纯净钢炉外精炼与连铸工艺和配置技术问题探讨.docx
《纯净钢炉外精炼与连铸工艺和配置技术问题探讨.docx》由会员分享,可在线阅读,更多相关《纯净钢炉外精炼与连铸工艺和配置技术问题探讨.docx(15页珍藏版)》请在冰豆网上搜索。
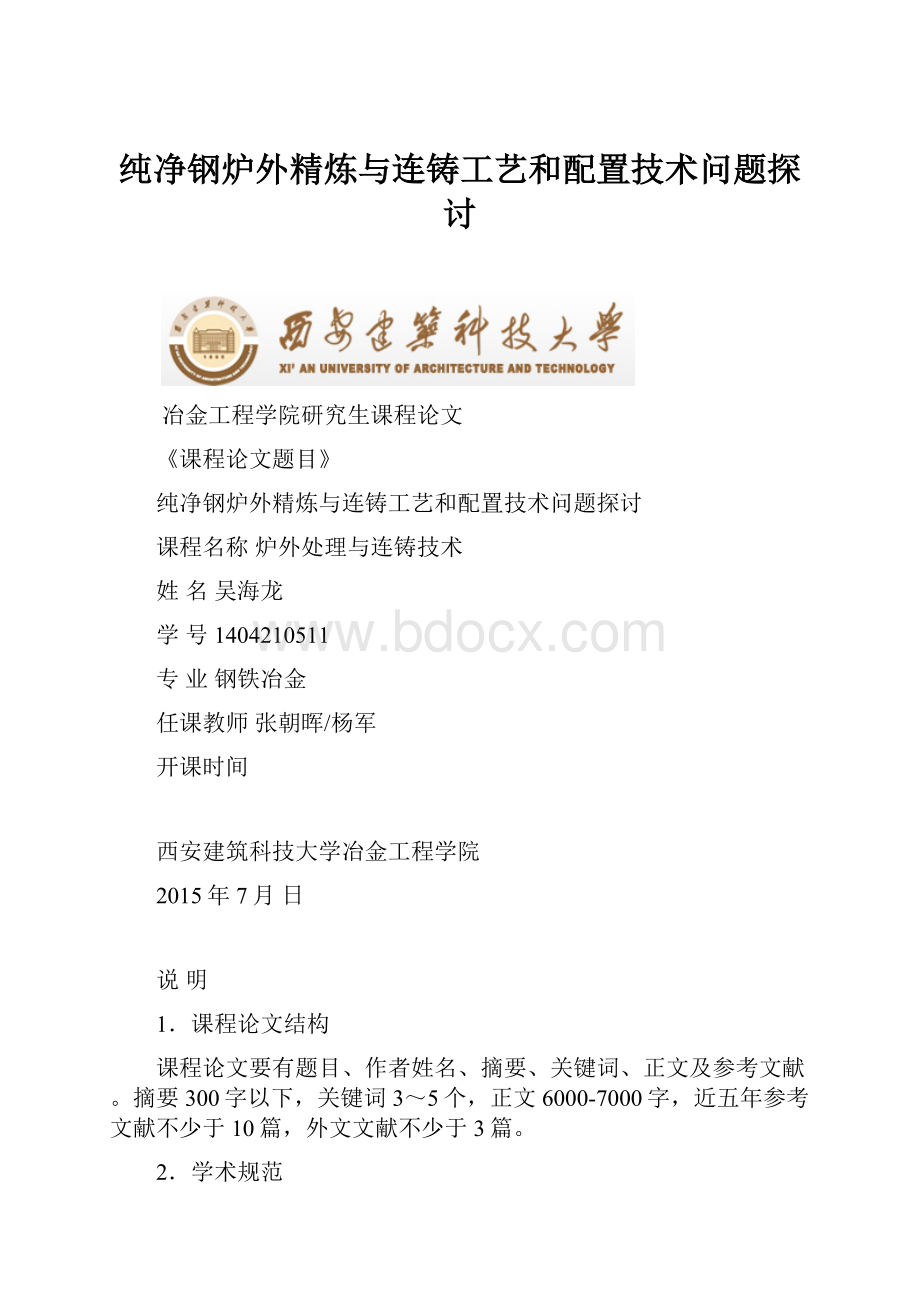
纯净钢炉外精炼与连铸工艺和配置技术问题探讨
冶金工程学院研究生课程论文
《课程论文题目》
纯净钢炉外精炼与连铸工艺和配置技术问题探讨
课程名称炉外处理与连铸技术
姓名吴海龙
学号1404210511
专业钢铁冶金
任课教师张朝晖/杨军
开课时间
西安建筑科技大学冶金工程学院
2015年7月日
说明
1.课程论文结构
课程论文要有题目、作者姓名、摘要、关键词、正文及参考文献。
摘要300字以下,关键词3~5个,正文6000-7000字,近五年参考文献不少于10篇,外文文献不少于3篇。
2.学术规范
课程论文应符合一般学术规范,具有一定学术价值,严禁抄袭或应付,引用部分必须标注,否则该门课程成绩为零分。
3.课程论文格式
课程论文用A4单面纸打印。
字体全部用宋体简体,题目要求用小二号字加粗,标题行要求用四号字加粗,标题行要求用14号字加粗,正文内容用小四号字,12号字,行距为2倍行距,页边距左为3cm、右为2cm、上为2.5cm、下为2.5cm;其它格式请参照西建大学位论文要求。
4.课程论文题目(任选一):
(1)纯净钢炉外精炼与连铸工艺和配置技术问题探讨
(2)超级低碳钢炉外精炼与连铸工艺和配置技术问题探讨
(3)不锈钢炉外精炼与连铸工艺和配置技术问题探讨
(4)轴承钢炉外精炼与连铸工艺和配置技术问题探讨
(5)模具钢炉外精炼与连铸工艺和配置技术问题探讨
5.提交时间:
2015年7月16日。
纯净钢炉外精炼与连铸工艺和配置技术问题探讨
吴海龙1
(1.西安建筑科技大学,陕西西安710055)
摘要:
本文对纯净钢炉外精炼与连铸工艺的原理进行了简要阐述,归纳分析了近年来已成功制备出的纯净钢特性和制备方法,总结了炉外精炼与连铸工艺和配置技术的解决办法等,并对其技术发展方向及产业化前景进行了分析预测。
关键字:
纯净钢;炉外精炼和连铸;前景
Toinvestigatethecleansteelrefiningandcontinuouscastingprocessandconfigurationtechnicalproblems
WUHailong1
(1Xi'anUniversityofArchitectureandTechnology,Xi’an710055,Shanxi,China)
Abstract:
Thecleansteelrefiningandcontinuouscastingprocessprincipleisbrieflydescribed,thecleansteelpropertiesandpreparationmethodsweresummarizedandanalyzedinrecentyears,therefiningandcastingprocessandconfigurationtechnologysolutionsweresummarized,etc.Finally,thewritermadeapredictionontheresearchprospectofconcerningtopic.
Keywords:
cleansteel;refiningandcontinuouscasting;prospects
1前言
纯净钢是脱除了不希望有的溶质元素的钢种,纯净钢生产工艺的基础理念是控制夹杂物的数量、尺寸、分布和种类,求得所希望的产品性能。
主要技术来自氧气冶炼、脱氧和二次精炼,通过合理设计和采用磁场控制中间包和结晶器内流场,也采用各种措施防止外来夹杂,如防止炉渣进入大包,防止炉渣、保护渣、耐火材料使钢水二次氧化。
近年,随着炉外精炼技术和连铸技术的推广和迅猛发展,钢材的纯净度显著提高。
对铸造碳钢和低合金钢而言,纯净铸钢杂质应控制在:
[S]+[O](或[N])<200×10-6的水平,超纯净钢中杂质总量≤100×10-6。
提高纯净度明显改善了钢材的加工和使用性能,如氧化铝簇夹杂物可导致汽车和电气产品用薄钢板表面缺陷,也能引起DI罐用薄钢板裂纹,还可造成轮胎子午线等线材断线,以及使轴承钢等棒钢的疲劳性能恶化。
对模具钢来说,提高其纯净度已经成为提高模具性能和寿命的重要手段,当SKD(H13)钢的W(S)从0.03%降低到0.01%时,可使钢的冲击韧性提高1倍。
18Cr2NiMo不锈钢中W(P)从0.026%降到0.002%时,其耐硝酸腐蚀的能力提高100倍以上[1]。
不同用途钢中的夹杂物质量分数和尺寸要求不同。
典型钢种的洁净度要求见表1。
表1典型钢种的洁净度要求
Table1Atypicalsteelcleanlinessrequirements
钢种
Wb/10-6
夹杂物尺寸/μm
C
S
N
H
T.O
汽车板和深冲板钢
≤30
≤30
≤100
DI灌钢
≤30
≤30
≤20
≤20
管线钢
≤30
≤35
≤30
≤100
滚珠轴承钢
≤10
≤15
轮胎帘线钢
≤40
≤2
≤15
≤10
厚板钢
30~40
≤2
≤20
点簇状夹杂≤200,单个夹杂≤13
线材钢
≤60
≤30
≤20
2纯净钢的质量和性能
2.1杂质与钢水纯净度
钢中杂质对钢材性能有多种影响。
根据用途不同,对钢材中各种杂质的要求也有很大差别。
通常钢中杂质分为表面活性杂质和间隙型杂质两大类。
表2给出钢中杂质对钢材造成的缺陷及其对性能的影响。
此外,钢中杂质所形成的非金属夹杂物破坏了钢基体的连续性特别是Al2O3类不变形夹杂物,在钢材加工变形时成为应力源,引起钢材脆断,对钢材性能的危害更严重。
表2夹杂诱导钢材的脆性
Table2Thebrittlenessofsteelproductsinductedbyinclusions
缺陷类型
缺陷位置或特点
对钢材性能的危害
线缺陷
固熔于晶体转位线
红热脆性(N、C)
面缺陷
晶界、相边界偏析
低温脆性(O、P、Sb)
体缺陷
非金属夹杂物
晶界液相
发裂
疲劳破坏(O、N、S)
高温脆性(S)
氢脆性(H)
2.2纯净度对钢材性能的影响
2.2.1纯净度对钢材力学性能的影响
(1)钢材的强韧性
降低钢中S、P、N等杂质含量,可以提高钢材的强韧性。
当钢中[S]做0.016%降低到0.004%时NiCrMo钢在62℃的平均冲击性能提高一倍[2],对AISI4340钢[P]从0.03%下降到0.003%,室温V型缺口冲击性能约提高20%。
对于含硼钢制[N]<20×10-6气可获得高的强度和低温韧性[3]。
(2)疲劳寿命
降低钢中全氧含量,明显提高轴承钢寿命。
高质量轴承钢要求钢中T[O]≤10×10-6。
降低钢中夹杂物有利于提高钢材的疲劳强度。
(3)钢材的磁性和耐腐蚀性
对于硅钢(Si=3%),降低钢中硫和T[O]含量([S]≤20×10-6,T[O]≤15×10-6),使无取向硅钢片铁芯损失降到23W/kg以下[4],降低钢中碳含量,可提高硅钢片的最大导磁率,降低矫顽力[5],提高铁的纯度明显改善钢材耐蚀性能,提高使用寿命。
当铁的纯度Fe≥99.95%时,耐蚀性已达到不锈钢水平;当Fe≥99.99%时,耐蚀性将与黄金相当。
2.2.2纯净度对钢材加工性能的影响
(1)焊接性能是钢材最重要的使用性能之成降低钢的碳含量或者降低钢的碳当量,有利于改善钢的焊接性能。
(2)深冲和冷拔性能
汽车杭家用电器、DI罐用钢等钢材不仅要求一定的强度,还要求良好的深冲性能降低钢中碳氮含量明显改善钢的深冲性能汽车用高强度正钢要求钢中C+N≤50×10-6。
此外,生产热轧薄板须严格控制钢中大型Al2O3夹杂物数量,避免轧制产生裂纹,获得良好的表面质量生产0.3mmDI罐用钢板的关键技术是杜绝出现30~40μm大型脆性非金属夹杂物。
帘线钢生产要求连续拉拔钢丝25km,不允许出现断头(直径≤0.3mm)严格控制夹杂物含量,明显减少钢丝拉拔时的断头率。
(3)切削性能与耐磨性能
钢中夹杂物数量与类型对切削刀具寿命有明显影响[6],由于钢中脆性夹杂物(如Al2O3)增大了工件与刀具的摩擦阻力,不利于钢材的切削性能降低钢中脆性夹杂物含量,有利于改善钢材的切削性能[7]。
钢中脆性夹杂物(Al2O3)对钢的耐磨性能有极坏的影响。
钢轨钢和轴承钢中Al2O3等脆性夹杂物往往造成钢材表面剥落、腐蚀严格控制钢中Al2O3、可解决钢材表面磨损问题,提高钢的耐磨性。
(4)冷热加工性能
硫引起钢的热脆,显著降低钢的热加工性能碳钢中S≤60×10-6,可基本避免热加工时钢材产生热裂纹,对于铁素体不锈钢,控制钢中S≤20×10-6,可保证钢材良好的热加工性能。
N和C都是间隙型杂质,低温时容易在Fe原子晶格内扩散,引起时效,使钢材的低温锻造性能下降对0.35%的碳钢,控制钢中的固溶氮含量小于50×10-6,明显降低钢材冷锻时裂纹的发生率。
3国内外纯净钢的研究和生产水平
目前,世界纯净钢生产与研发水平最高的是日本,其次是欧美和韩国。
最近,新日铁开发了控制钢中夹杂物的新技术,通过向钢水中添加镁,控制夹杂物的成分,并细化夹杂物颗粒。
采用该方法,使夹杂物的变形性能接近钢的变形性能,可以提高产品的韧性和加工性能,国内外一些先进钢厂的纯净钢生产水平参见表2[7-9]。
表3国内外一些先进钢厂的纯净钢生产水平
Table3Somecleansteelproductionlevelofadvanceddomesticandforeignsteel
厂家
WB/10-6
钢种
工艺
C
P
S
N
H
T.O
合计
日本神户制钢
3
20
2~3
6~9
1.0
2~5
41(34)
250马氏体时效钢
真空感应炉
日本新日铁
10(3)
25
3
14
1.0
5
58(52)
深冲刚
LD+OB+OH
德国蒂森
20
15
5
15
0.7
10
65.7
深冲刚
LD+真空脱氧
韩国浦项
5~8
80
轴承钢
BOF+LF+RH
中国宝钢
≤15
15
5~10
11
≤1.0
≤15
67(55)
IF钢、管线钢
BOF+LF+RH
中国武钢
9
40
3。
4
12
1.0
10
81.4
IF钢、管线钢
BOF+LF+RH
中国攀钢
18
24
12
2.0
18
74
深冲刚
BOF+LF+RH
中国鞍钢
20
5
20
0.96
18
63.96
管线钢
BOF+LF+VD
4纯净钢的生产工艺
由于更广义的纯净钢是脱除了不希望有的溶质元素的钢种,纯挣钢生产工艺的基础理念是控制夹杂物的数量、尺寸、分布和种类,求得所希望的产品性能。
主要技术来自氧气冶炼,脱氧和二次精炼,通过合理设计和采用磁场控制中间包和结晶器内流场,也采用各种措施防止外来夹杂,如防止炉渣进入大包,防止炉渣、保护渣、耐火材料使钢水二次氧化。
然后根据IISI的纯净钢工作小组最近的报告总结了世界纯净钢生产的概况。
最后讨论了纯净钢的特性、使用效果和钢中夹杂物物化性能的关系和经济可行性[10]。
广义的纯净钢也包括脱除了碳、氮、氢、磷和硫的钢种。
脱氧产物是内在氧化物。
来自耐火材料、炉渣、保护渣及由它们造成的二次氧化产物属外来夹杂物。
这些夹杂物的不良作用必须消除,以求所需的钢材性能。
4.1铁水预处理
铁水在进入炼钢炉进行冶炼前,为除去某种有害成分或回收某种有益成分的处理过程。
日前,基于铁水预处理的纯净钢冶炼工艺有两种:
一种是铁水深脱硫处理+转炉脱磷、脱碳+钢水炉外喷粉脱磷、脱硫;另一种是铁水“三脱”预处理+复吹转炉少渣炼钢+钢水炉外喷粉脱硫。
两种工艺均能生产[P]100ppm,[S]50ppm的纯净钢,但后者经济效益显著高于前者。
铁水中含有钒、泥等有用金属元素,可运用选选性氧化的原理进行预处理,把钒、铌等金属成分氧化进入渣中予以富集,再把这些渣作为原料提炼出有用金属。
中国有丰富的多金属号召资源,为提取铁矿中的共生金属发展了适用的工艺技术。
内蒙占产的含铌和稀土金属铁矿,除先在选矿过程中提取稀土精矿并炼成稀土合金、氯化稀土等副产品外,含泥铁水预处理后得到铌渣,再冶炼成铌铁。
攀枝花等地的钒钛磁铁习矿,在选取钛精矿并进一步加工成钛合金或钛白外,在高炉中成功地以高氧化钛渣冶炼成含钒铁水,然后用雾化法或转炉法从铁水中提取钒渣,再把钒渣冶炼成钒铁。
这样不但有效地提取多种共生金属,而且还发展了具有中国特色的低合金钢的特殊系列。
4.2炉外精炼
20世纪炼钢技术中的革新,主要是纯氧顶吹转炉炼钢法和连续铸钢法。
由于这些实用技术的采用,炼钢生产率飞速提高。
炉外精炼技术是设置在转炉和连续铸钢的连接工序,这一技术的实用化,大大提高并完善亨利贝塞麦发明的液态炼钢法。
要提高铸钢生产的质量和产量,同样离不开冶金冶炼技术的发展。
炉外精炼技术就是铸件生产中的适用技术之一。
通过炉外精炼技术为铸造生产提供优质的钢液。
炉外精炼技术在生产中的应用日前得到公认并被广泛应用的炉外精炼方法有:
LF法、RH法、VOD法。
4.2.1LF法(钢包精炼炉法)
它是1971年由日本大同钢公司发明的,用电弧加热,包底吹氦气搅拌。
工艺优点
1)电弧加热热效率高,升温幅度大,控温准确度可达士5℃;
2)其具备搅拌和合金化的功能,吹氢搅拌易于实现窄范围合金成份控制,提高产品的稳定性;
3)设备投资少,精炼成本低,适合生产超低硫钢、超低氧钢。
LF法的生产工艺要点
1)加热与控温LF采用电弧加热,热效率高,钢水平均升温1℃耗电0.5~0.8kWh,LF升温速度决定于供电比功率(kVA/t),而供电的比功率又决定于钢包耐火材料的熔损指数。
因采用埋弧泡沫渣技术,可减少电弧的热辐射损失,提高热效率10%~15%,终点温度的精确度≤士5.0C。
2)采用白渣精炼工艺。
下渣量控制在≤5kg/t,一般采用A12O3-CaO-SiO2系炉渣,包渣碱度≥3,以避免炉渣再氧化。
吹氩搅拌时避免钢液裸露。
3)合金微调与窄成份范围控制。
据试验报道,使用合金芯线技术可提高金属回收率,齿轮钢中钛的回收率平均达到87.9%,硼的回收率达64.3%,钢包喂碳线回收率达90%,ZG30CrMnMoRE喂稀土线稀土回收率达到68%,高的回收率可实现窄成份控制。
使用钢包精炼炉还需解决如下问题:
①钢液温度下降。
由于钢包精炼炉与普通电弧炉相连操作,在普通电弧炉钢液氧化完毕向精炼炉出钢时,钢液温度下降,炉子越小,温降越大。
这样精炼炉需进行提温操作,会少许增加电耗。
②钢液倒包会增加气体含量,钢液进行炉外精炼后,其钢液中各类气体含量均有降低。
但在钢液倒包过程中,易使钢液吸气,造成钢液气体含量些许增加,目前已有解决办法。
4.2.2RH法的优点
1)反应速度快。
真空脱气周期短,一般10分钟可以完成脱气操作,5分种能完成合金化及温度均匀化,可与转炉配合使用。
2)反应效率高。
钢水直接在真空室内反应,钢中可达到[H]≤1.0×10-6,[N]≤25×10-6,[C]≤10×10-6,的超纯净钢。
3)可进行吹氧脱碳和二次燃烧热补偿,减少精炼过程的温降。
4.2.3VOD法(真空罐内钢包吹氧除气法)
VOD的特点VOD法是1965年西德首先开发应用的,它是将钢包放入真空罐内从顶部的氧枪向钢包内吹氧脱碳,同时从钢包底部向上吹氢搅拌。
此方法适合生产超低碳不锈钢,达到保铬去碳的日的,可与转炉配合使用。
他它的优点是实现了低碳不锈钢冶炼的必要的热力学和动力学的条件—高温、真空、搅拌。
4.3新型连铸工艺
常言逆“三分冶炼,七分铸造”。
连铸工序对钢的纯净度影响很大,采用保护浇注、中间包冶金、新型中间包覆盖剂、调整保护渣性能及电磁搅拌等手段可去除及控制夹杂物。
连铸的生产工艺流程:
将装有精炼好钢水的钢包运至回转台,回转台转动到浇注位置后,将钢水注入中间包,中间包再由水口将钢水分配到各个结晶器中去。
结晶器是连铸机的核心设备之一,它使铸件成形并迅速凝固结晶。
拉矫机与结晶振动装置共同作用,将各结晶器内的铸件拉出,经冷却、电磁搅拌后,切割成一定长度的板坯。
连铸钢水的准备
连铸钢水的温度要求:
钢水深度过高的危害:
①出结晶器坯壳薄,容易漏钢;②耐火材料侵蚀加快,易导致铸流失控,降低浇铸安全性;③增加非金属夹杂,影响板坯内在质量;④铸坯柱状晶发达;⑤中心偏析加重,易产生中心线裂纹。
钢水温度过低的危害:
①容易发生水口堵塞,浇铸中断;②连铸表面容易产生结疤、夹渣、裂纹等缺陷;③非金属夹杂不易上浮,影响铸坯内在质量。
宝钢开展了一系列旨在降低全氧含量,减少夹杂物和防止卷渣的研究,在生产中所采用的措施包括[11]:
1)采用挡渣出钢,要求钢包渣层厚度小于70mm。
2)钢包渣改质:
出钢时向钢包表面加入改质剂,降低渣的氧化性。
3)控制RH中自由氧浓度和纯脱气时间。
4)采用中间包纯净化技术。
5)为了防止结晶器保护渣卷入,采用不易卷入的高载度保护渣。
6)在连铸操作方面,保持适量的Ar气吹入量和维持结晶器液面稳定。
国内外先进炼钢厂纯净钢生产各工序钢中全氧量参见表3[12]。
表4国内外先进钢铁厂纯净钢生产各工序钢中全氧量
Table4advancedcleansteelproductionofvarioussteelplantsinthewholeprocessofsteeloxygen
钢厂
精炼方法
W(T.O)/×10-6
指标年份
钢水包
中间包
结晶器
板坯
美国Inland厂4号BOF
LMF
RH-OB
30
60~80
24
8~30
21
15
1990
2003
美国阿姆克Middletown厂
RH
60~105
15~40(25)
16.9~23.8
1991
美钢联Lorain厂BOP
真空脱气
13~17
1991
北美某厂
20~35
20~30
10~15
1991
加拿大Dofasco钢厂
LF+RH
19
13
美国Weirton炼钢车间
Dravo-RH
23±10
22±12
1995
芬兰RautaruukkiRaahe钢厂
48±12
32
38
17
1993
芬兰Koerhar厂
气体搅拌
32
2000
德国Dillinger厂
10~15
10
≤15
1994
荷兰霍戈文Ijmuiden厂
真空脱气
20~30
1994
法国索拉克Dunkirk厂
RH-DB
20~05
1997
英钢联
RH
<10
1994
日本JFE川崎千叶厂
RH
40
20
1989
韩国POCSCO
LF+RH
25~31
<10
1991
中国台湾中钢公司
LF+RH
<30
12
1994
中国武钢第二炼钢厂
RH
28~34
24~26
12~19
2000
中国攀钢
RH-MFB
20~24
2000
中国宝钢集团公司
LF+RH
40
23
10
8
2003
5氧化物冶金新技术
1990年,在日本名古屋召开的国际钢铁大会上,新日铁的高村和沟口首次提出氧化物冶金的概念。
15年来,氧化物冶金技术受到国际冶金材料学术界和产业界的广为关注。
主要产钢国均致力于其机理和应用的研究。
虽然目前公开报道实例仅限于高级别管线钢和非调质钢的试生产,但从氧化物冶金技术原理来看,有望应用于超细晶粒钢种。
新日铁采用氧化物冶金技术生产的X80级管线钢低温韧性较传统TiN冶金明显提高[13],生产的铁素体珠光体型非调质钢强度高且韧性好,已大量用于制造汽车轴和连杆等部件。
氧化物冶金技术的关键是通过精确地控制钢水凝固前沿的凝固条件对夹杂物的种类、大小和形态进行控制。
制约氧化物冶金技术应用的主要原因是其工艺的复杂性。
6总结
从纯净钢生产的社会需求出发,以及重点分析研究日本和德国纯净钢生产的LF工艺技术,我国应该明确提出尽快在各钢厂建立纯净钢生产体制;努力开发高效转炉生产工艺,实现全量铁水“三脱”预处理,建立多功能精炼设各和钢水保护体系,实现超纯净钢生产。
中国钢铁企业应把建立纯净钢生产体制作为企业给构调整的基本方向,将纯净钢生产与转炉高效化和低成本无污染的生产工艺结合起来。
通过优化纯净钢的冶炼工艺,在很大程度改善了冶炼过程中对于非金属杂质(磷、硫、氧、氮、氢等)的去除效果,满足了现代高纯净钢的冶炼工艺要求,可大幅提高钢的纯净度,满足市场对于高纯净钢的需求。
同时,纯净钢冶炼工艺的优化还能够缩短钢材精炼周期,提高劳动生产率,进而增加企业的市场竞争力。
参考文献
[1]潘秀兰,李震,王艳红,梁慧智.国内外纯净钢生产先进技术[J].炼钢,2007,01:
59-62.
[2]郑贻裕,蒋晓放.宝钢纯净钢炼钢生产技术的进展[J].炼钢,2011,01:
11-14+17.
[3]J.A.Wilson,A.J.Craven.ImprovingtheanalysisofsmallprecipitatesinHSLAsteels
usingaplasmacleanerandELNES[J].Ultramicroscopy.2003,94:
197~207.
[4]范治博,牛建平,黄中东.洁净钢生产技术的国内外现状和发展[J].热加工工艺,2011,08:
47-51.
[5]董晓亮,高元起,高扬,庞宗旭.真空碳脱氧纯净化技术在大型钢锭制备中的应用[J].铸造,2013,09:
843-845.
[6]刘永铨.易切削钢[M].沈阳:
东北工学院出版社,1990.
[7]袁武华,王峰.国内外易切削钢的研究现状和前景[J].钢铁研究,2008,05:
56-62..
[8]赵大同.高纯净钢冶炼工艺优化探讨[J].冶金经济与管理,2014,02:
48-49.
[9]]徐匡迪,肖丽俊,干勇,刘浏,王新华.新一代洁净钢生产流程的理论解析[J].金属学报,2012,01:
1-10.
[10]杨玉升.洁净钢生产技术的国内外现状和发展分析[J].科技风,2014,02:
19.
[11]Pei-weiHAN,Shao-junCHU,PingMEI,Yi-feiLIN.OxideInclusionsinFerromanganeseandItsInfluenceontheQualityofCleanSteels[J].IronandSteel,2014,22:
23~27.
[12]神克常,牛建平,李立新,毛慧英.洁净钢制备技术的研究现状及发展[J].山东冶金,2012,02:
10-12.
[13]XuWang,Fu-renXiao,Yan-hongFu.Mate