冶金机械设备安装.docx
《冶金机械设备安装.docx》由会员分享,可在线阅读,更多相关《冶金机械设备安装.docx(46页珍藏版)》请在冰豆网上搜索。
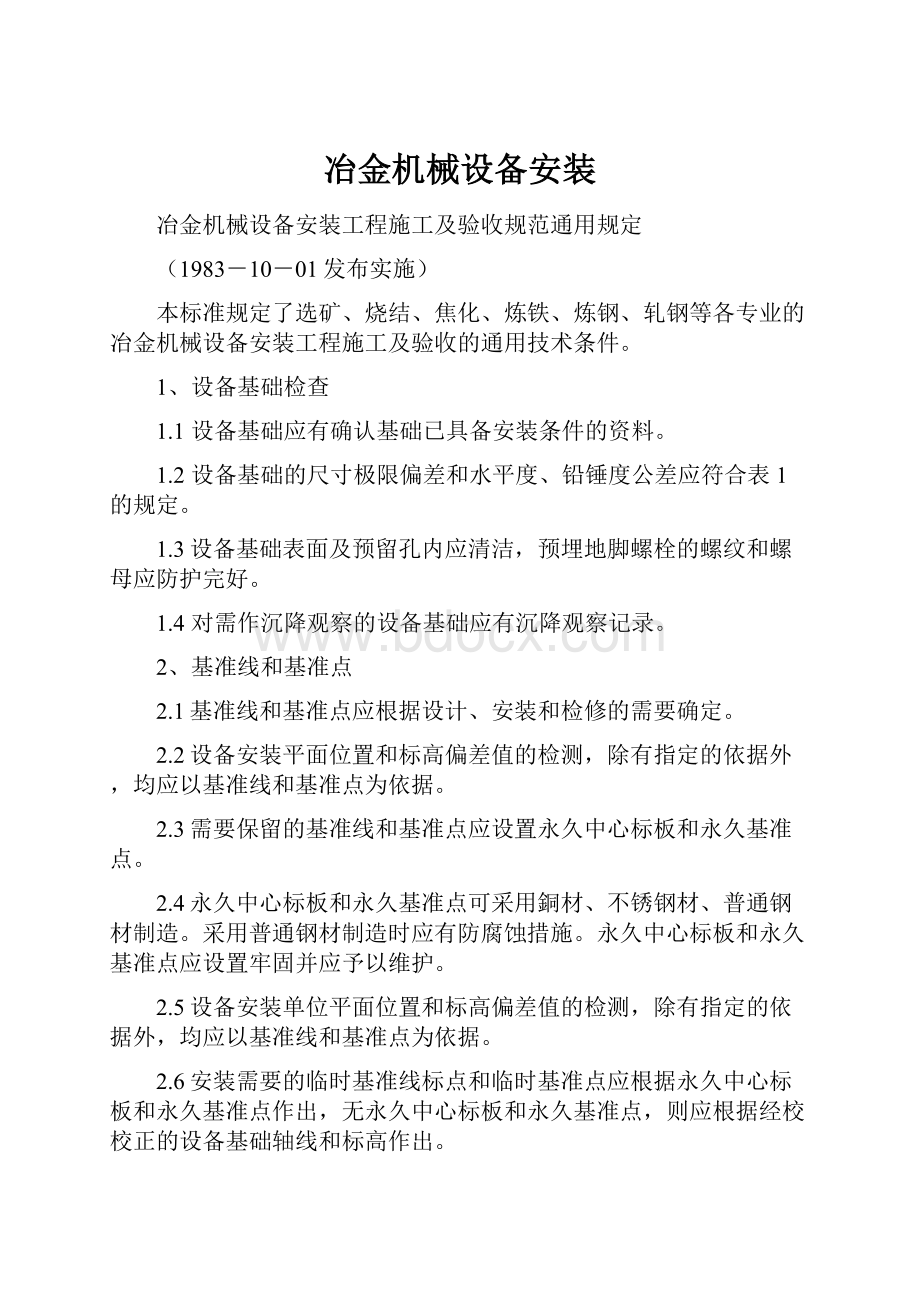
冶金机械设备安装
冶金机械设备安装工程施工及验收规范通用规定
(1983-10-01发布实施)
本标准规定了选矿、烧结、焦化、炼铁、炼钢、轧钢等各专业的冶金机械设备安装工程施工及验收的通用技术条件。
1、设备基础检查
1.1设备基础应有确认基础已具备安装条件的资料。
1.2设备基础的尺寸极限偏差和水平度、铅锤度公差应符合表1的规定。
1.3设备基础表面及预留孔内应清洁,预埋地脚螺栓的螺纹和螺母应防护完好。
1.4对需作沉降观察的设备基础应有沉降观察记录。
2、基准线和基准点
2.1基准线和基准点应根据设计、安装和检修的需要确定。
2.2设备安装平面位置和标高偏差值的检测,除有指定的依据外,均应以基准线和基准点为依据。
2.3需要保留的基准线和基准点应设置永久中心标板和永久基准点。
2.4永久中心标板和永久基准点可采用銅材、不锈钢材、普通钢材制造。
采用普通钢材制造时应有防腐蚀措施。
永久中心标板和永久基准点应设置牢固并应予以维护。
2.5设备安装单位平面位置和标高偏差值的检测,除有指定的依据外,均应以基准线和基准点为依据。
2.6安装需要的临时基准线标点和临时基准点应根据永久中心标板和永久基准点作出,无永久中心标板和永久基准点,则应根据经校校正的设备基础轴线和标高作出。
2.7挂设的基准线应根据设备安装精度要求和挂设跨距选用直径为0.3~0.75mm的整根钢丝,其拉紧力一般为钢丝破断拉力的40﹪~80﹪,水平或倾斜挂设的跨距不宜超过40m。
2.8基准线标点和基准点的施工测量应符合YBJ15-66《冶金工业建筑安装施工测量规程》的规定。
表1
设备的基础尺寸极限偏差及水平度、铅锤度公差mm
项次
项目
极限偏差
公差
1
基础座标位置(纵、横向轴线)
±20
2
基础各不同平面的标高
0
-20
3
基础上平面外形尺寸
凸台上平面外形尺寸
凹穴尺寸
±20
0
-20
+20
0
4
基础上平面的水平度(包括地坪上需要安装设备的部分)
每米
全长
5
10
5
铅锤度
每米
全长
5
20
6
预埋地脚螺栓
标高(顶端)
中心距(在根部和顶部两处测量)
+20
0
±2
7
预留地脚螺栓孔
中心距
深度
孔壁的铅锤度
±10
+20
0
8
预埋活动地脚螺栓锚板
标高
中心距
水平度(带槽的锚板)
水平度(带螺纹孔的锚板)
+20
0
±2
3、设备就位、找平找正和标高测定
3.1设备就位前,必须除去设备底面底油污、油漆。
泥土及地脚螺栓预留孔内的杂物。
二次灌浆处的设备基础表面应清除浮浆、凿成麻面,并不得有油污,以保证二次灌浆质量。
3.2设备的纵、横向中心线极限偏差、标高极限偏差、水平度或铅锤度公差应符合各专业《冶金设备安装工程施工及验收规范的规定》的规定,如无规定,一般应符合表2的规定。
表2
一般设备安装精度
设备位置情况
纵、横向中心线、标高
极限偏差
mm
水平度或铅锤度公差
单独布置的设备
±10
1/1000
与其他设备有机械上的
衔接关系的设备
±2
0.5/1000(0.20/1000)
3.3设备找平找正和标高测定的测点,一般可选择的下列部位:
A、设计或设备技术文件指定的部位;B、设备的主要工作面;C、部件上加工精度较高的表面;D、零、部件间的主要结合面;E、支承滑动部件的导向面;F、轴承剖封面、轴颈表面、滚动轴承外圈;G、设备上应为水平或铅锤的主要轮廓面。
3.4设备安装偏差或误差的方向,一般可按下列因素确定:
A、能补偿受力或温度变化后所引起的偏差或误差;B、能补偿使用过程中磨损所引起的偏差或误差;C、使有关的零、部件更好地连接配合;D、使运转平稳;E、使零、部件在负荷作用下受力较小。
3.5拉钢丝测检直线度、平行度、同轴度时,应根据测检精度要求和拉设跨距选用直径为0.2~0.75mm的整根钢丝,其拉紧力一般为钢丝破断拉力的50﹪~80﹪。
水平方向拉钢丝测检需要考虑钢丝挠度影响时,钢丝两支点间的距离不应大于16m;钢丝在自重作用下的挠度应按下式计算:
f=500qx(L-x)/P
式中:
f――测检点挠度,mm;
q――单位长度的钢丝重量,Kgf/m;
x――测检点至一支点的距离,m;
P――钢丝拉紧力,Kgf。
3.6常用的测量检查方法见附录表A(补充件)
4、地脚螺栓、垫板和二次灌浆
4.1预留地脚螺栓的安设
4.1.1地脚螺栓与混凝土接触的部位不得有油污和污垢。
4.1.2地脚螺栓底端不得碰预留地脚螺栓孔的孔底,与孔壁的距离应大于15mm。
4.1.3拧紧地脚螺栓应在预留地脚螺栓孔的二次灌浆混凝土达到设备基础混凝土设计的强度后进行。
4.2带锚板活动地脚螺栓的安设
4.2.1活动锚板设置应平稳,锚板与基础面的接触应均匀。
4.2.2带槽锚板活动地脚螺栓末端的端面上应标明矩形头的方向,基础表面上应标明带槽锚板矩形槽的方向,矩形头应正确嵌入锚板槽内。
4.2.3带锚板活动地脚螺栓预留孔或套管的密封应符合设计的规定,如无规定,可在预留孔或套管内充填干燥的砂子,上口以麻丝沥青封闭。
4.3胀锚地脚螺栓和环氧砂浆锚固地脚螺栓的安设
4.3.1胀锚地脚螺栓的安设应符合《YG型胀锚螺栓施工技术暂行规定》(待出版)的规定。
4.3.2环氧砂浆锚固地脚螺栓的安设应符合冶基规101-78《环氧砂浆锚固地脚螺栓技术规程》的规定。
4.4地脚螺栓的紧固
4.4.1设备底座上用于找平的调整螺钉,在地脚螺栓紧固前应与回松。
地脚螺栓紧固后,调整螺钉不应受力。
4.4.2地脚螺栓紧固工具的选择可参见附录B(参考件)
4.4.3地脚螺栓的紧固程度,一般用锤敲击螺母,根据响声和反弹力凭经验检查。
锤头规格可参照表3选用。
表3
检查地脚螺栓紧固的锤头规格
地脚螺栓公称直径
mm
锤头规格
Kg
≤36
﹥36~80
﹥80
0.5
1.5~5
6~8
4.4.4设备技术文件对地脚螺栓的紧固力有规定时,应对紧固力进行测定,测定方法可参见附录C(参考件)。
4.4.5地脚螺栓紧固后,螺母与垫圈、设备底座、锚板的接触应良好,局部间歇应符合表4的规定;螺栓应露出螺母,露出长度宜为1.5~5倍螺距。
表4
地脚螺栓的螺母与被连接件接触要求
地脚螺栓公称直径
局部间隙不得大于
≤36
﹥36~80
﹥80
0.05
0.10
0.15
4.5垫板
4.5.1垫板组的位置和数量一般应符合下列要求:
A、每个地脚螺栓的近旁至少应有一个垫板组,底座刚度较小或动负荷较大的设备,地脚螺栓的两侧近旁均应放置垫板组;无地脚螺栓处的设备主要受力部位亦应放置垫板组
B、垫板组在放置平稳和不影响二次灌浆的情况下,应尽量靠近地脚螺栓和主要受力部位。
C、相邻垫板组之间的距离宜为500~1000mm。
4.5.2放置在混凝土基础上的垫板,其总承力面积应按下式计算:
A=C×100(Q1+Q2)/R
式中:
A――垫板总承力面积,mm2;
C――安全系数,可采用1.5~3,采用座浆法放置垫板或采用无收缩混凝土进行二次灌浆时,取小值;
Q1――采用普通混凝土二次灌浆时为设备及承载物的重量,采用无收缩混凝土进行二次灌浆时为设备重量Kgf;
Q2――地脚螺栓紧固力【设备技术文件如无规定,可按附录D(补充件)确定】的总和,Kgf;
R――基础混凝土的抗压强度,Kgf/cm2。
4.5.3垫板的规格一般应根据垫板的总承力面积和垫板组的数量参照附录E(参考件)选用。
4.5.4直接放置垫板的混凝土基础表面应进行研磨,其与垫板接触面的接触点应分布均匀。
4.5.5采用座浆法放置垫板,座浆混凝土的配制、施工程序及注意事项可参照附录F(参考件)。
4.5.6每一垫板组应尽量减少垫板的块数。
平垫板组中,最厚的垫板应放在下面,最薄的垫板应放在中间。
4.5.7设备找正找平后,每一垫板组应符合下列要求:
A、每一垫板组应放置整齐,每对斜垫板的重叠面积应大于垫板面积的2/3。
B、垫板组伸入设备底座底面的深度应超过地脚螺栓。
C、平垫板组宜露出设备底座外缘10~30mm,斜垫板组宜露出设备底座外缘10~50mm。
D、每一垫板组均应被压紧,压紧程度可用手锤轻击垫板,根据响声凭经验检查;对于高速运转、承受冲击负荷和振动较大的设备,其垫板与垫板间、垫板与设备底座间,用0.05mm塞尺检查,塞入面积不得超过垫板面积的1/3。
E、钢垫板组的各垫板相互点焊牢固。
4.6二次灌浆
4.6.1预留地脚螺栓孔,设备底座与基础之间二次灌浆,应符合GBJ10-65《钢精混凝土工程施工及验收规范(修订本)》的规定。
4.6.2灌注时,不得使地脚螺栓歪斜和影响设备的安装精度。
4.6.3设备底座与基础之间二次灌浆层的厚度应符合设计的规定,如无规定,宜为50~100mm。
5、清洗和装配
5.1一般规定
5.1.1需要在安装现场装配的零、部件以及设备上原以装配的零。
部件,如有下列情况之一者,应进行清洗:
A、包装防护材料不需要保留的;B、包装防护材料不能作为润滑剂或掺入润滑剂使用的;C、包装防护材料可以作为润滑剂或掺入润滑剂使用但超过了规定的有效期;D、因运输、保管不善,致使包装防护材料发生变质或零、部件加工面已产生锈蚀、脏污。
5.1.2对于需要清洗的零、部件,清洗洁净后应涂以规定的润滑剂,必要时应涂以合适的防锈润滑剂。
5.1.3对于需要清洗的设备管路应清洗洁净并畅通。
5.1.4设备表面的防锈油脂可选择下列方法清洗:
A、用金属清洗剂(非离子表面活性剂)清洗。
B、用蒸汽或热空气吹洗,吹洗后必须及时除尽水分;
C、用热的机械油、气轮机油或变压器油清洗,油温不应超过100°C,如将被清洗的零、部件侵入油内加热溶解清洗时,被清洗的零、部件应与加热容器底部和四周保持适当的距离;
D、用碱性清洗液清洗,清洗液宜加热至60~90°C,清洗后应用清水冲洗洁净并使之干燥,常用的碱性清洗液的配方和实用范围可参见附录G(参考件)。
E、用煤油、柴油或汽油等溶剂油清洗。
5.1.5设备加工面上的防锈漆,应用适当的稀释剂或脱漆剂等溶剂清洗;用气相防锈剂溶液浸涂的零、部件,可用12﹪~15﹪亚硝酸钠和0.5﹪~0.6﹪碳酸钠的水溶液或酒精清洗。
5.1.6设备加工面如有锈蚀,应进行除锈。
常用的除锈方法和质量要求见附录H(补充件)。
5.1.7有禁油要求的设备,管路及其附件,应进行脱脂。
脱脂剂适用范围、脱脂方法和脱脂后的检验见附录I(补充件)。
脱脂后,应将脱脂见上残留的脱脂剂清除干净。
5.1.8设备拆卸、装配前,应了解设备的构造和技术要求,确定拆装顺序和方法。
5.1.9设备拆卸时,应对易于混淆的零、部件作出相对位置的标记。
5.2螺纹连接件、键、定位销装配
5.2.1螺纹连接件的装配,螺栓头部、螺母与被连接件的接触应紧密,紧固程度一般用手锤轻击螺母或螺栓头部,根据响声凭经验检查,或用塞尺检查。
如设备技术文件对紧固力有规定时,应对紧固力进行测定,测定方法可见附录C(参考件)。
5.2.2不锈钢、銅、和铝螺纹连接件的螺纹部分,装配时应涂以润滑剂。
5.2.3螺纹连接件的放松件应装配正确。
5.2.4螺纹连接采用加热螺栓多拧进螺母角度的方法紧固时,多拧进螺母的起始位置应使螺栓与被连接件的间隙消除,螺栓的加热温度应按下式计算:
t=P/AαE+t0
式中:
t――螺栓加热温度;
P――螺栓紧固力;
A――螺栓被拉伸部分的横截面积;
α――螺栓材料的线膨胀系数,见附录J(参考件)。
E――螺栓材料的弹性模量,见附录J(参考件)。
5.2.5平键、半圆键、楔键、薄型平键、切向键等与键槽的配合,应分别符合GB1095-79《平键、键和键槽的剖面尺寸》、GB1098-79《半圆键、键和键槽的剖面尺寸》、GB1566-79《薄型平键、键和键槽的剖面尺寸》、GB1974-80《切向键及其键槽》的规定。
5.2.6楔键的斜面与轮毂键槽的斜面应接触紧密。
切向键的每对键的斜面、键与轴槽和键与轮毂槽的工作面均应接触紧密。
5.2.7装配定位销时,定位销应能顺利装入销孔,销与销孔的接触面积应大于65﹪;装入销孔的深度应符合设备技术文件的规定。
5.3滑动轴承装配
5.3.1厚壁轴瓦与轴承盖、轴承座的结合面均应接触紧密,其接触面积,受力轴瓦应大于60﹪,不受力轴瓦应大于50﹪,且应均应分布均匀。
5.3.2轴瓦外径与轴承盖和轴承座内径为过盈配合时,其过盈量(紧力)应符合设备技术文件的规定。
5.3.3对于负荷方向不变的滑动轴承,轴瓦需要刮研时,轴颈与受力轴瓦的接触点数和接触角度应符合表5的规定。
表5
轴颈与受力轴瓦的接触要求
轴的转速,r.p.m
≤300
﹥300~1000
﹥1000
每25×25mm2面积上的接触点数
2~3
3~5
5~8
接触角度
90°~110°
60°~90°
应对称于轴承受力线
5.3.4对于负荷方向不变的滑动轴承,轴瓦需要刮研时,轴颈与受力轴瓦的间隙一般应符合下列规定。
A、顶间隙:
用润滑油润滑的轴承,应为轴颈直径的0.10﹪~0.15﹪;用润滑脂润滑的轴承,应为轴颈直径的0.15﹪~0.20﹪。
如负荷作用在上轴瓦时,上述顶间隙值应减小15﹪。
B、同一轴承两端顶间隙之差应符合表6的规定。
C、侧间隙:
单侧间隙应为顶间隙的1/2~1/3。
表6
滑动轴承两端顶间隙之差
轴颈公称直径
≤50
﹥50~120
﹥120~220
﹥220
两端顶间隙之差
≤0.02
≤0.03
≤0.05
≤0.10
5.3.5对于负荷方向变化的滑动轴承,轴瓦需要刮研时,轴颈与受力轴瓦的接触点数、接触角度、顶间隙、侧间隙均应符合设备技术文件的规定。
5.3.6厚壁轴瓦与轴承盖、轴承座的结合面不得刮研,但应检查其配合过盈量;厚壁轴瓦与轴颈的接触面不宜刮研。
5.3.7轴颈与轴瓦的顶间隙可用压铅法检查,压铅法用的铅丝直径不宜超过顶间隙的3倍。
顶间隙应按下列公式计算。
S1=b1-a1+a2/2
S2=b2-a3+a4/2
式中:
S1――一端顶间隙;
S2――另一端顶间隙;
b1、b2――轴颈上各段铅丝压扁后的厚度;
a1、a2、a3、a4――轴瓦合缝处结合面上各垫片的厚度或铅丝压扁后的厚度。
轴颈与轴瓦的侧间隙可用塞尺检查。
5.3.8对于在上、下轴瓦合缝处接合面间允许用垫片调整顶间隙的轴承,两边垫片的组合厚度应相等,垫片不得与轴颈接触,但距离轴瓦内缘不宜超过1mm。
5.3.9对于用润滑油润滑的轴承,装配时,轴承剖封面应涂以密封剂。
5.3.10液体摩擦轴承的装配应符合设备技术文件的规定。
5.3.11轴套与轴承座孔的配合及轴套与轴颈的配合均应符合设备技术文件的规定。
5.3.12含油轴套装配时,其表面若需擦洗,擦洗用油与轴套所含的润滑油相同,含油轴套与轴颈的间隙一般为轴颈直径的0.1﹪~0.2﹪。
5.3.13尼龙轴套与轴颈的间隙应为轴颈直径的0.5﹪~1.0﹪,装配时应涂以适量的润滑脂。
5.3.14推力滑动轴承的装配应符合设备技术文件的规定。
5.4滚动轴承的装配
5.4.1精度等级为E、D、C级需要清洗的滚动轴承,进行最后的清洗时,应用洁净的汽油将轴承冲洗干净。
5.4.2采用温差法装配滚动轴承时,加热温度不得高于100°C,冷却温度不得低于-80°C。
5.4.3轴承外圈与轴承座或壳体孔的配合应符合设备技术文件的规定;对于剖分式轴承座,轴承盖与轴承底座的接合面应无间隙,且轴承盖和轴承底座内孔的两侧不得卡紧轴承外圈(夹帮)。
5.4.4滚动轴承与轴肩或轴承座挡肩应靠紧,闷盖、透盖、垫环应均匀贴紧在轴承内圈或外圈的端面上,如设备技术文件的规定留有游隙,应按规定留出。
5.4.5单列向心球轴承、双列向心球面轴承和双列向心球面滚子轴承装配时,应预留出轴向热膨胀间隙,间隙一般应大于0.5mm,必要时,轴向间隙应按下式计算:
ΔL=L×α×Δt+0.15
式中:
ΔL轴向间隙;L两轴承的中心距;α轴材料的线膨胀系数,参见附录J(参考件);Δt工作时轴与环境的最大温差值。
对于人字齿轮轴的轴承,应留出因齿侧隙产生的轴向窜动间隙。
5.4.6单列向心推力滚子轴承、单列圆锥滚子轴承、双联单向推力球轴承和双向推力球轴承的装配,轴向游隙一般应符合表7~9的规定。
表7
单列向心推力球轴承轴向游隙
轴承
公称直径
轴承系列
36000
46000及66000
Ⅰ型
Ⅱ型
Ⅰ型
最小
最大
最小
最大
最小
最大
≤30
0.02
0.04
0.03
0.05
0.01
0.02
﹥30~50
0.03
0.05
0.04
0.07
0.015
0.03
﹥50~80
0.04
0.07
0.05
0.10
0.02
0.04
﹥80~120
0.05
0.10
0.06
0.15
0.03
0.05
﹥120~180
0.08
0.15
0.10
0.20
0.04
0.07
﹥180~260
0.12
0.20
0.15
0.25
0.05
0.10
表8
单列圆锥滚子轴承轴向游隙
轴承
公称直径
7000
27000
Ⅰ型
Ⅱ型
Ⅰ型
最小
最大
最小
最大
最小
最大
≤30
0.02
0.04
0.04
0.07
﹥30~50
0.04
0.07
0.05
0.10
0.02
0.04
﹥50~80
0.05
0.10
0.08
0.15
0.03
0.05
﹥80~120
0.08
0.15
0.12
0.20
0.04
0.07
﹥120~180
0.12
0.20
0.20
0.30
0.05
0.10
﹥180~260
0.16
0.25
0.25
0.35
0.08
0.15
﹥260~360
0.20
0.30
﹥360~400
0.25
0.35
表9
双联单向推力球轴承和双向推力球轴承轴向游隙
轴承
公称直径
轴承系列
8100
8200及8300
38200及38300
8400及38400
最小
最大
最小
最大
最小
最大
≤50
0.01
0.02
0.02
0.04
﹥50~120
0.02
0.04
0.04
0.06
0.06
0.08
﹥120~140
0.04
0.06
0.06
0.08
0.08
0.12
5.4.7双列圆锥滚子轴承和四列圆锥滚子轴承装配前,应检查轴承的游隙,径向游隙一般应符合表10的规定。
表10
双列圆锥滚子轴承和四列圆锥滚子轴承径向游隙
轴承公称内径
圆柱孔
辅助
1组
辅助
2组
基本组
辅助3组
辅助4组
辅助5组
圆锥孔
-
辅助
1组
辅助2组
基本组
辅助3组
辅助4组
最小
最大
最小
最大
最小
最大
最小
最大
最小
最大
最小
最大
﹥24~30
0
0.010
0.012
0.015
0.015
0.020
0.020
0.025
0.030
0.030
0.035
0.040
0.040
0.050
0.050
0.060
0.070
0.070
0.080
0.090
0.100
0.110
0.130
0.020
0.025
0.030
0.030
0.040
0.045
0.050
0.060
0.065
0.070
0.080
0.090
0.100
0.110
0.120
0.140
0.150
0.170
0.190
0.210
0.230
0.260
0.030
0.040
0.050
0.060
0.070
0.080
﹥30~40
0
0.040
0.045
0.060
0.075
0.080
0.090
﹥40~50
0
0.045
0.050
0.065
0.080
0.090
0.110
﹥50~65
0
0.050
0.070
0.090
0.120
﹥65~80
0
0.060
0.080
0.110
0.150
﹥80~100
0
0.070
0.100
0.130
0.170
﹥100~120
0
0.080
0.110
0.150
0.200
﹥120~140
0
0.090
0.120
0.170
0.230
﹥140~160
0
0.100
0.140
0.190
0.260
﹥160~180
0
0.110
0.150
0.210
0.280
﹥180~200
0
0.120
0.170
0.230
0.310
﹥200~225
0
0.140
0.190
0.260
0.340
﹥225~250
0
0.150
0.210
0.290
0.380
﹥250~280
0
0.170
0.230
0.320
0.420
﹥280~315
0
0.180
0.250
0.350
0.460
﹥315~355
0
0.210
0.280
0.390
0.510
﹥355~450
0
0.230
0.310
0.440
0.580
﹥400~450
0
0.260
0.350
0.490
0.650
﹥450~500
0
0.290
0.390
0.540
0.720
﹥500~560
0
0.320
0.430
0.590
0.790
﹥560~630
0
0.350
0.480
0.660
0.880
﹥630~710
0
0.400
0.540
0.740
0.910
5.5关节轴承
5.5.1外圈有装配槽的向心关节轴承的装配,应使轴承承受的径向负荷方向与外圈装配槽相垂直;特殊结构(非标准)的向心关节轴承,其承受径向负荷的方向应符合设备技术文件的规定。
5.5.2开型外圈的向心关节轴承,装配后外圈开缝处应合缝良好。
5.5.3关节轴承的旋转和摆动应灵活。
5.6齿轮传动装配
5.6.1轴心线平行且轴心线位置为可调整结构的渐开线圆柱齿轮副的装配,其中心距极限偏差±fa应符合表11的规定。
也可按设备技术文件规定的侧隙进行检查。
5.6.2轴心线平行且轴心线位置为可调整结构的“67”型圆弧齿圆柱齿轮副、圆柱蜗杆传动、圆弧齿圆柱蜗杆传动和圆锥齿轮副的侧隙应符合表12~15的规定。
如用压铅法检查侧隙,应沿大齿轮(或蜗轮)圆周不少于3处的等分部位检查,铅丝的长度应大于3个齿距,铅丝的直径不宜超过侧隙的3倍,对于齿宽较大的齿轮,沿齿宽方向应均匀放置至