机械加工工艺必备.docx
《机械加工工艺必备.docx》由会员分享,可在线阅读,更多相关《机械加工工艺必备.docx(10页珍藏版)》请在冰豆网上搜索。
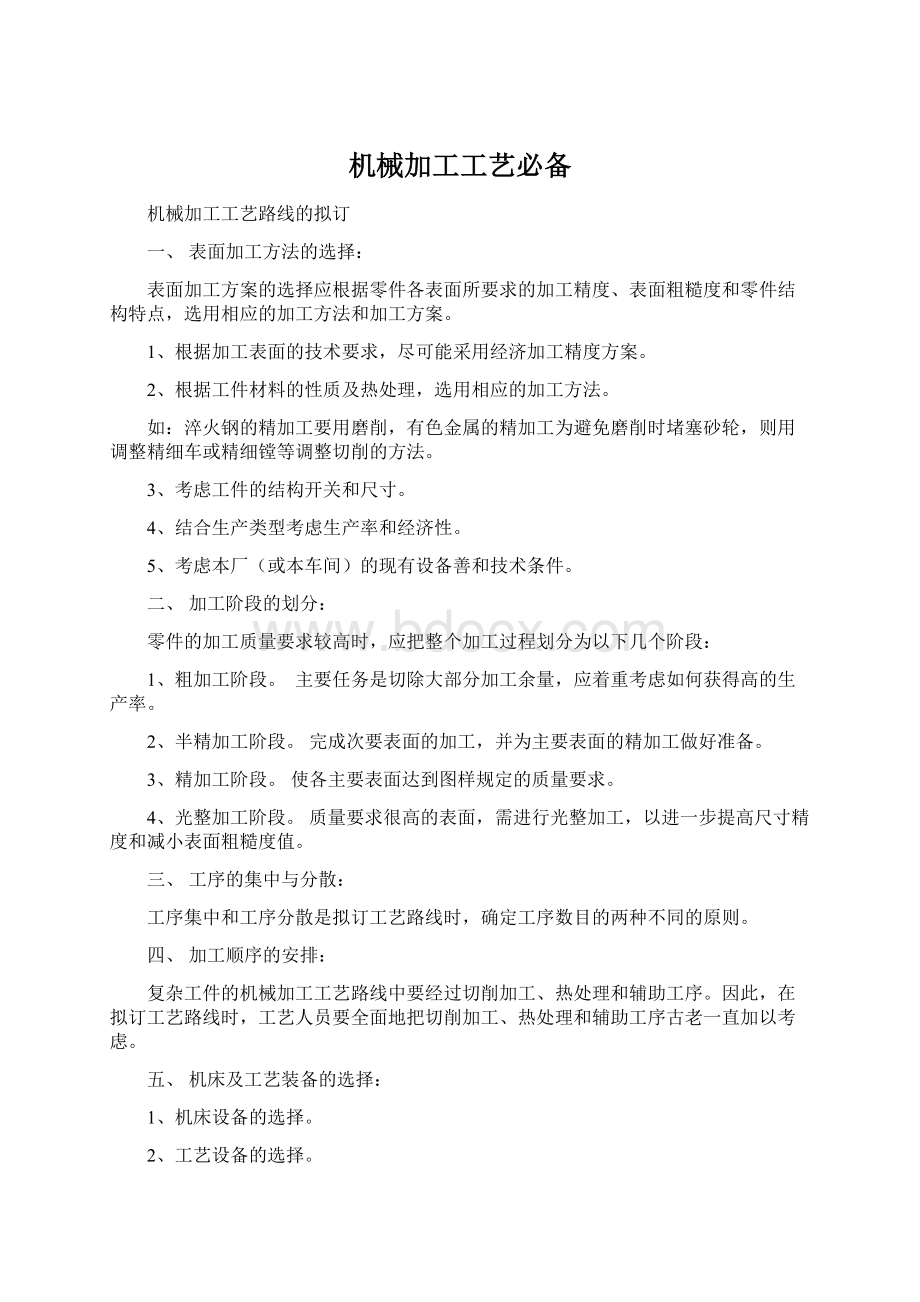
机械加工工艺必备
机械加工工艺路线的拟订
一、表面加工方法的选择:
表面加工方案的选择应根据零件各表面所要求的加工精度、表面粗糙度和零件结构特点,选用相应的加工方法和加工方案。
1、根据加工表面的技术要求,尽可能采用经济加工精度方案。
2、根据工件材料的性质及热处理,选用相应的加工方法。
如:
淬火钢的精加工要用磨削,有色金属的精加工为避免磨削时堵塞砂轮,则用调整精细车或精细镗等调整切削的方法。
3、考虑工件的结构开关和尺寸。
4、结合生产类型考虑生产率和经济性。
5、考虑本厂(或本车间)的现有设备善和技术条件。
二、加工阶段的划分:
零件的加工质量要求较高时,应把整个加工过程划分为以下几个阶段:
1、粗加工阶段。
主要任务是切除大部分加工余量,应着重考虑如何获得高的生产率。
2、半精加工阶段。
完成次要表面的加工,并为主要表面的精加工做好准备。
3、精加工阶段。
使各主要表面达到图样规定的质量要求。
4、光整加工阶段。
质量要求很高的表面,需进行光整加工,以进一步提高尺寸精度和减小表面粗糙度值。
三、工序的集中与分散:
工序集中和工序分散是拟订工艺路线时,确定工序数目的两种不同的原则。
四、加工顺序的安排:
复杂工件的机械加工工艺路线中要经过切削加工、热处理和辅助工序。
因此,在拟订工艺路线时,工艺人员要全面地把切削加工、热处理和辅助工序古老一直加以考虑。
五、机床及工艺装备的选择:
1、机床设备的选择。
2、工艺设备的选择。
各种加工方法所能达到的经济精度、表面粗糙度值以及表面开关、位置精度可查阅《金属加工工艺人员手册》。
下面列出一些常用的以作参考:
表1-1外圆表面加工方法
序号
加工方法
经济精度公差等级
表面粗糙度Ra/um
适应范围
1
粗车
IT13~IT11
50~12.5
适用于除淬火钢以外的金属材料
2
粗车-半精车
IT10~IT8
6.3~3.2
3
粗车-半精车-精车
IT8~IT7
0.8~1.6
4
粗车-半精车精车-滚压(抛光)
IT8~IT7
0.2~0.025
5
粗车-半精车-磨削
IT8~IT7
0.8~0.4
主要用于淬火钢,也可用于未淬火钢,但不宜加工有色金属
6
粗车-半精车-粗磨-精磨
IT7~IT6
0.4~0.1
7
粗车-半精车粗磨-精磨-超精加工
IT5
0.1~0.01
8
粗车-半精车-精车-精细车
IT7~IT6
0.4~0.025
主要用于有色金属加工
9
粗车-半精车粗磨-精磨-超精磨
IT5以上
0.025~0.005
极高精度的外加加工
10
粗车-半精车粗磨-精磨-研磨
IT5以上
0.1~0.01
表1-2平面加工方法
序号
加工方法
经济精度公差等级
表面粗糙度Ra/um
适应范围
1
粗车-半精车
IT13~IT11
6.3~3.2
回转体零件的端面
2
粗车-半精车-精车
IT8~IT7
1.8~0.8
3
粗车-半精车-磨削
IT8~IT6
0.8~0.2
4
粗刨(或铣削)-精刨(或精铣)
IT9~IT8
6.3~1.6
一般未淬硬表面
5
粗刨(或铣削)-精刨(或精铣)-刮研
IT7~IT6
0.8~0.1
6
粗刨(或铣削)-精刨(或精铣)-宽刀精刨
IT7~IT6
0.8~0.2
7
粗刨(或铣削)-精刨(或精铣)-磨削
IT7
0.8~0.2
精度要求高的淬硬表面和不淬硬表面
8
粗刨(或铣削)-精刨(或精铣)-粗磨-精磨
IT7~IT6
0.4~0.02
9
粗铣-拉
IT9~IT7
6.3~3.2
大量生产较小平面
10
粗铣-精铣-粗磨-研磨
IT5以上
0.1~0.008
高精度平面
表1-3内孔表面加工方法
序号
加工方法
经济精度公差等级
表面粗糙度Ra/um
适应范围
1
钻
IT13~IT11
>=12.5
加工未淬火钢及铸铁实心毛坯,也可用于加工有色金属(孔小于15~20mm)
2
钻-扩
IT11~IT10
12.5~6.3
3
钻-扩-铰
IT9~IT8
3.2~1.6
4
钻-扩-粗铰-精铰
IT7
1.6~0.8
5
钻-铰
IT10~IT8
6.3~1.6
6
钻-粗铰-精铰
IT8~IT7
1.6~0.8
7
钻-(扩)-拉
IT9~IT7
1.6~0.1
大批大量生产
8
粗镗(或扩孔)
IT13~IT11
12.5~6.3
除淬火钢外和各种钢材,毛坯上已有铸出或锻出孔
9
粗镗(扩)-半精镗(精扩)
IT9~IT8
3.2~1.6
10
粗镗(扩)-半精镗(精扩)-精镗(铰)
IT8~IT7
1.6~0.8
11
粗镗(扩)-半精镗(精扩)-精镗(铰)-浮动镗
IT7~IT6
0.8~0.4
12
粗镗(扩)-半精镗-磨
IT8~IT7
0.8~0.2
主要用于淬火钢,不宜用于有色金属
13
粗镗(扩)-半精镗-粗磨-精磨
IT7~IT6
0.2~0.1
14
粗镗-半精镗-精镗-金刚镗
IT7~IT6
0.4~0.05
主要用于有色金属
一:
机械加工划分加工阶段的原因
1、保证加工。
工件加工划分阶段后,粗加工因余量大、切削力大等因素造成的加工误差,可通过半精加工和精加工逐步得到纠正,保证加工质量。
2、有利于命题使用设备。
粗加工要求功率大、刚性好、生产率高、精度不高的设备。
精加工则要求精度高的设备。
划分加工阶段后,就可充分发挥粗精加工设备的特点,避免以精干粗,做到合理使用设备。
3、便于安排热处理工序,使冷热加工工序配合得更好。
例如粗加工后工件残余应力大,可安排时效处理,消除残余应力;热处理引起的变形又可在精加工中消除。
4、便于及时发现毛坯缺陷。
毛坯的各种缺陷如气孔、砂眼和加工余量不足等,在粗加工后即可发现,便于及时修补或决定报废,以免继续加工后造成工时和费用的浪费。
5、精加工、光整加工安排在后,可保护精加工和光整加工过的表面少受磕碰损坏。
二:
工序集中与分散的特点
我们在设计中应根据生产类型、现有生产条件、工件结构特点和技术要求等进行综合分析后选用。
生产批量小时多采用工序集中,生产批量大时可采用工序集中也可采用工序分散。
--集中--
1、有利于采用高效专用机床设备及工艺装备,生产率高。
2、工件安装次数少,不但可缩短辅助时间,还有利于保证各加工表面间的位置精度。
3、工序数目少,可减少机床数量、操作工人生产面积。
--分散--
1、设备及工艺装备简单,调整和维修方便。
2、可采用最合理的切削用量,减少基本时间。
3、设备数量多,操作工人多,占用生产面积大。
三:
加工顺序的安排:
1、甚而先行。
选为精基准的表面,应安排在起始工序先进行加工,以便尽快为后续加工提供精基准。
2、先粗后精。
当零件需要划分加工阶段时,先安排各表面的粗加工,中间安排半精加工,最后安排主要表面的精加工和光整加工。
3、先主后次。
先加工装配甚面和工作表面等主要表面,后加工键槽、紧固用的光孔与螺纹孔等次要表面。
因为将要表面的加工面积较小,它们又往往与主要表面有一定的相互位置要求,所以一般应放在主要表面半精加工之后进行加工。
4、先面后孔。
四:
热处理工序的安排
热处理在工艺路线中的位置安排主要取决于热处理的目的。
1、预备热处理。
A、退火与正火常安排在粗加工之前,以改善切削加工性能和消除毛坯的内应力;
B、调质一般安排在粗加工之后、半精加工之前进行,以保证调质层的厚度;
C、时效处理用以消除毛坯制造和机械加工中产生的内应力。
对于精度要求不太高的工件,一般在毛坯进入机械加工之前安排一次人工时效即可。
对于机床床身、立术等结构复杂的铸件,应在粗加工前、后都要进行时效处理。
对于一些刚性差的精密零件,在粗加工、半精加工和精加工过程中要安排多次人工时效。
2、最终热处理。
A、主要用于提高零件的表面硬度和耐磨性以及防腐、美观等。
淬火、渗碳淬火等安排在磨削加工之前进行;
B、氮化处理由于温度低,变形小,且氮化层薄,故应放在精磨之后进行。
C、表面装饰性镀层、发蓝处理,应安排在机械加工完毕之后进行。
3、辅助工序的安排。
A、检验工序是主要的辅助工序,是保证产品质量的重要措施。
除各工序操作者自检外,在关键工序之后、送往外车间加工前后、零件全部加工结束之后,一般均应安排检验工序。
B、此外,去毛刺、倒钝锐边、去磁、清洗及涂防锈油等都是不可忽视的辅助工序。
4、工序间的衔接。
有些零件的加工是由普通机床和数控机床共同完成的,数控机床加工工序一般穿插在整个工艺过程之间,应注意解决好数控工序与非数控工序间的衔接。
A、如作为定位基准和孔和面的精度是否满足要求;
B、后首工序的加工余量是否足够等。
一、加工余量的确定方法:
1、查表法
根据工艺手册或工厂中的统计经验资料查表,并结合具体情况加以修正来确定加工余量。
此法在实际生产中广泛应用。
2、经验估算法
凭经验来确定加工余量。
为防止因余量过小而产生废品,所估余量往往偏大。
此法只可用于单件小批生产。
3、分析计算法
通过对影响加工余量的各项因素进行分析和综合计算,来确定所需要的最小工序余量。
它是最经济合理的方法,但必须要有齐全而可靠的实验数据资料,且计算较烦琐,在实际生产中应用尚少。
应该指出的是,对于大批大量生产,应力求采用分析计算法。
二、工序尺寸的确定
工序尺寸及其公差的确定,不仅取决于设计尺寸及加工余量,而且还与工序尺寸的标注方法以及定位基准选择和转换有着密切的关系。
故计算工序尺寸时应根据不同和情况采用不同的方法。
1、设计基准重合时。
A、确定各工序的基本余量
B、确定各工序加工的经济精度
C、根据设计尺寸和各工序余量,从后往前推算各工序基本直到毛坯尺寸
D、最后将各工序尺寸的公差按“人体原则”标注
2、基准不重合时,就必须应用尺寸链原理进行分析计算。
建立尺寸链。
假设:
A0为封闭环,A1、A2、为增环,A3为减环。
计算A0?
①基本尺寸:
A0=A1+A2-A3
②上下偏差:
上、ES(A0)=ES(A1)+ES(A2)-EI(A3)增上减下
下、EI(A0)=EI(A1)+EI(A2)-ES(A3)增下减上
③按“人体原则”标注
生产成本
生产成本包括两大类费用:
1、与工艺过程直接有关的费用叫工艺成本,约占生产成本的70%~75%。
2、与工艺过程无关的费用,如行政人员工资、厂房折旧、照明取暖等。
由于同一生产条件下与工艺过程无关的费用基本上是相等的,因此对零件工艺方案进行经济分析时,只要分析与工艺过程直接有关的工艺成本即可。
一、工艺成本
1、可变费用V可变费用与产品年产量有关,它包括材料费或才干费、损人工人的工资、机床的维护费、万能机床和万能夹具及刀具的折旧费。
2不变费用C不变费用与零件年产量无关,它是指专用机床和专用夹具、刀具的折旧和维护费用。
因为起用机床、专用夹具及刀具是专为加工某零件所用,不能用来加工其他零件,而工艺装备及设备的折旧年限是一定的,因此专用机床、专用夹具及刀具的费用与零件的年产量无直接关系,即当年产量在一定范围内变化时,这种费用基本上保持不变。
一种零件的全年工艺成本E和单件工艺古本Ed,可用下式表示:
Ed=V+C/N
E=NV+C
式中V——每个零件的可变费用,单位为元/件;
N——工件的年产量,单位元/件;
C——全年的不变费用,单位元/件。
二、工艺方案的经济评比
1、工艺方案的基本投资相