精馏塔精馏段温度比值控制方案设计.docx
《精馏塔精馏段温度比值控制方案设计.docx》由会员分享,可在线阅读,更多相关《精馏塔精馏段温度比值控制方案设计.docx(20页珍藏版)》请在冰豆网上搜索。
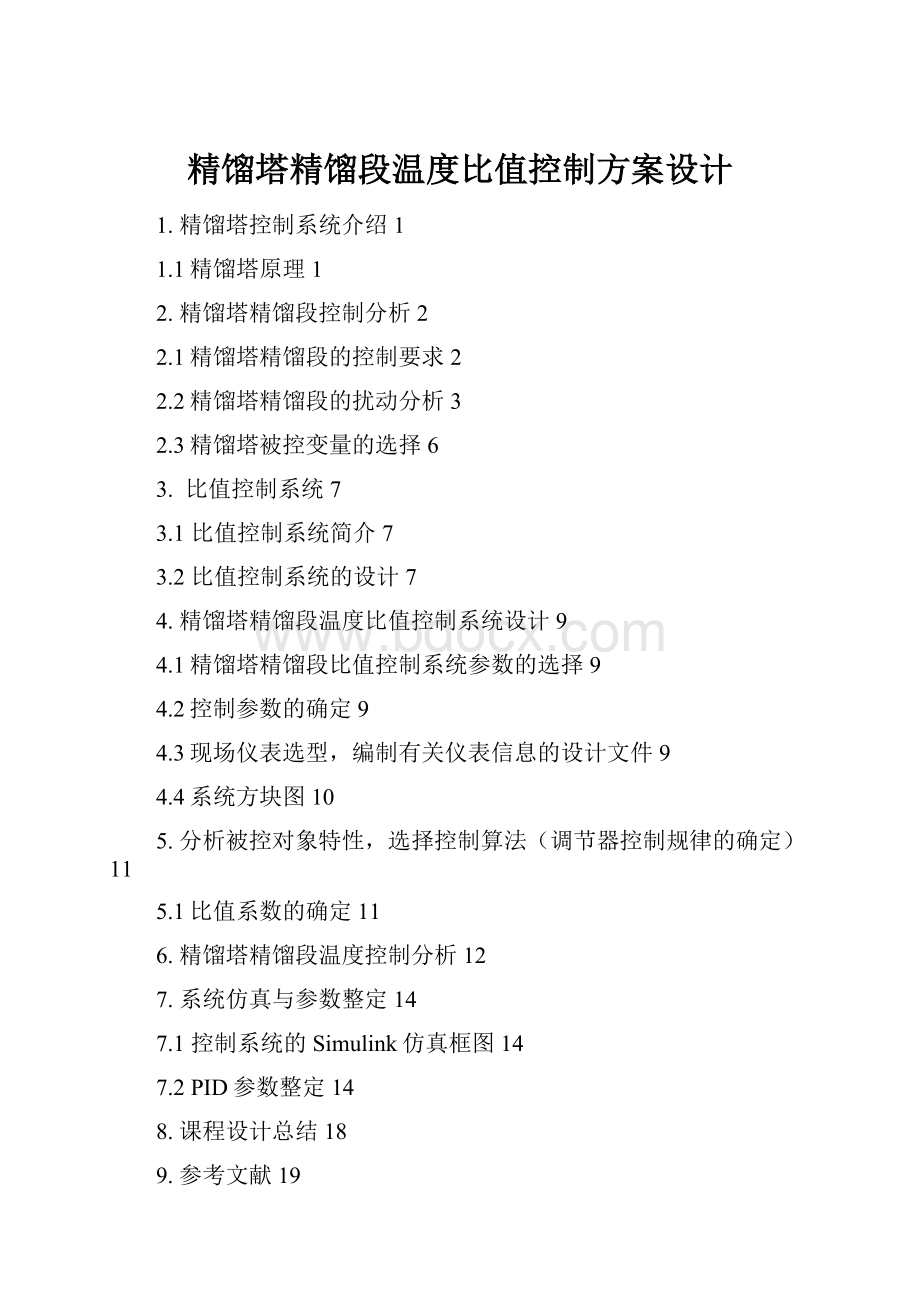
精馏塔精馏段温度比值控制方案设计
1.精馏塔控制系统介绍1
1.1精馏塔原理1
2.精馏塔精馏段控制分析2
2.1精馏塔精馏段的控制要求2
2.2精馏塔精馏段的扰动分析3
2.3精馏塔被控变量的选择6
3. 比值控制系统7
3.1 比值控制系统简介7
3.2 比值控制系统的设计7
4.精馏塔精馏段温度比值控制系统设计9
4.1精馏塔精馏段比值控制系统参数的选择9
4.2控制参数的确定9
4.3现场仪表选型,编制有关仪表信息的设计文件9
4.4系统方块图10
5.分析被控对象特性,选择控制算法(调节器控制规律的确定)11
5.1比值系数的确定11
6.精馏塔精馏段温度控制分析12
7.系统仿真与参数整定14
7.1控制系统的Simulink仿真框图14
7.2PID参数整定14
8.课程设计总结18
9.参考文献19
1.精馏塔控制系统介绍
1.1精馏塔原理
精馏塔是进行精馏的一种塔式汽液接触装置,又称为蒸馏塔。
有板式塔和填料塔两种主要类型。
根据操作方式又可分为连续精馏塔和间歇精馏塔。
蒸汽由塔底进入,与下降液进行逆流接触,两相接触中,下降液中的易挥发组分不断地向蒸汽中转移,蒸汽中的难会发组分不断地向下降液中转移,蒸汽越接近塔顶,其易挥发组分浓度越高,而下降液越接近塔底,其难挥发组分则越富集,达到组分分离的目的。
由塔顶上升的蒸汽进入冷凝器,冷凝的液体的一部分作为回流液返回塔顶进入精馏塔中,其余的部分则作为馏出液取出。
塔底流出的液体,其中的一部分送入再沸器,热蒸发后,蒸汽返回塔中,另一部分液体则作为釜残液取出。
蒸馏的基本原理是将液体混合物部分气化,利用其中各组分挥发度不同的特性,实现分离目的的单元操作。
蒸馏按照其操作方式可分为:
简单蒸馏,闪蒸,精馏,特殊精馏等。
1.2精馏装置的作用
(1)精馏段的作用
加料版以上的塔段为精馏段,其作用是逐板增加上升气相中的易挥发组分的浓度。
(2)提馏段的作用
包括加料版在内的以下塔板为提馏段,其作用是逐板提取下降的液相中易挥发组分。
(3)塔板的作用
塔板是供气液两相进行传质和传热的场所。
每一块塔板上气液两相进行双向传质,只要有足够的塔板数,就可以将混合液分离成两个较纯净的组分。
(4)再沸器的作用
其作用是提供一定流量的上升蒸气流。
(5)冷凝器的作用
其作用是提供塔顶液相产品并保证有适当的液相回流。
回流主要补充塔板上易挥发组分的浓度,是精馏连续定态进行的必要条件。
精馏是一种利用回流使混合液得到高纯度分离的蒸馏方法。
2.精馏塔精馏段控制分析
2.1精馏塔精馏段的控制要求
精馏塔的控制目标是,在保证产品质量合格的前提下,使塔的总收益(利润)最大或总成本最小。
具体对一个精馏塔来说,需从四个方面考虑,设置必要的控制系统。
(1)产品质量控制
塔顶产品合乎规定的纯度,塔底成品维持在规定的范围内。
所谓产品的纯度,就二元精馏来说,其质量指标是指塔顶产品中轻组分(或重组分)含量和塔底产品中重组分(轻组分)含分,塔顶产品的关键组分是易挥发的,称为轻关键组分,塔底产品是不易挥发的关键组分,称为重关键组分。
(2)物料平衡控制
进出物料平衡,即塔顶采出量应和进料量相平衡,维持塔的正常平稳操作,以及上下工序的协调工作。
物料平衡的控制是以回流罐与介于规定的上、下限之间为目标的。
(3)能量平衡控制
精馏塔精馏段的输入、输出能量应平衡,使塔内的操作压力维持稳定。
(4)约束条件控制
为保证精馏塔的正常、安全操作,必须使某些操作参数限制在约束条件之内。
常用的精馏塔限制条件为液泛限、漏液限、压力限及临界温差限等。
所谓液泛限,也称气相速度限,即塔内气相速度过高时,雾沫夹带十分严重,实际上液相将从下面塔板倒流到上面塔板,产生液泛,破坏正常操作。
漏液限也称最小气相速度限,当气相速度小于某一值时,将产生塔板漏液,板效率下降。
防止液泛和漏液,可以塔压降和压差来监视气相速度。
压力限是指塔的操作压力的限制,一般是最大操作压力限,即塔操作压力不能过大,否则会影响塔内的气液平衡,严重越限甚至会影响安全生产。
临界温差限主要是指再沸器两侧间的温差,当这一温差低于临界温差时,给热系数急剧下降,传热量也随之下降,不能保证塔的正常传热的需要。
2.2精馏塔精馏段的扰动分析
精馏塔精馏段的操作就是按照塔顶产品的组成要求来对这几个影响因素进行调节。
精馏操作过程的影响因素有以下几方面:
1.塔的温度和压力;2.进料量;3.进料组分;4.进料温度;5.回流量;6.塔顶冷剂量;7.塔顶采出量等.在精馏塔精馏段操作过程中要克服各种影响因素的变化,防止对塔顶产品的数量和组成的影响。
(1)精馏塔操作压力的变化对精馏塔精馏段操作的影响
塔的设计和操作都是基于一定的塔压下进行的,因此一般精馏塔总是首先要保持压力的恒定。
塔压波动对塔的操作将产生如下的影响。
①影响产品质量和物料平衡
改变操作压力,将使每块塔板上汽液平衡的组成发生改变。
压力升高,则气相中重组分减少,相应地提高了气相中轻组分的浓度;液相中轻组分含量较前增加,同时也改变了气液相的重量比,使液相量增加,气相量减少。
总的结果是:
塔顶馏分中轻组分浓度增加,但数量却相对减少;釜液中的轻组分浓度增加,釜液量增加。
同理,压力降低,塔顶馏分的数量增加,轻组分浓度降低;釜液量减少,轻组分浓度减少。
正常操作中,应保持恒定的压力,但若因操作不正常,引起塔顶产品中重组分浓度增加时,则可采用适当提高压力的办法,使产品质量合格,但此时釜液中的轻组分损失增加。
②改变组份间的相对挥发度
压力增加,组份间的相对挥发度降低,分离效率下降,反之,组份间的相对挥发度增加,分离效率提高。
③改变塔的生产能力
压力增加,组份的重度增大,塔的处理能力增大。
④塔压的波动
这将引起温度和组成间对应关系的混乱。
我们在操作中经常以温度作为衡量产品质量的间接标准,但这只有在塔压恒定的前提下才是正确的。
当塔压改变时,混合物的泡点、露点发生变化,引起全塔的温度发生改变,温度和产品质量的对应关系也将发生改变。
从以上分析可看出,改变操作压力,将改变整个塔的操作情况,因此在正常操作中应维持恒定的压力(工艺指标),只有在塔的正常操作受到破坏时,才可根据以上的分析,在工艺指标允许的范围内,对塔的压力进行适当的调节。
应该指出,在精馏操作过程中,进料量、进料组成和进料温度的改变,塔釜加热蒸汽量的改变,回流量、回流温度和冷剂压力(对内回流塔而言)的改变以及塔的堵塞等,都可能引起塔压的波动,此时应首先分析引起塔压波动的原因,及时处理,使操作恢复正常。
(2)进料量的变化对精馏塔精馏段操作的影响
进料流量是上工序的出料,因此,通常不可控但可测,当进料流量较大时,对精馏塔的操作会造成很大的影响。
进料流量影响物料平衡,也影响能量平衡。
因此,控制策略应保持流量的基本恒定。
进料成分影响物料平衡和能量平衡,但进料成分通常不可控,多数情况下也难于测量。
因此,控制策略是尽量控制上一工序的操作,从外围着手,使进料成分能够保持恒定,减小其变化对精馏塔操作的影响。
(3)进料组份的变化对精馏塔精馏段操作的影响
进料组份的变化直接影响精馏塔精馏段的操作,当进料中重组份的浓度增加时,精馏段的负荷增加。
对于固定了精馏段塔板数的塔来说,将造成重组份带到塔顶,使塔顶产品质量不合格。
若进料中轻组份的浓度增加时,此时精馏段的负荷增加。
对于固定了提馏段塔板数的塔来说,将造成提馏段轻组份蒸出不完全,釜液中轻组份的损失加大。
同时,进料组成的变化还将引起全塔物料平衡和工艺条件的变化。
组份变轻,则塔顶馏份增加,釜液排出量减少。
此时,全塔温度下降,塔压升高。
组成变重,情况相反。
进料组成变化时,可采取如下措施:
①改进料口 组成变重时,进料口往下改;组成变轻时,进料口往上改。
②改变回流比 组成变重时,加大回流比;组成变轻时,减少回流比。
③调节冷剂和热剂量 根据组成的变动情况,相应地调节塔顶冷凝器的冷剂和塔釜热剂量,维持塔顶及塔底产品质量不变。
(4)进料温度的变化对精馏塔精馏段操作的影响
进料温度的变化对精馏操作的影响是很大的。
总的来讲,进料温度降低,将增加塔底蒸发釜的热负荷,减少塔顶冷凝器的冷负荷;进料温度升高,则增加塔顶冷凝器的冷负荷,减少塔底蒸发釜的热负荷。
当进料温度的变化幅度过大时,通常会影响整个塔身的温度,从而改变汽液平衡组成。
例如:
在进料温度过低,塔釜的加热蒸汽量没有富裕的情况下,将会使塔底馏分中轻组分含量增加。
进料温度的的改变,意味着进料状态的改变,而进料状态的改变将影响精馏段、提馏段负荷的改变,进而产品质量、物料平衡都将发生改变。
因此,进料温度是影响精馏塔操作的重要因素之一。
(5)回流比的大小对精馏塔精馏段操作的影响
操作中以改变回流比的大小来保证产品的质量。
当塔顶馏分中重组份含量增加时,常采用加大回流比的方法将重组份压下去,以使产品质量合格。
当精馏段的轻组份下到提馏段造成塔下部温度降低时,可以用适当减少回流比的办法以使塔下部温度提起来。
增加回流比,对从塔顶得到产品的精馏塔来说,可以提高产品质量,但是却要降低塔的生产能力,增加水、电、汽的消耗。
回流比过大,将会造成塔内物料的循环量过大,甚至能导致液泛,破坏塔的正常操作。
(6)塔顶冷剂量的大小对精馏塔精馏段操作的影响
对采用内回流操作的塔,其冷剂量的大小,对精馏操作的影响比较显著;同时也是影响回流量波动的主要因素。
对于采用外回流的塔,同样会由于冷剂量的波动,在不同程度上影响精馏塔的操作。
例如,冷剂量减少,将使冷凝器的作用变差,冷凝液量减少,而在塔顶产品的液相采出量作定值调节时,回流量势必减少。
假如冷凝器还有过冷作用(即通常所称的冷凝冷却器)时,则冷剂量的减少,还会引起回流液温度的升高。
这些都会使精馏塔的顶温升高,塔顶产品中重组份含量增多,质量下降。
(7)塔顶采出量的大小对精馏塔精馏段操作的影响
塔顶采出量的大小和该塔进料量的大小有着相互对应关系,进料量增大,采出量应增大。
众所周知,采出量只有随进料量变化时,才能保持塔内固定的回流比,维持塔的正常操作,否则将会破坏塔内的气液平衡。
例如,当进料量不变时,对采用内回流的塔,若塔顶采出量增大,则回流比势必减少,引起各板上的回流液量减少,气液接触不好,传质效率下降;同时操作压力也将下降,各板上的气液相组成发生变化。
结果是重组分被带到塔顶,塔顶产品的质量不合格。
在强制回流的操作中,如果进料量不变,塔顶采出量突然增大,则易造成回流液槽抽空。
回流液一中断,顶温就升高,这同样也会影响塔顶产品质量下降。
如果进料量加大,但塔顶采出量不变,其后果是回流比增大,塔内物料增多,上升蒸汽速度增大,塔顶与塔釜的压差增大,严重时会引起液泛。
由上述分析可以看出,精馏塔的主要干扰因素为进料状态,即进料流量、进料组分、进料温度。
其中,进料流量与进料组分是不可控的,而进料温度可通过热焓来控制。
2.3精馏塔被控变量的选择
精馏塔被控变量的选择,主要讨论质量控制中得被控变量的确定,以及检测点的位置等问题。
通常,精馏塔的质量指标选取有两类:
直接的产品成分信号和间接的温度信号。
(1)采用产品成分作为直接质量指标
以产品成分的检测信号直接用作质量控制的被控信号,应该说是最为理想的。
过去,因成分参数在检测上的困难,难以直接对产品成分信号进行质量控制。
近年来,成分检测仪表发展迅速,尤其是工业色谱的在线应用,为以成分信号直接作为质量控制的被控变量,创造了现实条件。
然而,因成分分析仪表受以下三方面的制约,至今在精馏塔质量控制上成功地直接应用还是为数不多的:
① 分析仪表的可靠性差;
② 分析测量过程滞后大,反应缓慢;
③ 成分分析针对不同的产品组分,品种上较难一一满足。
因此,目前在精馏操作中,温度仍是最常用的间接质量指标。
(2)采用温度作为间接质量指标
温度作为间接质量指标,是精馏塔质量控制中应用最早也是目前最常见的一种。
对于一个二元组分精馏塔来说,在一定的压力下,沸点和产品的成分有单值的对应关系,因此,只要塔压恒定,塔板的温度就反应了成分。
3. 比值控制系统
3.1 比值控制系统简介
实现两个或多个参数符合一定比例关系的控制系统,称为比值控制系统。
例如要实现两物料的比例关系,则表示为:
Q2=K Q1。
比值控制系统分为开环比值控制系统、单闭环比值控制系统、双闭环比值控制系统和变比值控制系统。
3.2 比值控制系统的设计
(1)主、副流量的确定
①生产中起主导作用的物料流量,一般选为主流量,其余的物料流量跟随其变化,为副流量。
②工艺上不可控的物料流量,一般选为主流量。
③成本较昂贵的物料流量一般选为主流量。
④当生产工艺有特殊要求时,主、副物料流量的确定应服从工艺需要。
(2)控制方案的选择
控制方案选择应根据不同的生产要求确定,同时兼顾经济性原则。
①如果工艺上仅要求两物料流量之比值一定,而对总流量无要求,可用单闭环比值控制方案。
②如果主、副流量的扰动频繁,而工艺要求主、副物料总流量恒定的生产过程,可用双闭环比值控制方案。
③当生产工艺要求两种物料流量的比值要随着第三参数的需要进行调节时,可用变比值控制方案。
(3)调节器控制规律的确定
比值控制系统中,调节器的控制规律是根据控制方案和控制要求而定。
在单闭环比值控制系统中,比值器F1C起比值计算作用,若用调节器实现,则选P调节;调节器F2C使副流量稳定,为保证控制精度可选PI调节。
双闭环比值控制不仅要求两流量保持恒定的比值关系,而且主、副流量均要实现定值控制,所以两个调节器均应选PI调节;比值器选P调节。
(4)正确选择流量计及其量程
各种流量计都有一定的适用范围(一般正常流量选在满量程的70%左右),必须正确地选择和使用,可参考有关设计资料、产品手册。
(5)比值系数的计算
工艺规定的流量(或质量)比值K不能直接作为仪表比值使用,必须根据仪表的量程转换成仪表的比值系数K’后才能进行比值设定。
变送器的转换特性不同,比值系数K’的计算公式不同。
①流量与测量信号之间成线性关系
如果Q1的流量计测量范围为0~Q1max 、Q2的流量计测量范围为0~Q2max,则变送器输出电流信号和流量之间的关系为:
(1)
②流量与测量信号之间成非线性关系
如果Q1的流量计测量范围为0~Q1max 、Q2的流量计测量范围为0~Q2max,则变送器输出电流信号和流量之间的关系为:
(2)
4.精馏塔精馏段温度比值控制系统设计
4.1精馏塔精馏段比值控制系统参数的选择
被控参数选择 由于此系统为温度控制系统,所以选用精馏塔精馏段的温度为被控参数。
控制参数选择 由图1的精馏塔精馏段过程流程图可知引起精馏段温度变化的因素大概主要有:
(1)进料流量F
(2)冷却介质
(3)回流量(4)塔顶采出量
图1精馏段流程图
4.2控制参数的确定
精馏段中对温度有影响的主要有进料流量F、回流量L、冷却介质。
由图1知进料流量和回流量直接进入精馏段,滞后最小,对于精馏段温度的校正作用最灵敏。
对于旁路冷却介质和塔顶采出量不进入精馏段,对精馏段的温度影响较小,故控制通道的时间滞后较大,对于精馏段的温度校正作用的灵敏度要差一些。
所以综合考虑选择进料流量为主流量和回流量L作为副流量,且回流量L为被控变量。
4.3现场仪表选型,编制有关仪表信息的设计文件
根据流程图,需要选择一个流量测量变送器、一个温度测量变送器、一个流量调节阀。
①流量变送器的选择。
流量测量仪表也称为流量计,它通常由一次仪表和二次仪表组成。
一次仪表亦称为传感器,二次仪表称为显示装置或变送器。
差压式流量计基于在流通管道上设置流动阻力件,流体通过阻力件时将产生差压,此差压与流体流量之间有确定的数值关系,通过测量压差值便可求得流体流量,并转换成电信号输出。
因此,差压式流量计由产生压差的装置和差压计两部分组成,其结构简单,可靠。
节流式流量计可用于测量气体、液体或蒸汽的流量。
②温度测量变送器的选择。
温度测量的方法很多,一般可分为接触式测温法和非接触式测温法。
接触式测温法是测量体与被测物体直接接触,两者进行热交换并最终达到热平衡,这时测量体的温度就反应了被测物体的温度,而非接触式测温法的误差较大。
由于原料油的裂解需要对温度有较严格的规定,因此,选择接触式测温法。
热电偶温度仪表是基于热电效应原理制成的测温仪器。
两种不同材料的导体A、B组成一个闭合回路,当回路两端接点t0、t温度不相同时(假设t>t0),回路中就会产生一定大小的电势,形成电流,这个电流的大小与导体材料性质和接点温度有关。
把两种不同材料的组合称为热电偶,它感受被测温度信号,输出与温度相对应的直流电势信号。
③执行机构(调节阀)的选择。
执行器可分为气动、液动、和电动执行器,液动执行器使用较少,气动执行器是以压缩空气为能源的执行器(气动调节阀),主要特点是:
结构简单、动作可靠、性能稳定、故障率低、价格便宜、维修方便、本质防爆、容易做成大功率等。
与电动执行器相比,性能优越得多,故应用广泛。
4.4系统方块图
下图为单闭环比值控制系统方框图,该系统的主流量为进料流量q1,副流量回流量q2
T
图2精馏塔精馏段比值控制系统方块图
5.分析被控对象特性,选择控制算法(调节器控制规律的确定)
变比值控制系统又可称为串级比值控制系统,它具有串级控制系统的一些特点,仿效串级控制系统调节器的选择原则,主调节器选PI控制规律,比例控制器选用P控制规律。
被控对象为单容对象,即
(3)
检测环节均为比例环节,即Gm1(s)=Km1(4)
控制阀为比例控制,即Gv(s)=Kv(5)
5.1比值系数的确定
工艺物料流量的比值K,是指两流量的体积流量或质量流量之比。
比值系统K'是流量比值K的函数,当控制方案确定后,必须把工艺上的比值K折算成仪表上的比值系数K',并正确设定在相应的控制仪表上,这是保证系统正常运行的前提。
本系统的流量与测量信号成线性关系,设工艺要求Q2/Q1=K,测量流量Q1和Q2的变送器的测量范围分别为0~Q1max和0~Q2max,则折算成仪表的比值系数为
(6)
K'即为比值器的比值系数。
6.精馏塔精馏段温度控制分析
对于单闭环比值控制系统、双闭环比值控制系统的主动量来说,可按单回路控制系统的整定方法和要求来进行。
一般希望主动量回路的过渡过程变化缓慢一些,以便从动量得以跟踪上。
变比值控制系统结构上属于串级控制系统,因此其主调节器的参数可按串级控制系统进行整定。
而从动量回路实质上是一个随动系统,要求从动量能迅速、准确地跟踪主动量变化,而且不宜有过大超调。
从动量回路的过渡过程整定非周期临街状态为最佳,此时从动量回路的过渡过程既不震荡有反应最快。
从动量回路控制器参数整定步骤如下:
1、根据计算的比值系数K'在满足工艺生产流量比的情况下,将比值控制系统投入进行。
2、将积分时间常数置于最大,由大到小改变调节器的比例度,使系统响应迅速,并处于振荡与不振荡的临界过程。
3、若有积分作用,则适当的加大比例度,投入积分作用,并减小积分时间,直到系统出现振荡与不振荡的临界过程。
回流量测量仪表为线性单元,动态滞后可忽略,则有:
(7)
进料流量测量仪表亦为线性单元,动态滞后亦可忽略,则有:
温度测量环节用一阶环节来近似:
(8)
假设
(9)
对于调节阀,由于其流量特性为直线和等百分比:
(10)
比值控制器的传递函数由线性环节代替,即
流量对象的传递函数模型近似为一阶惯性环节,即传递函数为
对于流量控制精馏段温度对象,控制通道的动态特性为:
(11)
假设:
,
,
,
,
即可得:
7.系统仿真与参数整定
7.1控制系统的Simulink仿真框图
控制系统的Simulink仿真框图,如图3:
图3控制系统仿真框图
7.2PID参数整定
临界比例度法又称Ziegler-Nichols方法,早在1942年就已提出。
它便于使用,而且在大多数控制回路中能得到良好的控制品质。
尽管还有一些另外的方法,但与临界比例度法相比看不出明显的改进,所以临界比例度法仍是常用方法之一。
因此本次PID参数整定采用临界比例度法。
将控制器的积分作用和微分作用全部切除,将比例增益由小到大变化,以获得临界情况下的等幅振荡,如图4、图5所示。
图4PID控制器参数设置
图5临界振荡
由图所示,可得控制器临界比例增益
,临界振荡周期
根据表1所列的经验算式求取控制器的最佳参数值。
表1临界比例度法整定参数
控制规律
Ti
Td
P
0.5
PI
0.45
0.83
PID
0.6
0.5
0.12
临界比例度法整定参数可得到衰减比为n=4:
1的响应曲线
图6衰减比为n=4:
1的整定值
图7衰减比为n=4:
1的响应曲线
用临界比例度法整定PID参数后,系统相对其他情况下的响应达到稳定所需时间短,且能在达到稳定后保持在稳定值附近变化,超调量相比而言也较小,即此时的出最佳参数,用Simulink仿真如下图所示。
图8PID控制器参数设置
图9最佳参数下系统响应曲线
8.课程设计总结
刚开始拿到题目的时候,完全不知道该从哪里开始。
以前学的东西都忘得差不多了,对精馏塔精馏段的具体工艺流程也不是特别的了解,感觉这次课程设计好难的,迟迟不能动手开始做。
但是,当自己真的下定决心开始弄的时候,却慢慢的在其中找到了感觉。
因为每个人的设计题目都是不一样的,所以也就不存在去参考别人的了,设计的对象也是我们以前没有接触过的,这就要求我们花更多的精力去查阅资料,了解更多的知识,对我们提出了更强的独立性要求。
在自己探索,查资料的过程中,也对自己的课程设计的那一部分的内容有了一些大致的了解,自己的课程设计也慢慢的有了一个雏形,虽然最终做的不是特别的好,但是也是自己一步一步的做出来的,心里也还是有一点小小的成就感的。
通过这个简单的控制系统的设计,我对控制系统又有了更深的理解,尤其是对比值控制系统的认识了解的更多了。
9.参考文献
[1]胡寿松.自动控制原理. 第2版. 北京:
科学出版社,2008
[2]王毅,张早校编.过程装备控制技术及应用.第2版.北京:
化学工业出版社,2007
[3]谭天恩等.化工原理[M].北京:
化学工业出版社,2008,45-63
[4]王树青,戴连奎,于玲.过程控制工程.第2版.北京:
化学工业出版社,2008,84-85
[5]吴勤勤.控制仪表及装置.第2版.北京:
化学工业出版社,2002.
[6]俞金寿.过程自动化及仪表.北京:
化学工业出版社,2003.
[7]康勇、张建伟、李桂水.过程流体机械.北京:
化学工业出版社,2008.
[8]刘文定,王东林.过程控制系统的MATLAB仿真.北京:
机械工业出版社,2009.