合模装置的设计1.docx
《合模装置的设计1.docx》由会员分享,可在线阅读,更多相关《合模装置的设计1.docx(12页珍藏版)》请在冰豆网上搜索。
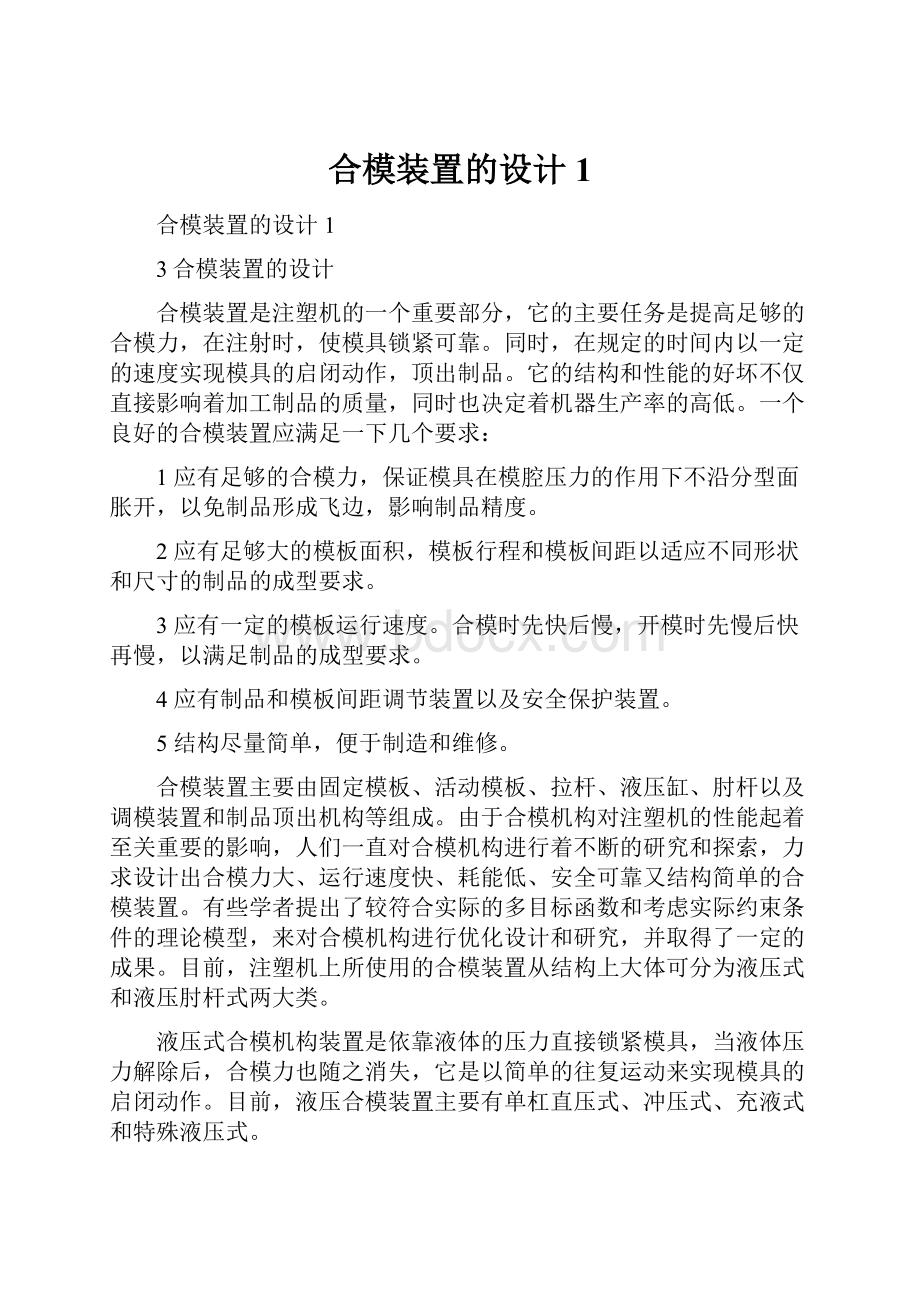
合模装置的设计1
合模装置的设计1
3合模装置的设计
合模装置是注塑机的一个重要部分,它的主要任务是提高足够的合模力,在注射时,使模具锁紧可靠。
同时,在规定的时间内以一定的速度实现模具的启闭动作,顶出制品。
它的结构和性能的好坏不仅直接影响着加工制品的质量,同时也决定着机器生产率的高低。
一个良好的合模装置应满足一下几个要求:
1应有足够的合模力,保证模具在模腔压力的作用下不沿分型面胀开,以免制品形成飞边,影响制品精度。
2应有足够大的模板面积,模板行程和模板间距以适应不同形状和尺寸的制品的成型要求。
3应有一定的模板运行速度。
合模时先快后慢,开模时先慢后快再慢,以满足制品的成型要求。
4应有制品和模板间距调节装置以及安全保护装置。
5结构尽量简单,便于制造和维修。
合模装置主要由固定模板、活动模板、拉杆、液压缸、肘杆以及调模装置和制品顶出机构等组成。
由于合模机构对注塑机的性能起着至关重要的影响,人们一直对合模机构进行着不断的研究和探索,力求设计出合模力大、运行速度快、耗能低、安全可靠又结构简单的合模装置。
有些学者提出了较符合实际的多目标函数和考虑实际约束条件的理论模型,来对合模机构进行优化设计和研究,并取得了一定的成果。
目前,注塑机上所使用的合模装置从结构上大体可分为液压式和液压肘杆式两大类。
液压式合模机构装置是依靠液体的压力直接锁紧模具,当液体压力解除后,合模力也随之消失,它是以简单的往复运动来实现模具的启闭动作。
目前,液压合模装置主要有单杠直压式、冲压式、充液式和特殊液压式。
液压——曲肘合模机构由液压系统和曲肘机构两部分组成。
它是利用肘杆机构在油压作用下使合模系统产生变形而锁紧模具。
其最大特点是具有自锁作用,即当模具锁紧后,油压撤除,合模力也不会消失,且运动特性也符合开、合模的要求。
3.1合模装置工作过程中的特性
在对合模装置的三个基本要求中(力、速度、位置和行程空间),显然,力是最主要的。
因此,根据液压式和肘杆式两种合模装置的工作原来,首先,讨论一下在力学方面所具有的一些特性。
在本节讨论中将涉及如下几种力的概念:
合模力:
合模终结时,模板对模具形成的锁紧力;
锁模力:
在合模终结时,当熔料注入模腔时,模板对模具形成的最终锁紧力;
变形力:
在锁紧模具过程中,机构由于变形而产生的内力;
移模力:
在启闭模时,对动模板的作用力;
胀模力:
因熔料模腔压力作用,而产生欲使模具分开的力。
3.1.1液压式合模装置基本特征
这种形式的合模,是依靠液体压力经油缸活塞直径实现对模具的合紧,并以其简单的往复运动来完成模具的启闭动作。
在合紧模具时所形成的合模力应为:
pcm=
×
(3-1)
式中pcm——合模力(KN)
DO——合模油缸直径(m)
po——工作油压力(MPa)
移模过程中的速度
Vm=
=
(3-2)
式中Vm——移模速度(m/min)
Q——工作油流量(L/min)
F——合模油缸的截面积(cm2)
因此,对液压式合模一般均具有如下特征:
1由式(3-1)可知,在油缸已定的情况下,合模力仅同工作油的压力有关。
所以合模装置在整个工作过程中,油缸一定要保持与负载相适应的力。
要改变合模力,可直接通过调节工作油的压力来实现。
所以调整方便,读数易于显示。
2以式(3-2)可知,若油缸已定,移模速度仅取决于油泵的流量。
在移模过程中,油泵的流量不变,其移模速度不变。
对于一般用定量泵组合起来的变速系统,则反映出所示有级变速的特征。
3动模板在油缸行程范围内的任意点,可以停止并施压,故对不同厚度的模具适应性好,合模时,模具和模板因仅受活塞杆推力作用,故受力也比较均匀。
3.1.2肘杆式(机械式)合模装置基本特征
肘杆式合模装置是利用各种形式的肘杆机构,在合模时,使合模系统形成预应力,进而对模具实现锁紧的一种合模装置。
例如图13所示的单曲肘机构,当压力油进入油缸的活塞杆端,使活塞下移,从而带动肘杆机构并推动模板向前运动。
当运动至图(13-2a)所示状态时,即模具的分型面刚接触,而肘杆机构尚未成一线排列时,动模板将受到变形阻力的作用,只有在合模油缸的工作油继续升压,并足以克服系统的变形阻力,才能使肘杆成为图(13b)所示的一线排列。
此时,合模系统因发生弹性变形(△LP)而对模具实现预紧,此预紧力pcm即为合模力。
当肘杆机构伸直并对模具实现预紧后,即使工作油的压力卸去,只要合模系统保持着原变形,其合模力是不会随之改变的。
在模具合紧后,如所有受力构件都遵守胡克定律以及不考虑接触点处的非线性变形,则受拉力作用的构件(即拉杆)的变形应为:
△LP=
3.2调模装置的选择
在注塑机合模部分的技术参数中,有最大模厚和最小模厚。
调模装置就是用于调节移动模板和前固定模板之间的距离,以适应不同的模具厚度。
对于液压——曲肘式合模装置来说,调模装置也是调整合模力的装置。
对调模装置的要求是调模要方便,便于操作;轴向位移准确、灵活、受力均匀;安全可靠,调节行程应有限位和过载保护措施。
目前,使用的调模装置形式很多,常见的几种形式有:
1将动模板设计成由两块组合起来的板,其厚度(H)可调。
2将肘杆设计成长度可调的形式。
3将整个肘杆机构设计成轴向位置可移动的结构。
本次设计选用形式1的调模装置,其结构如图3-7。
此结构的动模板是由左、右两块并用螺纹方式连接起来,通过旋动调节螺母,使动模板厚度B发生变化,从而实现模具高度和合模力的调整。
其特点是调模比较方便,但增加了模板和机器的长度,此式多用于中小型机器上。
图3-7调模装置
3.3顶出装置的设计
为了取出模内制品,在各类的合模装置上均需设置顶出装置。
顶出装置设计是否完善,将对制品质量和产量都有较大影响。
对顶出装置的要求有如下几点:
1顶出位置可选、行程可调、顶出次数可随意、直到顶出制品落下为止。
2力量足够,速度合适。
3操作方便。
3.3.1顶出形式的确定
目前使用的形式主要有:
机械顶出、液压顶出、气压吹出数种。
除部分小型机只用机械顶出外,其余均是机械、液压两种顶出同时采用。
本机属小型机器,故选用机械顶出。
机械顶出是利用固定在厚模板或其它非移动件上的顶杆,在开模过程中与移动件(模具或动模板)形成相对运动,从而推动模具的顶板(杆),使制品顶出。
因这种顶出力和速度都取决于合模机构的开模力和移模速度,所以这种装置比较简单。
但是,这种装置必须在快速开模转为慢速时才能顶出制品,从而影响到机器的循环周期。
顶出时,模具上的顶板(杆)复位,需要在闭模后当模具的顶板(杆)脱离机器的顶杆后才能实现。
这对加工需复位后才能安放嵌件的模具就不方便。
所以,只要机械顶出的机器不多,主要是在小型机器上。
3.3.2顶出位置和结构
由于本次设计采用继续顶出的合模装置,其顶出杆主要根据合模机构的结构特点来定,可放置在动模板的中心可放在模板的两侧。
故设计出“十”字形顶出架斜放与四根拉杆上下角用四个螺母定位,顶出杆放置在中间孔用螺母,垫圈锁紧,顶出架置于动模板下侧适当位置。
3.3.3顶出速度与顶出力
顶出制品时所需的力,受树脂性能、模具设计的拔模锥度,模具制造精度和光洁度,制品的面积和结构的复杂程度、冷却时间的长短等影响。
因此,很难用计算方法求得,一般根据经验来定。
机械顶出的速度和力是由机器的开模速度和开模力决定。
肘杆式的开模时的移模力则随开模行程而变化。
顶出速度一般取为1-2m/min。
3.4肘杆机构设计
3.4.1肘杆机构的运动分析
机构的运动分析主要讨论肘杆机构的几何尺寸及位置与模板行程及其速度之间的关系。
1机构的运动行程与最大起始角
图3-8双曲肘机构运动图
如上图,双曲肘在合模完毕及开模终了的运动原理图
合模装置的基本参数的确定采用参数确定方法来定,统计的频带约为15-20%。
机构的自由度为:
F=3×5-2×7=1
模板行程(mm):
Sm=11.2pcm0.5=11.2×3200.5=200.3mm
式中:
pcm——合模力
考虑到统计频带误差,取Sm=181mm
模具最大厚度(mm):
Hmax=17.42pcm0.45=17.42×3200.45=233.5mm
取Hmax=220mm
模具最小厚度Hmin=0.56Hmax=0.56×233.5=130.8mm
取Hmin=130mm
由图可写出动模板行程为:
Sm=(L1+L2)-L1Cosαmax-[L22-(L1Sinαmax)2]0.5
=L1(
+1-Cosαmax-
)(3-14)
式中:
L1、L2——后连杆、前连杆的长度
αmax——杆件L1起始位置与最终位置的夹角
λ——杆件1与2的长度比
油缸行程即为:
S0=L5[Cosγ-Cos(αmax+γ)]-[L42-(e-L5Sinγ)]0.5+{L42-[e-L5Sin(γ+αmax)]2}0.5(3-15)
L4=
(3-16)
式中:
L4=ABL5=BD
γ——L1与L5的夹角
φ——L4杆与水平轴线的夹角
e——D点至A点水平轴线的距离
从上式可知,肘杆机构的行程S是随λ(L1/L2)、αmax增大而增加。
可是,后连杆L1是由模板尺寸所决定的。
2肘杆机构参数选择
机构力的放大倍数随杆长比λ和φ角的增加而增大。
因此,机构的力的放大和速度之间的关系是相互矛盾的。
在设计时要根据具体条件,试用多种结构方案,在同一方案中又经多种参数的试算,再经结构设计的比较,才能确定一个比较合适的肘杆机构。
根据文献综合,对肘杆机构合模装置的优化设计,目前主要存在下列问题。
1讨论的重点是在证明优化方法的可行性和有效性,而不是解决具体工程设计问题;
2由于缺少经验,对目标函数,约束条件的确定与构成不够全面;
3缺少工程实践的验证。
在双曲肘设计中,在不影响性能的原则下,应尽可能的缩短中间杆L4的长度和后连杆B点至L1的距离。
后连杆夹角γ通常取10O-25O,这样设计的肘杆机构具有比较合适的开模力和整个机构的外形尺寸。
杆长比λ一般等于0.75-0.85。
参照(模板)拉杆有效间距及模板的估算尺寸,经过试算,取后连杆L1=114mm,λ=0.75
可求前连杆长为:
L2=
=153mm
后连杆夹角γ=25O,在Rt△中可求:
L3=L1tgγ=114×tg25o=53mm
L5=
=
=125.9mm
把有关数据代人(3-15)式可求得:
So=220mm
3.5合模装置主要零件设计
3.5.1模板
模板是作固定模具和运动导向的定位基准之用。
因此,模板结构和加工精度及其刚度都将直接影响到机器的使用性能。
1模板结构与尺寸确定
模板的平面布置形式采用图20所示,其特点是承载打,定位导向性能好,并采用正方形设计的模板(Ho=Vo)。
模板常用材料为35号或45号钢的铸锻件,或高标号球墨铸铁,这里选用ZG35。
模具面积(H×V)大约是拉杆间有效面积(Ho=Vo)的2-2.5倍,即:
H=V=
=415-542mm
取H=V=430mm
由拉杆有效间距(310mm)查《塑料机械设计》P461表3知,螺孔尺寸M36×30,模具定位孔直径φ100mm。
3.5.2拉杆
拉杆又称导柱,它是合模装置的重要支撑件和受力件,同时又是动模板的导向基准。
因此,拉杆应有足够的强度和刚度,导向表面要有足够的精度、光洁度和必要的硬度。
1结构形式与技术要求
拉杆结构设计,主要考虑与模板连接时的安装和安装后对合模装置有关的定位与导向精度的影响。
综合各种因素考虑,拉杆与前模板以轴肩定位,与厚模板采用通孔加螺母锁紧。
拉杆常用材料为45号钢,表面粗糙度不低于0.8,直度允差不大于0.05/1000。
2拉杆直径的确定及校核
已知:
合模力pcm=320KN,结构为四柱式(Z=4),拉杆材料45号调质(表面镀Cr),取[σ]=85000N/cm2,σ-1=27000N/cm2,n=1.6Kσ=1.8,Kε=1。
解:
a按纯拉伸计算,初选拉杆直径
DP≥
=
=3.5cm
取DP=44mm
B拉杆疲劳强度验算
由初选直径DP=44mm进行拉杆结构化设计,拉杆最小直径在轴肩处d0=36mm,按此进行疲劳强度的验算。
拉伸应力:
σt=
=
=7863.5N/cm2
压应力(取开模力p=0.1pcm)
σc=
=
=786.35N/cm2
将上式计算值代入下式取得拉杆的计算应力为:
σ=
=
=5275N/cm2
材料的耐劳许用应力:
[σ-1]=
=
=9400N/cm2
因σ≤[σ-1],故满足疲劳极限要求。
超载时的强度
若取
=65000N/cm2,n=1.8,超载系数1.4,则拉杆的最大拉应力
σtmax=
=
=11008.9N/cm2
满足σtmax≤[σt],故满足条件。