一种使玻璃表面层具有裂纹或剥离效果的方法分析.docx
《一种使玻璃表面层具有裂纹或剥离效果的方法分析.docx》由会员分享,可在线阅读,更多相关《一种使玻璃表面层具有裂纹或剥离效果的方法分析.docx(8页珍藏版)》请在冰豆网上搜索。
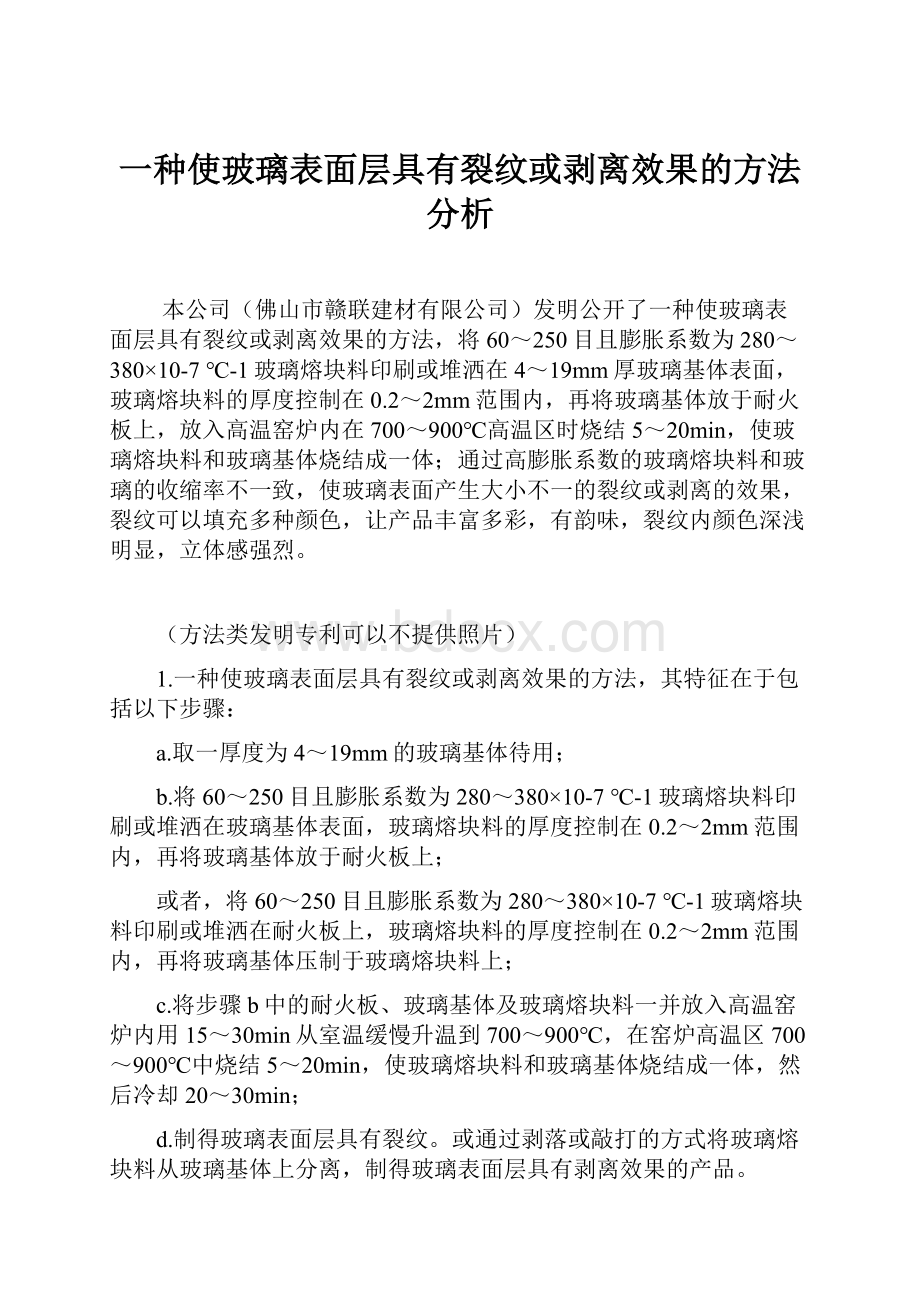
一种使玻璃表面层具有裂纹或剥离效果的方法分析
本公司(佛山市赣联建材有限公司)发明公开了一种使玻璃表面层具有裂纹或剥离效果的方法,将60~250目且膨胀系数为280~380×10-7℃-1玻璃熔块料印刷或堆洒在4~19mm厚玻璃基体表面,玻璃熔块料的厚度控制在0.2~2mm范围内,再将玻璃基体放于耐火板上,放入高温窑炉内在700~900℃高温区时烧结5~20min,使玻璃熔块料和玻璃基体烧结成一体;通过高膨胀系数的玻璃熔块料和玻璃的收缩率不一致,使玻璃表面产生大小不一的裂纹或剥离的效果,裂纹可以填充多种颜色,让产品丰富多彩,有韵味,裂纹内颜色深浅明显,立体感强烈。
(方法类发明专利可以不提供照片)
1.一种使玻璃表面层具有裂纹或剥离效果的方法,其特征在于包括以下步骤:
a.取一厚度为4~19mm的玻璃基体待用;
b.将60~250目且膨胀系数为280~380×10-7℃-1玻璃熔块料印刷或堆洒在玻璃基体表面,玻璃熔块料的厚度控制在0.2~2mm范围内,再将玻璃基体放于耐火板上;
或者,将60~250目且膨胀系数为280~380×10-7℃-1玻璃熔块料印刷或堆洒在耐火板上,玻璃熔块料的厚度控制在0.2~2mm范围内,再将玻璃基体压制于玻璃熔块料上;
c.将步骤b中的耐火板、玻璃基体及玻璃熔块料一并放入高温窑炉内用15~30min从室温缓慢升温到700~900℃,在窑炉高温区700~900℃中烧结5~20min,使玻璃熔块料和玻璃基体烧结成一体,然后冷却20~30min;
d.制得玻璃表面层具有裂纹。
或通过剥落或敲打的方式将玻璃熔块料从玻璃基体上分离,制得玻璃表面层具有剥离效果的产品。
2.根据权利要求1所述的一种使玻璃表面层具有裂纹或剥离效果的方法,其特征在于:
将325~1200目的颜料与工业酒精混合,化成浆后通过浸润或擦拭的方式填充到所述步骤d得到的玻璃表面的裂纹内,产生深浅明显的有色裂纹。
3.根据权利要求2所述的一种使玻璃表面层具有裂纹或剥离效果的方法,其特征在于:
所述的颜料和工业酒精之间的重量比例为3:
1。
4.根据权利要求1所述的一种使玻璃表面层具有裂纹或剥离效果的方法,其特征在于:
所述的玻璃熔块料是由35~70份的纳长石、5~70份的霞石、5~35份的硼砂和5~15份的纯碱进行混合后,在1250度温度下煅烧熔化后流入到冷水中形成的。
一种使玻璃表面层具有裂纹或剥离效果的方法
技术领域
本公司发明涉及玻璃装饰材料技术领域,具体涉及一种使玻璃表面层具有裂纹或剥离效果的方法。
背景技术
玻璃作为比较廉价的装饰建材,通常受到广泛的应用,但其表面的深加工技术近年来没什么创新。
以往的玻璃表裂纹处理技术只是将150℃的玻璃放入冷水内,通过热胀冷缩原理使玻璃通体产生裂纹,且裂缝内没有颜色。
用该技术生产的裂纹是通体有的,产品合格率不高,因为很多是通体裂缝,直接裂碎了一部分。
发明内容
本公司发明的目的是提供一种使玻璃表面层具有裂纹或剥离效果的方法,使产品不会直接裂碎,可以让玻璃表面因收缩过度而产生裂纹或剥离的效果,形成自然的装饰纹理状。
本公司发明解决其技术问题所采用的技术方案是:
一种使玻璃表面层具有裂纹或剥离效果的方法,其特征在于包括以下步骤:
a.取一厚度为4~19mm的玻璃基体待用;
b.将60~250目且膨胀系数为280~380×10-7℃-1玻璃熔块料印刷或堆洒在玻璃基体表面,玻璃熔块料的厚度控制在0.2~2mm范围内,再将玻璃基体放于耐火板上;
或者,将60~250目且膨胀系数为280~380×10-7℃-1玻璃熔块料印刷或堆洒在耐火板上,玻璃熔块料的厚度控制在0.2~2mm范围内,再将玻璃基体压制于玻璃熔块料上;
c.将步骤b中的耐火板、玻璃基体及玻璃熔块料一并放入高温辊道窑炉内。
用15~30min从室温缓慢升温到700~900℃,在辊道窑炉高温区700~900℃中烧结5~20min,使玻璃熔块料和玻璃基体烧结成一体,然后缓慢冷却20~30min;
d.通过剥落或敲打的方式将玻璃熔块料从玻璃基体上分离,制得玻璃表面层具有裂纹或剥离效果的产品。
作为优选的,将325~1200目的颜料与工业酒精混合,化成浆后通过浸润或擦拭的方式填充到所述步骤d得到的玻璃表面的裂纹内,产生深浅明显的有色裂纹。
进一步的,所述的颜料和工业酒精之间的重量比例为3:
1。
优选的,所述的玻璃熔块料是由35~70份的纳长石、5~70份的霞石、5~35份的硼砂和5~15份的纯碱进行混合后,在1250度温度下煅烧熔化后流入到冷水中形成的。
本公司发明的有益效果是:
通过高膨胀系数的玻璃熔块料和玻璃的收缩率不一致,使玻璃表面产生大小不一的裂纹或剥离的效果,烧结的温度只要700~900℃.裂纹可以填充多种颜色,让产品丰富多彩,有韵味,裂纹内颜色深浅明显,立体感强烈。
若玻璃熔块料的厚度增加,则可以让玻璃表面因收缩过度而产生玻璃表面剥离,形成自然的装饰纹理状,是用其它方法做不出该种自然的纹理。
具体实施方式
为了使本发明所解决的技术问题、技术方案及有益效果更加清楚明白,以下结合实施例,对本发明作进一步的说明。
应当理解,此处所描述的实施例仅仅用于解释本发明,并不用于限定本发明。
实施例1:
取一厚度为8mm的玻璃基体待用;将100~200目混合且膨胀系数为360×10-7℃-1玻璃熔块料印刷或堆洒在玻璃基体表面,玻璃熔块料的厚度控制在0.6mm,再将玻璃基体放于耐火板上;放入辊道窑炉内在850℃的高温区烧结13min,使玻璃熔块料和玻璃基体烧结成一体,缓慢冷却23min;制得玻璃表面层具有裂纹效果的产品。
将600目的颜料与工业酒精之间的以重量比例为3:
1混合,化成浆后通过浸润或擦拭的方式填充到玻璃表面的裂纹内,产生深浅明显的有色裂纹。
实施例2:
取一厚度为12mm的玻璃基体待用;将80~200目混合的且膨胀系数为340×10-7℃-1玻璃熔块料印刷或堆洒在耐火板上,玻璃熔块料的厚度控制在1.8mm范围内,再将玻璃基体压制于玻璃熔块料上;放入辊道窑炉内在880℃的高温区烧结17min,使玻璃熔块料和玻璃基体烧结成一体,缓慢冷却26min;再通过剥落或敲打的方式将玻璃熔块料从玻璃基体上分离,且会剥落玻璃基体表面1-3mm,制得局部厚度在9-11mm的玻璃且表面层具有剥离效果的产品。
再通过后期喷涂或电镀着色在被剥落的玻璃表面制得纹理饱满丰富的装饰品。
以上所述仅为本发明的较佳实施例,并不用以限制本发明,凡在本发明的精神和原则之内所作的任何修改、同等替换和改进等,均应落在本发明的保护范围之内。
本公司发明公开了一种使玻璃表面层具有裂纹或剥离效果的方法,将60~250目且膨胀系数为280~380×10-7℃-1玻璃熔块料印刷或堆洒在4~19mm厚玻璃基体表面,玻璃熔块料的厚度控制在0.2~2mm范围内,再将玻璃基体放于耐火板上,放入高温窑炉内在700~900℃温区时烧结5~20min,使玻璃熔块料和玻璃基体烧结成一体;通过高膨胀系数的玻璃熔块料和玻璃的收缩率不一致,使玻璃表面产生大小不一的裂纹或剥离的效果,裂纹可以填充多种颜色,让产品丰富多彩,有韵味,裂纹内颜色深浅明显,立体感强烈。
要不要拍照生产效果图片放进来?
蓝色的字为修改过的
膨胀系数为280~380×10-7℃-1玻璃熔块料的配方为纳长石35-70份,霞石5-70份,硼砂5-35份,纯碱5-15份,以上材料进行混合后在1250度煅烧熔化后流入到冷水中形成玻璃熔块。
要不要拍照生产效果图片放进来?
1.一种使玻璃表面层具有裂纹或剥离效果的方法,其特征在于包括以下步骤:
a.取一厚度为4~19mm的玻璃基体待用;
b.将60~250目且膨胀系数为280~380×10-7℃-1玻璃熔块料印刷或堆洒在玻璃基体表面,玻璃熔块料的厚度控制在0.2~2mm范围内,再将玻璃基体放于耐火板上;
或者,将60~250目且膨胀系数为280~380×10-7℃-1玻璃熔块料印刷或堆洒在耐火板上,玻璃熔块料的厚度控制在0.2~2mm范围内,再将玻璃基体压制于玻璃熔块料上;
c.将步骤b中的耐火板、玻璃基体及玻璃熔块料一并放入高温窑炉内用15~30min从室温缓慢升温到700~900℃,在窑炉高温区700~900℃中烧结5~20min,使玻璃熔块料和玻璃基体烧结成一体,然后冷却20~30min;
d.制得玻璃表面层具有裂纹。
或通过剥落或敲打的方式将玻璃熔块料从玻璃基体上分离,制得玻璃表面层具有剥离效果的产品。
4.根据权利要求1所述的一种使玻璃表面层具有裂纹或剥离效果的方法,其特征在于:
将325~1200目的颜料与工业酒精混合,化成浆后通过浸润或擦拭的方式填充到所述步骤d得到的玻璃表面的裂纹内,产生深浅明显的有色裂纹。
5.根据权利要求2所述的一种使玻璃表面层具有裂纹或剥离效果的方法,其特征在于:
所述的颜料和工业酒精之间的重量比例为3:
1。
一种使玻璃表面层具有裂纹或剥离效果的方法
技术领域
本公司发明涉及玻璃装饰材料技术领域,具体涉及一种使玻璃表面层具有裂纹或剥离效果的方法。
背景技术
玻璃作为比较廉价的装饰建材,通常受到广泛的应用,但其表面的深加工技术近年来没什么创新。
原本陶瓷的裂纹产生是经过多年自然风化和自然气候冷热交替使陶瓷的坯与釉收缩不一致逐渐形成细小的裂纹。
裂纹内只有陶瓷原坯的颜色,色彩单一,且陶瓷烧成需要1250℃以上的高温才能成品。
(有没必要说明此项陶瓷的裂纹情况?
?
?
)
而且,以往的玻璃表裂纹处理技术只是将150℃的玻璃放入冷水内,通过热胀冷缩原理使玻璃通体产生裂纹,且裂缝内没有颜色。
用该技术生产的裂纹是通体有的,产品合格率不高,因为很多是通体裂缝,直接裂碎了一部分。
发明内容
本公司发明的目的是提供一种使玻璃表面层具有裂纹或剥离效果的方法,使产品不会直接裂碎,可以让玻璃表面因收缩过度而产生裂纹或剥离的效果,形成自然的装饰纹理状。
本发明解决其技术问题所采用的技术方案是:
一种使玻璃表面层具有裂纹或剥离效果的方法,其特征在于包括以下步骤:
a.取一厚度为4~19mm的玻璃基体待用;
b.将60~250目且膨胀系数为280~380×10-7℃-1玻璃熔块料印刷或堆洒在玻璃基体表面,玻璃熔块料的厚度控制在0.2~2mm范围内,再将玻璃基体放于耐火板上;
或者,将60~250目且膨胀系数为280~380×10-7℃-1玻璃熔块料印刷或堆洒在耐火板上,玻璃熔块料的厚度控制在0.2~2mm范围内,再将玻璃基体压制于玻璃熔块料上;
c.将步骤b中的耐火板、玻璃基体及玻璃熔块料一并放入高温辊道窑炉内。
用15~30min从室温缓慢升温到700~900℃,在辊道窑炉高温区700~900℃中烧结5~20min,使玻璃熔块料和玻璃基体烧结成一体,然后缓慢冷却20~30min;
d.通过剥落或敲打的方式将玻璃熔块料从玻璃基体上分离,制得玻璃表面层具有裂纹或剥离效果的产品。
作为优选的,将325~1200目的颜料与工业酒精混合,化成浆后通过浸润或擦拭的方式填充到所述步骤d得到的玻璃表面的裂纹内,产生深浅明显的有色裂纹。
进一步的,所述的颜料和工业酒精之间的重量比例为3:
1。
本发明的有益效果是:
通过高膨胀系数的玻璃熔块料和玻璃的收缩率不一致,使玻璃表面产生大小不一的裂纹或剥离的效果,烧结的温度只要700~900℃,对能耗的使用比陶瓷的要少很多。
裂纹可以填充多种颜色,让产品丰富多彩,有韵味,裂纹内颜色深浅明显,立体感强烈。
若玻璃熔块料的厚度增加,则可以让玻璃表面因收缩过度而产生玻璃表面剥离,形成自然的装饰纹理状,是用其它方法做不出该种自然的纹理。
具体实施方式
为了使本发明所解决的技术问题、技术方案及有益效果更加清楚明白,以下结合实施例,对本发明作进一步的说明。
应当理解,此处所描述的实施例仅仅用于解释本发明,并不用于限定本发明。
实施例1:
取一厚度为8mm的玻璃基体待用;将100-200目混合且膨胀系数为360×10-7℃-1玻璃熔块料印刷或堆洒在玻璃基体表面,玻璃熔块料的厚度控制在0.6mm,再将玻璃基体放于耐火板上;放入辊道窑炉内在850℃的高温区烧结13min,使玻璃熔块料和玻璃基体烧结成一体,缓慢冷却23min;制得玻璃表面层具有裂纹效果的产品。
将600目的颜料与工业酒精之间的以重量比例为3:
1混合,化成浆后通过浸润或擦拭的方式填充到玻璃表面的裂纹内,产生深浅明显的有色裂纹。
实施例2:
取一厚度为12mm的玻璃基体待用;将80-200目混合的且膨胀系数为340×10-7℃-1玻璃熔块料印刷或堆洒在耐火板上,玻璃熔块料的厚度控制在1.8mm范围内,再将玻璃基体压制于玻璃熔块料上;放入辊道窑炉内在880℃的高温区烧结17min,使玻璃熔块料和玻璃基体烧结成一体,缓慢冷却26min;再通过剥落或敲打的方式将玻璃熔块料从玻璃基体上分离,且会剥落玻璃基体表面1-3mm,制得厚度在9-11mm的玻璃且表面层具有剥离效果的产品。
再通过后期喷涂或电镀着色在被剥落的玻璃表面制得纹理饱满丰富的装饰品,
以上所述仅为本发明的较佳实施例,并不用以限制本发明,凡在本发明的精神和原则之内所作的任何修改、同等替换和改进等,均应落在本发明的保护范围之内。