旋流器分选摘录.docx
《旋流器分选摘录.docx》由会员分享,可在线阅读,更多相关《旋流器分选摘录.docx(15页珍藏版)》请在冰豆网上搜索。
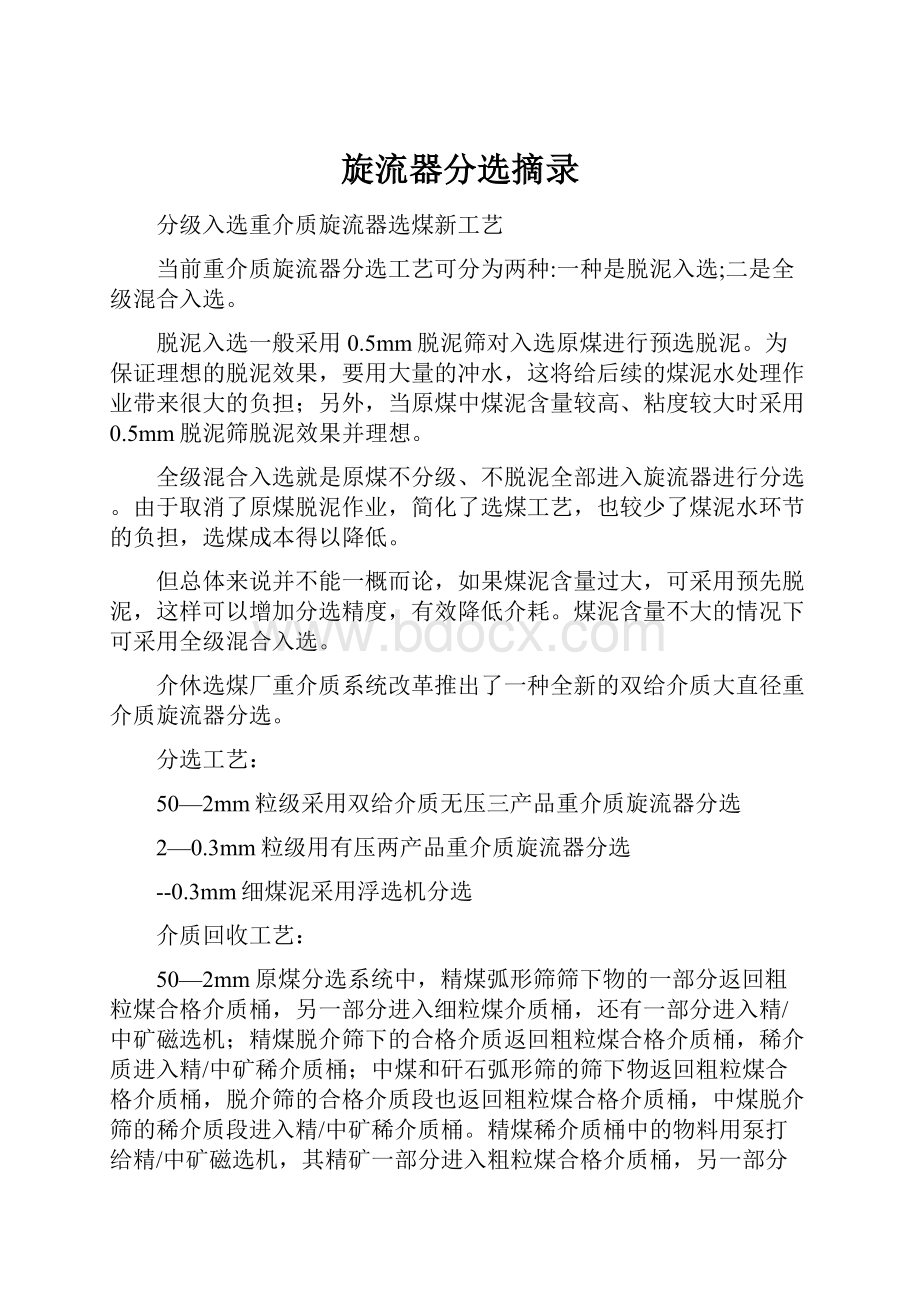
旋流器分选摘录
分级入选重介质旋流器选煤新工艺
当前重介质旋流器分选工艺可分为两种:
一种是脱泥入选;二是全级混合入选。
脱泥入选一般采用0.5mm脱泥筛对入选原煤进行预选脱泥。
为保证理想的脱泥效果,要用大量的冲水,这将给后续的煤泥水处理作业带来很大的负担;另外,当原煤中煤泥含量较高、粘度较大时采用0.5mm脱泥筛脱泥效果并理想。
全级混合入选就是原煤不分级、不脱泥全部进入旋流器进行分选。
由于取消了原煤脱泥作业,简化了选煤工艺,也较少了煤泥水环节的负担,选煤成本得以降低。
但总体来说并不能一概而论,如果煤泥含量过大,可采用预先脱泥,这样可以增加分选精度,有效降低介耗。
煤泥含量不大的情况下可采用全级混合入选。
介休选煤厂重介质系统改革推出了一种全新的双给介质大直径重介质旋流器分选。
分选工艺:
50—2mm粒级采用双给介质无压三产品重介质旋流器分选
2—0.3mm粒级用有压两产品重介质旋流器分选
--0.3mm细煤泥采用浮选机分选
介质回收工艺:
50—2mm原煤分选系统中,精煤弧形筛筛下物的一部分返回粗粒煤合格介质桶,另一部分进入细粒煤介质桶,还有一部分进入精/中矿磁选机;精煤脱介筛下的合格介质返回粗粒煤合格介质桶,稀介质进入精/中矿稀介质桶;中煤和矸石弧形筛的筛下物返回粗粒煤合格介质桶,脱介筛的合格介质段也返回粗粒煤合格介质桶,中煤脱介筛的稀介质段进入精/中矿稀介质桶。
精煤稀介质桶中的物料用泵打给精/中矿磁选机,其精矿一部分进入粗粒煤合格介质桶,另一部分分流到细粒煤介质桶。
矸石脱介筛稀介质段进入矸石稀介质桶,然后用泵打给细粒煤矸石磁选机,其精矿全部返回粗粒煤合格介质桶。
2—0.3mm原煤分选系统中,精煤弧形筛的筛下物一部分返回细粒煤介质桶,另一部分分流到精煤磁选机;弧形筛的筛上物也进入精煤磁选机,磁选机精矿进入细粒煤介质桶。
矸石弧形筛的筛下物进入粗粒煤合格介质桶;筛上物进入矸石磁选机,磁选精矿也进入粗粒煤合格介质桶。
综合介质回收系统可知,在粗粒煤重介质系统中,随溢流排出的细粒级介质有一部分进入到细粒级煤重介质系统(50—2mm粒级分选系统中精煤弧形筛下的一部分筛下物进入细粒煤介质桶;精煤稀介质桶中的物料经过精/中矿磁选机分选后其中精矿中的一部分分流进入细粒煤介质桶);而在细粒级煤重介质系统中,随底流排出的粗粒即介质全部回到粗粒煤重介质系统中(矸石弧形筛的筛下物进入粗粒煤合格介质桶;筛上物进入矸石磁选机,磁选精矿进入粗粒煤合格介质桶)。
双给介质大直径无压三产品中介质旋流器简介:
3SNWX1300/920重介质旋流器为国内新研制开发的大型化先进重介质选煤设备:
一段旋流器采用圆筒型,而且是双给介质,其中一个是稳定的大流量入口,另一个是可调节的小流量入口。
圆筒型旋流器内的速度场和密度场更均匀,对物料按悬浮也世纪密度分选更有利,分选精度更高、产品质量控制也更容易,双给介口是得其入料压力大大降低,能延长旋流器的使用寿命,而且更易于调节悬浮液的密度。
另外,对于双给介质旋流器来说,只需用小功率泵加上变频器即可灵活调节进入旋流器悬浮液的流量和压力。
这样可降低购买变频器的成本,因为对于只用一个介质入口的常规重介质旋流器,只能用一台大功率泵。
若想调节悬浮液的流量和压力,只能加一台大变频器。
分级入选重介质旋流器选煤工艺的优点:
1)分级入选符合等λ原则,可以最大限度地提高精煤产率。
2)降低介耗和能耗,提高了设备的可靠性。
3)降低入浮量。
常规的重介质工艺中,单一采用大直径旋流
器不能对煤泥进行有效分选,即使配套煤泥重介质分选工艺,也只是对精煤弧形筛筛下分流的部分煤泥进行分选,达不到全部入选;而分级入选工艺中,2—0.3mm粒级原煤全部进入小直径旋流器进行有效分选,分选精度大幅度提高,这样就减少了进行入浮作业的煤泥量,降低生产成本。
4)减少厂房体积。
50—2mm粒级产品脱介是采用小面积脱介筛;2—0.3mm粒级产品采用磁选机脱介。
、因此减少厂房面积。
5)降低工程投资。
高效、简化的重介质选煤及煤泥水处理新工艺
原料煤不分级、不脱泥重介质旋流器选煤新工艺,可利用单一低密度重悬浮液系统一次分选出质量合格的精煤、中煤和矸石三种产品或精煤和尾煤两种产品,也可以低密度悬浮液系统实现高密度分选。
而且也彻底解决了浅槽等块煤重介质分选机和量产品重介质旋流器无法实现高密度(大于1.9kg/L)排矸的难题。
重介质旋流器工艺指标:
由于重介质旋流器内的速度梯度破坏了悬浮液的结构化粘度,如果重介质旋流器的结构尺寸和工作参数合理,处理不脱泥原煤时分选精度依然很高。
对于一些可选性极差或要求有效分选粒度下限更低的煤泥,还可采用国华科技的专利技术——煤泥重介质旋流器进行分选。
其原理是在重介质旋流器中,磁铁矿粉收到了离心分级作用,随精煤悬浮液携带而出的磁铁矿粉粒度细,可以作为煤泥重介质旋流器的分选悬浮液。
这样,就不需要单设超细粒悬浮液的制备、输送和回收系统。
煤泥重介质旋流器分有效分选粒度下限可达0.1mm。
具体工艺流程如图2所示;
介耗:
根据生产实践,实现低介耗需要注意一下几点:
1)磁选机的选型及操作调整。
2)脱介筛的选型,筛宽、筛面结构和喷水位置等都很重要。
3)循环悬浮液的分流量要足够,以免粘度过高。
4)煤泥水深度澄清,实现清水脱介。
煤泥水处理工艺:
炼焦煤选煤厂的煤泥水分为2个部分,即精煤泥处理流程和尾煤泥处理流程。
精、尾煤泥处理流程均选用LWZ系列沉降过滤式离心脱水机。
精煤泥处理流程:
精煤泥处理的主要目的是对煤泥实现经济、有效的分选,同时尽可能降低精煤泥水分。
国华科技倡导的精煤泥两次浮选、双段脱水回收的工艺流程如图3所示。
精煤磁选机尾矿用泵送到精煤泥弧形筛进行分级,其筛下水进入一次浮选作业,其筛上物与浮选泡沫汇合“掺粗”后,由沉降过滤式离心脱水机回收大于0.045为主的粗精煤泥;携带小于0.045mm细精煤泥为主的沉降过滤式离心脱水机的滤液和离心液进入二次浮选作业,其浮选泡沫由压滤机脱水回收,压滤机滤液汇入循环水。
沉降过滤式离心机的脱水产物与压滤机滤饼(两者为选煤厂的精煤泥)掺入重介选的精煤中,作为最终销售商品——炼焦精煤。
精煤泥处理的特点:
精煤泥两次浮选、双段脱水回收的工艺流程具有以下特点:
1)独特的分级浮选技术
中国煤泥普遍难浮选,原因是浮选入料中粒度小于0.03mm的高灰分粘土类泥质含量高,他们混杂在浮选泡沫产物中,增加了浮选精煤灰分。
流程第一次浮选的泡沫产物经沉降过滤式离心机脱水机脱出的含有较高灰分泥质的离心液、滤液进行二次浮选,排除混杂在泡沫产物中的高灰分泥质,使浮选精煤灰分降低了约1%,浮选完善指标提高了约3%。
2)离心机入料“掺粗”
将粗煤泥弧形筛的筛上物与浮选泡沫产品混合“掺粗”,是泡沫产物中小于0.045mm粒级的产率小于40%,满足后续脱水回收设备的要求,同时简化了弧形筛筛上物的处理工序。
3)两段脱水
掺粗后的浮选泡沫产物首先用处理能力大、产率水分低的沉过滤式离心脱水机回收约80%大于0.045mm的“粗粒”精煤泥和30%以上小于0.045mm的“细粒”精煤泥;其余的精煤泥则用压滤机脱水回收。
尾煤泥处理:
国华科技倡导的尾煤泥处理流程的目的主要有以下几个方面:
(1)最大限度地回收较粗粒度为主的尾煤,降低其灰分,掺入中煤,提高其产值;
(2)对于少量细尾煤泥,彻底实现固液分离
(3)采用添以钙、镁离子型凝聚剂为主,聚丙烯酰胺絮凝剂为辅的煤泥水深度澄清技术,实现清水洗煤。
两段浓缩两段回收的尾煤泥处理流程如图4所示。
尾煤泥(浮选尾煤和截粗后的中煤、矸石磁选机尾矿)首先进入一段斜管浓缩机进行水力分级,其底流用沉降过滤式离心机脱水回收大于0.045mm为主的粗粒尾煤泥,其离心液和一段浓缩机的溢流进入二段斜管浓缩机实现煤泥水深度澄清,其清净溢流循环使用,作为脱介筛喷水和浮选稀释水,其底流有压滤机脱水回收。
国际上普遍采用尾煤泥水单段浓缩单段回收工艺,工艺一般采用压滤机处理,缺点是滤饼粘结成团,给销售和利用带来很大的困难;压滤机处理能力低,需要台数,基建投资大;当原生煤泥量大、粘土细泥多时,常因处理不及时,造成煤泥聚集、恶性循环。
高效重介质旋流器脱硫选煤新工艺
中国中硫和高硫煤约占储量的12%,据统计高硫煤矿区的原煤,大多属于肥煤和焦煤,是冶金工业不可缺少的煤种。
鉴于中国一般高硫煤中含有相当多可选的硫化铁硫,应首先重视价廉有效的物理洗选脱硫,并以选煤为龙头全面综合考虑高硫煤的洁净利用。
煤炭科学研究总院唐山分院在总结二产品重介质旋流器选三产品和三产品重介质旋流器选煤工艺的优缺点的基础上,结合南桐矿务局南桐选煤厂分选高硫难选煤的需要,研究成功了“单一低密度介质、实现双段介质密度自控选三产品的重介质旋流器选煤新工艺”,取得了良好的技术经济效果。
新的重介质旋流器选三产品(包括煤泥重介质旋流器选煤)工艺的特点是:
主选(Φ600mm)旋流器、再选(Φ450mm)旋流器和煤泥精选(Φ150mm)旋流器都各自独立,都配备有各自的分选介质密度自动测量、调整和控制设施,但循环悬浮液只有一个低密度介质系统。
在保证高分选精度和效率的基础上,实现了高低密度分选多种产品。
南桐选煤厂的工艺:
入选原煤(25—0mm高硫煤),选前不脱泥直接入煤介混合桶,经泵压送到Φ600mm主选(一段)重介质旋流器内。
分选悬浮液密度控制在1450±10kg/m3。
主选(一段)中将诶之旋流器选出精煤,重产物与悬浮液一起入二段再选旋流器,再选旋流器入料段设有检测和调整分选悬浮液密度装置,要求悬浮液达到和控制在1750±20kg/m3以内。
二段重介质旋流器选出中煤和矸石。
小于0.5mm级煤泥从脱介筛脱出于合格介质一起分流出来,进入煤泥分选调节桶,在这里对煤泥分选介质密度检测、调整,再经泵送入煤泥分选旋流器组(投入台数视其来料量而自动控制),煤泥分选的介质密度控制在1380±10kg/m3或1400±10kg/m3范围。
生产试验结果表明:
主选(一段)选精煤的可能偏差Ep=0.015—0.025;再选(二段)选中煤和矸石的可能偏差Ep=0.03—0.035;煤泥重介质旋流器分选0.5—0.04mm级煤泥的可能偏差Ep=0.06—0.07,大于0.5mm级精煤无机硫脱硫率达到85%以上,无机硫降硫率达75%以上,见下表。
同时新的重介质旋流器选煤脱硫工艺的煤泥水量大大减少,据测定的循环水处理量降到2.41m3/t原煤,考虑生产不均衡系数20%,也只有2.89m3/t原煤。
比常规跳汰—浮选流程的循环水量减少17%--30%,比跳汰—重介—浮选流程可减少30%--40%。
同时与常规二产品和三产品重介质旋流器选三种产品中介相比电耗量降低16%--33%。
开滦集团选煤工艺改造的探索与实践
各种选煤工艺特点与选择应用:
跳汰粗选—重介质旋流器精选工艺:
对原煤中大于50mm部分大多数为矸石,块煤较少,并含有大量的杂物,并且其选煤厂原来采用跳汰选煤方法,采用跳汰粗选—重介质旋流器精选工艺。
跳汰分选原煤处理量大,生产成本较低,对易选煤分选指标较好,适合高密度分选,作为原煤排矸工艺可获得比较理想的效果。
优点如下:
(1)利用跳汰机处理能力大、可不分级入选,在粗选过程中排出大部分的矸石,并起到脱泥的作用;使粗选时的分选密度在1.6g/L左右,在这种情况下,精煤损失也比较小。
(2)跳汰分选出的粗精煤通过捞坑脱水,既消除了原精煤脱水筛脱水效果不好、易跑水的问题,也起到了除杂的作用。
(3)减少了进入重介质旋流器分选的物料量,减少了重介质系统的生产负荷,并克服了重介质旋流器排矸能力较差的问题;同时,也降低了介质的消耗、设备和管理的磨损,运行费用较低。
块煤。
末煤分级重介质分选工艺:
块煤重介质立轮—末煤重介质旋流器分选洗选工艺的系统较复杂,生产成本也较高,但对块煤含量高,块、末煤可选性均较差的原煤,采用分级重介质分选工艺,无论在技术上还是在经济上都是必要的。
末煤分选工艺的选择可根据末煤的特性,选择量产品中将诶之旋流器主再选或三产品重介质旋流器分选。
此工艺的主要特点:
(1)块煤重介质立轮分选上限高,处理能力大。
(2)针对小于0.5mm级原煤含量大的问题,在原煤分级过程中进行脱泥,不但简化了工艺流程,还可防止大量煤泥进入末煤分选系统,致使重介质悬浮液粘度过高,合格介质需要大量分流,导致磁选机负荷加大的问题。
(3)块、末煤分级重介质洗选分选精度高,但是分选系统和介质循环系统相对复杂。
随着介质密度控制技术的发展,块、末煤两个重介质系统可使用一个介质循环系统,这样可使介质系统得到简化。
量产品重介质旋流器主再选和三产品重介质旋流器分选工艺:
重介质旋流器适合分选难选煤或极难选煤,要求原煤准备系统比较完善,入选原煤中无粒度超限的大块煤或大块矸石,原煤杂物少,不会造成堵泵或堵旋流器等生产事故;并且原煤硬度较高,不易破碎和泥化。
使用这种工艺在流程和设备选择时,需在充分考虑和分析原煤性质、可选性、原煤准备系统的完善程度、精煤和中煤产品的质量要求等多种因素基础上,再确定是选用量产品重介质旋流器主再选,还是三产品中将诶之旋流器分选工艺。
直接浮选、分级浮选和二次精选工艺:
由于煤比矸石易碎,因而小于0.5mm粒级原煤往往质量较好,精煤理论产率较高,在洗选焦煤、肥煤等比较稀缺的煤种时,一般设置浮选系统。
在选择浮选工艺时,应充分考虑煤泥可浮性的难易程度,以实现在降低浮选精煤灰分的同时最大限度地提高浮选精煤产率的目的。
二次浮选或分级浮选流程系统相对复杂,比较适合难浮选煤的浮选。
尾煤二次浓缩、两段回收流程:
选煤厂通常采用浓缩—压滤工艺处理煤泥水,实现煤泥(尾煤)厂内回收、洗水闭路循环。
但是,单一的使用压滤机(或个别的采用过滤机)往往因对尾煤矿浆的性质,包括粒度组成、浓度等指标要求较高,系统的适应性差,当矿浆的粒度组成或浓度变化时,会严重影响系统的处理能力,甚至导致系统不能正常运行。
设计二段浓缩、两段回收的联合处理工艺或分级处理工艺,不但可提高煤泥回收系统的工作效率,还可根据分级处理后的产品质量,完善产品结构,提高选煤的经济效益。
选煤新工艺在响水矿选煤厂的应用
响水矿选煤厂的主要工艺流程为:
原煤首先经脱泥筛脱泥(筛缝1.2mm),50—1.2mm进入三产品重介质旋流器分选,1.2—0.25mm进入TBS干扰床分选机分选,-0.25mm粒级进入浮选工艺。
选煤工艺方案分析:
响水矿选煤厂入洗原煤为主焦煤偏瘦,原煤中细粒级物料含量高(-0.5mm粒级约占40.00%),若洗选灰分为10.00%的精煤,分选密度±0.1含量为62.60%,属于极难选煤。
因此,选用重介质分选工艺有两种:
一是不脱泥无压给料全重介质分选;二是跳汰粗选、重介质精选工艺。
不脱泥无压给料全重介质分选工艺:
优点:
(1)选煤方法单一,系统简单。
(2)设备台数少,管理、操作、维护方便。
(3)耗电、耗水少。
缺点:
(1)由于原煤煤泥量大,所以若煤泥直接进入重介质悬浮液系统,导致悬浮液粘度增加,将严重恶化对细粒级物料的有效分选,分选下限达不到规定的要求。
(2)为减轻悬浮液粘度异常增加的问题,需要加大合格介质的分流量,从而导致介质密度稳定性变差,影响重介质系统的分选效率。
(3)大量合格介质分流进入稀介质,加大了磁选机的负荷,磁选效率降低,导致单位介耗增加。
(4)不脱泥工艺对煤泥水系统管理难度加大,煤泥水系统处理负荷大,产品质量不易控制。
跳汰粗选、重介质精选工艺:
优点:
(1)煤泥预选脱出,循环介质粘度小。
(2)预先脱泥减小了进入介质系统的煤泥量和循环介质量,从而可减少脱介筛面积、降低磁选机负荷,是磁选效率增加、介耗降低。
缺点:
(1)60%的物料需要重复分选。
(2)设备台数多,电耗、水耗高(3)次生煤泥量高。
(4)煤泥水系统处理难度仍然很大。
预先脱泥无压入料重介质旋流器+TBS干扰床粗煤泥分选新工艺:
工艺流程如下图:
工艺特点:
新工艺与原有的两个重介质分选工艺具有如下特点:
(1)50—1.2mm粒级采用分选精度高,精煤回收率高,系统相对简单的预先脱泥无压给料重介质旋流器分选工艺。
(2)1.2—0.25mm粗煤泥采用TBS干扰床分选。
TBS具有分选效率高、结构简单及运行成本低等优点;同时,其密度分割点可控,单位处理量高,占地面积小,入料矿浆粒度分布窄。
(3)原煤预先脱泥后,有效控制了合格介质内的煤泥量,分流量减少,介质密度稳定性提高,提供啊了分选效率。
分流量的减少,使磁选机负荷更为合理,保证了单位介耗指标,控制了选煤成本。
选煤新工艺在晋华选煤厂的成功应用
选煤新工艺的特点:
入选原煤为动力煤,入厂原煤的粒度为80—0mm,原煤经脱泥分级后,大于1.5mm由重介质旋流器分选,1.5—0mm煤泥经分级旋流器分级,1.5—0.1mm由螺旋分选机分选,小于0.1mm煤泥经浓缩机浓缩由压滤机回收后掺入末精煤中,也可随矸石排弃。
重介质旋流器分选系统:
大于1.5mm原煤采用重介质旋流器分选,可得到最大的精煤回收率,重介质分选对煤质的适应性较强,特别是对原煤粒度组成及含矸量变化适应性较强。
分选下限定为1.5mm可是重介质系统环节简化,避免煤泥对重介质分选的影响,重介质系统的稳定性好,可以大大改善分选效果。
同时可改善脱介效果,使介耗大幅度降低并且节约用水。
1.5mm以下的煤泥由生产成本比较低的螺旋分选机分选,且1.5mm是螺旋分选机分选的理想上限。
螺旋分选机分选系统:
1.5—0.1mm粗煤泥用螺旋分选机分选,螺旋分选机物运动部件,节约动力,维护操作极为方便,选别过程稳定,对入料性质变化适应性强,可实现低成本分选,降灰脱硫效果比较明显。
煤泥水处理系统:
对小于0.1mm的细煤泥不再分选,分级旋流器溢流、末矸石浓缩旋流器溢流进入浓缩机,加絮凝剂后,溢流作为循环水复用,底流由压滤机回收,根据用户对产品质量的要求,滤饼破碎后既可掺入精煤中也可随矸石排弃
新工艺的应用效果:
重介质旋流器作为主选设备,分选效果好,可能偏差E=0.031kg/l,分离出矸石灰分为82.18%。
而且产品质量稳定,实际分选密度控制在1.68—1.71g/cm3之间,精煤灰分一直稳定在6.50%以下。
螺旋分选机分选系统:
螺旋分选机作为粗煤泥分选设备,可能偏差E=0.18kg/L,入选煤泥灰分为11.5%--13.5%,选后精煤灰分为6.9%--7.2%;入料硫分为1.1%--1.2%,选后精煤硫分为0.54%--0.61%,对其技术检查,理论分选密度为1.75g/cm3,煤泥为易选,经计算数量效率达到90%以上。
国内外选煤技术与装备的现状及发展趋势
近年来,重介质旋流器分选技术取得了重大进展,提高了选煤效率;煤泥分选的研究进一步深入,果味除了传统浮游选煤工艺研究外,还进行了油团聚发的研究、选择性絮凝法和选择性聚团法的研究以及调浆和矿物表面改性方面的研究,并取得了一定的进展;流化床选煤技术、干扰床选煤技术逐步进入生产实践。
选煤工艺情况:
当前,选煤工艺及设备存在的主要不足是:
选煤工艺流程主要以跳汰+浮选、重介+浮选、跳汰+重介+浮选这三种工艺为主,为了简化生产环节和系统,在工程设计上,尽量简化工艺,大多采用混合入选,因而在实际的分选过程中导致粗细颗粒在运动上互相干扰;同时,不同的粒级在灰分—密度的关系上存在差别。
因此,采用混合入选工艺,在同一分选密度下,各个粒级必然产生不同的分选效果,必然会影响的分选的效率,造成分选效率低,产品质量波动范围大。
而国外选煤厂在分级入选上做的相对较好,在重选工艺方面虽然以不分级入选为主,但入选前往往先进行脱泥,同时设有粗煤泥分选环节。
近年来,国内出现了粗煤泥的分选工艺、技术和设备,如煤泥重介质分选工艺、TBS分选工艺等。
在选煤工艺设备方面,国内外的选煤设备均存在分选粒度下限高、工艺参数不合理、产品质量差波动大等问题。
选煤装备的发展趋势:
“十二五”期间,为适应大量煤炭洗选加工的需要,要研究符合中国煤质特点的、具有知识产权的单系统1000万t/a特大型动力煤选煤厂成套技术和关键装备、但系统600万t/a特大型炼焦煤选煤厂成套技术和关键设备及其配套通用的关键设备。
需要研发的设备主要有小时处理能力为1000—1200t,入选上限大于150mm的特大型三产品重介质旋流器;小时处理能力为900—1000t,入料粒度为300—13mm的大型高效重介质浅槽分选机;小时处理能以大于500t,入料粒度为350—25mm的大型动筛跳汰机;小时处理能力为2000他,入料粒度为325—25mm的大型动力煤跳汰机;小时处理矿浆能力1500—2500m3的大型浮选机;小时处理能力为300—450t的大型末煤离心脱水机;小时处理能力为60—150t的大型全自动快开压滤机;小时处理能力400m3的大型高效磁选机等。
此外,还要代发远转可靠、处理能力大的选煤厂辅助设备以及智能化的自动控制系统,从而提高原煤的洗选能力。
选煤工艺、技术发展趋势:
对于难选的炼焦煤,为提高精煤产率,需要开发给予中煤释放的二次分选工艺及中煤破碎关键技术。
针对矸石运至地面所带来的问题,“十二五”期间,原煤井下洗选、井下排矸的技术和设备将得到开发利用。
完成原煤井下分选,需要开发适合矿井下运行的选煤成套工艺和设备,主要需要有适应井下的恶劣环境、满足井下安全生产的选择性破碎设备,满足物料杂物较多、工作环境恶劣的井下粘湿物料筛分设备,工艺简单、工作可靠、,满足井下安全生产的动筛跳汰机、浅槽重介质分选机等井下分选设备,以及相关的产品运输、给排水设备等。
国内外选煤工业必将得到迅速的发展,主要发展趋势为:
(1)煤炭的洗选比例将不断提高,保证煤炭资源得到合理的利用,实现节能减排,降低环境污染。
(2)将开发出适合难选和极难选煤的分选工艺和技术。
(3)设备大型化。
(4)选煤厂自动控制方面将实现管、控、监综合智能化控制。
(5)洁净煤技术得到迅速的发展,实现清洁能源。
[文档可能无法思考全面,请浏览后下载,另外祝您生活愉快,工作顺利,万事如意!
]