计算机在材料加工中的应用.docx
《计算机在材料加工中的应用.docx》由会员分享,可在线阅读,更多相关《计算机在材料加工中的应用.docx(8页珍藏版)》请在冰豆网上搜索。
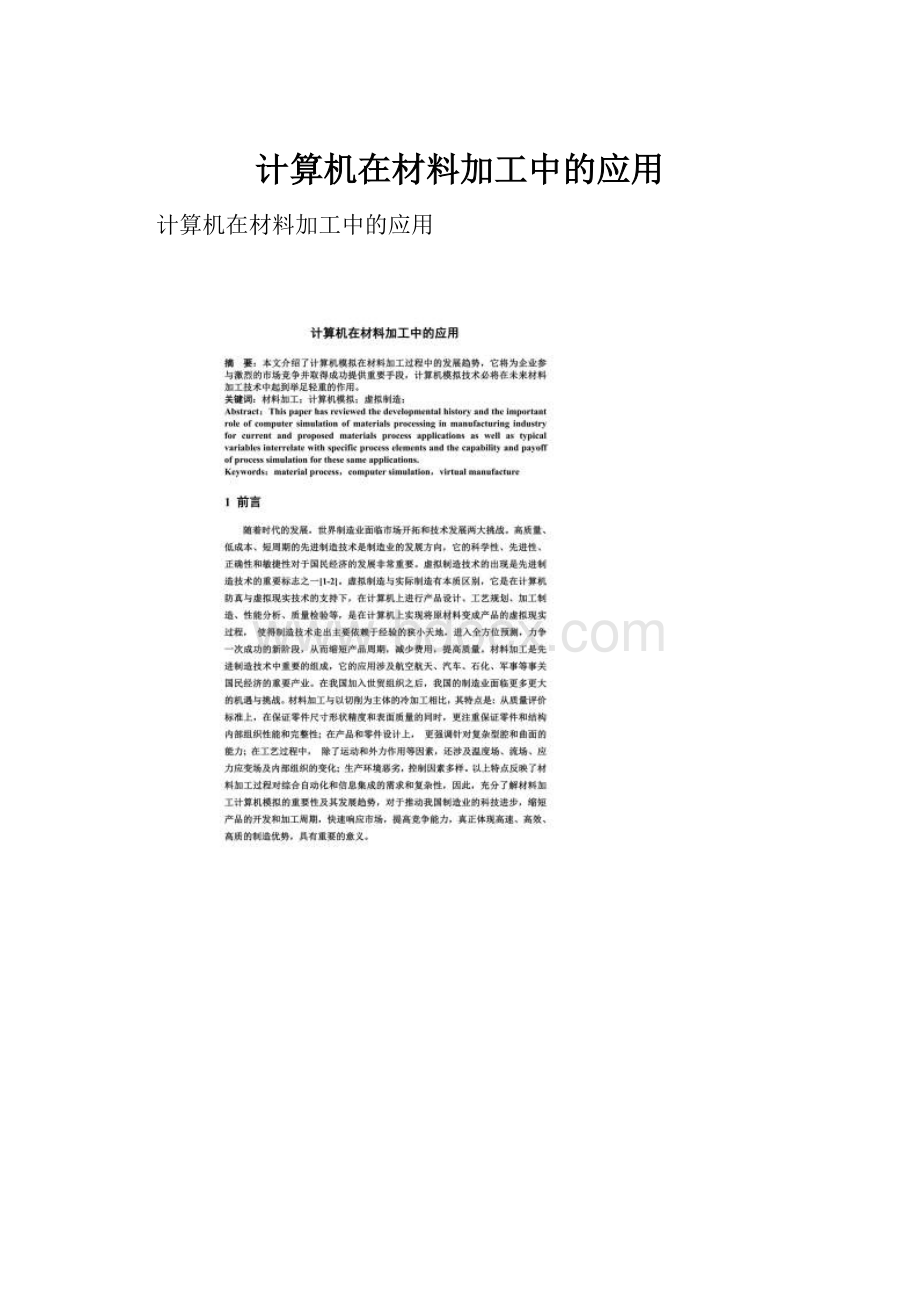
计算机在材料加工中的应用
计算机在材料加工中的应用
品的缺陷等问题,符合金属成形对于精密化模拟分析的要求。
目前,二维大变形弹-(粘)塑性有限元法模拟技术已日趋成熟,并已在工程中得到成功的应用。
但大变形弹-(粘)塑性有限元法是建立在有限变形理论基础上的,需要对变形梯度进行多次分解,从分析金属成形过程的角度出发,计算工作量大,而金属成形过程通常是在高温下进行的,工件在发生变形的同时伴随有温度的变化,因此,在分析金属成形过程模拟中,还必须考虑温度的影响,即进行温度场与变形场的耦合计算,特别是工程中可以简化为二维分析的问题并不多,三维模拟是必然趋势,三维问题分析在数学模型和图形处理上的复杂程度大大增加,由此引起的计算量猛增,比二维问题的计算量高出几十倍甚至上百倍,这对于计算机存储量的要求也随之增加。
近年来,由于计算机软硬件技术的迅速发展和数值计算方法的不断完善,使三维问题的分析成为可能。
一方面,人们在研究提高计算速度的方法,开发了大规模计算问题的并行计算方法(ParallelComputation),利用并行处理机中多CPU可同时工作的特点,配以软件编程中的并行处理方法,使计算速度大为加快,目前国际上许多商业软件都推出了并行版,如ANSYS、MARC、LS-DYNA3D等;另一方面人们在研究改善计算方法,众所周知,金属成形过程中,坯料的变形特别大,若采用更新的拉格朗日法(UpdatedLagrangianMethod)进行计算时[10],初始划分的单元网格逐渐畸变,若将已经畸变的网格形状作为增量计算的参考构形,将导致计算精度降低,甚至引起不收敛,为克服上述问题,通常当网格畸变到一定程度后,必须停止计算,重新划分适合于计算的网格,通过新旧网格间信息场量的插值传递,再继续进行计算,要完成一个成形问题的模拟,通常需要多次重划网格,这将导致计算量的增加和由于多次插值带来的计算精度的降低,因此,许多研究开发人员正致力于改进三维网格重划的自适应能力和自动化程度,改进新旧网格间信息传递的插值方法,取得了可喜的进展。
同时,开发了ALE法(ArbitraryLagrangianEulerianMethod)和显式解法(ExplicitSolution)[11],而ALE法不再象Lagrangian公式中将网格固定在材料上,而是不依赖于材料的运动而移动,因此可控制网格的几何形态,ALE通过利用高阶的技术不断进行网格重划,从而避免上述问题,提高计算速度和精度,这对于为提高计算精度和效率而进行的网格细划十分有利,该方法已在MSC/DYTRAN、PressForm等软件中得到成功的应用,而显式解法主要是为解决非线性问题隐式求解时为保证求解精度需反复迭代,使计算量猛增的问题,目前该方法已成功地应用于LS-DYNA3D中[12]。
另外,随着计算机软硬件的迅速发展,计算速度问题也将逐步得到解决。
到目前为止,二维大体积金属成形过程有限元模拟技术已趋成熟,国内外先后开发了许多商品软件,这些软件多适用于二维问题、伪三维问题及简单三维问题的分析。
通过使用弹-塑性-实时响应模型,可确定完整的应力、应变和挠曲变化状况,残余应力也容易被计算。
近年来,金属成形工业对三维过程模拟提出了更高更精确的要求。
对于处理复杂三维金属塑性成形问题,虽然存在模具型腔几何形状描述、动态边界条件及网格重划等技术难点[5],随着计算方法的完善和计算机技术的进步,开发出使用便捷且适用范围广的三维有限元程序已成必然。
一方面研究提高计算速度的方法,通过计算机技术中多个CPU可同时运行的并行处理技术和软件编程中的并行处理方法,开发大规模计算问题的并行计算方法,从而大大提高计算效率;另一方面不断完善计算方法,对于影响三维模拟精度的若干技术问题,如初始速度场的生成、摩擦边界条件的处理、刚性区和塑性区的区分、缩减因子的确定、收敛准则的选择和热力耦合等问题,在保证求解精度和效率的前提下,均可采用二维有限元模拟中相关的算法和处理技术。
而模具型腔几何形状描述、动态边界条件及网格生成和重划等技术难点与二维模拟相比有较大的区别,这些问题处理的正确与否将直接关系到模拟分析的可靠性和求解效率。
因此,人们在不断地寻求解决的方法。
Cho等[6]为了解决复杂三维问题,采用考虑热传导的三维热黏塑性有限元模型,将一个无法用解析式描述的任意复杂形状的模具表面,通过Ferguson分片,用一个分片连续的形式给出,将被网格重构的变形体分为表面自适应层和中心区两部分,提出一种基于体适应映射法的三维网格重构技术。
所提出的网格重构方法是以产生线性八节点六面体单元为基础的。
在表面自适应层上自动产生网格后,中心区通过体适应映射法自动生成网格,并对万向节的热锻过程进行了完整的模拟。
此外,在计算机上处理三维金属成形,还需进一步提高模拟的可视化水平,拥有良好的用户界面是非常重要的。
随着计算机装载了三维图形处理程序及计算速度和硬件水平的提高,可在前后处理中大量应用可视化技术,用户在二维屏幕上可直接观看物体的三维图形和数据。
在金属成形过程模拟中,可通过采用切片技术和镜像显示技术观测物体某一横截面或整个结构的变化情况,点跟踪技术可使用户了解在成形过程中原始材料上任意点的流动情况,同时绘制这些点的过程参数变化曲线图。
2.3单目标优化设计到多目标优化设计渗透
金属材料的成形通常在高温下进行,工件塑性成形是一个复杂的热力学过程,受到应力应变分布不均匀、硬化和再结晶等因素的影响,而工件的形状和尺寸精度及其内部质量和性能决定着产品质量。
热处理过程作为材料加工中不可缺少的环节,是一个包含温度、相变、应力/应变相互作用的复杂过程,是一个多机制综合作用的过程。
对其进行组织性能预测的数值模拟,首先必须通过大量实验,使模拟技术建立在可靠的试验数据基础上,建立准确的数学模型,将组织场-变形场-温度场三者进行耦合计算,将成形过程与热处理工艺的模拟与质量控制相结合,使模拟结果更准确。
由此可作为参考对影响成形过程和热处理工艺的各种工艺参数进行综合优化设计,以适应先进制造技术的要求(高精度、高质量、高效率)。
2.4虚拟制造系统的开发
现代化制造加工业的目的应是适应全球市场需求,目标应是应用CAD/CAE/CAM技术来实现优质、高效、低费用产品生产。
为适应现代化制造业中要求柔性化、快捷、低成本及高质量的要求,在生产设计中互相借助彼此硬件和软件技术,把最先进的技术集中起来不失为一种好的解决方法。
但这种集成与常规的集成技术不同,它是虚拟的,是一种并行工程思想与先进制造技术的综合体现。
它主要包括:
1、敏捷制造(AM):
利用“竞争—合作/合同”机制,发挥局部特长;2、并行工程(CE):
实现同步设计、加工、核算和管理;3、专家系统(ES):
实现领域知识和复杂问题的评价和求解;4、网络技术及先进的管理系统(NT-MS):
实现先进集成技术的最快捷的手段。
图1为虚拟系统的结构图。
基于虚拟系统的制造业,将是21世纪市场上一种较好较快实现产品的运营方针,可大大减低新产品开发风险,提高经济效益,最终使企业在激烈的市场竞争中立于不败之地。
图1 虚拟系统的结构图
2.5反向设计技术与专家系统
在某一给定的成形工艺中,最终产品的材料状态和几何形状取决于诸多工艺参数(加载条件、模腔形状、模具润滑条件、初始坯料几何尺寸等),若考虑某些工艺参数固定不变,则通过对另一些工艺参数的反复模拟和修改,以得到所希望得到的最终产品的材料状态和几何尺寸,成形工艺的设计可认为是对于初始坯料和随后的各预成形坯及模具的设计,但这种反复迭代的方法需要花费大量的计算时间是极不经济的。
八十年代中,S.Kobayashi等系统研究了这一问题,提出了反向模拟技术(BackwardTracingTechnique),即从一给定的最终形态,沿着相反的加载路径,反向模拟实际的工艺过程,该方法为工艺设计开辟了新途径。
近十年来,反向模拟技术得到了一定的进展和应用,但始终没取得突破性进展,其主要原因是从最终形态反向模拟时,无法给定初始场量,因此获得的初始毛坯设计在理论上存在缺陷,无法估计设计所带来的误差。
近年来,工艺设计与优化的技术取得了新的进展,提出了敏感性分析(SensitivityAnalysis)的反向设计方法(InverseMethod),该方法将预成形设计和模具设计问题处理为优化问题,用严密的数学公式进行描述,将优化问题的目标函数定义为一组给定设计变量中所希望的最终状态和数值计算状态之间的误差的某种度量,敏感性分析是一种广泛用于计算目标函数梯度的方法,由于所求解的问题高度非线性并具有历史依赖性,因此,最适合应用直接差分法(DirectDifferentiationMethod),控制方程直接由敏感性场的场量公式差分得到。
该方法已成功地应用于坯料和模具形状的优化设计中。
另外,在材料加工领域中,许多设备和工艺问题主要还是利用已经总结出来的经验公式和参数,加上仍存在于专家头脑中的经验知识来解决。
在实际生产中,经验知识的运用往往多于数学分析运算,且很有效,因此,如何充分发挥这些知识的作用,充分利用这一资源,具有非常重要的意义。
专家系统就是很好的解决方法,它利用知识的显式表示、事实和推理技术,以解决通常需要专家才能解决的问题。
一个典型的专家系统包括:
知识获取的装置,收集专家们在该领域的规则和知识,这一装置也包括规则编辑器,允许用户改进现有规则和增加新的规则;存储事实和规则的数据库,该数据库通常可与其它数据库系统结合;一个推理机,以确定如何应用知识规则来解决问题:
一个用户界面,以允许非专家的用户使用该系统来解决特殊问题。
该方法正广泛应用于材料加工的工艺设计中。
2.6新模拟技术开发
数值分析的巨大成果是有限元方法。
但是,当网格高度畸变时,这种以单元作为基本概念的方法却有许多难以处理的问题,主要原因是网格的存在妨碍了处理与原始网格线不一致的不连续性和大变形。
在处理这类问题时,有限元法通常采用网格重构,但这样不仅计算费用昂贵,而且会使计算精度受损[13]。
为解决上述问题,近年来,一种新的无网格数值方法正在迅速发展。
无网格方法将连续体离散为有限数目的质点,位移场函数在没有明显网格的情况下通过这些质点的插值得到,该方法仅采用基于点的近似,而不需要节点的连续信息,不仅避免了繁琐的单元网格生成,而且提供了连续性好、形式灵活的场函数,具有前后处理简单、精度高等方面的优点。
在处理弹塑性、裂纹扩展、移动界面、高速碰撞以及具有大变形特征的工业成形问题时具有重要的研究价值和广阔的应用前景。
无网格方法以其在场函数近似、局部特征描述等方面特有的优点,越来越受到国内外学者的关注,呈现出强劲的发展势头,具有广阔的应用前景和重要的研究价值。
3结语
先进制造技术是制造业赖以生存、国民经济得以发展的主体技术,以制造技术为焦点的技术竞争已在全球展开。
计算机模拟技术使制造技术走出从前主要依赖于经验的狭小天地,进入全方位预测,力争一次成功的新阶段,从而实现有效的现代工程设计和迅速的新产品开发。
随着计算机模拟技术的不断完善发展,它将继网络技术和数据库技术后成为21世纪材料加工技术的又一技术支撑环境。
参考文献:
[1]AliheimerWE,ShahinpoorM,StantonSL.VirtualManufacturing[R].Albupuerpue,NewMexico.USA,1995.
[2]HatamuraY,NagaoTMitsuishi.AfundamentalstructureforIM.[J].ProcisionEngin.,1993,15(4):
266-273.
[3]NakamachiE,DongX.Elastic/Crystalline2viscoplasticfiniteelementanalysisofdynamicdeformationofsheetmetal[J].Engineeringcomputation,1996,31:
56-62.
[4]董湘怀.金属塑性变形中织构演化的计算机模拟[J].塑性工程学报,1998,5(3):
8-14.
[5]ChoJR,YangDY.Three-dimensionalfiniteelementsimulationofaspiderhotforgingprocessusinganewremeshingscheme[J].JounalofMaterialsProcessingTechnology,2000(99):
219-225.
[6]王纪武,胡忠,王本一,等.高精度三维塑性有限元网格重划技术的研究[J].塑性工程学报,1998,5
(1):
15-19.
[7]ShenShan-fu,DawasonPaulR.(Eds.)SimulationofMaterialsProcessing:
Theory,MethodsandApplications.ProceedingsoftheFifthInternationalConferenceonNumericalMethodsinIndustrialFormingProcesses.NewYork,1995
[8]胡忠.塑性有限元模拟技术的最新进展.塑性工程学报,1994,1(3):
3~13
[9]胡忠,王志诚,陈国学等.塑性有限元数值模拟的二维及三维网格重划技术.清华大学学报,1996,36(3):
78~83
[10]DuttwellerRE,GriffithWMandJainSC.ProcessModeling-It'sHistory,CurrentStatus,andFuture.SAETechnicalPaperSeries.1991(No:
911138):
357~369
[11]BenedictDK.TheComputerIntegratedManufacturing(CIM)ofNetShapeForgedBevelGears,Journal.ofMaterialShapingTechnology,1989,7:
7~11
[12]SuzukiT.RecentDevelopmentofForginginJapan.InternationalJournalofMachineandToolsManufacturing,1989,29
(1):
5~27
[13]ArsenaultRJ,BeelerJRJr.andEsterlingDM.ComputerSimulationinMaterialsScience.ASMInternational,USA,1988
[14]王建国.基于快速原型技术的快速反馈设计系统研究(博士学位论文)北京.清华大学.1996