五万七散货船施工要领.docx
《五万七散货船施工要领.docx》由会员分享,可在线阅读,更多相关《五万七散货船施工要领.docx(66页珍藏版)》请在冰豆网上搜索。
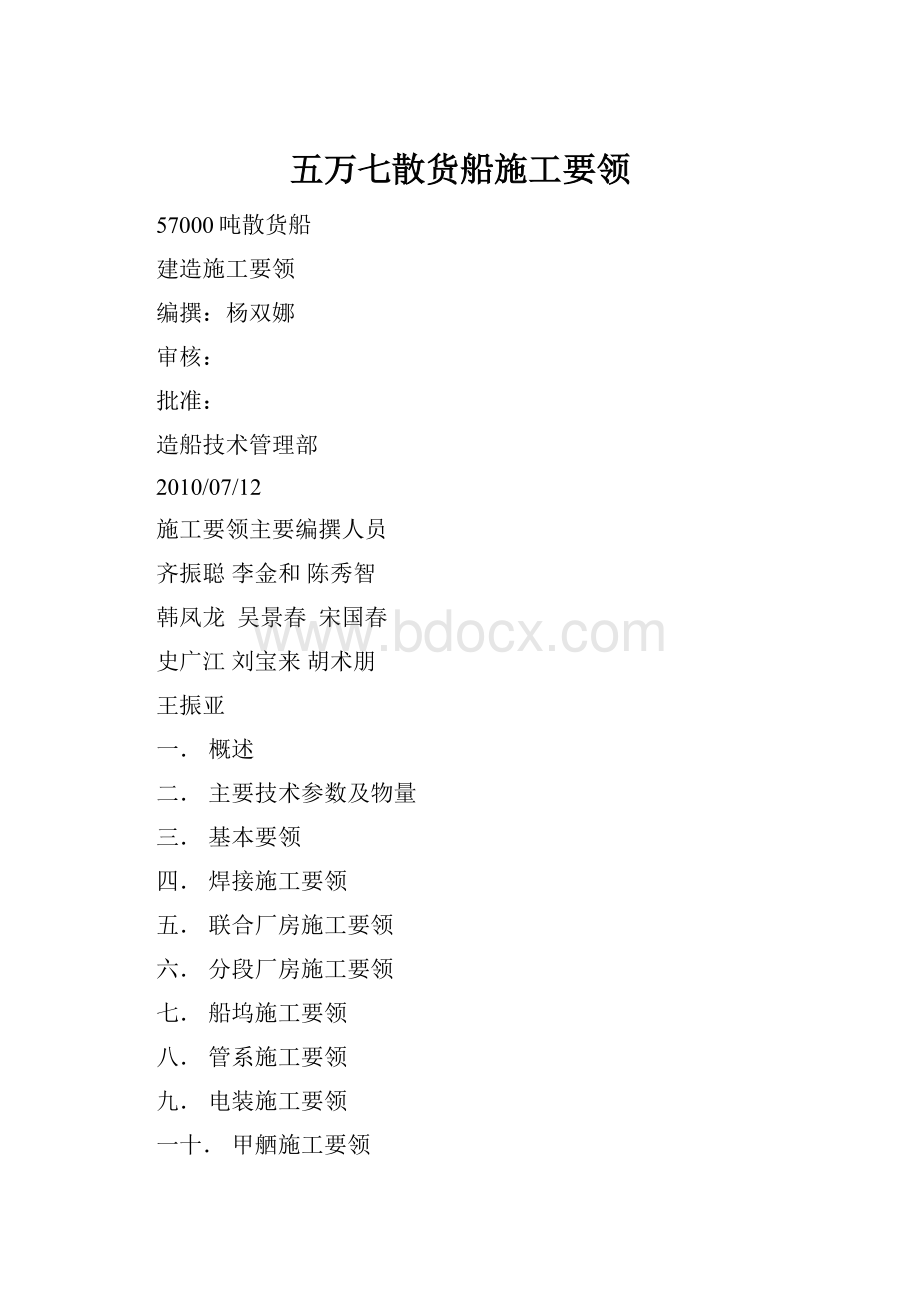
五万七散货船施工要领
57000吨散货船
建造施工要领
编撰:
杨双娜
审核:
批准:
造船技术管理部
2010/07/12
施工要领主要编撰人员
齐振聪李金和陈秀智
韩凤龙吴景春宋国春
史广江刘宝来胡术朋
王振亚
一.概述
二.主要技术参数及物量
三.基本要领
四.焊接施工要领
五.联合厂房施工要领
六.分段厂房施工要领
七.船坞施工要领
八.管系施工要领
九.电装施工要领
一十.甲舾施工要领
一十一.涂装施工要领
1.概述:
本船是为香港宏达国际船务公司建造的57000吨用于无限航区贸易航运散货船,运煤矿、铁矿、谷物、铁卷及干货。
不装载甲板货及危险品等。
船型:
本船为单机单桨、单壳型散货船,柴油机驱动,载重57000吨散货船。
1.1船东和工程编号
船东:
香港宏达国际船务公司
工程编号:
NB001—1、NB001—2/3
1.2规范和入级
NB001—1、NB001—2/3本船包括其机械装置和设备应按LR规范设计和建造。
入级:
LR级挂旗:
香港旗
1.3建造质量检验标准:
按CSQS、GB、CB和新港船舶重工有限责任公司有关标准。
1.4建造日成计划表:
工程编号NB001-1NB001-2NB001-3
开工:
2010/08/302010/11/012010/11/30
漂浮状态:
2010/03/102011/04/302011/04/30
出坞:
2011/04/302011/06/152011/06/15
试航:
2011/07/102011/08/152011/08/25
交船:
2011/07/302011/08/302011/09/15
2.主要技术参数和物量
2.1船型参数:
总长189.98m
垂涎间长185.0m
型宽32.26m
型深18.10m
设计吃水11.20m
结构吃水12.85m
航速14.30kn(11.20m吃水)
主机:
MAN-B&W6S50MC-C8型
数量:
1台
CMCR:
输出功率:
9960KW,转数:
127rpm
发电机:
600KW×3台
载重量:
(结构吃水12.85m时,平浮状态下,海水密度1.025t/m3,载重吨约为)57000t
2.2船体结构参数:
2.2.1甲板间高上甲板~A甲板3.10m
A甲板~B甲板2.80m
B甲板~C甲板2.80m
C甲板~驾驶甲板2.80m
驾驶甲板~罗经甲板2.85m
2.2.2甲板梁拱主甲板梁拱(折角直线梁拱)0.7m
驾驶甲板0.10m
罗经甲板0.10m
其它甲板梁拱0
机舱平台0
首部升高0
2.2.3肋距和双层底主船体肋距艉~FR12600m/m
FR12~FR217820m/m
FR217~艏600m/m
货舱双层底高度1780m/m
机舱双层底高度1980m/m
克令吊4台
2.3主要物量:
分段总数:
84个
坞内钩数:
30钩(不包括舱口围、克令吊及围屋)
空船重量:
~10900吨
钢板:
~9340吨(船体8492t舱盖~800t铁舾~210t)
全船管子重量:
~270吨
电缆总长度:
~130km
除锈涂装面积:
~162000m2
2.4本船特点:
主甲板为露天连续干舷甲板,设置艏楼,带球鼻首。
上建和机舱位于船舶尾部。
本船设置5个货舱,货舱区为单壳外板,设置顶边舱和底边舱。
首、尾防撞舱壁之间设置双层底。
除4、5舱顶边舱外,所有货舱区双底、顶边舱、底边舱设置为压载舱。
3货舱可以用于压载水舱。
4舱、5舱的顶边舱设置为燃油舱。
首、尾尖舱设置为压载舱。
货舱区(除1舱外)双层底设置管隧。
2.5分段划分及基本建造方针:
2.5.1分段划分原则及方针:
为缩短造船周期,加快造船进度,根据新基地总吊能力,贯彻“扩大分段总组范围”的建造方针,实行分段——总段——坞内合拢的工艺流程。
2.5.2分段划分原则上为15.2m分段。
2.6分段划分方式:
2.6.1货舱区双层底分为两个边底左(P)、右(S)分段,仅101,109分为中底分段和边底分段,即101P/C/S,109P/C/S。
2.6.2货舱舷侧为带上边舱单层船壳分段,横舱壁处带部分舱壁,分为左(P)右(S)分段。
2.6.3主甲及横壁中间嵌补部分为甲板嵌补分段,舷侧分段定位后嵌入嵌补分段。
2.6.4上层建筑前部的分段总组(总组与分段上台同步进行),整体吊装。
2.6.5首尾划分详见《分段划分图》。
2.7钢板定货基本尺寸为:
2.7.115.250m×3.0m和8m×3.0m为主(单板重量不能超过20吨);
2.7.212m×1·8m和8m×1·8m为辅
2.8分段数量为84个,总组分段数量为23个。
2.8.1上建总组分段812+821+831+841+851、861+811
2.8.2分段总组
2.8.2.1双层底102P/S左右舷进行总组,101P/C/S、109P/C/S左右舷边底与中底进行总组,103P+104P、103S+104S、105P+106P、105S+106S、107P+108P、107S+108S进行总组,共计9个总组分段;货舱区舷侧分段前后三个分段总组,左右各3组,共6个总组分段。
5个舱口间甲板分段不进行总组,单独进行吊装。
2.8.2.2机舱区及尾部:
机舱底部分段、机舱下平台以下分段以及尾部分段为一个总组分段,即301+322+311+321P/S;331P+341P,331S+341S为两个总组分段,302+303分段进行总组。
2.8.2.3首部区域:
401+403,402+404为2个总组分段。
2.8.2.4上层建筑区域:
812+821+831+841+851分段为一个总组分段,861+811分段进行总组。
2.8.2.5分段总组明细表:
分段进坞合拢顺序分段名称分段重量吊装设备
第一钩H1(102P+102S)600t
第二钩H2(103P+104P)600t
第三钩H3(103P+104S)600t
第四钩H4(101P+101C+101S)600t
第五钩H5(105P+106P)600t
第六钩H6(105S+106S)600t
第七钩H7(311+322+321P/S+301)600t
第八钩H8(201P+202P+203P)600t
第九钩H9(201S+202S+203S)600t
第十钩252600t
第十一钩H11(331P+341P)600t
第十二钩H12(331S+341S)600t
第十三钩251600t
第十四钩H14(204P+205P+206P)600t
第十五钩H15(204S+205S+206S)600t
第十六钩253600t
第十七钩254600t
第十八钩H18(302+303)600t
第十九钩H19(107P+108P)600t
第二十钩H20(107S+108S)600t
第二十一钩H21(109P+109C+109S)600t
第二十二钩341C600t
第二十三钩H23(207P+208P+209P)600t
第二十四钩H24(207S+208S+209S)600t
第二十五钩255600t
第二十六钩H26(401+403)600t
第二十七钩H27(402+404)600t
第二十八钩256600t
第二十九钩H29(812+821+831+841+851)600t
第三十钩H30(861+811)600t
第三十一~三十五钩911~915600t
第三十六~三十九钩951~954600t
第四十~四十七钩901P/S~904P/S600t
3.基本要领:
3.1本船建造重要攻关项目:
3.1.1尾段301以横壁为胎卧造、艉柱进行单装,301完成后与311,322,321P/S进行总组。
3.1.2251~256嵌补分段,舷侧分段搭载后嵌入。
3.1.3货舱区舷侧分段由平面流水线工位制作外板组合体、上坡板组合体与甲板组合体进行中组。
3.1.4船舶在坞内漂浮、移位、落墩——漂浮状态控制、移位操作、落墩定位的工艺。
3.2建造厂地安排
板材、型材、数切下料新基地厂房内切割加工工场
部件制作新基地部件焊接工场
拼板平面流水线旁预留工位
分段制造平直分段工场及曲面分段工场
分段翻身及露天装焊场地
分段预舾装分段预舾装场
翻身工位曲面线厂房内、600t平台
分段涂装分段涂装堆场及涂装工场
分段总组600t平台
坞内合拢1#船坞
3.3设计要求
3.3.1采用电子计算机进行线型光顺和外板展开,并生成外板和结构的下料数据或软盘。
3.3.2船体放样套料要与分区一致,尽量避免跨区套料,需要开坡口、过渡的构件尽量套在一起,采用无限全回转切割机进行切割,并兼顾钢材利用率的提高。
小构件搭桥需要搭在焊接面中,尽量避免搭在自由边上。
3.3.3生产设计中的工位编号
原则上沿用我厂编号原则,但根据新厂工位流程情况增加若干编号
小组装
S
大组装
A、A1、A2…
中组
ZW、ZA、ZS
平台总组
H
围壁
W
船坞内
E
平面分段流水线
L
拼板
P
平面分段流水线组装
ZL
3.3.4设计部门提供分段吊环的位置,并用图表示,发图前应与施工单位进行评审,应提供准确的分段结构重量和舾装重量,对形状较复杂的分段还应提供重量重心位置,供分段翻身时参考。
3.3.5对人员出入、设备或管子进舱、通风和高效焊接等要求的工艺开口,生产设计时应考虑周密,并标明在图纸上。
施工时如需增开工艺开口应由施工主管工程师绘出草图报设计所船体室批准,经船东和验船师认可后方可施工。
3.3.6各种放样图纸是船体工艺文件的组成部分,各工位无权随意更改,有问题时应通过造船技术管理部反馈。
3.3.7应通过合理的利用材料和严格管理来提高钢材利用率。
但工艺文件(含放样图纸)一经形成不得任意更改。
在钢材利用率与施工工艺发生矛盾时,必须首先考虑施工工艺,避免出现以提高钢材利用率为由,而置施工工艺不顾的现象。
3.3.8各工位、工序应提高自身的质量意识、严肃“三检”制度,不符合质量要求的产品不能流入下工序,对流入下工序的不合格产品,应由上工序解决。
放样工作应加强内部的管理,建立校对和事故处理记录等制度,减少出错率。
3.3.9由生产设计确定的生产流程,原则上不得变更,如确有需要变更时,应由生产主管部门协调。
3.3.10为能更合理的利用板材,要求船体放样室除了出“外板拼板图”以外,还应出“上(主)甲板排板图”、“内底板排板图”,在此基础上与车间工艺研究确定加工方法,在图纸上标示出加工工艺符号。
3.3.12各种型材许可焊接起来使用,接头长度不小于1m,在6m之内许可有一个接头。
12m以内的型材应在型材工位焊妥,超过12m的型材,在分段组装只许可有一个接头。
接头的位置应与结构位置或板口位置有相应的距离。
3.3.13各种舾装通舱件在结构上的开孔,尽量在结构图上表示出来。
3.3.14使用外包工进行施工时,施工车间除对外包工进行日常管理外,还应向其传授工艺要求和工艺纪律。
3.3.15各工位、工序应加强自身的质量意识,不符合质量要求的产品不能流入下工序。
对已经流入下工序的不合格产品,原则上应由上工序负责解决。
3.3.16每个工位应有各自的质量关键点。
现根据最近期间工程中出现的问题提示如下:
工位名称
质量关键点
改进的建议
预处理
抛丸后钢板表面清洁和漆膜均匀性
经常检查毛刷的磨损情况及时更换。
检查漆膜厚度及时调整喷漆量
下料切割
1切割后切割边缘的熔渣和毛刺
2数切划线精度
3数切机切割精度
铲除或用砂轮清磨,尤其是各种开孔的边缘
开工前校对数切机精度
开工前校对数切机精度
型材加工
1切割后切割边缘的熔渣和毛刺
2冷弯和热弯后的表面质量
铲除或用砂轮清磨。
修正补磨
板材加工
1弯板精度
2冷弯板的表面质量
3热弯板的表面质量
认真比照样板和样箱,发现超标及时修复,应尽量作到不合格品不出工位
合理排列压杠的间距和力度,使外表光顺平滑,避免压杠痕迹明显
认真控制火焰温度和走向,减少局部非正常变形的出现
小组装
1构件定位精度
2焊接质量
3焊接变形
严格按划线定位,并注重方正度
严格执行焊接工艺和设计要求,彻底清除飞溅等焊接缺陷
认真进行“背烧”要求,消除焊接变形和焊接应力
拼板
1引、止弧板
2完工板的存放
严格按要求设置
采取必要措施,避免存放时因吊鼻将上面板局部顶凸的现象
围壁
1焊接变形
2焊接质量
认真进行“背烧”要求,消除焊接变形和焊接应力
严格执行焊接工艺和设计要求,彻底清除飞溅等焊接缺陷
分段组装
1胎架
2划线
3切割
4定位焊
5装配精度
6焊接
7焊接变形
认真封胎,吊运前检查挑胎情况
划线后必须进行复查,确认无误后方能交给切割
如无检查线不能切割。
切割的坡口角度和间隙要准确。
装配时须切割时,下面必须有衬物,不得直接将火焰喷在船体上
定位焊长度、间距及焊角要按要求,且应定位牢固
构件定位、构件重合性一定要准确。
须切调时不得留台,边缘要清理干净
要按照设计的焊角施焊;包角焊要完整;装配不良的结构和影响焊接的结构,须请装配工修正或暂时拆吊后再施焊
大口处附近肋位进行“背烧”
坞内
1分段定位
2坡口准备
3其余
认真仔细,反复确认
角度准确,间隙均匀,干净整洁
参照“分段组装”的要求
3.4余量要求(具体反映在生产设计图和各种放样图上)
3.4.1船坞大口:
3.4.1.1构件有间隙或削斜为实料;
3.4.1.2板口分段二次划线时,按《分段划分图》的要求,上台前切实的要求由车间工艺确定。
3.4.2分段制作:
3.4.2.1外板的板口之间的要求,按《外板排板图》;
3.4.2.2本分段内的构件对接口为实料。
3.4.3内场制作:
3.4.3.1凡不经(预)拼板而一次形成的构件,应在下切工位划线切割成。
3.4.3.2车间工艺组应在《外板排板图》上标注一次和二次划线、切割的荒(余)量值和完成工位的符号。
3.4.3.3为了减小装配难度,全船过梁孔在理论开孔的尺寸上,向焊接部位的外缘加大2mm
3.4.3.4为了装配和焊接的精度,在双顶焊构件设计下料阶段,两端要各去掉2mm,如下图所示。
3.5船体理论线位置:
按57000吨散货轮基本设计理论线图为准。
3.6全船分段水对平合线位置分布:
货舱区.3M.7M.10M.13M.16M
首部.3M.6M.8M.10M.13M.16M.20M
尾部.3M.7M.10M.12M.14M.17M
3.7船体结构对合线和较长有曲度结构的平线
为提高船体结构制造和装配精度,方便施工,分段结构安装时应有水线或对合线控制其装配精度。
对于较长的结构件在切割、组合焊接后的变形应调直,平直构件以平直边为基准,有曲度的构件(舱口横梁、甲板强横梁、上建围沿等)应按平线校平。
3.8船体结构线型差
为保证船体外观线型精度,减少角焊焊接填充量,控制由于焊角过大而产生的变形,首尾部分肋板、平台与外板,和斜度较大结构与平直结构在角接部位应切线型差。
有线型差部位的切割,应先切直口,再按划线图的要求切线型差坡口,切割时应注意切割线型差坡口的角度的变化。
3.9全船焊接收缩补偿量:
3.9.1全船焊接收缩补偿量的分布(见分段划分图):
3.9.1.1底部分段102P/S-108P/S,横向大口处,内底、外底、艏端为实料+10mm,纵骨艉端为实料+2mm,艏端为实料+12mm。
T型材沿船长方向布置的,艉端为实料,艏端为实料+10mm,全船长度超过4m的T型材,每米延尺1mm。
纵桁艉端为实料+5mm艏端为实料+15mm。
其余分段101P/C/S横向大口处尾端为荒料。
109P/C/S尾端为实料,艏端为荒料。
3.9.1.2横壁槽型壁下端为实料加放20mm焊接收缩补偿量,底墩分段下端为实料加放5mm焊接收缩补偿量。
3.9.1.3上层建筑横、纵壁探出自由边的在探出自由边的基础上再加10mm的焊接收缩补偿量。
4.焊接施工要领:
4.1焊缝间距要求
4.1.1两对接板缝的平行间距应大于100mm,且避免尖角相交(应大于300)
4.1.2对接板缝和角焊缝的间距应大于80mm(以考虑焊肉在内)。
4.2高效焊接分布详细要求见生产设计(含放样)、(分段划分图)和有关图纸。
4.3船体建造各阶段(分段、总组、内坞合拢)的坡口形式必须按照船级社认可的坡口形式进行生产设计和施工。
4.4所有平板口(含预拼板)为埋弧自动焊或FCB焊;
4.5分段制造阶段的曲面板口为TC焊。
4.6坞内合拢阶段的平面口、水平口、货舱区的曲面和斜面大口为TC焊(个别曲面大口为手工焊,详见《分段划分图》);
4.7船台合拢阶段的货舱区外板垂直大口及内纵壁垂直大口为SG-2焊,其它曲面大口为TC焊;
4.8坞内合拢阶段的桁材和骨材对接口为TC焊;
4.9小组装、中组装的角接焊尽量多地采用CO2焊;
4.10手工平面角焊可采用铁粉焊条,但上层建筑、尾楼、首楼、甲板室、舷墙结构、舱口围板以及舱室围壁等板厚在10mm(含10mm)以下的板梁结构和焊角设计要求在4mm(含4mm)以下的,不宜用铁粉焊条。
4.11本船高强度钢采用较多,焊接施工时应按要求使用与母材相同材质或高一挡的焊接材料。
4.12分段槽型壁的对接口采用陶瓷衬垫焊的工艺方法。
4.13坞内合拢外板对接口:
水平口、上下坡板对接口、横壁与舷侧的对接口、全部采用CO2单面焊双面成型焊接工艺。
4.14横壁底墩与内底板的外侧角焊缝、中底、边底坡板与内底板的角焊缝必须使用CO2半自动角焊机施焊。
4.15分段舷顶列板与甲板的外侧角焊缝,也必须使用CO2半自动角焊机施焊,以减少舷顶列板自由边的变形。
4.16舷侧分段总组的甲板对接口201P/S+202P/S、203P/S+204P/S、205P/S+206P/S、207P/S+208P/S、为SG-2焊。
其它对接焊缝均为TC焊工艺。
4.17底部、舷侧分段制造阶段管隧纵桁、边纵桁、平台全部焊完,其余结构保留300mm暂不焊。
4.18主要对接坡口形式(CO2焊接按QJ/XG04.035-93Q取)
下表为本船的主要坡口形式,其余参见生产设计、本厂厂标或另行确定
主要坡口型式
种类
规格
简图
适用范围
埋
弧
自
动
焊
t≤16
c=0
埋弧自动焊拼板
埋
弧
自
动
焊
16<t≤25
f=10
c=0
埋弧自动焊拼板
埋
弧
自
动
焊
t>25
f=h=t/3
c=0
埋弧自动焊拼板
手
工
焊
t≤6
c=0~2
薄板的手工焊
手
工
焊
t>6
f=0
c=0~2
手工焊的平焊和立焊
手
工
焊
6<t≤14
f=2
t>15
f=10
手工焊的仰焊
手
工
焊
t≤24
f=0
c=0
手工焊的横焊
T
C
焊
c=8
α=45°
CO2陶瓷衬垫单面焊双面成型焊--平面焊
T
C
焊
c=6
α=40°
CO2陶瓷衬垫单面焊双面成型焊--水平(横)焊
T
C
焊
c=8
α=45°
CO2陶瓷衬垫单面焊双面成型焊--立向(立)焊
S
G
|
2
垂
直
自
动
焊
c=8
t≤16
α=50°
16<t≤20
α=45°
20<t<24
α=40°
t≥24
α=35°
垂直自动焊
5.联合厂房加工施工要领:
5.1钢板预处理流水线
5.1.1根据开工分区放样下达的资料,核定材料定额。
建立工位生产用料台帐,开出钢材领料单,递交物资钢板和型材库,按搬入时间进料。
严格按分区的前后顺序及生产进料计划进行,严禁先搬后抛,后搬先抛的颠倒现象。
5.1.2钢材表面应保持平整、光顺,不得有凹凸缺陷存在涂装表面应达到工艺要求,喷漆膜后15μ-30μ,除锈达到SA2.5级。
5.1.3钢材表面的麻点超出规定范围内的要进行修整、补磨、出现夹层应予以退换材料。
5.1.4钢材进行抛涂时,根据天气湿度进行预热和烘干,对于漏砂、漏漆现象应采取清扫、补漆措施。
钢材规格、材质、船名应字迹工整,标注清楚。
检验每张板的船级代号及炉批号,且钢印用色漆圈划。
5.1.5根据切割单位提供的用料计划,按工位批量发料。
新等离子(干式)数控切割工位采用托盘配材,用拖车运入切割区。
5.1.6高强度钢板的油漆颜色按规定喷漆。
5.2下料切割工序
5.2.1数控切割(等离子)机,高精度门式切割机,无限回转边坡口等离子等设备,应定期检查其精度,超出精度标准的应进行检修调试。
5.2.2切割平台应保持平整,对于出现严重影响钢板平度的缺陷,应予以正改。
5.2.3下料、划线、切割前应对图纸进行认真审阅,领会图纸意图及要领,核对钢板规格,材质及构件数量,采用连续尺寸截取,对角线校正方度的手段,控制好板构件外形尺寸精度及位置线精度,减少积累误差及切割变形。
号料时应清晰地写出产品编号、分段编号、零件号及各种符号和标识,一次下料后,应将一平方米面积以上的余料进行板厚、材质、炉号移植,并用色漆标写在余料边缘,对划线所用工具,尤其直尺定期检验或换新。
5.2.4零件切割分工原则:
5.2.4.1新基地切割机,平板下料切割用高精门切,曲板下料切割用全回转坡口等离子切割机。
5.2.4.2构件下料切割有全回转坡口等离子切割机一台、等离子切割机一台(此台不带坡口),所以不带坡口的构件尽量套在一起。
5.2.4.3扁铁下料切割尽量安排在多头切割机上。
5.2.5在“等离子切割规范”允许的条件下,尽量将易变形结构件采用等离子切割,半自动切割重要构件时(如舱口面板,机座纵绗面板等)应按预先设置的检验直线放置轨道,(其轨道要经常校直),防止切后出现不直,易变形的扁钢及窄条子,要扩大平行切割及等离子切割。
5.2.6直口割逢应将割枪,割嘴处于垂直钢板的表面进行,合理选择各种工艺参数。
如板厚、割嘴型号、供氧纯度、氧压、切割速度等相匹配,保证最高切割速度下的最佳断面质量,杜绝氧化铁流入下工序。
5.2.7坡口过渡应按构件所注明的要求认真切割,确保应有的“留底”量。
凡无“底”坡口,应将坡口尖控制在0-2mm,不允许出现“伤根”,防止造成构件外形尺寸不足,坡口角度不应凭经验估算,应取决于板直角边长“L”,其计算方法按板厚乘以角度参数。
各角度参数
角度
15
20
2.5
25
30
35
40
45
50
60
板厚
(T)
T
T
T
T
T
T
T
T
T
T
直角边(L)
.268
T
.364
T
.414