钢在轧制中常见的缺陷总结.docx
《钢在轧制中常见的缺陷总结.docx》由会员分享,可在线阅读,更多相关《钢在轧制中常见的缺陷总结.docx(32页珍藏版)》请在冰豆网上搜索。
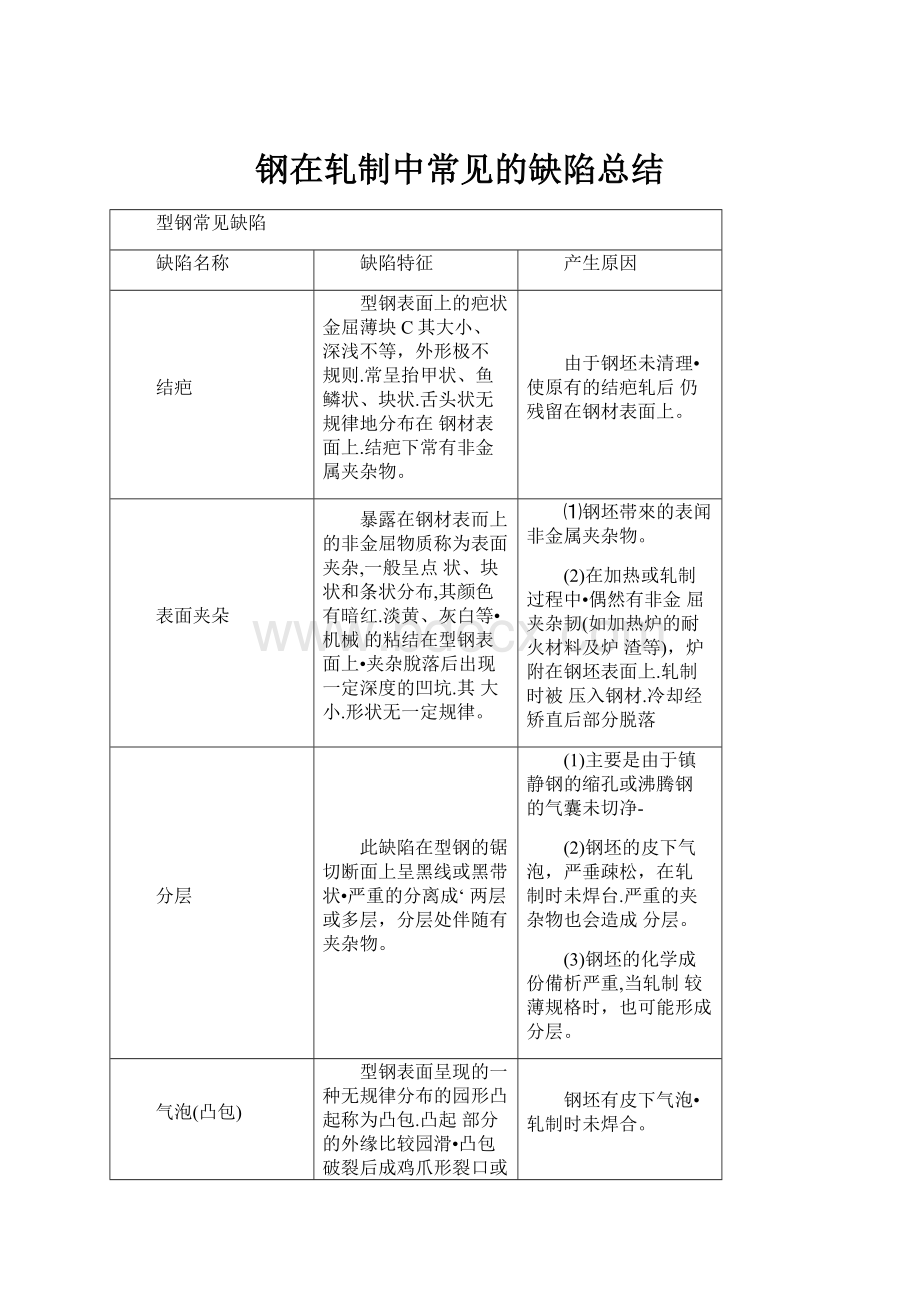
钢在轧制中常见的缺陷总结
型钢常见缺陷
缺陷名称
缺陷特征
产生原因
结疤
型钢表面上的疤状金屈薄块C其大小、深浅不等,外形极不规则.常呈抬甲状、鱼鳞状、块状.舌头状无规律地分布在钢材表面上.结疤下常有非金属夹杂物。
由于钢坯未清理•使原有的结疤轧后仍残留在钢材表面上。
表面夹朵
暴露在钢材表而上的非金屈物质称为表面夹杂,一般呈点状、块状和条状分布,其颜色有暗红.淡黄、灰白等•机械的粘结在型钢表面上•夹杂脫落后出现一定深度的凹坑.其大小.形状无一定规律。
⑴钢坯帯來的表闻非金属夹杂物。
(2)在加热或轧制过程中•偶然有非金屈夹杂韧(如加热炉的耐火材料及炉渣等),炉附在钢坯表面上.轧制时被压入钢材.冷却经矫直后部分脱落
分层
此缺陷在型钢的锯切断面上呈黑线或黑带状•严重的分离成‘两层或多层,分层处伴随有夹杂物。
(1)主要是由于镇静钢的缩孔或沸腾钢的气囊未切净-
(2)钢坯的皮下气泡,严垂疎松,在轧制时未焊台.严重的夹杂物也会造成分层。
(3)钢坯的化学成份備析严重,当轧制较薄规格时,也可能形成分层。
气泡(凸包)
型钢表面呈现的一种无规律分布的园形凸起称为凸包.凸起部分的外缘比较园滑•凸包破裂后成鸡爪形裂口或舌形结疤•叫气泡。
多产生于型钢的角部及腿尖。
钢坯有皮下气泡•轧制时未焊合。
裂纹
顺轧制方向出现在型钢表面上的线形开裂,一般呈宜线形•有时呈形.多为通长出现•有时局部出现。
(1)钢坯有裂缝或皮下气泡.非金属夹杂物.经轧制破裂暴露。
(2)加热温度不均匀.温度过低,轧件在轧制时各部延伸与宽展不一致。
⑶加热速度过快.炉尾温度过岛或轧制后冷却不当,易形成裂纹,此种情况弱发生在岛碳钢和低合金钢上。
尺寸超差(尺
寸不合、规格
不合)
尺寸超差是指型钢截面几何尺寸不符标准规定婆求的统称。
这类缺陷名目紧女.大部以产生部位以及其超差程度加以命名。
例匸、槽、角钢的腿长、腿短、腰厚、樱簿及一腿长•一腿短。
(1)对1:
字钢成品孔腿长往往表现在开口腿上•主要由于腰部压下量不够,角钢和槽钢成品孔压下fit的大小,直接影响腿长和腿短。
(2)切深孔切人太深•造成腿长无法消除。
⑶轧規不水平或有轴向串动■以及8OO咬入不正•成品孔夹板上偏等都会造成一腿长•一腿短等。
(4)腰的厚.薄主要是成品孔及成品前;孔压下址不合理所造成。
划伤(刮伤、
擦伤、划痕)
一般呈直线或弧形的沟槽.其深度不等.通长可见沟底,长度自几亳米到几米.连续或断续地分布于钢材的局部或全长.多为单•条,有时出现多条。
(1)导卫板安装不当•对轧件压力过大,将轧件表面划伤。
(2)导卫板加工不良•口边不圆滑.或磨损严重,粘有氧化铁皮,将轧件表面划伤。
(3)孔型侧壁磨损严重,当轧件接触H产生弧形划伤。
(4)钢材在运输过程中与表而粗糙的辗道、盖板.移钢机.活动挡板等接触划伤。
缺肉
型钢其一侧面沿轧制方向全长或周期性的缺少金屈称缺肉.缺陷处没有成品孔轧槽的热轧印迩色暗、表而枚粗糙。
⑴孔型设计不良,轧規午削不正确及轧机调整不、S使轧件进入成品孔时由于金屈虽不足.造成孔型充填不
⅜4<∙
(2)轧椚错牙或入口导板安装不、*造成轧件某一面缺少金属.再轧时孔型充填不满。
(3)前.后孔磨损程度不一样。
(4)园轧件弯.扭造成进孔不正。
(5)对于工、槽钢,困钢坯不淸理・往往出现结疤掉到闭口腿内,在轧制过程中便会出现周期性的腿尖缺肉。
i∖f
在空钢表而上与}L型开口处相对应的地方,出现顺轧制方向延伸的凸起部分称为耳子。
有贰边的,也有双边的,有时耳子产生在型钢的全长•也有局部或断续的•方、圆钢产生较多。
⑴轧机调整不当或孔型磨损严重,阔
成品前孔來料过大或成品孔压下虽过大,产生过充满,多产生双边耳子。
(2)进入成品孔前[対事故适成温度过低•进入成品孔时延伸降低•宽展过大•多产生双边耳子。
(3)成品孔入口夹板向孔型-•侧安偏或松动。
金屈挤人孔型一侧規缝里,产生单面耳子。
(4)成品入口夹板间隙过大或松动,进钢不稳•易产生双面断续耳子。
扭转
型钢绕其轴线扭成螺旋状称为扭转
⑴卫板安装不良,使轧件出孔时受到力偶的作用产生扭转。
(2)两侧延伸不一致,主要是压下不均或規子有轴向串动。
(3)方、园钢由干入口夹板安装不正确,使钢料进孔不正•造成延伸不一致。
(4)轧規安装不正确■上、下轧規轴线不在同一垂直平面内,即上.下規成水平投影交叉,使轧件扭转。
(5)矫直机调整不当。
弯曲(弯头)
型钢沿垂直或水平方向呈现不平直的现象称为弯曲,一般为镰刀形或波浪形•仅只头部的弯曲叫弯头。
(1)轧机调整不当,轧規倾斜或跳动,上.下規径差大.造成速度差大。
(2)出口卫板安装不正确,卫板梁过低或过高。
(3)轧件温度不均匀■使金属延伸不H致。
(4)冷床拉钢小午不同步或滑轨不光滑。
(5)运输辗道速度过快•容易把钢材头部撞弯。
(6)矫直温度过高,冷却后容易产生弯;曲。
(7)成品捆扎长短不齐较大。
在运输中装卸不当。
⑻堆垛时不按规定进行。
(9)锯片用的太老,也容易产生弯头。
形状不正
型钢断面几何形状歪斜不正,这类缺陷对不同品种⅛⅛>名称繁藝。
如匸槽钢的内并外斜,弯腰挠度,角钢顶角大、小腿不平等。
(1)矫直轮孔型设讣不合理。
(2)矫直机调整操作不当Q
(3)矫直總磨损严重。
(4)轧馄磨损或成品孔出口卫板安装不良。
重轨常见缺陷
缺陷名称
缺陷特征
产生原因
结疤
在钢轨的头、腰底部等处局部粘附的金属蒲片状疤皮为重轨结疤.外形轮廓不规则,有闭合和不闭合的•有生根和不生根的.结疤下ihi常有肉眼可见的非金属夹杂物。
由于钢坯未清理,钢坯原有的结疤经热轧变形后残留在钢勒表面上。
裂纹
在钢轨表面上呈现的与轧制方向一致的直线形缝隙叫“裂纹",长短不一,多出现在轨头。
裂纹通常较深,缝底尖细.有氧化诜皮和非金属夹杂物
(1)钢坯原有的裂纹经热轧变形后,演变在钢轨表面上。
(2)加热工艺不台理,即温度过高或加热速度过快,造成热应力.形成裂纹。
(3)轧制过程中冷却不当,即因爭故浇水时间过长或孔型冷却
水开得太大•低温轧制易形成裂纹。
表而夹杂
暴露在钢轨表面上的非金屈物质称为表而夹朵。
一般呈点状、块:
状和条状,其大小、深浅无规律,颜色有暗红.淡黄、灰白等。
钢坯有夹杂。
分层
轨腰断而中心线附近显露的金属分离层叫分层。
常呈现黑线或黑带,内有大虽非金屈夹杂物。
(1)主要因钢坯缩孔部分未切净。
(2)钢坯中心聚集大虽的非金屈夹杂物•在轧制中不能使金属焊合。
开裂
钢坯在轧制中■自动裂开称开裂。
匸业轨尤为多见。
(1)由于钢锭中心部位集中大fit气体和非囊属夹杂物所致。
(2)由于钢“内裂"或〃穿孔"所致。
过烧
因钢坯加热不当,钢轨表面出现的横向粗糙裂口叫竹过烧”•裂口多出现在轨头和轨底侧边,金相观察裂口处金屈晶粒粗大。
(1)主要是由于加热温度过高或在高温区停留时间太长。
钢轨上某部分相对另一部分,沿长度方向绕其轴线旋转定角度称扭转.严重时彖麻花.扭转分全长和局部扭转两种。
(1)卫板安装不良,使钢轨产生力偶,形成扭转。
(2)轧件温度不均或压下虽不均.造成各部延伸不一致。
(3)娇直机调整不当,钢轨受力偶作用。
(4)在冷却台架上翻钢时因温度较高也会出现扭转。
弯曲
钢轨沿垂直或水平方向呈现不平直的现直叫弯曲,一般呈镰刀形或波浪形,仅在端部的弯曲又叫弯头。
(1)由于重轨的头、腰、底面积相差较大,使轧制、冷却等工序操作易产生弯曲。
(2)娇直机操作调整不良或娇直温度过高。
(3)成品孔出口卫板过低,锯齿
磨损太老,垫板太低,在轮道运送速度过快时,碰迪档扳等都容易产生弯头。
尺寸超差(规格
不合)
钢轨断面几何尺寸不符合标准规定,统称尺寸超差。
其中:
钢轨头部超过正偏差的叫头大,超过负偏差的叫头小。
腰厚度超过正偏差的叫腰厚.超过负偏差的叫腰薄C轨底宽度超
(1)头太、头小产生的主要原因是轧制溫度和轴瓦的磨损及轧机部件的松动等造成。
娇裂(矫断、压
断)
2)腰厚、腰薄产生的主要原因是:
如按孔型设计头部压下量为77-=6.7mm:
腹部斥下量为16—=1.5mm,如果六孔压下虽:
加大l.5mm,则头部尺寸为75.5mm压下虽由6.7mm减少到5.2mm.腰部压下虽由l∙5mm减少到6自然头部对腰部有拉伸加之腰部无斥下而宽展•所以腰变薄.反之腰部变厚。
(3)底大主要是由成品孔腰卑,上腿长引起及六孔开口腿磨损严重等。
(4)底小主要是帽形孔未能将腿部宽展到足够的长度•或由腰簿引起。
(5)轨高、轨低主要是由于轧件的温度商.低,成品前孔轨头部分或成品孔轨头部分磨损情况引起。
(6)腹高、腹低主要是导卫板安装不良•孔型严重磨损造成C
(1)W^式或立式娇直机调整操作不当•将钢轨矫断。
(2)钢质不好•如局部夹杂、偏析,在矫直过程中被矫(压)裂
(断)。
钢轨在冷状态娇直、圧直过程中,产生的直线形或折线形的裂纹。
其裂口棱角尖锐,呈银亮色,严重时劈裂成碎断。
线材常见缺陷
缺陷名称
缺陷特征
产生原因
耳子
盘条表而沿轧制方向的条状凸起称为耳子,有取边耳子,也有双边耳子。
在商速线材轧机(连轧)生产中•最终产品头尾两端很难避免耳子的产生。
1)轧槽导卫安装不正及放偏过钢,使轧件产生耳子。
(2)轧制温度的波动或局部不均匀.彩响轧件的宽展虽,产生耳子。
(3)坯料的缺陷.如缩孔、偏析.分层厦外來夹朵物•影响轧件的正常变形,形成耳子。
折叠
盘条表面沿轧制方向平直或弯曲的细线.在横断面上与表倆呈小角度
(1)前道次的耳子及其他纵向凸
交角状的缺陷多为折叠。
折叠两侧伴有脱碳层或部分脱礦层•折缝中间常存在氧化铁夹杂。
起物折倒轧入木体所造成。
再轧形成折迭。
(2)导卫板安装不当,有棱角或粘有饮皮使轧件产生划痕,再轧形成折迭。
裂纹
盘条表而沿轧制方向有平直或弯曲.折曲的细线•这种缺陷*为裂纹。
由于钢坯上的缺陷经轧制后形成的裂纹常判有氧化圆点、脱碳现象.裂纹中间常存在氢化亚铁。
由于轧后控冷不、形成的裂纹无脱碳现彖伴生•裂缝中一般无氧化亚铁。
(1)钢坯上未消除的裂纹(无论纵向或横向)•皮下气泡及非金屈夹杂物都会在盘条上造成裂纹缺陷。
(2)钢坯上的针孔直口不清除,经轧制被延伸、氧化.熔接就会造成成品的线状发纹。
针孔是铸坯常见的重婆缺陷之一,不显爲时很难检査出來•应特别予以汪
(3)高碳钢盘条或合金舍址高的钢坯加热工艺不当(预热速度过快•加热温度过高等),以及盘条孔成后冷却速度过快,也可能造成成品裂纹•后者还可能出现横向裂纹。
凸起及压痕
盘条表而呈现一些连续性.周期性的凸起或凹下的印痕(某些印痕无规律性),缺陷形状、大小相似。
凸起.压痕主翌是孔槽损坏或磨损造成的。
缩孔
盘条彼而中心部位的疏松或空洞称为缩孔•缩孔处存在非金属夹杂.同时某些非铁元素富集。
连铸方坯按“小钢锭理论"有时出现周期性的缩孔,轧后不能焊台。
截面夹杂
暴露在钢材碰面上的非金属物质称为截面夹杂。
这样的缺陷般是铸钢时外來的非金属物质进入钢液•粘附铸坯某个部位造成的。
中厚板常见缺陷
缺陷名称
缺陷特征
产生原因
裂缝(裂纹)
钢板表面呈现的形状不同,深浅不等,方向任意的裂口称为裂缝(裂纹)。
板坯上的纵裂缝活理不净或漏清理•经轧制残留在钢板上。
I入氧化
恢皮
钢板表面压入的氧化铁皮.呈灰照色或红棕色•分布血积有大有小,有呈块状.也有呈条状或点状
(1)压八氧化铁皮的生成取决于加热条件,加热时间愈长,加热温度愈商,氧化性气氛愈强•生成
的.其压入深度有深有浅。
氧化铁皮就愈多,而且不容易脫落C
(2)r⅛压水斥力不足.商压水嘴堵塞、立辗侧压小.轧制爆破去鳞不尽。
(3)含合金元素Ni含量较高。
厚薄不均
钢板呂部分厚度不致称厚薄不均•凡厚度不均的钢板•般同板差过大.局部钢板厚度超过规定的允许偏差。
(1)⅛缝的调整和轮型的配宜不当。
(2)轧規和轧轮两侧轴瓦磨损不一样。
(3)板坯加热温度不均。
折迭
钢板表Ifii有局部互相折合的双层金屈称折迭。
其外形与裂纹相似,深浅不一,在横截曲上一般呈现锐角,多在钢板的边部或角部出现。
⑴轧件刮你轧制时产生折迭.炙出现在钢板的下表面C
(2)立眾挤压过大,眾环啃伤轧件下表面。
⑶加热炉滑道磨损,推钢时使板坯下表血产生划伤。
(4)钢坯表面存在凸台•横轧时产生压折。
麻点
钢板表而呈现局部或连续的凹坑叫麻点.其大小不同,深度不等。
加热过程中.板坯氧化严重•轧制时铁皮压人表面,脱落后形成细小的口坑。
瓢曲
钢板在纵横方向同时出现同一方向的翘曲,严重者呈船形。
(1)钢板两而冷却条件不一致,上下表而温差大。
(2)钢板在中压水区域停留时间过长。
镰刀弯
钢板两纵边向同一侧弯曲,形似镰刀•称讎刀弯。
(1)轧轮车削不正确或規缝调整不平行。
(2)轧件两边溫度不均,钢板延伸不一致。
(3)用圆盘明珂边时.两剪刃重合址不一致。
切斜
钢板未切成直角.而切成平行四边形、梯形.无规则的四边形等•称切斜。
剪切机调整不、S钢板剪切时未摆正缱齐或操作人员误操作等•都会造成钢板切斜C
热轧板(卷)常见缺陷
缺陷名称
缺陷持征
产生原因
規印
是一组具有周期性,大小形状基木一致的凸口缺陷,并且外观形状不规则。
一方而由于眾子疲劳或换度不够,使規面一部分掉肉变凹•另一方面可能是轨子表而粘有片物,使表面部分呈凸出状轧钢或精整加工时压人钢板表面形成凸凹缺陷。
表面
夹朵
在钢板表面破皮处•有不规则的点状、块状或长条状的非金属夹杂物•其颜色般呈棕红色.黄褐色.灰白色或灰黑色。
(1)板坯皮下夹杂轧后暴露,或板坯原有的表啲夹杂轧后残留在钢板表ifri上。
(2)加热炉耐火材料及泥沙等非金屈物落在板坯表Ilii
上,轧制时压入板而。
I
氧化
铁皮
氧化铁皮一般粘附在钢板表面,分布于板而的局部和全部「铁皮有的疏松易脱落.有的斥入板面不易脫落。
根据其外观形状不同有:
红铁皮、线状铁皮、木纹状诜皮、流星状诜皮、纺镭状诙皮.拖曳状诜皮和散沙状诜皮等。
(1)板坯加热制度不合理或加热操作不良时产生一次铁皮难以除尽,轧制时被压人到钢板表面上。
(2)大立轮设定不合理,铁皮未挤松,难以除掉。
(3)由于商圧除鳞水管的水圧低.水咀堵塞.水咀角度不对及使用不为等原园•使钢板上的铁皮没有除尽,轧制后被压A引钢板表面上。
(4)氧化铁皮在沸腾钢中发生较多•在含硅较禹的钢中易产生红铁皮。
气泡
钢板表面有无规律分布的园形凸包•有时呈蚯蚓式的直线状,其外缘比较光滑,内有气体。
'勺气泡轧破后,呈现不规则的细裂纹。
某些气泡不凸起.经平整后,表面光亮,剪切断而呈分层状。
(1)园板坯上存在较女的气泡气囊类缺陷.经多道轧制没有焊合.残留在钢板上。
(2)板坯在炉时间长,气泡暴露。
折迭
(折印、
折皱、
折边、
折角)
钢板局部性的折合称折迭。
沿轧制方向的直线状折迭称顺折垂直于轧制方向的折选称横折,边部折迭称折边。
折造与折印、折皱的区别主要在于缺陷的形状,程度不同而界,折边与折角根据角度大小不同相区别。
横向折选女发生在簿规格的带钢中。
含碳量小于的软钢种•因开平机没有安装张力轮易产生折皱。
⑴扳坯缺陷淸理的深宽比过大。
(2)板坯温度不均匀或精轧轧規辗空配宜不合理及轧制负荷分配不合理等,轧制中的帯钢园不均匀变形成大波浪后被压合。
⑶立银轮环的挤压或轧件有严重刮伤以及由干粗轧來料有较大的镰W弯,对中不良等原因,刮框后再次被轧制压合。
(4)卷取机前的側导板严重磨损出现洶搐开口度过小,夹送總缝呈楔形,易使帶钢跑備•在恻导板沟槽处的部位被夹送轮压。
(5)1大I故没及时卷取,使卷取温度过低或卷取速度设定不台适。
(6)钢卷卷边错动•或因钢卷松动•在用吊千上吊,下降落地时易产生折边(折角),此时,常发生在厚度较薄的钢卷上。
(7)带钢开卷溫度过高,或开卷时的张力及压紧银的压力设定不台适。
塔形
(卷
边钳
动)
钢卷上下端下齐,一圈比一圈高称塔形。
卷边上下错动称卷边错动。
(1)助卷轮间隙涮整不当。
(2)夹送總規缝呈楔形。
(3)帶钢进卷取机时对中不良。
(4)卷取张力设定不舍适。
(5)成形导板的间隙调整不当。
(6)卷取机前的侧导板动作时间不同步。
(7)卷筒与推卷器之间有间隙。
(8)卷筒传动端磨损严重。
回转时有较大的离心差。
(9)带钢有较大的镰月弯或板形不好。
松卷
钢卷未卷紧.层与层之间有间隙称松卷。
(1)卷取张力设定不合适。
(2)帶钢有严重浪形或因卷取故障.带钢在银道上有变形。
(3)钢材屈服强度而卷取温度又过低。
(4)卷取完毕后•园故卷筒打反转。
(5)捆带未打紧.或捆带断。
扁卷
钢卷端呈椭圆形称朋卷。
容易发生在较软的和较薄的钢卷中。
(1)钢卷在吊运过程中.承受了大:
十击。
(2)钢卷卷得太紧•温度较高,平放在地面上或上面又堆放钢卷。
镰刀弯
沿钢带长度方面的水平面上向一边弯曲。
(1)板坯有镰刀弯或严重的厚度不均。
(2)粗轧.精轧規磨损不均,規缝出现楔形。
(3)轧件两側温度不均或加热温度不均。
(4)轧机调整不良,两边斥下址不一致。
(5)立轨的中心线有偏差。
(6)轧银发生轴向串动或两侧轴承磨损不均。
(7)侧导板开口度过大.轧件跑偏或轧件对中不好。
楔形
钢板一边厚,一边薄在钢板宽度方向的横断Ihi上看,类似楔形。
楔形程度有大有小。
(1)轧轨磨损严重。
(2)辗缝调整不舍适。
⑶轧件跑偏。
(4)轧件温度不均。
凸度
钢板中间厚,两边薄,从钢板宽度方向的横断面来看,类似弧形.弧形程度有大有小。
(1)轧規严重磨损。
(2)轧規的热膨胀的冷却不均。
(3)規型设计不合理。
(4)轧制负荷分配不均,轧轮弹跳变形过大。
(5)弯規装宜不好。
(6)加热温度不均或轧件温度不均。
瓢曲
钢板的纵横部分同时在同一个方向出现的翘曲称瓢曲。
(1)轧件温度不均•轧制过程变形不均。
(2)钢带在轧钢眾道上喷水冷却不均。
⑶终轧压下率过小。
(4)钢帯在精整时•矫直机压下设定下良,开卷温度过高,圧力琨.矫直規磨损严重。
冷轧板(卷)常见缺陷
缺陷名称
缺陷特征
产生原因
表面夹
杂
钢板(带)表面呈现点状,块状或线条状的非金屈夹杂物,沿轧制方向间断
(1)炼钢时造渣不良,钢水粘度大.流动性差,渣子不能上浮,钢中非金属夹杂物多。
或连续分布,其颜色为红棕色.深灰色或白色。
严重时•钢板出现孔洞.破裂、断带。
(2)铸温低,沸腾不良.夹杂物未上浮。
3)连铸时,保护渣带A钢中。
⑷钢水確、钢锭模或注管内的非金屈材料未淸扫干净。
结疤
钢带表面出现不规则的舌状化鱼磷状"或条状翘起的金属起层•有的与钢板木体相连结•有的与钢板木体不相连,前面叫开口结剋后者叫闭口结疤,闭口结疤在轧制时易脱落,使板面成为口坑。
⑴炼钢方面锭模内壁淸理不净,模壁掉肉.上注时,钢腐飞瓶粘于模壁.发生氧化.铸温低,有时中断注流•继续注钢时.形成翻皮下注锭•保护渣加八不当一造成钢液飞溅。
(2)轧钢方面板坯表面残余结疤未淸除V巾,经轧制后留在钢板上。
圧入氧化铁皮
缺陷呈点状.条状或鱼鳞状的黑色斑点.分布面积大小不等•压人的深浅不。
这类铁皮在酸洗工序难以洗尽,当铁皮脱落时形成口坑。
仕)板坯加热温度过商,时间过长炉内呈强氧化气氛,炉生氧化铁皮轧制时压入。
(2)f⅛≡水压力不足,连轧前氧化铁皮未淸除干净。
⑶高压水喷咀堵药局部氧化铁皮未清除。
(4)集鳞管道打开组数不足,除鳞不干净。
欠酸洗
带钢上下表而严重时整个板面呈现条片状.黑灰色条斑,无光泽。
⑴热轧帯钢各部分温度和冷却速度不同•即沿带钢长度方向的头.中、尾以及沿宽度方面的边部和中部的温度和冷却速度不同•使同带钢各部份的诜皮结构和厚度不同.一般说•热轧带钢的头、中部比尾部温度ι⅛30-5OOC,因此头部铁皮较厚•尾部铁皮较薄•闵而,在酸洗速度相同的情况下.易产生局部未洗净。
(2)酸洗1:
艺不适如酸洗的浓度.温度偏低,酸洗速度太快,酸洗时间不足•或亚诜浓度高未及时补充酸液等。
⑶拉伸除鳞机拉伸系数不够,使铁皮未经充分破碎、剥离.影响酸洗效果。
(4)带钢外形差■如镰丿J弯、浪形等•使机械除鳞效果差•易造成局部欠酸洗。
粘结痕
退火钢卷层间相互粘合在一起称Z为粘结.平整后产生点状恻弧折痕是点粘沿轧制方向呈现成排弧状折痕的是条状粘结严重的血粘结.平整开卷被撕裂或出现孔洞成为废卷。
(1)轧钢卷取张力过大或张力波动•板形不好.造成隆起•在层间压力转大部位产生粘结;
(2)带钢表面粗糙度太小;
(3)钢质太软,碳、硅耆址少;
(4)热处理炉温过高或退火冷却速度过快。
(5)钢卷在装炉前碰撞受伤。
氧化色
钢板厦钢带表面被氧化.其颜色由边部的深蓝色逐步过渡到浅蓝色.棕色.淡黄色,统称氧化色。
仕)退火时保护罩密封不严或漏气•导致钢卷氧化。
(2)罩式炉退火匸序,高温出炉(钢卷温度大TllOoC),导致钢卷氧化。
3)保护气体露点过髙或氢含虽过低.加热前予吹洗时间不足,炉内存在残氧,钢卷在氧化性气氛中退火。
乳化液斑
经退火的钢板表血呈现不规则的或纵小岛状的黑色、褐色图形。
⑴在轧机岀口处乳化液未加尽,加热时碳化.形成斑点
(2)末机架岀口吹风机压力小.吹不净
(3)穿带时风机未开•甩尾时风机关闭
(4)装炉后,予吹洗时间不足.加热时乳化液碳化形成斑点。
划伤
钢板表Ifti呈现直而细.深浅不一的沟槽。
平行于轧向,连续或断续,疏密不一.无一定规律,平整前划伤处较平滑.沟槽处颜色为灰黑色,平整后划伤.有毛刺•呈金属亮色。
(1)酸洗.轧钢.平整.牯整各机组与带钢相接触的零件有尖锐棱角或硕!
物.产生相对运动。
(2)∣⅛整线的各种辗(夹送規、压紧筑S导板等)不运转产生划伤。
(3)开卷或卷収时,带钢速度变化或层间相对运动。
折皱
薄钢板表面呈现凹凸不平的皱折.多发生在小于以下的薄板.皱纹边部成一定角度.严重折皱成压褶。
(1)带钢跑偏,一边拉伸.另边产生褶皱。
(2)板形不良.有大边浪或中间浪.帯钢过平整机•娇直机或夹送規时.有浪形处产生褶皱。
(3)矫直机调整不当.变形不均造成。
規印
钢板表啲出现周期性的凹坑或凸包•严重的轮印导致薄带钢轧穿。
(1)带钢焊缝过高或清理不平.连轧时引起粘規。
(2)總子上粘有硕金屈物(焊珠.金屈屑等)或污垢•轧制或平整时•硕物或污物压在带钢表面上•留下压痕。
(3)1:
作牠掉肉。