炼油厂一常减压工艺配管焊接方案.docx
《炼油厂一常减压工艺配管焊接方案.docx》由会员分享,可在线阅读,更多相关《炼油厂一常减压工艺配管焊接方案.docx(10页珍藏版)》请在冰豆网上搜索。
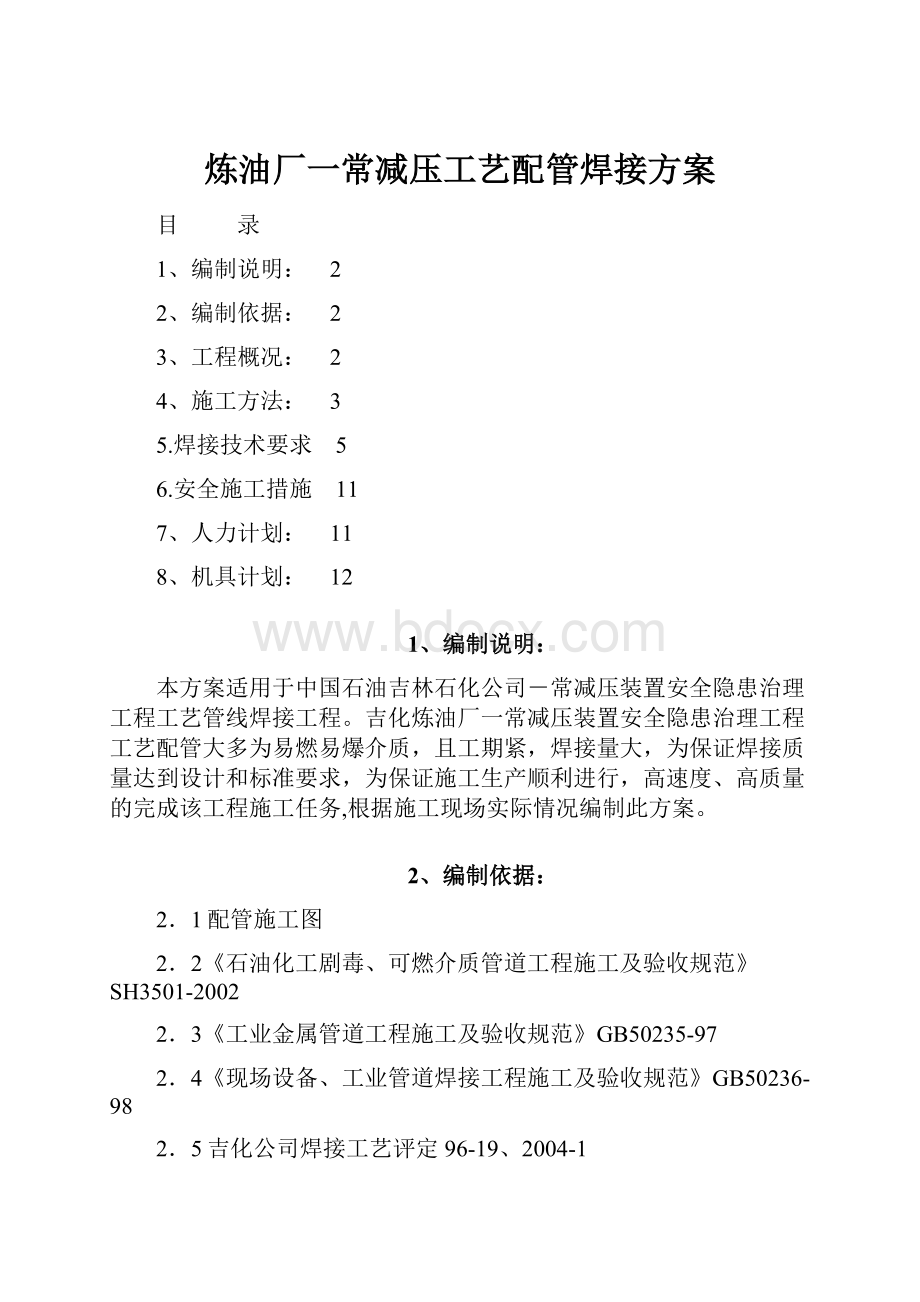
炼油厂一常减压工艺配管焊接方案
目 录
1、编制说明:
2
2、编制依据:
2
3、工程概况:
2
4、施工方法:
3
5.焊接技术要求 5
6.安全施工措施 11
7、人力计划:
11
8、机具计划:
12
1、编制说明:
本方案适用于中国石油吉林石化公司-常减压装置安全隐患治理工程工艺管线焊接工程。
吉化炼油厂一常减压装置安全隐患治理工程工艺配管大多为易燃易爆介质,且工期紧,焊接量大,为保证焊接质量达到设计和标准要求,为保证施工生产顺利进行,高速度、高质量的完成该工程施工任务,根据施工现场实际情况编制此方案。
2、编制依据:
2.1配管施工图
2.2《石油化工剧毒、可燃介质管道工程施工及验收规范》SH3501-2002
2.3《工业金属管道工程施工及验收规范》GB50235-97
2.4《现场设备、工业管道焊接工程施工及验收规范》GB50236-98
2.5吉化公司焊接工艺评定96-19、2004-1
3、工程概况:
本工程工艺配管包括冷换区、热油泵房、电脱盐、一原油罐区俄油泵、三台常减压塔及初顶空冷器等的管线,焊接当量约为30000DIA-IN,管道材质为20#钢和1Cr5Mo钢。
焊接工期三个月。
4、施工方法:
4.1施工程序:
4.1.120#钢焊接施工程序:
切割 打磨 组对 焊接 外观检查 无损检验 试压前核查
4.1.21Cr5Mo钢焊接施工程序:
切割 打磨 坡口着色检查 预热 组对 焊接 消氢 外观检查 无损检验 焊后热处理 硬度检验 试压前核查
4.2施工方法:
4.2.1φ≤57mm钢管焊接采用全氩弧,φ>57mm钢管采用氩弧焊+手工电弧焊。
支架采用手工电弧焊。
4.2.220#钢焊丝采用H08Mn2Si,焊条采用J507。
支架采用J422焊条。
1Cr5Mo钢焊丝采用H1Cr5Mo,焊条采用R507。
4.2.3切割采用机械切割或氧-乙炔火焰切割。
4.2.4坡口采用砂轮打磨,坡口角度60°-65°,单面坡口。
4.2.5焊机采用氩弧焊机和交、直流电焊机。
4.2.6预热、消氢和焊后热处理采用电加热,预热测温采用触点式测温仪,具体方法另编方案。
4.2.7 1Cr5Mo钢底层焊接必须充氩保护。
氩气纯度高于99.9%
4.2.8接管、三通、凸台焊接时第一层应采用氩弧焊,确保根部焊透,并在组对后要进行停点检查,经检查员检查合格后方可焊接。
4.2.9对于承插焊缝、法兰焊缝必须至少焊两层,层间接头要错开。
4.2.10焊接接头形式简图
图二 具有ФB>1.5ФA的支管连接
5.焊接技术要求
5.1一般规定
5.1.1凡是从事本工程的焊工,必须持有劳动部门颁发的焊工合格证书,而且只能焊符合自己考试合格项目的材料。
从事本工程的技术员、质检员必须有相应的证件,检测单位和检测人员必须有相应资质证书。
5.1.2焊条、焊丝应有产品质量证明书,焊条的药皮不得脱落或明显裂纹。
焊丝在使用前应清除其表面的油污、锈蚀等。
焊条应按说明书要求进行烘烤,并在使用中保持干燥。
5.1.3在施焊前必须确认材质后按要求进行领用焊丝、焊条,并做好记录。
领用焊条时须携带焊条筒,每个焊条筒内不允许装两样焊条以防用错。
5.1.4除焊接成型管件外的其他管子对接焊缝中心到管子弯曲起点的距离不应小于管子外径,且不应小于100mm;管子对接焊缝与支吊架边缘的距离不应小于50mm;同一直管段上两对接焊缝中心距离应满足下列要求:
当公称直径大于或等于150mm时不应小于150mm,公称直径小于150mm时不应小于管子外径。
5.1.5不应在焊缝及边缘开孔。
当不可避免时,应对开孔部位焊缝进行外观检查,外观合格后再进行射线探伤检验,确认无不允许缺陷时,方可进行下道工序施工。
5.2焊前准备
5.2.1在采用热加工方法加工坡口后,必须除去坡口表面及附近20mm范围内的氧化皮,熔渣及影响接头质量的表面层,并应将凹凸不平处打磨平整。
5.2.2焊件组对前应将坡口及其内外表面不小于10mm范围内的油、漆、垢、锈等清除干净,且不得有裂纹、夹渣等缺陷。
5.2.3除设计规定需进行冷拉伸或冷压缩的管道外,焊件不得进行强力组对。
5.2.4管子或管件对接焊缝组对时内壁应平齐,SHB级管道内壁错边量不宜超过管壁厚的10%,且不应大于1mm。
5.2.5不等厚对接焊件组对时,薄件端面应位于厚件端面之内;当内壁错边量超过4.2.4条规定或外壁错边量大于2mm时,应对焊件进行加工,斜坡高与长按1:
4比例加工。
如下图:
内壁尺寸不等时
5.2.6焊件组对应垫置牢固,并应采取措施,防止焊接过程中产生附加应力和变形。
5.2.71Cr5Mo钢坡口应做着色检验。
5.3焊接工艺要求
5.3.1定位焊接与正式焊接工艺相同,定位焊的位置应均匀分布在管周围。
5.3.2在施焊前应将所点焊处的两端打磨成斜坡口后进行底层的焊接,焊接时必须保证根部全熔透,其熔透高度:
≤50NPS的管子,内壁≯1.5mm;>50NPS的管子,内壁≯3mm。
5.3.3焊前预热:
a:
1Cr5Mo钢焊接前,应预热到250-350℃,应采取电阻加热方法,可委托检验所进行。
当焊件温度低于0℃时,应在始焊钢材100mm范围内预热到15℃以上才能焊接。
b:
异种钢焊接时,应按可焊性较差的一侧母材选择预热方式和温度。
c:
焊前预热的加热范围,应以焊缝中心为准,每侧不应小于焊件厚度的3倍,且不小于100mm。
d:
焊前预热过程中,焊件内外壁温度应均匀。
5.3.4施焊采用多层焊接,必须注意起弧和收弧的质量,并且没层的接头应错开20mm,并将没层之间的焊渣清理干净。
5.3.5与母材焊接的工卡具,其材质宜与母材相同或同一类别号,焊接工艺与正式焊接相同;拆除工卡具时不应损伤母材,拆除后应将残留焊疤打磨修整,与母材表面平齐,1Cr5Mo钢应做着色检查。
5.3.6严禁在坡口之外的母材表面引弧和试验电流,并防止电弧擦伤。
1Cr5Mo钢不允许有电弧擦伤,如果电弧擦伤超过0.5mm则进行补焊,焊接工艺与正式焊接相同;如果擦伤深度不超过0.5mm则直接打磨成圆滑过度。
5.3.7施焊过程中应保证起弧和收弧处的质量,收弧时应将弧坑填满,多层焊的层间接头应错开。
5.3.8管子焊接时,管内应防止穿堂风。
5.3.9除工艺或检验要求分次焊接外,每条焊缝宜一次连续焊完;当因故中断时应根据工艺要求采取保温缓冷或后热等防止产生裂纹的措施,再次焊接前应检查焊层表面,确认无裂纹后,方可按原工艺要求继续施焊。
5.3.101Cr5Mo钢
焊缝焊接完或中断焊接必须立即进行后热处理,后热处理温度为300-350℃,时间为15min。
后热处理后应保温缓冷。
5.3.111Cr5Mo钢焊缝焊接完后,应进行焊后热处理,热处理温度750-780℃,恒温时间每毫米壁厚3min,且总恒温时间不得少于30min。
升温至300℃后,升温速度不大于220℃/h。
降温速度不大于260℃/h,300℃以下,自然冷却。
5.3.12需预拉伸或预压缩的管道焊缝,组对时所使用的工卡具应在每个焊缝焊接完毕并检验合格后方可拆除。
5.4.焊接环境
5.4.1当施焊环境出现下列条件之一时又无防护措施不能进行施焊,现场必须设有温度计和湿度计,并做好记录:
相对湿度≥90%,
1Cr5Mo环境温度低于0℃时,
碳钢环境温度低于-20℃时,
风速≥8米/秒,
雨、雪天气。
5.4.2施焊温度要求
5.4.2.1对于碳钢,环境温度低于-20℃时,不可进行焊接。
5.4.2.2要求焊前预热的焊件,其层间温度应在规定的预热温度范围内。
5.5焊材的烘干使用制度
5.5.1焊材从库房领出后要妥善保管并经过严格烘干才能发放给焊工。
5.5.2保管焊条时,要按照材料的规定执行,存放地点要通风干燥,保持烘干室内相对湿度不大于60%,当超过时要进行去湿处理;室内温度不低于+5℃。
焊条要放在格架上,离开地面和墙壁的距离不小于300mm。
5.5.3要使用远红外线式焊条干燥箱和保温箱。
干燥箱、保温箱由焊条烘干员负责保管。
5.5.4焊条烘干之后,存放于保温箱内,要尽快使用完,保温箱温度始终保持在100-150℃。
5.5.5焊工领取焊条,一定要有焊条筒,无焊条筒或筒盖,可拒发焊条。
在一个焊条筒内,不准装入两种不同性质的焊条,以免用错。
领用时,一次不可多领,当湿度为80%—90%时,应保证在两小时内用完。
湿度小于80%时,使用时间不超过4小时。
5.5.6焊工领取焊条要有领取记录,必须是谁领谁签名不许带领;剩余焊条要返回焊条烘干室,而且要有返回记录。
焊条再烘干的次数不超过两次。
5.6焊后检查
5.6.1焊后应对焊缝表面进行100%检查,焊渣及熔合性飞溅应清理干净,不应有裂纹,未熔合,气孔,夹渣存在。
5.6.2焊缝表面加强高e≤1+0.2b1且不大于3mm。
5.6.3管道焊缝咬边深度不应大于0.5mm,连续咬边长度不应大于100mm,且焊缝两侧咬边总长不大于该焊缝全长的10%,咬边应进行打磨圆滑过渡或补焊修磨。
5.6.4射线检验的比例:
蒸汽等公用介质管线按GB50235-97执行;工艺介质管线按SH3501-2002标准执行,SH3501射线透视规定如下:
焊接接头射线检测百分率及合格等级
设计条件
检测百分率(%)
合格等级
压力(表压)P(Mpa)
温度t(℃)
SHA
任意
任意
100
Ⅱ
SHB
SHBⅠ
≥4
≥400
100
Ⅱ
≥4
-29≤t<400
20
Ⅱ
1<p<4
≥400
20
Ⅱ
1<p<4
-29≤t<400
10
Ⅱ
≤1
≥-29
10
Ⅱ
任意
<-29
100
Ⅱ
SHBⅡ
≥4
≥400
100
Ⅱ
≥4
-29≤t<400
10
Ⅱ
1<p<4
≥400
10
Ⅱ
1<p<4
-29≤t<400
5
Ⅲ
≤1
≥-29
5
Ⅲ
任意
<-29
100
Ⅱ
注:
①设计压力小于4Mpa(表压)的管道中,包括真空管道;