自考催化剂工程导论复习提纲完整.docx
《自考催化剂工程导论复习提纲完整.docx》由会员分享,可在线阅读,更多相关《自考催化剂工程导论复习提纲完整.docx(36页珍藏版)》请在冰豆网上搜索。
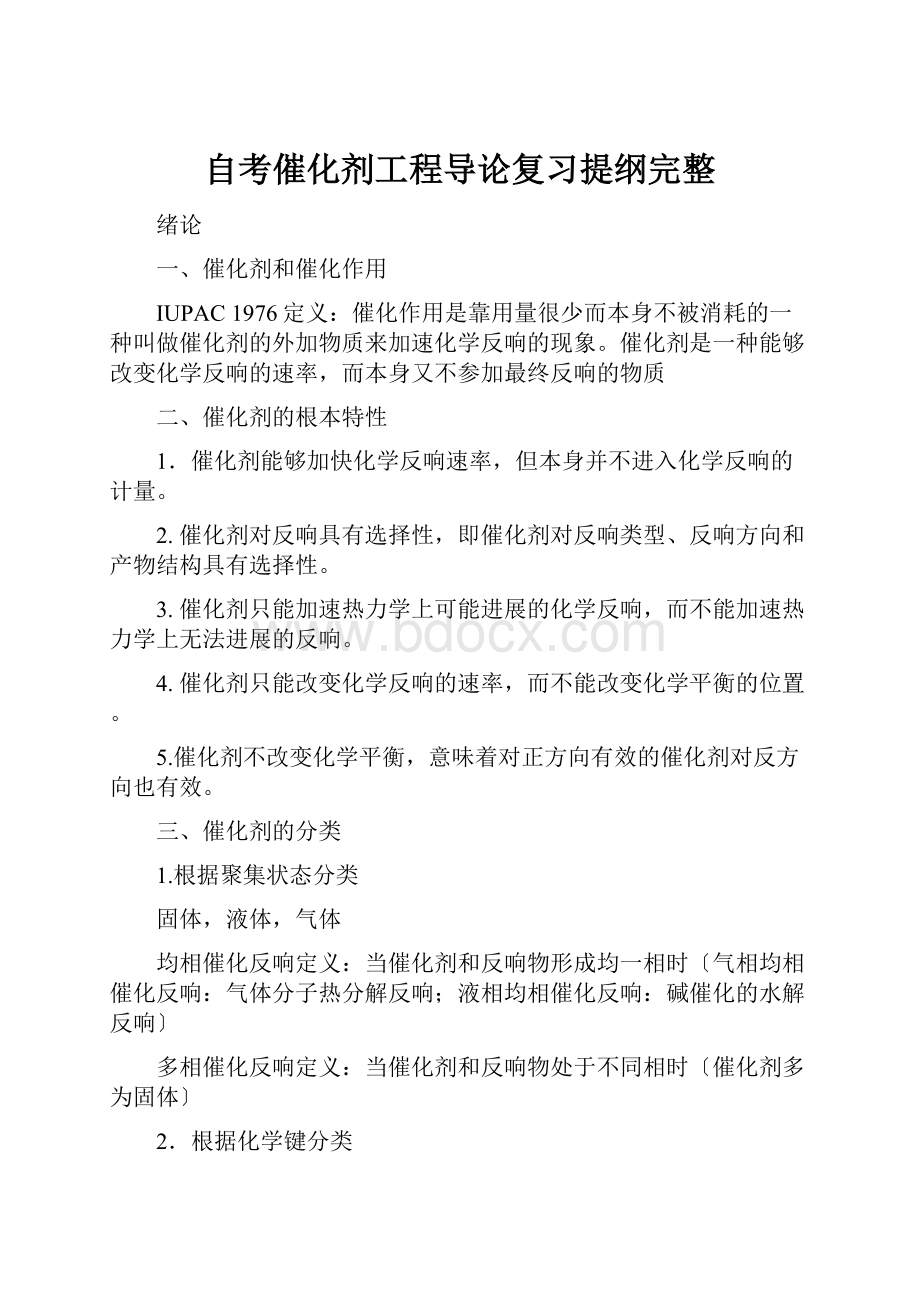
自考催化剂工程导论复习提纲完整
绪论
一、催化剂和催化作用
IUPAC1976定义:
催化作用是靠用量很少而本身不被消耗的一种叫做催化剂的外加物质来加速化学反响的现象。
催化剂是一种能够改变化学反响的速率,而本身又不参加最终反响的物质
二、催化剂的根本特性
1.催化剂能够加快化学反响速率,但本身并不进入化学反响的计量。
2.催化剂对反响具有选择性,即催化剂对反响类型、反响方向和产物结构具有选择性。
3.催化剂只能加速热力学上可能进展的化学反响,而不能加速热力学上无法进展的反响。
4.催化剂只能改变化学反响的速率,而不能改变化学平衡的位置。
5.催化剂不改变化学平衡,意味着对正方向有效的催化剂对反方向也有效。
三、催化剂的分类
1.根据聚集状态分类
固体,液体,气体
均相催化反响定义:
当催化剂和反响物形成均一相时〔气相均相催化反响:
气体分子热分解反响;液相均相催化反响:
碱催化的水解反响〕
多相催化反响定义:
当催化剂和反响物处于不同相时〔催化剂多为固体〕
2.根据化学键分类
金属键、等极键、离子键、配位键、金属键
3.按元素周期律分类
主族元素、过渡元素
4.根据催化剂组成与使用功能分类(P17)
类别
功能
例子
金属
加氢、脱氢、加氢裂解
Fe,Ni,Pt,Pd,Ag
半导体氧化物和硫化物
氧化、脱氢、脱硫
NiO,ZnO,MnO2,CrO3,WS2
绝缘性氧化物
脱水
Al2O3,Si2O3,MgO
酸
聚合、异构化、裂化、烷基化
H3PO4,H2SO4
5.按工艺与工程特点分类〔以组成结构、性能差异和工艺工程特点为依据〕
分为多相固体催化剂,均相配合物催化剂,和酶催化剂等三大类。
四、催化剂的化学组成和物理结构
1.多相固体催化剂〔使用比例最高〕
〔1〕主催化剂〔活性组分〕是起催化作用的根本性物质
〔2〕共催化剂是能和主催化剂同时起作用的组分
〔3〕助催化剂是催化剂中具有提高主催化剂活性、选择性,改善催化剂的耐热性、抗毒性、机械强度和寿命等性能的组分。
助催化剂本身无活性。
①结构助催化剂:
能使催化活性物质粒度变小、外表积增大,防止或延缓因烧结而降低活性等。
②电子助催化剂:
通过改变主催化剂的电子结构提高活性和稳定性。
③晶格缺陷助催化剂:
使活性物质晶面的原子排列无序化,通过增大晶格缺陷浓度提高活性。
②和③合称为调变性助催化剂
〔4〕载体是固体催化剂所特有的组分,起增大外表积,提高耐热性和机械强度的作用,有时还担当共催化剂或助催化剂的角色。
甾体是活性组分的分散剂、胶黏剂或支载物。
与助催化剂不同:
载体在催化剂中的含量远大于助催化剂。
载体分为低比外表积、高比外表积、中比外表积〔1-50或1-100〕
〔5〕其他稳定剂抑制剂等
稳定剂的作用:
从晶体结构的角度考虑,会导致结晶外表积减少的主要因素是由于相邻的较小的结晶的扩散、聚集而引起的结晶长大,像金属或金属氧化物以累简单的固体,如果它们是以细小的结晶形式存在,特别容易烧结。
鉴于这种理由,当催化剂中活性组分是一种熔点较低的金属时,通常还应含有很多耐火材料的结晶,后者起着“间隔体〞的作用。
常用的稳定剂有:
氧化铝、氧化镁、氧化锆
抑制剂定义:
如果在主催化剂中添加少量的物质,能使前者的催化活性适当降低,甚至在必要时大幅度下降,那么这种少量的物质称为抑制剂。
〔和助催作用相反〕
加抑制剂的目的〔场合〕:
过高的活性反而有害,它会影响反响器散热而导致"飞温",或者导致副反响家剧,选择性下降甚至引起催化剂积碳失活。
适时添加抑制剂,使为了使工业催化剂的诸性能到达均衡匹配,整体优化。
2.均相配合物催化剂
化学组成:
由中心金属M和环绕在其周围的许多其他离子或中性分子〔配位体〕组成
配位体:
含有两个或者两个以上孤对电子或π键的分子或离子,例如:
Cl-Br-,-,H2O,NH3,C2H4,(C6H5)3P等。
配合物催化剂的中心金属M:
多采用d轨道未填满电子的过渡金属,如:
Fe,Co,Ni,Ru,Zr,Ti,V,Cr,Hf等
均相配合物催化剂的缺点:
催化剂别离回收困难、需要稀有贵重金属,热稳定性差即对反响器腐蚀严重
配合物催化剂中:
一类是中心金属周围没有配位体存在的原子状态催化剂,另一类那么是中心金属持有假设干配位体。
3.生物催化剂:
酶
五、多相、均相催化剂的功能特点
优点
缺点
固体非均相催化剂
气液相产物易于固体催化剂相别离,满足其催化过程,仅需要简单的设备条件和有限的操作,催化剂耐热性好,因而易于控制,产物质量高
多相催化机理复杂,相间现象变得重要,扩散和吸收,吸附等所有因素,对反响速率起着重要的作用,说明反响机理分析困难,难以在实验室研究清楚。
均相催化
易于在实验室研究清楚,易于表征,由于均相配合物可溶于反响介质,分子扩散于溶液中,不受相间扩散的影响,因而它的活性往往比多相催化剂高
需要增加许多复杂的工艺操作,来解决催化剂的别离、回收与再生问题
酶
具有较高的活性和高选择性
六、多相、均相催化剂的同一性
1.在不参与最终产物但参与中间过程的循环而起做作用这一点上,二者共通。
2.与对应的给催化反响相比,催化反响的速度加快。
催化本质:
催化剂之所以具有催化活性,是由于它能够降低所催化反响的活化能,而催化剂之所以够降低所催化反响的活化能那么又是由于在催化剂的存在下,改变了非催化反响得历程。
催化剂对化学工业乃至整个国计民生的重要作用
(1)合成氨与合成甲醇催化剂
(2)催化剂与石油炼制与合成燃料工业
(3)根底无机化学工业用催化剂〔H2SO4〕
(4)根本与有机合成工业用催化剂
(5)三大合成材料工业用催化剂〔合成树脂与塑料、合成橡胶、合成纤维〕
(6)精细化工专用化学品中的催化
(7)催化剂在生物化工中的应用
(8)催化剂在环境化工中的应用
第二章工业催化剂的制造方法
一、沉淀法
以沉淀操作作为其关键和特殊步骤的制备方法,是制备固体催化剂最常见的方法之一,广泛应用于制备高含量得非贵金属,金属氧化物,金属盐催化剂或催化剂载体。
一般操作:
在搅拌的情况下把碱性物质〔沉淀剂〕参加金属盐类的水溶液中,再将生成的沉淀物洗涤过滤、枯燥、焙烧,制造出所需要的催化剂粉状前驱物。
沉淀法的关键设备一般是:
沉淀槽,其结构如一般的带搅拌的釜式反响器。
〔一〕沉淀法的分类
1.单组分沉淀法:
通过沉淀剂与一种待沉淀溶液作用以制备单一组分沉淀物的方法。
可以用来制备非贵金属的单组分催化剂或载体,如与机械混合和其他单元操作组合使用,又可以用来制备多组分催化剂。
氧化铝是最常见的催化剂载体。
分为酸法和碱法两大类。
酸法:
以碱性物质为沉淀剂,从酸化铝盐溶液中沉淀水合氧化铝
碱法:
以酸性物质为沉淀剂,从偏铝酸盐溶液中沉淀水合物,所用酸性物质包括硝酸,盐酸,CO2,等。
2.多组分共沉淀法:
共沉淀法是将催化剂所需的两个或两个以上组分同时沉淀的一种方法。
常用来制备高含量的多组分催化剂或催化剂载体。
优点:
一次可以同时获得几个催化剂组分的混合物,而且各个组分之间的比例较为恒定,分布也比拟均匀。
共沉淀法的分散性和均匀性好,是它较之于混合法等的最大优势。
例子:
合成CuO-ZnO-Al2O3三组分催化剂,将给定比例的Cu〔NO3〕2、Zn〔NO3〕2、Al〔NO3〕3混合盐溶液与Na2CO3并流参加沉淀槽,在强烈搅拌下,于恒定的温度与近中性的PH值下,形成三组分沉淀,沉淀经洗涤,过滤、枯燥、焙烧后,即为该催化剂的先驱物。
单组分沉淀法和多组分共沉淀法缺点:
会出现沉淀剂与待沉淀组分的混合不均匀、沉淀颗粒粗细不等、杂质带入较多等现象。
均匀共沉淀法可以克制此现象。
3.均匀共沉淀法:
是使待沉淀金属盐溶液与沉淀剂母体充分混合,预先造成一种十分均匀的体系,然后调节温度和时间,逐渐提高PH值,或者在体系中逐渐生成沉淀剂等方式,创造形成沉淀的条件,使沉淀缓慢进展,以制得颗粒十分均匀而且比拟纯洁的沉淀物。
例子:
为了制取氢氧化铝沉淀,可在铝盐溶液中参加尿素溶化其中,混合均匀后,加热升温至90-100℃,此时溶液中各处的尿素同时水解,释放出OH–。
4.浸渍沉淀法:
待盐溶液浸渍操作完成后,再加沉淀剂,使待沉淀组分沉积在载体上。
5.导晶沉淀法:
借助晶化导向剂〔晶种〕引导非晶型沉淀转化为晶型沉淀的快速而有效的方法。
制备分子筛很有效
〔二〕、沉淀操作的原理和技术要点
1.金属盐类的选那么
首选硝酸盐〔提供无机催化剂材料所需要的阳离子〕,金钯铂铱等贵金属氯化物〔氯金酸等〕提供对应的阳离子,铼的阳离子来自于高铼酸
2.沉淀剂的选择常用的沉淀剂:
NH4OH,NH3﹙NH4﹚2CO3:
碱类、碳酸盐类、有机酸、铵盐等。
沉淀剂的要求〔选择沉淀剂考前须知〕1〕.尽可能使用易分解挥发的沉淀剂2〕.形成的沉淀物必须便于过滤和洗涤3〕.沉淀剂的溶解度要大4〕.形成的沉淀物溶解度要小5〕.沉淀剂必须无毒,不应造成环境污染。
3.沉淀形成的影响因素沉淀过程:
①晶核生成和②晶核长大
〔1〕浓度:
晶形沉淀适当稀溶液中进展沉淀反响;非晶型沉淀,易在含有适当电解质的较浓的热溶液中进展沉淀。
〔2〕温度:
70~80℃〔低温时有利于晶核的形成,而不利于晶核的长大〕
〔3〕溶液的pH值的影响
〔4〕加料方式和搅拌强度
加料顺序有:
正加法——把沉淀剂加到金属盐溶液中。
逆加法——把金属盐溶液加到沉淀剂中称为逆加法。
并流加法——把金属盐溶液和沉淀剂同时按比例加到中和沉淀槽中。
注意:
逆加法在整个沉淀过程中pH值是一个变值。
搅拌晶型沉淀:
开场沉淀时,沉淀剂应在不断搅拌下均匀而缓慢的参加,以免发生局部过浓现象,同时也能维持一定生物过饱和度;非晶型沉淀:
宜在不断搅拌下,迅速参加沉淀剂,使之尽快分散到全部溶液中,以便迅速析出沉淀。
4.沉淀的陈化和洗涤
A陈化定义沉淀在其形成之后发生的一切不可逆变化称为沉淀的陈化。
陈化操作:
沉淀形成后并不立即过滤,而是将沉淀物与其母液一起放置一段时间。
影响因素:
时间,温度,母液的PH值等。
陈化作用:
〔针对晶型催化剂〕因为在陈化过程中,沉淀物与母液一起放置一段时间〔必要时保持一定温度〕时,由于细小晶体比粗大晶体溶解度大,溶液对于粗大晶体而言已达饱和,而对于细晶体尚未饱和,于是细晶体逐渐溶解,并沉积于粗晶体上,如此反复溶解,沉积的结果,根本上消除了细晶体,获得颗粒大小较为均匀的粗晶体。
注意:
多数非晶形沉淀,再沉淀形成后不采取陈化操作,宜待沉淀析出后,参加较大量热水稀释,以减少杂质在溶液中的浓度,同时使一局部被吸附的杂质转入溶液。
B洗涤:
以洗涤液除去固态物料中杂质的操作。
常用的洗涤液是纯水,包括去离子水和蒸馏水。
目的:
除去沉淀中的杂质沉淀带入杂质的原因:
外表吸附、形成混晶〔固溶体〕、机械包藏等。
溶解度很小的非晶型沉淀〔热的溶液洗涤〕;溶解度大的晶型沉淀〔冷的洗涤液洗涤〕
实际操作:
常用倾析法和过滤法〔P37〕
5.枯燥、焙烧和活化
枯燥:
是用加热的方法脱除已洗净湿沉淀中的洗涤液。
固体物料的脱水过程,通常在60~200℃下的空气中进展,一般对化学结构没有影响,但对催化剂的物理结构,特别是孔结构与机械强度会产生影响。
焙烧目的
1除去化学结合水和挥发性物质〔CO2、NO2、NH3等〕,使之转化成所需的化学成分和化学形态。
2借助固态反响、互溶、再结晶,获得一定的晶型、微粒粒度、孔径和比外表积等。
③让微晶适度的烧结,提高产品的机械强度,
焙烧的设备:
高温电阻炉、旋转窑、隧道窑、流化床等
从控制催化剂的孔径和比外表等,控制其初活性,还可以提高机械强度
活化〔复原〕:
经过焙烧后的催化剂〔或半成品〕,多数尚未具备催化活性,必须用氢气或其他复原性气体,复原成为活泼的金属或低价金属氧化物这步操作称为复原,亦叫活化
注意:
复原操作可以叫做活化,但是并非所有的活化操作都是复原操作。
比方:
脱硫催化剂,用钴钼催化剂,活性状态为硫化物,使用前要硫化,该操作为预硫化,非复原。
影响因素:
复原温度,压力,复原气体组成和空速等〔气-固相催化反响〕
强调:
温度的影响:
复原吸热反响,提高温度有利于催化剂的彻底复原,反之,提高温度不利于复原。
提高温度可以加大催化剂的复原速度,缩短反响时间,但温度过高,催化剂微晶尺寸增大,比外表积下降,复原速的太慢,影响催化剂的生产周期,而且也可能延长已复原催化剂暴露在水汽中的时间〔复原伴有水分产生〕增加氧化复原的反复时机,也使催化剂质量下降。
复原气体:
氢气,一氧化碳,烃类等含氢化合物〔甲烷、乙烯等〕工艺气体〔N2-H2,H2-CO〕一般,复原气中水分和氧的含量越高,复原后的金属晶体越粗。
沉淀法实例:
P39-P40
晶化导向剂,就是化学组成、结构类型与分子筛相类似、具有一定粒度的半晶化分子筛。
这种外加晶种引导结晶的方法称为导晶法。
导晶沉淀法制备分子筛以水玻璃、硫酸铝、氢氧化钠为原料。
二、浸渍法
浸渍法是将载体放进含有活性物质〔或连同助催化剂〕的液体〔或气体〕中浸渍,到达浸渍平衡后,将剩余的液体除去,再经过枯燥、焙烧和活化等与沉淀法相近的后处理。
〔浸渍过程〕
1.浸渍原理:
一方面是固体的空隙与液体接触时,由于外表X力的作用而产生毛细管压力使得液体透到毛细管内部;另一方面,是活性组分在载体外表上的吸附。
2.浸渍法优点:
1〕可以用既成外形与尺寸的载体,省去催化剂成型的步骤。
2〕可以选择适宜的载体,提供催化剂所需物理结构特性〔比外表积,孔半径。
机械强度、热导率〕。
3〕附载组分多数情况下仅仅分布在载体外表上,利用率高,用量少,本钱低。
〔这对Pt,Rh,Pd贵金属催化剂特别重要〕
浸渍法缺点:
焙烧分解工序常产生废气污染。
3.常用的载体:
氧化铝,氧化硅,活性炭,硅酸铝,硅藻土,浮石,石棉,陶土,氧化镁,活性白土
载体的选择:
惰性载体;载体与活性组分具有相互作用,它使活性组分有良好的分散并趋于稳定,从而改变催化剂的性能;载体具有催化功能。
活性物质一般采用硝酸盐、氯化物、醋酸盐、铵盐、熔盐,特性是溶解度大,结构稳定且在焙烧时可分解为稳定活性化合物。
4.浸渍液配制的原那么:
〔课本上没有〕
浸渍液的浓度必须控制恰当;浸渍液的浓度取决于催化剂中活性组分的含量。
通常用活性组分金属的易溶盐配成溶液,所用的活性组分化合物应该是易溶于水〔或其它溶剂〕的,且在煅烧时能分解成所需的活性组分,或在复原后变成金属活性组分;同时还必须使无用组分,特别是对催化剂有毒的物质在热分解或复原过程中挥发除去。
一般以去离子水为溶剂,但当载体能溶于水或活性组分不溶于水时,那么可用醇或烃作为溶剂。
5.活性组分的负载
活性组分在球形载体断面上:
蛋壳型、蛋黄型、蛋白型、均匀型。
〔图见P42〕
制备各种类型断面分布催化剂的方法是竞争吸附法。
在浸渍溶液中除活性组分外,还要再加以适量的第二种称为竞争吸附剂的组分,浸渍时,载体在吸附活性组分的同时,也吸附第二组分。
6.浸渍方法:
1)过量溶液浸渍法:
将载体浸入过量的浸渍溶液中,〔浸渍液体积超过载体可吸收体积〕,待吸附平衡后,沥去过剩溶液,枯燥,活化后得催化剂成品。
2)等体积浸渍法:
将载体与其正好可吸附体积的浸渍溶液相混合,由于浸渍溶液的体积与载体的微孔体积相当,只要充分混合,浸渍溶液恰好浸没载体颗粒而无过剩,可省去废浸渍液的过滤与回收。
3)屡次浸渍法:
重复屡次的浸渍,枯燥,和焙烧,为了制取活性物质含量较高的催化剂的方法。
原因:
浸渍化合物的溶解度小,一次浸渍的负载量少,需要重复浸渍屡次,第二,为了防止多组分浸渍化合物各组分的竞争吸附,应将各个组分按次序先后浸渍。
每次浸渍后必须进展枯燥和焙烧。
效率低。
除非特殊一般不用。
4)浸渍沉淀法:
即先浸渍而后沉淀的制备方法。
本法是某些贵金属浸渍型催化剂充用的方法。
优点:
制得的活性组分贵金属,不仅易于复原,而且粒子较细,并且还不产生高温焙烧分解氯化物时造成的废气污染。
5〕流化喷洒浸渍法:
对于流化床反响器所使用的细粉状催化剂,可应用本法,即浸渍溶液直接喷洒到反响器中处于流化状态载体上,完成浸渍后,接着进展枯燥和焙烧。
6〕蒸气相浸渍法:
可借助浸渍化合物的挥发性,以蒸气的形态将其负载道载体上去。
7.实例:
由乙炔制醋酸乙烯的醋酸锌/活性炭催化剂的制备〔等体积浸渍法〕;铂/氧化铝重整催化剂的制备〔过量浸渍法〕;浸渍型镍系水蒸气转化催化剂的制备〔屡次浸渍法〕;钯/炭粉状催化剂的制备〔浸渍沉淀法〕【P44-P45】
三、混合法
制备多组分固体催化剂时,常用的方法。
它使将几种组分用机械混合的方法制成多组分催化剂。
其原理是将组成催化剂的各种组分以粉状粒子的形态在球磨机或碾合机内边磨细边混合,使各组分粒子之间尽可能均匀分散。
可分为干法和湿法两种。
四、热熔融法
熔融法是在高温条件下进展催化剂组分的熔合,使其成为均匀的混合体,合金固溶体或氧化物固体。
适用于少数不得不经熔炼过程的催化剂,为的是要借助高温条件将各个组分熔炼成为均匀分布的混合物,甚至形成氧化物固溶体或合金固溶体。
固溶体:
只几种固体成分相互扩散所得到的极其均匀的混合体,也称固体溶液。
特征操作工序:
熔炼〔复杂、高能耗工序〕熔炼温度、次数、环境气氛、熔浆冷却速度等因素对催化剂的性能都会有一定影响,操作时应予以充分注意。
制备程序:
固体的粉碎,高温熔融或烧结,冷却、破碎成一定粒度、活化。
Raney镍制备
五、离子交换法
离子交换反响发生在交换剂外表固定而有限的交换基团上,是化学计量的,可逆的〔个别交换反响不可逆〕,温和的过程。
[利用载体外表上可进展交换的离子,将活性组分通过离子交换〔通常是阳离子交换〕交换到载体上,然后经过适当的处理,如洗涤、枯燥、焙烧、复原,最后得到金属负载型催化剂。
]
定义:
借用离子交换剂作为载体,以阳离子的形式引入活性组分,制备高分散、大比外表积、均匀分布的附载型金属或金属离子催化剂。
特点:
负载的活性组分分散度高,尤其适用于低含量,高利用率的贵金属催化剂的制备。
能将小至0.3nm~4nm直径的微晶的贵金属粒子负载在载体上,而且分布均匀;在活性组分含量一样时,催化剂的活性和选择性比一般用浸渍法制备的催化剂要高。
沸石作为无机交换物质,在催化反响中得到较多的应用。
1.由有无机离子交换剂制备催化剂
1〕沸石是由SiO2、Al2O3和碱金属或碱土金属组成的硅酸吕盐,特别是指Na2O、SiO2、Al2O3三者组成的复合结晶氧化物〔复盐〕
由于Na2O、SiO2、Al2O3三者数量比不用,形成了不用类型的分子筛:
根据晶型和组成中硅铝比不同,把分子筛分成A、X、Y、L、ZSM等各种类型。
硅铝比不同,分子筛的耐酸性、热稳定性等各不一样。
孔径分为3A4A5A等
注意:
高硅沸石〔丝光沸石和ZSM-5分子筛〕假设将Na+型转化成H+型分子筛,可直接用盐酸交换处理,而低硅A、X、Y型分子筛那么不能。
2〕钠型分子筛的一般制法
水热合成和碱处理两大类
水热合成:
在适当的温度下进展,反响温度在20~150℃之间,称为低温水热合成反响;反响温度高于150℃,称为高温水热合成反响;所用原料主要是用含硅化合物、含铝化合物、碱、水。
碱处理法所用的原料有高岭土、膨润土、硅藻土、火山玻璃等天然矿物,也可采用人工合成的凝胶颗粒。
Y型分子筛,偏铝酸钠、氢氧化钠和水玻璃反响生成硅铝酸钠,称为成胶
成胶以后的硅铝酸钠凝胶经一定时间和温度晶化成晶体,这相当于前面沉淀法中的陈化工序。
晶化温度和时间应严格控制,且不宜搅拌过于剧烈,通常采用反响沸点左右为晶化温度,Y型分子筛一般控制温度为97~100℃
ZSM-5分子筛主要原料Na2SO4、NaCl、Al2(SO4)3、硅酸钠、有机铵盐
3〕分子筛上的离子交换
最常用的例子交换法是常压水溶液交换法〔一般酸性溶液下交换〕
交换液的酸性以不破坏分子筛的晶体结构为前提,将质子H+引入沸石结构,得氢型分子筛。
低硅沸石一般用铵盐溶液交换,形成铵型沸石,再分解脱除NH3后间接氢化。
高硅沸石由于耐酸,可直接用酸处理,得氢型分沸石。
2.由离子交换树脂制备催化剂
离子交换树脂可以看作是不溶于水和有机溶剂的固体碱或固体酸。
有机离子交换剂缺点:
机械强度低,耐磨性差,耐热性往往不高,再生时较分子筛催化剂困难。
离子交换树脂是一种聚合物,带有相应的功能基团。
离子交换树脂可以分为阳离子交换树脂和阴离子交换树脂。
1〕强酸性阳离子树脂
这类树脂含有大量的强酸性基团,如磺酸基-SO3H,容易在溶液中离解出H+,故呈强酸性。
树脂离解后,本体所含的负电基团,如SO3-,能吸附结合溶液中的其他阳离子。
这两个反响使树脂中的H+与溶液中的阳离子互相交换。
2〕弱酸性阳离子树脂
这类树脂含弱酸性基团,如羧基-COOH,能在水中离解出H+而呈酸性。
树脂离解后余下的负电基团,如R-COO-(R为碳氢基团),能与溶液中的其他阳离子吸附结合,从而产生阳离子交换作用。
这种树脂的酸性即离解性较弱,在低pH下难以离解和进展离子交换,只能在碱性、中性或微酸性溶液中(如pH5~14)起作用。
3〕强碱性阴离子树脂
这类树脂含有强碱性基团,如季胺基(亦称四级胺基)-NR3OH(R为碳氢基团),能在水中离解出OH-而呈强碱性。
这种树脂的正电基团能与溶液中的阴离子吸附结合,从而产生阴离子交换作用。
这种树脂的离解性很强,在不同pH下都能正常工作。
它用强碱(如NaOH)进展再生。
4〕弱碱性阴离子树脂
这类树脂含有弱碱性基团,如伯胺基(亦称一级胺基)-NH2、仲胺基(二级胺基)-NHR、或叔胺基(三级胺基)-NR2,它们在水中能离解出OH-而呈弱碱性。
这种树脂的正电基团能与溶液中的阴离子吸附结合,从而产生阴离
子交换作用。
六、催化剂的成型
1.成型工艺概述
形状、尺寸不同,甚至催化剂外表粗糙度不同,都会影响催化剂的活性、选择性、强度阻力等性能。
一般而言,这里最核心的影响是对活性、床层压力降和传热三个方面的影响。
成型原那么:
改变催化剂形状的关键问题,是在保证催化剂的机械强度以与压降允许的前提下,尽可能地提高催化剂的外表利用率〔即活性〕。
2.催化剂形状与要求
比方:
固定床催化剂中圆柱形与其变体,球形催化剂适用最广。
圆柱形有规那么的、光滑的外表,易于滚动,充填均匀,空心圆柱形那么有表观密度小,单位体积内催化剂外表积大的优点。
催化剂颗粒的形状、尺寸和机械强度要能与相应的催化反响过程和催化反响器相匹配。
〔1〕固定床用催化剂强度、粒度允许X围较大,过去,形状不一催化剂易造成气流分布不均。
后改用尺寸一样。
〔2〕移动床用催化剂直径3~4mm,或更大的球形颗粒〔通常为无角的小球〕
〔3〕流化床用催化剂直径20~150μm或更大直径的微球颗粒
〔4〕悬浮床用催化剂在反响时使催化剂在液体中易悬浮循环流动,通常用微米级至毫米与的球形颗粒
3.成型方法选择
主要考虑两方面因素:
①成型前物料的物理性质②成型后催化剂的物理、化学性质。
4.成型助剂添加:
胶黏剂和润滑剂
添加目的:
为了提高催化剂强度和降低成型时物料的内部或物料与磨具之间的摩擦力,有时需要在配方中参加某种胶黏剂和润滑剂。
胶黏剂的主要作用是增加催化剂的强度。
胶黏剂分三类:
根本胶黏剂:
沥青石蜡树脂
薄膜胶黏剂:
水、水玻璃〔用量主要取决于物料的性质〕
化学胶黏剂:
铝溶胶〔通过胶粘剂组分之间发生化学反响或胶粘剂与物料之间发生化学反响〕
强调去除胶黏剂:
催化剂成型后,都不希望产品被胶黏剂污染,所以应中选用枯燥或焙烧过程中可以挥发或分解的物质。
润滑剂:
多为可燃火可挥发物质,能在焙烧中分解,故可同时起造孔作用。
〔石墨、甘油〕
固体润滑剂一般使用较高压力成型的场合。
5.成型方法:
①压片成型:
和西药片剂的成型