FMEA管理程序.docx
《FMEA管理程序.docx》由会员分享,可在线阅读,更多相关《FMEA管理程序.docx(15页珍藏版)》请在冰豆网上搜索。
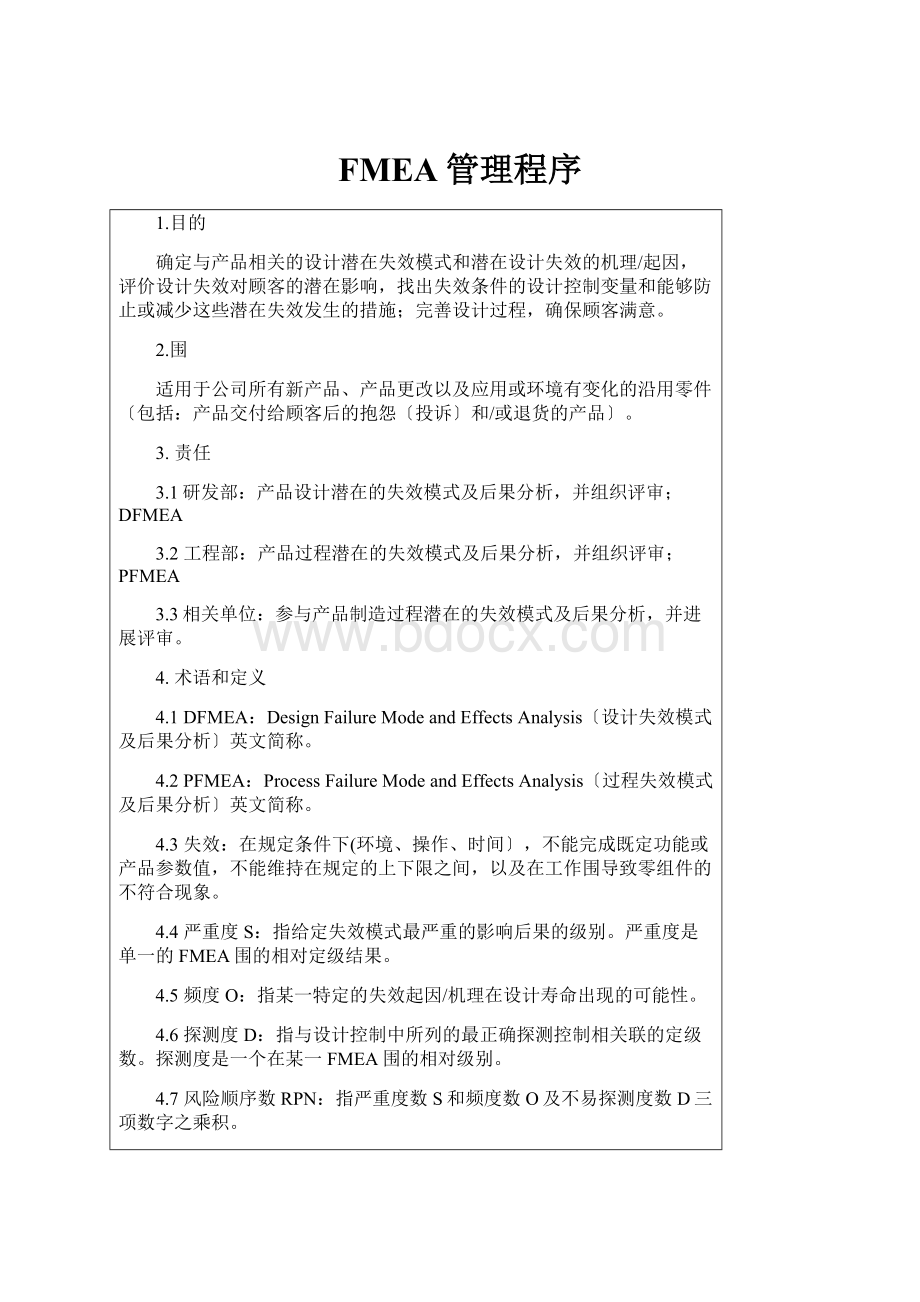
FMEA管理程序
1.目的
确定与产品相关的设计潜在失效模式和潜在设计失效的机理/起因,评价设计失效对顾客的潜在影响,找出失效条件的设计控制变量和能够防止或减少这些潜在失效发生的措施;完善设计过程,确保顾客满意。
2.围
适用于公司所有新产品、产品更改以及应用或环境有变化的沿用零件〔包括:
产品交付给顾客后的抱怨〔投诉〕和/或退货的产品〕。
3.责任
3.1研发部:
产品设计潜在的失效模式及后果分析,并组织评审;DFMEA
3.2工程部:
产品过程潜在的失效模式及后果分析,并组织评审;PFMEA
3.3相关单位:
参与产品制造过程潜在的失效模式及后果分析,并进展评审。
4.术语和定义
4.1DFMEA:
DesignFailureModeandEffectsAnalysis〔设计失效模式及后果分析〕英文简称。
4.2PFMEA:
ProcessFailureModeandEffectsAnalysis〔过程失效模式及后果分析〕英文简称。
4.3失效:
在规定条件下(环境、操作、时间〕,不能完成既定功能或产品参数值,不能维持在规定的上下限之间,以及在工作围导致零组件的不符合现象。
4.4严重度S:
指给定失效模式最严重的影响后果的级别。
严重度是单一的FMEA围的相对定级结果。
4.5频度O:
指某一特定的失效起因/机理在设计寿命出现的可能性。
4.6探测度D:
指与设计控制中所列的最正确探测控制相关联的定级数。
探测度是一个在某一FMEA围的相对级别。
4.7风险顺序数RPN:
指严重度数S和频度数O及不易探测度数D三项数字之乘积。
4.8顾客:
不仅仅是"最终使用者〞,并且包括负责整车设计或更高一层总成设计的工程师们/设计组,以及在负责装配和售后效劳活动的生产/工艺工程师们,也可以是下游制造、装配工序,维修工序或政府法规。
5.实施流程
5.1FMEA筹划
5.1.1DFMEA:
应在一个设计概念最终形成之时或之前开场,而且在产品开发的各阶段中,当发生更改或获得更多的信息时,应及时、持续、不断地修改和更新,并最终在产品加工图样完成之前全部完成。
5.1.2根本的操作方法讨论完成时,生产方案制定和生产批准之前,要使用PFMEA分析;
5.1.3现有的产品出现质量故障时,要使用DFMEA或PFMEA去分析。
5.2组建FMEA小组
各单位组建DFMEA/PFMEA小组,根据需要,小组成员可包括工程、制造、采购、品保、业务、供应商和顾客方面的代表;
5.3收集FMEA所需的信息。
5.3.1DFMEA小组需收集以下信息:
a.所设计产品的构造清单;
b.所设计产品应有的功能,及不应有的功能;
c.与成熟产品相近的产品质量情况等信息。
5.3.2PFMEA小组要收集以下信息:
a.零部件生产过程流程图;
b.过程有关的产品质量特性;
c.制造和装配的要求;
d.与成熟产品相近的产品过程质量情况等信息。
5.4失效模式确认
5.4.1PFMEA小组分析产品的故障模式;DFMEA小组分析产品的功能失效模式。
5.4.2可以使用鱼骨图,从人、机、料、法、环五方面分析失效模式的每一个起因/机理;DFMEA着重从设计方面分析。
5.4.3.对于一个特定工程,列出每一个潜在的失效模式,前提是这种失效可能发生,但不是一定发生。
5.5失效模式的后果
分析失效模式可能产生的后果,给顾客带来的影响。
5.6严重度评定
分析潜在失效的后果,设计阶段的严重度评价依据一"设计FMEA严重度评价准那么",制造过程阶段依据四"过程FMEA严重度评价准那么",进展评定。
5.7失效的潜在起因/机理
失效的潜在起因的结果就是失效模式。
尽可能地列出每一个失效模式的所有可以想到的失效起因和/或失效机理。
起因/机理应尽可能简明而全面地列出,以便有针对性地采取补救的努力和/或适当的纠正措施。
5.8频度评价
对失效模式的起因或机理,根据频度O评价准那么〔分别对应二、五〕进展频度评价,描述频度级别数着重在描述可能性的级别数之相对意义,而不是绝对具体的数值,频度数的取值与失效率围有关,但并不反映实际出现的可能性。
5.9现行控制
列出已经完成或承诺要完成的预防措施、设计/过程确认/验证或其它活动,并且这些活动将确保设计/过程对于所考虑的失效模式或起因/机理是足够的。
5.10探测度评价
选择现行的设计控制方法,根据探测度D评价准那么〔对应三、六〕进展探测度评价,小组成员应对相互一致的评定准那么和定级方法达成一致意见,尽管对个别产品分析可作调整。
在设计开发过程中,最好是尽早采用探测控制。
5.11确定风险顺序数
根据严重度、频度、探测度的评定,计算出风险顺序数RPN=严重度S×频度O×探测度D,在一般情况下,不管RPN值的大小如何,当严重度S高时就应予以特别注意。
a.当RPN≥100〔或按顾客规定要求〕时,应采取建议措施并努力减小该数值。
b.当严重度数S≥8〔或按顾客规定要求〕时,应采取建议措施。
对于严重度S≥8,风险顺序数RPN≥100的工程要制定改进措施,当RPN相近时,应优先注意严重度S高的失效模式,以及严重度S和频度O都较高的失效模式。
5.12建议措施
当失效模式按RPN值排出次序后,应首先针对高严重度S、高RPN值和小组指定的其它工程进展预防/纠正措施的工程评价。
任何建议措施的意图都是要按以下顺序降低其风险级别:
严重度S、频度O、探测度D。
5.12.1一般情况下,不管其RPN值是多大,当严重度S是9或10时,必须予以特别注意,以确保现行的设计控制或预防/纠正措施针对了这种风险。
在所有的已确定潜在失效模式的后果可能会给最终用户造成危害的情况下,都应考虑预防/纠正措施,以便通过消除、减弱或控制起因来防止失效模式的产生。
5.12.2在对严重度值为9或10的工程给予特别关注之后,FMEA小组再考虑其它的失效模式,其意图在于降低严重度S,其次频度O,再次探测度D。
5.12.3建议措施的主要目的是通过改进设计/过程,降低风险,提高顾客满意度。
5.12.4只有设计更改才能导致严重度S的降低。
5.13建议措施的责任和实施
填入建议措施的责任组织的名称和个人的以及目标完成的日期,并在措施实施之后,填入实际措施的简要说明以及生效日期。
5.14措施评价
当确定了预防/纠正措施以后,估算并记录纠正后的严重度、频度和探测度值的结果。
计算并记录纠正后的RPN值的结果。
如果没有采取任何措施,将"纠正后的RPN〞档和对应的取值栏目空白即可。
所有纠正后的定级数值都应进展复查和评审,而且如果有必要采取进一步措施的话,应重复以上的步骤。
5.15工程小组应负责保证所有的建议措施已被实施或已妥善落实。
FMEA是一个动态文件,它不仅应表达最新的设计水平,而且还应表达最新采取的有关措施,包括开场生产后发生的设计更改和措施。
6.相关文件
6.1"FMEA手册"
6.2"文件控制程序"
6.3"质量记录管理程序"
6.4"APQP管理程序"
7.相关记录
7.1产品设计的潜在失效模式及后果分析表(DFMEA)
7.2过程设计的潜在失效模式及后果分析表(PFMEA)
7.3DFMEA检查清单
7.4PFMEA检查清单
8.相关
一"设计FMEA严重度评价准那么"
二"设计FMEA频度评价准那么"
三"设计FMEA探测度评价准那么"
四"过程FMEA严重度评价准那么"
五"过程FMEA频度评价准那么"
六"过程FMEA探测度评价准那么"
一"设计FMEA严重度评价准那么"
后果
判定准那么:
产品后果的严重度〔顾客后果〕
级别
未能符合平安和/或法规要求
潜在失效后果影响车辆平安行驶和/或涉及不符合政府法规,失效发生时无预警
10
潜在失效后果影响车辆平安行驶和/或涉及不符合政府法规,失效发生时有预警
9
根本功能的损失或降级
根本功能损失〔车辆不能运转,但不影响平安操作〕
8
根本功能降级〔车辆可运转,但功能等级降低〕
7
次要功能的损失或降低
次要功能损失〔车辆可行驶,但舒适性/便利性功能丧失〕
6
次要功能减弱〔车辆可行驶,但舒适性/便利性性能等级降低〕
5
其他功能不良
外观或噪音不符合要求,汽车可行驶,大多数顾客〔>75%〕抱怨不舒适
4
外观或噪音不符合要求,汽车可行驶,很多顾客〔50%〕抱怨不舒适
3
外观或噪音不符合要求,汽车可行驶,被有识别能力的顾客〔<25%〕抱怨不舒适
2
没有影响
没有可区分的影响
1
二"设计FMEA频度评价准那么"
失效可能性
评价准那么:
针对DFMEA要因发生率〔设计寿命/工程可靠性车辆〕
评价准那么:
针对DFMEA要因的发生率〔事件/工程/车辆〕*
等级
非常高
没有历史的新技术/新设计
≥100次每1000个中
≥1次每10辆
10
高
新设计\新应用或使用寿命/操作条件的改变情况下防止的失效
50次每1000个
1次2每20辆中
9
新设计\新应用或使用寿命/操作条件的改变情况下很可能发生的失效
20次每1000个
1次2每50辆中
8
新设计\新应用或使用寿命/操作条件的改变情况下不确定是否会发生失效
10次每1000个
1次2每100辆中
7
一般
与类似设计相关或在设计模拟和测试中频繁失效
2次每1000个
1次2每500辆中
6
与类似设计相关或在设计模拟和测试中偶然发生的失效
0.5次每1000个
1次2每2000辆中
5
与类似设计相关或在设计模拟和测试中较少发生的失效。
isolated
0.1次每1000个
1次2每10,000辆中
4
低
仅仅在与几乎一样的设计关联或在设计模拟和测试发生的失效
0.01次每1000个
1次2每100,000辆中
3
在与几乎一样的设计关联或在设计模拟和试验时不能观察的失效
≤0.001次每1000个
1次2每1,000,000辆中
2
非常低
失效通过预防控制来消除
失效通过预防控制消除
1
三"设计FMEA探测度评价准那么"
探测时机
评价准那么:
被设计控制发现的可能性
等级
探测可能性
没有探测时机
没有现有设计控制;不能探测或不能分析
10
几乎不可能
在任何阶段不可能探测
设计分析/探测有微弱的探测能力;实际的分析〔如CAE、FEA、etc〕与期望的实际操作条件不相关
9
非常细微
快速冻结设计,预先投放
在设计冻结以及在试验〔具有如乘坐、操作、出货评价等承受准那么下的子系统或系统试验〕通过/失败的情况预先投放后的产品验证/确认
8
细微
在设计冻结和在失效测试试验〔直到失效发生、系统相互作业试验为止的子系统或系统试验〕在情况下的预先投放后的产品验证/确认
7
非常低
在设计冻结以及在降级试验情况下预先投放后的产品验证/确认〔在耐力试验后的子系统或系统试验,如功能检查〕
6
低
预先冻结设计
使用通过/失效试验进展产品验证〔可靠性试验,开发或确认试验〕,预先冻结设计〔如:
性能、功能检查承受准那么等〕
5
一般
使用失效试验〔如:
直到泄漏、屈服、破裂等〕预先冻结设计的产品确认〔可靠性试验、开发或确认试验〕
4
有点高
使用降级试验〔如数据趋势、之前/之后值等〕预先冻结设计的产品确认〔可靠性试验、开发或确认试验〕
3
高
实质性分析—有相关
设计分析/探测控制有强探测能功。
在实际或期望运作条件下预先停顿设计与实质性分析〔如CAF、FEA等〕高相关
2
非常高
探测不需用到;失效预防
通过设计解决方案〔如已证实的设计标准、最好惯例或普通材料〕充分执行预防,失效要因或失效模式将不会发生
1
几乎一定
四"过程FMEA严重度评价准那么"
后果
评定准那么:
后果的严重度
当潜在失效模式导致最终顾客和/或一件制造/装配厂产生缺陷时便得出相应的定级结果。
最终顾客永远是要首先考虑的。
如果两种可能存在的,采用两件严重度值中的较高者〔顾客的后果〕
严重度级别
后果
评定准那么:
后果的严重度
当潜在失效模式导致最终顾客和/或一件制造/装配厂产生缺陷时便得出相应的定级结果。
最终顾客永远是要首先考虑。
如果两种可能都存在的,采用两件严重值中的较高者〔制造/装配后果〕
未能符合平安和/或法规要求
当潜在的失效模式在无警告的情况下影响用户人身平安运行和/或涉及不符合政府法规的情形时,严重度定级非常高
10
失效符合平安和/或法律要求
可能没有预警下危害操作者〔机械或装配〕
当潜在的失效模式在有警告的情况下影响用户人身平安运行和/或涉及不符合政府法规的情形时,严重度定级非常高
9
可能在有预警下危害操作〔机械或装配〕
根本功能的损失或降级
产品不能工作〔丧失根本功能〕
8
大规模中断
100%的产品是废品,流水线停顿或停顿出货
产品可运行但性能水平下降。
顾客非常不满意
7
显著中断
生产运转一定会产生局部废品,背离最初过程包括流水线速度降低或增加
舒适功能的损失或降级
产品可运行但舒适性/便利性工程性能水平有所下降。
6
一般
100%需脱线返工,是被成认的
产品可运行但舒适性/便利性工程性能水平有所下降
5
局部需脱线返工,是被成认的
令人不舒服的工程
配合和外观不舒服。
多数〔75%以上〕顾客能觉察缺陷
4
一般中断
在加工前100%须在位置上加工
配合和外观不舒服。
50%的顾客能觉察缺陷
3
在加工前局部须在位置上加工
配合和外观不舒服。
有辨识力顾客发烧友〔25%以下〕能觉察缺陷
2
微小中断
过程,操作或操作者的轻微不便利
没有影响
没有可区分的后果
1
没有后果
没有可区分的后果
五"过程FMEA频度评价准那么"
失效可能性
准那么:
PFMEA要因发生率
〔事件每工程/车辆〕
等级
很高:
持续性失效
≥100次每1000个
≥1次每10辆中
10
50次每1000个
1次每20辆中
9
高:
经常性失效
20次每1000个
1次每50辆中
8
10次每1000个
1次每100辆中
7
中等:
偶然性失效
2次每1000个
1次每500辆中
6
0.5次每1000个
1次每2000辆中
5
0.1次每1000个
1次每10,000辆中
4
低:
相对很少发生的失效
0.01每1000个
1次每100,000辆中
3
≤0.001每1000个中
1次每1000,000
2
极低:
失效不太可能发生
失效通过预防控制消除了
1
六"过程FMEA探测度评价准那么"
探测时机
评价准那么:
过程控制探测的可能性
级别
探测可能性
没有探测时机
没有现有控制;不能探测或不能解析
10
几乎不可能
在任何阶段不太可能探测
失效模式和/或错误〔要因〕不容易探测〔如:
随机检查〕
9
非常微小
加工后问题探测
操作者通过目测/排列/耳听法的/事后后失效模式探测
8
微小
开场时问题探测
操作者通过目测/排列/耳听法在位置上做失效模式探测或操作都通过使用插性测量〔行/不行、手动转矩检查等〕做加工后探测
7
非常低
加工后问题探测
操作者通过使用变量测量或操作者在位置上通过使用特性测量事后失效模式探测,〔行/不行、手动转矩检查等〕
6
低
开场时问题探测
操作者在位置上使用变量测量或通过位置上的自动控制探测差异零件和通知操作者〔光、杂音等〕。
在设置上或首件检验时执行测量〔仅对于设置要因〕
5
一般
加工后问题探测
由自动控制探测变异零件并锁住零件预防进一步加工的事后失效模式探测
4
一般高
开场时问题探测
由自动控制在位置上探测变异零件并在位置上自动锁住零件预防进一步加工的失效模式探测。
3
高
错误探测和/或问题预防
由自动控制在位置上探测错误并预防制造中的变异零件的错误〔要因〕探测
2
非常高
探测不能用;防错
以夹具设计、机械设计或零件设计所做的错误〔要因〕预防,因为过程/产品设计的防错工程,不会产生变异零件。
1
几乎确定