推荐焊接质量事故反思word版本 17页.docx
《推荐焊接质量事故反思word版本 17页.docx》由会员分享,可在线阅读,更多相关《推荐焊接质量事故反思word版本 17页.docx(20页珍藏版)》请在冰豆网上搜索。
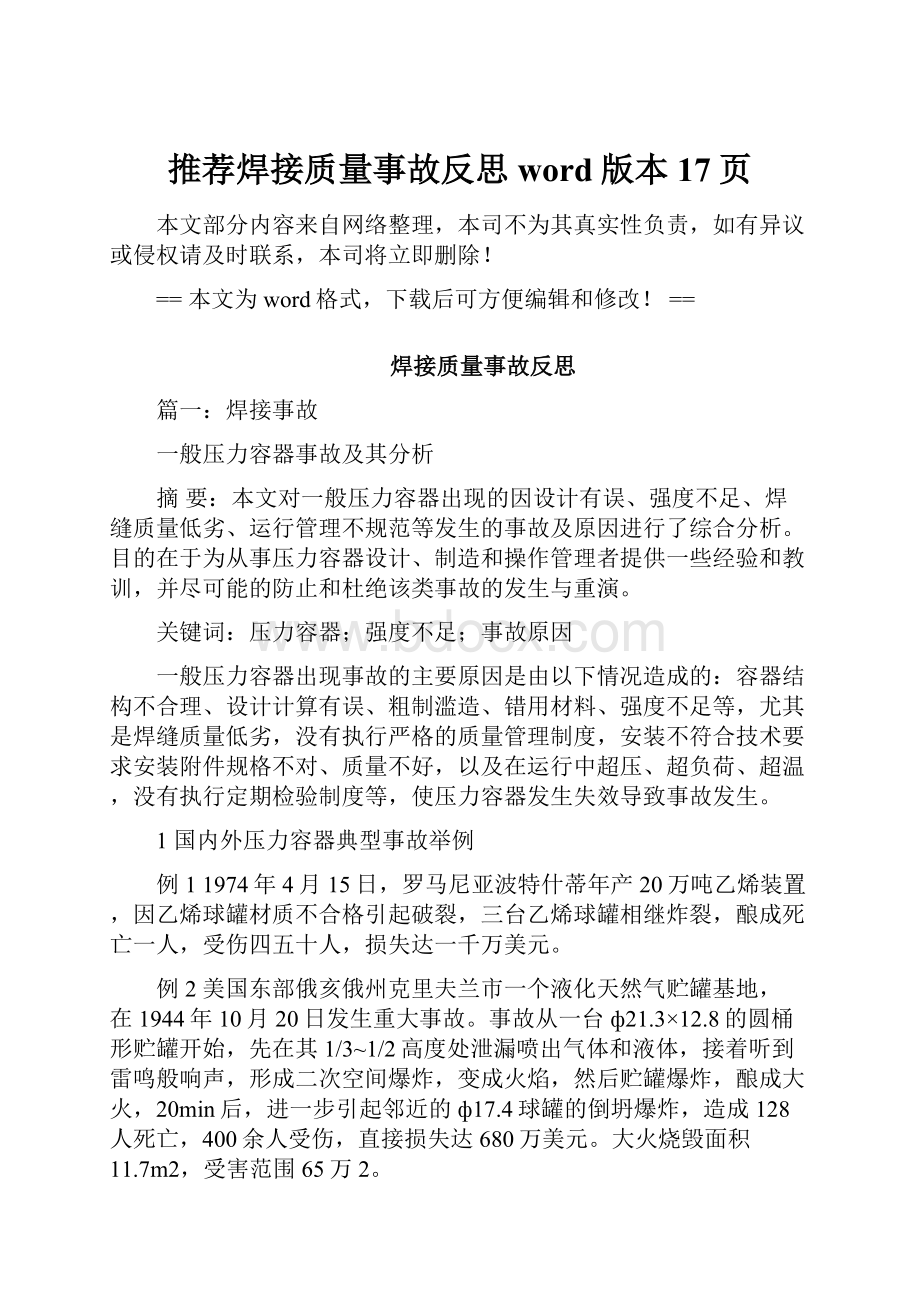
推荐焊接质量事故反思word版本17页
本文部分内容来自网络整理,本司不为其真实性负责,如有异议或侵权请及时联系,本司将立即删除!
==本文为word格式,下载后可方便编辑和修改!
==
焊接质量事故反思
篇一:
焊接事故
一般压力容器事故及其分析
摘要:
本文对一般压力容器出现的因设计有误、强度不足、焊缝质量低劣、运行管理不规范等发生的事故及原因进行了综合分析。
目的在于为从事压力容器设计、制造和操作管理者提供一些经验和教训,并尽可能的防止和杜绝该类事故的发生与重演。
关键词:
压力容器;强度不足;事故原因
一般压力容器出现事故的主要原因是由以下情况造成的:
容器结构不合理、设计计算有误、粗制滥造、错用材料、强度不足等,尤其是焊缝质量低劣,没有执行严格的质量管理制度,安装不符合技术要求安装附件规格不对、质量不好,以及在运行中超压、超负荷、超温,没有执行定期检验制度等,使压力容器发生失效导致事故发生。
1国内外压力容器典型事故举例
例11974年4月15日,罗马尼亚波特什蒂年产20万吨乙烯装置,因乙烯球罐材质不合格引起破裂,三台乙烯球罐相继炸裂,酿成死亡一人,受伤四五十人,损失达一千万美元。
例2美国东部俄亥俄州克里夫兰市一个液化天然气贮罐基地,在1944年10月20日发生重大事故。
事故从一台ф21.3×12.8的圆桶形贮罐开始,先在其1/3~1/2高度处泄漏喷出气体和液体,接着听到雷鸣般响声,形成二次空间爆炸,变成火焰,然后贮罐爆炸,酿成大火,20min后,进一步引起邻近的ф17.4球罐的倒坍爆炸,造成128人死亡,400余人受伤,直接损失达680万美元。
大火烧毁面积11.7m2,受害范围65万2。
例3国内某厂浴室用的一台换热器发生爆炸,强大气浪将浴室后墙冲垮,房屋倒坍134m2,房顶板全部倒坍,所有洗澡人员全部压在里面。
该换热器系自行制造,工艺质量特别是焊缝质量低劣,1978年10月发现焊缝大量漏水,敷焊了事,导致灾难性事故的发生。
例4国内某厂ф1000mm加压变换冷却塔,8mm厚16Mn钢板卷焊,操作压力为0.8MPa。
1970年投产时原高8m,1973年为提高冷却能力,增高3m,在现场焊接施工,当时为抢时间,在提高的3m内壁处未经喷铝防腐,因受H2S腐蚀而壁厚逐渐减薄,在使用、维修中也有所觉察(补焊过三次),终于在1976年12月爆成二段而倒坍,爆炸口位于接高段筒体器材上,壁厚已不到1mm,最厚的不到3mm。
2对一般常见事故技术分析
压力容器事故的原因,一般来说往往是多方面的,对事故的技术分析,要找出主要原因和直接原因。
首先进入事故现场,进行认真的检查与调查,必要时进行技术检验和鉴定,作出综合分析并确定事故原因。
2.1检查事故现场
在事故发生后,应迅速进入现场,进行周密的检查、观察和必要的技术测量,搜集容器爆炸碎片,拍摄现场照片等,尽力搜集较完整的第一手资料,其检查的主要内容有:
(1)容器本体破裂情况检查
检查容器本体的破裂情况是事故现场检查的最主要内容。
首先对容器破断面进行初步观察,对断口的形状、颜色、晶粒和断口纤维等特征进行认真观察和记录。
若破断口在容器焊缝部位,则应认真检查焊缝破断口有无
裂纹、未焊透、夹渣、未融合等缺陷以及有无腐蚀物痕迹。
对破断面的初步观察,大体上可以确定容器的破裂型式。
其次是对容器破裂形状的检查和尺寸测量。
当容器破裂后无碎块、碎片时,应测量开裂位置、方向、裂口的宽度、长度及其壁厚,并与原有周长和壁厚进行比较,计算破裂后的伸长率及壁厚减薄率;对碎裂后几大块的容器,可按原来的部位组装进行测量计算,并计算其破裂时的容积变形及碎块或碎片飞出距离,飞出破片的重量。
最后检查容器内外表面金属光泽、颜色、光洁程度。
有无严重腐蚀,有无燃烧过的痕迹等。
(2)检查安全装置是否完好
当容器发生爆炸事故后,在初步检查安全阀,压力表、温度测量仪表后,再拆卸下来进行详细检查,以确定是否超温运行。
对压力表主要检查进气口是否被堵塞以及爆炸前压力表是否已失灵。
对安全阀主要检查进气口是否被堵塞,阀瓣与阀座是否被粘住,弹簧锈蚀,卡住或过分拧紧,重锤被移动等失灵现象,以及安全阀有否开启过的迹象。
必要时应放到安全阀试验台上检查开启压力的试验。
对温度测量仪表主要是检查温度计或温度测量仪表是否失灵。
若容器上有减压阀者,应检查有否失灵现象。
装有爆破片的容器,可检查是否已爆破。
若未爆破,如有必要应作爆破压力试验,测定其爆破压力。
(3)事故现场破坏及人员伤亡情况
压力容器爆炸后,周围建筑物的破坏情况,即地坪损坏情况、室顶、墙壁厚度及其破坏状况,与爆炸中心的距离以及门窗破坏情况与离爆炸中心的距离等。
这对于估算容器爆炸量的计算有反证作用。
人员伤亡,包括受伤部位及其程度,以便确定重伤或轻伤。
另外,对现场及其周围有否易燃物燃烧痕迹等也应作检查分析。
2.2事故过程调查
容器在发生事故前的运行情况,即物料数量、压力、温度等运行参数是否正常;容器是否渗漏、变形以及异常响声等。
容器开始出现异常现象的时间,采取的应急措施以及安全泄压装置的动作情况;操作人员所在位置,爆炸过程及现象,如有无闪光、着火、一次或两次响声等。
操作人员的操作技术水平,有无经过安全培训考试合格等情况,以利于判断有无误操作现象。
2.3压力容器设计、制造情况的调查
查阅压力容器技术资料,检查设计结构是否合理,强度是否足够;检查压力容器选材是否满足工艺要求,制造质量尤其是焊接质量是否合格;容器使用年限、投产使用年份以及检验情况等,以便判断是否因设计、制造不良引起的事故。
2.4技术检验和鉴定工作
当压力容器的操作条件比较复杂,在通过上述事故分析后仍未能确定事故原因时,需要进一步进行技术检验、计算和鉴定工作,才能确切地查明事故原因。
2.4.1材质分析
通过分析容器的材质成分、性能、核对制造压力容器的材料,或检查容器使用过程中所发生的变化。
(1)化学成分检查
当压力容器发生事故后,应复验材质的化学成分,或着重检验对容器性能有影响的元素成分。
对可能发生脱碳现象的压力容器,还要化验表面层含碳量,和内层钢材的含碳量进行对比,以便查明是否由于介质对钢材的影响,所以复验化学成分
可鉴别容器是否用错钢种或运行中的影响。
(2)机械性能测定
压力容器的破裂与金属材料的机械性能直接有关。
一般是检查材料强度、塑性,以判断是否用错材料;对于低温下工作的容器,通过金属材料韧性指标(冲击值)的测定,即可鉴别容器是否因脆性断裂破坏的。
做机械性能测定的试件,可从断口部位截取,并与其它部位的试件作对比。
(3)金相检查
金相检查观察断口及其它部位金属相的组成,判断是否有/脱碳0及裂纹性质,对于鉴别事故性质作用甚大。
例如可以观察到是穿晶裂纹还是晶间裂纹,观察裂纹尖端是圆纯的还是尖锐的。
(4)工艺性能试验
工艺性能试验主要是钢材的焊接性能试验、耐腐蚀性能试验等。
试验时应取与破裂容器相同的材料、焊条和焊接工艺,以观察试样与破裂容器类同的缺陷的可能性。
工艺性能试验往往是事故检查的一种辅助手段,起验证作用。
2.4.2压力容器断口分析
断口分析是研究分析破坏现象微观机理的一种重要手段。
断口分析可分为宏观分析和微观分析两种。
(1)断口的搜集及其保护、保存在压力容器发生事故的现场,应尽可能地搜集破断口或碎片截取制成断口试样。
对于破断口,防止沾污表面,并用水玻璃涂其表面防止腐蚀。
被沾污了的断面应加以清洗。
清洗后的断口用酒精漂净,并用热风吹干,保存在干燥器中备用、备查。
(2)断口宏观分析
断口宏观分析是用肉眼或借助于放大镜对断口进行观察,这是断口分析的主要手段。
金属的拉伸断口,一般由三个区域组成,即纤维区、放射区和剪切唇。
根据这三个区域在整个断口所占有的断面积,大体上可确定其断裂类型。
凡脆性断裂的断口,纤维区和剪切唇很小,大部分是放射区,就是说金属在断裂前没有较大塑性变形,断裂主要是在高速扩展下进行的。
脆裂断口还可根据放射线(常称人字形)的指向确定裂源的起始点,并可由此查清裂纹的扩展情况。
需要指出,破裂断口的裂纹起始点可能不(3)断口微观分析
断口微观分析是利用光学显微镜、电子显微镜对断口的微观形态进行观察,结合宏观分析确定断裂性质。
目前广泛使用的是电子显微镜,它的放大倍数可达201X0倍。
通常使用的是透视式电子显微镜和扫描电子显微镜。
前者是对用断口表面复制的薄膜进行观察,后者则可直接观察实物断口。
有的电子显微镜配有电子计算机,不仅可作断口定性分析,还可对断口的成分作定量分析。
2.4.3压力容器事故分析中的计算
在压力容器事故分析中,往往要进行计算和液化气体过量充装可能性的计算等工作。
对压力容器进行强度计算,主要是为了判断是设计强度不足还是运行后因腐蚀减薄导致强度不足的破裂。
在强度计算中测量的壁厚,应注意是破裂前的厚度,而不是破裂变形后的壁厚。
对于在焊缝处破裂的容器,若有未焊透缺陷时,还要考虑未焊透处的应力集中或对疲劳强度的削弱。
液化气体容器的事故分析中,还应作过量充装可能量的计算,即液化气体满液充装和过量充装时,在环境温度升高几度时,容
器将发生破裂。
3压力容器事故综合分析
压力容器破裂爆炸事故的调查分析工作,在经过事故现场的观察检查和测量,对事故发生过程和容器设计、制造、投产后运行情况的调查了解,以及必要的技术检验、鉴定和计算之后,则应对事故原因进行综合分析确定其直接原因和主要原因。
由于压力容器类型繁多,每一次事故均应按具体情况作具体分析。
3.1爆炸事故性质及过程的判断
压力容器的破裂,有的是在工作压力下发生的,有的是在超压的情况下发生的。
其中有的属于物理性爆炸,有的属于化学性爆炸,所以要具体分析事故原因,首先要正确判断爆炸的性质或过程以及容器破裂压力等。
一般容器破裂及其由此引起的气体爆炸,可有以下几种情况:
(1)工作压力破裂的容器
当安全泄压装置正确、可靠,容器在破裂前没有开启泄放,压力表也无异常,事故后检查尚无失效、失灵,操作和工艺条件也属正常等,无超压迹象。
则可判断为在工作压力下的破裂。
工作压力下破裂的容器,一般是发生在容器粗制滥造,即壁厚不够、焊缝有严重缺陷、以及容器长期不作技术检验、年久失修和器壁严重腐蚀而普遍减薄的容器。
工作压力下器壁上的应力超过材料屈服极限的则少见。
(2)超工作压力下破裂的容器
当容器内压力较多的超过工作压力而发生爆炸,象这类事故一般是操作人员违章作业,超过工作压力,而容器本身的安全泄压装置不全或失灵、失效,器壁上的应力超过材料的强度极限而发生破裂,这种破裂一般都有一段增压过程,故破裂一般都属于韧性破裂。
(3)化学反应而爆炸的容器
容器内化学反应爆炸是指发生不正常的化学反应,使气体体积增加或温度剧烈增高致使压力急剧升高导致的容器破裂。
发生化学反应爆炸的容器,其安全阀可能有排放过的迹象,但一般却来不及全量排放。
爆炸后检查压力表可发现指针撞弯、不能返回零位等异常现象,以及器内可能有燃烧的痕迹或残留物等。
(4)容器破裂后的二次空间爆炸
一般盛装易燃介质的容器,在其破裂后,器内逸出的易燃介质与空气混合后,在爆炸极限范围又发生的第二次爆炸,这种爆炸一般形成火灾,往往导致灾害性事故。
容器破裂后的二次空间爆炸,其特征是可以看到闪光和两次响声以及常有燃烧痕迹或残留物等。
3.2.2脆性破裂
脆性破裂的容器,在破裂形状、断口形貌等方面具有一些与韧性破裂相反的特征。
即没有明显的伸长变形,容器的壁厚一般也无减薄。
裂口齐平,断口呈闪烁金属光泽的结晶状,厚壁容器的断口上,还常可找到人字形纹路(幅射状)。
由于脆性破裂往往在一瞬间发生,器内压力无法通过一个裂口释放,因此脆性破裂的容器常裂成碎块飞出。
金属的脆性断裂是由于裂纹引起的,所以破裂时实际应力较低。
在运行中因温度突变而发生脆断的也多见。
篇二:
质量事故报告及原因分析
关于5、6、7月份客户反馈所出的质量事故报告及原因分析
一.北京北益:
1.不该打磨的打磨掉了
2.法兰失圆,明知道失圆还发了过去。
事故原因:
由于技术工艺指导文件不明,造成装焊后的加工余量太多,所以将法兰敲打
变形,造成法兰孔变形,法兰中间部分的厚度变薄,边缘部分勉强达到图纸要求。
造成的直接损失:
运费8000元,29件法兰更换3500元。
合计11500元。
另去北京返
工费用及对我公司造成的不良印象暂不计算。
主要责任:
公司处罚:
二.山东恒信:
1:
15件主母线孔小,扩孔。
2:
26件主母线孔偏1.5~2mm以上。
3:
17件出线壳体支筒的度数不对。
其中四件的支筒法兰孔不对称。
事故原因:
1:
主母线壳体孔偏小及孔的位置偏差,受上海西电老的传统检验观点,任
意表态放行。
2:
对出线壳体的支筒角度偏差a:
外协厂家对图纸要求不明确,未理解的
基础上盲目加工。
B:
装焊前未按图纸要求,强行施工。
造成的直接损失:
主母线孔扩孔及对主母线孔偏进行矫正除派去我公司人员现场维修所
耽误的时间(顾晨在恒信维修了5天)及费用,补贴给对方维修费用2500元。
来回运费4000元。
合计6500元。
出线壳体角度不对,对方帮忙想办法将导体改制,现改制费用要听对方反馈。
退
厂4件壳体的运费1000元。
主要责任:
主母线孔小由质检部门负主要责任。
钳工班组钻孔人员。
出线壳体角度偏差及孔不对称由技术部门负主要责任。
公司处罚:
三.山东互感器:
1:
主法兰的内R25不到位,光洁度达不到要求。
2:
支筒法兰的R8不到位,光洁度达不到要求。
3:
筒体内表面的光洁度达不到要求。
4:
支筒背面φ250的尺寸现只有φ245,绝缘盆子装不进去。
5:
252KV壳体支筒背面φ250范围内的光洁度严重不合要求。
车削刀痕严
重。
6:
沉孔的深度不一致。
7:
252KV壳体支筒法兰缺料未车出,就擅自发货到现场。
8:
内焊缝用半自动焊,焊缝高度高低不一,造成打磨不光滑。
事故原因:
a:
R不到位及光洁度达不到要求是由于加工人员不按图纸要求加工造成。
B:
筒体内表面光洁度达不到要求,是由于打磨人员赶时间,不讲求质量。
C:
支筒背面尺寸不对及光洁度达不到要求,是镗床加工人员不按图纸加工
造成。
D:
沉孔深度不一致,是我公司的加工工艺工序有问题,需改进加工工艺。
e:
法兰缺料,主要责任是检验人员未检查出。
F:
内焊缝焊接有缺陷,焊接人员敷衍了事。
造成的直接损失:
公司先后派4人前去维修返工合计15天,退货运费201X元。
如加上4人前去维修的费用,将达上万元。
主要责任:
机加工
焊接
修磨
公司处罚:
四.山东兴驰:
1:
18件共箱壳体退货返工。
2:
三工位壳体10件φ536处的R3过渡不圆滑。
其中一件充气嘴偏差2mm。
3:
接地壳体4-M12不要求镶钢丝螺套反而镶了钢丝螺套。
导致无法装配。
4:
接地壳体上的两个焊接块,背面未打磨。
5:
CT壳体5XC.002.009,010,388,409共21件,下主筒法兰得孔与上主筒
孔位置度偏差,导致厂家无法装配。
事故原因:
a:
共箱壳体的制作,接到订单后,未按照图纸要求准备相应的模具及工装,
胡乱施工。
B:
三工位壳体上出现的问题,质检部门未仔细检查。
其中一件充气嘴偏差,
在生产会议上已经提出,生产技术不同意更换,坚持发货,造成退货。
C:
接地壳体不该镶钢丝螺套的是由于生产管理人员图纸未发放,工人盲目生
产。
检验人员未按图纸仔细检查。
D:
接地壳体焊接块未打磨,主要是检验人员未检查到位,修磨人员怕麻烦,
未打磨。
F:
钳工划线未按工艺要求去做。
出厂未检验。
造成的直接损失:
公司先后派3人到现场返修,造成退货的损失单运费7000元,钢丝
螺套费用100元。
21件退货来去运费6000元,回来后还得换法兰。
主要责任:
技术部门
质检部门
钳工班组
修磨班组
公司处罚:
五.广西中电:
共箱壳体的支筒返工后的R造成的尖角,未清除。
事故原因:
检验人员在壳体返工后未按规定复检。
造成的直接损失:
公司派员去现场返工处理。
费用500元。
主要责任:
质检部门
公司处罚:
六.西安西开:
西安新产品PASS壳体,筒体内部的4个焊接块,我公司单边烧焊,西开公
司自己找陕西富通焊接后在镗床上加工。
事故原因:
我公司技术部门工艺不明确。
七.北京天威瑞恒:
1:
法兰筒与法兰帽直径13的孔偏1-3mm。
2:
法兰筒密封槽尺寸为φ312+0.11,实测311.5-311.9.
3:
测量端子安装孔(4—M4)偏约1mm,测量端子法兰安装不上。
4:
法兰筒厚度要求35,实测(36-37)
5:
密封槽有振刀痕迹。
事故原因:
a:
工人在打孔时,打孔模具未完全靠实,导致打孔移位。
检验未检查。
B:
操作者未严格按照图纸要求加工,出厂未检验,导致质量失控。
造成的直接损失:
有部分需退货,此类产品正在协商中,待处理。
主要责任部门:
钳工班组相关人员,机加工班组相关人员,质检部门。
八:
上海西电:
1:
漏气率太高。
单7月15日一天漏6件工件。
2:
外观质量严重下滑,磕碰划伤严重,焊缝的质量严重下滑。
A:
带支柱的盖板,支柱和盖板连接的外焊缝,手工焊接高低不平,焊缝外
观形状很难看。
B:
拔口后的环焊缝,手工焊接,焊缝高低不平,宽窄不一,歪歪扭扭。
收
弧点未认真修磨,收弧点的气孔比较严重。
C:
自动焊焊缝严重的咬边,烧伤,气孔比较严重。
详见现场照片。
3:
盖板上所用的φ60的铝棒,材质任意选取供应商,未经检验试制,大面积
使用,导致a:
场内现场检测出漏气的,无法使用的,前后将近100件。
B:
单
7月19日从上海退回221件盖板,现上海还有10多件要退回。
4:
按照上海西电领导到我公司现场反应的问题:
A:
拔口后,口不正,使用锤子敲打,导致敲打的痕迹留在壳体上,油漆后相
当难看。
(共箱)原因:
划线开孔未严格按照工艺要求。
造成拔口后形位不正。
B:
拔口模具未修磨就使用,造成拔口后表面损伤。
原因:
指挥人员不负责任。
C:
环焊缝的自动焊的收弧点,未修磨就直接出厂,导致外观难看。
原因:
焊
工未对自己的收弧点按要求处理,加上修磨人员不负责任。
D:
纵焊缝焊接时的接头未控制好,修磨时也未认真修磨。
原因:
焊工未对
自己的收弧点按要求处理,加上修磨人员不负责任。
F:
表面喷漆,未清理干净,不光亮。
原因:
底漆未清理干净,有缺陷处未用
腻子将其修补好。
事故原因:
A:
焊接班只顾抢工时,不顾焊接质量,导致大面积漏气,焊缝不美观。
B:
采购人员对材料的使用要求关注度不够,任意采购。
质检部门对材料进
场的检验未执行。
技术部门未对新供应商提供的材料进行小批量试制,未通
知质检部门对其进行严格的试验。
C:
检漏人员未认真检漏。
造成的经济损失无法估量。
九:
山东恒信和重庆博森:
产品在运输过程中发生碰撞,导致法兰面有磕碰划伤。
事故原因:
在装车过程中及产品发运过程中,未能做到很好的保护。
201X/7/22
篇三:
焊接质量保证措施
焊接质量保证措施
批准:
审核:
编制:
河南第二火电建设公司工程公司焊接班
年月日
焊接质量保证措施
1.总则
1.1为贯彻公司质量方针,实现公司质量目标,保证焊接工艺被严格执行、焊接质量管理制度真正落实,确保焊接施工过程处于受控状态,特制定本措施。
1.2焊接班质量管理人员、技术人员、施工人员必须严格执行本措施。
2.质量责任
2.1.焊接班班长为本班质量第一责任人,对质量问题从行政角度负全面领导责任。
2.2.焊接班专工全面负责本班管理范围内的工程焊接技术和质量管理以及焊接人员的资格审核等工作,同时监督本班质量体系的运行情况,保证质量体系持续有效运行。
2.3.焊接班质检员负责工程焊接质量监督检查和班级验收工作,代表焊接班行使质量监督权。
2.4.各班班长为本班质量第一责任人,对本班的质量工作负责。
班组技术员对分管范围内的质量工作负责,对焊接质量有监督检查权,并配合质检员进行二级验收,和班长、班兼职质检员共同进行一级检查验收。
2.5.焊接施工人员是工程质量的直接形成者,对属焊工应知应会部分或不遵守工艺纪律、不按技术交底要求施焊而出现的质量问题承担主要责任。
对其施焊的焊口出现泄漏承担质量责任。
3.质量保证要求
3.1.焊接班组织机构成立后,建立质量保证体系,以落实各级人员的质量责任,以书面形式明确各级质量管理人员的分工、职责与权限。
3.2.贯彻公司质量保证手册及程序文件,建立质量管理的制度,并组织有关人员认真学习执行。
3.3.焊接施工过程程序化,按照“焊接施工过程流程图”组织施工和检查验收。
3.4.焊接技术管理程序化、标准化、微机化,按照“焊接班技术管理制度”的要求开展技术工作。
3.5.对上级和公司、工程公司下发的或焊接班制定的与质量有关的文件认真传达,组织学习,贯彻执行,并妥善保存。
3.6.持续开展质量教育培训活动,组织职工学习焊接专业规程、规范和标准,学习焊接理论和操作技术,不断提高全员质量意识、技术水平和管理水平。
3.7.严格质量监督,保证施工工艺的执行,及时发现并消除焊接质量通病。
严格质量检查验收,发现并消除超标焊接缺陷。
3.8.中低压管道焊接质量视同高压管道焊口。
4.焊接人员要求
4.1.技术人员要恪守岗位职责,遵守焊接技术管理制度。
4.2.焊接质检员要恪守岗位职责,参与作业指导书等技术措施的审核,对违章操作应及时制止并报告。
注重质量监督资料的积累和总结,掌握焊工的技术状况,对虽有相应资格但已不能胜任重要部件焊接的焊工,有权向班长提出降级使用。
4.3.焊工必须持证上岗,从事受监部件,承压管道、承重钢结构等焊接的焊工,必须根据《焊工技术考核规程(DL/T679-1999)》质量检验检疫总局颁布的《锅炉压力容器、压力管道
焊工考试与管理规则》考核合格,并只能担任其合格项目范围内的焊接工作,严禁无证焊接(包括点焊)或担任超越其合格项目的焊接工作。
4.4.参加受热面管子焊接的焊工,上岗前必须经过模拟练习,焊接两个试样,经外观检查和折
断面检查全部合格,才能上岗作业。
4.5.从事受监部件焊口焊接的焊工,当日一次合格率低于80%者,须下岗练习,待合格后重新
上岗。
对焊口一次合格率连续3日均低于85%者,停止该焊工从事该项目焊接作业。
4.6.对焊接质量一贯低劣、严重违反工艺纪律,造成严重焊接质量事故,或给公司和焊接班带
来严重不良影响的焊工,停止其焊接施工的资格。
4.7.焊工上岗前要接受技术交底,未经交底不得上岗。
焊工接受交底时,要弄清焊接部件名
称、材质、使用焊接材料的牌号、工艺要求、质量标准等内容,方可上岗施焊。
4.8.焊工对钳工的装配或对口质量进行检查验收,不合格不得进行点焊。
4.9.焊口(缝)外观质量不合格不得进行无损检验。
4.10.焊工必须严格执行焊接施工工艺纪律。
5.质量检查验收要求
5.1.实行焊接质量三级检查验收制度,自检与专检相结合。
5.2.坚持日常质量监督检查制度,质检员每天将管理范围内的施工场所巡视一至两遍,深入实
际监督技术措施的实施,记录检查情况,对发现的违反工艺纪律的行为(如焊后清渣不净或不清渣、不自检或不认真自检、不处理焊接缺陷、焊后不打钢印、不按技术交底要求施焊或未经技术交底施焊、无证施焊或超越其合格项(来自:
:
焊接质量事故反思)目施焊等)或焊接质量不合格的焊口(焊缝),以“焊接质量整改通知单”的形式通知到施工班组,限期整改合格,并保存反馈和复检结果。
施工班组在接到整改通知单后,应及时安排处理,不得以任何理由拒接、拒不安排整改,或无正当理由拖延整改时间。
5.3.施工过程中焊工应对自己所焊的焊缝及时清理和修整,按焊接接头表面质量标准认真进行
外观检查,并消除超标缺陷