年产15万套汽车发动机铝合金缸盖生产线技术改造资金申请报告.docx
《年产15万套汽车发动机铝合金缸盖生产线技术改造资金申请报告.docx》由会员分享,可在线阅读,更多相关《年产15万套汽车发动机铝合金缸盖生产线技术改造资金申请报告.docx(33页珍藏版)》请在冰豆网上搜索。
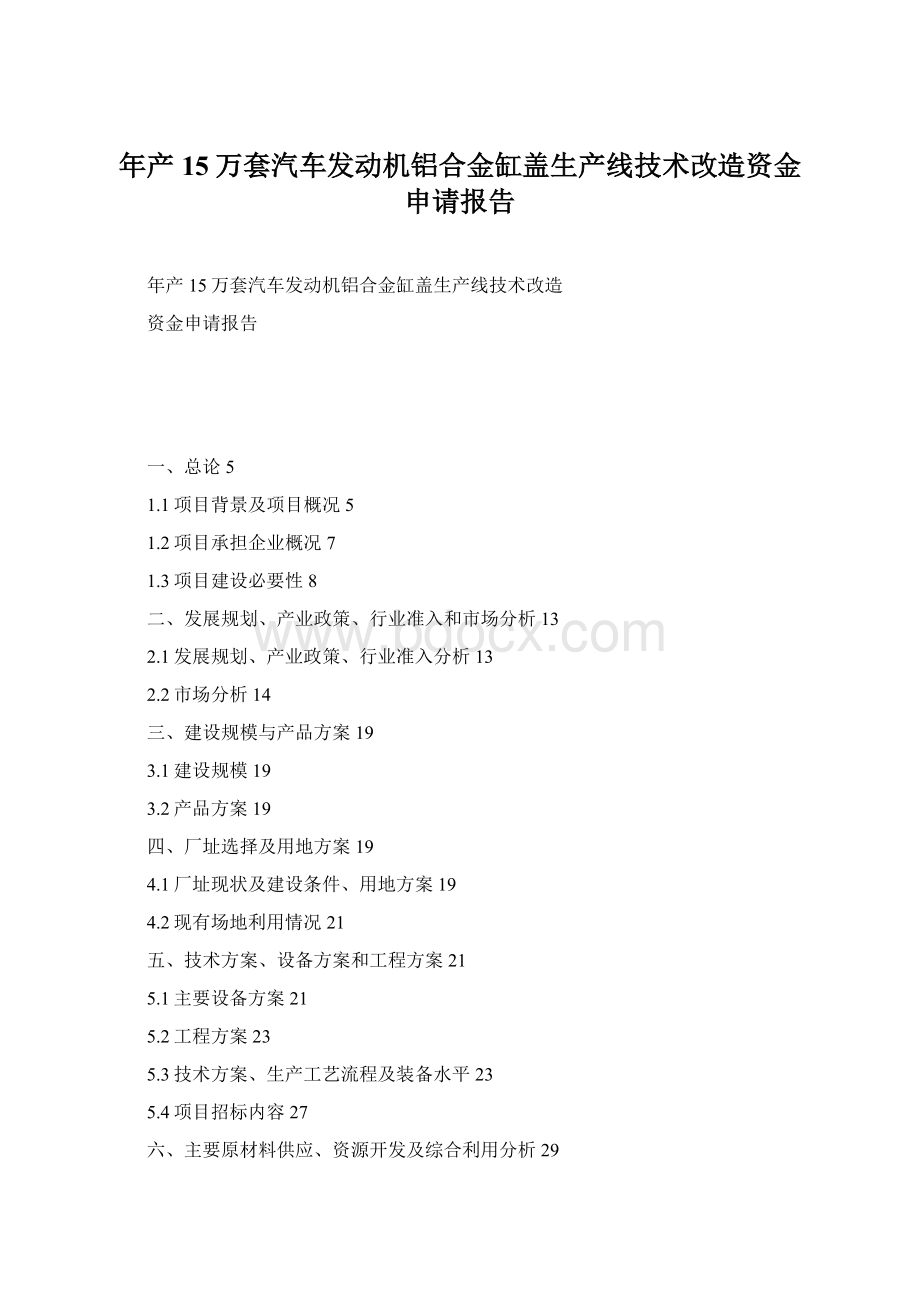
年产15万套汽车发动机铝合金缸盖生产线技术改造资金申请报告
年产15万套汽车发动机铝合金缸盖生产线技术改造
资金申请报告
一、总论5
1.1项目背景及项目概况5
1.2项目承担企业概况7
1.3项目建设必要性8
二、发展规划、产业政策、行业准入和市场分析13
2.1发展规划、产业政策、行业准入分析13
2.2市场分析14
三、建设规模与产品方案19
3.1建设规模19
3.2产品方案19
四、厂址选择及用地方案19
4.1厂址现状及建设条件、用地方案19
4.2现有场地利用情况21
五、技术方案、设备方案和工程方案21
5.1主要设备方案21
5.2工程方案23
5.3技术方案、生产工艺流程及装备水平23
5.4项目招标内容27
六、主要原材料供应、资源开发及综合利用分析29
6.1主要原材料供应29
6.2资源开发和利用方案29
6.3资源节约措施30
七、总图、运输与公用辅助工程30
7.1总图布置30
7.2场内外运输32
7.3公用辅助工程32
八、节能措施35
8.1能耗状况和能耗指标分析35
8.2节能措施和节能效果分析35
九、环境影响分析36
9.1厂址环境条件和现状36
9.2项目建设和生产对环境的影响36
9.3环境保护措施方案38
9.4环境保护投资39
9.5环境影响评价39
十、劳动安全卫生与消防39
10.1危害因素与危害程度39
10.2安全措施方案40
10.3消防设施41
十一、投资估算及资金筹措41
11.1投资估算表41
11.2资本金筹措42
11.3申请专项资金的主要原因和政策依据42
十二、财务分析及评价结论43
12.1不确定性分析43
12.2财务评价结论44
12.3项目风险分析46
十三、经济和社会影响分析47
13.1项目的影响47
13.2项目对社会的影响分析48
13.3项目与所在地互适性分析49
13.4社会评价结论49
十四、项目进展情况49
十五、结论与建议51
十六、需要提交的有关附件51
一、总论
1.1项目背景及项目概况
项目名称:
年产15万套汽车发动机铝合金缸盖
生产线技术改造
承担单位:
某汽车工业有限公司
企业负责人:
当前国家汽车零部件行业发展的思路是:
实施“市场导向,调整结构,科技创新,发挥优势,实现同步发展,参与国际分工”的发展战略,即以市场为导向,以结构调整为重点,以科技创新为突破口,继续支持和鼓励一批具有比较优势和发展潜力的关键汽车零部件产品排头兵企业,围绕上品种、上水平、上效益,充分利用高新技术,提高开发能力,推动汽车零部件行业结构优化和产业升级,增强竞争实力,实现与主机厂同步发展,参与国际分工的目标。
铝合金件金属型铸造方法由于其生产率高、劳动环境清洁、铸件表面光洁和内部组织致密等优点而被广泛应用。
尤其是汽车发动机部件,日、美、英、德和意等工业发达国家很多采用金属型重力浇注方法生产汽车发动机铝缸体、铝缸盖和铝活塞。
近几年,我国许多厂家也引进先进金属型设备或自制设备生产汽车发动机缸盖、进气管和活塞等铝铸件。
某汽车工业有限公司根据市场需求,经调研,拟实施年年产15万套汽车发动机铝合金缸盖生产线技术改造,以对产品质量进行提升,适应市场需求,创造更多的经济效益和社会效益,增强市场竞争能力,在国际市场开辟了一个崭新空间,特提出实施本项目。
1、建设规模:
年产15万套汽车发动机铝合金缸盖
2、项目完成后的生产规模以及具体的产品数量见下表。
产品方案表
序号
产品名称
规格
单位
生产规模
备注
1
缸盖
套
150000
3、主要原辅材料消耗量:
主要原辅材料用量表
序号
产品名称
规格
单位
需求数量
1
铝合金
吨
2250
2
包装材料
万套
15
4.主要公用工程需求量(略)
5.主要经济指标
⑴总投资:
4950万元
其中固定资产投资4750万元
流动资金200万元
(2)总成本:
7353万元
(3)销售收入:
15000万元
(4)销售税金及附加:
1587万元
增值税:
1442万元
(5)利润总额:
5760万元
(6)所得税:
1440万元
(7)税后利润:
4320万元
(8)主要经济评价指标
●财务内部收益:
25.63%
●投资回收期:
3.3年
●投资利润率:
116.37%
●投资利税率:
177.56%
●盈亏平衡点:
30.3%
1.2项目承担企业概况
某汽车工业有限公司位于某机械工业园,是一家专业从事汽车发动机缸盖、活塞系列产品研发、生产、销售的厂家。
优越的自然条件和宏观环境,是企业生存发展良好的外部空间,公司目前拥有员工180多人(其中技术人员、管理人员占总数的25%以上)。
有3条缸盖、3条活塞高效柔性生产线,拥有整套先进的铸造、热处理、机加与检测设备。
为保证产品质量。
公司引进一系列国内外先进加工设备,专门从事铸造件生产设备的有熔化炉、金属模铸造机、树脂混砂机、壳芯机、射心机等铸造设备,机加工设备的有活塞专用加工流水线和用于缸盖加工的多台进口、国产加工中心,以及精密的检测设备等。
主要生产20多种系列多种规格型号汽车缸盖、活塞等产品.
公司自建立以来,为满足顾客愿望及达到“企业上规模,管理上台阶,产品上档次”的目的,先后建立了一整套从设计开发到售后服务的管理体系。
企业不仅依靠价格的优势、优质的售后服务赢得顾客,更重要的是依靠先进的科学技术、系统的管理理念不断的开拓创新,以高质量的产品优势赢得市场。
为了满足客户要求和适应市场需要,公司在上海设立了新产品研发中心。
本公司生产的产品在欧洲、北美、澳大利亚、中东、东南亚市场受到客户的一致辞好评和支持,国际市场前景非常乐观。
公司奉行以人为本的管理理念,本着“让每个客户满意的目标而努力,高品质的和一流的服务”的经营宗旨,培养造就了一支素质优良、经验丰富、技术娴熟的职工队伍。
公司按照IS09000的质量管理体系标准组织、管理生产。
在生产的全过程中,通过严密的管理程序和严格的控制手段,追求产品的零缺陷。
公司管理基础稳固,人力物力资源充裕,产品市场前景广阔。
全体员工上下一心,众志成城,依托技术进步,不断追踪行业技术前沿,“强化质量管理,确保公司信誉,致力科技开发,争创世界水准”。
1.3项目建设必要性
①、是汽车工业战略发展的需要
目前我国运输用铝型材的市场增幅很快,汽车、高速列车、城市轻轨、航空航天、船舶、集装箱及自行车用铝型材的应用不断增长,已占有全国铝型材市场1/3强。
而近一段时间,尤以汽车用铝型材的发展更加引人注目。
从世界范围的角度来看,汽车用铝量是逐渐上升的。
在欧美和日本等发达国家和地区增幅达10%。
按照2000年统计,全球汽车平均每车用铝已由1978年的50公斤上升到107公斤,增长1.14倍。
据专家预测,到2008年世界中级轿车平均每车用铝将达到130公斤,美国1977年生产汽车平均每车用铝45公斤,而进入90年代,单车用铝量以每年4%的增长幅度递增,1999年各种汽车用铝平均达112公斤,到2005年美国汽车用铝平均每车将超过130公斤,个别车型达到200公斤以上。
欧洲在1990年生产的汽车平均每车用铝53公斤,90年代后期已达到65公斤,2000年增至83公斤,到2005年达到119公斤,欧洲铝业协会统计和预测,到2015年欧洲汽车用铝平均每车将达到200公斤。
德国汽车用铝不断增长,由1977年的单车用铝35公斤到90年代末已达到70公斤。
1998年汽车用铝量约占该国铝业制品总产量的38%,已成为德国铝业最重要的用户之一。
日本汽车轻量化程度较高,用铝较多是主要原因。
2000年每车用铝已高达270公斤。
由此可见,进入21世纪以来,世界发达国家轿车生产厂家依然对汽车用铝的应用充满了浓厚的兴趣,铝合金用量持续增长,这种需求是基于当今世界各国极为关注的能源、环境和安全这三大问题。
多年以来,汽车行业一直在汽车的结构设计、材料选用和制造技术等方面开展试验研究工作,努力开发安全可靠、高速舒适、节能环保型现代汽车,其首要的问题是汽车轻量化。
汽车轻量化是实现高速、安全、环保、舒适的最佳途径。
据专家研究表明,一辆汽车使用铝材的减重空间为35%以上,减重节油的潜力为39%左右,汽车质量每少3%,油耗的降低可达1~3%。
据有关资料,汽车每使用1公斤铝,可降低自身质量2.25公斤,减重效应高达125%。
同时在汽车整个使用期内,还可减少废气排放2公斤。
铝合金代替传统的钢铁制造汽车,可使整车质量减轻30%~40%,制造发动机可减重30%,制造缸体和缸盖可减重30%~40%,轿车全铝车身比原钢材制品轻40%以上,汽车铝合金车轮减重可达50%左右。
早在20世纪初期,欧美各国就将铝合金材料用到汽车车身和发动机上,日本的汽车铝化是从1950年以后开始的。
率先用到汽车上的铝合金铸件主要是发动机上的零部件以及变速箱、制动器等部件上的零件。
日本在90年代初,汽车用铝材的品种主要以铸件为主,占全部铝合金的80%,近年来的发展,铝合金铸件以延伸到发动机缸体、变速箱的壳体、轮毂等大型汽车零件的开发与应用。
据统计,近20年来,全球铝铸件的总产量平均每年以约3%的速度递增,而总产量中的60%~70%用于汽车制造。
目前,汽车用铝铸件的主要部件为:
发动机系的发动机缸体、缸盖、活塞、进气歧管、水泵壳、油泵壳等;传动系的变速箱壳、离合器壳等;底盘行走系的横梁、上/下臂、转向机壳、制动总泵壳等;汽车用铸造合金以AL-Si系合金为主,所用铝铸件多采用压力铸造、低压铸造和金属型重力铸造工艺生产,其中压铸件占70%以上。
21世纪初,北美轿车市场上铝质发动机占有率几乎接近100%。
除铸造铝合金以外,变形铝合金主要用于汽车的车身系统、热交换器系统、箱式车厢及其它系统部件等,主要包括板、带、箔、管、各种形状的挤压型材和锻件等。
美国汽车工业用变形铝合金占该国汽车用铝量的1/3左右。
汽车轻量化的需求使得铝合金的发展面临一个更广阔的空间,据专家预测,汽车材料铝化率达到60%以上在经济上是可取的。
据此推测,未来汽车的铝化极限可达30%~50%或以上。
新的汽车铝材开发与应用集中在三个方面,其一,车身、车架全铝化及大型铝合金型材的开发应用。
其二,防冲挡及车门刚性结构的全铝化。
其三,转动部分零部件的全铝化。
国产汽车用材与国外有一定的差距,尤以轿车最为突出。
上世纪90年代初期的产品或技术所用材料构成基本与国外同期同车型一致,但铝材用量低于当前国外各类汽车。
并且受铝价及零部件加工技术水平所限,使一些引进车型原有的铝合金零件改用了其他材料,制约了铝合金材料在国产汽车上的应用。
随着世界汽车轻量化进程的加快,特别是加入WTO后,汽车市场竞争国际化日趋剧烈,国产汽车要达到国外同类车水平,汽车用铝增加是必然趋势。
由此可见,该项目的建设符合国家产业政策,是汽车工业战略发展的需要。
②、项目实施是企业自身发展的需要
随着我国汽车工业的迅猛发展,整车的更新换代速度不断加快,对汽车零部件企业的要求更加严格和迫切,不仅要跟上整车开发的速度,还要求有上乘的产品质量和相当的生产规模。
为此,企业必须具备很强的产品开发能力、快速应变能力、综合配套能力和丰富的项目管理经验。
公司成立以来,得到了当地政府和奇瑞公司的大力支持。
企业根据市场调研,结合国家产业政策,为顺应市场转化的迫切需求,致力于新产品开发,项目实施后,将有机会更多更快地引进国外先进设备和先进技术,从而提高企业核心竞争力,逐步成为品种齐全,专业化发动机缸盖的生产基地,积极开拓外围市场,跻身