重沸器零部件的结构尺寸设计.docx
《重沸器零部件的结构尺寸设计.docx》由会员分享,可在线阅读,更多相关《重沸器零部件的结构尺寸设计.docx(22页珍藏版)》请在冰豆网上搜索。
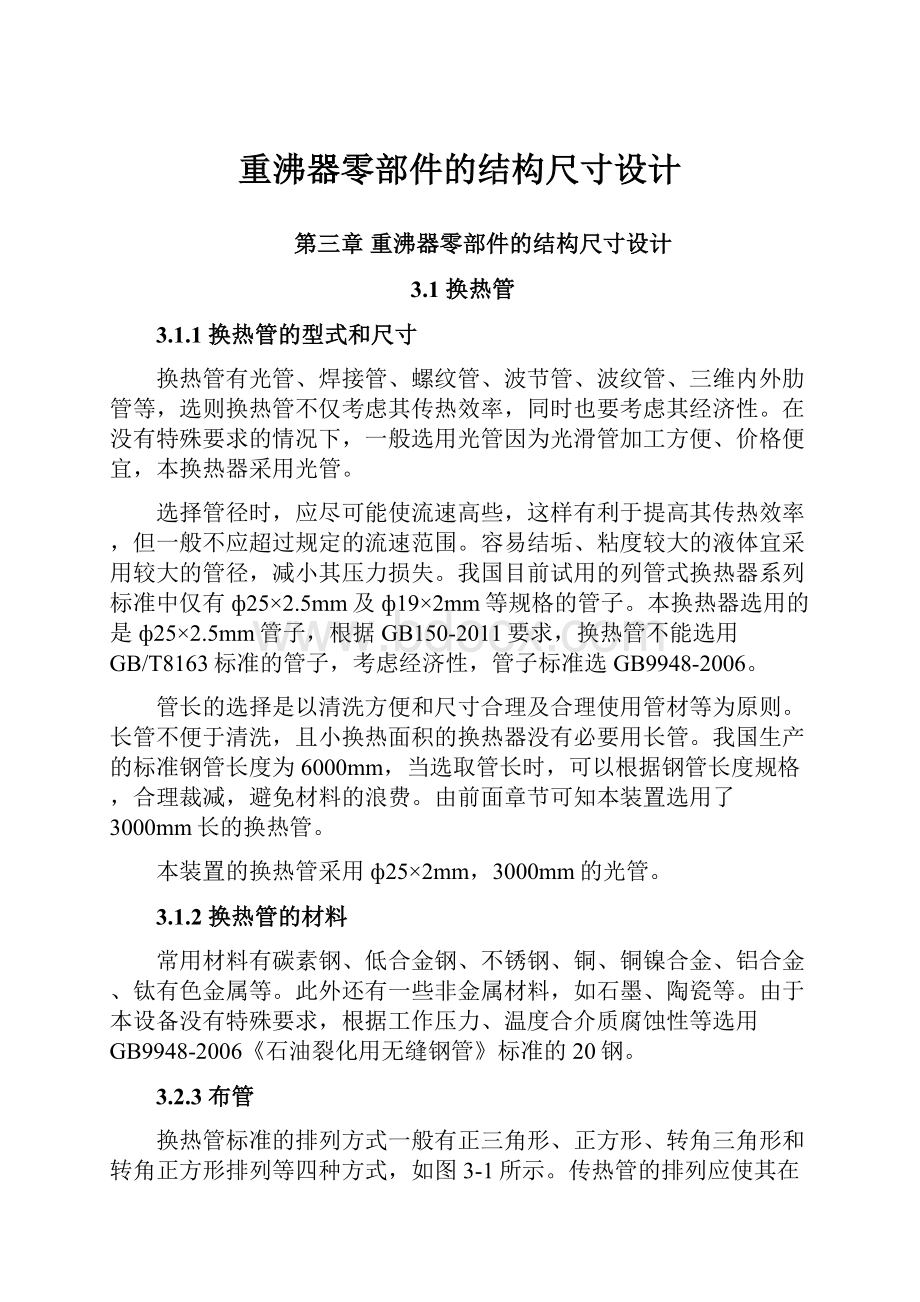
重沸器零部件的结构尺寸设计
第三章重沸器零部件的结构尺寸设计
3.1换热管
3.1.1换热管的型式和尺寸
换热管有光管、焊接管、螺纹管、波节管、波纹管、三维内外肋管等,选则换热管不仅考虑其传热效率,同时也要考虑其经济性。
在没有特殊要求的情况下,一般选用光管因为光滑管加工方便、价格便宜,本换热器采用光管。
选择管径时,应尽可能使流速高些,这样有利于提高其传热效率,但一般不应超过规定的流速范围。
容易结垢、粘度较大的液体宜采用较大的管径,减小其压力损失。
我国目前试用的列管式换热器系列标准中仅有ф25×2.5mm及ф19×2mm等规格的管子。
本换热器选用的是ф25×2.5mm管子,根据GB150-2011要求,换热管不能选用GB/T8163标准的管子,考虑经济性,管子标准选GB9948-2006。
管长的选择是以清洗方便和尺寸合理及合理使用管材等为原则。
长管不便于清洗,且小换热面积的换热器没有必要用长管。
我国生产的标准钢管长度为6000mm,当选取管长时,可以根据钢管长度规格,合理裁减,避免材料的浪费。
由前面章节可知本装置选用了3000mm长的换热管。
本装置的换热管采用ф25×2mm,3000mm的光管。
3.1.2换热管的材料
常用材料有碳素钢、低合金钢、不锈钢、铜、铜镍合金、铝合金、钛有色金属等。
此外还有一些非金属材料,如石墨、陶瓷等。
由于本设备没有特殊要求,根据工作压力、温度合介质腐蚀性等选用GB9948-2006《石油裂化用无缝钢管》标准的20钢。
3.2.3布管
换热管标准的排列方式一般有正三角形、正方形、转角三角形和转角正方形排列等四种方式,如图3-1所示。
传热管的排列应使其在整个换热器圆截面上可以均匀分布,同时还要考虑流体的性质,管箱结构及加工和制造等方面的问题。
其中正三角形排列最为普遍,其优点是:
在同一直径的管板上可以排列最多的管子数,而且管板的强度高;流体流动短路的机会少,壳程流体扰动大,因而对流传热系数较高;但是正三角形排列的换热管管外机械清洗较为困难,其用于壳程介质较清洁,可以进行化学清洗或者换热管外不需清洁的情况下。
正方形排列有利于换热管外壁的机械清洗,适用于壳程流体易产生污垢的场合;但是其在同样的管板面积上可排列的管子数量为最少。
此外还有同心圆排列方式,其优点是靠近壳体的地方管子分布较均匀,管子排列紧凑,在管板直径较小的换热器中可以排列的传热管数比三角形排列还多。
考虑到本重沸器要排列的管子较多,流体的性质属于比较洁净和不易结垢,因此采用正三角形排列,如图3-1(a)所示。
图3.1-1管子的排列方式
换热管中心距确定,管心距的大小主要与传热管和管板的连接方式有关,以及是否有分程隔板等,此外还要考虑到管板强度和清洗管外表面时所需的空间。
根据GB151-1999规定管心距S不小于1.25倍换热管外径,所以有S=1.25d=1.25X25=31.25mm,取32mm。
3.2管板结构尺寸
管板在换热器的制造成本中占有相当大的比重,近年来也有不少对薄管板进行研究以节约成本。
管板设计与管板上的孔数、孔径、孔间距、开孔方式以及管子的连接方式有关。
1、选用固定管板兼作法兰形式的管板,
图3.2-1固定管板式换热器管板尺寸
这种管板结构尺寸的确定先按第二章确定的壳体内径,在依据确定的设计压力,壳体内径和压力等级来设计法兰,然后根据法兰相应结构尺寸确定管板的最大外径,密封面位置、宽度、螺栓直径、位置、个数等,根据上述确定的壳体内径D=1000mm和设计压力PN=0.7MPa,由JB/T4702-2000选择PN1.6乙型平焊法兰,从而确定管板尺寸如图3-9所示,管板重量209kg。
2、管板孔直径和允许公差,由GB151-1999的表4-17的管孔直径为25.4,允许偏差为
3、管板材料
在选择管板材料时,除力学性能外,还应考虑管程和壳程流体的腐蚀性,以及管板和换热管之间的电位差对腐蚀的影响,此装置管板材料采用16MnⅢ三级锻件。
3.3折流板
列管式换热器的壳程流体流通截面积大,若不加折流板,其壳程流体很难进行有效的湍动。
在壳程流体属对流传热条件时,为增大壳程流体的流速,加强其湍动程度,提高其表面传热系数,需要设置折流板。
而折流板又有横向折流板和纵向折流板两类,单壳程的换热器仅需设置横向的折流板,横向折流板同时兼有支撑板的作用,还可以款热管防止产生振动作用。
管壳式换热器常用的有弓形和盘环形。
在弓形折流板中,流体在板间交错的冲刷管子,而流经折流板弓形缺口时又是顺流经过管子外面后进入下一板间,改变方向,流动中死区很少,即使有死区,要会通过导流筒进行有效的导流,所以比较优越,结构比较简单,一般标准换热器中只采用这种。
盘环形折流板制造和安装都不方便,流体在管束中为轴向流动,效率较低。
而且要求介质必须是清洁的,否则沉淀物将会沉积在圆环后面,从而使传热面积失效,此外,如有惰性气体或溶解气体释放出来,它不能有效地从圆环上部排出,所以一般用于压力比较高而又清洁的介质。
由于本设备直径不大,采用采用单弓形折流板。
3.3.1折流板的主要几何参数
取弓形折流板圆缺高度为壳体内径的25%,则切去的圆缺高度为h=0.5x1000=250(mm)。
取折流板间距B=0.5D,则
B=0.5X1000=500(mm)
折流板数:
图3.3-1折流板几何参数
3.3.3折流板与壳体间隙
折流板外边缘与壳体内径之间的间隙越小,壳程流体介质在此处的泄漏越小,使传热效率提高,但时间隙越小,给制造、安装带来困难。
参考GB151-1999表41选取折流板名义外直径D=DN-6=1000-6=994mm。
3.3.4折流板厚度
折流板厚度与壳体直径、换热管无支承长度有关,其厚度根据GB151表34,δ≥12mm。
取16mm。
3.3.5折流板的管孔
①、折流板的管孔直径和公差按GB151-1999规定,Ⅰ级管束折流板管孔直径为d+0.7=25+0.7=25.7mm,及允许偏差为
②、管孔中心距折流板上管孔中心距t=32,公差为相邻两孔
,允许4%相邻两管孔中心距偏差±0.5mm;任意两孔中心距偏差±1mm
③管孔加工折流板上管孔加工后两端必须倒角0.5X45°。
3.3.6材料的选取
设计温度170℃、由于折流板不是受压元件,选取Q235-B钢板。
3.4拉杆、定距管
3.4.1拉杆的结构形式
折流板与支持板一般均采用拉杆与定距管等元件与管板固定,其固定方式有如下几种:
a.焊接方式,如图3-2(c)拉杆一端插插进管板孔并与管板焊接,每块折流板间距固定后再把其与拉杆焊接固定。
常用于拉杆与折流板为不锈钢结构或换热管外径≤14mm的管束。
b.采用拉杆定距管的结构,拉杆一端用螺纹螺孔的方式与管板连接,每两块折流板之间的间距用定距管控制,每根拉杆上最后一块折流板与拉杆焊接如图3-2(d);也可以是最后一块折流板用两个螺母锁紧固定,这种形式易于调节折流板之间夹紧程度,在穿进换热器后,各折流板都处于相对自由状态,是列管换热器最常用的形式如图3-2(b)所示。
c.螺纹与焊接相结合,如图3-2(a)拉杆一端用螺纹螺孔与管板连接,然后将每块折流板焊在拉杆上,同样不需要定距管,适于换热管外径≤14mm的管束。
d.定距螺栓拉杆,如图3-2(e)是依靠一节节定距螺栓将折流板夹持而达定距及固定折流板的目的。
定距螺栓分为A、B两种形式,A型是与管板连接的定距螺栓,其两端均为螺纹,B型是两折流板之间采用的,其一端是螺栓,另一端是螺母,该结构安装简单又方便,间距精确。
换热器直径小于等于1000mm时,每台换热器只用两根拉杆固定即可。
图3.4-1拉杆的结构形式
考虑到制造难度和经济性,本装置的换热管外径为25mm,换热器直径为1000mm,根据上述所说选用拉杆定距管结构。
3.4.2拉杆尺寸和数量
①、拉杆直径和数量根据GB151-1999规定,拉杆直径d=16mm,拉杆数量可取为10根。
②、拉杆尺寸、公差和表面粗糙度根据折流板的间距可以确定拉杆的长度,其具体尺寸如图所示
拉杆I结构尺寸及公差
图3.4-2拉杆II结构尺寸及公差
3.4.3拉杆的布置
拉杆应尽量均匀布置在管束的外边缘。
拉杆位置占据换热管的位置,本换热器拉杆的布置位置参见管板的拉杆孔位置。
3.5定距管
定距管的尺寸根据折流板的间距而定,第一块折流板与管板之间距离520mm,折流板间距616mm,拉杆数量10根,折流板数量4块,由此可计算的需要520mm定距管8根,1216mm定距管4根,600mm定距管18根,1136mm定距管2根。
定距管采用φ25×3管子,材料选用20钢。
由于定距管属于非受压元件,所以选用标准无特殊要求。
3.6防冲板
为了防止壳程物料进口处流体对换热管表面的直接冲刷,引起侵蚀及振动,在必要时应在流体入口处装置防冲板,以保护换热管。
设置防冲板或导流筒时,接管处圆筒脮表面与防冲板或导流筒表面之间介质通过的面积需要大于壳程进出口处的流道面积;壳程进出口处设置防冲板时,至少要为管束进出口处流道面积为折流板与管板或折流板之间距内换热管之间的通道面积减去防冲板的投影面积。
管程防冲板设置的条件是流速超过3m/s,设置防冲板可以减小管板冲蚀。
壳程设置防冲挡板的条件是,对于非腐蚀的的流体
。
对其他流体
1、壳程进口防冲挡板
本换热器是一再沸器,
防冲板在壳体内的位置,应使防冲板周边与壳体内壁所形成的流通面积为壳程进口接管截面积的1~1.25倍。
壳程进口防冲板规格取325mm×380mm。
根据GB151-1999规定,防冲板的固定形式有A)防冲板的两侧焊在定距管或拉杆上,也可同时焊在靠近管板的第一块折流板上;B)防冲板焊在圆筒上;C)用U形螺栓将防冲板固定在换热器上。
本装置才用防冲板焊在定距管上。
其结构如图所示:
图3.6-1壳程进口防冲挡板结构尺寸
根据GB151-1999规定,防冲板的最小厚度:
当壳程进口接管直径小于300mm时,对碳钢、低和金钢取4.5mm;对不锈钢取3mm。
当壳程进口接管直径大于300mm时,对碳钢、低合金钢取6mm;对不锈钢取4mm.本装置的壳程进口接管直径为325mm大于300mm,因为不是受压元件,防冲板的材料选为Q235-B,厚度取6mm。
2、管程进口防冲挡板
流速超过3m/S,应设置防冲板,防冲板外径大于接管外径50mm以上,接管外径219mm,取防冲板外径φ280,采用支筋支撑,直接焊接在封头上,高度取97mm,大于
d接管符合最小流通截面积的要求,其中支筋采用100mm的φ8钢条,挡板厚度取6mm。
其具体结构尺寸见图示。
图3.6-2管程防冲挡板结构尺寸
3.7接管和法兰的选用
3.7.1接管和法兰的要求
根据GB151-1999的要求
①.接管(含内焊缝)不允许凸出壳体内表面,并在该部位打磨平滑,以免妨碍管束的拆装。
②.接管应该尽管沿径向或轴向布置,(4管程的例外)以方便配管与检修。
③.设计温度在300℃以上时,不允许使用平焊法兰,必须采用整体法兰。
④.对利用接管(或接口)仍不能放气和排液的换热器,应在管程和壳程的最高点设置放气口,最低点设计排液口或排污口,其最小公称尺寸为20mm。
本装置选用DN20管子。
⑤.操作允许时,一般是在高温、高压或不允许介质泄漏的场合,接管与外部管线的连接也可采用焊接形式。
由于本装置压力温度较高高,介质易燃易爆,所以都采用带颈对焊法兰连接。
⑥.必要是可设置温度计接口、压力表及液面计接口。
3.7.2接管高度(伸出长度)确定
接管伸出壳体外壁的长度,主要考虑法兰形式,焊接操作条件,螺栓拆装,有无保温及保温厚度等一系列原因因素决定。
一般最短应符合下式计算值
l≥h+h1+δ+15(mm)
式中:
h――接管法兰厚度,mm;
h1――接管法兰的螺母厚度,mm;
δ――保温层厚度,mm;
l――接管安装高度,
根据公式,及参考HG/T20583《化工容器结构设计规定》,考虑到接管外观和规格同一,外伸长度都取为200mm。
其接管长度
由此计算可算得接管b、e管子(即装配图中件10)长度158mm。
接管c即件(15-3)长度130mm.
3.7.3接管位置最小尺寸
壳程接管位置最小尺寸见图3-5,按下式估算:
无补强圈L1≥do/2+(b-4)+C
管程接管最小尺寸见图3-6,按下式估算:
无补强圈L1≥do/2+hf+C
为考虑焊缝影响,一般取C≥3倍壳体壁厚且不小于50~100mm。
有时壳径较大且折流板间距也很大,则L1值在设计时尚应考虑第一块折流板与管板的间距,以使流体分布均匀。
经过计算,得接管高度和位置尺寸如下:
表3.7-1接管工艺安装尺寸
循环液进/出口
导热油进/出口
排气口
排污口
外伸高度l/mm
200
200
200
位置尺寸L1/mm
\
300
见装配图节点
见装配图节点
材料
20
20
20
20
3.7.4排气,排液管
为提高传热效率,排除或回收工作残液(气),凡是不能借助其他接管排气和排液的换热器应在其壳程和管程的最高,最低点,分别设置排气、排液接管,其接管的端部必须与壳体或管箱壳体内壁平齐。
对高压立式换热设备中壳程的排气、排液口采用在管板上开设不小于16mm的孔,但是这种结构制造不方便,且堵塞后不易清洗。
一般用于压力温度较高和较为清洁的场合。
另一种方式就是设置齐平管进行排液和排气,不然易堵塞而又不易清理。
由于此设备压力不高,可设置齐平接管作为排气和排污管。
齐平接管的结构尺寸如图所示。
图3.7-1齐平接管与筒体法兰连接结构
图3.7-2齐平接管尺寸结构
3.8管箱
管箱的作用是把由管道流入的管程流体均匀分布到各传热管,把管内流体汇集在一起再送出换热器。
在多管程换热器中,管箱还起到改变流体流向的作用。
无论那一种管箱,其管箱的最小内侧深度应当满足这样的要求:
使连接双程间流体流动的横截面至少大于或等于单管程通过的截面。
3.8.1管箱结构形式
(1)、A型(平盖管箱)如图3-8(a)装有管箱平盖(或称盲板),清洗管程时只要拆开盲板即可,而不必拆卸整个管箱和与管箱相连的管路,缺点是盲板结构用材多,且尺寸较大是得用锻件,耗费大量机加工时,提高制造成本,并增加一道密封的泄漏可能。
一一般多用于DN<900mm的浮头式换热器中。
(2)、B型封头管箱型如图3-8(b),用于单程或多程管箱,优点是结构简单,便于制造,适于高压,清洁介质,可省掉一块造价高的盲板、法兰和几十对螺栓,且椭圆封头受力情况要比平端盖好的多,缺点是检查管子和清洗管程时必须拆下连接管道和管箱。
(3)、C型、N型管箱这种形式是管箱一端与壳体及管板连成一体,或是用于可拆管束与管板制成一体的管箱,另一端可采用A型结构,减少了泄漏的可能性。
一般用的较少,只在高压情况下采用。
本装置的管箱选用d型封头管箱。
3.8.2管箱结构尺寸
管箱法兰通采用长颈法兰,管箱所要确定的尺寸主要是管箱长度,分程隔板位置尺寸是由排管图确定,管箱直径是由壳程直径决定。
表3.8-2管箱结构尺寸表
长度L/mm
直径D/mm
厚度δ/mm
材料
进口管箱
266
1000
16
Q345R
出口管箱
266
1000
16
Q345R
具体结构尺寸见零件图
3.9筒体尺寸
壳程筒体内径1000mm,介质没有特殊要求,采用Q345R材料,材料标准为GB713-2008,其钢板的厚度负偏差为0.3mm,壳程筒体其长度为:
H=换热管长度-换热管伸出管板长度X2-管板厚度X2-焊缝宽度X2
=3000-2X2-44X2-2X2
=2904mm
筒体的壁厚在后面章节中强度计算确定。
管箱筒节考虑到法兰标准中的规定,与相应法兰连接的同节壁厚为16mm;长度由法兰标准定。
3.10封头的选用
压力容器封头的种类很多,分为凸形封头、锥壳、变径段、平盖及紧缩口等,其中凸形封头包括半球形封头、椭圆形封头、碟形封头和球冠形封头。
每种封头各有优缺点,采用什么样的封头要根据工艺条件的要求、制造的难易程度和材料的消耗等情况来决定。
a)、半球形封头,在均匀内压作用下,薄壁球形容器的薄膜应力为相同直径圆筒的一半,其受力是最好的,故从受力分析来看,球形封头是最理想的结构形式。
但缺点是曲面深度大,直径小时,整体冲压困难,大直径采用分瓣冲压其拼焊工作量也较大。
半球形封头常用在高压容器上可以节约材料,但是会增加制造费用。
b)、椭圆形封头是由半个椭球面和直边组成,由于封头的椭球部分经线曲率变化平滑连续,故应力分布比较均匀,且椭圆形封头深度较半球形封头小得多,易于冲压成型,标准椭圆形封头是目前中、低压容器中应用较多的封头之一。
c)、碟形封头是带折边的球面封头,该边缘弯曲应力与薄膜应力叠加,使该部位的应力远远高于其他部位,故受力状况不佳。
但过渡环壳的存在降低了封头的深度,方便了成型加工,而且压制碟形封头的钢模加工简单,制造成本很低,使碟形封头的应用范围较为广泛。
d)、锥壳,轴对称锥壳可分为无折边锥壳和折边锥壳,根据GB/T25198有30o和60o两种,由于结构不连续,锥壳的应力分布并不理想,但其特殊的结构形式有利于固体颗粒和悬浮或粘稠液体的排放,有时封头小端可以接管连接,从而避免了接管开孔补强,它可作为不同直径圆筒的中间过渡段,在中、低压容器中使用较为普遍。
对受均匀内压封头的强度计算,由于封头和圆筒相连接,所以不仅需要考虑封头本身因内压引起的薄膜应力,还要考虑与圆筒连接除的不连续应力。
但在常规设计中一般只考虑其薄膜应力,以较大的安全系数进行控制。
3.9.1封头尺寸
设计依据GB150-2009《压力容器》
GB/T25198-2010《压力容器封头》
为了制造的方便,采用椭圆形封头。
设计温度170℃,设计压力P=1.32MPa,选用Q345R,材料在设计温度下的的许用应力[σ]t=183MPa取焊缝系数ф=1。
腐蚀裕度C2=2mm.
符合GB150-1998规定标准椭圆形封头的有效厚度应不少于封头内直径的0.15%且大于3mm,满足最小厚度要求。
设计温度下圆筒的最大允许工作应力:
压力校核合格。
封头型号EHA1000X10(8.5),公称直径1000,总深度275mm,直边高度H1=25mm,内表面积1.1625m2,容积0.15m3,封头质量90.5kg。
前端管箱和后端管箱采用同一型号封头。
3.11法兰
3.11.1法兰结构类型
法兰的基本结构形式按组成法兰的圆筒、法兰环及锥颈三部分的整体性程度可分为松式法兰、整体法兰和任意式法兰三种形式。
1)、松式法兰:
指法兰不直接固定在壳体上或者虽固定而不能保证与壳体作为一个整体而承受螺栓载荷的结构。
适用于有色金属和不锈钢制设备或管道上,这样法兰可采用碳素钢钢板制作,以节约贵重金属。
但法兰刚度小,厚度较厚,一般只适用于压力较低的场合。
2)、整体法兰:
将法兰于壳体锻或铸成一体或经全熔透的平焊法兰,这种结构能保证壳体与法兰同时受力,其强度更高,使法兰厚度可适当减薄,但会在壳体上产生较大应力。
其中,带颈法兰可以提高法兰与壳体的连接刚度,适用于压力、温度较高的重要场合。
3)、任意式法兰:
从结构来看,这种法兰与壳体连成一体,但刚性介于整体法兰和松式法兰之间,这类法兰结构简单,加工方便,故在中低压容器或管道中得到广泛应用。
3.11.2管法兰
管法兰的要求:
a)、凹凸和榫槽密封面的法兰,密封面向下的,一般应选用凸面或榫面,其他朝向的,则设计成凹面或榫面,且在同一设备上必须成对使用。
b)、结构法兰螺栓通孔不应和壳体主轴中心线相重合,应对称地分布在在主轴中心线两侧,称之为跨中布置法兰螺栓孔。
根据换热器的公称直径、公称压力、工作温度、工作介质特性以及法兰的材料,按HG/T20592-2009《钢制管法兰(PN系列)》选取,考虑本装置介质温度较高,选用带颈对焊法兰,其规格WN20(B)-16RFS=4mm,WN300(B)-16RFS=10mm,WN200(B)-25RFS=8mm。
3.11.3管箱法兰
选取乙型平焊法兰,设计压力1.32MPa,公称直径DN=1000mm,有前面章节可知,其结构尺寸如图3-12所示,尺寸数据见图中标注。
图3.11-1法兰结构及尺寸
3.12垫片的选取
设备垫片主要有:
非金属软垫片、缠绕垫片和金属包垫片。
根据JB/4704-7规定,一般非金属软垫片适用于甲型平焊法兰、乙型平焊法兰、长颈对焊法兰,法兰密封面形式为光滑密封面或凹凸密封面。
缠绕垫片适用于乙型平焊法兰、长颈对焊法兰,法兰密封面形式为光滑密封面、凹凸密封面及榫槽密封面。
而金属包垫片适用于乙型平焊法兰和长颈对焊法兰,法兰密封面形式为光滑密封面、凹凸密封面及榫槽密封面。
垫片的选取要综合考虑操作介质的性质、操作压力、操作温度以及需要密封的程度;而对垫片本身要考虑垫片性能,压紧面的形式,螺栓的大小以及拆装后复用的次数。
中温,中压毒性程度较低的介质可采用金属与非金属组合式或非金属垫片。
本装置容器法兰用垫片采用缠绕垫,根据JB/T4705-2000选取B22-1000-1.6型号,其金属带材料为0Cr18Ni9,填充带材料为柔性石墨。
接管法兰垫片不属于本压力容器设计范围,故不用考虑。
3.13支座的选取
对于立式容器来说,一般采用群座、腿式支座、支承式支座和耳座。
群座一般用于高径比大于5的设备。
考虑外接管线对换热器的影响,此设备采用耳式支座。
耳式支座是由底板、筋板和垫板组成,如图3-14所示。
当容器的DN≤900mm,且筒体的有效厚度δe>3mm,筒体材料又与支座材料相同或相近时,也可不要垫板,此设备DN=1000mm,需设置垫板。
根据JB/T4712.3-2007选用B型带垫板的结构,初选支座号4,支座筋板和底板材料选用Q345R。
此型号支座本体允许载荷[Q]=90KN,适用容器公称直径DN=1000~2000mm,高度H=250mm,底板l1=200mm,b1=140mm,δ1=14mm,S1=70mm,筋板l2=290mm,b2=140,δ2=10mm,垫板l3=315mm,b3=250,δ3=8mm,e=40mm,螺栓d=30,螺纹M24,支座质量15.7Kg。
3.14支撑选用
耳式支座的支撑一般有钢框架支撑,水泥基础支撑,钢结构支撑等,本装置重量较小,采用槽钢支撑,支撑高度由耳座的安装位置和最下端接管的离地高度确定,其具体尺寸见零件图SCU-EQ-E106-2所示。
3.15吊耳设计
在设备安装和检修的时候都需要对设备进行吊装,设置吊耳非常重要,吊耳种类较多,有侧壁式吊耳、轴式吊耳、而式吊耳等。
侧壁吊耳不能安装在有法兰的设备上,轴式吊耳适用于重量较大、长度较长的长容器上,本设备直径和重量较小,可设置耳式吊耳。
其结构尺寸见图。
吊耳结构尺寸
由于此吊耳仅作为安装时吊装上管箱所用,其受力情况不是很苛刻,所以不用加垫板,对其强度结构设计要求也不高,其安装尺寸见装配图SCU-EQ-E106-1所示。
3.16其他零部件的结构尺寸设计
A)拉筋的设置
由于f接管外伸较长,且带有弯曲部分,其自重所产生的弯矩较大,对连接处的筒体影响较大,为减小其对筒体的弯矩,以及防止接管的水平度,在此接管上设置拉筋,原则上拉筋应尽量焊接在远离力矩中心的地方,但是考虑法兰的焊接和螺栓的安装等