完整版某国产轿车制动系设计本科生毕业设计.docx
《完整版某国产轿车制动系设计本科生毕业设计.docx》由会员分享,可在线阅读,更多相关《完整版某国产轿车制动系设计本科生毕业设计.docx(38页珍藏版)》请在冰豆网上搜索。
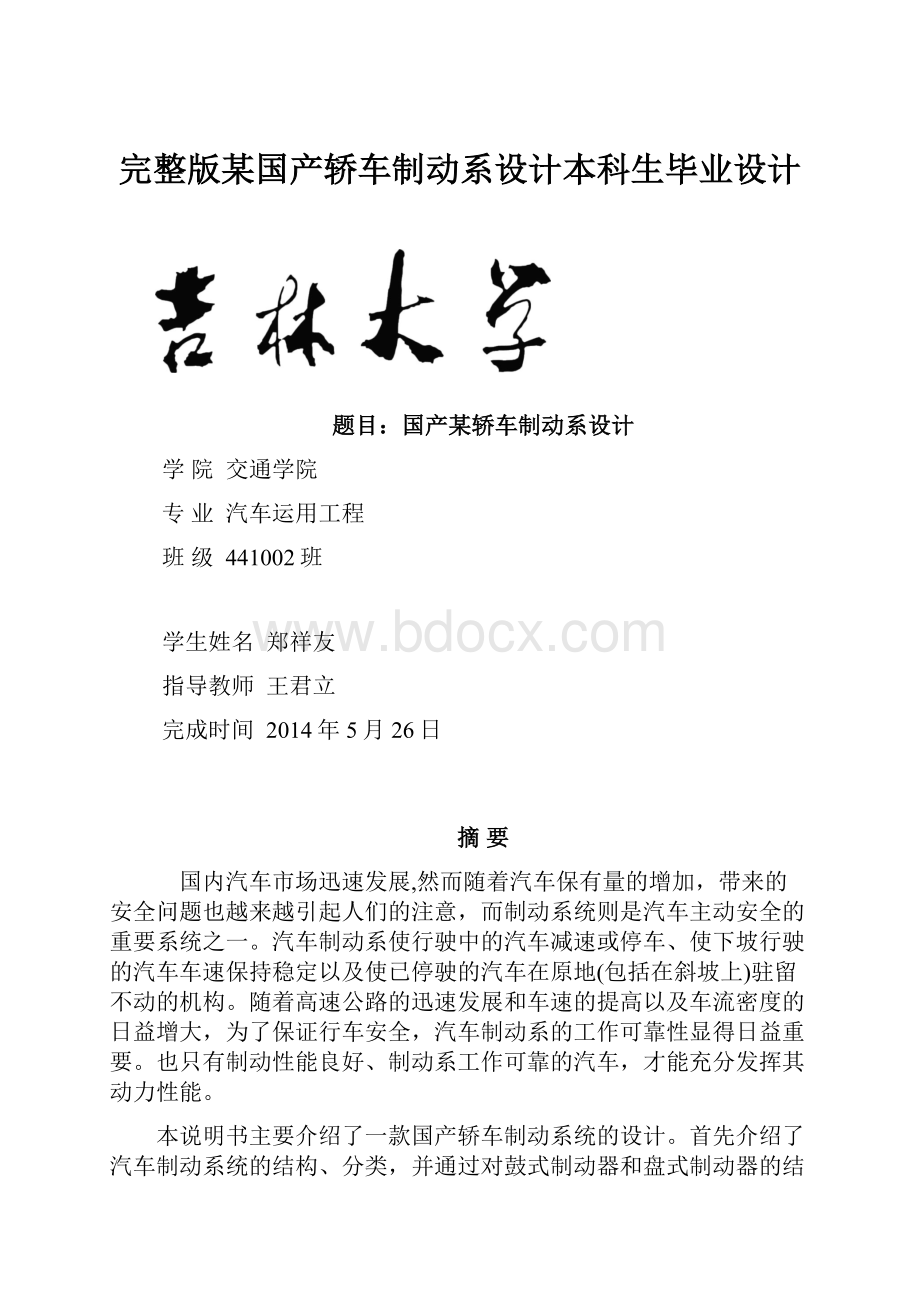
完整版某国产轿车制动系设计本科生毕业设计
题目:
国产某轿车制动系设计
学院交通学院
专业汽车运用工程
班级441002班
学生姓名郑祥友
指导教师王君立
完成时间2014年5月26日
摘要
国内汽车市场迅速发展,然而随着汽车保有量的增加,带来的安全问题也越来越引起人们的注意,而制动系统则是汽车主动安全的重要系统之一。
汽车制动系使行驶中的汽车减速或停车、使下坡行驶的汽车车速保持稳定以及使已停驶的汽车在原地(包括在斜坡上)驻留不动的机构。
随着高速公路的迅速发展和车速的提高以及车流密度的日益增大,为了保证行车安全,汽车制动系的工作可靠性显得日益重要。
也只有制动性能良好、制动系工作可靠的汽车,才能充分发挥其动力性能。
本说明书主要介绍了一款国产轿车制动系统的设计。
首先介绍了汽车制动系统的结构、分类,并通过对鼓式制动器和盘式制动器的结构及优缺点进行分析。
最终确定方案采用液压双回路前盘后鼓式制动器。
关键词:
制动、盘式制动器、鼓式制动器、设计参数、制动性能
ABSTRACT
Domesticautomobilemarketdevelopingquickly,however,withtheincreaseoftheautopossession,bringsecurityismoreandmoreattention,andbrakesystemistheimportantcaractivesafetysystemone.Thebrakeisamovingcarslowdownorstop,makethedownhillcarsspeedstabilityandmakealreadyinplaceofthecartheyoffend(includinginslope)stayfixedinstitution.Withtherapiddevelopmentofthehighwayspeedandtheimprovementoftrafficdensityandincreasesdaybyday,inordertoguaranteesafety,carbrakesystemreliabilityofworkappearincreasinglyimportant.Alsoonlybrakeperformanceisgood,brakesystemreliablecarandfullyplayitsdynamicperformancethismanualmainlyintroducesthedesignofthecarbrakesystemflyingacross.
Firstthispaperreviewedtheautomobilebrakingsystemstructure,classification,andthroughtothedrumbrakediscbrakeandthestructureandtheadvantagesanddisadvantagesareanalyzed.Ultimatelydeterminetheschemeadoptshydraulicdoublecircuitwithdiskanddrumbrakesystem.
Keywords:
brake、diskbrake、drumbrake、designparameters、brakingperformance
第1章绪论1
第1章绪论
1.1研究的目的和主要工作内容
人的生命和财产安全与轿车的安全性能息息相关,而轿车安全性的一个重要衡量标准标准是轿车的制动性能。
要保证轿车具有较高的制动性能前提是对车的制动系统进行可靠合理的设计。
本文研究对象为某国产轿车的制动系统,对轿车的制动系统建立模型,并在符合国家法规要求的前提下,计算和设计轿车制动系统相关参数。
主要工作内容包括以下几个部分:
(1)队国内外目前制动系统设计技术研究状况进行介绍,对制动系统设计的工作的具体内容以及可行性方法阐述分析。
(2)详细的说明了制动系统的各个组成部分结构型式以及各个组成部分的基本工作原理。
(3)对制动系统的功用进行了阐述同时对制动性能的评价方法进行了说明,阐述和归纳轿车制动系统设计要求并且对我国法规在轿车制动系方面的规定进行了说明。
(4)对汽车的制动曲线,理想制动力分配,前、后轴的制动力,利用附着系数和斜坡停车制动器的制动转矩和制动能力分析。
(5)选取某一轿车为设计对象,对其制动系统进行了设计计算,并分析研究计算结果,然后为了达到使轿车制动力分配、制动时减速度及斜坡驻车能力完全符合我国法规要求的目的进行结构参数调整。
1.2 国内外制动系统技术概况及可行性方法
国外汽车工业上世纪70年代就已进入自动化阶段,优化设计、计算机数字仿真、可靠性设计等一系列现代话设计方法取代了传统汽车设计方法。
进入21世纪以来,我国大力进行高级别公路建设,因此,轿车的行驶速度在不断提高,而且汽车保有量持续增加,所以现在对汽车特别是轿车制动性能的要求日趋严格。
中国现行的汽车制动性能要求标准以及法规政策正逐渐与国际接轨。
近年在汽车制动系统研究成果方面国内学者取得了丰硕的成果。
通常选取两方面对轿车制动系统进行设计:
首先是设计选取结构参数,其中包含确定制动力分配的过程;其次是预测分析整车制动性能。
布置多样、结构复杂、零部件多、计算方法差异大等是轿车制动系统特点,这些特点导致进行制动系统设计要做大量工作。
手工操作在传统的设计工作中是主要方式,为了使制动性能结果达到理想的效果,一般调整修改、试算的工作要进行多次,经过繁琐的工作最终才能得出与设计初衷相近的设计方案,然后还需要进行样车制动试验,再分析其主要参数和性能判别结果是否满足要求。
然而现在借助计算机进行设计工作,可以在最开始分析汽车制动性能、重要相关参数,这样既能保证数据的准确性而且工作简便迅捷,此外还能建立汽车制动过程中力以及稳定性的数学模型,模拟实际制动过程。
因此对于提高设计效率、提高工作结果的可视性、缩短新产品开发周期,特别是在提高整车制动性能方面计算机工具具有非常重的要意义。
第2章制动系统方案论证分析与选择
2.1 制动器形式方案分析及工作原理
几乎所有汽车都使用机械摩擦式制动器,这种制动器的工作原理是利用固定元件与旋转元件工作表面间的相互摩擦产生的制动力矩将动能转化为热能从而使汽车减速。
按其旋转元件的形状差异摩擦式制动器被分为鼓式和盘式两种。
使行驶中的轿车减速或停车,使轿车下坡时车速保持稳定以及使轿车在原地(包括在上下坡上时)驻留不动是制动系统的基本功用。
2.1.1鼓式制动器
如图2—1鼓式制动器工作原理图所示。
现对其结构及工作原理进行阐释。
由图2-1可以看出,金属制动鼓8的内圆柱面是其工作表面,它随车轮转动,因为它被固定在车轮的轮毂上。
制动底板11与车身相固结,所以是固定不动的。
有两个支承销12安装在制动底板上,两个弧形制动蹄10的下端与支承销连接,由支撑销支承着。
摩擦片9被安装在制动蹄两侧外圆柱面上。
制动轮缸6用油管5与制动主缸4连通,制动轮缸装在制动底板上,制动主缸安装在车架上,所以两者之间位置相对固定。
驾驶员通过踩踏制动踏板1,制动力经由主缸活塞3与推杆2相作用到主缸上继而传递到制动器上。
图2-1鼓式制动器工作原理示意图
1.制动力踏板2.推杆3.主缸活塞4.制动主缸5.液压油管6.鼓式制动器制动轮缸7.轮缸活塞8.制动鼓9.外侧摩擦片10.制动蹄片11.制动底板12.支承销13.制动蹄回位弹簧
为了不影响与制动鼓固定的车轮的自由旋转,在制动系不工作时,要求制动鼓的工作表面与制动蹄的外圆柱面间存在一定间隙,。
当制动时,制动踏板1被驾驶员踩下,推杆2推动主缸活塞3,制动主缸4内的制动液被强制压入制动轮缸6内,之后制动蹄被轮缸活塞推动绕支撑销转动,从而制动鼓8的内表面与摩擦片的工作表面相互接触。
之后,一个摩擦力矩在制动蹄10与相对其转着的制动鼓8之间产生。
制动鼓与车轮固结,所以这个摩擦力矩同样作用在车轮上,车轮和地面间存在附着作用,地面受到车轮一个向前的边缘力,同时车轮也受到地面对其产生的一个向后的反作用力,即制动力。
通过车轮、车桥等将制动力传给车架和车身,从而汽车产生一定的减速度,即制动系统发挥了作用。
当松开制动踏板时,制动蹄被回位弹簧13拉回原位,制动蹄与制动鼓之间产生间隙,摩擦力矩消失,同时地面与车轮之间的制动力也不再存在,即制动作用终止。
2.1.2盘式制动器
盘式可分为全盘式和钳盘式,分类依据是制动器摩擦片面积的不同。
而根据固定元件的差异,钳盘式制动器又可分为定钳盘式和浮钳盘式两种。
盘式制动器的各主要部件是制动盘、油缸、制动钳、油管等。
这种制动器的摩擦副是旋转工作的制动盘的端面和固定在车架上的制动块构成。
制动块由摩擦材料与其金属底板组和而成,制动块及其张紧装置装在制动钳中,制动钳横跨制动盘两侧。
固定在车轮上的制动盘随车轮转动。
油缸固定在制动器底版上,制动钳上有两个摩擦片,它们分别装在制动盘的两侧。
油管输来的液压作用压迫油缸的活塞,从而使摩擦片向制动盘运动,最终相接触而发生摩擦制动。
图2-2钳盘式制动器示意图
1.制动盘2.制动钳3.活塞4.油缸5.油管6.导向销7.车桥
2.2盘式制动器与鼓式制动器优缺
2.2.1盘式制动器的优点:
(1)热稳定性好。
摩擦助势作用在制动盘与摩擦衬块间不存在,因而摩擦因数对制动器效能稳定性的影响几乎可以忽略;此外,摩擦衬块的尺寸不大,产生的热量可以迅速排出。
(2)水稳定性好。
制动衬块作用在制动盘两侧较大的压力,能够使上面的水很快排出,同时制动盘高速旋转产生的离心力可以将水甩出,另外衬块可以经过一两次制动即可将制动盘上的水擦拭干净。
(3)相同结构尺寸和质量的制动器,盘式比鼓式的可以输出更大的制动力矩。
(4)制动盘在液压缸作用力方向上的热膨胀量很小,制动器间隙没有明显变化,制动稳定性好。
(5)间隙自动调整装置设计简便,易于修理更换。
(6)制动稳定性好:
制动过程中制动力矩的增长较缓,无增力作用,能保证较高的制动稳定性。
(7)汽车前进或者倒退对制动力矩没有影响。
(8)可以提高制动系统的可靠性与安全性,因为盘式制动器可以组成多回路制动系统,因而车轮制动平稳。
(9)磨损报警器检测量可以较直观准确的测得,故磨损过度时可以及时发现。
2.2.2盘式制动器也存在一些不足之处:
(1)尘污和锈蚀问题是大部分盘式制动器难以解决的问题。
(2)若后轮采用盘式制动器,驻车制动器要增加相当复杂的传动机构才可使用。
(3)需要安装液压伺服系统来提供额外的压力,来弥补盘式制动器无自增力,制动效能低的缺陷。
现在的轿车,多数采用四轮全盘式制动器,但是驻车制动若不是采用中央制动系统,在后轮的盘式制动器中要加装一个小的鼓式制动器(DIH,韩国车和日本车采用较多),用来提供驻车制动力。
此外货车和一部分低端轿车仍然采用鼓式制动器,故鼓式制动器的设计仍然具有研究价值。
第三章制动系统主要参数及其设计计算
3.1参考车型制动系相关主要参数数值
本设计选取的某国产轿车其前后轴采用的分别是浮钳盘式制动器和领从蹄鼓式制动器。
整车质量:
空载:
1210kg
满载:
1660kg
质心位置:
满载=1.356m空载=1.4m
质心高度:
空载:
=0.9m满载:
=0.8m
轴距:
L=2.656m
轮距:
轮距1.414/1.422m(前/后)
车轮工作半径:
390mm
轮毂尺寸:
6Jx14
轮胎:
195/60R14
3.2制动力及制动力矩分配系数
由汽车理论可知:
汽车制动时,若忽略路面对车轮滚动阻力矩和汽车回转质量的惯性力矩,则对任一角度ω>0的车轮,其力矩平衡方程为
-=0
式中:
—制动器的摩擦力矩,是作用在车轮上的由制动器施加的制动力矩,与车轮旋转方向相反,
—轮胎之间与地面的摩擦力,地面施加给车轮的制动力,又称地面制动力,与汽车行驶方向相反,N;
—车轮有效半径,m。
=
为制动器产生的制动力,它是动器摩擦力矩作用在轮胎周缘所产生的力,因此又称为制动周缘力。
方向与地面制动力的方向相反,当车轮角速度>0时,与相等,且的大小与其他因素无关,仅由制动器结构参数决定。
即制动器结构形式,尺寸,摩擦副的摩擦系数及车轮半径等决定着,并与制动系的液压压力成正比。
当踏板力增加是也增大,和同样随之增大。
但路面附着条件限制着地面制动力不能一直增加,不可能大于附着力,即
≤=Z
或
==Z
其中—地面与轮胎之间的附着系数;
Z—地面对车轮的法向反力。
当制动器制动力和地面制动力直线增加,当它们的值等于附着力值时,车轮会抱死拖滑,不再滚动。
抱死之后制动力矩即不再变化,表现为静摩擦力矩,而=/与相平衡,作为周缘力的极限值阻止车轮再旋转。
当制动到车轮角速度=0以后,地面制动力就不再增大,而由于踏板力增大使得制动器制动力继续上升(如图图3.1所示)。
图3.1制动器制动力,地面制动力与踏板力的关系
在汽车制动过程中,对整车进行受力分析,考虑到在制动时的轴荷略有转移,求得地面对前、后轴轮的法向反力,为:
Z1=
Z2=
式中:
G—汽车所受重力,N;
L—汽车轴距,mm;
—汽车质心离前轴距离,mm;
—汽车质心离后轴距离,mm;
—汽车质心高度,mm;
—附着系数。
取一定值附着系数=0.6;所以在空,满载时可得前后制动反力Z为以下数值
满载时:
前轮
=11245.5N
后轮
=5022.5N
空载时:
前轮
=8464.9N
后轮
=3393.1N
以上求得的法向反力结果如表3.1所示
表3.1汽车前后轴法向反力
车辆工况
前轴法向反力,N
后轴法向反力,N
汽车空载
8464.9
3393.1
汽车满载
11245.5
5022.5
汽车总的地面制动力为
=
式中q=—制动强度,亦称比减速度或比制动力;考虑到制动强度q=0.35以下的制动次数占总制动次数的90%以上,为安全考虑此处取制动强度q=0.5
—前后轴车轮所受的地面制动力。
故可推到出前后车轮附着力即地面最大制动力为
由已知条件可得得前、后轴车轮附着力为
故满载时:
前轮
=6453.3N
后轮
=3307.5N
空载时:
前轮
=4955.7N
后轮
=1891N
以上求得的前、后轴车轮附着力结果如表3.2所示
3.2前、后轴车轮附着力
车辆工况
前轴车轮附着力,N
后轴车轮附着力,N
汽车空载
4955.7
1891
汽车满载
6453.3
3307.5
表
可得分配系数
=
满载时:
满载时:
===0.69
空载时:
===0.73
在没有超出地面附着条件的前提下,地面制动力大小等于制动周缘力的大小,因此又称为制动力分配系数。
又由于满载和空载时的理想分配曲线非常接近,故应采用结构简单的非感载式比例阀,同时整个制动系应加装ABS防抱死制动系统。
3.3同步附着系数分析
(1)当时:
制动过程中只有前轮抱死或前轮先抱死,汽车基本上沿直线减速停车,这是一种稳定工况,但转向能力丧失了;
(2)当时:
制动过程中总是后轮比前轮先抱死,这时后轴容易发生侧滑而导致汽车失去方向稳定性;
(3)当时:
汽车前、后轮同时抱死,是一种稳定工况,但同样丧失了转向能力。
研究表明,当汽车在同步附着系数为的路面上进行制动时,其产生的制动减速度为,为制动强度。
前后制动器制动力分别等于各自的附着力,且它们的和等于附着力。
而在路面附着系数不是的路面上制动时,在前轮或后轮快要抱死时,制动强度,这说明了只有在的路面上,才可充分利用地面的附着条件。
取一附着系数值=0.6
3.4制动器制动力及制动力矩的计算
在忽略路面对车轮的滚动阻力矩和汽车回转质量的惯性力矩的条件下汽车达到最佳制动效果是所需的后轴和前轴的最大制动力矩为:
前轴最大制动力矩:
轮胎有效滚动半径:
re=195×60%+(14×25.4)/2=0.3m
后轴最大制动力矩:
即:
前轮双轮制动力
后轮双轮制动力
3.5制动强度和附着系数利用率
一条通过坐标原点斜率为的直线,它是具有制动器制动力分配系数的汽车的实际前,后制动器制动力分配线,简称线{。
线与I曲线交于一点,同步附着系数为线与I线交线处的附着系数。
它是汽车制动性能的一个重要参数,是由汽车结构参数所决定。
同步附着系数的计算公式是:
0=
满载时:
0==(2.6560.69-1.356)/0.8=0.6
空载时:
0==(2.6560.73-1.356)/0.9=0.65
则制动强度
满载时:
空载时:
附着系数利用率
满载时
空载时
3.6制动器制动力分配曲线分析
对于一般汽车而言,根据其前、后轴制动器制动力的分配、载荷情况及路面附着系数和坡度等因素,当制动器制动力足够时,制动过程可能出现如下三种情况:
1)前轮先抱死拖滑,然后后轮抱死拖滑。
2)后轮先抱死拖滑,然后前轮抱死拖滑。
3)前、后轮同时抱死拖滑。
所以,前、后制动器制动力分配将影响汽车制动时的方向稳定性和附着条件利用程度,是设计汽车制动系必须妥善处理的问题。
图5.1轿车制动力分配曲线
根据所给参数及制动力分配系数,应用MATLAB编制出制动力分配曲线如下:
当I线与β线相交时,前、后轮同时抱死。
当I线在β线下方时,前轮先抱死。
当I线在β线上方时,后轮先抱死[]。
通过该图可以看出相关参数和制动力分配系数的合理性。
3.7制动器制动因数
3.7.1前轮盘式制动效能因数
根据公式BF=2f
f——取0.5
前轮盘式制动器
BF=2×0.5=1.0
制动器大多使用摩擦系数的稳定值约为0.3~0.5的摩擦材料,少数会使用达到0.7的。
一般说来材料的耐磨性与材料的摩擦系数成反比。
当使用温度低于250℃时,国产的制动摩擦片材料可以保持摩擦系数f=0.35~0.40。
此处的盘式制动器摩擦材料摩擦系数选0.5,在接下来的鼓式制动器设计中其摩擦材料的摩擦系数取0.3。
第四章制动器结构参数
4.1后轮鼓式制动器参数
4.1.1制动鼓直径
若输入力F保持不变,则制动力矩和制动器的散热性能随制动鼓的直径变大而增大和变好。
但轮辋内径限制了制动鼓的直径的尺寸,且制动鼓直径的增大意味着制动鼓的质量也会随之变大,制动鼓固结在车轴上,如果质量增加则汽车非悬挂质量会变的很大,这将会使汽车的行驶平顺性变差。
同时为了便于散热,轮辋与制动鼓外表面之间的间隙应不小于20mm~30mm,这样轮胎因为轮辋过热而损坏的情况即可避免。
制动鼓的壁厚应该足够,这样可以保证制动鼓的刚度和热容量比较大,制动时的温升不会太大。
另外,为了保证加工精度,其直径越小越好,因为制动鼓刚度随其直径增大而减小。
故设计时通常规定制动鼓直径与轮辋直径的比值范围如下:
轿车=0.64~0.74
货车=0.70~0.83
专业标准QC/T309—1999《制动鼓工作直径及制动蹄片宽度尺寸系列》[]规定的制动鼓直径系列,如表3.3所示
3.3制动鼓工作直径及制动蹄片宽度尺寸系列
轮辋直径/in
12
13
14
15
16
制动鼓内径/mm
轿车
180
200
240
260
----
货车
220
240
260
300
320
该车轮辋直径=14*25.4=355.6mm
所以=227.584~263.144,故可取D=240mm
4.1.2制动蹄摩擦衬片包角ɑ和宽度b
摩擦衬片的使用寿命受摩擦衬片的宽度尺寸b的影响。
选取衬片宽度b较小的缺点是磨损速度快,则衬片寿命短;若选取的衬片宽度b较大,缺点是质量大,不易加工,并且成本增加了。
衬片的摩擦面积为=ɑb,其中为制动鼓半径。
制动时所受单位面积的正压力和能量负荷随制动器所有蹄片的摩擦总面积的增大而越小,从而磨损特性越好。
根据资料统计分析,如表3.4所示,汽车总质量越大单个车轮鼓式制动器的衬片面积越小。
表3.4制动器衬片摩擦面积
制动蹄摩擦衬片包角ɑ一般在β=90°~120°范围内选取。
另外有试验研究表明,若摩擦衬片包角取在90°~100°之间时,磨损最小,制动鼓温升最小,且产生的制动效果最好。
然而若包角ɑ<90°,则散热性变好,但由于接触面变小致使压强过高,磨损加剧;若包角ɑ过大,则会制动蹄摩擦衬片中间压强大,两端小,不仅导致单位压力效果减小,而且导致制动不平顺,故包角ɑ不可取的大于120º。
该设计取为100º。
本文研究车型总质量为m=1660kg=1.66t。
由上表可以分析得到,该车单个制动器总的衬片摩擦面积为=200~300。
由公式=ɑb可以得出,衬片宽度b=47.76~95.51cm。
专业标准QC/T309—1999《制动鼓工作直径及制动蹄片宽度尺寸系列》[]规定了制动器摩擦衬片的宽度系列如表3.5所示。
表3.5制动鼓工作直径及制动蹄片宽度尺寸系列
故摩擦衬片宽度可取b=75cm。
4.1.3摩擦衬片起始角
图3.3鼓式制动器的主要结构参数示意图
如图3.3所示,一般情况下,在制动蹄外周的中央装上摩擦衬片,所以摩擦衬片的起始角可由公式求得。
但是有时,在最大压力点两侧装置摩擦衬片,这样可以适应压强分布变化的情况,从而改善制动效能和磨损均匀性。
故该设计的摩擦衬片起始角=
4.1.4张力F的作用线到制动器中心的距离a
最大程度的增大张力F的作用线到制动器中心的距离a,可以把制动效能提高。
为了达到这个目的,要把制动轮缸布置在制动鼓内。
初步设计时常取距离a=0.8,故初步取a=0.8120=96mm。
4.1.5制动蹄支承销中心位置k和c
在两蹄支承端面不互相干涉的前提下,使c尽可能大而k尽可能小。
初步设计时,也可取c=0.8。
故c=96mm。
这里取k=20mm。
4.1.6后轮鼓式制动器效能因数
1)领蹄制动蹄因数:
图3.2鼓式制动器受力简化图
根据公式
h/b=2;c/b=0.8
得
2)从蹄制动蹄因数:
根据公式
得=0.48
所以这个领从蹄制动器的制动因数=1.27
4.2制动器主要结构元件设计
4.2.1制动鼓
选取热容量较大的材料制作制动鼓,防止温升超过材料极限,还要保证制动鼓的刚度,减少制动鼓变形对制动效果的影响。
同时为了确保高的摩擦系数,制动鼓材料应与摩擦衬片材料相匹配,这样工作表面磨损比较均匀使用寿命较长。
轮毂的圆柱表面与制动鼓配合定位,为了使这两者的轴线重合,要在两者装配紧固后对制动鼓内工