应炉燃烧后红外吸收法(常规方法)》、
15349-2-1999《非合金钢低碳含量的测定第2部分:
感应炉(经预加热)内燃烧红红外吸收法》、5121.4-2008《铜及铜合金化学分析方法第4部分:
碳、硫含量的测定》,20975.26-2013《铝及铝合金化学分析方法第26部分:
碳含量的测定红外吸收法》。
本标准是根据1.1-2009《标准化工作导则第1部分:
标准的结构和编写规则》和20001.4-2015《标准编写规则第4部分:
试验方法标准》的要求进行编写的。
4确定标准主要内容的论据
4.1标准题目与适用范围
4.1.1本标准立项名称为“铜及铜合金管材内表面碳含量的测定”,英文名称“”。
根据杭州会议各位专家意见,将标准名称改为“铜及铜合金管材内表面碳含量的测定方法”,英文名称改为“”。
4.1.2规定了本标准适用范围:
本标准规定了铜及铜合金管或管件内表面碳含
量的测定方法。
本标准适用于铜及铜合金管或管件内表面碳含量的定量检测,测量范围52~5002。
根据实际测量情况,将检测范围由0.05~20.002调整为0.052~5.002,单位由
2改为2与《空调与制冷设备用铜及铜合金无缝管》17791新标准中清洁度单位一致。
4.2术语和定义
根据铜管内表面碳的存在形式,将铜管内表面碳分为残碳()、全碳()、潜碳(),并做了定义。
定义参照723-2009中的定义。
残碳():
以单质形式存在的碳含量。
潜碳():
以有机化合物形式存在的碳(如:
有机化合物:
油,油脂等)。
全碳()残碳和潜碳的总和。
4.3方法提要:
在氧气流中将铜及铜合金管或管件样品加热到一定温度,燃烧其内壁上存在的碳。
用红外吸收光谱法测定产生的二氧化碳,分别测定残碳及全碳的含量。
潜碳含量通过全碳量减去残碳量计算得出。
测定方法与723-2009中一致,也是采用管式炉加热,红外吸收光谱的测定
方法。
根据杭州会议的要求,将“铜管或铜管件”改为“铜及铜合金管或管件”。
4.4试剂
试剂包括去氧气(最低质量纯度99.99%)、去离子水(不含二氧化碳)、四氯乙烯(分析纯)、三氯乙烯(分析纯)、三氯乙烷(分析纯)、碱石棉、无水高氯酸镁、硝酸(1+1)、甘露醇和二氧化碳气体气体等。
涉及方法全过程中所有使用到的试剂。
氧气(最低质量纯度99.99%):
可通过净化装置净化到99.99%纯度的氧气。
去离子水(不含二氧化碳):
将去离子水煮沸30,在冷却至室温的过程中通
氧气(4.1)15,使用前制备。
四氯乙烯(分析纯)。
三氯乙烯(分析纯)。
三氯乙烷(分析纯)。
碱石棉。
无水高氯酸镁。
硝酸(1+1)。
甘露醇标准溶液:
称取1.2640g甘露醇(C6H14O6,预先经100℃~105℃烘干并置于干燥器中冷却至室温),置于100的烧杯中,加去离子水(4.2)溶解。
移入100容量瓶中,以去离子水(4.2)稀释至刻度,混匀。
此溶液1含5000μg碳。
甘露醇标准溶液
(1):
移取10.00甘露醇标准溶液(4.9)于100容量瓶中,
以离子水(4.2)稀释至刻度,混匀。
此溶液1含500μg碳。
二氧化碳气体(最低质量纯度99.99%)
723-2009中使用甘露醇(C6H14O6)或二氧化碳作为标准物质,实际试验中,甘露醇(C6H14O6)和二氧化碳的重复性能够满足试验要求,因而选用甘露醇(C6H14O6)和二氧化碳气体作为标准物质。
与讨论稿不同的是,根据企业的建议和试验结果,由加入固定体积的不同浓度的甘露醇标准溶液改为加入同一浓度不同体积的甘露醇标准溶液。
新加液方法具有溶液配置简单,加液量灵活等特点,但使用移液枪加入标准溶液体积时,应注意加入量不少于10μL,小体积量的移液枪的相对误差会较大。
表1为两种加液方法的测量结果,内表面积以252计。
表1两种加液方法的测量结果
(2)
(2)
4.9、5.0、4.9
甘露醇标准溶液入12.5μg
4.10,25μL,即加
4.8、5.0、4.9
10.2、10.4、10.4
甘露醇标准溶液
4.10,50μL,即加
9.9、10.2、10.1
入25μg
19.6、19.5、19.7
甘露醇标准溶液加入50μg
4.10,100μL,即
20.0、20.3、20.1
50.4、50.0、49.9
甘露醇标准溶液
4.9,25μL,即加
50.1、50.1、50.3
入125μg
100μL溶液中碳的重量(μg)
结果1
(2)
新方法加入标准物质的量
结果2
(2)
497.5入1250μg
从表1中可以看出,两种不同的加液方法对测定几乎无影响。
因此采用新的加液方式,更简单、快捷。
在723-2009标准中,并未对如何使用标准溶液有任何说明,仅指出“擦拭
甘露醇”。
4.5仪器设备
本标准涉及的仪器设备包括管式炉加热-红外分析碳硫仪、微量移液管(枪)、量具。
4.5.1管式炉加热-红外分析碳硫仪
装置连接示意图如图1所示。
燃烧过程在石英管道中进行。
图1.装置连接示意图
1氧气瓶:
附氧气表、减压阀。
2净化炉:
盛满氧化铜,可以使温度维持在450℃~500℃。
3干燥塔:
下部盛碱石棉,上部盛无水高氯酸镁,中间隔玻璃棉,塔顶塔底均铺有玻璃
棉。
4三通活塞:
辅助调节氧气流量。
5管式电炉:
可以加热至800℃的温度。
6石英管:
大约600长,可以承受维持800℃的温度。
7除水除尘器:
内置无水高氯酸镁。
8流量调节器:
调节流量。
9红外吸收器:
带一氧化碳转换器。
氧气经两级压力调节器至净化炉,净化炉是一个盛满氧化铜石英管,温度维持在450℃~500℃,氧气经净化炉净化后,其中含有的微量有机物氧化为二氧化碳和水。
经高氯酸镁、碱石棉吸收水和二氧化碳后,纯净氧气在管式炉中与铜管内表面的碳进行反应,产生二氧化碳,与氧气经除尘器、除水器一起,进入检测器,检测器包含一氧化碳转化器、除硫器、二氧化碳红外线检测器。
由原方框组成的简图,改成实物图形的示意图,更加直观。
根据实际操作情况及企业建议,在实际操作中将锡囊放入铜管内,很容易发生倒翻,因此送审稿中去掉锡囊的使用,在实际操作中将液体放入瓷舟中或直接放入铜管中,蒸发干燥后再进行测试。
4.5.2微量移液管(枪)误差小于1%。
由于调整了加液方法,液体加液量更加灵活,因此将移液枪的要求改为误差
小于1%。
表2某品牌手动可调移液枪不同加液体积的容量允许误差。
可以看出,小体积下会有较大的误差,因此采用了两种浓度的标准溶液,减少小体积下的误差。
4.5.3量具
应满足测量精度要求,测量精确到0.1。
表2某品牌手动可调移液枪不同加液体积的容量允许误差
4.6试样
4.6.1一般要求
铜管及铜管件试样经制样与清洁后进行的碳含量测定,应注意下列操作要
求:
a)金属工具应没有涂漆;
b)夹具的材料应为铜、铝、钢材或替代材料制成,替代材料应洁净;
c)在试样制备前,所有的切割刀和钳子等工具都应脱脂处理;
d)脱脂处理应用带有四氯乙烯、三氯乙烯或三氯乙烷或其他类似的溶剂(如丙酮)的软布擦拭。
这些溶剂也用于试样的清洁处理;
e)应有适当的保护手套以避免皮肤直接接触试样表面;
注意:
在清洁操作和试验操作之间,试样应保持在无污染环境中,如清洁实验室或放有氢氧化钠小球的干燥器。
试验应在试样清洁后约5小时之内完成,如没有,试样应重新清洁。
本节主要说明试样加工时应注意的一些情况。
应防止油漆、油脂等物质在加工过程中与试样接触。
同时,指明了试验应在试样清洁后约5小时之内完成。
4.6.2试样的清洁
4.6.2.1试样的清洁及封闭方法
4.6.2.1.1试样的清洁方法有表3中规定的3种。
表3试样的清洁方法
将723-2009中的所涉及的三种清洁方法归纳在一起,定义为方法A、方法B
和方法C,避免了之后标准中的多次重复叙述,更符合我国标准的叙述习惯。
同时,将铜管和铜管件清洁方法进行了合并,减少重复,更加简洁。
4.6.2.1.2试样的封闭方法如下
一般试样采用适当尺寸的硅树脂或氯丁橡胶封堵管材的一端的封闭方法。
软态铜及铜合金管或管件也可采用将管材放置在夹具中,压扁管头一端约20,将压扁
的一端折叠,再次将管材放置在夹具中,压扁相邻一端约20的封闭方法。
将封闭方法在此说明,减少重复,更加简洁。
4.6.2.2残碳含量试样的清洁
对试样的内表面采用方法A清洁,然后进行封闭,对外表面采用方法B清洁,得到残碳含量试样。
对于软态管材,也可采用该方法:
对试样的内表面采用方法A清洁,对外表面采用方法C
清洁,得到残碳含量试样。
4.6.2.3全碳含量试样的清洁
对试样先进行封闭,然后对外表面采用方法B清洁,得到全碳含量试样。
对于软态管材,也可采用该方法:
对试样的外表面采用方法C清洁,得到全碳含量试样。
4.6.2.4空白试样的清洁
直接使用方法B对试样的内外表面进行清洁,得到空白试样。
4.6.3试样的制备
对于使用方法B清洁过的试样,从塞紧或压扁的铜及铜合金管或管件端部(如需要,应先去掉端部的塞子)开始切除25mm长部分。
用清洁的量具测量所需的管材长度,以达到内表面积为2000mm~2500mm。
用清洁的方形锯或密齿的弓形锯等工具切取需要的长度,应避免试样过热。
如试样的长度大于样品放置室中规定的燃烧装置燃烧区的长度,将管材切为两段,以便两段试样可同时进入燃烧区。
如使用电动锯,也应保证与管材所有表面接触的锯面已进行脱
脂处理。
当对管材进行切割和锉时,应保证管样固定牢固(如置入钳子中),而无过分的扭曲。
当铜及铜合金管或管件直径超过炉子直径时,使用压扁铜及铜合金管或管件的方式得到一个内表面积符合试验要求的试样。
压扁操作应在经三氯乙烯或三氯乙烷脱脂处理的铝质钳子或其他替代材质的钳子中进行,其他代替材质不能对试样的清洁造成破坏。
4.6.4内表面积的计算
铜及铜合金管或管件试样为规则的圆柱形,通过测量管材的内径和长度计算得到内表面,按公式
(1)计算。
测量精度为±0.1。
当管材太长需切为两段时,切割导致的长度减少,应对表面积进行重新计算。
SdL
(1)
式中:
2
S——内表面积();
d——内径();
L——长度()。
其他形状试样的内表面积的计算,按相应方法计算。
内表面积计算公式根据样品的特点,多种多样,如产品标准中有说明,则可以根据产品标准中的说明进行计算。
4.7试验步骤
4.7.1试样
取制备完毕的试样(见6.3)。
写明试验用的试样必须按标准要求进行制备。
4.7.2测定次数
独立地进行两次测定,取其平均值。
与一般化学分析方法要求一样,说明必须要进行两次测定,并取平均值为最终结果。
4.7.3分析前的准备
按仪器说明书更换失效的试剂管,调试检查仪器,使仪器处于正常稳定状态。
在仪器使用前应对仪器进行检查,使仪器处于正常稳定状态。
相应加热炉应
预先升温至相应温度。
4.7.4空白试验
在测量之前,按以下方法进行二次空白试验。
取空白试验试样(见6)。
空白值用空白试样的总表面积(内外表面积)来计算。
空白值为两个试样测试所获得的算术平均值。
空白值应不大于1.52。
如果空白值较大,应重新评估试样的制备和设备的空白值。
根据50个空白试验的测试结果,测定结果均小于1.02,因此将标准中,空白值由不大于12,调整为不大于1.52。
表4为50个空白试验测定结果。
表4空白试验测定结果
4.7.5校正试验
根据试样中碳含量,选择相应的量程或通道,用已知的碳含量的试样进行校准,也可以用空白试验的试样加入甘露醇标准溶液(4.9、4.10)或纯度99.992
(4.11),进行校正,测得结果的波动应在允许差范围内,以确认仪器的线性,否则应按仪器说明书校正仪器,得到精确的线性校正系数。
当分析条件变化时要重新测定空白值并进行校正试验。
4.7.6测定
试验前,应确保试样清洁不超过5h,见6.1。
接通电源,升温。
铜管和铜管件升温至800°C,铜合金管件升温至550°C。
通入氧,检查整个装置的管路及活塞是否漏气。
调节并保持仪器装置在正常
的工作状态。
启开玻璃磨口塞,迅速将试样放入石英管内,用长钩推至瓷管加热区中部,立即塞紧磨口塞,燃烧不少于2。
经过燃烧和测量之后,启开玻璃磨口塞,用长钩将试样拉出。
此章节讲述了试验次数、空白值的计算公式、校准试验,燃烧分析测定的具体过程。
文中要求试验次数为2次,对如何进行校正试验进行了说明。
提高温度有助于内表面碳含量的燃烧,加长燃烧时间有利于碳的燃烧,但由
于不同的铜合金熔化温度不一致,长时间燃烧容易增加空白值,也不利于检测,
在查阅相关资料后,确定纯铜的温度设定为800℃,铜合金的温度设定为550℃,燃烧时间定为3分钟。
表5为不同牌号的铜合金的熔化温度表
表5同牌号的铜合金的熔化温度表
H96
液相线温度
1071.4
固相线温度
1056.4
H90
1046.4
1026.3
H85
1026.3
991
H80
1001.2
966
H75
981.2
—
H70
951
916
H68
939
910
H65
936
906
H63
911
901
H62
906
899
H59
896
886
89-2
1040
1010
66-0.5
940
905
63-3
906
886
63-0.1
62-0.8
62-3
900
885
62-2
905
885
61-1
900
885
60-2
895
880
59-3
59-1
900
885
77-2
971
931
67-2.5
971
932
66-6-3-2
900
—
61-4-3-1
921
903
60-1-1
905
—
59-3-2
957
893
57-3-1
870
—
合金牌号熔化温度/℃
液相线温度固相线温度
58-2
881
866
62-3-3-0.7
901
855
90-1
1016
906
70-1
936
891
62-1
907
886
60-1
901
885
59-1-1
901
886
65-5
960
—
80-3
900
—
713431
944
988
8133
950
980
81332
949
987
92
1048
1061
9442
1040
1060
103
1039
1047
1032
1040
1045
1044
1037
1054
10432
1040
1045
11761
1050
1070
2.5
1090
1080
3-1
1026.3
971
铬青铜
1075~1080
1070~1073
0.2
1081.5
—
0.4
1066.4
966
1
1076
1040
同时,对T2铜和H62黄铜进行了试验燃烧后再次燃烧的试验。
在对T2纯铜管按标准进行燃烧后,冷却,然后在950℃条件下,进行3分钟的燃烧,试验结果见表6。
对H62黄铜管按标准进行燃烧后,冷却,然后在800℃条件下,进行3分钟的燃烧,试验结果见表7。
从表中可以看出,再次首次燃烧测量结果即标准结果数值稳定,再次燃烧测量结果符合标准空白值的要求,可以认为第一次燃烧试验铜管内表面碳含量已经燃烧完全。
表6
1
2
3
4
5
0.05
0.06
0.05
0.06
0.06
样品序号
首次燃烧测量结果
(2)
0.008
0.010
0.005
0.008
0.006
252,空白试验结果0.006,再次燃烧测量结果未减去空白试验。
表
7
1
2
3
4
5
0.09
0.09
0.08
0.07
0.09
0.006
0.010
0.010
0.008
0.011
再次燃烧测量结果
(2)
注:
内表面面积
样品序号
首次燃烧测量结果
(2)
再次燃烧测量结果
(2)
注:
内表面面积252,空白试验结果0.006,再次燃烧测量结果未减去空白试验。
4.8分析结果的表示
2
碳含量以表示,为两个试样测试所获得的算术平均值。
碳含量包括:
残碳
()、