流体力学结课论文实用干货.docx
《流体力学结课论文实用干货.docx》由会员分享,可在线阅读,更多相关《流体力学结课论文实用干货.docx(17页珍藏版)》请在冰豆网上搜索。
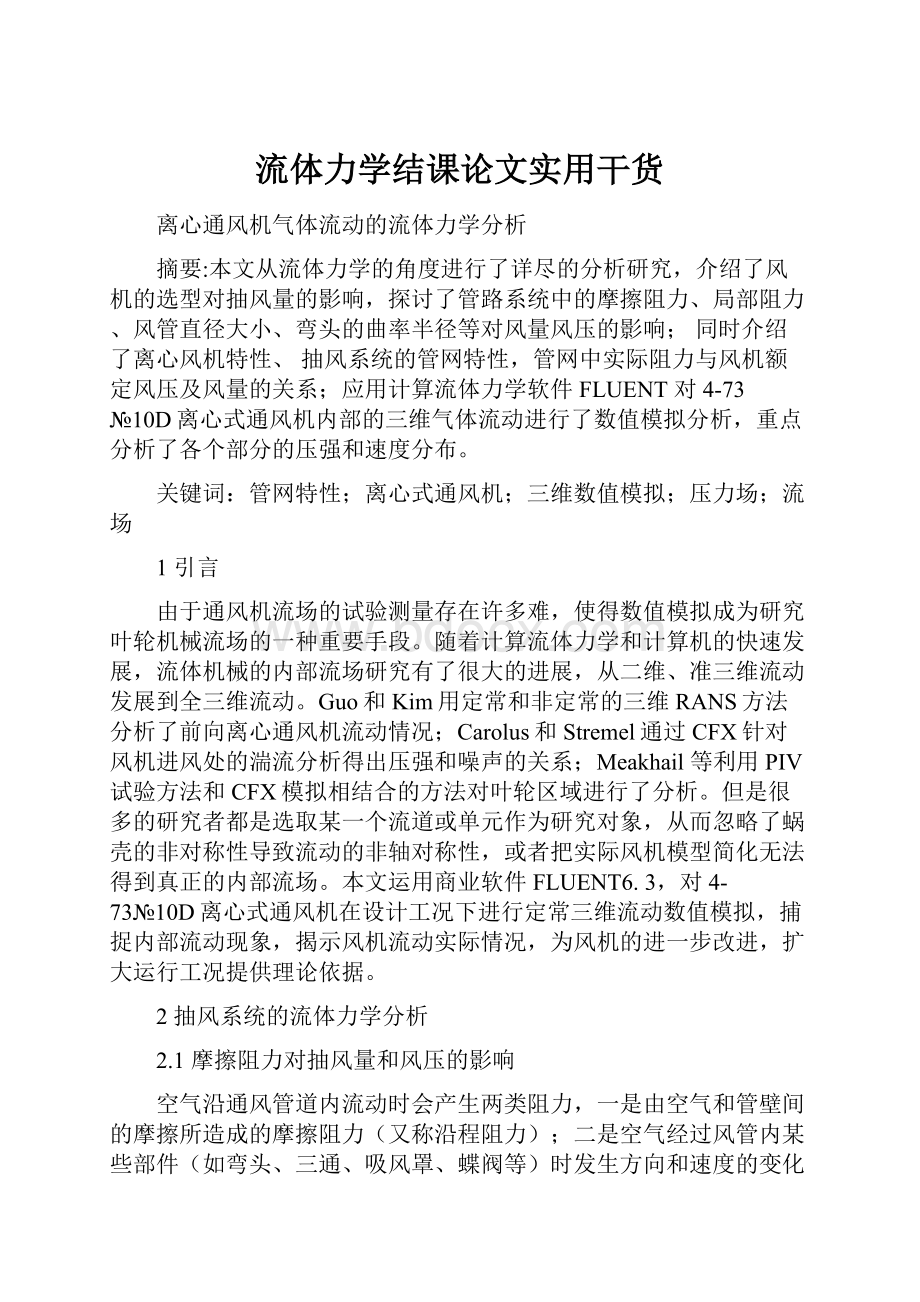
流体力学结课论文实用干货
离心通风机气体流动的流体力学分析
摘要:
本文从流体力学的角度进行了详尽的分析研究,介绍了风机的选型对抽风量的影响,探讨了管路系统中的摩擦阻力、局部阻力、风管直径大小、弯头的曲率半径等对风量风压的影响;同时介绍了离心风机特性、抽风系统的管网特性,管网中实际阻力与风机额定风压及风量的关系;应用计算流体力学软件FLUENT对4-73№10D离心式通风机内部的三维气体流动进行了数值模拟分析,重点分析了各个部分的压强和速度分布。
关键词:
管网特性;离心式通风机;三维数值模拟;压力场;流场
1引言
由于通风机流场的试验测量存在许多难,使得数值模拟成为研究叶轮机械流场的一种重要手段。
随着计算流体力学和计算机的快速发展,流体机械的内部流场研究有了很大的进展,从二维、准三维流动发展到全三维流动。
Guo和Kim用定常和非定常的三维RANS方法分析了前向离心通风机流动情况;Carolus和Stremel通过CFX针对风机进风处的湍流分析得出压强和噪声的关系;Meakhail等利用PIV试验方法和CFX模拟相结合的方法对叶轮区域进行了分析。
但是很多的研究者都是选取某一个流道或单元作为研究对象,从而忽略了蜗壳的非对称性导致流动的非轴对称性,或者把实际风机模型简化无法得到真正的内部流场。
本文运用商业软件FLUENT6.3,对4-73№10D离心式通风机在设计工况下进行定常三维流动数值模拟,捕捉内部流动现象,揭示风机流动实际情况,为风机的进一步改进,扩大运行工况提供理论依据。
2抽风系统的流体力学分析
2.1摩擦阻力对抽风量和风压的影响
空气沿通风管道内流动时会产生两类阻力,一是由空气和管壁间的摩擦所造成的摩擦阻力(又称沿程阻力);二是空气经过风管内某些部件(如弯头、三通、吸风罩、蝶阀等)时发生方向和速度的变化以及产生涡流等原因而产生的局部阻力。
圆形风管单位长度的摩擦阻力可按下式计算:
式中:
Pmr——圆形风管单位长度的摩擦阻力,Pa/m;
λ——摩擦阻力系数;
ν——风管内空气平均流速,m/s;
ρ——空气的密度,kg/m3;
D——圆形风管的直径,m。
在计算这两类阻力时,通常是按照层流状态来取摩擦阻力系数λ的,这时,沿程的压力损失与空气流速的一次方成正比,当流速增大超过临界流速Re=2300时,风管内的空气流型变为紊流状态,则管内沿程的压力损失与空气流速的1.75~2.0次方成正比,也就是说,沿程阻力增加了近1倍。
通常把风管内壁看作是水力光滑管,即管壁的绝对粗糙度K=0.1mm来计算的,而实际上,使用一段时间后,风机叶轮、风管、弯头、伞形抽风罩、折流板气水分离器等处内壁沾满了油漆,这时风管内壁已经变成了水力粗糙管(或称阻力平方区),管壁的绝对粗糙度值K≈0.9~3.0mm;这时,单位长度实际摩擦阻力P′mr应为计算单位长度摩擦阻力乘以修正系数β,即:
P′mr=β×Pmr
假设:
风管内空气流速为10m/s,绝对粗糙度值K=0.1mm,则:
修正系数β=(Kν)0.25=(0.1×10)0.25=1
(1)
式中:
K——风管内壁绝对粗糙度,mm;
ν——风管内空气流速,m/s。
再假设:
风管内空气流速不变,仍为10m/s,但绝对粗糙度值K=1mm,则:
修正系数β=(Kν)0.25=(1×10)0.25=1.78
(2)也就是说,这时单位长度风管内的摩擦阻力是原来的1.78倍。
再假设:
风管内空气流速为10m/s,绝对粗糙度值K=2mm,则:
修正系数β=(Kν)0.25=(2×10)0.25=2.114(3)这时,单位长度风管内的摩擦阻力是原来的2.114倍。
还有一个很重要的原因是,很多厂家在使用水帘喷漆室时,不添加或不按时按量添加漆雾絮凝剂,再就是不定时打捞漆泥漆渣,水中大量的漆泥随着循环水流挂在折流板、挡水板、涡旋板、风管内壁上,使得内壁绝对粗糙度大幅增加,摩擦阻力也增加了许多倍。
这就是众多的喷漆室使用一段时间后风压下降、抽风量减小、漆雾外溢的原因之一。
笔者认为,设计时风压选择不能仅仅放10%~20%的余量,而是最好增加80%左右的富余量;要定期清理风机叶轮、蜗壳、风管、折流板等抽风系统内的漆泥,而这是许多厂家不注重的,应对操作人员进行使用和维护的培训。
2.2局部阻力的影响
在风道中流动的流体,在通过弯头、阀门、变径管等处,方向和断面积大小发生改变,有可能产生涡流损失或碰撞损失,这些称为局部阻力。
风道部件的局部阻力可按下式计算:
式中:
ΔP——风管部件的局部阻力,Pa;
ξ——局部阻力系数;
ν——风管内空气平均流速,m/s;
ρ——空气的密度,kg/m3。
在一般通风系统中,由于风管中各部件形状不一,局部阻力系数很难计算,通常通过试验测定,而后查表确定。
而实际风管系统由于管径、流速、介质、曲率半径、渐扩角等大小不一,一旦有1个参数变化,其管路系统中实际局部阻力也是变化的。
例如,折流板汽水分离器在使用一段时间后,表面会沾上漆泥,使得局部阻力增大,空气流速下降;断面面积变小,又使得空气流速加快,空气中含漆雾颗粒增加,空气密度增大,局部阻力系数也会变大,在这种状况下,气体会产生漩涡,气流变成紊流状态,这些因素都会导致折流板处的局部阻力增大、抽风量下降。
局部阻力系数ξ是针对某一过流断面平均流速而言的,但是,各种管件的局部阻力损失,不是发生在流动的某一断面上,而是发生在一段长度的流段中,如果2个部件相隔太近,那么它们之间就会相互影响,这时流动的状况就复杂了,就不能用手册中给定的ξ来计算了。
因为,手册中的ξ值都是在没有其它阻力影响的条件下测定的。
例如:
为了降低喷漆室的高度,在喷漆室后部顶上,往往是1个伞形吸风罩和蝶阀、弯头及风机吸风口直接连接,中间很少有直管过渡,这时,这一流段的局部阻力就不是几个部件的阻力相加那么简单了。
阻力系数ξ会有变化,管道中会产生漩涡,主流受到压缩或扩散,流速分布会迅速改组,黏性阻力和惯性阻力都会显著增大。
2.3风管直径大小对风速的影响
管内空气流速在6~14m/s为宜,最好不超过10m/s。
有些制造商为节省材料成本,将风管直径做得很小,使管内风速过大,甚至达到24m/s,使得风阻急剧增大,当轴功率一定时,抽风量会下降,导致漆雾无法抽出去。
例如,某企业为外地某厂生产的2台喷漆室,抽风效果一直很差,漆雾外溢严重,2次更换风机后,仍然无法解决问题,笔者到现场发现,风机风管直径设计太小,风管内的摩擦阻力和局部阻力都陡然增大,导致抽风量严重下降,结果仅仅更换了大直径的风管就彻底解决了问题。
还有,风机出风口至风管排气口长度问题,一般应将排风管接出车间外屋顶2m以上高度,以利用大气压差。
目前常见的问题是一些设计人员设计时往往只考虑风机进风段的阻力问题,不考虑风机出风段的风阻,更不考虑室外排风管的高度,这是欠妥的。
2.4弯头的曲率半径对局部阻力系数的影响
90°的风管弯头其局部阻力系数ξ与风管弯曲的曲率半径与与风管直径之比R/D成反比,R/D越大,ξ值越小;如:
R/D为1时,ξ为0.23,R/D为2时,ξ为0.15,R/D为2.5时,ξ为0.13,当R/D大于2.5时,减少效果就不明显了。
一般应采用R/D为2.0~2.5,这样局部阻力系数ξ可小些。
需要说明的是,这里所指的风管弯头是指的光滑圆风管,在制造中,一般都是分成5段制作,放样、滚圆,再咬边或焊接成一个整体(俗称虾米弯),而这样一个90°的虾米弯头,其阻力系数比光滑园风管弯头的又要大,如:
R/D为1时,虾米弯的ξ值为0.33,R/D为2时,ξ为0.19,而这是设计者们通常忽视的地方。
更有些厂家为降低造价,多采用R/D为1,这是不可取的。
这些地方累积起来,管网系统的压力损失就大了。
风管弯头的局部阻力系数ξ同时还与弯曲角度成正比,如弯曲角度越大,则阻力系数越大,一般应尽量采用45°、60°和90°的弯头。
3抽风系统的管网特性及工作点分析
3.1离心风机特性
离心风机即使在转速相同时,它所输送的风量也可能各不相同。
系统的压力损失小时,要求的风机风压ΔP=ξ2ν2ρ就小,则输送的风量就大;反之,系统的压力损失大时,所要求的风机风压就大,则输送的风量就小。
风机的特性曲线见图1。
从中可看出,风机可以在各种不同的风量下工作。
在抽风系统中,风机将按其特性曲线上的某一点工作,在此点上,风机的风量与系统中的压力得到平衡,由此也确定了风机的风量。
但正是风机的这种自动平衡的性能,致使有时在实际情况下,风机的风量和风压满足不了设计要求。
图1风机的特性曲线
3.2抽风系统管网特性
风机在抽风管路系统中工作时,其风量、风压等参数不仅取决于风机本身的性能,还与整个管网系统的特性有关(管网特性曲线及工作点见图2)。
管路系统的总阻力由系统中各种压力损失的总和、吸入气体所受压力与排出气体所受压力的压力差(当由大气吸入气体并排出大气时,压差等于0)和由管网排出时的动压3部分组成,即图中的P2=f2(Q)曲线所示。
更多情况下,管路特性曲线只取决于管路系统的总阻力和管网排出时的动压,且二者均与流量Q的平方成正比;管路特性曲线P2=f2(Q)和风机的性能曲线P1=f1(Q)的交点D也就是风机的工作点。
当管网中实际阻力大于风机的额定风压时,则风量会减少;反之,当管网中实际阻力小于风机的额定风压时,则风量会增大(管内特性曲线与风机性能关系见图3)。
图2管网特性曲线及工作点图3管内特性曲线与风机性能曲线
如上所述,喷漆室在使用一段时间后,由于管网系统中阻力逐渐变大,风机渐渐无法克服系统的压力损失,致使抽风量逐步降低,无法将过喷的漆雾及有机溶剂抽出,造成漆雾外溢到车间里;同时,喷漆室内工件表面附近的空气中充斥着粒径大小不等的漆雾颗粒,很多黏在工件表面,影响表面喷涂质量。
还要指出的是:
一般风管系统中的局部阻力计算是建立在一个理想的管网结构和静态的模型基础上的,但实际上多种结构设计本身的不足和在使用过程中动态的变化,使得所计算的局部阻力和实际使用中的风阻差别很大,这也是现今一些喷漆室的问题所在。
4流场控制方程的建立
通风机内流速较低,可视为不可压缩流动,以恒定角速度旋转的叶轮中,当选用与叶轮一起旋转的非惯性坐标系来描述相对运动时,可认为叶轮内的相对运动是定常的。
因此叶轮内不可压缩,均质,密度为常数的连续性方程和运动方程为
(1)质量守恒方程
(2)动量守恒方程
式中W——相对速度;
P——压强
f——质量力;
μ——粘性系数;
R——半径;
-2ω×W——哥氏力;
-ω×(ω×R)——离心力。
(3)湍动能方程
(4)湍动能耗散率方程
(5)湍流粘度系数方程
式中C1,C2,σK,σε,Cμ——经验常数;
Ui,Uj——i,j方向的速度;
Xi,Xj——i,j方向的节点坐标;
ρ——流体密度;
P——压力;
Fi——体积力;
η,ηt——层流和湍流的粘度系数;
K——湍动能;
Ε——湍动能耗散率。
5计算对象及边界条件
5.1 风机模型参数
分析对象为4-73№10D离心通风机,由进气室、集流器、叶轮和蜗壳组成。
在Pro/E中建立模型,为解决问题的方便,在整机的装配中让绝对坐标和相对坐标处于同一位置,原点位于叶轮后盘中心外壁上,X轴负方向为蜗壳出口方向,Y轴负方向为蜗壳的进气方向,Z轴正方向为进气室进口方向。
叶片后倾,进、出口角分别为32°、45°,叶轮内径720mm,叶轮外经1000mm,叶片进口宽350mm,叶片出口宽250mm,进气室吸风口为1300mm×600mm,蜗壳宽650mm,出风口为900mm×650mm,叶片12个,转1200r/min。
5.2 网格划分
在GAMBIT中对流道区域划分网格如图4所示。
由于风机结构较复杂,采取四面体和六面体网格相结合的方式划分,网格共计676045。
叶轮流动区域采用旋转参考系MRF坐标法;叶片、前盘和后盘采用相对静止参考系;进气室、集流器和蜗壳采用绝对静止参考系。
图4 4-73№10D通风机整体网格
5.3 计算方法及假定
(1)假定流动是稳定、粘性、不可压缩;流动过程中忽略质量力作用;
(2)叶轮进口和集流器间有间隙,但在计算中处理为0,避免间隙区域压力梯度过大;
(3)旋转坐标系下离散方程采用压力速度耦合SIMPLE算法,湍流模型采用标准k-ε方程,使用标准壁面函数法。
5.4边界条件
进口:
按照容积流量计算所得,采用均匀进口,速度12.6m/s。
出口:
设置压力出口静压为大气压,空气密度为1.2kg/m3。
6结果分析
6.1静压分析
由图5可看出,静压从进口至出口逐渐变化,在蜗壳外壁面达到最大,由于出口存在流动损失而使此处的静压有所下降,这与文献[6]结论相符。
由图5a可知,由于受到蜗壳的非轴对称性影响,蜗壳较低静压处与叶轮中心不在同一轴上;由图5b可知,在进气室的拐弯处和蜗舌处,由于这两者的形状发生变化,导致静压较低。
图5(a)整机蜗壳壁面后视静压分布
图5(b)整机蜗壳、进气室前室静压分布
6.2Y轴方向静压分析
Y轴为叶轮中心轴,叶轮后盘与蜗壳外壁有40mm的间隙,在Y轴方向截取面:
Y=-20mm如图6a;Y=150mm如图6b;Y=250mm如图6c;Y=350mm如图6d。
从4个图中看出,叶轮压强分布并不因为叶轮的轴对称而对称,渐扩螺旋蜗壳是非轴对称的,叶轮进口处静压最低。
叶轮内静压中心偏向蜗壳扩大处,出叶轮后静压逐渐增大在蜗壳外壁达到最大。
由于流动损失的存在,静压沿着蜗壳出口逐渐降低。
图6(a)Y=-20mm后盘与蜗壳外壁间隙中间面静压
图6(b)Y=150mm叶轮轴向中间面静压
图6(c)Y=250mm叶轮出口与前盘接触轴向面静压
图6(d)Y=350mm叶轮进口与前盘接触轴向面静压
6.3叶轮区域静压分析
叶轮区域的静压分布如图7所示。
图7(a)叶轮壁面静压(b)叶轮区域前盘和叶轮出口静压
叶片非工作面和前盘附近,特别是两者的交汇区域积累了一个低能流体区,静压、相对速度均较低,此处形成了尾迹区,但是尾迹区不是完全的“死水区”,有流体通过只是速度较低。
叶片工作面和前盘附近的流体静压、相对速度均较高,此处形成了射流区。
Fisher和Thpo-ma用颜料做离心泵叶轮中的显示试验,曹淑珍等用PIV法进行三维流动测定,根据流动照片也验证这一区域的存在。
这就是后来吴玉林等学者所说的射流-尾迹流动结构。
6.4叶片静压分析
叶片工作面图8a上的静压比非工作面图8b上的高且分布明显不同:
叶片工作面上静压分布不均,由分布可看出85%以上的做功来自于工作面;非工作面上静压分布较均匀,从叶片根部向顶端逐渐增大。
在单个叶道内,两侧壁附面层中的气流前进的速度比较低,气体受到压力差的作用从高压区流向低压区,这种流动与主气流方向垂直从而产生了二次流。
图8(a)叶片工作面静压分布(b)叶片非工作面静压分布
6.5 整机全压分析
包括全部外壁时无法看清内部全压分布,取图9所示分析。
图9壁面全压侧视图
从图9很清楚地看出全压的变化分布情况,特别是在集流器和叶轮区域变化最为明显。
在集流器处全压很低这是由于气流从轴向开始向径向转变而产生的。
叶轮区域依赖叶轮做功,全压在叶道内逐渐升高,且在叶片工作面出口处达到最大,进入蜗壳后由于流动损失存在又逐渐降低。
这两个区域流动情况差别很大,这是由于流道的位置不同和蜗壳的非对称性引起的。
所以对整个通风机来说,不能单单研究某个部分或对某个流道计算,因为这不但难反映整体流场的实际情况,而且计算的边界条件也很难确定,这就为计算的准确性、合理性带来困难。
6.6流道区域速度分析
此区域速度大小变化不太明显,但是受旋转的后盘和静止的蜗壳壁的共同作用使这部分流体产生了扭曲,流体旋转的中心接近蜗舌处与叶轮内的流动完全不在同一轴上,这是整机模拟得到的又一重要现象。
在前盘和蜗壳间的流体速度变化较明显,气流在叶轮出口处突然扩压,导致气流速度降低与主流气体发生冲击扰动,从而在蜗舌处产生了二次流风机叶轮中截面上的速度分布,从中看出流体从叶轮进口到叶轮出口方向速度逐渐增大,出叶轮后速度逐渐降低。
在靠近蜗壳出口处的叶轮通道内的速度比其他部分的叶轮通道内速度小,因此计算风机叶轮通道流场的时候,假设每个叶轮通道都是相同的也是不对的。
蜗壳出口处,可看到在出口的右下角有二次流的现象出现,此处位于蜗壳扩大一方近蜗舌处,是受到蜗壳出口流道的主流和蜗舌处的扰流共同作用而产生。
从涡流的位置来看,上部涡流比较靠近蜗壳的前壁面处,下部涡流比上部涡流强烈,且靠近蜗壳后壁面处。
对图综合分析,可以得出流体在蜗壳内不是以平流流出,而是以麻花状旋流状态流出。
看出在蜗壳出口流道内有回流产生,并且由此图可以清楚的看到流体不是平流而是扭曲着旋流流出。
显示气流在进气室内的变化不大,且在进入叶轮中心后流动比较均匀,流速随着叶片的方向逐渐增大,在前盘一方的蜗壳扩大处有二次流产生且比较明显。
同时也可以看出在后盘和蜗壳壁的间隙处、蜗舌处二次流较多较强,所以此处的噪声比较大,可为噪声的分析提供理论依据。
蜗壳出口的延伸部分很明显的有股较强的气流,这也是吴玉林等所说的尾流—射流结构。
7结论
本文有针对性地对离心通风机内部湍流场进行三维数值模拟,观察了离心通风机内部流动情况,重点分析了流道内部各个部分的压强和流场,得出如下结论:
(1)发现了由于整机的非轴对称性而产生了流体区域的压强和流速的非轴对称性。
后盘与蜗壳间隙中的流体流动的中心偏向蜗舌处,叶轮区域内部压力场和流场的中心不是沿中心轴方向,而是偏离中心轴。
蜗壳内部整体的流动像扭曲的麻花状旋流流出;
(2)结果显示叶片和前盘间,蜗壳出口处存在尾流-射流现象;
(3)靠近叶轮前盘的叶片处所受全压偏高于叶根处的压力。
工作面上的压力大于非工作面叶片上的压力,由于压力差的产生,从而使流体从高压向低压流动产生了轴向的二次流现象。
参考文献
[1]曹淑珍,祁大同,张义云,等.小流量工况下离心风机蜗壳内部的三维流动测量分析[J].西安交通大学学报,2002.
[2]吴玉林,陈庆光,刘树红.通风机和压缩机[M].清华大学出版社,2005.1.
[3]徐宝仁.变频调速泵特性与节能的探讨[J].农业装备技术,2008.
[4]孙宏雁.高压变频技术在生产用水系统中的应用[J].一重技术,2008.
[5]郭立君.泵与风机[M].北京中国电力出版社,2004.
[6]杨乃乔.液力调速与节能[J].节能与安全,2008.
[7]关凡醒.现代泵技术手册[M].北京:
北京宇航出版社,1995.
[8]机械工业部第四设计研究院.油漆车间设备设计[M].北京:
机械工业出版社,1985.
[9]陆耀庆.供暖通风设计手册[M].北京:
中国建筑工业出版社,1987.
[10]长春冶金建筑学校.通风工程[M].北京:
中国建筑工业出版社,1981.
[11]陆耀庆.供暖通风设计手册[M].北京:
中国建筑工业出版社,1987.
[12]苏福临,邓沪秋.流体力学泵与风机[M].北京:
中国建筑工业出版社,1985.
[13]王嘉冰,区颖达.多翼离心风机的内流特性及其噪声研究[J].流体机械,2004
[14]刘路.翼离心风机叶轮的结构优化研究[D].浙江杭州:
浙江工业大学,2009.
[15]王维斌.对旋式通风机全流场内压力脉动及气动噪声特性的数值研究[D],山东青岛:
山东科技大学,2009.
[16]陈怀修,李嵩.利用三维数值模拟改进离心通风机设计[J].风机技术,2003.
[17]张莉,王启杰,陈汉平.离心叶轮机械内部非定常流动的数值计算[J].风机技术,2004.
[18]王福军,张玲,张志闽.轴流泵不稳定流场的压力脉动特性研究[J].水利学报,2007.
[19]邵杰,刘树红,吴墒锋,吴玉林.轴流式模型水轮机压力脉动试验与数值计算预测[J].工程热物理学报,2008.
[20]张梁,吴伟章,吴玉林,陶星明,刘树红.混流式水轮机压力脉动预测[J].大电机技术,2002.
[21]吴墒锋,吴玉林,刘树红.轴流式水轮机摆度对压力脉动的影响[J].工程热物理学报,2007.
[22]王福军.计算流体动力学分析.北京:
清华大学出版社,2004.
[23]童秉纲.孔祥言,邓国华,等.气体动力学,北京:
高等教育出版社,1995.
[24]EspinaPI,PiomelliU.StudyoftheGasJetinaClose-coupledGas-metalAtomizer.TechnicalReport,AmericanInstituteofAeronauticsandAstronautics,98-0959.1998.
[25]SinghDD,DangwalS.Effectsofprocessparametersonsurfacemorphologyofmetalpowdersproducedbyfreefallgasatomization.JMaterSci,2006,41(12):
3853—3860.
[26]JeyakumarM,GuptaGS,KumarS.Modelingofgasflowinsideandoutsidethenozzleusedinspraydeposition.JMaterProcessTech,2008,203(1-3):
471—479.
[27]Meakhail,T.,Zhang,L.,Du,Z.H.,Chen,H.P.,andJansen,W.,2001,“TheApplicationofPIVintheStudyofImpellerDiffuserInteractioninCentrifugalFan.PartII-Impeller-VanedDiffuserInteraction,”ProceedingsofTheASMEFluidEngineeringDivision-IMECE2001/FED-24953November11-16,2001,NewYork,USA.
[28]FisherK,ThpomaD.InvestigationoftheFlowConditioninaCentrifugalPuma.TransitionofASME,HYD,1932,54(8):
45-56.
【感谢您的阅览,下载后可自由编辑和修改,关注我每天更新】