DEFORM黄铜挤压.docx
《DEFORM黄铜挤压.docx》由会员分享,可在线阅读,更多相关《DEFORM黄铜挤压.docx(17页珍藏版)》请在冰豆网上搜索。
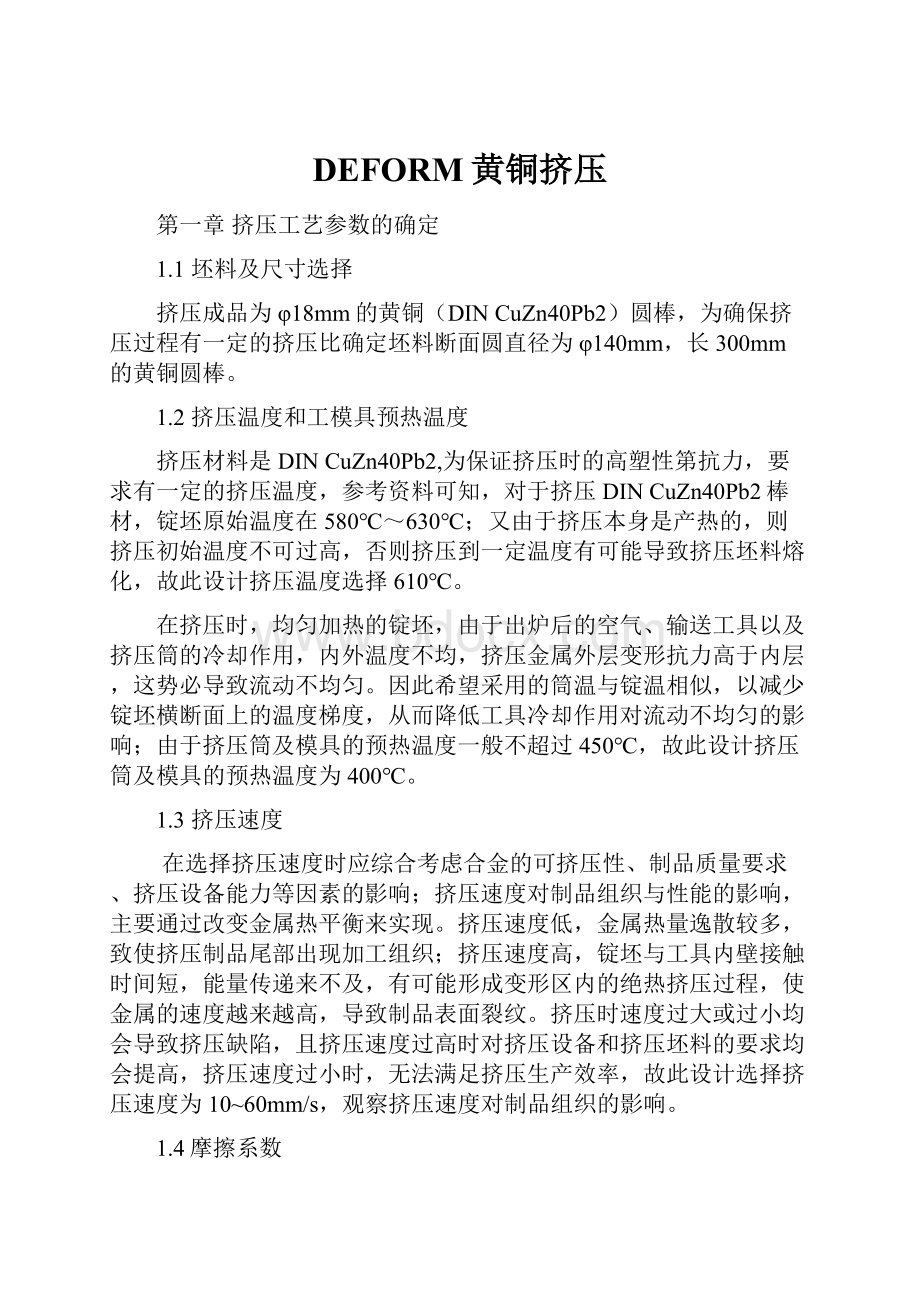
DEFORM黄铜挤压
第一章挤压工艺参数的确定
1.1坯料及尺寸选择
挤压成品为φ18mm的黄铜(DINCuZn40Pb2)圆棒,为确保挤压过程有一定的挤压比确定坯料断面圆直径为φ140mm,长300mm的黄铜圆棒。
1.2挤压温度和工模具预热温度
挤压材料是DINCuZn40Pb2,为保证挤压时的高塑性第抗力,要求有一定的挤压温度,参考资料可知,对于挤压DINCuZn40Pb2棒材,锭坯原始温度在580℃~630℃;又由于挤压本身是产热的,则挤压初始温度不可过高,否则挤压到一定温度有可能导致挤压坯料熔化,故此设计挤压温度选择610℃。
在挤压时,均匀加热的锭坯,由于出炉后的空气、输送工具以及挤压筒的冷却作用,内外温度不均,挤压金属外层变形抗力高于内层,这势必导致流动不均匀。
因此希望采用的筒温与锭温相似,以减少锭坯横断面上的温度梯度,从而降低工具冷却作用对流动不均匀的影响;由于挤压筒及模具的预热温度一般不超过450℃,故此设计挤压筒及模具的预热温度为400℃。
1.3挤压速度
在选择挤压速度时应综合考虑合金的可挤压性、制品质量要求、挤压设备能力等因素的影响;挤压速度对制品组织与性能的影响,主要通过改变金属热平衡来实现。
挤压速度低,金属热量逸散较多,致使挤压制品尾部出现加工组织;挤压速度高,锭坯与工具内壁接触时间短,能量传递来不及,有可能形成变形区内的绝热挤压过程,使金属的速度越来越高,导致制品表面裂纹。
挤压时速度过大或过小均会导致挤压缺陷,且挤压速度过高时对挤压设备和挤压坯料的要求均会提高,挤压速度过小时,无法满足挤压生产效率,故此设计选择挤压速度为10~60mm/s,观察挤压速度对制品组织的影响。
1.4摩擦系数
温度改变常引起摩擦系数的变化,在较高的温度下回产生较多的氧化铁皮,是挤压时的摩擦系数增大。
技术流动均匀程度除了与其的导热性有关,还由于加热制度不同时,氧化膜与锭坯间的结合强度不同,从而改变了接触界面的边界条件。
根据相应的温度设定其摩擦系数,故此设计的挤压垫摩擦系数为0.6,挤压筒及挤压模摩擦系数为0.1。
第二章模具尺寸及工艺参数的确定
2.1工模具结构示意图
挤压工模具示意图如下图2-1所示:
图2-1工模具示意图
2.2工模具结构分析
挤压制品为φ18mm的棒材,挤压所需的工具有挤压筒、挤压垫和挤压模。
挤压筒容纳高温锭坯,是由两层或三层以上的衬套以过盈热配合组装在一起构成的;挤压筒的尺寸包括筒内径、外径和长度。
挤压垫是用来防止高温的锭坯直接与挤压杆接触,消除其消除其端面磨损和变形的工具;其尺寸包括挤压垫直径和厚度。
挤压模是挤压生产中最重要的工具,是锭坯成形的直接工具;模子尺寸只要有模角、工作带长度和直径、出口直径、入口圆角、模子的内径和外径及长度。
2.3工模具尺寸设计
根据挤压成形要求,挤压所用坯料为φ140×300mm,挤压制品为φ18mm的棒材。
2.3.1挤压筒尺寸设计
挤压筒是所有挤压工具中最贵重的部件,在挤压过程中防止锭坯金属外流;其尺寸有筒内径、外径和筒长。
2.3.1.1挤压筒内径
计算挤压筒内径时要考虑挤压筒内径与锭坯的偏差量,即筒锭之间有间隙值
,
按间隙值计算:
(2-1)
式中,
—锭坯直径,mm;
—筒锭之间的间隙值,mm,可查下表2-1。
表2-1筒、锭间隙选择
金属材料
挤压机
挤压筒直径
mm
间隙值,mm
类型
吨位,MN
铜
卧式
—
≤100
100~300
≤300
1~3
5
10
立式
6
75~120
1~2
2.3.1.2挤压筒外径
根据经验数据初步确定,挤压筒的外径应大致等于其内径的4~5倍,即:
(2-2)
2.3.1.3挤压筒长度
(2-3)
式中,
—挤压垫厚度,mm;
2.3.2挤压垫尺寸设计
挤压垫做成圆形,其外径应比挤压筒内径小
。
值与挤压筒的内径有关,由于我们所用的挤压机卧式挤压机,所以其
值可取0.5~1.5mm。
挤压垫的厚度可等于其直径的0.2~0.7倍。
2.3.2.1挤压垫直径
可根据经验式:
(2-4)
2.3.2.2挤压垫厚度
可根据经验式:
(2-5)
2.3.3挤压模尺寸设计
挤压模的结构形式和各部分尺寸对挤压力、金属流动均匀性、制品尺寸精度及其使用寿命都有极大影响,所以模子的尺寸设计是最重要的。
2.3.3.1模角α、工作带长度
和入口圆角r
(1)模角α是模子的最基本参数之一,它的大小直接影响死区的大小,进而影响制品的质量;这里的模角α=45℃;
(2)工作带长度有称定径带,是以稳定尺寸和保证制品表面质量的关键部分。
这里的工作带长度
=50,mm;
(3)入口圆角半径的作用是为了防止低塑性合金在挤压时产生表面裂纹和减轻金属在进入工作带时所产生的非接触变形,同时也是为了减轻在高温下挤压时模子的入口棱角被压颓而很快改变模孔尺寸用的;这里的r=5mm。
2.3.3.2工作带直径
模子工作带直径与实际所挤出的制品直径并不相等。
挤压棒材的模孔直径
可用下式计算:
(2-6)
式中,
—挤压制品的直径,mm,为φ18mm;
—裕量系数,用来考虑各种因素对制品尺寸的影响,看查下表2-2得。
表2-2裕量系数
合金
值
含铜量不超过65%的黄铜
紫铜、青铜及含铜量大于65%的黄铜
纯铝、防锈铝及镁合金
硬铝和锻铝
0.014~0.016
0.017~0.020
0.015~0.020
0.007~0.010
2.3.3.3出口直径
模子的出口直径一般应比直径大3~5mm,因过小会划伤制品的表面。
根据经验式:
(2-7)
2.3.3.4模子的外径
和
(1)根据经验,对于棒材,其模子外径
等于
的(1.25~1.45)倍,
为一般挤压棒材的外接圆最大直径,通常等于挤压筒内径的(0.8~0.85)倍;即:
(2-8)
(2)
为出口段长度,这里
取30mm。
2.3.4工模具尺寸的确定
结合式(2-1)~(2-8)以及表2-1、2-2和有关数据得:
(1)挤压筒内径:
=145mm;
(2)挤压筒外径:
=580~725mm,这里取
=600mm;
(3)挤压筒长度:
=350mm,其中
取20mm;
(4)挤压垫直径:
=143.5~144.5mm,取
=144mm;
(5)挤压垫厚度:
=28.8~100.8mm,取
=30mm;
(6)工作带直径:
=18.252~19.908mm,取
=18.5mm;
(7)出口直径:
=21.5~23.5mm,取
=22mm;
(8)模子的外径:
=145~178.7mm,取
=175mm。
以上数据即为挤压工模具尺寸。
第三章挤压设计方案的制定
3.1设计方案分组
本设计方案共分为8组进行挤压模拟,其分组数据如下表3-1所示;
表3-1挤压方案的分组
序号
挤压垫摩擦系数
挤压筒挤压模摩擦系数
挤压杆速度
/mm.s-1
挤压模锥角
/°
挤压温度
/℃
定径带长度
/mm
工模具预热温度
/℃
1
0.6
0.1
10
45
610
50
400
2
15
3
20
4
25
5
30
6
40
7
50
8
60
3.2实验过程
3.2.1挤压工模具及工件的三维造型
根据给定的几何尺寸,运用PRO/E分别绘制坯料、挤压垫、挤压模、挤压筒的几何实体,文件名称分别为workpiece,topdie,bottomdie,object4。
输出stl格式。
3.2.2挤压模拟前处理
建立新问题:
程序→DEFORM6.1→Problem→Next→在ProblemName栏中填写Stickextrusion→Finish→进入前前处理界面;
在SimulationControl中,勾选SI以及勾选“Deformation”和“HeatTransfer”。
定义对象材料,设置挤压温度610℃,选择属性为DIN-CuZn40Pb2。
实体网格化,用绝对网格划分,SizeRatio改为1.5,MinElement改为2。
定义topdie、bottomdie和object4,定义温度为400℃,
设置topdie速度10mm/s。
其他7组方案的速度如表3-1所示。
模拟控制设置,在SimulationControl中,设置NumberofSimulationSteps为100、StepIncrementtoSave为5、WithDieDisplacement为1→点击OK按钮完成模拟设置;在Stop中,设置Z轴距离为-100。
调整对象位置关系:
在ObjectPositioning中设置Z轴方向为300。
边界条件定义,填入挤压垫的摩擦系数0.6、挤压筒和挤压模的摩擦系数为0.1以及传热类型为Fomging,完成边界条件设置。
3.2.3生成库文件
在工具栏上点击Databasegeneration按钮→点击Check按钮→没有错误信息则点击Generate按钮→完成模拟数据库的生成。
然后退出前处理程序界面。
3.2.4模拟运算和后处理
完成运算后进行后处理,观察载荷曲力、温度变化、破坏系数的曲线图和云图。
第四章实验结果分析
本设计按照挤压杆速度共分为8组方案,下面是这8组方案的比较分析,通过各组方案中载荷曲力、温度变化、破坏系数的曲线图或者云图进行分析,由于方案较多且各组方案的云图趋势相似,故只取方案一分析。
。
4.1挤压速度对挤压力的影响
(1)如下图4-1和载荷曲线在开始极短的时间内曲线呈垂直上升,此段属于填充挤压阶段,发生弹性变形,变形均匀,载荷均匀增加;而后阶段呈缓慢的曲线上升,此段属于平流挤压阶段,发生塑性变形,变形不均匀,载荷不均匀增加,随着挤压过程的进行,产生加工硬化,变形抗力增加,挤压力越来越大。
在挤压的最后阶段,载荷曲线变化剧烈,此段是紊流挤压阶段,筒内的金产生剧烈的径向流动。
图4-1方案一载荷曲线图
(2)根据挤压杆的速度不同,从deform中提取载荷曲线的数据,然后在excel中做出8组方案的相应表格,求出每组的平均载荷,即平均挤压力;其数据如表4-1所示:
表4-1平均挤压力
方案
方案一
方案二
方案三
方案四
方案五
方案六
方案七
方案八
挤压杆速度/mm.s-1
10
15
20
25
30
40
50
60
平均载荷/N
881739
869645
890676
878233
875571
769661
877296
907634
从表4-1中平均挤压力做出的图表如下图4-2,可以看出方案六的平均挤压力最小,方案八最大;随着挤压速度的增加,坯料的温度不能及时散出,则坯料的温度越来越高;温度越高,坯料与工模具的粘结愈严重,怎摩擦力越大,所需的挤压力也越来越大;从图4-3中可以看出,挤压力整体呈上升趋势,但是有波动,特别是方案六,这说明了挤压力不仅仅与挤压速度呈正比;根据资料得知,金属变形抗力、挤压温度、挤压方法、挤压比、锭坯长度、挤压速度、挤压模角、工具表面状态等.
图4-28组方案的平均挤压力折线图
4.2挤压速度对温度的影响
(1)如下图4-3相所示,在整个挤压过程中,坯料中心温度分布比较均匀且较高,因为工件中心不与挤压模具接触,传热都很少,温度不能及时散出;挤出来的部分坯料温度最高,而在制品的最前端温度有所降低,因为该段与空气接触,热量散出,温度降低;而与挤压垫相接触的一端温度最低,主要是由于在挤压过程中与挤压垫接触的一端存在着热交换,使温度降低。
(2)根据挤压杆速度的不同,从deform中提取温度变化的数据,然后在excel中做出8组方案的相应表格,制成8组方案的对比图如图4-4所示。
从下图温度变化中可以看出每组方案在一开始的填充挤压阶段温度基本不变,变形产生的热量较少;当坯料进入挤压模锥形区,温度急剧增加,这是由于不均匀变形导致的;由于本设计的定径带长度较长,摩擦较大,所以坯料通过定径带时温度有所增加。
(3)
不同的挤压速度,坯料的温度不同,挤压速度越大,坯料的温度越高。
从下图中可以看出随着挤压速度的增加,坯料的最高温度也相应的增加;因为速度越快,热量越来不及散出,温度越高。
其各组最高温度如下表4-2所示以及最高温度走势图4-5。
表4-2坯料最高温度表
方案
方案一
方案二
方案三
方案四
方案五
方案六
方案七
方案八
挤压杆速度/mm.s-1
10
15
20
25
30
40
50
60
最高温度/℃
639
645
646
656
660
662
667
663
4.3挤压力对最大应变的影响
(1)
如下图4-5所示,从图中可以清晰地看出,挤压过程中刚开始出现应力最大的位置在刚刚进入挤压模的位置,因为在此处由于工件的直径急剧变化,金属流动的阻力最大,不均匀变形也最大,产生较大的附加应力;在挤压制品段应力分布较均匀,且数值较大,该段是在锥形区三向压应力状态下挤压后的结果;未挤出的部分应力分布比较均匀但应力较小,因为挤压筒的摩擦力有摩擦力使得此处金属流动很难,变形很小,则应变很小。
因为8组方案的最大应变云图相似,故只取方案一最大应变云图分析。
(2)根据8组方案中的最大应变云图可以总结出每组应变的最大值,如下表4-3所示;以及利用表4-3中数据做出不同挤压速度对应的最大应变值变化趋势如下图4-6所示。
表4-3各方案最大应变值
方案
方案一
方案二
方案三
方案四
方案五
方案六
方案七
方案八
挤压杆速度/mm.s-1
10
15
20
25
30
40
50
60
最大应变值/(mm/mm)
2.98
3.05
2.92
3.16
3.08
4.16
3.43
2.94
图4-6方案一最大应变变化图
从表4-3和图4-6中可以看出,挤压速度的与最大应变之间没有一定的线性关系,这说明了挤压杆速度的变化对坯料的最大应变影响很小,纵使在某方案区其最大应变值有增大的趋势。
从理论上分析,挤压速度越大,所需的挤压力越大,坯料挤出的速度加快,但是这与应变的变化没有直接影响。
查有关资料应变的变化与摩擦系数、材料性质以及载荷和温度等综合因素,某一个因素的变化对其影响不大。
4.4挤压力对表面损伤的影响
(1)如下图4-7所示,随着挤压变形的进行,坯料破会愈严重,因为随着挤压过程的进行工件的变形越来越大,不均匀变形也越严重,同时残余应力也增加,金属内部晶格畸变也是越来越严重,则挤压变形的进行破坏情况越来越严重。
从8组方案的破坏系数云图中可以看出,破坏最严重的部分是挤压制品,而挤压出的部分基本没有什么损伤;由于8组方案中的破坏情况相似,所以只选取方案一中破坏系数云图进行分析。
图4-7方案一破换系数云图
(2)从deform中导出8组破坏数据,观察8组方案的破坏趋势,如下图4-8所示分析不筒的挤压速度对制品表面质量的影响,
从上图中可以看出挤压杆的速度越大,挤压制品的破坏情况越严重;如果挤压速度过大的话,有可能导致挤压制品表面出现微裂纹,甚至会出现断裂;所以挤压速度越大对制品的表面质量影响很大,制品的质量越差。
4.5挤压力对等效应力的影响
(1)后处理中观察最大应变云图如下图4-9所示,由于方案多且云图相似,故仅取方案一等效应力分析。
从图中可以清晰地看出,锥形变形区应力分布较集中,且数值较大,为三向压应力状态,因为此区域不均匀变形剧烈;挤压筒内的坯料中心应力分布均匀且应力较小,因为此段变形均匀。
图4-9方案一等效应力云图
(2)从deform中导出8组破坏数据,观察8组方案的等效应力趋势,如下图4-10所示分析不筒的挤压速度对制品表面质量的影响;不同的挤压速度对应各组方案中的等效应力如下表4-4所示。
表4-4各组方案等效应力
方案
方案一
方案二
方案三
方案四
方案五
方案六
方案七
方案八
挤压杆速度/mm.s-1
10
15
20
25
30
40
50
60
等效应力/(MPa)
91.93
94.39
97.37
96.03
98.41
93.42
97.86
98.44
从表4-4和图4-10中可以看出,随着挤压速度的增大,等效应力出现波动,但整体还是呈增加的趋势,也就说挤压速度越大,等效应力越大。
理论分析,挤压力越大,等效应力越大,虽然与实验模拟有所差异,这可能是由于挤压模拟本身的差异导致的。
总结
本设计是通过改变挤压杆速度探究对棒材挤压的影响,例如挤压力、挤压温度、最大应变、损伤和等效应变。
本设计通过DEFORM进行四分之一棒材的挤压模拟,我们更加熟悉了挤压设计的过程;首先,选择坯料和挤压参数的设计;其次,挤压模具的工艺设计;再次,挤压方案的制定,对设计进行分组;最后,挤压结果分析。
对于本次DEFORM数值模拟,我总结如下几点:
(1)挤压杆速度越大,所需的挤压力越大;
(2)挤压杆速度越大,挤压制品的温度越高;
(3)挤压杆速度队最大应变的影响很小;
(4)挤压杆速度越大对制品表面质量的影响越大,破坏越严重,表面质量越差;
(5)加油干速度越大,等效应力相应增大。
挤压速度越大,对挤压制品的质量影响越大,故挤压速度应取值合理,不能过大也不能过小。
通过本设计来探究挤压杆速度对挤压数值模拟出的而结果可能与理论有点出入,因为对挤压实验的影响因素很多,坯料的材质、摩擦力等诸多因素,再者由于不同组挤压模拟本身存在着差异以及动态载荷没有出现平衡点也影响本次设计的结果。
通过这次模拟训练,我们学会了许多知识。
熟悉PRO\E三维绘图软件的使用,学会了DEFORM-3D的基本操作以及相关参数的合理设置。
在这次设计过程中,我们熟悉了以前学的一些专业基础知识,设计的过程让我们将所学知识融会贯通,也为我们以后做产品设计提供的宝贵的经验。
在整个设计完成后,我才感觉到做课程设计需要很多团队合作,分工的明确,持之以恒的态度。
我要将这些经验深入到以后的工作中,这样才能在以后的工作中完成每项任务。
参考文献
[1]马怀宪主编.金属塑性加工学—挤压、拉拔与管材轧制.冶金工业出版社,1991.5
[2]胡建军主编.DEFORM-3D塑性成形CAE应用教程.北京大学出版社,2011.1
[3]王广春主编.金属体积成形工艺及数值模拟技术.机械工业出版社,2009.11
[4]郝斌海主编.挤压模具简明设计手册.化学工业出版社,2..6.2