电极板冲孔模设计.docx
《电极板冲孔模设计.docx》由会员分享,可在线阅读,更多相关《电极板冲孔模设计.docx(36页珍藏版)》请在冰豆网上搜索。
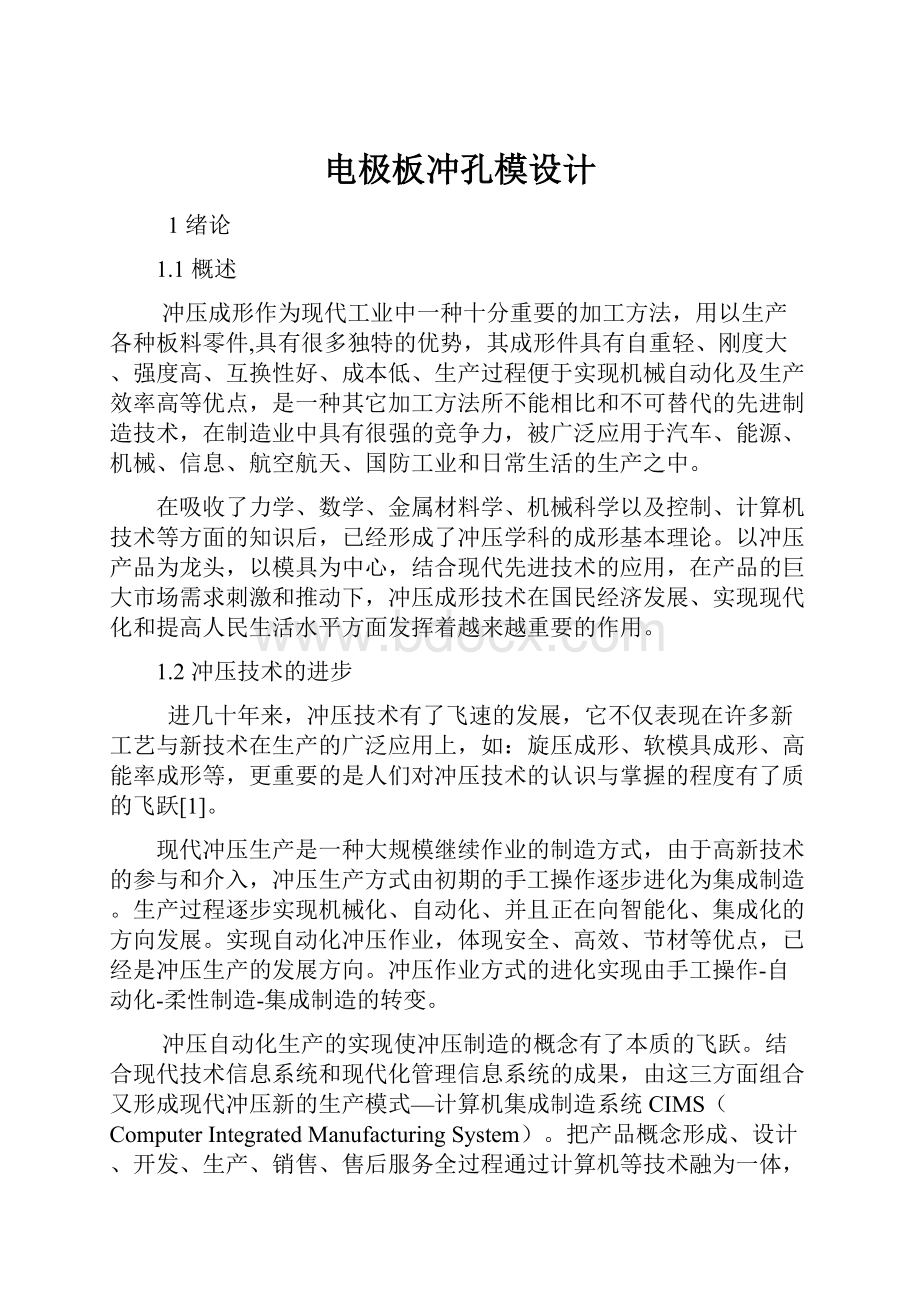
电极板冲孔模设计
1绪论
1.1概述
冲压成形作为现代工业中一种十分重要的加工方法,用以生产各种板料零件,具有很多独特的优势,其成形件具有自重轻、刚度大、强度高、互换性好、成本低、生产过程便于实现机械自动化及生产效率高等优点,是一种其它加工方法所不能相比和不可替代的先进制造技术,在制造业中具有很强的竞争力,被广泛应用于汽车、能源、机械、信息、航空航天、国防工业和日常生活的生产之中。
在吸收了力学、数学、金属材料学、机械科学以及控制、计算机技术等方面的知识后,已经形成了冲压学科的成形基本理论。
以冲压产品为龙头,以模具为中心,结合现代先进技术的应用,在产品的巨大市场需求刺激和推动下,冲压成形技术在国民经济发展、实现现代化和提高人民生活水平方面发挥着越来越重要的作用。
1.2冲压技术的进步
进几十年来,冲压技术有了飞速的发展,它不仅表现在许多新工艺与新技术在生产的广泛应用上,如:
旋压成形、软模具成形、高能率成形等,更重要的是人们对冲压技术的认识与掌握的程度有了质的飞跃[1]。
现代冲压生产是一种大规模继续作业的制造方式,由于高新技术的参与和介入,冲压生产方式由初期的手工操作逐步进化为集成制造。
生产过程逐步实现机械化、自动化、并且正在向智能化、集成化的方向发展。
实现自动化冲压作业,体现安全、高效、节材等优点,已经是冲压生产的发展方向。
冲压作业方式的进化实现由手工操作-自动化-柔性制造-集成制造的转变。
冲压自动化生产的实现使冲压制造的概念有了本质的飞跃。
结合现代技术信息系统和现代化管理信息系统的成果,由这三方面组合又形成现代冲压新的生产模式—计算机集成制造系统CIMS(ComputerIntegratedManufacturingSystem)。
把产品概念形成、设计、开发、生产、销售、售后服务全过程通过计算机等技术融为一体,将会给冲压制造业带来更好的经济效益,使现代冲压技术水平提高到一个新的高度。
1.3模具的发展与现状
模具是工业生产中的基础工艺装备,是一种高附加值的高技术密集型产品,也是高新技术产业的重要领域,其技术水平的高低已成为衡量一个国家制造水平的重要标志。
随着国民经济总量和工业产品技术的不断发展,各行各业对模具的需求量越来越大,技术要求也越来越高。
目前我国模具工业的发展步伐日益加快,“十一五期间”产品发展重点主要应表现在[2]:
(1)汽车覆盖件模;
(2)精密冲模;
(3)大型及精密塑料模;
(4)主要模具标准件;
(5)其它高技术含量的模具。
目前我国模具年生产总量虽然已位居世界第三,其中,冲压模占模具总量的40%以上[2],但在整个模具设计制造水平和标准化程度上,与德国、美国、日本等发达国家相比还存在相当大的差距。
以大型覆盖件冲模为代表,我国已能生产部分轿车覆盖件模具。
轿车覆盖件模具设计和制造难度大,质量和精度要求高,代表覆盖件模具的水平。
在设计制造方法、手段上已基本达到了国际水平,模具结构功能方面也接近国际水平,在轿车模具国产化进程中前进了一大步。
但在制造质量、精度、制造周期和成本方面,以国外相比还存在一定的差距。
标志冲模技术先进水平的多工位级进模和多功能模具,是我国重点发展的精密模具品种,在制造精度、使用寿命、模具结构和功能上,与国外多工位级进模和多功能模具相比,存在一定差距。
1.4模具CAD/CAE/CAM技术
冲压技术的进步首先通过模具技术的进步来体现出来。
对冲模技术性能的研究已经成为发展冲压成形技术的中心和关键。
20世纪60年代初期,国外飞机、汽车制造公司开始研究计算机在模具设计与制造中的应用。
通过以计算机为主要技术手段,以数学模型为中心,采用人机互相结合、各尽所长的方式,把模具的设计、分析、计算、制造、检验、生产过程连成一个有机整体,使模具技术进入到综合应用计算机进行设计、制造的新阶段。
模具的高精度、高寿命、高效率成为模具技术进步的特征。
模具CAD/CAE/CAM是改造传统模具生产方式的关键技术,是一项高科技、高效益的系统工程。
它以计算机软件的形式,为企业提供一种有效的辅助工具,使工程技术人员借助于计算机对产品性能、模具结构、成形工艺、数控加工及生产管理进行设计和优化[4]。
模具CAD/CAE/CAM技术能显著缩短模具设计与制造周期,降低生产成本和提高产品质量已成为模具界的共识。
模具CAD/CAE/CAM在近20年中经历了从简单到复杂,从试点到普及的过程。
进入本世纪以来,模具CAD/CAE/CAM技术发展速度更快,应用范围更广。
在级进模CAD/CAE/CAM发展应用方面,本世纪初,美国UGS公司与我国华中科技大学合作在UG-II(现为NX)软件平台上开发出基于三维几何模型的级进模CAD/CAM软件NX-PDW。
该软件包括工程初始化、工艺预定义、毛坯展开、毛坯排样、废料设计、条料排样、压力计算和模具结构设计等模块。
具有特征识别与重构、全三维结构关联等显著特色,已在2003年作为商品化产品投入市场。
与此同时,新加波、马来西亚、印度及我国台湾、香港有关机构和公司也在开发和试用新一代级进模CAD/CAM系统。
我国从上世纪90年代开始,华中科技大学、上海交通大学、西安交通大学和北京机电研究院等相继开展了级进模CAD/CAM系统的研究和开发。
如华中科技大学模具技术国家重点实验室在AutoCAD软件平台上开发出基于特征的级进模CAD/CAM系统HMJC,包括板金零件特征造型、基于特征的冲压工艺设计、模具结构设计、标准件及典型结构建库工具和线切割自动编程5个模块。
上海交通大学为瑞士法因托(Finetool)精冲公司开发成功精密冲裁级进模CAC/CAM系统。
西安交通大学开发出多工位弯曲级进模CAD系统等。
近年来,国内一些软件公司也竞相加入了级进模CAD/CAM系统的开发行列,如深圳雅明软件制作室开发的级进模系统CmCAD、富士康公司开发的用于单冲模与复合模的CAD系统Fox-CAD等[4]。
展望国内外模具CAD/CAE/CAM技术的发展,本世纪的科学技术正处于日新月异的变革之中,通过与计算机技术的紧密结合,人工智能技术、并行工程、面向装配、参数化特征建模以及关联设计等一系列与模具工业相关的技术发展之快,学科领域交叉之广前所未见。
今后10年新一代模具CAD/CAE/CAM系统必然是当今最好的设计理念、最新的成形理论和最高水平的制造方法相结合的产物,其特点将反映在专业化、网络化、集成化、智能化四个方面。
主要表现在[4]:
(1)模具CAD/CAM的专业化程度不断提高;
(2)基于网络的CAD/CAE/CAM一体化系统结构初见端倪;
(3)模具CAD/CAE/CAM的智能化引人注目;
(4)与先进制造技术的结合日益紧密。
1.5课题的主要特点及意义
该课题主要针对电极板零件,在对电极板冲孔、落料等工艺分析的基础上,根据冲裁件的生产批量、尺寸精度的高低、尺寸大小、形状复杂程度、材料厚度、冲模制造条件和冲压设备等多方面的因素,采用导柱导向冲裁模,保证了工件的尺寸和形状位置精度要求的同时,提高了工作效率。
本课题涉及的知识面广,综合性较强,在巩固大学所学知识的同时,对于提高设计者的创新能力、协调能力,开阔设计思路等方面为作者提供了一个良好的平台。
2.冲裁件的工艺性
零件名称:
电极板
生产批量:
4000件/年
材料:
硬紫铜
料厚:
5mm
如图冲裁工件的形状结构,电极板从总体上看是一个对称、简单、带双孔的零件电极板冲孔模主要实现对电极板上两孔的冲裁,所以冲裁件并无尖锐清角,细长悬臂和狭槽,冲裁件长162.6mm宽50.8mm属于小型冲裁件。
因为孔与孔之间孔与边缘之间的距离,受模具强度和冲裁件质量的限制,其值不能过小,由《冲压模具简明设计手册》查得距离a≥2t,t=5mm为材料厚度,但a不得小于3~4mm。
由图可知孔与孔之间距离为129.8mm,孔与边缘的距离为20,符合要求。
冲压件最小孔直径8.33mm大于冲孔的最小尺寸4.5mm,符合要求。
冲裁件所能达到的经济精度为IT12~14,为普通冲裁;由《冲压模具简明设计手册》查得冲裁件内经公差:
直径8.33mm的为0.36mm,直径14.3mm的为0.43mm;冲压件孔距公差为±0.575mm,公差为1.15mm。
冲裁件的表面粗糙度和毛刺:
查《冲压模具简明设计手册》第9页表2.6可知,取冲裁件的表面粗糙度为0.63mm[15]。
冲裁件的材料性能:
硬紫铜具有良好的导电性,满足做电极板的要求,由《冲压模具简明设计手册》第27页表2.34查出其抗剪强度为240Mpa,抗拉强度为300Mpa,具有良好的冲压性能,满足冲压工艺要求[15]。
3.模具的总体结构设计
3.1模具的定型
(1)联系冲裁模的结构特点建立以下三种方案
方案一:
采用无导向简单冲裁模
方案二:
采用导板导向简单冲裁模
方案三:
采用导柱导向简单冲裁模
各种方案分析:
方案一分析:
无导向简单冲裁模结构简单、尺寸小、质量轻、模具制造容易、成本低,但冲模在使用安装时麻烦,需要调试间隙的均匀性,冲裁精度低且模具寿命低。
它适用于精度要求低、形状简单、批量小或试制的冲裁件。
方案二分析:
导板导向简单冲裁模比无导向简单冲裁模高、使用寿命长、单模具较复杂、冲裁时视线不好。
不适合单个毛坯的送料冲裁。
方案三分析:
导柱导向简单冲裁模导向准确、可靠,能保证冲裁间隙均匀、稳定,因此冲裁精度比导板模具高,使用寿命长。
冲压加工方法所得到的产品质量稳定、材料利用率高、操作简单、生产率高等诸多优点而被广泛使用。
由于模具制造成本高,冲压加工的单件成本取决于生产批量,它对冲压加工的经济性起决定性作用。
综合考虑所冲零件的要求,采用方案三,导柱导向简单冲裁模。
3.2电极板冲孔模结构形式的确定
3.2.1送料方式的选择
按照送、出件方式,送料方式可分为手动、半自动和自动三种。
手动送料方式:
采用手工上下料,劳动强度高,生产效率低,适用于小批量生产。
半自动送料方式:
采用手工与机械结合的方法完成上下料与成形过程,适用于中批量生产。
自动送料方式:
与条料开卷展平装置连线使用,上下料与成形过程全部自动完成,适用于大批量生产。
由于零件为小批量生产、重量轻、工件较小,所以选择手动送料。
3.2.2定位方式的选择
工件在模具中的定位主要考虑定位基准、上料方式、操作安全可靠等因素。
定位板和定位销通常用于冲裁、修边和成形工件和毛坯轮廓的定位。
其中定位板又可以分为非圆孔用定位板、小型孔用定位板、中型孔用定位板、大型孔用定位板和拉伸工件冲底孔用定位板。
定位销:
适用于大型矩形冲压件或毛坯外形的定位。
非圆孔用定位板:
适用于非圆形孔的大型冲压件或毛坯的定位。
小型孔用定位板:
适用于带直径D<15mm孔的冲压件或毛坯的定位。
中型孔用定位板:
适用于带直径D=15~30mm孔的冲压件或毛坯的定位。
大型孔用定位板:
适用于带直径D>30mm孔的冲压件或毛坯的定位。
拉伸工件冲底孔用定位板:
用于拉伸工件冲底孔时定位。
考虑到工件的形状尺寸,采用定位销定位。
如图所示定位销的定位放式:
图3-1销钉定位方式
3.2.3卸料方式的选择:
卸料方式有刚性卸料和弹性卸料两种。
刚性卸料方式:
用于厚料和硬材,特点是卸料力大,使用安全,但送料操作受约束,常用于料厚大于0.5mm,平面度要求不高的工件,特别适用于卸料力较大的简单冲裁模。
弹性卸料方式:
弹性卸料板具有卸料和压料的双重作用,多用于冲制薄料,使工件的平整度提高。
借助弹簧、橡胶、或气垫等弹性装置卸料,常兼作压边、压料装置或凸模导向。
生产过程中常用橡皮直接卸料,用于小批量生产薄料冲裁卸料。
由于采用单个毛坯,手动操作送进和定位,并且材料不是太硬,所以采用弹性卸料方式,如图所示,采用卸料橡胶进行卸料,并通过螺钉与凸模固定板将卸料橡胶进行固定。
图3-2卸料方式
1下模座;2导柱;3弹性卸料板;4导套;5上模板;6卸料螺钉;7卸料橡胶;8大孔凸模;9定位销;10导套;11凸模固定板;12凹模固定板;13下模座;14大孔凹模;15螺钉;16工件
4.电极板冲孔工艺计算
4.1刃口尺寸确定原则
凹凸模刃口尺寸和公差的确定,直接影响冲裁生产的技术经济效果,是冲裁模具设计的重要环节,必须根据冲裁的变形规律、冲裁模的磨损规律和经济的合理性综合考虑,遵循以下原则。
设计落料模时,应以凹模尺寸为基准,间隙取在凹模上,靠减小其尺寸获得;设计冲孔模时,应以凸模尺寸为基准,间隙取在凹模上,靠增大其尺寸获得。
根据冲模的磨损定律,凹模的磨损使落料件轮廓尺寸增大,因此,设计落料模时凹模的刃口尺寸应等于或接近工件的下极限尺寸;凸模的磨损使冲孔件的孔径尺寸减小,因此,设计冲孔模时,凸模的刀口尺寸应等于或接近工件的上极限尺寸。
冲裁模在使用时,磨损间隙值将不断增大,因此,设计时无论是落料模还是冲孔模,新模具都必须选取最小合理间隙Zmin,使模具具有较长的寿命
根据工件尺寸公差的要求,确定模具刃口尺寸的公差等级,由《冲压模具简明设计手册》30页表2.38查得模具刃口尺寸的公差与冲裁件尺寸公差的关系[15]
模具刃口的尺寸公差
料厚t/mm
0.5
0.8
1.0
1.5
2
3
4
5
6
8
10
12
冲裁件尺寸公差
IT6~7
IT7~8
IT8~9
IT8IT8IT9IT10IT10
IT9IT10IT10IT12IT12IT12
IT12IT12IT12IT12IT12IT14IT14IT14IT14
表4-1模具刃口尺寸的公差与冲裁件尺寸公差的关系
所以冲裁件尺寸公差等级为IT12。
4.2凹凸模刃口间隙的选择
凸、凹模间隙值的大小对冲压制件质量、模具寿命、冲压力的影响很大,是冲压工艺与模具设计中的一个极其重要的工艺参数。
根据零件材料及料厚,查文献《冲压模具简明设计手册》取[15]:
4.3凹凸模的加工方法
模具凹凸模的加工方法分两种:
一,凹凸模分开加工此方法用于加工冲裁批量较大的工件。
在这种情况下,需要分别计算和标注凹模和凸模的尺寸和公差。
落料时,间隙取在凸模上。
适用于加工形状简单的冲模
二:
凹凸模配合加工这种方法有利于获得最小间隙,放宽对模具加工设备的精度要求,对于冲制复杂形状零件的冲模、单件或小批量生产的冲模时,多采用此方法。
根据所要加工冲模模具外形等综合方面的考虑,选取方案一为模具制造方案。
4.4凹凸模刃口的尺寸计算
4.4.1凹凸模刃口尺寸的计算原则
(1)设计基准:
落料以凹模为设计基准,间隙取在凸模上;冲孔以凸模为设计基准,间隙取在凹模上。
(2)设计间隙时一律采用最小合理间隙值Zmin。
(3)刃口方向的制造偏差方向:
单项注入实体内部。
即磨损后,凹凸模刃口尺寸变大的取+б;磨损后凹凸模刃口尺寸变小的取-б。
(4)刃口尺寸制造偏差的大小:
形状简单,按IT6~IT7取值;复杂形状,取公差的1/4,磨损后尺寸无变化取公差的1/8。
4.4.2计算凹凸模刃口尺寸
由于此模具凹凸模采用分别加工方法,所以凹凸模的尺寸及制造公差都对间隙有影响,计算凹凸模尺寸前需要对模具的制造公差进行检验。
由《冲压工艺与模具设计》第31页查得由分别加工的互换性要求采用较小的模具制造公差来满足下式[15]
(4-1)
式中:
бa为凹模的制造偏差值,mm;
бt为凸模的制造偏差值,mm;
Zmin为最小合理间隙
Zmax为最大合理间隙
(1)电极板中直径8.33mm的孔公差等级为IT14,偏差为+0.36mm;直径为14.3mm的孔偏差为+0.43mm;孔边距20mm的公差为0.62mm.由《冲压工艺与模具设计》第8页表2.5、第9页表2.8查得:
按IT6~IT7取刃口尺寸制造偏差值
;磨损系数x=0.5
根据紫铜板厚度5mm,取
,
。
所以,有上式可得
mm
结果满足要求
(2)由《模具结构型式与应用手册》第9页表2.6查得孔心距129.8mm的偏差为±0.575mm,公差为1.15mm。
由《冲压工艺与模具设计》查得,刃口尺寸制造偏差值бa和бt取±1/8Δmm,则
。
磨损系数x=0.5。
所以,由上式可得
mm
结果不满足要求,所以制造公差过大,若要满足制造公差应对制造公差进行修改,取下式进行修改。
mm
mm
将
代入(4-1)得:
结果成立。
(3)由《实用冲压工艺及模具设计手册》第93页查得冲孔凹凸模的计算公式如下:
冲孔凸模:
(4-2)
冲孔凹模:
(4-3)
孔中心距:
(4-4)
上面几个式子中:
Δ为制件公差
da为凹模的基本尺寸
dt为凸模的基本尺寸
将上述计算数据代入(4-2)(4-3)(4-4)式中
冲直径为8.33孔时:
凸模:
mm
凹模:
mm
冲直径14.3mm孔时:
凸模:
mm
凹模:
mm
孔边距20mm:
凸模:
mm
凹模:
mm
由于以上尺寸属于半边磨损,所以取0.5бa、0.5бt、0.5Zmin
孔心距129.8mm:
mm
4.4.3冲裁力的计算
由《冲压手册》第86页查得冲裁力的计算公式为[6]:
(4-5)
式中:
P为冲裁力;
L冲裁件受剪切周边长度,mm;
t冲裁件的料厚;
τ材料抗剪强度Mpa,由《冲压模具简明设计手册》表14.7查得硬紫铜的抗剪强度为240Mpa[15]。
冲孔时可视冲裁为纯剪切变形,所以取K为1.3。
4.4.4卸料力、推件力和顶件力的计算
冲裁时材料在分离前存在弹性变形,一般情况下,冲裁后的弹性恢复使落料件或冲孔废料塞在凹模内,而板料或冲孔件则附着在凸模上。
为是冲裁工作继续进行,必须及时将附着在凸模上的板料或冲孔件卸下,将塞在凹模内的落料件或冲孔废料向下推出或向上顶出。
从凸模上卸下板料或冲孔件所需的力为卸料力P卸,,从凹模内向下推出落料件或废料所需的力称为推件力P推,从凸模内向上顶出落料件或冲孔废料所需的力称为顶件力P顶。
在生产实际中,P卸、P推、P顶的计算用以下公式:
(4-6)
(4-7)
(4-8)
式中:
P为冲裁力
K卸为卸料力系数
K推为推件力系数
K顶为顶件力系数
n为梗塞在凹模内的冲件数,
,
,
,所以
。
查《冲压工艺与模具设计》表2.3可知[15],
,
,
。
因为
,所以将已知数代入上述各式子可得:
;
;
冲裁时,所需总冲压力为冲裁力、卸料力、推件力和顶件力之和。
选择压力机时是否考虑进去,应根据不同的模具结构进行区分。
采用刚性卸料装置和下出料方式的总冲压力为;
(4-9)
采用弹性卸料装置和下出料方式的总冲压力为:
(4-10)
采用弹性卸料装置和上出料方式的总冲压力为:
(4-11)
因为此模具采用弹性卸料装置和下出料方式,所以
4.4.5压力机选择
(1)由于此模具属于结构简单的中小型冲裁件,且属于小批量生产、冲压件对尺寸及精度要求不高,所以采用开式机械压力机
(2)压力机规格的选择
压力机规格的选择主要依据冲压件尺寸、变形力大小及模具尺寸等,初选压力机规格时主要选择压力机的公称压力、行程次数等参数。
公称压力的选择:
压力机选用时必须保证所需的工艺力小于液压力的标称压力,并留出15%~30%的余量。
根据上述冲压力的计算,
。
所以所选压力机的公称压力
;初步选用型号为J23-16开式双柱可倾压力机。
该型号压力机主要技术规格如下[8]:
公称压力160KN;
滑块行程50mm;
最大闭合高度220mm;
最小闭合高度175mm;
最大装模高度180mm;
连杆调节量45mm;
工作台尺寸(前后mm
左右mm)
;
垫板尺寸(厚度mm
孔径mm)
;
模柄孔尺寸(直径mm
深度mm)
;
滑块中心至床身中心距离160mm;
最大倾斜角35°
由J23-16型压力机的参数可知,
;
所以所选压力机的公称压力符合要求。
所选压力机的模具闭合高度应遵循下列关系
式中Hmax为压力机最大闭合高度,mm;
Hmin为压力机最小闭合高度,mm;
H为模具的闭合高度,mm;
Hd为压力机垫板厚度,mm;
压力机是否设置垫板需要在模具零件设计计算结果和绘制草图后得知,在不设置垫板的情况下,模具闭合高度范围为185~215mm之间。
所以,初选压力机为J23-16。
4.4.6冲压压力中心的计算
(1)冲模对工件施加的冲压力合力的中心称为冲压压力中心。
要使冲压模具正常工作,必须使压力中心与模柄的中心线相重合,从而使压力中心与所选冲压设备滑块的中心相重合。
否则在冲压时将产生弯矩,使冲压设备的滑块和模具发生歪斜,引起凹凸模间隙不均匀,刃口迅速变钝,并使冲压设备和模具的导向机构产生不均匀磨损,直接影响模具寿命和冲裁质量。
(2)所设计的模具压力中心是冲两个圆孔冲压力合力的作用点。
计算各凸模压力中心的坐标位置x1、x2、y1、y2。
x1=0、x2=129.8、y1=0、y2=0
计算各凸模刃口轮廓的周长L1、L2
mm
可通过下式进行压力中心计算
将计算数据分别代入以上两式得:
x0=82.02,y0=0,最后求的总压力中心的坐标位置B(82.02,0)如图所示:
图4-1凸模压力中心
5:
模具主要零件的设计计算
5.1凹模的设计计算
根据《冲压模具简明设计手册》[15]表2.40所列各模具类型、特点及应用,采用直筒式孔口凹模,这种凹模的特点是:
制造方便,刃口强度高,刃磨后工作部分尺寸不变,但易积存冲件或废料,胀力大,推件力大,孔壁磨损大,刃磨层较厚。
同时根据材料厚度5mm,选取凹模刃口高度h=10mm。
凹模高度的计算:
(5-1)
式中:
H为凹模高度;
P为冲裁力,一般情况下P取冲裁总压力。
在这里取冲裁力、卸料力、推件力总和,据前面计算知
选取凹模高度为25mm。
凹模壁厚的计算:
根据凹模刃口轮廓不同,凹模壁厚C与凹模高度H的关系可按下式确定:
轮廓线为光滑的曲线时:
(5-2)
轮廓线为凹模边缘平行时:
(5-3)
轮廓线具有复杂形状或尖角时:
(5-4)
因为此凹模刃口轮廓为圆形,故按式中1进行计算
如图所示为小孔凸模:
图5-1小孔凸模
如图所示为大孔凹模:
图5-2大孔凹模
凹模的强度校核:
主要是检查其高度H。
凹模在冲裁力的作用下会产生弯曲,如果凹模高度不够,就会产生较大的弯曲变形甚至断裂。
由《冲压手册》第45页表2.50查得凹模校核公式如下:
(5-5)
(5-6)
式中P为冲裁力
бw弯曲应力的计算值,N;
为许用弯曲应力,Mpa;对于淬火硬度58~62HRC的T8A、T10A、Cr12