原位合成熔铸法制备TiC颗粒增强Cr钢基复合材料显微组织性能及工艺研究可编辑.docx
《原位合成熔铸法制备TiC颗粒增强Cr钢基复合材料显微组织性能及工艺研究可编辑.docx》由会员分享,可在线阅读,更多相关《原位合成熔铸法制备TiC颗粒增强Cr钢基复合材料显微组织性能及工艺研究可编辑.docx(41页珍藏版)》请在冰豆网上搜索。
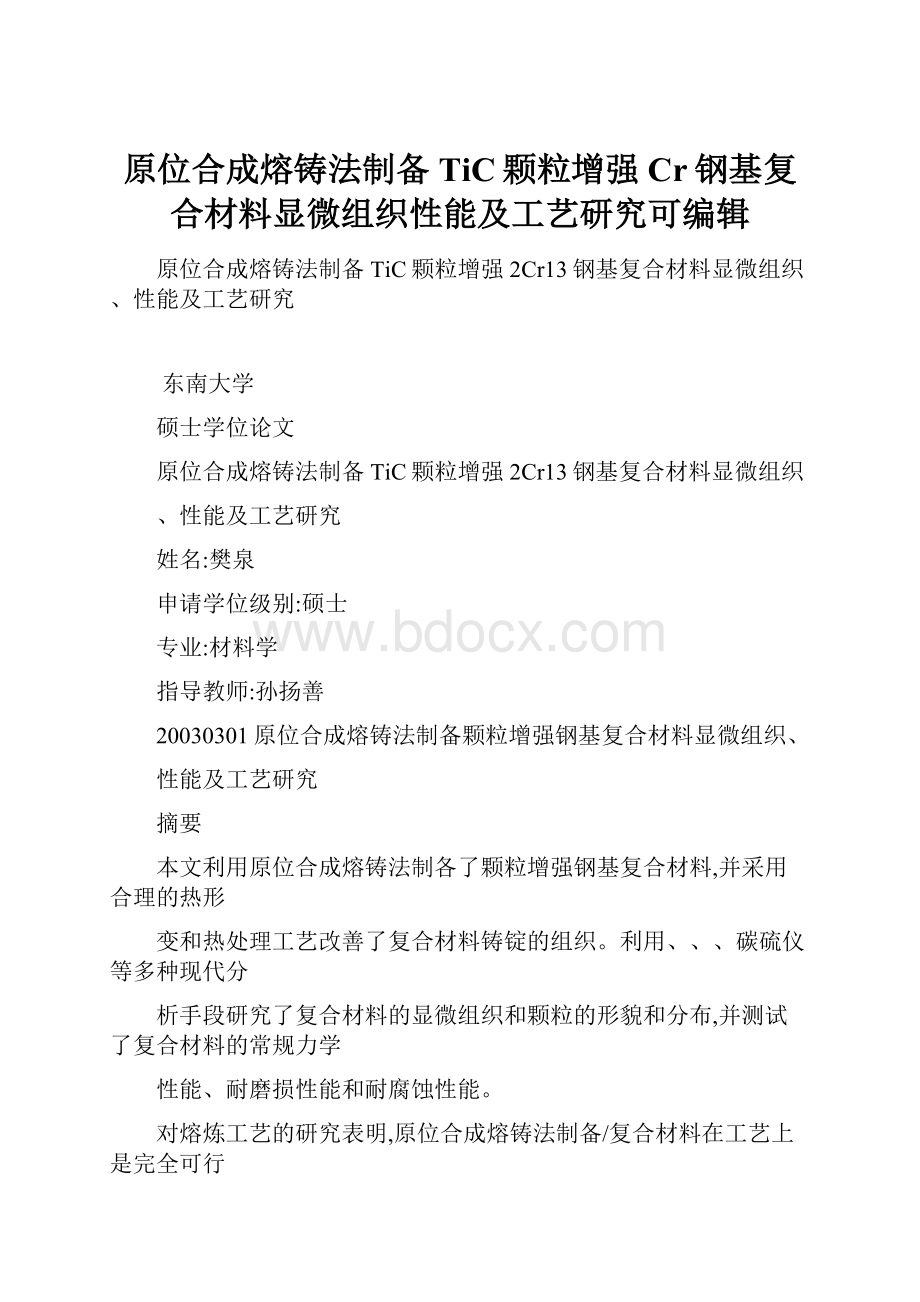
原位合成熔铸法制备TiC颗粒增强Cr钢基复合材料显微组织性能及工艺研究可编辑
原位合成熔铸法制备TiC颗粒增强2Cr13钢基复合材料显微组织、性能及工艺研究
东南大学
硕士学位论文
原位合成熔铸法制备TiC颗粒增强2Cr13钢基复合材料显微组织
、性能及工艺研究
姓名:
樊泉
申请学位级别:
硕士
专业:
材料学
指导教师:
孙扬善
20030301原位合成熔铸法制备颗粒增强钢基复合材料显微组织、
性能及工艺研究
摘要
本文利用原位合成熔铸法制各了颗粒增强钢基复合材料,并采用合理的热形
变和热处理工艺改善了复合材料铸锭的组织。
利用、、、碳硫仪等多种现代分
析手段研究了复合材料的显微组织和颗粒的形貌和分布,并测试了复合材料的常规力学
性能、耐磨损性能和耐腐蚀性能。
对熔炼工艺的研究表明,原位合成熔铸法制备/复合材料在工艺上是完全可行
的。
熔体中的和在高温下发生原位合成反应,可以在基体中形成稳定存在的颗粒。
铬元素、钛元素和颗粒的含量基本到位。
本文采用的生产性工艺。
可以在大气中大炉量
地制备颗粒分布均匀的复合材料。
对复合材料的热变形和热处理工艺的研究表明,锻、轧等热形变工艺和均匀化退火、淬
火回火等热处理工艺可以在很大程度上的改善基体的组织,从而提高复合材料的性能。
空冷
淬火和油冷淬火均可使基体获得马氏体组织。
随着回火温度的降低,复合材料的强度和硬度
提高,塑性下降。
在温度范围回火时,基体会出现回火脆性。
随着回火温
度的变化,复合材料的耐磨损性能无大的变化。
对复合材料显微组织的研究表明,当颗粒的含量为%和%、预制块中钛碳
原子比为:
和时,颗粒在基体中分布均匀,与基体结合良好,界面干净,具有很
高的热稳定性。
颗粒大小在左右,呈现为不规则多边形状。
高温℃回火
后,复合材料的组织为细小均匀的回火索氏体上分布着颗粒。
低温℃、回
火后,基体的组织则为回火马氏体。
当颗粒的含量达到%,预制块中钛碳原子比达
到:
时,基体中的颗粒发生了一定程度的团聚。
高温℃回火后,复合材料的
显微组织除了回火索氏体和颗粒外,还有因偏析形成的莱氏体和块状碳化物,以及大量
细小弥散的析出碳化物。
对复合材料常规力学性能的研究表明,颗粒的引入提高了基体的室温抗拉强度和屈
服强度。
本文中以引入%、预制块中钛碳原子比为:
的复合材料的强度最高,但塑
性和韧性有一定程度的下降。
当颗粒的含量为%和%、预制块中钛碳原子比为
:
和:
时,复合材料的塑性和韧性下降幅度不大。
对复合材料耐磨损性能的研究表明,颗粒的引入极大地减少了基体产生犁沟和显微
切削的几率,使得复合材料的耐磨损性能较之基体有了显著的提高。
对复合材料耐腐蚀性能
的研究表明,在本文的腐蚀试验条件下,复合材料的耐腐蚀性优于基体。
随着颗粒含量
和预制块中碳量的增加,复合材料的耐腐蚀性能下降。
啊含量在%%范围内、预制块中钛碳原子比在:
到:
范围内的复合材料配
比是合理的、成功的。
将复合材料的热处理工艺定为℃油淬,℃回火可以使复合材
料的硬度、韧性、耐蚀性、耐磨性等性能最好的满足刀口材料的使用要求。
在本文的磨损试
验条件下,不同热加工、热处理状态下的%:
复合材料的耐磨损性能都明显优于硬
质合金。
关键词:
不锈钢复合材科显微组织常规力学性能耐磨损性能耐腐蚀性能?
士●?
蛾
耶/..
币
..,
,.,幛.
他
,..
,
.
?
。
.
.%%:
:
.%.
..
:
..
%:
.
塘啊
;..
弱妇,
.啊%%:
:
..℃..
.
:
,
学位论文独创性声明
本人声明所呈交的学位论文是我个人在导师指导下进行的研究工作及取得
的研究成果。
尽我所知,除了文中特别加以标注和致谢的地方外,论文中不包含
其他人己经发表或撰写过的研究成果,也不包含为获得东南大学或其它教育机构
的学位或证书而使用过的材料。
与我一同工作的同志对本研究所做的任何贡献均
已在论文中作了明确的说明并表示了谢意。
签名:
日期:
关于学位论文使用授权的说明
东南大学、中国科学技术信息研究所、国家图书馆有权保留本人所送交学位
论文的复印件和电子文档,可以采用影印、缩印或其他复制手段保存论文。
本人
电子文档的内容和纸质论文的内容相一致。
除在保密期内的保密论文外,允许论
文被查矛:
借阅,可以公布包括刊登论文的全部或部分内容。
论文的公布包
括刊登授权东南大学研究生院办理。
签名日
导师签名:
期:
第一章前言
.复合材料
..复合材料的定义
复合材料;是由两种或两种以上的不同材料通过复合
工艺组成的新型材料。
它既能保留原组成材料的主要特色,又能通过复合效应获得原组分所
不具备的性能,可以通过设计使各组分的性能互相补充并彼此关联,从而获得新的优越性能,
与一般材料的简单混合有着本质的区别【】。
从复合材料的定义中可以看出,复合材料不仅能够综合基体和增强体材料的优势,扬长
避短,而且具有可设计的特点,即可以根据用途和要求的不同对增强体的比例、分布、排列
和取向等进行设计。
随着材料科学与技术的进步,复合材料已经发展成为一个庞大的技术体系。
这个体系包
括了对复合材料的力学理论、分析计算、材料与结构的理论、设计、制造工艺、试验、管理
以及工程中的应用等。
图.中综合了有关复合材料技术体系的概貌。
..复合材料的发展历程
自然界中就存在许多天然的复合材料,人类也从很早的时候就开始接触和使用各种天然
的复合材料,并效仿自然界制作复合材料。
现代复合材料应用的开端则要从年,第二
次世界大战中玻璃纤维增强聚酯树脂复合材料被美国空军用于制造飞机构件开始算起。
材料科学家们认为,就世界范围而论,从年到年这年间,是玻璃纤维增
强塑料的时代,可以称为复合材料发展的第一代。
从年到年这年间是先进复
合材料得到发展的时期。
年到年英国研制出碳纤维,年美国杜邦公司开发出
年先进复合材料“碳纤维增强环氧树脂复合材料及开芙拉纤维增强环氧树
脂复合材料”已用于飞机、火箭的主承力件上,这一时期被称为复合材料发展的第二代。
年到年问,是纤维增强金属基复合材料的时代,其中以铝基复合材料的应用最为广泛,
这一时期是复合材料发展的第三代。
年以后则被认为是复合材料发展的第四代,主要
发展多功能复合材料,如机敏智能复合材料和梯度功能材料等。
除了纤维增强型以外,
粒子弥散型、金属陶瓷型复合材料的研究也有了长足的发展。
复合材料不仅只应用在导弹、
火箭、人造卫星等尖端领域中,在航空,汽车、造船、建筑、电子、桥梁、机械、医疗和体
育等各个领域都的到了应用。
..复合材料的分类
复合材料可按基体类型、增强体类型、用途和性能高低等进行分类,如图所示。
按
基体材料类型可以分为有机材料基、无机非金属材料基和金属基复合材料三大类。
金属基包
括铝基、铜基、镁基、钛基和铁基等。
按增强体的几何形状可以分为颗粒增强型、纤维增强■【.囊诧童
一力制一融观力学宏观力学断裂力学陶瓷力刳
一复合测一协学型复合其它物理型复刽
?
做计条俐一结构要求条件、性能、重量、统荷要求条件、
机械、物理、气象、放射性等环境条件
卡才料设训一材料学材料设训
?
性构设计一峙构理论结构设训
一设计去
澉优设训一才料结构
?
何靠性设训一材料可靠性、结构可靠性;可靠性管理、管
理、计划、实施;可靠性技术、监视、预测
危险状态分析分致命、重大、极
?
按全设训一
限、可忽略四级、失效树分析
技术体系卜
龃分材料制备工到
一制造工艺
峪构制造工刻一路构成型结构制造工到
一工业管理品质管到一从设计、生产、销售、直到运筹学、
工业工程学、市场研究等
生产量、销售量、价格预测、
一管理卜一羟济管到一
控制、调整、经济设计分析
一网
‘
一齄料试列
一试利一
结构缺陷表面状态、尺寸变化、物理
缺陷异物混入、剥离、力学缺陷密
一非破坏试验
度、弹性模量、硬度
一工程应用
图复合材料技术体系概貌
?
.曩■■啦捌失
型和板状复合材料三大类,如图所示。
按颗粒尺寸的大小又可分为弥散增强型和颗粒增
强型两类。
复合材料按用途可以分为结构复合材料与功能复合材料两大类。
结构复合材料指
以承受载荷为主要目的,作为承力结构使用的复合材料。
功能复合材料指具有除力学性能以
外其它物理性能的复合材料,如导电、超导、半导、磁性、压电、阻尼、吸波、吸声、摩擦、
屏蔽、阻燃、防热、隔热等功能复合材料。
其中人工介质材料、隐身功能复合材料、梯度功
能复合材料等已被广泛应用到军事、航空航天等领域【】。
按复合材料性能的高低可以分为
常用复合材料与先进复合材料两大类。
常用复合材料如玻璃钢就是用玻璃纤维等性能较低的
增强体与普通的树脂构成,由于箕价格低廉而得以大量发展和应耀;先进复合材料指用高性
能增强体如碳纤维、芳纶等与高性能耐熟树脂构成的复合材料,后来又把金属基、内瓷基和
碳基以及功能复合材料包括在内。
广有机材料基复台材料
强体类型分无机非金属材料基复合材料
金属基复合材料
颗粒增强复合材料
强体类型分卜纤维增强复合材料
何形状卜板状复合材料
复合定向凝固麸晶复合材料
结构复合材料
途分一
一功能复合材料
广常用复合材料
能高低分叫
先进复合材料
图.复合材瓣的分类方法
颗粒
单片晶须,纤维
图根据增强体的类型而划分的三神复合材料的示意图【】
打
国外还常用英文简写来表示不同类型的复合材料,如
表示纤维增强塑料,而玻璃纤维,环氧树
表示金属基复合材料,”
脂则可表示为髟“螂戋/?
一?
一女■坷健支
..复合材料的性能特点
一.比强度与比模量高
复合材料的突出优点是比强度和比模量即强度、模量与密度之比高。
比强度和比模
量是度量材料承载能力的一个指标。
比强度愈高,同一零件的自重愈小;比模量愈高,零件
的刚性愈大。
以纤维增强环氧树脂复合材料为例,其密度约为钢的,,为铝的,强;其
比强度和比模量都比钢和铝合金高出许多。
这是复合材料非常突出的一个特点.
二.优异的抗磨性能
陶瓷粒子作为增强体制成的颗粒增强复合材料,由于陶瓷粒子优异的耐磨性能,获得了
比基体材料优异得多得抗磨性能。
同时综合的机械性能也获得了一定程度的提高。
在许多工
况恶劣,磨损严重的场合,这种复合材料无疑具有极强的应用潜力。
三.耐热性好
碳纤维增强树脂复合材料的耐热性比树脂基体有明显的提高。
金属基复合材料在耐热性
方面也显示出很强的优越性。
而碳化硅纤维、氧化铝纤维与陶瓷复合,在空气中能耐
。
.高温,要比常用的超高温合金的耐热温度高出。
以上。
用于柴油发动机
可取消原来的散热器、水泵等冷却系统,减轻重量约。
用于汽车发动机,使用温度可
高达【】。
四.复合材料的其它性能特点
由于复合材料的种类繁多,因此它们的性能特点和优点也各有不同。
复合材料的其它性
能特点还有抗疲劳性能好、减振减摩性能好、耐腐蚀性好等,视不同的复合材料而有不同的
特点。
另外,一些复合材料在绝缘、导电和导热性等方面也有比较显著的优势。
..复合材料的产业化
复合材料经过六十几年的发展。
在美国已经形成了一个年产值上百亿美元,从业人数达
几十万的新兴产业,并自九十年代中期以来,一直保持着高于美国增长速度的搞增长
速率。
图显示了.年美国各主要工业部门复合材料用量的增长情况。
..■士●啦佬走
图
蛤年美国各主要工业部门复合材料用量【】
可以看出以汽车为主的交通运输业和建筑业的复合材料的用量和增长速度都是相当大
的。
此外,为了适应二十一世纪汽车工业、航空航天工业、基础设施的建设与修复和延寿以
及美国国家环保局的环保的要求,美国的复合材料产业已经发展了相应的工艺技术
和产业运作模式。
这些都为我国复合材料产业的快速发展提供了一些可借鉴的经验【】。
图
?
所示的为美国复合材料工业成型工艺的应用情况。
图美国复合材料工业成型工艺应用情况【】
.颗粒增强金属基复合材料
..增强颗粒和金属基体
颗粒增强金属基复合材料是以金属为基体,添加颗粒作为增强相,通过一定工艺复合而
成。
颗粒增强金属基复合材料相界面的润湿性、化学反应以及组分的溶解对相界面的结合有
..●士摹∞,文
着重要的影响。
所选取的增强颗粒与金属基体在用相应的工艺进行制各时。
要能够满足润湿
性、相组分的弹性、化学性能和热力学性能的相容性等诸多苛刻的条件。
目前使用的金属基体主要有铝。
钛、镁、铜、铁钢、锰以及金属间化合物等,增强
颗粒有,、、、、、、、、、、、、、
、、、忙、、、、、州、等【】。
这些颗粒通常都具有
强度高、硬度高、热稳定性高的特点.这些颗粒的弹性模量.显微硬度,抗拉强度、热力学
动力学数据详见参考文献【】。
..颗粒增强金属基复合材料的制各工艺
目前,颗粒增强金属基复合材料的制各工艺很多,本小节将着重介绍国内外比
较成熟的燃烧合成法、粉末冶金法、普通铸造法等制备工艺。
?
.燃烧合成法
在粉末元素闻利用强烈的放热反应而形成某一化合物的方法叫燃烧合成法。
这种工艺的
优点在于工艺简单、界面干净。
根据反应发生的方式和加压方式的不同,可以分为自蔓延高
温合成.,简称、
法、热压放热反应合成法
简称、反应熔铸法
、反应加压法
。
自蔓延高温合成法
将欲获得增强体的组成元素与基体粉末按比例混合压制成坯,利用一个热脉冲使压坯的
一端温度上升直至发生放熟反应,反应以燃烧波迅速蔓延至整个压坯,通过放熟反应,原位
生成反应产物,这种方法称为自蔓延高温合成法。
这是年前苏联科学家发明的一种合
成材料的高新技术,由于其原位生长特性,并且可以通过改变反应物的组成和控制工艺参数
较大幅度的调节材料的结构和性能,是一种有效的制各“可设计材料”的技术。
技术
已被广泛的应用于制备复合材料材料、金属问化合物、陶瓷材料、电子材料等。
利用这种方法制备颗粒增强金属基复合材料有很多优势:
颗粒细小,分布均匀,与基体
结合良好,界面无污染,颗粒与基体的比例允许范围较大。
但是对反应过程不能控制。
另外
得到的材料往往致密度不够高。
等人采用自蔓延高温合成法制各了.和.弥散强化复合材
料。
他将”、、或者、、混合粉末压制成坯,在空气中用乙炔火焰将其点
燃,利用啊和的放热反应使合成过程自动完成【。
邹正光、傅正义、袁润章等】】采用自蔓延高温合成技术制备了/复合材料。
研
究了原料组分,粘度对合成过程及产物特征的影响,探讨了燃烧反应及结构形成机理。
探讨
了金属相的作用及其含量变化对燃烧波速度、粒度的影响。
如何提高反应产物的致密度,是发展的重要方向。
法
美国公司用燃烧合成法合成颗粒增强基及基复合材料,称之为
工艺。
该工艺经济实用,适用性强。
其基本原理是把待反应的元素与基体金属或合金的粉末
混合均匀并加热到基体金属或粉末的熔点以上,此时反应剂元素发生放热反应,生成粒子。
该工艺的实质是以熔体为介质,通过组元间的扩散反应而生成增强颗粒。
法除了具有
法的常规优点之外,还可以进一步提高产物的致密度。
由于一般的反应放热量相对较低,采
用工艺时系统通常达不到较高的温度,而法由于温度较高,促使大量的液相形成,
一■士■捌文
从而使产物致密。
我国开展和工艺的研究是从八十年代末期开始的,有关的研究已被列入了
“”计划,并成立了中国协会。
相关研究得到了较为快速的发展。
热压放热反应合成法
玎,是国内研究认基复合材料的一种重要技术。
它是由郭建亭、邢占平等人发展
起来的并成功制各出了认.啊、认?
等复合材料。
它的主要特点在于针对反应合成
法致密度不高的缺点,在燃烧合成反应发生时,反应产物尚处在高温时,对其施加一定的压
应力,使反应产物的合成与致密几乎同时完成,有效地提高了产物的致密度。
将镍粉、铝粉、钛粉、碳黑或硼粉按相应比例混合均匀后,经Ⅱ,工艺制备出认坷、
.复合材料,细小的耵和均匀分布在基体中,两种复合材料的致密度可分别
达到,%和.%【】。
反应加压法
与在燃烧合成时加压不同,方法是直接将反应坯料按照接近常规的热压或热
等静压工艺进行操作,在升温过程中,坯料会发生化学反应。
它包括反应热压法和
反应热等静压法等。
和采用法制各了认/颗粒增强复合
材料,工艺参数为℃,,。
法可以使产物达到完全的致密,但它的缺点是设备结构复杂、昂贵。
另外一种与
之效果接近但造价低廉的制备工艺为反应准等静压法。
等采用这艺,
获得了相对密度高于%的一材料【】。
反应熔铸技术
在过程中,合成颗粒相的元素态粉末原料、在金属相的熔体中通过
放热反应在金属熔体内生成细小的增强体颗粒。
用法制备的复合材料的基体,颗粒界面
无污染。
在完成放热反应后,可结合一些传统的冶金过程如铸造、锻造、热挤压等工艺制备
型材。
其缺点是当颗粒含量过高时,颗粒容易聚集长大,而且分布不均匀。
目前用这一技术
已制备出铁基/、/、认仍等多种复合材料。
其工艺过程如图所示。
加热
?
?
?
?
?
?
静
图缶方法制备颗粒增强金属基复合材料示意图
孙扬善、孙建荣等【【】】【】【】【】【】利用原位合成铸造法制备了弼颗粒增强
、、钢基复合材料。
将钛粉和碳粉按一定的比例混合压制成块,然后加
入到熔融的钢液中去,钛和碳在高温下发生原位反应生成颗粒,在中频感应的搅拌作用
下得到了分散均匀的增强颗粒。
另外,通过调整预制块中的钛和碳的比例,也获得了不同含
量的增强体颗粒和不同组织、性能的复合材料。
严有为、魏伯康等利用反应铸造法制备铁基复合材料时采用了多种配方方法,突破了燃
烧合成法利用粉末合成的局限,既有铸造生铁、钛铁合金和钢的组合【】,也有钛、碳、
..铁的组合【】。
以及啊.合金加合金,活性碳粉加融币母合金等组合【。
都是利
用钛和碳在铁熔体内的原位反应来生成颗粒增强铁基复合材料的。
二.粉末冶金方法
粉末冶金法是制备颗粒增强金属基复合材料的主要工艺方法之一。
它是一种将增强体粉
末与金属粉末均匀混合后采用一定的压制、烧结方式来制各复合材料的工艺。
粉末冶金法
与燃烧合成法的区别在于,在粉末冶金工艺中增强体和基体不是原位合成的。
根据具体压制
和烧结方式的不同,粉末冶金法又可分为熟压
、热等静压
、机械合金化法
与准等静压、熟挤压法及喷雾沉积
等【】。
热压法和热等静压是粉末压制和烧结同时进行的工艺。
这两种方法能有效消除制品中的
残留空隙,得到接近完全致密的材料。
热挤压法适于制造有均匀截面且较长的棒状材料。
在
喷射雾化沉积过程中,熔化的金属基体被高能氮气分散成弥散分布的微米尺寸的液滴,同时
将增强体颗粒注射进雾化的金属喷射物中,一起沉积在水冷的基片上。
再经挤压等第二次加
工成型。
喷雾沉积装置示意图如图一所示。
机械合金化法的基本过程是将混合粉末在高能
球磨机内研磨,经历反复的冷焊、断裂、再冷焊过程得到所需微观结构合金粉末的过程,它
是一种控制合金相及微观组织,扩大固溶度,制取弥散强化材料的有效方法。
机械合金化法
的示意图如图.所示。
硝器
‰
慷
亿蒸
§管
麓:
豹
蜥’
麟净
图刁喷射雾化沉积装置示意图【】
图机械合金化法示意
.嘎士■位,定
三铸造法
颗粒增强金属基复合材料最初是采用粉末冶金方法制造的。
粉末冶金法具有颗粒均匀分
散、陶瓷颗粒可达到相当高的体积分数、零件尺寸精度高、表面质量好等优点,但也存在设
备投资大、生产成本高、工件的形状和大小受到一定限制等缺点,所以用粉末冶金法生产的
颗粒增强金属基复合材料虽已商品化,但仅限于制造切削刀具和钻探工具。
采用铸造法制备
颗粒增强金属基复合材料。
克服了粉末冶金法的缺陷,具有便于一次形成形状复杂件、工件
可大可小且设备投资鞍少等优点【】。
为了解决铸造法制备过程中增强颗粒与液态金属之闯
的润湿性不好和比重差异较大的矛盾,材料学者们研究了很多工艺方法,下面是对各种方法
的一个概述【】。
压力铸造法
这种方法是预先把增强体颗粒充填在铸型中,然后在一定的压力下把熔融金属压入铸型
并使其凝固。
它解决了润湿性和比重差异的问题,如果温度、压力等参数控制得当,可以得
到均匀的高含量颗粒增强金属基复台材料。
这是一种较为成熟、极有发展前途的工艺。
机械搅拌法
这种方法是通过搅拌桨的旋转,对熔融态的金属基体进行搅拌,同时加入颓粒并使其分
散。
此方法操作方便,设备简单,适用于两相差异较小的复合系统。
如果比重差异较大,容
易产生粒子的偏聚。
另外,搅拌时卷入的气体,也对浇铸构成不利的影响。
喷射分散法
这种方法是用氢气等惰性气体,把增强体高速的喷射到液态金属中并使其分散。
长古川
正义采用此法成功制取了低合金钢基体的复合材料。
另据文献【介绍,采用喷射法生产
.颗粒复合材料,的含量可以达到%。
离心铸造法
在制备回转体类型零件的表面复合材料时,可以采用离心铸造法。
它的原理是利用旋转
时的离心现象,把增强体颗粒分布在铸件外表面或者内表面。
可以用来制造表面有特殊性能
要求的零件。
文献【】介绍了采用此法制造铁基碳化硅颗粒表面复合材料,其最大表层厚度
可达。
中间合金法
这种方法是把颗粒与金属耪束混合成中间合金团块,通过中间合金把粒子引入到液态金
属基钵中去。
文献【报道了用石墨和铝粉混合翻成中间合金团块,使其在铝液中熔化,分
散,结果获得了石磨粒子均匀分布的复合材料。
研涂覆铸造法
这种方法是在铸型壁上涂覆增强体粉末,然后把基体金属浇铸进去。
在毛细管力、液态
金属的静压力等的作用下,金属液渗入涂覆层,将增强颗粒俘获。
强化相颗粒深入表层中,
这样就形成了具有一定厚度的表面复合层。
这种方法的主要问题是将增强体涂覆在型壁上所
使用的粘结剂在浇铸过程中会变成渣,从而使复合层产生夹渣、气孔、缩孔等缺陷。
另外,
颗粒的加入使得靠近型壁的金属熔点下降,凝固缓慢。
与普通的铸型的凝固顺序相反,心部
先凝固。
乃渗透铸造法
这种方法先把粒子放置在铸型底部,然后盖上一块与液态金属基体成分相同的薄板以
防在浇铸过程中粒子被冲散,然后浇入液态金屈基体。
浇铸过程使薄板熔化,粒子向基体
渗透,从而形成表面复合层。
如果在此工艺的基础上采用真空吸渗工艺,利用液态金属的静
压力、毛细管力的作用,加快了金属液在颗粒间隙的运动速度,可以获得比普通浇铸厚?
倍的复合层。
四.其它方法
上述介绍了三大类、若干种工艺方法。
燃烧合成、粉末冶金和铸造工艺分别是从三种不
同的角度来发展工艺的。
燃烧合成的基本思路是原位?
合成;粉末冶金的基本思路
是粉末的混合、压制和烧结;而铸造法则是立足于铸造工艺之上展开的。
在具体的工艺方法
上,这三大类工艺经常会有交叉和共同使用的情况。
除此之外,还有一些较为特殊的工艺方
、
法,如快速凝固技术、高能高速法
动态固结工艺。
关予它们的详细介绍请参见文献【。
..弥散增强与颗粒增强
?
..弥敌增强【】
弥散增强金属基复合材料是由弥散微粒与金属基体复合而成。
作为弥散强化的粒子应满
足两个基本条件:
一是弹性模量要远高于基体的弹性模量:
二是要与基体里非共格关系。
位
错运动受到粒子阻碍时,难于切过粒子本身,而以绕过方式通过粒子,并在粒子周围留下位
错圈,阻碍基体的位错运动,从而达到强化效果,即所谓的机制。
如图所示。
此时,载荷主要由基体承担,弥散颗粒阻碍基体的位错运动。
微粒阻碍基体位错运动的
能力越大,增强的效果越大。
在剪切应力作用下,位错的曲率半径为
。
/.
其中。
是基体的剪切模量,是柏氏矢量。
若微粒之间的距离为,当剪切应力大到使位错的曲率半径/时,基体发生位
错运动,复合材料产生塑性变形,此时剪切应力即为复合材料的屈服强度
产/
假设基体的理论断裂应力为./,基体屈服强度为,,