加氢设备主要损伤形式选材.docx
《加氢设备主要损伤形式选材.docx》由会员分享,可在线阅读,更多相关《加氢设备主要损伤形式选材.docx(25页珍藏版)》请在冰豆网上搜索。
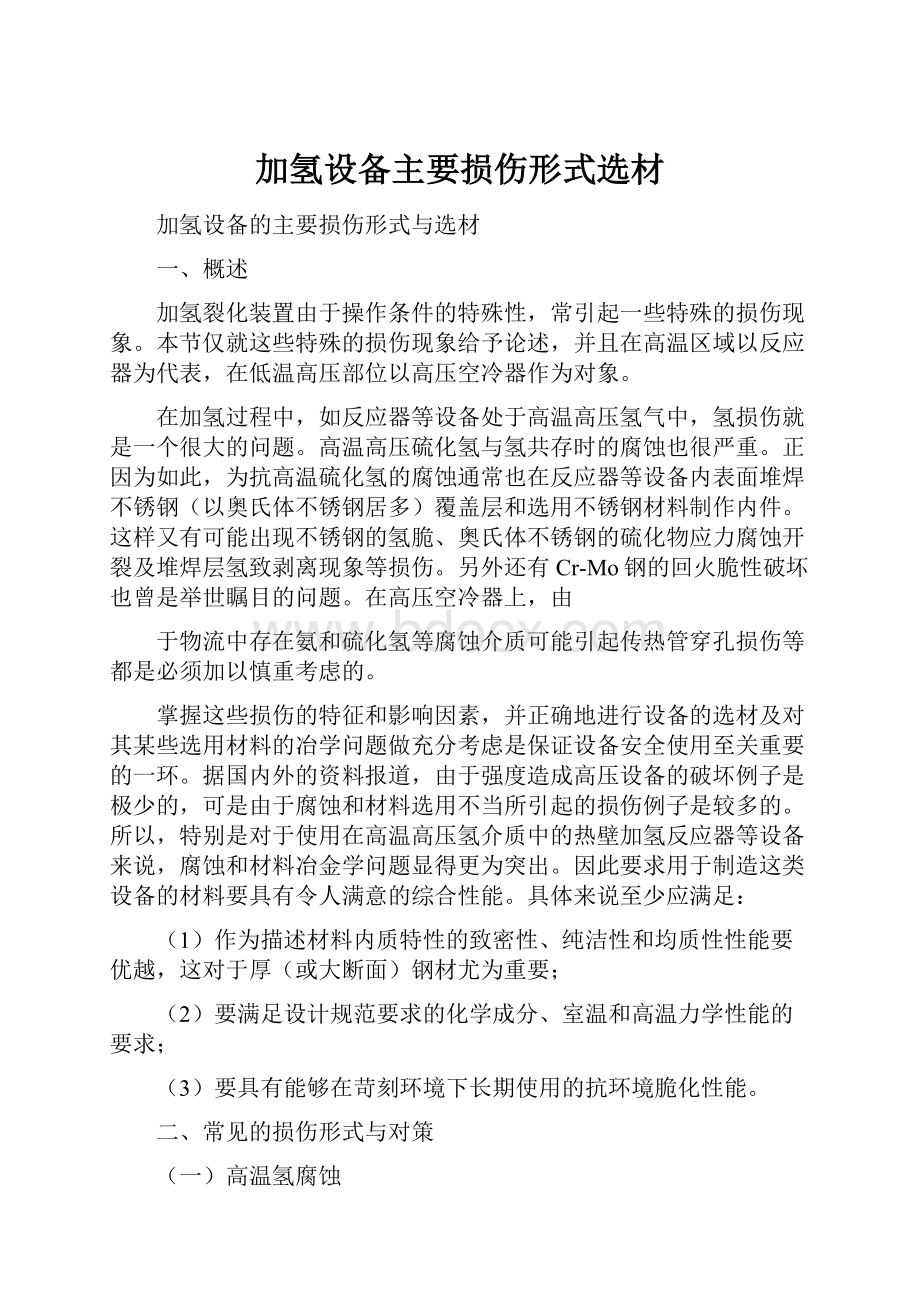
加氢设备主要损伤形式选材
加氢设备的主要损伤形式与选材
一、概述
加氢裂化装置由于操作条件的特殊性,常引起一些特殊的损伤现象。
本节仅就这些特殊的损伤现象给予论述,并且在高温区域以反应器为代表,在低温高压部位以高压空冷器作为对象。
在加氢过程中,如反应器等设备处于高温高压氢气中,氢损伤就是一个很大的问题。
高温高压硫化氢与氢共存时的腐蚀也很严重。
正因为如此,为抗高温硫化氢的腐蚀通常也在反应器等设备内表面堆焊不锈钢(以奥氏体不锈钢居多)覆盖层和选用不锈钢材料制作内件。
这样又有可能出现不锈钢的氢脆、奥氏体不锈钢的硫化物应力腐蚀开裂及堆焊层氢致剥离现象等损伤。
另外还有Cr-Mo钢的回火脆性破坏也曾是举世瞩目的问题。
在高压空冷器上,由
于物流中存在氨和硫化氢等腐蚀介质可能引起传热管穿孔损伤等都是必须加以慎重考虑的。
掌握这些损伤的特征和影响因素,并正确地进行设备的选材及对其某些选用材料的冶学问题做充分考虑是保证设备安全使用至关重要的一环。
据国内外的资料报道,由于强度造成高压设备的破坏例子是极少的,可是由于腐蚀和材料选用不当所引起的损伤例子是较多的。
所以,特别是对于使用在高温高压氢介质中的热壁加氢反应器等设备来说,腐蚀和材料冶金学问题显得更为突出。
因此要求用于制造这类设备的材料要具有令人满意的综合性能。
具体来说至少应满足:
(1)作为描述材料内质特性的致密性、纯洁性和均质性性能要优越,这对于厚(或大断面)钢材尤为重要;
(2)要满足设计规范要求的化学成分、室温和高温力学性能的要求;
(3)要具有能够在苛刻环境下长期使用的抗环境脆化性能。
二、常见的损伤形式与对策
(一)高温氢腐蚀
1、高温氢腐蚀的特征。
高温氢腐蚀是在高温高压条件下扩散侵入钢中的氢与不稳定的碳化物发生化学反应,生成甲烷气泡(它包含甲烷的成核过程和成长),即FeC+2H2→CH4+3Fe并在晶间空穴和非金属夹杂部位聚集,引起钢的强度、延性和韧性下降与劣化,同时发生晶间断裂。
由于这种脆化现象是发生化学反应的结果,所以它具有不可逆的性质,也称永久脆化现象。
在高温高压氢气中操作的设备所发生的高温氢腐蚀有两种形式:
一是表面脱碳;二是内部脱碳。
表面脱碳不产生裂纹,在这点上,与钢材暴露在空气、氧气或二氧化碳等一些气体中所产生的脱碳相似。
表面脱碳的影响一般很轻,其钢材的强度和硬度局部有所下降而延性提高。
内部脱碳是由于氢扩散侵入到钢中发生反应生成了甲烷,而甲烷又不能扩散出钢外,就聚集于晶界空穴和夹杂物附近,形成了很高的局部应力,使钢产生龟裂、裂纹或鼓包,其力学性能发生显著的劣化。
高温高压氢引起钢的损伤要经过一段时间。
在此段时间内,材料的力学性能没有明显的变化;经过此段时间后,钢材强度、延性和韧性都遭到严重的损伤。
在发生高温氢腐蚀之前的此段时间称为“孕育期”(或称潜伏期)。
“孕育期”的概念对于工程上的应用是非常重要的,它可被用来确定设备所采用钢材的大致安全使用时间。
“孕育期”的长短取决于许多因素,包括钢种、冷作程度、杂质元素含量、作用应力、氢压和温度等。
2、影响高温氢腐蚀的主要因素。
1)温度、压力和暴露时间的影响
温度和压力对氢腐蚀的影响很大,温度越高或者压力越大发生高温腐蚀的起始时间就越早。
例如Naumann曾用含碳量为0.11%的碳素钢在29.42MPa氢压下,以各种温度加热100h观察其力学性能的变化。
直到350℃时,还未发现有变化,但一到400℃,力学性能就劣化了,氢的影响显著地表现出来。
另外,在400℃下,改变其压力等级,加热100h,发现随着压力的增大,力学性能就容易劣化,特别是冲击功受到的影响更严重。
当氢压增加到9.81MPa以上时,各种力学性能都下降,明显地受到了氢腐蚀。
2)合金元素和杂质元素的影响
从高温氢腐蚀的机理可知,金属碳化物的分解是很主要的原因。
它对整个氢腐蚀现象的发生起着支配作用。
已有实验证明,在钢中添加不能形成稳定碳化物的元素(如镍、铜等)对改善钢的抗氢腐蚀性能毫无作用;而在钢中凡是添加能形成很稳定碳化物的元素(如铬、钼、钒、钛、钨等),就可使碳的活性降低,从而提高钢材抗高温氢腐蚀的能力。
在合金元素对抗氢腐蚀性能的影响中,实验还证明,元素的复合添加和各自添加的效果不同。
例如铬、钼的复合添加比两个元素单独添加时可使抗氢腐蚀性能进一步提高。
在加氢高压设备中广泛地使用着铬—钼钢系,其原因之一也在于此。
关于杂质元素的影响,在针对21/4Cr-1Mo钢的研究中已发现,锡、锑会增加甲烷气泡的密度,且锡还会使气泡直径增大,从而对钢材的抗氢腐蚀性能产生不利影响。
因为甲烷“气泡”的形成,其关键还不在于“气泡”的生产,而是在于“气泡”的密度、大小和生成速率。
3)热处理的影响
钢的抗氢腐蚀性能,与钢的显微组织也有密切关系。
合金钢经淬火、回火可形成稳定的碳化物,抗氢腐蚀性能就得到改善。
另外,对于在氢环境下使用的铬-钼钢设备,施行了焊后热处理同样具有可提高抗氢腐蚀能力的效果。
曾有实验证明,21/4Cr-1Mo钢焊缝若不进行焊后热处理的话,则发生氢腐蚀的温度将比纳尔逊曲线表示的温度低100℃以上。
4)应力的影响
在高温氢腐蚀中,应力的存在肯定会产生不利的影响。
已有一些实验证明,在高温氢气中蠕变强度会下降。
特别是由于二次应力(如热应力或由冷作加工所引起的应力)的存在会加速高温氢腐蚀。
例如对SAE1020钢给予各种冷变形量并在特定条件下实验时发现:
当没有变形时,钢材具有较长的“孕育期”;随着冷变形量的增大,“孕育期”逐渐缩短,当变形量达39%时,则无论在任何实验温度下都无“孕育期”,只要暴露到此条件的氢气中,裂纹立刻就发生。
3、高温高压氢环境中的材料选用及应注意问题。
多少年来对于操作在高温高压氢环境下的设备材料选用,都是按照原称为“纳尔逊曲线”来选择的。
该曲线最初是在1949年由G.A纳尔逊收集到的使用经验数据绘制而成,并由API(美国石油学会)提出。
1967年前版权属G.A纳尔逊;其后再版权由G.A纳尔逊转让给API并由API于1970年作为API出版物941(第一版)公开发行。
从1949年至今,根据实验室的许多实验数据和实际生产中所发生的一些按当时的纳尔逊曲线认为安全区的材料在氢环境使用后发生氢腐蚀破坏的事例,相继对曲线进行过7次修订,现最新版本为APIRP(推荐准则)941第(5版)“炼油厂和石油化工厂用高温高压临氢作业用钢”。
一直是最有用的抗高温氢腐蚀选材的一个指导性文件。
在应用此图进行选材时,还应该注意以下几点:
(1)本图线仅仅只涉及到材料的高温氢腐蚀,它并不考虑在高温时的其他重要因素引起的损伤,比如系统中还存在着像硫化氢等其他腐蚀介质的情况,可能发生回火脆性等损伤以及可能与高温氢腐蚀发生叠加作用的损伤等。
(2)由于纳尔逊曲线已经过多次修订,使用时务必按照最新版的曲线选用,以保证使用的可靠性。
(3)在实际应用中,对于一台设备来说,焊缝部位的氢腐蚀更不可忽视。
因为通常焊接接头的抗氢腐蚀性能不如母材,特别是在热影响区的粗晶区附近更显薄弱。
(4)在依据图4-30进行选材时,尽量减少不利影响的杂质元素含量,注意控制非金属夹杂物的含量和作用应力水平以及进行充分的回火和焊后热处理等对提高钢材抗高温氢腐蚀都是有好处的。
(二)氢脆
1、氢脆现象的特征。
所谓氢脆,就是由于氢残留在钢中所引起的脆化现象。
产生了氢脆的钢材,其延伸率和断面收缩率显著下降。
这是由于侵入钢中的原子氢,使结晶的原子结合力变弱,或者作为分子状在晶界或夹杂物周边上析出的结果。
但是,在一定条件下,若能使氢较彻底地释放出来,钢材的力学性能仍可得到恢复。
这一特性与前面介绍的氢腐蚀截然不同,所以氢脆是可逆的,也称作一次脆化现象。
氢脆的敏感性一般是随钢材的强度的提高而增加,钢的显微组织对氢脆也有影响。
钢材氢脆化的程度还与钢中的氢含量密切相关。
强度越高,只要吸收少量的氢,就可引起很严重的脆化。
对于操作在高温高压氢环境下的设备,在操作状态下,器壁中会吸收一定量的氢。
在停工的过程中,若冷却速度太快,使吸藏的氢来不及扩散出来,造成过饱和氢残留在器壁内,就可能在温度低于150℃时引起亚临界裂纹扩展,对设备的安全使用带来威胁。
2、加氢设备中的氢脆损伤。
在高温高压临氢设备中,特别是内表面堆焊有奥氏体不锈钢堆焊层的加氢反应器,曾发生过一些氢脆损伤的实例。
其部位多发生在反应器支持圈角焊缝上以及堆焊奥氏体不锈钢的梯形槽法兰密封面的槽底拐角处。
这是在反应器上所发生的典型的氢脆裂纹情况。
这些裂纹经实验分析认为是下列因素作用的结果:
1)此类反应器从正常操作状态下停工时,在器壁的母材(如21/4Cr-1Mo)中一般吸收有2~5ug/g的氢,而在不锈钢堆焊层或焊接金属中吸藏约30~50ug/g的氢而使材料发生氢脆;
2)TP347堆焊或焊接金属中因含有一定量的铁素体,在制造中的最终焊后热处理过程中有一部分δ铁素体转变成脆性的相δ;
3)由于铬-钼钢母材与奥氏体不锈钢堆焊层或焊接金属之间的线膨胀系数差别较大而形成较大的热应力,或这些部位存在一些尖角或过度半径偏小等造成较大的应力集中。
已有许多实验证明,像回火脆化敏感性较强的21/4Cr-1Mo钢,有可能存在着回火脆化和氢脆的叠加效应。
由于回火脆化使夏比断口转变温度VTrs上升,氢致裂纹的晶间断口率也随之增加,氢致裂纹临界应力强度因子Kih相应就下降。
所以此损伤实例就是因为氢致裂纹扩展引起了亚临界裂纹扩展而进入到母材。
3、防止氢脆的若干对策。
从上述一些氢脆损伤例的原因分析中可以归纳出,要防止此类损伤发生,主要应从结构设计上、制造过程中和生产操作方面采取如下措施:
(1)尽量减少应变幅度,这对于改善使用寿命很有帮助。
采取降低热应力和避免应力集中等措施都是有效的。
(2)尽量保持TP347堆焊金属或焊接金属有较高的延性。
为此,
一、是要控制TP347中δ铁素体含量,焊态时最大值以10%为宜(为防止焊接中产生热裂纹,下限可控制不低于3%),以避免含量过多时在焊后最终热处理过程转变成较多的Ó相而产生脆性;
二、是对于前述那些易发生氢脆的部位,应尽量省略TP347堆焊金属或焊接金属的焊后最终热处理,以提高其延展性。
因为不锈钢焊接金属的氢脆与奥氏体基体中的铁素体含量和Ó相的存在密切相关。
δ铁素体量越多,经焊后热处理后所形成的Ó相的比例越大,其材料延性越差,这时再吸收氢的话,焊接金属的延性将进一步降低.
(3)装置停工时冷却速度不应过快,且停工过程中应有使钢中吸藏的氢能尽量释放出去的工艺过程,以减少器壁中的残留氢含量。
另外,尽量避免非计划的紧急停工:
(紧急放空)也是非常重要的。
因为此状况下器壁中的残留氢浓度会很高。
(三)高温硫化氢的腐蚀
在加氢装置中,一般都会有硫化氢腐蚀介质存在。
对于以碳钢或低铬钢制的设备,在操作温度高于204℃,其腐蚀速度将随着温度的升高而增加。
特别是当硫化氢和氢共存的条件下,它比硫化氢单独存在时产生的腐蚀还要更为剧烈和严重。
氢在这种腐蚀过程中起着催化剂的作用,加速了腐蚀的进展。
对于在硫化氢和氢共存条件下的材料选择,一是参考相似条件的经验数据来预计材料的腐蚀率后确定;二是在无经验数据依据时,可根据柯珀曲线来估算材料的腐蚀率。
该曲线是美国腐蚀工程师学会的一个专门小组通过大量的实验和生产数据经电子计算机反复回归处理、关联后整理出来的。
据验证按此曲线估算出来的腐蚀率与工业装置的经验比较接近。
对于不同铬含量(0~9%)的铬钢的腐蚀率,先按给定的硫化氢浓度和温度求出碳钢的腐蚀率,然后再乘以相应铬含量的系数。
(P801)
湿硫化氢腐蚀(主要设备有空冷器、冷换设备、冷高分器、冷闪蒸罐,汽提塔顶、回流罐)
1、湿硫化氢环境(H2S+H2O)主要是由于电化学腐蚀和反应产生的氢原子扩散到钢中引起:
H2S→H++HS-
HS-→H++S2-
Fe→Fe2++2e
Fe2++S2-→FeS
2H++2e→2H→H2(H向钢中扩散)
2、湿硫化氢引起的钢材损伤的几种形式
●均匀腐蚀
●氢鼓泡
●氢致开裂(HIC)
●应力导向氢致开裂
低强度钢易发生氢鼓泡(HB)和氢致开裂(HIC),而高强钢易发生应力腐蚀开裂。
3、防腐对策(选材)
●对介质中硫化氢含量较低,腐蚀不太严重者,往往采用普通碳素钢,适当加大腐蚀裕量。
●对于介质中硫化氢中等场合,腐蚀严重者,可采用抗氢钢(HIC)如16MnR(镇静钢)
●非常苛刻的工况,可采取“隔绝”方法,即在内壁衬上(或堆焊上)一层抗腐蚀的金属将硫化氢腐蚀介质与基层钢板隔开。
如铁素体不锈钢(0Cr13)TP410,奥氏体钢和镍合金,蒙耐尔合金。
●注入缓蚀剂缓蚀剂的作用是覆着在器壁、罐管壁上,起到保护作用。
(四)连多硫酸引起的应力腐蚀开裂
1、连多硫酸应力腐蚀开裂的特征。
应力腐蚀开裂是某一金属(钢材)在拉应力和特定的腐蚀介质共同作用下所发生的脆性开裂现象。
奥氏体不锈钢对于硫化物应力腐蚀开裂是比较敏感的。
连多硫酸(H2SXO6X=3~6)引起的应力腐蚀开裂也属于硫化物应力腐蚀开裂,一般为晶间裂纹。
这种开裂与在高温运转时由于碳化铬析出在晶界上,使晶界附近的铬浓度减少形成贫铬区有关。
连多硫酸的形成是由于设备在含有高温硫化氢的气氛下操作时生成了硫化铁,而当设备停止运转或停工检修时,它与出现的水分和进入设备内的空气中的氧发生反应的结果。
即:
3FeS+5O2→(Fe2O3+FeO)+3SO2
SO2+H2O→H2SO3
H2SO3+O2→H2SO4
FeS+H2SO3→mH2SxO6+nFe2+
FeS+H2SO4→FeSO4+H2S
H2SO3+H2S→mH2SxO6+Ns
Fes+H2SxO6→FeSxO6+H2S
2、连多硫酸应力腐蚀开裂实例。
在石化工业装置中,奥氏体不锈钢或管道发生硫化物应力腐蚀开裂多有见到。
连多硫酸应力腐蚀开裂在加氢装置中也都发生过。
如日本一些加氢脱硫装置上的若干冷凝器的浮头盖连接螺栓由此原因发生过多根折断损伤。
3、防止对策。
针对此种损伤发生的机理和影响因素,为防止其发生,应从设计上、制造上和使用上采用如下措施:
(1)设计上的措施选用合适的材料是有效的措施之一。
一般应选用超低碳型(C≤0.03%)或稳定型的不锈钢(如SUS321,SUS347),采用奥氏体,铁素体双相不锈钢也有较好的使用效果。
还可以选用铁素体不锈钢,因它对连多硫酸的应力腐蚀开裂不敏感,在结构上应尽量避免有应力集中。
(2)制造上的措施要尽量消除或减轻由于冷加工和焊接引起的残余应力,并注意加工成不形成应力集中或尽可能小的结构。
因为已有实验表明,此种裂纹发生时间的对数值与应力大小大致成直线的关系。
这从国外曾对不锈钢设备发生应力腐蚀开裂原因之一的应力种类的调查统计分析中,发现80%以上的损伤是由于焊接和加工中造成的残余应力引起的也得到证实。
另外,为不使碳化物在晶间上析出,在加工后应进行固溶化热处理(约1100℃,急冷)。
实行稳定化处理(约870~950℃.)也可减少裂纹的敏感性。
(3)使用上的措施主要是缓和环境条件。
在装置停工时,采取措施抑制连多硫酸生成或用中和溶液将形成的连多硫酸中和掉。
根据不同的停工方案,用1.5~2%浓度的碳酸钠溶液进行中和清洗或用惰性气(如氮气)封闭,以隔绝空气进入到设备中去或向系统中供给一定的热量(加热),以防止水汽析出等都是有效的措施。
(五)铬-钼钢的回火脆性
1、铬-钼钢回火脆性现象及其特征。
铬-钼钢的回火脆性是将钢材长时间地保持在325~575℃(也有人提出是在371~593℃或354~565℃或400~600℃等等)或者从这温度范围缓慢地冷却时,其材料的断裂韧性就引起劣化损伤的现象。
它产生的原因是由于钢中的杂质元素和某些合金元素向原奥氏体晶界偏析,使晶界凝集力下降所至。
从破坏试样所表明的特征来看,在脆性断口上呈现出晶间破坏的形态。
回火脆性对于抗拉强度和延伸率来说,几乎没有影响,主要是在进行冲击性能实验时可观测到很大的变化。
回火脆性还具有如下两个特征:
(1)这种脆化现象是可逆的,也就是说,将已经脆化了的钢加热到600℃.以上,然后急冷,钢材就可以恢复到原来的韧性。
(2)一个已经脆化了的钢试样的夏比断口上存在着的晶间破裂,当把该试样再加热和急冷时,破裂就可以消失。
1)影响回火脆性的主要因素。
影响回火脆性的主要因素很多,如化学成分、制造时的热处理条件、加工时的热状态、强度大小、塑性变形、碳化物的形态、使用时所保持的温度等等。
而且有些因素相互间还有关联,情况较为复杂。
下面仅从实用效果上对主要影响回火脆性特性的化学成分和热处理条件加以说明。
2)化学成分的影响
铬—钼钢化学成分中的杂质元素和某些合金元素对回火脆性影响很大。
(1)磷、锡、砷、锑杂质元素的影响
在杂质元素中,磷、锡、砷、锑元素对回火脆化都有影响。
特别是当P、Sn的含量较高时,脆化就特别显著。
对脆性敏感性的影响顺序是:
磷、锡、砷、锑。
在这些元素中,锡、锑和砷的含量可以通过对炼钢原材料的严格管理而使其降低到合适的程度,比较关键的是对磷的控制。
(2)硅、锰、铬、镍的影响
硅、锰含量高时对脆化都有促进作用,特别是硅对回火脆性敏感性影响很大,对于21/4Cr-1Mo钢来说,当硅的含量小于0.10%时,由于回火脆化引起的转变温度的变化量是很小的。
但是当含量较高(≧0.25%)时,对磷的影响很强烈。
因此要控制回火脆性,调整好硅-磷之间的比例是很有效的。
已有实验表明,对于显微组织为贝氏体的21/4Cr-1Mo钢,要达到使钢材经阶梯冷却后几乎不产生脆化。
Mn或Cr的添加,也会使回火脆性敏感性明显地提高。
特别是Cr的含量在2.0~3.0%的范围内时,脆化敏感性较高。
这从临氢装置中常用的几种Cr-Mo钢的回火脆性敏感性实验结果的比较也得到证明:
以21/4Cr-1Mo钢和3Cr-1Mo钢的回火脆性敏感性最大,1Cr-0.5Mo钢几乎看不到脆化现象,纯的镍钢没有回火脆性敏感性。
但是在含有P、Sn等元素的合金钢中加入Ni时,回火脆性敏感性就增加,并且Cr和Ni共存时比起它们分别单独添加时的回火脆性还要显著。
在这些元素中,影响回火脆性敏感性的顺序可以认为是:
Mn>Cr>Ni。
(3)钼、钨、铜的影响含有少量的Mo和W时,回火脆性敏感性比较低。
但是含量较高时,脆化敏感性就增高了。
如以Mo为例,有认为只要钢中的含量在0.5%以上时,回火脆性现象就可以发生。
像回火脆性敏感性比较明显的21/4Cr-1Mo钢和3Cr-1Mo钢,它们的Mo含量已达1.0%左右也是个说明。
Cu也能提高脆化敏感性,但是它的有害影响只限于贝氏体组织和杂质元素含量较多的情况下。
因此可以认为,Cu本身并不是脆化的元素,但在一定条件下可促进脆化的作用。
(4)碳的影响降低碳的含量可以使回火脆性减少。
但即使将碳抑制到极微量时,脆化也不会消除,因为碳不是脆化的必需元素。
2)热处理条件的影响
在热处理过程中,奥氏体化的温度和从奥氏体化的冷却速度都将对回火脆性敏感性产生很大的影响。
就21/4Cr-1Mo钢的回火脆性特性来说,提高其奥氏体化温度,就会使脆化敏感性增大其原因一是因为奥氏体化温度越高,奥氏体晶粒就会越粗大,这时如果处于脆化条件下,则在晶界上所偏析的脆化元素量就增加;二是已有实验证明,即使在晶界上的脆化元素量是相同的,但在粗晶情况下,比起细晶来说,晶界更容易遭到破坏。
另外,从奥氏体化温度以不同的冷却速度急冷时,也将对回火脆性产生不同的影响。
因为随着冷却速度的不同,将会形成不同的显微组织。
在急冷时,提高冷却速度将增加回火脆性的敏感性。
从组织上来看,当钢的化学成分相同时,其脆性敏感性按着马氏体、贝氏体、珠光体的顺序递减。
3、回火脆化度的研究方法。
对材料的回火脆性度进行研究时,最理想的方法是在脆化温度范围内进行等温时效处理,也即等温脆化处理。
但是这种处理方法,需要几万小时的长时间实验。
这在工程上是很难满足需要的。
因此采取了一种在较短时间内给予加速脆化的手段来衡量脆化度的方法,这种方法叫做阶梯冷却法,并在工程上广泛地被采用。
所谓阶梯冷却法就是将实验材料的试样置于回火脆化温度范围内阶梯式地进行保温与冷却(一般多是采用9个阶梯),使它发生回火脆化的方法。
阶梯冷却虽然能在较短时间内使材料发生脆化,并对其性能进行评价,但是要用这种方法来研究每一个元素的脆化特性是不能达到目的的,因为它需要使温度和所保持的时间在)个阶梯内发生变化。
可是采用等温脆化的方法,就可以将温度维持在一个恒温的温度上,并且保持时间也可以设定为一个任意值。
这样,对于每个元素引起脆化值的变化就可以随着时间的迁移来掌握。
4.回火脆性破坏实例。
在加氢裂化和加氢脱硫装置中,于20世纪70年代初期以前曾发生过多起回火脆性破坏事故,其中最严重的实例是日本一台渣油直接加氢脱硫装置的反应器。
其主要设计参数和操作条件如下:
内径3350长度14100
设计压力:
15.42MPa
设计温度:
427℃
操作压力:
13.73~14.71MPa
操作温度:
350~400℃
主体材料:
筒体ASTMA336F22+TP.309和TP.347堆焊
封头ASTMA387D级+TP.309和TP.347堆焊
厚度:
筒体200,封头120(均包括堆焊层最小厚度6.5在内)
金属重量:
~310t
该反应器于1970年4月投用,累积运行约26000h后为了它用目的,在1974年3月对内部检查时发现了内件支持圈填角焊缝上产生了裂纹,在对其焊缝修补后进行局部消除应力退火时发生了脆性破坏事故。
经调查研究和开展各种实验结果发现,在制造状态,母材vTr54的周向值为-38℃,纵向值数为-46℃。
而经三年使用后相应变为53℃和40℃,转变温度约提高了100℃。
另外从Jic测定值换算得到的断裂韧性Kic为:
在10℃下,使用前推算得Kic
为732kg.mm-3/2,而使用后则下降为330kg.mm-3/2,确认母材发生了严重的回火脆化现象(此外还确认有不锈钢焊接金属发生由于Ó相引起的脆化和由于吸收了氢引起的氢脆)。
从化学成分分析结果来看,该反应器材料中能引起脆化或促进脆化的元素如Mn、P、Si、Sn等含量都比较高,其J系数达到323,使钢材的脆性敏感性大为提高。
5.防止21/4Cr-1Mo钢制设备发生回火脆性破坏的若干措施。
加氢裂化装置所选用的铬-钼钢,以21/4Cr-1Mo钢为多,而它又是几种铬-钼钢中回火脆性敏感性较大的,下面以它作为代表提出防止产生回火脆性的一些措施。
1)尽量减少钢中能增加脆性敏感性的元素
首先要尽量减少P、Sb、Sn、As杂质元素的含量。
一般认为,当21/4Cr-1Mo钢中As和Sb的含量分别控制在,0.02%和0.004%以下时,它们对钢材的回火脆性影响不大。
另外还应降低Si、Mn的含量。
但是,为保证钢材的力学强度,Mn降到0.5%以下就困难了。
从J系数和(X)系数的经验式可看出,最终应着眼于降低Si或P的含量。
为此国外对21/4Cr-1Mo钢的冶炼,基本形成了2种系列。
一种是采用真空碳脱氧VCD的冶炼方法,生产低SIP钢。
Si含量可控制到0.01~0.02%的水平,且钢材纯洁度大为提高,偏析少,回火脆性敏感性小。
另一种是采用新的冶炼工艺,降低P的含量(可控制到0.005%以下),生产高Si超低P钢。
如日本已冶炼出0.35%-0.003%P的21/4Cr-1Mo钢,既能达到规范要求的力学性能,又具有很好的抗回火脆性性能。
至于焊缝金属的回火脆性,一般比母材还要严重,而影响因素也要比母材复杂。
它不仅受到焊接材料中杂质元素和某些合金元素的影响,而且还受到焊接金属自身焊接条件和层间多次再热的影响,也就是说,焊接金属中显微组织和晶粒度大小的变化都对脆化产生影响。
已有实验研究表明,仅用由化学成分表示的脆化