三爪卡盘的改进设计.docx
《三爪卡盘的改进设计.docx》由会员分享,可在线阅读,更多相关《三爪卡盘的改进设计.docx(31页珍藏版)》请在冰豆网上搜索。
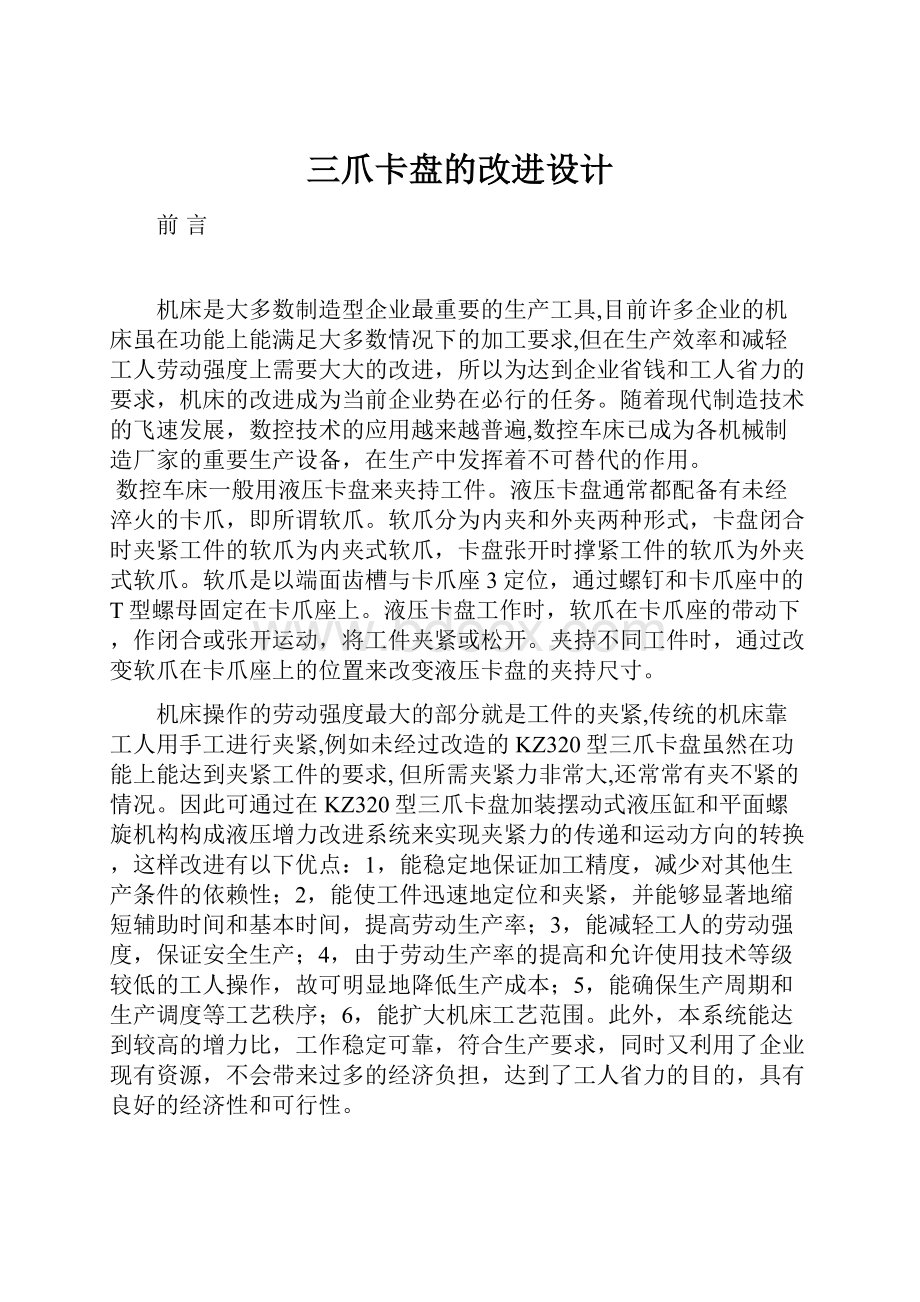
三爪卡盘的改进设计
前言
机床是大多数制造型企业最重要的生产工具,目前许多企业的机床虽在功能上能满足大多数情况下的加工要求,但在生产效率和减轻工人劳动强度上需要大大的改进,所以为达到企业省钱和工人省力的要求,机床的改进成为当前企业势在必行的任务。
随着现代制造技术的飞速发展,数控技术的应用越来越普遍,数控车床已成为各机械制造厂家的重要生产设备,在生产中发挥着不可替代的作用。
数控车床一般用液压卡盘来夹持工件。
液压卡盘通常都配备有未经淬火的卡爪,即所谓软爪。
软爪分为内夹和外夹两种形式,卡盘闭合时夹紧工件的软爪为内夹式软爪,卡盘张开时撑紧工件的软爪为外夹式软爪。
软爪是以端面齿槽与卡爪座3定位,通过螺钉和卡爪座中的T型螺母固定在卡爪座上。
液压卡盘工作时,软爪在卡爪座的带动下,作闭合或张开运动,将工件夹紧或松开。
夹持不同工件时,通过改变软爪在卡爪座上的位置来改变液压卡盘的夹持尺寸。
机床操作的劳动强度最大的部分就是工件的夹紧,传统的机床靠工人用手工进行夹紧,例如未经过改造的KZ320型三爪卡盘虽然在功能上能达到夹紧工件的要求,但所需夹紧力非常大,还常常有夹不紧的情况。
因此可通过在KZ320型三爪卡盘加装摆动式液压缸和平面螺旋机构构成液压增力改进系统来实现夹紧力的传递和运动方向的转换,这样改进有以下优点:
1,能稳定地保证加工精度,减少对其他生产条件的依赖性;2,能使工件迅速地定位和夹紧,并能够显著地缩短辅助时间和基本时间,提高劳动生产率;3,能减轻工人的劳动强度,保证安全生产;4,由于劳动生产率的提高和允许使用技术等级较低的工人操作,故可明显地降低生产成本;5,能确保生产周期和生产调度等工艺秩序;6,能扩大机床工艺范围。
此外,本系统能达到较高的增力比,工作稳定可靠,符合生产要求,同时又利用了企业现有资源,不会带来过多的经济负担,达到了工人省力的目的,具有良好的经济性和可行性。
本设计是一种变型设计,即在原有产品的基础上,基本工作原理和总体结构不变,通过改变或更换部分机构,形成变型产品。
由于其开发周期较短,经济性好,因此,有广阔的市场前景,预期将能产生好的经济效益和社会效益。
第1章
现有装置概论
1.1各种夹具的比较
在机床上加工工件时,我们可以看到两种不同的情况:
一种是用划针或指示表等量具,按工件的某一表面,或者按工件表面上所划的线进行找正,使工件在机床上处于所需要的正确位置,然后夹紧工件进行加工;另一种是把工件安装字夹具上进行加工。
为了在工件的某一部位上加工出符合规定技术要求的表面,一般都按工件的结构形状,加工方法和生产批量的不同,采用各种不同的装置将工件准确,方便的而可靠地安装在机床上,然后进行加工.这种用来安装的工件以确定工件与切削刀具的相对位置并将工件夹紧的装置称为“机床夹具”。
在实际的生产中,例如活塞,连杆的生产线上,几乎每道工序中都采用了夹具。
十分明显,如果不采用夹具,不但工件的加工精度难以保证,而且加工生产率也会大大降低,有时甚至会造成无法加工的情况。
除了机床加工时需要使用夹具外,有时在检验,装配等的工序中也要用到夹具,因之在这种场合中用到的夹具可分别称为“检验夹具”和“装配夹具”。
机床夹具通常是指装夹工件用的装置:
至于装夹各种刀具用的装置,则一般称为“辅助工具”。
辅助工具有时也广义地包括在机床夹具的范围内。
按照机床夹具的应用范围,一般可分为通用夹具,专用夹具和可调整式夹具等。
通用夹具是在普通机床上一般都附有通用夹具,如车床上的卡盘,铣床上的回转工作台,分度头,顶尖座等。
它们都一标准化了,具有一定的通用性,可以用来安装一定形状尺寸范围内的各种工件而不需要进行特殊的调整。
但是,在实际生产中,通用夹具常常不能够满足各种零件加工的需要;或者因为生产率低而必须把通用夹具进行适当的改进;或者由于工件的形状,加工的要求等的不同须专门设计制造一种专用夹具,以解决生产实际的需要。
专用夹具是为了适应某一工件的某一工序加工的要求而专门设计制造的,其功用主要有下列几个方面:
1.保证工件被加工表面的位置精度,例如与其他表面间的距离精度,平行度,同轴度等。
对于外行比较复杂,位置精度要求比较高的工件,使用通用夹具进行加工往往难以达到精度要求。
2.缩短了工序时间,从而提高了劳动生产率。
进行某一工序所需要的时间,其中主要包括加工工件所需要的机动时间和装卸工件等所需要的辅助时间两部分。
采用专用夹具后,安装工件和转换工位的工作都可以大为简化,不再需要画线和找正,缩短了工序的辅助时间并且节省了画线这个工序,从而提高了劳动生产率.在生产中由于采用了多工件平行加工的夹具,使同时加工的几个工件的机动时间将与加工一个工件的机动时间相同。
采用回转式多工位连续加工夹具,可以在进行切削加工某个工件的同时,进行其它工件的装卸工作,从而使辅助时间与机动时间相重合。
总之,随着专用夹具的采用和进一步改善,可以有效地缩短工序时间,满足生产不断发展的需要。
3.采用专用夹具还能扩大机床的工艺范围。
例如在普通车床上附加镗模夹具后,便可以代替镗床工作;装上专用夹具后可以车削成型表面等,以充分发挥通用机床的作用。
4.减轻劳动强度,保障安全生产。
根据生产需要,采用一些气动,液压或其它机械化,自动化程度较高的专用夹具,对于减轻工人的劳动强度,保障生产安全和产品的稳质高产都有很大作用。
加工大型工件时,例如加工车床床身上,下两面上的螺孔,需要把床身工件翻转几次进行加工,劳动强度大而且不安全。
采用电动回转式钻床夹具后,就能够达到提高生产效率,减轻劳动强度,保障生产安全的目的。
专用夹具在生产上起着很大的作用,那么是不是在任何场合都要设计和采用呢?
这个问题就是具体问题具体的分析。
上面说的关于专用夹具在生产中的作用,只是事物的一个方面。
另一方面,由于夹具的设计,制造和所用的材料等须消耗一定的费用,增加了产品的成本。
因之,在什么情况下采用什么样的夹具才是经济合算的,这是一个大问题,特别对于重大的、设计制造工作量大的专用夹具需与工人师傅等三者结合共同研究解决。
事物总是一分为二的,专用夹具也存在缺点,即专用夹具的专用性和产品多样性的矛盾。
由于专用夹具只适用于一个工件加工的某一个工序,因而随着产品品种的不断增多,夹具数量也不断上升,造成存放和管理上的困难;而当某产品不再进行生产时,原来的夹具一般都无法重新利用,造成浪费。
同时,专用夹具的设计生产时间周期长,与生产的迅速发展也有矛盾。
但是在当前成批生产的机械工厂中,多数还是采用通用机床加上专用夹具进行工件的机械加工。
可调整夹具是为了扩大夹具的使用范围,弥补专用夹具只适用与一个工件的某一特定工序的缺点,正在逐步推广使用可调整式的夹具。
可调整式夹具一般可分为标准化夹具,成组夹具和组合夹具等。
1.标准化夹具:
标准化夹具就是利用本厂已规格化了的部分或全部标准零件装配成的专用夹具。
专用夹具中的大件,如夹具体,以及定位元件,夹紧件和机械夹紧用的气缸部件等,经过标准化,尺寸规格化后有利于工厂成批准备配件,成批加工,这样可使夹具的设计,制造工作加快,节省费用。
另外,当产品更改,夹具不再使用时可以拆开,把标准零件保存起来,备以后使用。
2.成组夹具:
多品种,小批量生产的机械加工车间中,往往可以采用成组加工法。
采用成组加工法,是把多种产品的零件按加工所用的机床和刀具,夹具等工艺装备的共性分组,同一组的零件能在同一台机床上用共同的工艺装备和调整方法进行加工。
例如分成轴类,套类,盘类,齿轮,杠杆,支架类等各种零件。
成组夹具就是根据一组安装方法相类似的零件而设计的,只要稍作调整或更换夹具上的某些定位,夹紧件,就可以从加工某一工件转为加工另一工件。
3.组合夹具:
组合夹具是有一套专门设计制造,便于组装和拆卸的有各种不同的形状,不同尺寸规格并且有完全互换性和耐磨性的标准元件和合件所组成。
利用这些元件和合件,根据加工工件的需要可以组装成车、磨、铣、刨、钻、镗等工序用的各种不同的机床夹具。
夹具使用完毕,可以方便的拆开,洗净元件存放起来,留待以后组装新夹具时再用。
因之组合夹具是具有高度标准化和系列化元件的新型工艺装备。
关于组合夹具的问题,其设计原理基本相同。
在实际生产中应用的夹具很多,分类方法也有很多种。
通常还可按使用夹具的工序不同分为车床夹具,铣床夹具……等;还可以根据在机床上运动的特点归并成以下几类,
(1)车床类夹具:
包括车床、内外圆磨床、螺纹磨床用夹具,其特点是夹具与工件一起作旋转运动。
(2)铣床类夹具:
包括铣床、刨床、平面磨床等机床用夹具,其特点是夹具固定于工作台上,只作纵向或横向往复运动或回转运动。
(3)钻、镗床类夹具:
用于在钻床上钻、扩、铰等工序或在镗孔工序,其实就是夹具固定在机床上,刀具通过夹具上的导向装置进行送进运动。
上述的各种夹具都是固定在机床上的,但是在自动线加工中,有的夹具带着工件由生产线的输送装置,挨着每台机床逐步向前输送,这类夹具通常称为“随行夹具”。
自动线上的随行夹具除了完成工件的定位、支承和夹紧外,还带着工件沿自动线的加工机床进行定位(相对于每台机床的刀具位置)、夹紧,待加工完了再自动送至下一台机床加工,以便通过自动线的各台机床,完成工件的全部工序加工。
随行夹具主要适用于采用组合机床自动线加工,但又无良好的输送基面和定位基面的工件,以便将这种畸形工件先装夹于基面完整的随行夹具上,然后在通过自动线进行加工。
对一些有色金属等软件性材料的工件,虽然具有良好的输送基面,但为了保护工件的基面不受划伤,有时也采用随行夹具。
通用可调夹具,若产品中有若干零件具有相似性,有选用通用可调整夹具的可能,应进一步探索,应用下面三方面分析判断
(1)工件结构要素的相似性:
主要是被加工表面形式和部位的相似,工序内容和技术要求基本相似;能有相似或相同的定位基准和定位方式。
(2)有可能采用功能相同的定位方式和夹紧方式(包括夹紧动力源)。
(3)工件尺寸要素相似,如定位基准和外廓尺寸的近似程度,看能否使用,可调夹具结构紧凑,布局协调的夹具。
综上所述,机床夹具已成为机械加工中的重要装备。
机床夹具的设计和使用是促进生产发展的重要工艺措施之一。
随着我国机械工业生产的不断发展,机床夹具的改进和创造已成为广大机械工人和技术人员在技术革新中的一项重要任务。
1.2三爪卡盘的介绍
三爪卡盘是一种应用很广泛的夹紧装置,在生产过程中扮演着很重要的角色。
它能保证加工精度,提高整体工作效率,减轻劳动强度,充分发挥和扩大机床的工艺性能。
它具有以下居多的优点:
1.将数个夹盘边结安装于固定盘上,快速换模的目的可达成,省时迅速。
2.把油缸直接装在夹头内部,更能确保连结的稳定性、提升夹持力,其重心较低不占空间,倍增机械效益。
3.本体采用铬钼合钢,滑轨经硬化处理。
4.油压驱动可达省力目的,连接自控系统。
5.安装时只需配合T型螺丝安装简易。
6.与CNC车床夹盘之硬爪及生爪皆可替换。
7.切屑及冷却液不易进入夹盘内,确保夹盘寿命及精度。
1.3夹紧装置简介
1.3.1夹紧基本原理理论
夹紧的目的是保证工件在夹具中的定位,不致因工时受切削力,重力或伴生离心力,惯性力,热应力等的作用产生移动或振动。
夹紧装置是夹具完成夹紧作用的一个重要的而不可以缺少的组成部分,除非工件在加工过程中所受到的各种力不会使它离开定位时所需确定的位置,才可以设有夹紧装置。
夹紧装置设计的
优劣,对于提高夹紧的精度和加工作效率,减轻劳动强度都有很大的影响。
图1-1夹紧功能原理方案设计目录组成结构
分析各类夹具的基本功能要求可以将夹紧装置概括为两类:
第一类是性能要求,要指定位唯一性、定位稳定性,夹紧稳定性及总体约束;第二类要求是夹具的结构刚性、成本及易操作性、易于维修等要求。
本设计目录中功能项包括夹紧对象特征项、加工信息特征及夹紧要求特征。
夹紧对象特征项目:
包括夹紧对象类型、材料、形状、体积、数量、物理特性、磁性、导电性、刚性等信息。
加工信息特征项:
加工类型、机加工、装配、检测、焊接等、加工参数、切削参数、运动参数、几何参数等。
夹紧要求特征项:
主要指性能要求,包括定位要求、定位基准选择,如特征点、特征面。
夹紧力大小、夹紧方向、夹紧行程、夹紧松开速率、自锁性等。
元件功能分析:
夹紧功能主要包括四种元功能:
定位功能、传动功能、执行功能和分度功能等辅助功能。
定位功能由定位元件完成,定位元件按定位面特征分为平面定位元件、圆孔定位元件、外圆定位元件。
传动功能由中间递力机构完成,该机构一般有三个作用:
改变作用力的方向、大小和自锁作用。
目前常用的有以下机构:
斜楔机构、螺旋机构、圆偏心机构、杠杆铰链机构、连杆机构、联动机构、对中机构、定心机构等。
设计夹紧装置时,应满足下述主要要求:
1.夹紧装置在对工件夹紧时,不应破坏工件的定位,为此,必须正确选择夹紧力的方向及着力点。
2.夹紧力的大小应该可靠、适当,要保证工件在夹紧后的变形和受压表面的损伤不致超出允许的范围。
3.夹紧装置结构简单合理、夹紧动作要迅速、操作方便省力、安全。
4.夹紧力或夹紧行程在一定范围内可进行调整和补偿。
1.3.2夹紧座
在不考虑重力和其它的伴生力的情况下,夹紧力的大小既与切削力的大小有关,也与切削力对支承的作用有关。
W=KM(f1Rf1+f2Rf2)N(其中K=K1K2K3K4,K1=1.5~2,K2=1.2,K3=1.1~1.3,K4=1.2)
W=1.8X1.2X1.2X1.2X85X(0.2X7+0.2X7)N=740.28NM(切削扭矩)
Q需=KP/(f1+f2)=1.8X1.2X1.2X1.2X100/(0.2+0.2)=777.4NQ需(切削力)
为简化夹具的成本及考虑工厂实际情况,拟用螺钉夹紧装置。
计算螺钉的夹紧力:
W=2QL/D中/tg(α+φ1)。
此公式采用中的数据以M16标准螺纹计算。
α为螺纹升角;tgα=S/лD中;φ1螺纹摩擦角;D中螺纹中径;Q人工作用力;其中有f=0.1(螺母端面与工件间的摩擦系数),φ1=6。
34,;计算W=836.8公斤力。
很明显,可以使用螺钉夹紧机构。
见总装图:
夹紧座加工要求:
1.表面发蓝或其它的防锈处理;2.热处理:
T10A,淬火HRC60~64;渗碳深度0.2~0.6mm;3.锐边无毛刺;4.螺纹孔以国家标准的M16配做。
1.3.3夹紧支板
夹紧支板和夹紧座的目的相同,都是夹紧工件的,保证在加工过程中工件不移动,限制它的自由度,夹紧支板的工件接触装置拟用夹紧螺钉,支板在其中是辅助支承的,最终起决定作用的还是人的操作,不同人操作同样的夹具或者是在夹紧的过程中用力和速度的不同,都对工件的加工精度有影响。
由于取用的夹紧螺钉是一样的,前面已经计算过了,在此不重复了。
具体的结构见零件图。
夹紧支板加工要求:
1.表面发蓝或其它的防锈处理;2.热处理:
T10A,淬火HRC38~45;渗碳深度0.2~0.6mm;3.锐边无毛刺;4.螺纹孔以国家标准的M16配做。
1.3.4夹紧螺钉
根据公司的实际情况选用夹紧螺钉,人工操作。
节省成本,制造夹具的时间缩短并以国家标准的规格生产。
夹紧功能的原理方案设计目录是设计目录应用的具体体现,由于夹具种类繁多,如何对其进行抽象化整理,以利于运用设计目录的结构形式,还需要更深入的研究。
建立原理方案设计目录涉及的知识面较广,难度较大,目前本身的构造规律也很复杂。
这里仅作最基本的原理方案设计研究。
第2章总体方案的设计
2.1设计方案
2.1.1设计方案的提出
本设计是在三爪卡盘的结构基础上增设一个液压机构和一个平面螺旋机构来实现夹紧省力的。
2.1.2几种典型夹紧机构的比较:
1.楔块夹紧
楔块夹紧是夹紧机构中最基本的一种形式。
其它一些夹紧如偏心轮、螺钉等都是这种楔块的变型。
图2-1所示为楔块夹紧钻模。
图2-1楔块夹紧
楔块夹紧的工作特点:
(1)楔块的自锁性:
当原始力Q一旦消失或撤除后,夹紧机械在纯摩擦力的作用下,仍应保持其处于夹紧状态而不松开,以保证夹紧的可靠性。
楔块的自锁条件为:
α≤φ1+φ2。
为保证自锁可靠,取α=5~7°;
(2)楔块能改变夹紧作用力的方向;
(3)楔块具有增力作用,增力比i=Q/F≈3;
(4)楔块夹紧行程小;
(5)结构简单,夹紧和松开需要敲击大、小端,操作不方便。
材料:
楔块一般用20号钢渗碳淬火达到HRC58~62,有时也用45号钢淬硬至HRC42~46。
2.螺旋夹紧机构
将楔块的斜面绕在圆柱体上就成为螺旋面,因此螺旋夹紧的作用原理与楔块相同。
图2-2是最简单的单螺旋夹紧机构。
夹具体上装有螺母2,转动螺杆1,通过压块4将工件夹紧。
螺母为可换式,螺钉3防止其转动。
压块可避免螺杆头部与工件直接接触,夹紧时带动工件转动,并造成压痕。
图2-2单螺旋夹紧
1—螺杆2—螺母3—螺钉4—压块
螺旋夹紧的工作特点:
1)自锁性能好
通常采用标准的夹紧螺钉,螺旋升角α甚小,如M8~M48的螺钉,α=3°10′~1°50′,远小于摩擦角,故夹紧可靠,保证自锁。
(2)增力比大(i≈75)
(3)夹紧行程调节范围大
(4)夹紧动作慢、工件装卸费时
3.偏心夹紧
(1)圆偏心夹紧的自锁条件:
D/e≥14。
D/e值叫做偏心轮的偏心特性,表示偏心轮工作的可靠性,此值越大,自锁性能好,但结构尺寸也大。
(2)增力比:
i=12~13。
偏心夹紧的主要优点是操作方便、动作迅速、结构简单,其缺点是工作行程小、自锁性不如螺旋夹紧好、结构不耐振,适用于切削平稳且切削力不大的场合,常用于手动夹紧机构。
由于偏心轮带手柄,所以在旋转的夹具上不允许用偏心夹紧机构,以防误操作。
4.联动夹紧机构
联动夹紧机构是操作一个手柄或用一个动力装置在几个夹紧位置上同时夹紧一个工件(单件多位夹紧)或夹紧几个工件(多件多位夹紧)的夹紧机构。
根据工件的特点和要求,为了减少工件装夹时间、提高生产率、简化结构,常采用联动夹紧机构。
在设计联动夹紧机构时应注意的问题:
(1)必须设置浮动环节,以补偿同批工件尺寸偏差的变化,保证同时且均匀地夹紧工件。
(2)联动夹紧一般要求有较大的总夹紧力,故机构要有足够刚度,防止夹紧变形。
(3)工件的定位和夹紧联动时,应保证夹紧时不破坏工件在定位时所取得的位置。
5.定心夹紧机构
当工件被加工面以中心要素(轴线、中心平面等)为工序基准时,为使基准重合以减少定位误差,需采用定心夹紧机构。
定心夹紧机构是指能保证工件的对称点(或对称线、面)在夹紧过程中始终处于固定准确位置的夹紧机构。
它的特点是:
夹紧机构的定位元件与夹紧元件合为一体,并且定位和夹紧动作是同时进行的。
定心夹紧机构按其工作原理分为两种类型,一种是按定位——夹紧元件等速移动原理来实现定心夹紧的,三爪自定心卡盘就是典型实例;另一种是按定位——夹紧元件均匀弹性变形原理来实现定心夹紧的机构,如弹簧夹筒、膜片卡盘、液性塑料等。
6.快速夹紧机构
众所周知,螺旋夹紧机构是应用最广的一种夹紧机构,它主要是利用螺纹直接夹紧工件,或者是与其他元件或机构组成复合夹紧机构来夹紧工件。
螺旋夹紧机构具有结构简单、制造容易、夹紧可靠、增力比大、行程不受限制等优点。
但同时也具有夹紧动作慢、辅助时间长、效率低等缺点,尤其是当用同一夹具频繁交替夹紧大小不同的工件时,更要不停的转动螺杆以改变行程(如型材切割机)。
为了使螺旋夹紧机构更好的发挥作用,扬长避短。
人们设计了各种各样的能快速夹紧的螺旋夹紧机构,本文就是笔者设计的快速夹紧机构。
整个夹紧机构结构如图1所示:
夹紧螺杆与夹具体为螺纹联结。
为便于旋转,夹紧螺杆右端安装手轮(或手柄);顶杆与夹紧螺杆间为较大的间隙配合,以使螺杆能滑动自如;防转销是可以防止螺杆转动的,在夹紧螺杆上防转螺钉的另一侧装有防止顶杆后退的定位销;为了改善夹紧效果,避免因顶杆转动带动工件偏转而破坏定位、破坏工件表面,还可在顶杆头部装上可摆动的光面压块或槽面压块。
整个操作过程极其简单,放置好工件后,根据工件大小直接将顶杆向左推抵工件或接近工件,此时定位销自动卡住顶杆,使之不能右移;此时转动夹紧螺杆,即可完成工件夹紧工作。
本机构具有以下特点:
a.机构结构简单、尺寸、精度要求低、便于加工制造。
即使利用现有夹具改造也不复杂,只要把现有夹具螺杆稍做加工,再加工一顶杆即可。
b.夹紧迅速、快捷。
一般夹紧时转动螺杆不超过一圈。
例:
夹紧螺杆螺纹为M48×5,顶杆上齿条间距为5,则无论工件大小如何,推动顶杆时顶杆到工件的最小距离L<5,此时,夹紧螺杆最多再转动一周,便可将工件夹紧。
c.夹紧螺杆、顶杆和定位销为主要受力元件,在设计时要进行强度校核。
一般夹紧螺杆为铸钢或铸铁材料、顶杆、定位销采用45#钢,顶杆和定位销的齿牙部位要求进行适当热处理,以提高耐磨性和机械强度。
d.本机构行程调节快速方便,彻底避免了传统夹具频繁转动夹紧螺杆的繁琐工作,尤其适用于小修理厂或加工厂频繁更换工件的场合。
综上所述,采用快速夹紧机构最适合,它能缩短夹紧工件的时间,同时节约生产成本。
2.2液压缸简介
此设计的最终目的是达到在工件夹紧过程中的轻松省力的要求,达到省力要求的元件主要通过在原三爪卡盘上增设液压元件的,它与其他夹具动力装置相比具有以下特点:
1,液压油油压高、传动动力大,在生产同样原始作用力的情况下,液压缸的结构尺寸比气压的小许多倍;2.油液的不可收缩性使夹紧刚度高、工作平稳、可靠;3.液压传动噪声小、劳动条件比气压的好。
根据各方案采用元件的特点及机床本身的特征。
对可选择的元件进行比较:
1.采用液压马达虽然能将电能转换为液压机械能代替人的手工操作,同时,其摆动式结构有利于实现连续性夹紧,但由于液压马达体积比较大,不利于安装,且由于卡盘体在工作中高速旋转,故供电源很难接入,所以其可行性不大。
2.采用电液侍服阀能变电气信号为液压信号以实现流量或压力控制的转换,它控制灵活、精度高、快进性好、输出功率大装置。
但其体积大,不适合于安装,同时由于卡盘体高速旋转,电能不易实现安全输入,由于液压马达和电液侍服阀同样都还要依赖于外加压力油源,故在高速旋转的场合也不易实现。
3.液压缸是液压系统的执行元件,它把液体的压力能转化为机械能,它能实现增压的要求,将外加压力能转换成直线往复运动,且其结构简单,工作可靠,若能设法将直线往复运动转换为圆周运动,将能实现对工件的夹紧。
要实现省力,则要设计一个转换机构,使这个机构能提高输出力矩与输入力矩之比。
由以上分析可知,采用液压缸是最好的一种方案,且要求将锥齿轮输入的力最终转化为推动卡爪进给的力。
液压缸有直动缸和摆动缸两种:
直动缸需要一个转换机构才能将轴向直线运动转换为径向直线运动,会增加系统的复杂程度,减低紧凑性,这在高速运动场合是不允许的,同时,由于直动缸不能实现连续夹紧,当工件塑性较大时,就有夹不紧的可能,还不能进行反向夹紧,因此,这将大大缩小机车的加工应用范围。
摆动缸能实现连续夹紧,同时能将轴向压力转换为扭矩,因此可有效克服直动缸的上述不足。
同时,摆动缸由于其自身的结构,可实现与原有卡盘体的较好结合,因此,采用摆动缸是一种最理想的方案。
综上所述,本设计最终采用摆动式液压缸方案。
第3章各零部件的设计
3.1结构及原理
设计方案如图1所示,主要是在原有结构的基础上增加了一个螺旋盘,一个摆动油缸及柱塞等。
大锥齿轮背面加工出凹槽,圆柱活塞一端与槽配合,另一端装在液压缸定子叶片的孔中,端部装有弹簧,柱塞在弹簧作用下,一端始终与凹槽接触。
工作时利用转动杠转动小锥齿轮2带动大锥齿轮3,当卡爪7未接触工件时,圆锥螺旋弹簧5所受载荷较小,圆柱活塞4与大锥齿轮3无相对运动,缸体6随之一起转动,卡爪7径向移动,接近工件,此为空行程。
当卡爪7接触工件后,所受阻力激增,进
1.卡盘体