承压设备焊后热处理技术全.docx
《承压设备焊后热处理技术全.docx》由会员分享,可在线阅读,更多相关《承压设备焊后热处理技术全.docx(15页珍藏版)》请在冰豆网上搜索。
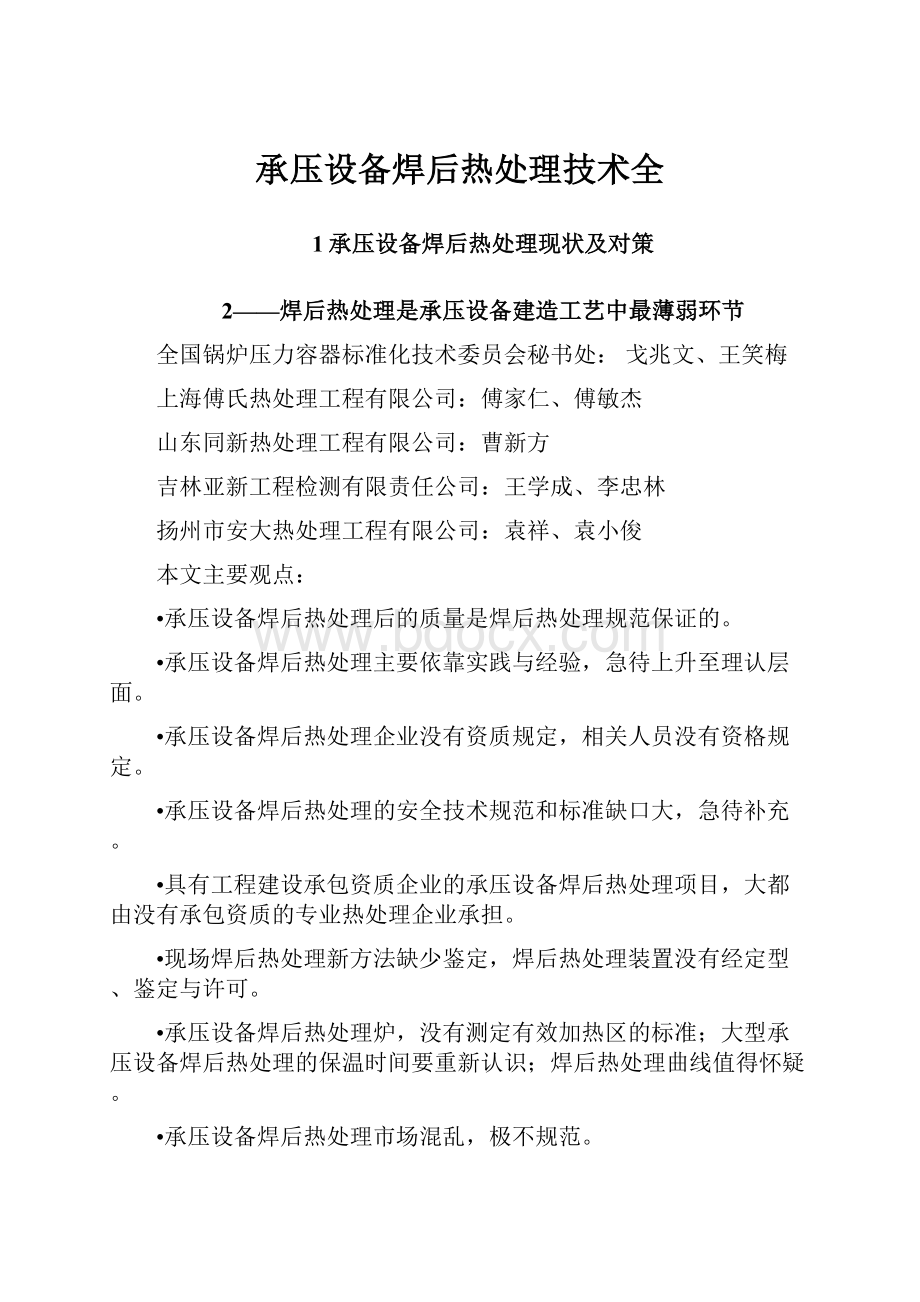
承压设备焊后热处理技术全
1承压设备焊后热处理现状及对策
2——焊后热处理是承压设备建造工艺中最薄弱环节
全国锅炉压力容器标准化技术委员会秘书处:
戈兆文、王笑梅
上海傅氏热处理工程有限公司:
傅家仁、傅敏杰
山东同新热处理工程有限公司:
曹新方
吉林亚新工程检测有限责任公司:
王学成、李忠林
扬州市安大热处理工程有限公司:
袁祥、袁小俊
本文主要观点:
•承压设备焊后热处理后的质量是焊后热处理规范保证的。
•承压设备焊后热处理主要依靠实践与经验,急待上升至理认层面。
•承压设备焊后热处理企业没有资质规定,相关人员没有资格规定。
•承压设备焊后热处理的安全技术规范和标准缺口大,急待补充。
•具有工程建设承包资质企业的承压设备焊后热处理项目,大都由没有承包资质的专业热处理企业承担。
•现场焊后热处理新方法缺少鉴定,焊后热处理装置没有经定型、鉴定与许可。
•承压设备焊后热处理炉,没有测定有效加热区的标准;大型承压设备焊后热处理的保温时间要重新认识;焊后热处理曲线值得怀疑。
•承压设备焊后热处理市场混乱,极不规范。
•承压设备焊后热处理当务之急是加强监督管理和过程控制。
1、国内承压设备焊后热处理概况
焊后热处理可以调整、改善焊接接头的力学性能和蠕变性能,松弛焊接残余应力,稳定承压设备结构尺寸,软化淬硬区,改善热影响区组织,减少焊缝金属氢含量,提高焊接接头耐腐蚀性能,焊后热处理是承压设备建造过程中重要的、无可替代的工艺。
在承压设备行业中使用最为广泛的焊后热处理是指为改善焊接区域的性能,消除焊接残余应力等有害影响,将焊接区域或其中部分在金属相变点以下加热到足够高的温度,并保持一定的时间,而后均匀冷却的热过程。
承压设备焊后热处理实施技术关键:
a)在规定范围内的升温和降温速度;
b)焊后热处理过程中保温温度的均匀性;
c)焊后热处理过程中保温温度控制波动范围。
截至2008年底,全国承压设备制造、安装企业许可证数量统计见表1。
表1全国承压设备制造、安装许可证企业统计
种类
分类
数量(个)
锅炉
制造证企业
1555
安装、改造维修证企业
3888
压力容器和气瓶
制造证企业
3855
安装、改造、维修证企业
525
压力管道
元件制造证企业
3906
安装、改造、维修证企业
3398
从表1可见,到2008年为止,我国计有17127家企业取得了承压设备制造、安装许可资质,中国已成为世界范围内承压设备生产大国。
我国承压设备正朝向大型化、高参数、长周期方向发展,对焊后热处理提出更高、更严的要求。
国内独立自主的完成了若干大型承压设备焊后热处理,代表了国内最高水平。
如煤制油工程中的反应器,材料为21/4Cr-1Mo-V,总重量为2040吨,高度60m,壁厚约340mm,内径4800mm,在现场炉内整体分两段进行焊后热处理,环焊缝再用火焰加热进行局部焊后热处理;二甲苯塔高约130m,外径7.2m,壁厚60mm,总重1200~1300吨,在现场采用内燃法分段焊后热处理,逐段组装后进行环焊缝局部焊后热处理;丙烯塔塔体(不含裙座)高78m,外径3m,壁厚36mm~48mm不等,自重500吨,内构件200吨,采用内燃法上、下两台燃烧器,整体一次完成焊后热处理;再生器塔体为Φ7m~Φ13m变径,塔体高60m,使用Q345R制成,总重600吨,采用两台燃烧器内燃,整体一次完成焊后热处理;我国还自行设计核电站装备专用热处理炉;国内还研制和开发了球罐和塔器用内燃式焊后热处理装置,可以小批量生产。
承压设备焊后热处理的质量,主要靠焊后热处理规范(保温温度、保温时间等)来保证。
承压设备焊后热处理牵涉到化工机械、锅炉、压力管道、热处理、焊接、金属材料、结构、热工及装置、仪表及自动化等多种专业类别。
国内专业的承压设备焊后热处理企业约有15家左右,此外还有若干“游兵散勇”,其中只有3-4家业务水平高,人员专一,设备维护好。
国内一些重大承压设备焊后热处理项目都是由专业的企业完成的。
2 承压设备焊后热处理特点
2.1 焊后热处理的整体性、一次性和终结性
a)焊后热处理标准或安全技术规范都优先推荐整体焊后热处理。
整体焊后热处理不仅节省时间,节省能源,更重要的是可以使承压设备免受二次加热带来局部残余应力与残余变形难以控制后果。
在炉内可以做到整体焊后热处理,在容器内部加热、以筒体作炉膛外侧保温也是整体焊后热处理。
由于是整体焊后热处理,承压设备的质量也具有强烈的整体性,好则全好,坏则全坏。
整体焊后热处理也给控制承压设备温度的均匀性和变形带来难题。
整体焊后热处理应注意下列问题:
1)承压设备大型化后,整体焊后热处理时温度均匀性难以控制。
立置塔器采用内燃法进行焊后热处理,使用一台燃烧器,通常可以做到三倍塔器内径的高度范围内温度均匀,个别的企业可以做到五倍塔器内径的高度范围内温度均匀。
走出此范围,则要改变焊后热处理工艺了。
2)大型承压设备,特别是塔器类设备内径大、塔身长,变形更为严重。
卧置比立置的变形更难控制。
3)焊后热处理的保温时间,应按该承压设备尚未进行过焊后热处理的最大焊缝厚度进行计算。
b)焊后热处理质量一次性确定
焊后热处理与焊接、无损检测等工艺不同,焊后热处理一次连续完成,则热处理质量也随之确定。
质量符合要求则热处理成功,质量不符合规定,则热处理失败。
与焊接、无损检测不同,热处理失败后,很难有第二次重新再来的可能,也不存在“返修”的可能。
浙江某地焦碳塔体经焊后热处理后呈“香蕉形”,没有哪位能人,也没有哪个单位可以矫正合格。
c)焊后热处理是承压设备建造工艺最后一环
如果最后一道工艺失败,而且又不能返修,则以前所有劳动,全部付诸东流,损失惨重。
2.2 承压设备焊后热处理后的质量是规范保证的,各种检测都具有局限性
焊后热处理规范包括:
焊件升(降)温速度、焊件升温、保温期间各点温差、保温温度,保温时间等。
焊后热处理质量对于同一台设备来讲呈现多方面的要求,除过烧、变形、表面裂纹等可以直接观察外,残余应力、硬度、金相组织和试件力学性能等都需要借助于仪器或专用手段进行检测。
除外观检查外,几乎所有检验方法都是具有局限性,难以评价总体效果。
残余应力测定方法虽然很多,但能用于工程中的方法并不多,而且误差很大,如:
一些新研制方法如磁性法、小孔法、压痕法都没有标准,重复性很差,在工程中常用的X光衍射法虽然有标准,在工程现场使用误差很大,更重要的是,X光衍射法用仪器不能进行法定检验,所出示数据没有法律效用。
经焊后热处理产品中,残余应力的大小及其分布情况,设计人员和使用单位非常感兴趣,限于目前技术水平还不能够在工程中规定出各方都能接受的方法与标准,所以在技术文件中也不规定残余应力检测。
通过对焊后热处理规范与焊接应力关系研究,基本可以肯定,对于碳钢和低合金钢承压设备按ASMEⅧ中规定的规范进行焊后热处理,产品中残余应力可以减低80%左右。
硬度试验是典型的局部试验方法。
国内承压设备行业内,管道相关标准中采用硬度试验比较多,锅炉、压力容器产品标准基本不用硬度检验,在少数技术条件中也有规定硬度试验。
国内管道标准和锅炉压力容器技术条件中的硬度指标经常参照ASME压力管道规范B31.3《工艺管道》中的规定。
使用时需要注意下列问题:
a)ASMEB31.3中管道焊后热处理规范与国内锅炉压力容器标准不完全相同,其基本原因是中、美两承压设备用材料合金体系不同;
b)ASMEB31.3有关硬度检验要求只是针对紧靠焊接接头中熔合线的过热区(也即粗晶区),而国内一些标准中都将B31.3的规定,生搬到整个焊缝区,熔合区和热影响区,甚至母材内;
c)ASMEB31.3中硬度的合格指标与焊后热处理保温温度与保温时间关系密切,只有符合ASMEB31.3规定焊后热处理规范,才能引用其硬度试验指标。
我国不少标准中不按ASMEB31.3中的规定进行焊后热处理和检验,但却使用ASMEB31.3中的硬度验收指标,容易产生因标准不当造成的错误。
经焊后热处理的产品进行金相检验和试件进行力学性能检验也都是属于局部检验性质。
利用典型位置的检验力图说明产品焊后热处理的整体质量,但取样位置是否有代表性值得深思,例如球罐产品焊接试件的放置位置在标准中已变更过两次,即使按现行标准规定放在“球壳热处理高温区的外侧”,也不能保证试件经受焊后热处理的保温温度、保温时间与罐体相同。
根据笔者调研考证结果,可以毫不夸张的肯定:
没有一台球罐的产品焊接试件的焊后热处理规范是正确的,全部错误。
产品焊后热处理后的质量是由焊后热处理的规范来保证的,因此为了获得合格的焊后热处理效果必须制订与实施正确的焊后热处理工艺,保证焊后热处理温度均匀性及测温的准确性。
对焊后热处理的监督主要是过程监督。
2.3 焊后热处理的实践性极强,关键工艺靠经验
目前实施的焊后热处理标准中只规定了焊后热处理保温温度、保温时间及升、降温工艺,基本没有工艺实施要求,如焊后热处理的热工计算,特别是局部焊后热处理热工计算;加热区与隔热区的范围;测温点数量及布置;测温系统的误差;绝热材料选用及铺设厚度;变形控制等等关键工艺,都只能依靠焊后热处理操作人员的经验来确定,经验丰富的则效果好一些,没有经验的则难以保证焊后热处理质量。
焊后热处理企业当第一次遇到超长、超重、超大、材料与结构有特殊要求的产品,有要求焊后热处理时,则风险很大。
焊后热处理的主要目的之一是消除残余应力。
焊后热处理各工序中,大都与消除残余应力有非常密切关系,因此当缺少焊后热处理经验造成若干工序不合格,但都可以通过验收,而给产品留下终身隐患。
我们经常看到盛装液化石油气的球罐使用一年后开罐检验,发现大量表面微小裂纹,这是由于H2S引起的应力腐蚀裂纹,即使设计规定液化石油气中H2S含量小于10ppm,裂纹也照样出现,究其原因与焊后热处理不到位,残余应力消除不够有关。
2.4 焊后热处理曲线的值得怀疑
在承压设备行业,焊后热处理结果基本上都要求出示焊后热处理曲线。
作为见证资料,存档备查。
用纸质的焊后热处理曲线表达焊后热处理升、降过程,虽然比较直观但已经十分落后了。
焊后热处理曲线的真实性,不仅与起点对零,走纸速度,湿度等外界因数相关,而且受到测温点数量的限制,即在各种因素都正常条件下焊后热处理曲线在进入保温期间前后很难区分每个测温点的温度与时间数值,缺少几个点,也看不出来。
我们也多次听说过焊后热处理曲线做假太容易了,一台电脑加一台电炉,一天就可以画出几十条焊后热处理曲线,“保证曲线条条清晰”、“数据个个正确”。
在焊后热处理测温系统中采用无纸记录仪,不仅可以记录每个测温点的升、降温过程,而且可以瞬时记录下每个测温点的温度数值,累计下来后,便可统计出每个测温点的保温时间。
3 承压设备焊后热处理管理薄弱
3.1 承压设备的安全技术规范和标准对焊后热处理规定太少
TSGR0004—2009《固定式压力容器安全技术监察规程》中规定:
“压力容器及其受压元件应当按照设计图样和本规程引用标准要求进行焊后热处理”。
1996年版《蒸汽锅炉安全技术监察》中原则规定了低碳钢按筒体壁厚,合金钢按专业技术标准规定是否进行焊后热处理,以及焊后热处理的4条要点。
承压设备标准中有关焊后热处理规定如下:
a)GB150—2011《压力容器》中规定了:
1)焊后热处理厚度δPWHT确定方法;
2)需要进行焊后热处理范围;
3)焊后热处理基本要求及工艺。
b)GB/T20801—2006《压力管道规范工业管道》中规定了:
1)管子对接及支管连接时的焊后热处理厚度;
2)焊后热处理基本技术要求;
3)焊后热处理温度,最短保温时间及工艺;
4)硬度检验。
现行的承压设备安全技术规范和标准规定了焊后热处理范围和焊后热处理保温温度等技术要求。
但都没有具体规定出如何实现的途径和方法,对已经规定内容也必须深化与具体,如不同钢号、不同厚度、不同产品的焊后热处理温度;对焊后热处理装置的要求,对控温、测温和保温设备和材料的技术要求;对焊后热处理工艺卡及现场焊后热处理方案的要求;对焊后热处理报告要求等等,只有编制相应的安全技术规范条款和较全面的标准,才可能规范承压设备焊后热处理各过程,才能达到焊后热处理目的。
国际标准ISO/TR17663:
2001《焊接及相关工艺的热处理质量要求指南》有相关规定。
3.2 承压设备焊后热处理企业没有资质规定
按照相关规定,制造、安装承压设备的企业应经行政许可,获得相应资质,对承压设备的焊接与无损检测都有资格与条件要求,但对焊后热处理企业既没有资质要求,也没有具体的条件限制,对热处理责任人员和操作人员也没有资格、级别要求,焊后热处理可以分包,对分包企业及人员也没有资质、资格和级别要求。
目前,国内承接承压设备焊后热处理企业有两种情况,其一是具备工程建设承包资质的综合性建设安装企业,内部有焊后热处理职能机构;其二是不具备工程建设承包资质的专业热处理企业,他们只能从综合性建安企业手中分包焊后热处理项目。
由于焊后热处理没有资质、资格要求,任务分包给谁不违法、违规。
尽管昨天还是保温、防腐企业,今天买了一台加热装置就成了焊后热处理企业。
至于焊后热处理质量,则有“热处理曲线”作挡箭牌。
3.3 承压设备焊后热处理管理“漏洞”
a)建安企业实行的是项目经理负责制,承压设备建安工程中焊后热处理项目交给谁,往往由项目经理决定。
由于没有资质、资格限定,任务分包给谁都可以,即使本企业有热处理部门,项目经理也优先选用专业的焊后热处理公司,其中“低价中标”、“回扣”原由起了决定性作用。
某专业公司接受一台1000m3球罐焊后热处理合同,商定费用3.5万元,回扣1万给项目经理。
当施工方得不到应有的利润时,焊后热处理肯定会“缩水”,质量难以保证。
就这样,具有工程建设承包资质但没有焊后热处理能力的建安企业,完成了承压设备焊后热处理,质量令人担心。
b)大量建安企业,长期将承压设备焊后热处理委托专业公司完成。
因为这些企业所使用的加热装置、温控装置、测温装置都不是定型产品,随时要进行维护,不是原设计、组装企业很难弄清内部结构与线路,经常由于转场运输而使装置失灵,如进口燃烧器就有10个连锁,只要有一个地方出故障,马上“趴窝”,开动不起来。
没有焊后热处理装置主动权,不能正常进行焊后热处理工作,技术水平肯定落后,掌握不了焊后热处理真实情况,分辨不了热处理曲线真假与陷井。
作为专业公司在焊后热处理过程中,只是临时的操作工,而焊后热处理的责任工程师只能由委托方承担,签字认可对外发报告。
由于被委托方只对焊后热处理操作负责,因而不承担焊后热处理结果(如产品试件力学性能、硬度、内外缺陷、形状与尺寸)的责任。
造造假,做做小动作则经常会有,都要由不了解焊后热处理的承包承压设备建安单位负完全责任。
某石化公司,用55kg级Mn-Nb低合金钢建造了球罐群,内装液化石油气,使用一年后开罐检查,在环焊缝X形坡口的中部发现大量裂纹。
严重的是在返修以后,沿返修焊焊缝两端继续开裂。
我们认为这可能是第一次焊后热处理不到位造成的,球罐内部存在较高的残余应力,返修时残余应力重新分布,使返修焊缝两端开裂。
查交工报告,看到焊后热处理曲线明显造假。
中标的建安公司原想省钱压低热处理费用,承担焊后热处理的专业公司因费用太低,在施行热处理过程中大大缩水,没有按焊后热处理规定的温度与时间执行,致使残余应力仍保持较高水平,最终还是中标的建安公司花费了大量人力、物力进行大规模返修,个人占了小便宜,建安公司吃了大亏,业主将永远背上球罐质量不良的包袱。
3.4承压设备焊后热处理市场混乱,极不规范
由于招标方不懂得焊后热处理的重要性及其技术特点,没有自己的标底,心中无数,有时缺少评审技术标的过程,在招标时往往采取“低价中标”政策。
而投标方也没有资质、资格限制,谁都可以来投标。
为了中标则尽量压低报价,我们曾了解到某单位对厚度为40mm的管道进行焊后热处理,一道环焊缝的价格只有7元。
便宜没好货,焊后热处理质量也是“低价”。
焊后热处理的验收主要是焊后热处理曲线。
做不做焊后热处理,焊后热处理过程是否认真严格,都会有一条焊后热处理曲线出来应付各方面的检查。
4承压设备焊后热处理技术“漏洞”
4.1定义与术语不准确
GB3375—94《焊接术语》中规定“焊后热处理”指焊后,为改善焊接接头组织和性能,或清除残余应力而进行的“热处理”。
若完全按照这个术语用于焊接与承压设备的热加工,则容易产生歧意或误解,如拼焊钢板热成形封头,调质钢的淬火加回火、焊接钢坯搪玻璃等等,则不能称作为“焊后热处理”,但这些热过程能极大的影响焊接接头的力学性能。
故在焊接工艺评定标准中将“焊后热处理”定义为:
能改变焊接接头的组织、性能或焊接残余应力的热过程,如热处理、热成形、搪玻璃等。
ASME《锅炉压力容器规范》第Ⅸ卷“焊接和钎接评定”中,则将“焊后热处理”定义为“在焊接后的任何热处理”。
在承压设备行业中,大量的焊后热处理都是在“金属相变点以下加热”,具有改善焊接区域性能,消除焊接残余应力作用。
如果将这样的热过程称为“退火”或“回火”则是错误的,这种热过程是按“回火”的温度,而采取了“退火”的保温方式,也有些地方称为“消除应力热处理”,而忘记了还有改变显微组织,改善接头性能的作用,不能用“消除应力热处理”代替“焊后热处理”。
4.2焊后热处理装置无标准,产品无许可证
用于现场焊后热处理的加热装置,从1976年开始时,大量使用“霍克喷咀”,由于二次进风降低人孔周边温度,目前虽然仍有使用,但数量大大减少了,目前内燃法普遍使用的是燃烧器,即将用于锅炉的燃烧器经过改造成适用于焊后热处理的加热装置,再配置调控装置、测温装置和记录装置,用于现场。
专业的焊后热处理企业中的骨干企业都自己改造、组配,也少量出售,为数不多的企业生产供现场焊后热处理使用的全套装置。
无认是“霍克喷咀”还是内燃法中的加热装置都没有标准,也没有定型产品,更谈不上产品许可证。
用于管道或局部焊后热处理用装置在江苏有企业可以小批量生产,也是“三无”产品。
产品标准与产品许可证制度,是该产品是否成熟,稳定的标志。
各企业所用的现场焊后热处理装置都是自我为主,从改造、组装、调试,直至投入使用都无章可循,不仅工厂生产不便,使用中容易操作失控,售出后使用单位也不知道如何维护,严重影响焊后热处理质量,我们看到不少建安企业的燃烧器都静静的放置在仓库中,再也启动不了。
4.3没有焊后热处理相关标准
4.3.1没有焊后热处理工艺标准
在锅炉压力容器标准体系中,没有焊后热处理专用标准,只在相关标准中列有相关条款。
主要规定了:
焊后热处理条件,焊后热处理规范(温度与保温时间)和升、降温过程中的技术要求,这对于在社会化大生产中进行焊后热处理显然不够,不能解决在焊后热处理前、过程中及热处理后一系列工艺问题,比如:
a)焊后热处理方式:
整体或内部、外部加热或内部加热、炉内或炉外及各种方式的要求;
b)焊后热处理温度范围,保温时间范围;
c)对加热装置,温控装置,测温装置,记录装置要求;
d)对自动化程度及各种仪表及其精度规定;
e)焊后热处理工艺卡或方案内部及程序;
f)测温点数量、布置及与工件连接方法;
g)局部焊后热处理时均温区、加热区与隔热区的设置;
h)绝热材料及铺设要求;
i)焊后热处理报告及相应表格。
可以说,没有焊后热处理工艺标准就不能正确的、科学的、真实的完成焊后热处理。
4.3.2没有焊后热处理炉有效加热区测定标准
焊后热处理炉还有“有效加热区”,不少业内人士还不清楚这个概念,笔者估计,国内锅炉压力容器制造厂中约有80%的焊后热处理炉没有测定有效加热区,即使余下20%测定了,也不可靠,因为到目前为止,正在使用的GB9452—2003《热处理炉有效加热区测定方法》中箱式炉范围是宽≤1.5m、长≤5m、高≥0.5m,这只能用于气瓶,不适用于锅炉压力容器和压力管道。
为了使热处理炉装焊件区域内的温度及其保温精度满足热处理工艺要求,必须预先测定热处理炉膛内满足热处理工艺要求的允许装料区(即有效加热区),还要采取必要措施,把焊件装在有效加热区内,所以制定有效加热区测定方法标准是贯彻焊后热处理标准的基础,也是热处理技术进步和水平的重要标志。
4.3.3没有承压设备焊后热处理热工计算规范
承压设备焊后热处理按加热范围分为整体焊后热处理与局部焊后热处理,承压设备本体不可能是各部均匀的,筒体上还有法兰、封头、人孔、接管及其补强板,以及凸缘、盖板、甚至还有内件、挡板,筒体外侧还可能有匝和各种不同结构形式的裙座,这就除了考虑总体热工计算外,还得考虑各部分热工计算,究竟在哪儿加热?
加热到多少度?
究竟在哪儿隔热?
隔热层有多宽?
多厚?
等等
承压设备总体焊后热处理热工计算,毕竟不太复杂,但也需要编制相关规范,各部分局部焊后热处理则成为至今尚未看到热工计算实例,更不用说成为标准了。
4.4焊后热处理记录可信度
承压设备焊后热处理的核心是要求焊件上温度均匀,在规定范围内波动,保温时间可以统计。
要做到这两点实属不易。
尽管当前,焊后热处理结果都采用焊后热处理曲线来表达,但放在档案中的焊后热处理曲线可靠性如何,值得怀疑!
采用霍克喷咀进行球罐焊后热处理时,由二次进风助燃,下人孔及其附近的球壳板温度明显不足,越接近人孔的球壳板温度越低。
照理讲,应在离人孔1m~2m范围内的球壳板按温度梯度,大面积补温才对,但几乎所有热处理企业都不这样做,而焊后热处理曲线都是正确的,原来“补温”有“猫腻”,什么地方有热电偶,就在该地方补温,所以存入档案中的热处理曲线都可能是正确的。
我们也了解到,某厂生产的管道焊后热处理装置,可以保证任何使用单位,在任何条件下,对任何材料进行焊后热处理都能保证合格。
谜底是,制造商在销售加热装置产品同时,也配套供应各种常用材料焊后热处理曲线图。
即使按规定不做“小动作”的焊后热处理曲线也很难使人信服。
大型承压设备由若干个测温点,如2000m3球罐需要43个测温点,采用12点长图记录仪,则要4台,每张记录焊后热处理的曲线图上,当进入保温温度前后,各测温点都相当靠近,难以区分每个测温点的数值,不仅少一个点,即使少三个点也无法查证,少一个点就意味将近10m范围内温度数值为空白。
对于焊后热处理曲线来讲,如果图上没有标注走纸速度,没有将环境温度恢复到零度,不考虑当时湿度,那么记录曲线更难以确定数值的可靠性了。
对焊后热处理温度的测量与记录的可信度持疑,是从大量的现实教育中得出的。
如在温度测量导线进入接线柜时,时有“并线”情况发生。
所谓“并线”就是将温度指示不正确的测量导线与指示正确的测量导线并联,共同固定在温度记录接线柱上。
还有更“高级”的方法,即一台电炉、一台电脑,不管现场是否进行焊后热处理,也不管焊后热处理是否正确,早已在办公室内批量造出合格的焊后热处理曲线了,保证“曲线条条清晰,数据个个正确”,令人真假难辨,不得不防止焊后热处理曲线造假,数值造假。
焊后热处理正确性是焊后热处理规范保证的,焊后热处理的温度与时间是使用记录仪表来显示、储存、打印、存档的,不对记录仪表的正确性、真实性做出审定,不在现场进行有效监督,不能分辨每个测量点温度与时间数值,那么,记录仪表中的曲线有什么用呢?
4.6焊后热处理实践知识普及不足
承压设备焊后热处理重要性,需要进行焊后热处理的条件都十分清楚。
但如何实施焊后热处理不一定都明白。
举一个例子,球罐的焊后热处理是国内大型承压设备中数量最多的产品,球罐焊接工艺评定、球罐产品焊接试件、球罐焊后热处理工艺需要重新认识,标注焊后热处理规范的设计技术文件也绝大部分要重新核实。
焊后热处理保温时间是影响焊后热处理质量的重要参数。
如何确定承压设备焊后热处理保温时间做法相差很大。
部分技术人员按设备的焊后热处理厚度(