石化装置典型的开停工事故汇编.docx
《石化装置典型的开停工事故汇编.docx》由会员分享,可在线阅读,更多相关《石化装置典型的开停工事故汇编.docx(11页珍藏版)》请在冰豆网上搜索。
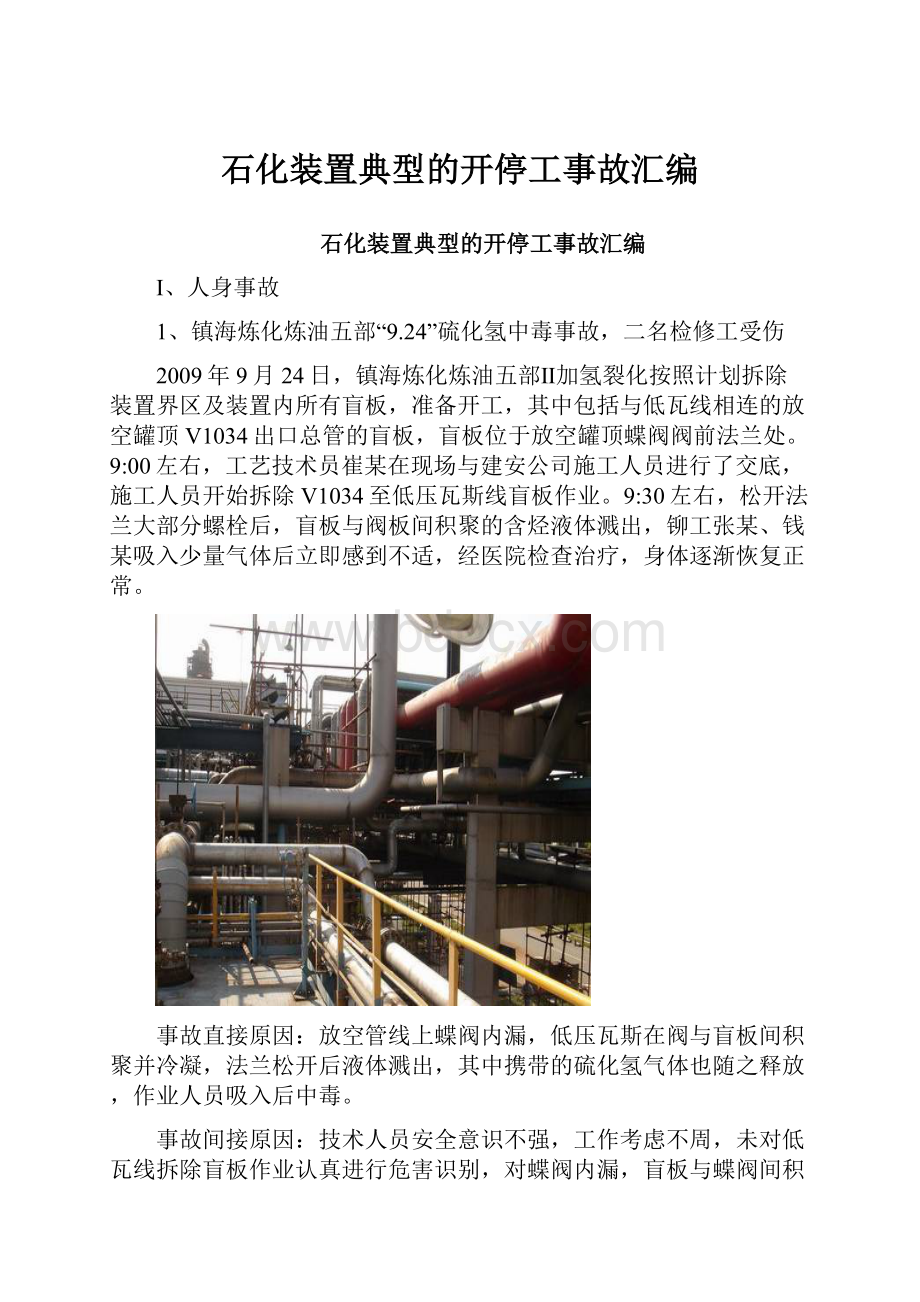
石化装置典型的开停工事故汇编
石化装置典型的开停工事故汇编
Ⅰ、人身事故
1、镇海炼化炼油五部“9.24”硫化氢中毒事故,二名检修工受伤
2009年9月24日,镇海炼化炼油五部Ⅱ加氢裂化按照计划拆除装置界区及装置内所有盲板,准备开工,其中包括与低瓦线相连的放空罐顶V1034出口总管的盲板,盲板位于放空罐顶蝶阀阀前法兰处。
9:
00左右,工艺技术员崔某在现场与建安公司施工人员进行了交底,施工人员开始拆除V1034至低压瓦斯线盲板作业。
9:
30左右,松开法兰大部分螺栓后,盲板与阀板间积聚的含烃液体溅出,铆工张某、钱某吸入少量气体后立即感到不适,经医院检查治疗,身体逐渐恢复正常。
事故直接原因:
放空管线上蝶阀内漏,低压瓦斯在阀与盲板间积聚并冷凝,法兰松开后液体溅出,其中携带的硫化氢气体也随之释放,作业人员吸入后中毒。
事故间接原因:
技术人员安全意识不强,工作考虑不周,未对低瓦线拆除盲板作业认真进行危害识别,对蝶阀内漏,盲板与蝶阀间积聚含烃液体及内含硫化氢估计不足,在安排拆盲板作业时,未要求施工作业人员采取防硫化氢中毒保护措施。
2、中原石化承包商“9.22”窒息事故,昏迷2人
2011年9月22日,中原石化有限责任公司新建MTO装置进入开车阶段。
下午16时30分,车间安排第十建设公司的1名分包商员工进入装置急冷塔C-2101更换垫片,在更换过程中窒息晕倒,监护人随之进入塔内施救也窒息晕倒。
两人随即被塔外人员救出,1人完全恢复,另1人也基本康复。
事故直接原因:
一是急冷塔C-2101与分离工段K-3001系统连接管线没加盲板,而是用两道阀切断隔离。
在进入塔内作业过程中,下游单元分离工段正在对K3001系统进行氮气置换。
在升压过程中,氮气经两道隔离阀反窜到反应再生单元的分离塔,然后进入与之相连的急冷塔。
因塔内氮气逐步积聚,氧气含量逐渐降低,致使两人相继因缺氧而晕倒。
二是在开工物料已经进入装置后,车间管理人员在未办理进入受限空间作业证的情况下,仅凭氧含量分析合格报告单就匆忙安排工人进入受限空间作业。
事故间接原因:
一是系统工艺处置方案不完善,在引入物料进行开工后,工艺管线未有效隔离,进入受限空间安全防护措施不落实。
二是作业人员和监护人安全意识薄弱,在安全措施未落实到位的情况下,违章进入作业和冒险施救,险些造成死亡的事故。
此类事故已发生多次,因救援不当造成事故扩大,伤亡人数增加,务必引起高度重视。
3、天津石化承包商“11.11”氮气窒息事故,死亡2人
2009年11月11日,天津石化炼油部230万吨/年焦化装置正处于装置开工前水联运阶段。
11日上午,车间技术员李某找到施工单位——第四建设公司天津石化项目部,要求安排人员将地下轻污油罐D-116(φ2000mm×7000mm,容积约24m3)内存水抽出。
项目部将此项任务分派给邳州众力建筑公司承担。
上午10时30分左右,邳州众力建筑公司员工张某某(男,44岁)等人来到现场,用绳索将潜水泵放到罐底进行抽水作业。
与此同时,车间正在对吸收稳定、火炬系统及泵区进行氮气气密。
气密过程中发现保压困难,初步判断系统存在漏点。
下午,张某某、闫某某(男,33岁)等4人来到现场继续作业。
13时30分左右,因潜水泵抽不出水,张某某自罐顶人孔沿斜梯进入罐内检查,下到罐底后摔倒在罐底。
闫某某随即进入罐内抢救,也倒在罐底。
现场其他人员迅速呼救。
救援人员赶到现场后将2人救出,经医生检查已死亡。
事故直接原因是氮气窒息。
事故后分析,罐内气体中氧含量仅3.81%(v)。
作业人员没有办理相关作业票,没有采取相应防范措施,贸然进罐导致窒息事故;抢救人员缺乏应急救援知识,盲目施救,导致事故扩大。
初步判定,是正处于气密过程的系统至污油罐管线上的阀门内漏,氮气进入污油罐内,形成窒息性环境。
4、石家庄炼化公司“5.29”人身伤亡事故,2人死亡、1人重伤
2005年5月29日,石炼化公司化纤公司硫酸装置开工,在投用三氧化硫蒸发器和冷却器后,由视镜未观察到三氧化硫进入储罐,系统压力升高,怀疑冷却器至储罐之间的管线堵,操作人员擅自用低压蒸汽对局部堵塞的三氧化硫管线外壁进行加热,三氧化硫急剧汽化,压力急剧上升,造成视镜破裂,三氧化硫喷出,导致2人死亡,1人重伤,2人轻伤。
事故直接原因是怀疑液态三氧化硫结晶、堵塞管线的情况下,擅自用蒸汽加热管线,导致管线内三氧化硫迅速气化、局部憋压,造成视镜超压破裂,三氧化硫大量喷出。
化纤公司有关领导及生产管理人员长期对孟山都公司硫酸生产工艺没有很好地消化吸收,对三氧化硫的物性和特点缺乏足够的认识,以致操作人员违规使用蒸汽胶皮管加热管线而没有得到及时制止,形成习惯性违章,这是造成事故发生的深层原因。
5、聚丙烯“9.5”窒息事故
聚丙烯事业部三聚车间按检修进度要求,8月5日全装置停车检修,8月8日上午9:
00维修中心维修人员将H303A封头拆开,继续通风置换。
8日下午13:
50左右维修中心检修人员彭京川、李广义、李联合到现场后,彭京川开始拆H-303B内部的滤芯支撑板上的螺栓,李广义在旁边。
随后张学兴到现场后取扳手,李联合见张学兴开始拆H-301A内部的滤芯支撑板上的螺栓后,随后去取检修用的工具。
李联合回到现场后,发现张学兴头里脚外休克在H-303A内,立刻叫彭京川一同将张学兴拖出H-301A,彭京川立即就地进行抢救,后送燕化医院进行急救。
事故原因:
1.认识上有误区。
安全管理制度学习不细,没有把H-303过滤器理解成容器。
认识上有误区,没有把H-303的清理工作当作进入受限空间作业,没有办理相关票证,违反相关制度。
2.习惯性操作,麻痹大意。
H-303系统经常发生堵塞,影响粉料的输送。
有时一天清理十几次。
为了不影响生产,检维修人员常常是拆开封头后用仪表风吹扫粉尘,而后拆过滤器更换,均没有发生窒息事故。
由此,以上工作程序成了拆卸H-303的习惯性操作。
这是发生事故的主要原因。
Ⅱ、火灾、爆炸事故
1、镇海炼化炼油三部“5.3”火灾事故,1人严重灼伤
2011年5月3日,裂化系列按停工网络安排开始降温降量,为确保装置冲洗油正常,班组按方案引外来低氮油(柴油组份)到冲洗油罐V320做冲洗油。
14:
07,外主操俞某指挥徒弟打开低氮油至V320的前二道切断阀,徒弟打开第一道阀至50%,在开第二道阀过程中,低氮油从第二道与第三道阀间的放空阀喷出,遇附近3.5MPa高温蒸汽管线着火,造成正在流程的另一端着手打开第三道阀门的班长王某45%浅Ⅱ°~Ⅲ°烧伤。
直接原因:
外主操在负责打通系统低氮油至V320流程的变更作业时,违反操作规程,未对流程上放空阀门的开关情况进行检查确认,就安排徒弟打开低氮油切断阀引油,因阀间放空阀处于开启状态,致使低氮油喷出,遇附近3.5MPa蒸汽“8”字盲板、热电偶及安全阀等高温裸露部位着火。
间接原因:
镇海炼化炼油三部对生产操作及变更作业管理不到位,操作人员对流程相关阀门开关操作行为不规范。
作业前没有进行风险识别并落实相关措施,新员工缺乏操作经验,在发现有低氮油喷出时,应急处置不到位,没有迅速及时关闭切断阀。
2、镇海炼化炼油五部“3.19”火灾事故,蜡油罐前法兰泄漏着火
2007年3月19日,Ⅱ加氢裂化装置处于开工状态,13:
50引低氮油,16:
20部分低氮油从尾油918#线外甩罐区,16:
44蜡油罐G931阀组918#线的阀前法兰泄漏着火。
Ⅱ催化外操发现蜡油罐区冒大量黑烟后报火警,经消防人员扑救,16:
55火势减小,查明是尾油918#线阀前法兰泄漏着火后,炼油五部切断尾油出装置流程、储运部关G931罐根阀,16:
56火被扑灭。
事故原因:
炼油五部在未与储运部相关岗位联系的情况下,直接操作将部分低氮油从尾油918#线外甩罐区,发现外排量不畅时,误认为泵入口过滤器有杂物堵塞,继续开泵退油,最终造成尾油918#线罐区阀组阀前法兰泄漏,低氮油遇伴热线着火。
3、镇海炼化炼油四部“3.28”爆炸事故,1人受伤
2003年3月28日8:
44,炼油四部3#CO锅炉开工点火过程中,操作人员未按规定对流程进行三级确认,没有检查发现液态烃进炉前的两个截止阀均未处于全关状态,致使液化气在总阀打开后就提前进入炉膛,并达到爆炸范围,遇点火时的明火引发炉膛爆炸。
事故造成锅炉部分损坏,震落的钢梁砸伤炉旁外副操甘某左腿,致使其胫骨骨折。
事故原因:
操作人员违反安全操作规程,在开工点火前没有对液态烃流程进行三级确认,未发现入炉前两个液态烃截止阀处于开启状态。
4、广州石化“5.10”闪爆事故,死亡1人,重伤3人
2011年5月3日,广州分公司1#催化裂化装置大修改造结束,转入开工阶段。
5月9日16时48分,反应提升管喷油。
17时30分,装置开始产出粗汽油。
因吸收稳定系统正在调整,粗汽油自分馏塔顶回流罐(V301)经不合格线进污油罐G307。
18时50分,改进污油罐G304,随后发现机械呼吸阀声响很大,罐顶多处撕裂、罐底翘起。
20时30分,粗汽油开始进中间原料罐G203。
5月10日13时10分,储运部罐区操作人员发现罐G203(5000立方米,内浮顶罐)附近可燃气体报警器报警,同时液位显示在6.9~7.1米之间波动,在操作室西侧二层平台看到罐G203透气窗冒出大量油气。
正在准备向调度汇报时现场发生闪爆,罐G203顶部通气管、罐壁透气窗处起火。
操作人员迅速开启罐组消防喷淋并报火警,经消防队奋力扑救,13时25分将火扑灭。
事故造成在2#罐区防火堤外下风向路边休息、等待施工的深圳建安公司4名员工,以及路过的华穗工程公司(改制单位)3名员工不同程度烧伤。
其中深圳建安公司1名员工经抢救无效于5月11日死亡,2人重伤,1人轻伤。
华穗工程公司1人重伤,2人轻伤。
这是一起典型的违章指挥、违章操作造成的责任事故。
事故暴露出在装置改造设计、施工、开车、生产运行和现场安全管理等方面存在漏洞。
事故的直接原因是催化裂化装置开工过程中,由于系统脱水不及时,分馏塔一中回流在长达18个小时里一直建立不起来,吸收稳定系统因缺乏热源而无法正常运行,粗汽油中的液态烃组分无法分离。
为避免放火炬,富气压缩机维持运行,期间产生的轻烃被间歇压送至粗汽油罐。
由于持续时间长,粗汽油中含有的液态烃等轻组分从G203罐顶通气管、罐壁透气窗溢出并扩散,遇位于下风向防火堤外施工板房内的非防爆电器而引发闪燃。
事故间接原因:
一是仓促开车,准备不足,开车方案、应急预案不完善。
广州分公司1#催化裂化按计划检修2个月,进行多产丙烯的MIP-CGP改造,包括增设外取热器、吸收稳定系统四塔更换等工作。
检修过程中主要设备不能如期到货、水压试验不合格,现场临时设计修改多,同时施工质量不高,特别是分馏系统漏点较多,至5月4日装置开主风机时仍有动火项目,最终装置检修时间达到78天。
装置边施工边开工,为事故发生埋下了隐患。
二是设计存在缺陷。
粗汽油至吸收塔管线与不合格粗汽油外送管线间缺少隔断阀(改造前粗汽油至吸收塔管线设置有塔壁阀门,本次改造时取消,但没有设计替代措施),存在吸收塔内气体倒串至粗汽油不合格线的隐患。
三是操作人员操作不当。
变更设计后对流程检查不到位。
当粗汽油调节阀失灵、改副线阀控制时,没有意识到吸收塔气体会倒串,导致吸收塔气体倒串至污油罐G304,造成罐顶部多处撕裂、底部翘起。
四是没有认真吸取教训。
污油罐G304损坏后,相关部门、单位没有引起足够重视,没有深入查找事故原因并采取相应防范措施,进而发生了更大事故。
五是现场管理存在漏洞。
在装置已经开车、储罐正在进油,特别是粗汽油中含有大量液态烃等轻组分情况下,没有及时停止现场施工,没有采取区域警戒、隔离等防护措施,仍然安排在临近罐区进行施工,导致多人受到意外伤害。
5、荆门分公司“3.26”闪爆事故。
荆门分公司柴油加氢精制装置2008年2月25日-3月12日进行检修,开工后,发现反应器上床层压降增大,决定进行催化剂撇头,3月26日打开反应器大盖,在车间人员进入反应器准备取出积垢栏时,反应器发生闪爆,造成3人轻伤。
事故直接原因是由于施工安全措施不到位,反应器置换不彻底,少量油气和焦粉尘形成了爆炸性混合物,因静电引起闪爆。
本次事故也反映出,装置停工检修时,工艺吹扫方案存在缺陷。
由于没有安排对反应器前的设备管线、加热炉炉管进行吹扫,造成开工后铁锈、焦粉等杂物被吹入反应器,导致反应器压降升高。
6、资产公司洛阳分公司“10.14”火灾事故,2人死亡
2008年10月14日,资产公司洛阳分公司下属集体企业——宏达实业总公司宏力化工厂动力车间循环水场发生火灾事故,造成2人死亡,2人重伤,3人轻伤。
2008年8月13日,宏力化工厂聚丙烯装置(含气分单元)停工保压。
停工后关闭了脱丙烷塔冷凝器E105A/B、精丙烯塔冷凝器E111A/B/C/D、丙烷冷却器E110的循环水出口调节阀。
9月25日,因动力车间发现循环水浊度增大,要求各装置查找泄漏情况。
聚丙烯车间检查确认精丙烯塔塔顶冷凝器E-111A/B/C/D内漏(从回水线排出气体),随即关闭了E-111A/B/C/D的物料及循环水进出口阀门。
10月14日,按照宏力化工厂调度安排,聚丙烯装置对E-111进行退料、排放、泄压处理。
10时30分,打开E-111A/B/C/D停车排空线,通过泵回收E-111A/B/C/D内液相料。
11时开始回收E-111A/B/C/D内的气相料,通过P104b回收线串到低压管线,进入火炬系统。
17时左右,聚丙烯装置操作人员在处理过程中,打开了E-111A/B/C/D循环水的回水手动阀和调节阀,导致积聚在E-111A/B/C/D管程和回水管中的丙烯液化气物料大量串入循环水中,在循环水场凉水塔泄放出来,并随风沿地面向西、向北方向扩散。
17时7分左右,泄漏出的丙烯扩散到循环水场北侧约50米的新建气柜处,被气焊火焰点燃,并迅速回燃到凉水塔,引起凉水塔填料起火,造成7名现场作业人员不同程度烧伤。
其中2人死亡,2人重伤,3人轻伤。
事故直接原因是违章操作。
在已知换热器内漏的情况下,未做任何处理,违章打开循环水回水线阀门,导致液化气沿循环水线串入循环水场,导致事故发生。
事故暴露出公司安全管理存在漏洞。
首先是装置的开停车管理有漏洞。
8月13日装置停工时没有制定停工处置方案。
对带压带料停工装置的风险认识不足,没有针对装置带料、带压的现状制定相应的停工维护方案。
对装置工艺参数变化、异常情况所采取的措施没有做出明确规定。
其次是设备管理存在漏洞。
车间在得知E111内漏时,没有引起高度重视,没有制定泄漏处置方案,只是采取了暂时性的隔离措施,设备在较长时间内得不到彻底处理,造成内漏加剧,物料积聚,为事故发生埋下了隐患。
7、塔河分公司“11.1”火灾事故。
2004年10月31日,塔河分公司常压焦化联合装置正在进行开工试车。
31日24时,焦炭塔进行切换,将焦化进料切至B塔。
1日12点40分左右,除焦班操作人员将焦炭塔A底盖的短节拆开后,开始有油从法兰缝隙流出,沿着溜槽流入贮焦池,且油量逐渐增大,直至喷到运行的B塔裸露入口高温短节上,自燃起火,并将贮焦池水面浮油引燃。
装置紧急停工。
14时30分火势得到控制,15时10分彻底扑灭。
事故直接原因是焦炭塔切换操作中,未关严A塔急冷油管线,急冷油继续进入塔内;焦炭塔放水不彻底,导致大量油品残留塔内。
拆卸短节前没有根据焦炭塔底压力表进一步确认水是否放净。
短节拆开后,大量急冷油喷出。
操作工盯表不认真,因急冷油没有切换而造成B塔出口超温近10个小时而没有引起重视,没有检查流程,失去了避免事故的时机;同时在A塔冷焦过程中,急冷油经接触冷却塔后,随冷凝水排入贮焦池,导致火灾扩大。
8、金陵石化公司烷基苯厂“9.17”事故
2003年烷基苯厂一车间安排9月3日起进行为期60天的停工检修,计划在检修中更换烷基化装置脱烷烃精馏塔C-405(高50.95米,直径5.2米)的塔内件和填料。
按照操作规程和开停车方案完成退料,13日至16日进行蒸汽连续吹扫,16日夜间因附近居民反映噪音大,停止吹扫,17日8时至15时恢复吹扫,15时30分至17时打开人孔通风,待塔冷却后交出检修。
当夜22时40分左右,该车间职工曹燕青发现C-405塔体中部发红,随即向车间领导报告,经有关领导和技术人员赶到现场后确认塔内着火,立即报警。
公司消防支队22时51分接警后赶到现场扑救。
在扑救过程中,约23时塔体中部断裂,上部向西南方向折倒在装置区空地上,断裂塔体继续燃烧,9月18日4时40分火被扑灭。
事故未造成人员伤亡,其它设备和管线未受损。
事故原因分析:
1.脱烷烃塔(C-405)自1980年建成投产以来已运行23年。
1993年因扩容改造,将原来的浮阀塔盘改为填料,现塔内装有约360立方米的规整和散装金属填料,按以往常规每年或每二年进行1次检修,本次检修要对塔内件和金属填料进行更换。
按检修方案,需对该塔进行48小时以上的蒸汽吹扫。
经分析,虽经过80小时蒸汽吹扫,但沉积在规整填料段的残留物(硫化物)仍不易被蒸汽吹扫干净,当打开塔的人孔后,硫化物遇空气后自燃,并引燃残留物及填料,因没有及时发现,致使塔体中部局部过热,塔壁温度升高引起碳钢材质的塔壁强度降低,最终导致塔体在20-21米处折倒。
2.工厂技术部门对改造后的填料塔没有认识到进料中微量硫化物(含硫量小于1ppm)能在规整填料表面不断积聚,故也未在该塔的操作规程中制定针对硫化物的处理对策和应急防范措施,犯了经验主义的错误。
3.认识不到位,认为此塔人孔打开后,工艺处理就已结束,没有安排人监控塔内的温度变化,车间在布置晚间值班时,对C-405塔的巡检内容没有专门要求,车间值班人员未按时巡检,致使出现异常时未及时发现。
4.集团公司事故通报学习贯彻不力。
集团公司《关于上海石油化工股份有限公司“1.20”事故的通报》(中国石化安〔2002〕65号)详细叙述了蒸馏塔折倒事故过程和原因,并提出各项安全要求。
烷基苯厂学习贯彻不力,只对前道工序加氢单元塔停工过程增加水洗等处理措施,没有对烷基化系统塔器增加相应处理程序,导致类似事故重复发生。
9、化工三厂“4.7”着火事故
1976年4月7日13:
30分,化工三厂烷基苯车间缩合岗位在撤料过程中突然发生物料着火。
起火迅速;火势蔓延较快2-3分钟之内火焰便充满一楼一泵房岗位的东侧,5-6分钟后火焰高达10米以上,烧毁一至三楼的门窗和一泵房全部机泵仪表、电器等设备,直至14时30分将火熄灭。
事故原因:
由于烯烃和苯在催化剂Acce3作用下,经反应使仍然有没反应的Acce3遇少量水产生大量热量引起可燃物燃烧。