连铸工艺控制培训讲义.docx
《连铸工艺控制培训讲义.docx》由会员分享,可在线阅读,更多相关《连铸工艺控制培训讲义.docx(62页珍藏版)》请在冰豆网上搜索。
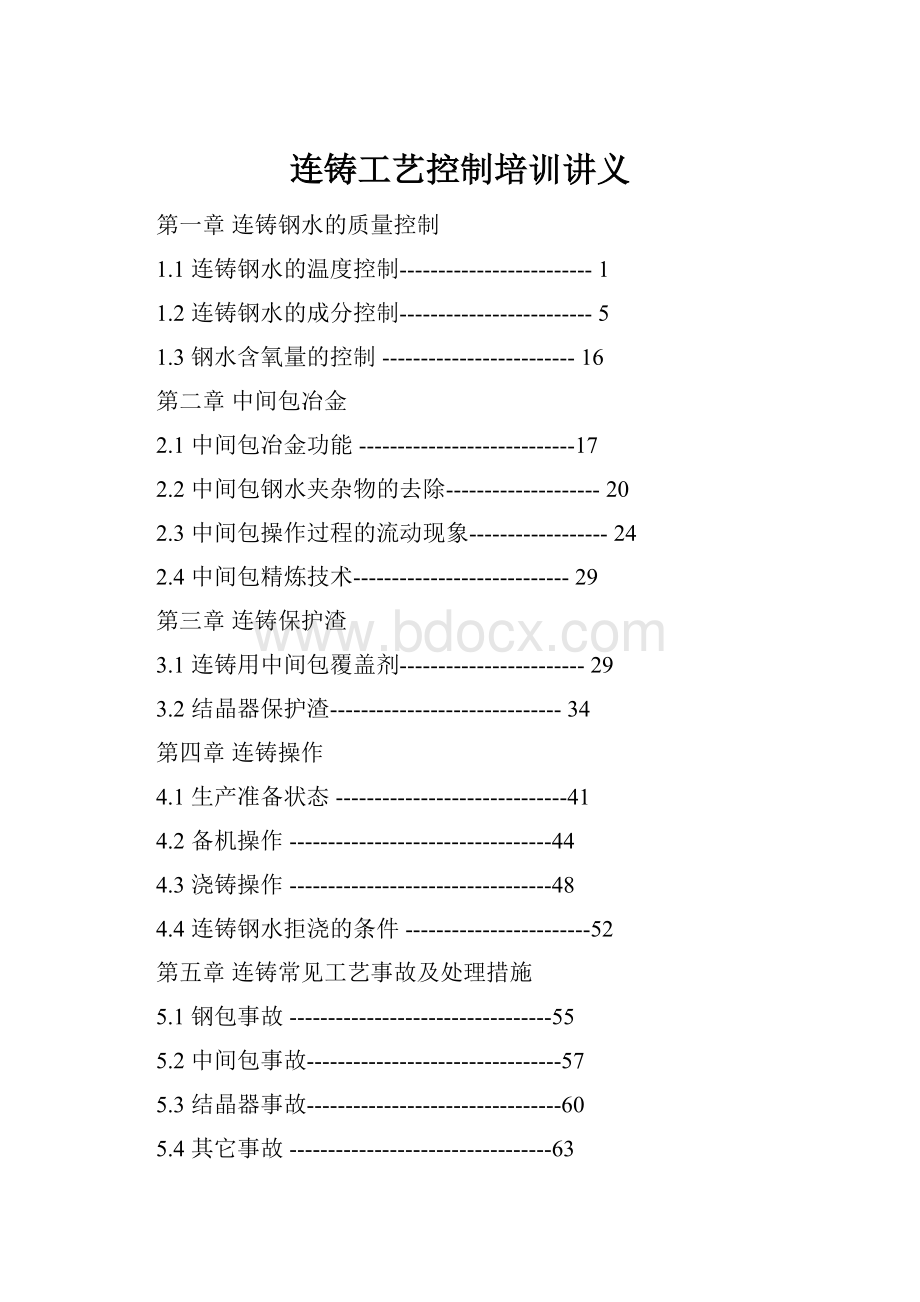
连铸工艺控制培训讲义
第一章连铸钢水的质量控制
1.1连铸钢水的温度控制-------------------------1
1.2连铸钢水的成分控制-------------------------5
1.3钢水含氧量的控制-------------------------16
第二章中间包冶金
2.1中间包冶金功能----------------------------17
2.2中间包钢水夹杂物的去除--------------------20
2.3中间包操作过程的流动现象------------------24
2.4中间包精炼技术----------------------------29
第三章连铸保护渣
3.1连铸用中间包覆盖剂------------------------29
3.2结晶器保护渣------------------------------34
第四章连铸操作
4.1生产准备状态------------------------------41
4.2备机操作----------------------------------44
4.3浇铸操作----------------------------------48
4.4连铸钢水拒浇的条件------------------------52
第五章连铸常见工艺事故及处理措施
5.1钢包事故----------------------------------55
5.2中间包事故---------------------------------57
5.3结晶器事故---------------------------------60
5.4其它事故----------------------------------63
第六章连铸的先进工艺
6.1结晶器液位自动控制------------------------65
6.2动态软压下-------------------------------68
6.3方坯连铸电磁搅拌技术----------------------70
6.4高碳连铸的组合电磁搅拌技术----------------78
第一章连铸钢水的质量控制
与传统的模铸相比,连铸对钢水质量有着严格的要求,它既要保证稳定适宜的钢水温度和脱氧程度,以满足可浇性;又要最大限度地降低钢中S、P杂质及气体含量,以确保连铸的顺行和铸坯质量的提高,保证合格钢水的及时供应,是提高连铸生产的基础和前提。
§1.1连铸钢水的温度控制
一、连铸钢水温度控制的重要性
钢水的浇注温度是浇注的重要工艺参数,连铸的要求比模铸要严格,原因:
1.合适的浇注温度是顺利连铸的基础
钢水温度过低:
容易引起中间包水口冻结,迫使浇注中断。
钢水温度过高:
容易引起钢水包水口失控,会使坯壳减薄和厚度不均,造成漏钢。
2.合适的浇注温度是获得良好铸坯质量的基础
浇注温度偏高:
会加剧钢水的二次氧化;加剧对钢水包衬耐火材料的侵蚀,增加钢中非金属夹杂物,使铸坯鼓肚,内裂,中心疏松和偏析等缺陷的产生。
浇注温度偏低:
使结晶器内钢液形成冷壳,恶化铸坯的表面质量,且使钢中的非金属夹杂物难于上浮排除,降低钢的纯净度。
二、连铸钢水的温度要求
1.高温:
由于增加了中间包的热损失,中间包水口小,浇注时间长,因此钢水温度比模铸高20~50℃,才能顺利浇注。
2.均匀:
实际上钢包内钢水温度是上下偏低,中间温度高,这样会造成中间包钢水温度也是两头低中间高,不利于浇注过程的控制,因此要求钢包内钢水温度均匀。
3.稳定:
连铸时供给的各炉钢水温度不要波动太大,保持在10~20℃
三、连铸钢水浇注温度的确定
连铸钢水的浇注温度,一般是指中间包内的钢水温度,钢水的浇注温度等于该钢种的液相线温度加上中间包钢水合适的过热度TC=TL+△T℃
TC:
浇注温度℃
TL:
钢的液相线温度℃
T:
中间包钢水的过热度℃
1.钢的液相线温度的计算
钢水的液相线温度是确定浇注温度的基础,它取决于钢水中所含元素的性质和含量。
(普碳、低合金应用)
TL=1537-{88[C%]+8[Si%]+5[Mn%]+30[P%]+25[S%]+5[Cu%]+4[Ni%]+2[Mo%]+2[V%]+1.5[Cr%]℃
2.过热度的确定
钢水的过热度的最大值出现在一炉钢的浇注总时间的四分之一左右,此时中间包内钢水温度最高,称为最大过热度。
浇注结束时钢水温度减去液相线温度等于浇注末期过热度。
连铸钢水过热度对连铸机产量和铸坯质量的影响:
高的过热度,会使拉速降低,增加拉漏的危险性;中心偏析严重;但有利于夹杂物的上浮。
相反,低的过热度会使拉速提高,拉漏的几率减小;中心偏析减轻;夹杂物上浮困难。
中间包内合适的钢水过热度决定于:
所浇注的钢种,钢包和中间包内的热状况,中间包容量和形状,中间包内衬材质,铸坯断面,钢水纯净度和铸坯的内部质量。
一般来说,钢种含碳量低,铸坯断面小,则钢水的过热度取低些,相反,钢种中C、Si、Mn含量高,铸坯断面大,则钢水的过热度取低些。
不同的钢种,过热度的取值如下:
板坯高C、高Mn钢5~10℃
碳结钢10~15℃
铝镇静钢15~30℃
硅钢5~10℃
不锈钢15~20℃
3.浇注温度的确定
TL=TC+△T选择合适的过热度,加上钢种的液相线温度。
例:
浇注普碳钢Q235其化学成分为:
钢号
C
Si
Mn
P
S
Q235
0.14~0.22
0.12~0.30
0.35~0.65
≤0.040
≤0.040
TL=1537-{88×0.14+8×0.12+5×0.35+30×0.04+25×0.04}
=1520℃
TL=1537-{88×0.22+8×0.30+5×0.65+30×0.04+25×0.04}
=1510℃
因此,该钢种的液相线温度范围为1510~1520℃,钢水过热度取30℃,则该钢种的浇注温度范围为1540~1550℃
四、连铸钢水传递过程中温度的变化规律
生产过程中,钢水进入钢包后,随着时间的推移,其温度逐渐降低,要确定不同钢种的合理浇注温度,必须确定出出钢至浇注各个阶段的温度损失。
钢水过程总温降T总=T1+T2+T3+T4+T5℃
T1—-出钢时的温降℃
主要取决于钢水的出钢温度,出钢时间,钢水包容量及包衬材质,加入合金的种类和数量,包衬的状态等。
缩短出钢时间,减少包衬吸热,可减少出钢时的温降。
T2—-出钢后到钢水炉外精炼站运输过程中的温降。
℃
主要取决于钢包容量,包衬材质和钢包表面覆盖,等待时间和运输距离等因素。
钢包包衬温度愈高,钢水热损失愈少,加快钢包周转,保证红包出钢,是减少钢水温降的有效办法。
T3—-钢水在钢包处理过程中的温降。
℃
主要取决于钢水的炉外处理方法。
当钢包采用吹氩处理时,50吨钢包不烘烤吹3分钟的氩气降温30℃
T4—-钢包运至中间包处的过程温降。
主要取决于大包开浇的等待时间。
℃
T5—-钢水在中间包内的温降。
℃
主要取决于中间包内衬吸热和钢水表面的辐射散热。
试验测定表明:
如果中间包钢液表面无任何覆盖剂,表面的辐射散热占总热损失的90%,因此中间包内钢液表面的覆盖保温是不可缺少的,炭化稻壳具有良好的保温效果。
五、出钢温度的确定
根据钢种,铸坯断面等确定了中间包钢水温度的目标值,再加上钢水传递过程中总温降T,就可确定出钢温度。
T出=TC+T总
浇注第一包钢水时,因中间包内钢水热损失较大,为便于开浇,要求出钢温度比连铸时提高10~15℃,例如国内本钢120吨转炉连铸Q235板坯的出钢温度:
(1)浇注温度:
1530~1535℃
(2)过程温降:
大包到中间包的温降30~35℃
吹氩后到开浇等待时间温降10℃
吹氩降温:
15℃
出钢降温:
60℃
所以,出钢温度为T出=1535+(35+10+15+60)=1655℃
六、连铸钢水温度控制的对策
连铸钢水温度控制的目的:
使中间包钢水浇注温度在目标温度范围内。
但实际生产中,影响因素很多,温度波动大,偏离预定的目标温度,为此必须对钢水温度进行调整。
1.稳定出钢温度
稳定出钢温度是控制的基础,具体措施为:
(1)转炉内钢水温度是不均匀的,终点测温点应选定具有代表性的位置。
(2)转炉冶炼应根据铁水成分,温度等确定适当的冷却剂加入量,并要稳定冶炼工艺操作,提高终点出钢温度的命中率。
(3)维护好出钢口,缩短出钢时间。
(4)各厂根据本厂的生产实际,建立出钢温度控制模式。
2.减少传递过程中的钢水温降
浇注过程温降中,出钢温降和中间包温降最大,且波动比较大,因此降低过程温降,关键是要降低出钢过程温降和中间包温降。
(1)红包出钢:
对于150吨的钢包,包衬提温20℃,出钢温降可减少1℃。
包衬温度低于800℃应用煤气烘烤。
(2)缩短钢包出钢前的等待时间:
对于150吨的钢包出钢前钢包等待时间10~20℃,由于包衬周围的热大量向四周散失,包衬散失热量相当于钢液温降11~13℃,所以应使钢包在出钢前的等待时间缩短到最低程度。
(3)钢包液面加覆盖剂:
采用炭化稻壳覆盖钢液可减少热损失13.3%。
(4)钢包加绝热层和钢包加盖:
150吨钢包,包衬采用绝热层可减少温降12℃。
钢包预热情况下,钢包加盖可减少温降22℃。
(5)加速钢包周转:
严格控制钢包周转,缩短钢包周转时间,虽然预热时间减少,但包内热含量要高,减少热损失。
(6)减少中间包的热损失。
A:
开浇时,降温较大,开浇困难,开浇前中间包必须预热。
B:
砌砖中间包烘烤时间在2小时以上,若预热温度从750℃提到1000℃,可减少开浇时温度损失1520℃。
C:
砌绝热板中间包,开浇前预热20~30℃,板子表面温度800℃,与冷包比减少初期温降1520℃。
D:
中间包加盖或加炭化稻壳覆盖。
七、钢水温度不正常的处理
(一)钢水温度不均匀时的处理:
吹氩
1.连铸钢水为什么要进行吹气搅拌?
(1)从炼钢炉出到钢包的钢水,在钢包内钢水温度分布是不均匀的,由于包衬吸热和钢包表面的散热,在包衬周围钢水温度较低,而钢包中心区域温度较高,这样如把钢水注入中间包,由于中间包衬的吸热再加上钢包底部钢水温度较低,就会造成中间包钢水温度降低过大而接近液相线温度,导致水口冻结,浇注中断。
(2)钢包上、下部钢水温度低而中间温度高的特点,导致浇注过程中中间包钢水温度前、后期低,中期温度高,引起结晶器坯壳生长厚度的不均匀性,同时影响铸坯的内部质量。
2.吹气的目的
借助吹惰性气体搅拌来均匀温度,使包底附近的低温钢水向表层移动,并且使包内温度均匀化。
(1)均匀钢水温度,促使钢包内上、下部钢水温度的均匀。
(2)均匀钢水成分,出钢时加入的铁合金,在搅拌时得到很好的均匀。
(3)促使钢水中的非金属夹杂物上浮。
3.吹气种类的选择
生产中常用的钢包搅拌气体有惰性气体(Ar)和不活泼气体(N2)
Ar:
不溶解于钢水,也不与任何元素发生化学反应,是一种理想气体,但其成本很高,约为N2成本的5~10倍。
N2:
便宜,高温下N能溶解在钢水中,能与钢中的一些元素反应生成氮化物,影响钢的质量,因而它的使用受到了一定的限制。
4.吹气量的确定
吹气压力和吹气流量的控制应以不使钢水裸露翻腾为原则,否则钢水发生二次氧化,使钢中氮和夹杂物含量增加,影响钢包吹气搅拌效果最重要的因素是吹气流量和吹气压力的选择。
吹入钢水中的气体,分散成无数的小气泡而上浮,同时,在高温钢水中气体被加热而膨胀,这样产生的上浮力、抽引力相当于吹入气体体积的50~100倍钢水进行循环运动,从而产生了强烈的搅拌作用。
随着吹气量的增加,搅拌强度的增加,如果吹气量超过某一临界值,吹入的气体从钢包底部向上形成穿流,容易引起钢水的喷溅,加重了钢水的二次氧化,减轻了搅拌强度。
吹氩压力:
0.2~0.3MPa
吹氩流量:
0.10~0.20m3/min
吹氩耗量:
0.1~0.5Nm3/t
吹氩搅拌时间应大于钢水温度和成分混匀的时间,3~5min
(二)包内钢水温度偏高时
在吹气搅拌的同时向钢水中加入轻型的洁净的废钢降温,冷却效果比较稳定。
加入1%的废钢,可使包内钢水温度降低约14℃,即每降温1℃,需加废钢0.7公斤。
(三)包内温度偏低时
在钢包内对钢水进行加热处理
1.加热对连铸带来的益处
(1)有可能进一步降低出钢温度,减轻转炉的额外负担,提高炼钢炉的生产率。
(2)可以更精确地控制钢水的温度和成分,特别是可对因各种事故造成的低温钢水进行应急补救,使连铸生产更趋于稳定。
(3)钢水包钢水加热装置可以成为炼钢和连铸之间的缓冲设备,有利于炼钢、连铸的均衡生产。
因此,钢水包内钢水的加热技术正在成为炼钢、连铸实现高效、均衡、稳定生产的重要措施。
2.加热的方法
(1)电弧加热法
也称钢包炉(LF炉)法:
它由钢包盖,盖上有三个电极孔,喷粉系统,除尘系统,电极加热系统和测温取样系统所组成。
钢水面上覆盖一层75mm左右厚的合成脱S渣,加热时降下电极,然后钢水在吹气搅拌的同时被电弧加热,根据需要喷吹脱氧剂和合金对钢水成分进行微调。
此种加热方法使用埋弧加热,热效率高,脱硫和扩散脱氧的效果好,费用低,采用的比较多。
(2)化学加热法
用喷枪吹氧使加入到钢水中的铝等元素氧化,释放大量的热量,使钢水快速升温,因在浸渍罩内几乎没有渣子,所以吹入的氧气,与钢水直接接触,氧化效率高,因而特别易于预测钢水的升温情况。
试验表明:
当吹氧4min铝粉耗量为0.5时kg/t,150吨钢水包内钢水温度可升高约20℃,
§1.2连铸钢水的成分控制
钢水成分首先应满足钢种规格的要求,但符合要求的钢水不一定完全适宜连铸,例如;普碳钢,模铸要求[S]含量为0.050%以下,但连铸要求[S]含量为0.030%以下。
因此,必须根据连铸工艺和铸坯质量的特殊要求,对钢水的成分进行严格的控制。
一、控制原则
1.成分的稳定性
控制成分在较窄的范围,连浇炉次的钢水成分一定要稳定,才能保证铸坯的性能均匀。
2.抗裂纹敏感性
连铸坯受到强制冷却凝固过程中的热应力、组织应力、静压力、拉坯矫直力等,一旦在铸坯的薄弱部位造成应力集中,就会引起铸坯的表面裂纹或内部裂纹,因此,必须控制裂纹倾向的元素,避开各成分裂纹敏感区;减少对裂纹有害元素的含量;加入第三种元素消除不良元素的影响。
3.钢水的可浇性
防止水口堵塞,采取合理的脱氧制度,不使铸坯产生皮下气泡。
二、钢水中元素的种类
1.合金元素:
有意加入到钢水中的,使其达到规定的成分范围,保证钢的机械性能和使用性能。
如:
Si、Mn等。
2.杂质元素:
不希望在钢中存在的,也不是有意加入的,对钢的性能起有害作用。
如:
P、S等。
3.微量元素:
有意加入的,是为了改变钢的某一种性能的。
如:
B、Ti、V等。
4.残余元素:
由原材料或耐火材料带入的,在炼钢的过程中难以去除的。
影响钢的热脆性和腐蚀性。
如:
As、Sb、Cu等。
三、成分控制
1.C:
是钢中最基本的也是对钢的组织性能影响最大的元素,必须对它进行精确控制,多炉连浇时,各包次之间钢水的含碳量的差别要求0.02%
因为:
C=0.10%~0.12%时,对铸坯纵裂纹的敏感性最大。
结晶器热流最低,结晶器内凝固坯壳不均匀,主要是此含C量在凝固过程中的包晶反应造成的。
2.Si、Mn:
控制在较窄的范围内,保证连浇炉的Si、Mn的相互稳定。
必须经过炉外精炼的成分微调,达到钢种的要求。
3.P、S:
[S]≥0.020%,板坯表面热裂纹增加,P、S含量应根据产品质量要求按钢种的下限控制。
4.残余元素:
钢中原料带入的,不是有意加入的,在钢水的精炼过程中又不能去除,残留在钢中的元素。
如:
Cu、Sn、Pb等。
其总量0.20%。
§1.3连铸钢水的纯净度控制
钢水纯净度是指钢中气体(N2、H2、O2)含量和非金属夹杂物的含量、形态和分布。
纯净度高,可改善钢的性能,减少铸坯的缺陷,提高内部质量。
提高最终产品的机械性能和使用性能。
一、冶炼钢水含氧量的控制
1.炼钢熔池中氧的行为
钢水的氧受熔池中的[C]和炉渣中的(FeO)的控制。
[O]实际随着[C]的降低而增加,[C]高则[O]低,终点氧愈高,产生的夹杂物愈多。
[O]实总是高于[O]平,,它们之间的差值称为熔池的过剩氧,这些过剩的氧靠出钢时的脱氧操作去除。
因此,要控制冶炼终点的钢水中的氧含量。
2.转炉终点氧含量的控制
转炉冶炼为了减少终点氧含量,应减少后期拉C次数,防止后吹,后吹的钢水一定要包内增C,利用C-O反应激烈沸腾,对钢水脱氧,降低钢中夹杂物的含量。
二、夹杂物种类和形态的控制
1.Si和Mn的脱氧
仅用Si、Mn脱氧的钢,Mn/Si=3.0脱氧产物为固态的SiO2,结晶器面上产生粘的浮渣,钢水流动性差,易造成漏钢的危险。
Mn/Si=3~6脱氧产物颗粒半径大,液态的硅酸盐,有利于夹杂物上浮。
因此,在保证钢的成分条件下:
钢中[Si]按中下限控制,[Mn]按中上限控制,易于得到液态的硅酸锰,提高流动性,改善了钢水的可浇性。
2.铝脱氧
强脱氧剂,与Si-Mn脱氧比可保持从出钢到浇注再到凝固时,钢中氧含量始终是低浓度。
AI2O3夹杂在钢中呈群簇状,具有树枝形的特点。
(1)AI2O3夹杂的影响
A:
尽管群簇状夹杂物尺寸相当大,但外形复杂的树枝状间包含钢,提高了夹杂物的显密度,因而显著降低夹杂物上浮速度。
B:
[AI]=0.006%时,全部为AI2O3夹杂,定径水口易造成结瘤。
C:
AI镇静钢中[AI]=0.02%~0.05%不发性水口堵塞的中包水口直径为50~70mm.
(2)防止钢水中AI2O3群簇状夹杂物堵水的措施
用Fe-Al-Si合金代替Al脱氧,可稳定提高Al的回收率。
纯Al的熔点是660℃,而合金熔化温度较高,加入的合金在钢包内保持固态时间较长,受热内部应力增加,合金炸裂有利于AI向钢水中溶解。
同时,合金中Si的初晶体包围Al—Si共晶体,保护Al不被空气氧化,使合金分散在钢水中
第二章中间包冶金
传统的中间包只起到储存,分配钢水和稳定注流的作用,随着连铸对钢的质量要求日益提高,人们把中间包作为钢包与结晶器之间的一个精炼反应器,以进一步改善钢的质量。
§2.1冶金功能
一、净化功能
在中间包内采用挡墙加坝,吹Ar,过滤器等措施,降低钢中非金属夹杂物的含量,生产高纯度钢。
改善钢水流动形态,延长钢水在中间包内的停留时间,促进非金属夹杂物的上浮排除。
二、调温功能
在中间包内可以对钢水进进行温度的调整,最后达到中间包前、中、后期钢水温差小于5℃。
三、精炼功能
由塞棒杆中心孔向结晶器喂入Al、Ti、B等合金元素,达到钢种的要求。
实现了上述要求,就进一步净化了进入结晶器的钢水清洁度,提高了中间包当作一个连续精炼冶金反应器的构想。
§2.2中间包钢水夹杂物的去除
夹杂物上浮速度
在静止液体中质点上浮速度:
V=2Rg(ρl-ρs)/9μcm/s
R—夹杂物质点半径cm
ρl-----钢流密度;ρs-----夹杂物密度
μ---钢液粘度;g----重力加速度
二、影响因素
由于中间包钢水流动的紊流作用,夹杂物相互碰撞聚合,加速了夹杂物上浮,而聚合速度取决于紊流动能的消失速率。
中间包的紊流强度可促使包内夹杂物质点的碰撞聚合,有利于夹杂物的上浮。
三、采取的措施
1.增加钢水在中间包平均停留时间,使夹杂物有足够的时间上浮,中间包大容量发展。
2.改善液体流动轨迹,液体把夹杂物带到中间包表面区,缩短了上浮距离,在中包内设障碍物,改变流动方向,消除死区。
3.钢包注流不应把夹杂物带入中间包底部而是在某一定高度,中包液位由浅熔池向深熔池方向发展。
四、钢水平均停留时间
1.钢水从钢包入口连续流出到结晶处所经历的时间叫理论平均停留时间。
2.钢水在中间包内的停留时间越长,夹杂物上浮的几率就越大,目前停留时间一般为3~10min。
促使中间包内夹杂物上浮的最有效的办法是:
采用大容量,深熔池的中间包。
§2.3中间包操作过程的流动现象
一、中间包钢液流动概念
描述液体流动的基本参数是流动速度,流动轨迹和紊流强度。
Re≤2000层流
Re>2000紊流
若钢包水口注流速度为3.2m/sRe=26105高度紊流。
中间包水口注流的Re=12105高度紊流。
中间包内流速1~2m/sRe=104中等紊流。
2.钢包注流冲击区
钢包注流进入到中间包的冲击区,可能存在的流动状态是:
(1)注流为自由流股,流股卷入周围液体而逐渐消失。
(2)注流流入一个对称的中间包,引起多种类型的循环流动。
(3)注流流入非对称的中间包,引起多种类型的循环流动。
3.注流卷入空气
钢包注流相当于“喷射泵”的作用,把周围的空气卷入到液体中,加重了二次氧化,污染钢水,卷入空气量主要取决于注流的紊流程度。
注流为光滑的层流卷入空气量较少
注流为脉动紊流卷入空气量较多
注流为高度紊流卷入空气量很多
注流为分散的液滴卷入空气量最大
注流卷入的空气进入中间包冲击区,破裂成细小的气泡而引起附加的环流。
4.旋涡
当容器中液体快流完而液面降到临界高度时,在流出口上方形成旋涡。
其危害:
(1)中间包渣卷入到结晶器中
(2)把空气卷入到液体中
(3)使中间包注流不稳定,搅乱结晶器的钢液流动。
防止的措施:
只要液面下降到临界高度时就产生,通过中间包的合理设计,控制合适的液面高度,在适当的位置安放挡墙和坝,减轻旋涡,卷渣带来的危害。
5.流动不稳定性和波的形成
在开浇时中间包液面升高或在换钢包和浇注末期中间包液面降低时,有液面升高或降低时,流速变化而导致表面波的形成;入口和出口条件变化,不稳定性导致表面波。
表面波的扩散,引起中间包钢渣界面的搅动而卷入渣子,对质量不利。
二、中间包流动形态控制
1.中间包无控制流动
(1)钢包注流带入大量空气,“沸腾作用”使中间包表面呈波浪运动,加剧了二次氧化。
(2)中间包底存在钢水停滞区,温度不均匀。
(3)由于有死区存在,中包容积未能充分利用,夹杂物不易上浮。
2.中间包控制流动
沿中间包宽度方向放置露出液面的挡墙,流体仅能从底部通道流过。
(1)挡墙的作用
A:
封闭钢包注流冲击区的紊流,防止表面卷渣,从底部通道流过的液体,分裂成两股回流,一个是沿中间包顶部的回流;另一个是向中间包边墙而流向水口,有利于夹杂物的上浮,加速液体的再循环。
B:
挡墙可消除中间包底部区域的死区。
C:
改善钢水流动的轨迹,使流动沿钢渣界面流动,缩短了夹杂物上浮距离,有利于渣子吸收。
(2)坝
中间包底部沿宽度方向砌一定高度的障碍物,有不同的形状和结构,与墙同时采用,减少了死区,平均停留时间比单用挡墙增加了2倍,比没有时增加了4倍,夹杂物可以充分地上浮。
缺点:
浇注结束时中间包和墙或坝之间保留一定量的钢水而不易清除。
三、中间包卷渣
1.中间包保持正常液位,钢包为敞开浇注,中间包内的流动特点是:
(1)沿钢-渣界面有剪切力作用把渣子卷入内部。
(2)注流冲击力引起液体表面波浪运动,液位下降时,这种剪切力和波浪造成的卷渣更严重。
2.中间包保持正常液位,采用长水口浇注,中间包内的流动特点:
(1)钢—渣界面流动剪切力减轻。
(2)减轻了由注流引起的波浪运动。
3.中间包卷渣的影响因素
(1)钢渣界面流动的剪切力和表面波。
(2)注流冲击区的紊流。
(3)低液位时水口上部形成的旋涡。
防止方法:
保持中间包