数控加工典型配合件数控车削工艺规程设计.docx
《数控加工典型配合件数控车削工艺规程设计.docx》由会员分享,可在线阅读,更多相关《数控加工典型配合件数控车削工艺规程设计.docx(35页珍藏版)》请在冰豆网上搜索。
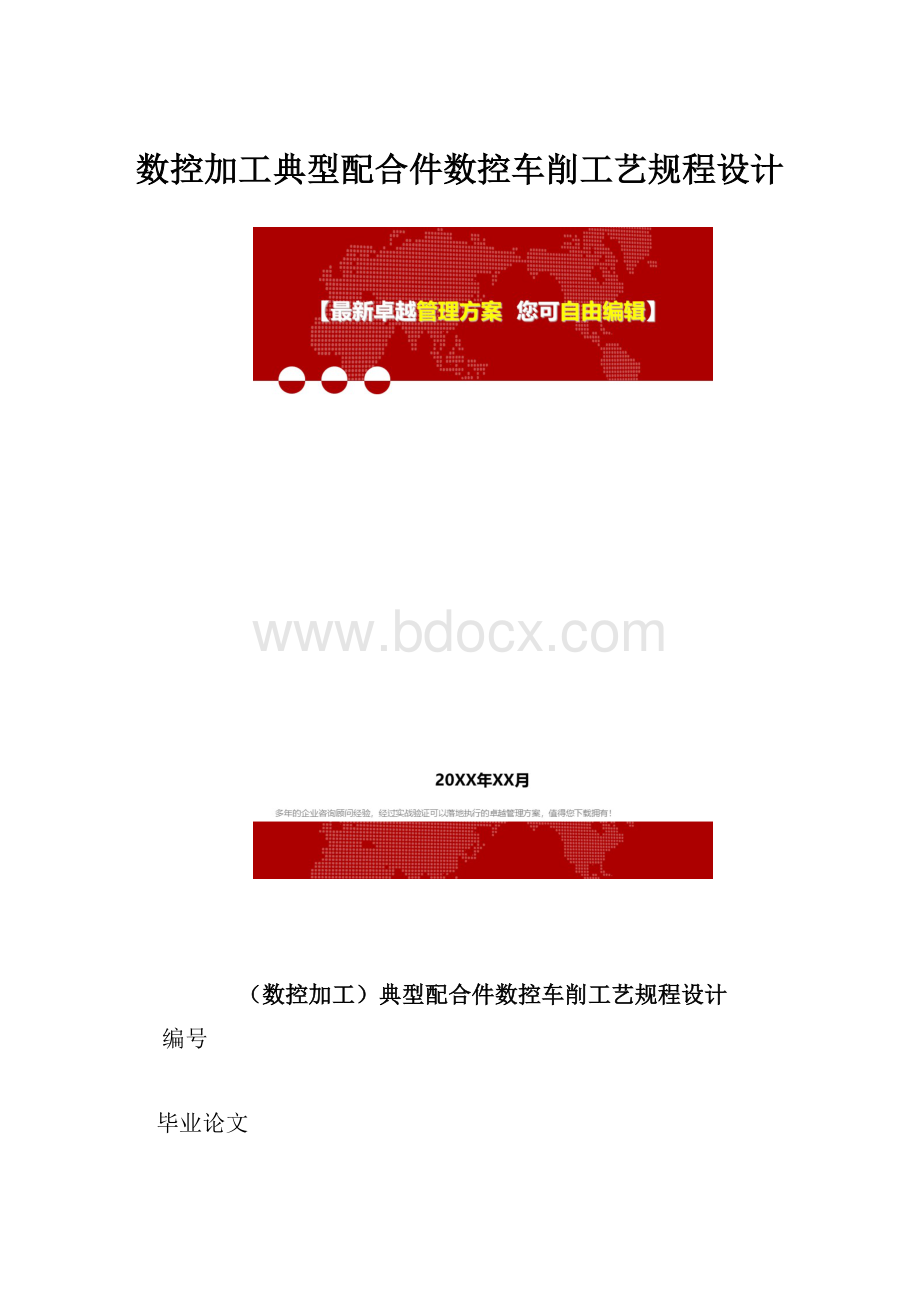
数控加工典型配合件数控车削工艺规程设计
(数控加工)典型配合件数控车削工艺规程设计
编号
毕业论文
题目
典型配合件数控车削工艺规程设计
学生姓名
学号
系部
专业
班级
指导教师
顾问教师
摘要
本文根据该零件的图纸及技术要求,首先对该零件进行了详细的工艺分析,确定毛坯种类。
重点介绍了该零件的工艺选择,其主要内容有,定位基准的确定、零件主要加工表面的加工方法的确定、安排零件主要加工表面的加工顺序等;接着设计合理的加工工序,包括零件加工余量的确定、选择机床、夹具的选择、确定切削用量等内容;然后在编制数控加工工艺卡,由于该零件的主要加工表面比较简单,本文没有详细的编制数控刀具卡;最后确定了零件的加工程序。
关键词工艺分析工艺路线加工工序程序编制
摘要I
第1章绪论1
第2章零件图分析及工艺分析2
2.1零件图及工艺分析2
2.1.1零件图的正确性及完整性分析3
2.1.2零件精度及技术要求分析3
2.2数控设备选择3
2.3零件定位基准及装夹方式的确定4
2.3.1正确选择定位粗基准及精基准4
2.3.2确定合理的装夹方式5
2.4选择刀具及对刀5
2.4.1正确选择粗、精加工刀具5
2.4.2确定对刀方式及对刀点5
2.4.3合理确定换刀点6
2.5制定合理的加工方案6
2.6合理划分数控加工工序6
2.7合理确定工步顺序绘制走刀路线图7
2.8确定数控工序加工余量,工序及工序图8
2.8.1合理确定数控加工余量8
2.8.2确定工序及工序图8
第3章切削用量的合理选择13
3.1确定背吃刀量13
3.2确定进给量及进给速度13
3.3在角铁上装夹校正工件13
3.3.1件1工序1:
车右端外轮廓13
3.3.2件2工序1车左内外轮廓15
第4章编制数控加工程序18
4.1部分数控加工程序18
第5章总结21
致谢22
参考文献23
附录程序24
第1章绪论
数控加工技术水平的提高,不仅与数控机床的性能和功能紧密相关,而且数控加工工艺对数控程序也起着相当重要的作用。
在数控加工过程中,如果数控机床是硬件,数控工艺和数控程序则相当于软件,两者缺一不可。
数控加工的特点是:
工艺内容十分明确而且具体;工艺工作相当准确而且严密;工序相对集中。
数控加工的特点和数控机床本身的性能与功能使数控加工体现出其中一些优点:
生产率高;加工精度较高;加工质量稳定可靠;加工零件适应性强,灵活性好。
数控加工工艺规程是规定零部件或产品数控加工工艺过程和操作方法等的工艺文件。
生产规模的大小、工艺水平的高低以及解决各种工艺问题和操作方法和手段都是通过加工工艺规程来体现。
因此,数控加工工艺规程设计是一项重要而有严肃的工作。
它要求设计者必须具备的生产实践经验和广博的机械制造工艺基础理论知识。
在机械加工工艺过程中,应针对零件的结构特点和技术要求,采用不同的加工方法和装备,按照一定的顺序依次进行才能完成由毛坯到零件的转变过程。
因此,机械加工工艺过程是由一个或若干个顺序排列的工序组成的,而工序又由安装、工位、工步、走刀、进给组成。
在产品投产前,要根据工艺规程来组织原材料和毛坯的供应,进行机床的调整,工艺装备(夹具、刀具、量具)的设计、制造或外购,编制生产计划,调配劳动力以及生产成本核算等。
在一定的生产条件下,确保加工质量和最少的生产成本是制定工艺规程的基本原则。
机械加工工艺规程首先应能够保证加工后的工件达到图样上规定的技术要求;其次,该工艺规程应该是在现场生产条件下、在规定的生产批量下最经济的,应能取得最好的经济效益;最后,该工艺规程要使工人具有良好而安全的劳动条件。
第2章零件图分析及工艺分析
2.1零件图及工艺分析
图2-1零件组装图
图2-2件一
图2-3件二
2.1.1零件图的正确性及完整性分析
在制订零件的机械加工工艺规程之前,对零件进行工艺性分析,以及对产品零件图提出修改意见,是制订工艺规程的一项重要工作。
此次设计的是一个轴类组合零件,此件几何要素间的相互关系明确,条件充分;采用一个主视图和一个剖视图完整的表达零件,尺寸表达完整,符合国家制图标准。
有利于编制程序时的数据分析和计算;表面粗糙度的标注明确了各加工面的加工精度要求。
检查零件图的完整性和正确性,在了解零件形状和结构之后,应检查零件视图是否正确和完整,是否能足够表达的直观、清楚,绘制是否符合国家标准,尺寸、公差以及技术要求的标注是否齐全、合理等。
2.1.2零件精度及技术要求分析
对图纸资料进行分析包括零件技术要求分析和结构工艺性分析两个方面。
这是制订机械加工工艺的重要步骤,也是学生应当掌握的基本技能。
分析技术要求包括四个方面。
(1)加工表面的尺寸精度。
(2)主要加工表面的形状精度。
(3)主要加工表面的相互位置精度。
(4)零件的表面质量
该组合零件件一的尺寸精度主要有Ф40㎜、Ф60㎜,长度尺寸54±0.2㎜,位置精度以Ф40㎜中心为基准,件二的尺寸精度主要有Ф40㎜、Ф60mm,长度尺寸60±0.1㎜,位置精度以Ф40㎜中心为基准。
零件表面质量有Ra3.2要求。
2.2数控设备选择
选择数控机床时,一般应考虑以下几个方面的问题:
(1)数控机床主要规格的尺寸应与工件的轮廓尺寸相适应。
即小的工件应当选择小规格的机床加工,而大的工件则选择大规格的机床加工,做到设备的合理使用。
(2)机床的工作精度与工序要求的加工精度相适应。
根据零件的加工精度要求选择机床,如精度要求低的粗加工工序,应选择精度低的机床,精度要求高的精加工工序,应选用精度高的机床。
(3)装夹方便、夹具结构简单也是选择数控设备是需要考虑的一个因素。
选择采用卧式数控机床,还是选择立式数控机床,将直接影响所选择的夹具的结构和加工坐标系,直接关系到数控编程的难易程度和数控加工的可靠性。
应当注意的是,在选择数控机床时应充分利用数控设备的功能,根据需要进行合理的开发,以扩大数控机床的功能,满足产品的需要。
然后,根据所选择的数控机床,进一步优化数控加工方案和工艺路线,根据需要适当调整工序的内容。
选择加工机床,首先要保证加工零件的技术要求,能够加工出合格的零件。
其次是要有利于提高生产效率,降低生产成本。
选择加工机床一般要考虑到机床的结构、载重、功率、行程和精度。
还应依据加工零件的材料状态、技术状态要求和工艺复杂程度,选用适宜、经济的数控机床,综合考虑以下因素的影响。
1)机床的类别(车、铣、加工中心等)、规格(行程范围)、性能(加工材料)。
2)数控机床的主轴功率、扭矩、转速范围,刀具以及刀具系统的配置情况。
3)数控机床的定位精度和重复定位精度。
4)零件的定位基准和装夹方式。
5)机床坐标系和坐标轴的联动情况。
6)控制系统的刀具参数设置,包括机床的对刀、刀具补偿以及ATC等相关的功能。
根据以上资料采用CKA6140数控机床,即可满足对工件加工精度的要求,另外再配备一些专用量具以提高工件的加工质量。
2.3零件定位基准及装夹方式的确定
2.3.1正确选择定位粗基准及精基准
在指定工艺规程时,定位基准选择的正确与否,对能保证零件的尺寸精度和相互位置精度要求,以及对零件各表面间的加工顺序安排都有较大的影响,当用夹具安装时,定位基准的选择还会影响到夹具结构的复杂程度,因此,定位基准的选择是一个很重要的工艺问题。
选择定位基准时,是从保证工件加工精度要求出发的,因此定位基准的选择应先选择精基准,再选择粗基准。
(1)精基准的选择原则
选择精基准时,主要考虑保证加工精度和工件安装方便可靠,其选择原则如下:
1)基准重合原则;
2)准统一原则;
3)自为基准原则;
4)互为基准原则;
5)所选精基准应保证工件安装可靠,夹具设计简单、操作方便。
结合工厂的现有设备、零件的加工要求及毛坯的质量,应以设计基准作为定位基准,这样设计基准与定位基准重合满足基准重合原则;选择以Ф40mm基准满足基准统一原则。
对工件的轮廓及整体形状精度的保证非常有利。
(2)粗基准的选择
选择粗基准时,主要要求保证各加工面有足够的余量,并注意应尽快获得精基面。
1)如果主要要求保证工件上某重要表面的加工余量均匀,则应选该表面作为粗基准。
2)若主要要求保证加工面与不加工面之间的位置要求,则应选不加工面为粗基准。
3)作为粗基准的表面,应尽量平整光洁,有一定面积,以使工件定位可靠,夹紧方便。
4)粗基准在同一尺寸方向上只能使用一次。
该组合零件以毛坯的外圆为粗基准。
2.3.2确定合理的装夹方式
数控机床常用装夹方式有
(1)在三爪自定心卡盘上装夹;
(2)在两顶尖之间装夹;(3)用卡盘和顶尖装夹;(4)用双三爪自定心卡盘上装夹
该组合零件是单件生产,并且是轴类零件,故采用三爪卡盘夹紧工件。
2.4选择刀具及对刀
2.4.1正确选择粗、精加工刀具
刀片的选择从材料、尺寸、形状、刀尖半径等方面来选取。
根据零件的结构、材料、余量及表面粗糙度选粗、精加工刀具
1)90°内外偏刀、2)5mm内外切断刀、3)60°内外螺纹刀。
2.4.2确定对刀方式及对刀点
1)对刀方式
对刀是数控加工中的主要操作和重要技能。
对刀的准确性决定了零件的加工精度,同时,对刀效率还直接影响数控加工效率。
深入理解数控车床的对刀原理对于操作者保持清晰的对刀思路、熟练掌握对刀操作以及提出新的对刀方法都具有指导意义。
对刀的实质是确定随编程而变化的工件坐标系的程序原点在唯一的机床坐标系中的位置。
数控车削的对刀方式有几种,我采用试切对刀的方法对刀。
2)对刀点
对刀点可以设在被加工工件上,也可设在夹具或机床上,选择对刀点的原则:
对刀点的位置容易确定;能够方便换刀,以便与换刀点重合;对刀点应与工件坐标系原点重合。
该组合零件件一加工时对刀点选在在距工件X68、Z3点,件二加工内轮廓选距工件在X23、Z3,加工外轮廓选在距工件X68、Z3点,这样可实现零件的快速加工。
2.4.3合理确定换刀点
换刀点是数控程序中指定换刀的位置点。
在数控车床上加工零件时,需要经常换刀,在编程时就要设换刀点。
换刀点位置应避免与工件、夹具和机床干涉。
普通数控车床换刀点由编程人员确定,通常将其与对刀点重合,车削中心与加工中心换刀点一般为固定点。
不能将换刀点与对刀点混为一谈。
该零件换刀点设定在X100、Z100位置上,避免与工件发生碰撞,而且利于换刀快速进刀。
同时如果将换刀点设置在远离毛坯的位置,当换第二把刀后,进行精车时的空行程路线必然较长,如果近离工件且不发生任何干扰,将缩短走刀行程,利于快速加工零件,所以我选择X100、Z100换刀位置。
2.5制定合理的加工方案
拟订工艺路线是制定工艺规程的关键步骤,其主要内容包括选择各表面的加工方法、安排工序的先后顺序,确定工序集中与分散程度等。
为保证达到零件的几何形状、尺寸精度、位置精度及各项技术要求,必须制定合理的工艺路线。
零件加工过程中,为满足零件的几何尺寸、形位精度以及其它各项技术要求,首先必须制订出经济、合理的工艺路线。
由于零件生产类型为单件生产,并采用了工序集中的工艺加工倾向安排,即采用通用数控机床配以通用的工装夹具,来保证零件的加工质量,同时也可以提高劳动生产率,尽量降低生产成本。
2.6合理划分数控加工工序
数控加工工序的划分一般可按下列方法进行:
1)以一次安装所进行的加工作为一道工序;
2)以一个完整数控程序连续加工的内容为一道工序;
3)以工件上的结构内容组合用一把刀具加工为一道工序;
4)以粗、精加工划分工序。
综上面分析,拟订以下两种加工方案:
第一种方案:
件1工序1车右端外轮廓
工序2车左端外轮廓
件2工序1车左内轮廓,车左外轮廓
工序2车右内轮廓,车右外轮廓
第二种方案:
件1工序1车左端外轮廓
工序2车右端外轮廓
件2工序1车左外轮廓,车左内轮廓
工序2车右外轮廓,车右内轮廓
加工方案分析:
对于外轮廓的加工工艺方案
(一)与工艺方案
(二)的区别在于:
件1先车左端外轮廓还是右端,方案
(二)能够保证局部外形的尺寸和表面光洁度的一致,但不能保证整体精度,且容易使工件变形,影响外观,加工时宜采用方案
(一)。
件2先车内轮廓还是外轮廓,方案
(一)先车内轮廓可使零件保证足够的强度,方案
(二)很可能使工件作废,所以宜采用方案
(一)。
综上我在加工零件时选用方案
(一)
2.7合理确定工步顺序绘制走刀路线图
数控车工步的安排原则:
先粗后精、先近后远、内外交叉、保证工件加工刚度的要求、同一把刀能加工内容连续加工原则。
件1工序1:
车右端外轮廓
1)粗车右端外轮廓,留0.5mm精车余量
2)精车右端外轮廓,保证其加工精度及表面粗糙度
3)切槽(宽5mm),保证其加工精度
4)车M30X2螺纹保证其加工精度
件1工序2:
车左端外轮廓
1)粗车左外轮廓,留0.5mm精车余量
2)精车左外轮廓保证其加工精度及表面粗糙度
3)切梯形槽保证其加工精度及表面粗糙度
件2工序1:
车左内外轮廓
1)钻孔直径为25mm
2)粗车左内轮廓,留0.5mm精车余量
3)精车左内轮廓保证其加工精度及表面粗糙度
4)切内槽保证其加工精度及表面粗糙度
5)车M30X2内螺纹保证其加工精度
6)粗车左外轮廓,留0.5mm精车余量
7)精车左外轮廓保证其加工精度及表面粗糙度
件2工序2:
车右内外轮廓
1)粗车右内轮廓,留0.5mm精车余量
2)精车右内轮廓保证其加工精度及表面粗糙度
3)车M30X2内螺纹保证其加工精度
4)粗车右外轮廓,留0.5mm精车余量
5)精车右外轮廓,保证其加工精度及表面粗糙度
走到路线见走刀路线图
2.8确定数控工序加工余量,工序及工序图
2.8.1合理确定数控加工余量
加工余量是指加工过程中,所切去的金属层厚度。
分工序加工余量(相邻两工序的工序尺寸之差)和加工总余量(毛坯尺寸与零件图设计尺寸之差),加工总余量等于各工序加工余量之和。
影响加工余量的因素:
①上工序表面粗糙度和缺陷层;②上工序的尺寸公差;③上工序的形位误差;④本工序的装夹误差。
确定加工余量的方法:
①经验估算法:
凭借工艺人员的实践经验估计加工余量,所估余量一般偏大,仅用于单件小批生产。
②查表修正法:
先从加工余量手册中查得所需数据,然后再结合工厂得实际情况进行适当修正。
此方法目前应用最广。
③分析计算法:
根据加工余量的计算公式和一定的试验资料,对影响加工余量的各项因素进行综合分析和计算来确定加工余量的一种方法。
适用于贵重材料和军工生产余量的方法。
确定加工余量时应该注意的几个问题:
①采用最小加工余量原则在保证加工精度和加工质量的前提下,余量越小越好,以缩短加工时间、减少材料消耗、降低加工费用;
②要充分防止因余量不足而造成废品;
③余量中应包含因热处理引起的变形;
④大零件取大余量,零件愈大,切削力、内应力引起的变形愈大,因此工序加工余量应取大一些,消除点变形量;
⑤总加工余量(毛坯余量)和工序余量要分别确定总加工余量的大小与所选择的毛坯制造精度有关。
粗加工工序的加工余量不能用查表法确定,应等于总加工余量减去其他各工序的余量之和。
2.8.2确定工序及工序图
工序是指一个人或一组人在一个工作地点或一台机床上,对同一个或几个零件进行加工所连续完成的那部分工艺过程。
工序以上已划分工序图见工序卡。
淮安信息职业技术学院
数控加工工序卡
产品名称或代号
零件名称
零件图号
典型配合件
典型配合件1
LYWH-1
车间
使用设备
数控加工车间
CKA6140
工艺序号
程序编号
1
O0001
夹具名称
夹具编号
三爪卡盘
1
工步号
工步作业内容
加工面
刀具号
刀补量
主轴转速
进给速度
背吃刀量
备注
1
粗车右端外轮廓,留0.5mm精车余量
外表面
T01
600r/min
120mm/min
1mm
2
精车右端外轮廓,保证其加工精度及表面粗糙度
外表面
T01
800r/min
80mm/min
0.25mm
3
切槽(宽5mm),保证其加工精度
外表面
T02
300r/min
30mm/min
5mm
4
车M30X2螺纹保证其加工精度
外表面
T03
500r/min
2mm/r
1.3mm
编制
华银龙
审核
批准
2010年9月1日
共4页
第1页
淮安信息职业技术学院
数控加工工序卡
产品名称或代号
零件名称
零件图号
典型配合件
典型组合件1
LYWH-1
车间
使用设备
数控加工车间
CKA6140
工艺序号
程序编号
2
O0002
夹具名称
夹具编号
三爪卡盘
1
工步号
工步作业内容
加工面
刀具号
刀补量
主轴转速
进给速度
背吃刀量
备注
1
粗车左外轮廓,留0.5mm精车余量
外表面
T01
600r/min
120mm/min
1mm
2
精车左外轮廓保证其加工精度及表面粗糙度
外表面
T01
800r/min
80mm/min
0.25mm
3
切梯形槽保证其加工精度及表面粗糙度
外表面
T02
300r/min
30mm/min
5mm
编制
华银龙
审核
批准
2010年9月1日
共4页
第2页
淮安信息职业技术学院
数控加工工序卡
产品名称或代号
零件名称
零件图号
典型配合件
典型组合件2
LYWH-2
车间
使用设备
数控加工车间
CKA6140
工艺序号
程序编号
1
O0003
夹具名称
夹具编号
三爪卡盘
1
工步号
工步作业内容
加工面
刀具号
刀补量
主轴转速
进给速度
背吃刀量
备注
1
钻孔直径为25mm
内孔
Z-1
450r/min
12.5mm
手动
2
粗车左内轮廓,留0.5mm精车余量
内表面
T04
600r/min
120mm/min
1mm
3
精车左内轮廓保证其加工精度及表面粗糙度
内表面
T04
800r/min
80mm/min
0.25mm
4
切内槽保证其加工精度及表面粗糙度
内表面
T05
300r/min
30mm/min
5mm
5
车M30X2内螺纹保证其加工精度
内表面
T06
500r/min
2mm/r
1.3mm
6
粗车左外轮廓,留0.5mm精车余量
外表面
T01
600r/min
120mm/min
1mm
7
精车左外轮廓保证其加工精度及表面粗糙度
外表面
T01
800r/min
80mm/min
0.25mm
编制
华银龙
审核
批准
2010年9月1日
共4页
第3页
淮安信息职业技术学院
数控加工工序卡
产品名称或代号
零件名称
零件图号
典型配合件
典型配合件2
LYWH-2
工序简图
车间
使用设备
数控加工车间
CKA6140
工艺序号
程序编号
2
O0004
夹具名称
夹具编号
三爪卡盘
1
工步号
工步作业内容
加工面
刀具号
刀补量
主轴转速
进给速度
背吃刀量
备注
1
粗车右内轮廓,留0.5mm精车余量
内表面
T04
600r/min
120mm/min
1mm
2
精车右内轮廓保证其加工精度及表面粗糙度
内表面
T04
800r/min
80mm/min
0.25mm
3
车M30X2内螺纹保证其加工精度
内表面
T06
500r/min
2mm/r
1.3mm
4
粗车右外轮廓,留0.5mm精车余量
外表面
T01
600r/min
120mm/min
1mm
5
精车右外轮廓,保证其加工精度及表面粗糙度
外表面
T01
800r/min
80mm/min
0.25mm
编制
华银龙
审核
批准
2010年9月1日
共4页
第4页
第3章切削用量的合理选择
切削用量是用来表示切削运动、调整机床加工参数的掺量,可用它对主运动和进给运动进行定量表述。
切削用量包括切削速度、进给量和背吃刀量三要素。
切削用量应根据加工性质、加工要求、工件材料及刀具的材料和尺寸等查阅切削用量手册并结合实践经验确定。
3.1确定背吃刀量
背吃刀量是根据余量确定的。
在工艺系统刚性和机床功率允许的情况下,尽可能选取较大的背吃刀量,以减少进给次数。
粗加工时,选取的背吃刀量要大一些,精加工时,背吃刀量要小一些。
3.2确定进给量及进给速度
在加工过程中,有四种进给速度设定,它们是:
快速走刀速度、进刀速度、切削进给速度及退刀速度。
(1)快速走刀速度(空刀进给速度)
为了节省非切削加工时间,降低生产成本,快速走刀速度应尽可能选高一些,一般选为机床所允许的最大进给速度,即G00进给速度。
在零件加工过程中,建立刀补即G00进给速度。
(2)退刀速度
为了缩短非切削加工时间,降低生产成本,退刀进给速度应选择机床所允许的最大快速移动速度,即G00速度。
在零件加工过程中,取消刀补即G00退刀速度。
3.3在角铁上装夹校正工件
对零件进行加工时,针对零件加工要求和零件上各部分尺寸的大小及工厂现有设备和加工条件等条件的限制。
应尽可能的选择较大直径的刀具,在机床的正常工作范围内制订出较大进给量和切削速度。
以提高工件的加工生产率。
主轴转速应根据允许的切削速度来确定,计算公式:
n=1000v/πD,式中:
v----切削速度,单位为m/min,由刀具的耐用度决定;
n----主轴转速,单位为r/min;
D----刀具直径,单位为mm;
计算的主轴转速n要根据机床说明书选取标准值。
3.3.1件1工序1:
车右端外轮廓
工步1粗车左端外轮廓,留0.5mm精车余量
由文献[1]P137表4-3查得背吃刀量ap=3mm取ap=1mm
由文献[1]P137表4-3查得切削速度=130m/min,计算主轴转速
取600r/min
由文献[1]P137表4-3查得进给量f=0.2㎜/r;计算进给速度F=Sf=120㎜/min.
工步2精车左端外轮廓,保证其加工精度及表面粗糙度
由文献[1]P137表4-3查得背吃刀量ap=0.3mm取ap=0.25mm
由文献[1]P137表4-3查得切削速度=100m/min,计算主轴转速
s==m/min=796r/min取800r/min
由文献[1]P137表4-3查得进给量f=0.1㎜/r;计算进给速度F=Sf=80㎜/min.
工步3切槽(宽5mm),保证其加工精度
根据所选刀具取背吃刀量ap=5mm
由文献[3]查得切削速度=30m/min,计算