钢铁联合企业重大环境因素和危险源的识别.docx
《钢铁联合企业重大环境因素和危险源的识别.docx》由会员分享,可在线阅读,更多相关《钢铁联合企业重大环境因素和危险源的识别.docx(11页珍藏版)》请在冰豆网上搜索。
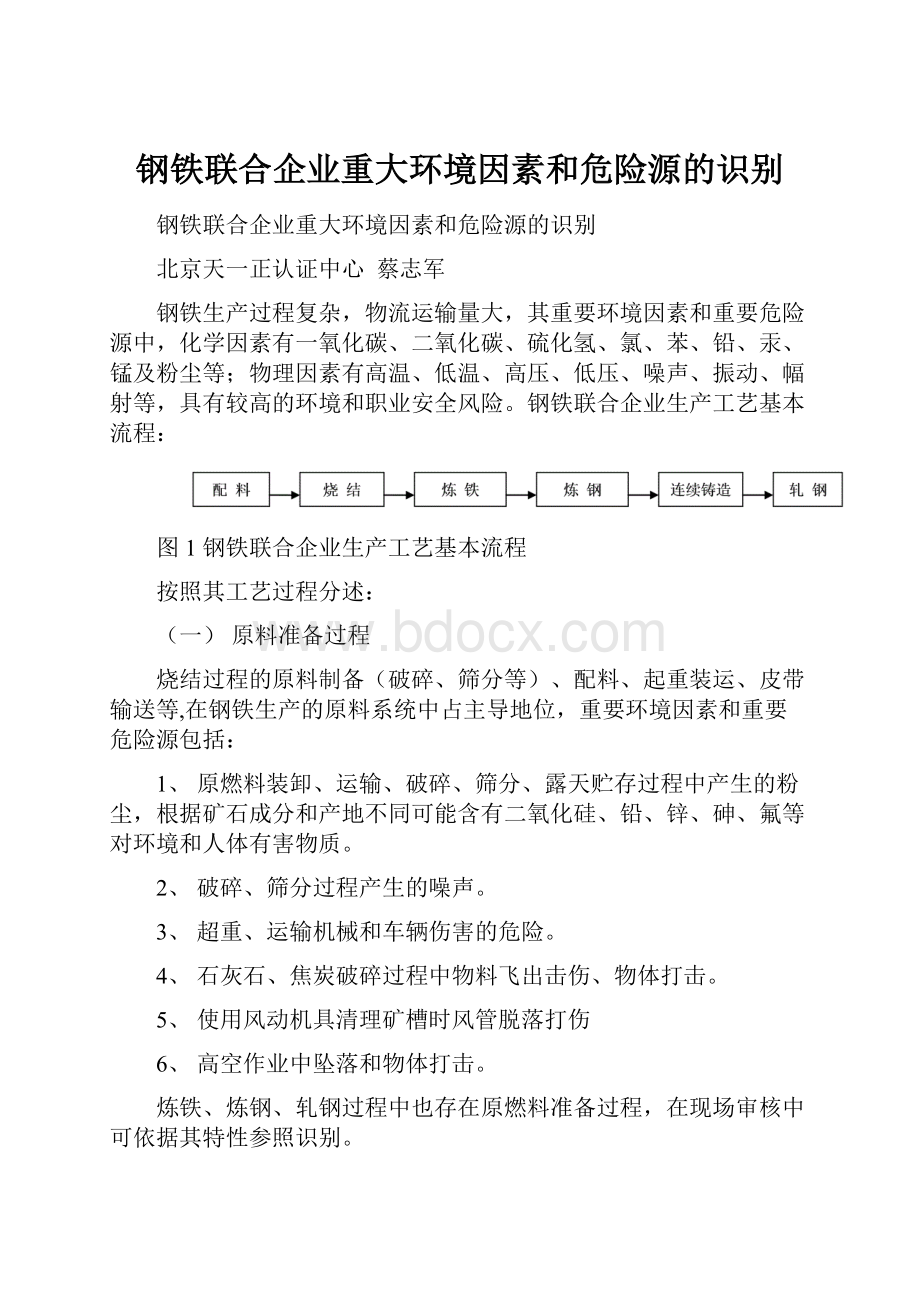
钢铁联合企业重大环境因素和危险源的识别
钢铁联合企业重大环境因素和危险源的识别
北京天一正认证中心蔡志军
钢铁生产过程复杂,物流运输量大,其重要环境因素和重要危险源中,化学因素有一氧化碳、二氧化碳、硫化氢、氯、苯、铅、汞、锰及粉尘等;物理因素有高温、低温、高压、低压、噪声、振动、幅射等,具有较高的环境和职业安全风险。
钢铁联合企业生产工艺基本流程:
图1钢铁联合企业生产工艺基本流程
按照其工艺过程分述:
(一)原料准备过程
烧结过程的原料制备(破碎、筛分等)、配料、起重装运、皮带输送等,在钢铁生产的原料系统中占主导地位,重要环境因素和重要危险源包括:
1、原燃料装卸、运输、破碎、筛分、露天贮存过程中产生的粉尘,根据矿石成分和产地不同可能含有二氧化硅、铅、锌、砷、氟等对环境和人体有害物质。
2、破碎、筛分过程产生的噪声。
3、超重、运输机械和车辆伤害的危险。
4、石灰石、焦炭破碎过程中物料飞出击伤、物体打击。
5、使用风动机具清理矿槽时风管脱落打伤
6、高空作业中坠落和物体打击。
炼铁、炼钢、轧钢过程中也存在原燃料准备过程,在现场审核中可依据其特性参照识别。
(二)烧结过程
如图2所示,从精矿粉到烧结矿和球团矿为烧结过程,其原料准备在
(一)中已述。
烧结过程的重要环境因素和重要危险源主要有:
1、粉尘的排放和危害。
一般烧结过程粉尘量占烧结矿产量的3%左右,主要发生在烧结机机尾卸矿,成品矿的热破热筛和冷破冷筛,进料、混料和出料的卸载装运及除尘系统的排放、卸灰和转运过程。
粉尘含有二氧化硅、铅、锌、砷、氟等有害物质对环境和员工健康的危害。
2、烧结点火用煤气(一氧化碳)和烧结机运转过程排放的烟尘及烟尘中的CO、SO2、H2S等,当煤气管道、烟道或闸阀泄漏、烟尘超标排放,对环境的影响和火灾、爆炸、人员中毒事故。
同时还应关注突然停电时,点火器炉内火焰窜出造成作业人员烧伤;突然停煤气导致空气进入煤气管道引起的爆炸;在机尾观测孔观察卸料或捅料时含尘热浪烧伤。
3、噪声排放的危害。
噪声主要来自风机、破碎机、振动筛、及机电设备运转撞击,特
图2钢铁联合企业生产工艺流程
别是主抽风机、原燃料破碎噪声可达100Db(A),造成对环境影响和员工健康的危害。
4、高温的危害。
烧结机、单辊破碎机、热矿筛、一次返矿、皮带运输机等操作位都属于高温作业。
5、生产异常时对操作人员的伤害。
如矿槽内发生堵料、粘料时采用人工挖、捅,容易发生物料喷射,击伤面部;烧结矿单辊破碎机和热矿筛出口堵塞时,用水捅料容易发生蒸汽和红料烫伤;烧结料烧不透时遇水“放炮”造成人员烫伤;进入煤气管道、烟道或除尘器内检查或处理故障时,有发生煤气中毒和窒息的危险,以及启动风机会危及人员生命安全;进入电除尘器检查或维护维修时电击伤的危险。
必须由具备相应资质、资格的单位和人员承担异常情况的处置,制定并遵守严格的操作规程,采取排净有害气体,通风,对现场、相应设备启动装置、孔门、闸阀实施监护等措施。
6、设备运行造成的机械伤害。
除通用的起重运输设备、车辆带来的危险因素外,振动筛部件、零件振断飞出击伤,抽风机转子失衡造成叶片脱落击破机壳飞出击伤等。
(三)高炉炼铁过程
高炉冶炼由炉体、渣铁系统、热风系统、上料系统、煤粉制备喷吹系统、烟气处理、煤气制备输送系统和冷却水循环系统组成,过程的重要环境因素和重要危险源主要有:
1、高炉气体的排放、处理和危害。
高炉冶炼是一个随着上升热煤气流和下降的冷炉料相向运动贯穿于始终和复杂工艺过程,煤气上升至炉顶被称为荒煤气,较多采用湿法除尘:
重力除尘(粗除尘)→洗涤塔(半精除尘)→文氏管(精除尘)→脱水→净煤气。
净煤气通过输送设备和输送管道,用于发电、烧结和钢坯加热炉等。
高炉煤气在产生、除尘处理、输送过程中的泄露会造成重大环境污染、一氧化碳中毒和火灾、爆炸事故。
煤气泄露的形成主要包括:
出铁或发生故障检修作业时;除尘系统和煤气输送管道和闸阀运行过程的泄露;高炉、除尘系统和煤气输送管道检修时的残留煤气,以及与并联煤气管道闸阀未关闭阻断或误操作。
针对形成原因采取的主要措施应包括:
a)加强铁口和液压泥炮的日常维护,保持炮泥性能质量稳定,出好每一次铁,保持正常运转。
并对高炉平台、除尘器操作岗位、渣口、泥炮等处CO、H2S、SO2、O3和酚等毒物浓度实施监视和测量;
b)对高炉炉顶工作压力、热风炉燃烧器、除尘系统、煤气管道、闸阀的运行实施监测和测量,对煤气管道还应定期做探伤检测。
主控室、变电室、动力开关室、煤气放散点火装置等处应配置CO自动检测报警装置和灭火器材。
热风炉燃烧器和煤气管道应装有煤气流量调节器、煤气自动切断阀和自动报警系统;
c)对除尘系统、煤气管道、闸阀的检修,必须由具备相应资质、资格的单位和人员实施,在实施过程中严格遵守操作规程,排净设施和管道内易燃易爆及有害气体,通风,对现场、相应设备启动装置、孔门、闸阀实施监护等措施。
2、烟尘的排放和危害。
在高炉出铁出渣以及渣铁流经渣铁沟时,产生大量烟尘。
高炉出铁场消烟除尘设施包括:
出铁口、铁沟、砂口、铁水罐、出渣口、渣铁沟等部位安装集尘罩捕集烟尘,使用布袋除尘器或电除尘器进行净化处理。
3、粉尘的排放和危害。
高炉炉料(烧结矿、球团矿、焦炭、块矿、熔剂等)的仓储、转运、筛分过程中产生粉尘的排放,造成环境污染和危及现场员工的职业健康。
目前主要采取尘源点密封捕集措施。
包括:
移动卸料车向仓内卸料移动式通风除尘或仓内通风除尘;皮带输送机采用工艺密封加吸尘罩;振动筛采用全封闭式和局部工艺密封加吸尘罩。
捕集的粉尘可选择电除尘器、袋式除尘器净化处理。
4、固废、废气的排放。
高炉炉渣、水渣和炉体、烟道废弃物中含有硫化氢和二氧化硫,应识别和控制,如:
水渣出口CO2、H2S等有害气体的捕集和处理、渣铁的运输和处理;高炉、热风炉、煤气管道大修和检修产生固废运输和处理;除尘设备捕集的灰、泥的运输和处理,以及过滤后气体的排放。
5、高炉喷吹煤粉的制备和喷吹设施,当温度和空气中煤粉浓度超过临界点时,潜在发生火灾和爆炸的危害,尤其是进行烟煤或含有烟煤的煤粉制备时。
目前在煤粉制备过程多采取惰性气体保护的方法控制气氛中的含氧量,同时应采取:
a)磨煤机与热风炉废气的抽吸输送系统、烟气炉之间应设置防误操作的安全连锁装置,保证挡板关闭时抽吸系统处在抽吸状态,在磨煤机入口前及收尘器出口处应设置氧浓度监测仪(一般磨煤机入口处氧浓度≤8%,收尘器出口处氧浓度≤12%);
b)煤粉仓、袋式收尘器、喷煤罐温度及喷煤系统的仪表、阀门应安装监测和自动报警装置。
煤粉仓还就设置吸潮管、一氧化碳浓度监测仪和自动报警装置。
煤粉制备和喷吹系统、袋式收尘器应采取防火、防爆、防雷和防静电措施;
c)煤粉制备厂房应按乙类厂房设计。
制粉系统应装设符合要求的爆破孔。
煤粉仓应设防爆孔,防爆孔及喷煤罐组的设计应符合《压力容器安全监察规程》的规定。
各种电气设备应按爆炸和火灾危险场所等级G-2级设计,并符合《爆炸危险场所电气安全规程》标准;
d)应设置煤粉管道、和容器吹扫用压缩空气,氮气和其它惰性气体,包括氮气源贮罐,供倒罐充压、流化、布袋反吹等,以及事故充氮用。
6、异常情况引起的突发事故。
主要包括:
a)鼓风机突然停风,煤气向送风系统倒流造成送风系统管道、风机爆炸。
以及煤气管道形成负压,吸入空气引起爆炸;
b)因停电、水泵故障、管道破裂等意外情况而致高炉供水系统水压降低或停水,冷却失效,炉体、炉缸烧穿,吹管风口烧出等情况,都会造成跑铁、跑渣、跑火,灼烫伤人员,遇水、煤气、油料等导致爆炸和火灾;
c)高炉出铁时开、堵铁口的泥炮操作失误,出铁沟的修补以及出渣、出铁的铁渣飞溅,造成人员灼烫。
7、出铁场起重机、解体机、泥炮等到设备的机械伤害。
8、炼铁过程的高温热幅射,应对铁口、渣口、渣沟、泥炮、平台等高温幅射区的单向幅射热强度实施监视和测量。
9、高炉鼓风、喷吹煤粉,煤气放散和机电设备运转产生的噪声,有时会超过100dB(A),应实施监视和测量。
(四)炼钢过程
目前国内一般采用转炉、电炉、平炉炼钢。
其中平炉因其热效率低、能耗大已逐步退出,电炉主要用于高合金钢的冶炼,转炉炼钢最为普遍。
如图2所示,炼钢工艺过程大略为:
装料→转炉吹炼→炉外精炼→连续铸造→钢坯。
过程的重要环境因素和重要危险源主要有:
1、转炉吹炼过程产生大量高温烟气、烟尘,含有一氧化碳、二氧化碳、氧化铁和其他微小颗粒,其温度高达1400~16000C。
通常采用烟罩捕集→汽化冷却烟道冷却并回收蒸汽→湿法除尘(文氏管净化器)→脱水→回收转炉煤气。
在以上过程中应关注:
a)一氧化碳中的空气、氧含量超过临界值发生爆炸危险,应对煤气中的含氧量实施监测和控制,并确保系统不吸入空气。
煤气、煤气柜、烟气分离器、蓄热器应设置自动检测报警、自动快速切断等安全设施;
b)烟气、烟尘处理装置、管道、闸阀泄露对环境的污染、人员中毒及遇明火发生火灾和爆炸和危害。
应确保:
对系统执行严格的检修维护制度,设备运行正常、完好有效;对一氧化碳浓度实施监测,主控室、煤气沟管、风机房、加压站及相对封闭场所设置自动报警装置,并采取安全、通风措施;
c)煤气放散时排气筒高度、微正压运行状态应符合要求,自动打火点燃装置应完好有效;
d)设置防爆板、水封器,确保能够起到泄爆作用;
e)严格控制火种和动火作业。
2、固废、废气的排放。
转炉炉渣和炉体、钢包拆炉修炉废弃的内衬耐火材料中含有硫化氢和二氧化硫,应识别和控制钢渣和炉体、钢包大修和检修产生固废的运输和处理;除尘设备捕集的灰、泥的运输和处理,以及过滤后气体的排放是否达标。
3、原料准备、冶炼和精炼过程中的粉尘排放。
如铁水装入转炉、铁水排渣和预处理、转炉拆炉修炉、连续铸造、原辅料装卸运输等过程产生的粉尘,以及冶炼过程中会有20%烟气微尘逸散在车间,应采取二次除尘及厂房除尘措施。
4、制氧系统、除尘风机、设备的液压泵、耐火材料拆除机等设备运转产生的噪声。
5、炼钢、连续铸造过程中使用燃油、润滑油、液压油、变压器油、乙炔气体的泄漏和火灾危险。
6、炼钢、连续铸造过程中钢包吊运及设备检修时设备、轧辊的吊装产生的钢水溢漏、起重伤害和高处坠落,除起重运输机械按照特种设备严格控制外,通常还应对钢水包、铁水包的耳轴及吊钩、吊具做定期探伤检测。
7、氧气引起的燃烧与爆炸。
危险源主要是:
氧枪、氧气输送管道内,在制造和安装过程中残留金属物、非金属物、油脂等杂物;氧气管道接口粗糙,管道内壁生锈,管道选用阀门不当;氧枪吸入杂物或管内堆积含碳微粒;通氧操作不当等。
都会引发管内氧火,气管爆裂,高纯高压氧气大量外溢,造成火灾和爆炸。
8、钢水遇水爆炸。
转炉氧枪、烟罩、炉口水箱、汽化冷却烟道等设备采取循环水冷却,焊缝开裂、喷头烧损脱落等原因都会造成大量水与钢水相遇,引起爆炸,对环境和人身造成危害。
9、余热锅炉爆炸的危险。
余热锅炉系统应有安全装置,包括防爆孔、检查孔、安全阀、放散阀、水位测定与报警装置;
10、异常情况引起突发事故。
主要包括:
钢水、炉渣喷溅;塌炉造成钢渣、钢水喷出;氧枪粘钢采取的割枪措施;穿炉事故;钢包穿漏事故;滑动水口穿钢等,都可能引发人员灼烫伤和火灾、爆炸重大事故,应制定并严格执行安全操作规程和应急措施。
11、铁水、钢水、钢渣、连续铸造的热幅射,连续铸造结晶器液面控制的同位素射线幅射对人体和危害。
(五)轧钢过程
轧钢主要包括板、带、型、线的轧制,基本工艺过程:
图3轧钢基本工艺
主要设备有加热炉、轧机、冷床、切边机、定尺剪切机、校平机、收线机等。
过程的重要环境因素和重要危险源主要有:
1、加热炉、除鳞装置、轧机运行过程中产生烟气、烟尘,含有一氧化碳、氮氧化合物、硫化氢、二氧化硫等有害气体和粉尘,应经过除尘净化处理,达标后排放。
2、大量使用煤气、氧气、乙炔气体,以及燃油、润滑油、液压油等油脂的泄漏和火灾、爆炸和危险。
3、轧机、风机运行产生的振动和噪声对环境和职业健康的影响。
4、加热炉炉渣、冷却循环池沉淀渣和废油、除尘净化设备捕集的粉尘和污泥、加热炉拆炉修炉废弃物等固体废物的运输和处理。
5、加热炉、轧件的高温灼伤、热幅射,金属监测器、测厚仪、无损探伤过程产生的射线对人体的危害。
6、加热炉应采取安全措施,包括:
a)安装安全水源或设置高位水源,水压不应低于0.1MPa,出口水温不应高于500C;
b)以煤气为燃料时,其煤气危险区的划分应符合AQ2003-2004《轧钢安全规程》表1的规定并实施控制:
第一类区域,应戴上呼吸器方可工作;第二类区域,应有监护人员在场,并备好呼吸器方可工作;第三类区域,可以工作,但应有人定期巡视检查。
c)有煤气危险的区域应设置明显的防火防爆警示标志、自动检测报警装置的快速切断阀门,在该区域作业应两人以上进行,并携带便携式一氧化碳报警仪;
d)加热设备与风机之间应设安全联锁、逆止阀和泄爆装置,严防煤气倒灌爆炸事故。
炉子点火、停炉、煤气设备检修和动火,应按规定事先用氮气或蒸汽吹净管道内残余煤气或空气,并经检测合格,方可进行。
7、电气、液压设备和火灾、爆炸和触电的危害。
8、处理故障和检修过程中的机械或物体打击、起重伤害、高处坠落等危险因素。
9、轧钢生产过程中意外事故的伤害。
主要包括:
轧机的机架、轧辊和传动轴过载破碎碎片飞散伤人,应设有过载保护装置;轧件沿辊道正常行走和异常飞出造成的意外伤害;轧机、剪切机、输送辊道运行和钢坯修磨过程中的机械伤害等。
10、天车限位装置故障、超重、吊钩吊具损伤的危害,以及天车运行中发生的挤压伤害。
11、运输、装载车辆事故产生的火灾、爆炸和人员伤害。
(六)焦化厂炼焦过程
现代炼焦是以烟煤为原料的煤化工过程,在隔绝空气的条件下,将煤从焦炉顶部装入炭化室,加热到900~10000C得到焦炭,并通过回收利用得到焦炉煤气、氨和轻吡啶、粗苯、煤焦油等副产品。
同时也带来焦炉煤气的泄露、爆炸,含有颗粒物、苯可溶物、苯并〔α〕芘、H2S、NH3等有害物质的烟尘排放,含有较高浓度的固体悬浮物和酚氰污水的排放,以及煤尘、焦尘、焦油渣、生化污泥、砌炉修炉产生的固废等,构成重大环境因素和职业健康安全危险源。
图4焦化生产工艺流程及“三废”产生点示意
图4给出了焦化生产工艺流程中“三废”排放点示意,因组织采用的工艺、设备不同而有所差异,如干法熄焦和湿法熄焦工艺产生的环境因素会有所不同,后者不仅会有焦尘、除尘废水的排放,还有大量的熄焦废水的产生。
在审核中还应从实际出发关注环境因素和危险源识别的充分性及控制的有效性。
通常焦化过程重大环境因素和危险源主要包括:
1、焦炉煤气的泄露对环境的影响和可能发生的火灾、爆炸事故。
关注焦炉地下室、烟道走廊、风机房等煤气操作区及煤气净化区的设备、管道、阀门、水封等处,是否设置一氧化碳监测和自动报警装置,实施了监测并有可行的紧急预案。
2、焦炉生产过程中,如炉顶装煤、推焦和熄焦等过程,会产生大量烟尘,其中含有粉尘、一氧化碳、硫化氢、二氧化硫、苯和焦油等。
目前,在装煤过程中通常采用上升管喷射法、装煤车抽烟气法、顺序装炉法控制烟气飘逸;推焦过程采用固定+移动烟罩和地面交货系统除尘;熄焦过程推广干法熄焦,在干熄灭炉顶部装焦处、槽底出焦处、出焦口皮带、循环风机放散口设置烟尘捕集装置,经除尘交货后排放。
由于干法熄焦采用密闭设备,用隋性气体循环冷却,避免对大气的污染,并达到节能、提高焦炭质量的目的。
湿法熄焦一般采用有熄灭焦塔顶装折流式捕尘装置。
3、在焦油氨水分离装置、蒸馏设备、贮槽和放散管等处,应对硫化氢、氯化氢和氨等气体进行监测,防止气体泄露造成对环境和人员的危害。
4、在脱苯蒸萃过程中,应关注苯类物质、吡啶蒸气飘逸泄露对人员眼睛、皮肤和呼吸道的伤害。
如有苯精制过程,还应关注在初馏分中含有的二硫化碳,属于易挥发、易燃易爆的化合物。
5、在焦化副产品酚、萘的生产过程中,其气态或液态的泄露,会造成对环境的污染和人员的伤害。
6、焦化生产过程中煤、焦破碎、筛分,鼓风机、空压机及各种泵、机械运转产生噪声污染和对人员和伤害。
7、炼焦、出焦、熄焦过程产生的热幅射。
8、焦化废水,主要包括各级除尘废水、蒸氨废水、粗苯分离水、精苯分离混合水、终冷排污水、焦油精制分离水、煤气水封排水等,含有挥发酚、氰化物、硫化物、焦油、COD、酸、碱等,对环境的污染和人员的伤害。
以上就钢铁联合企业的代表性工艺过程中的环境因素和危险源进行了概略叙述,因企业选择工艺、设备及产品结构、原燃料不同,而各有差异。
在建立、实施环境和职业健康安全管理体系或审核过程中,都应从实际出发,但识别和控制的思路大体相同,如果能提供粗浅的启发和提示是本文的的期望。