龙门刨床控制系统设计.docx
《龙门刨床控制系统设计.docx》由会员分享,可在线阅读,更多相关《龙门刨床控制系统设计.docx(16页珍藏版)》请在冰豆网上搜索。
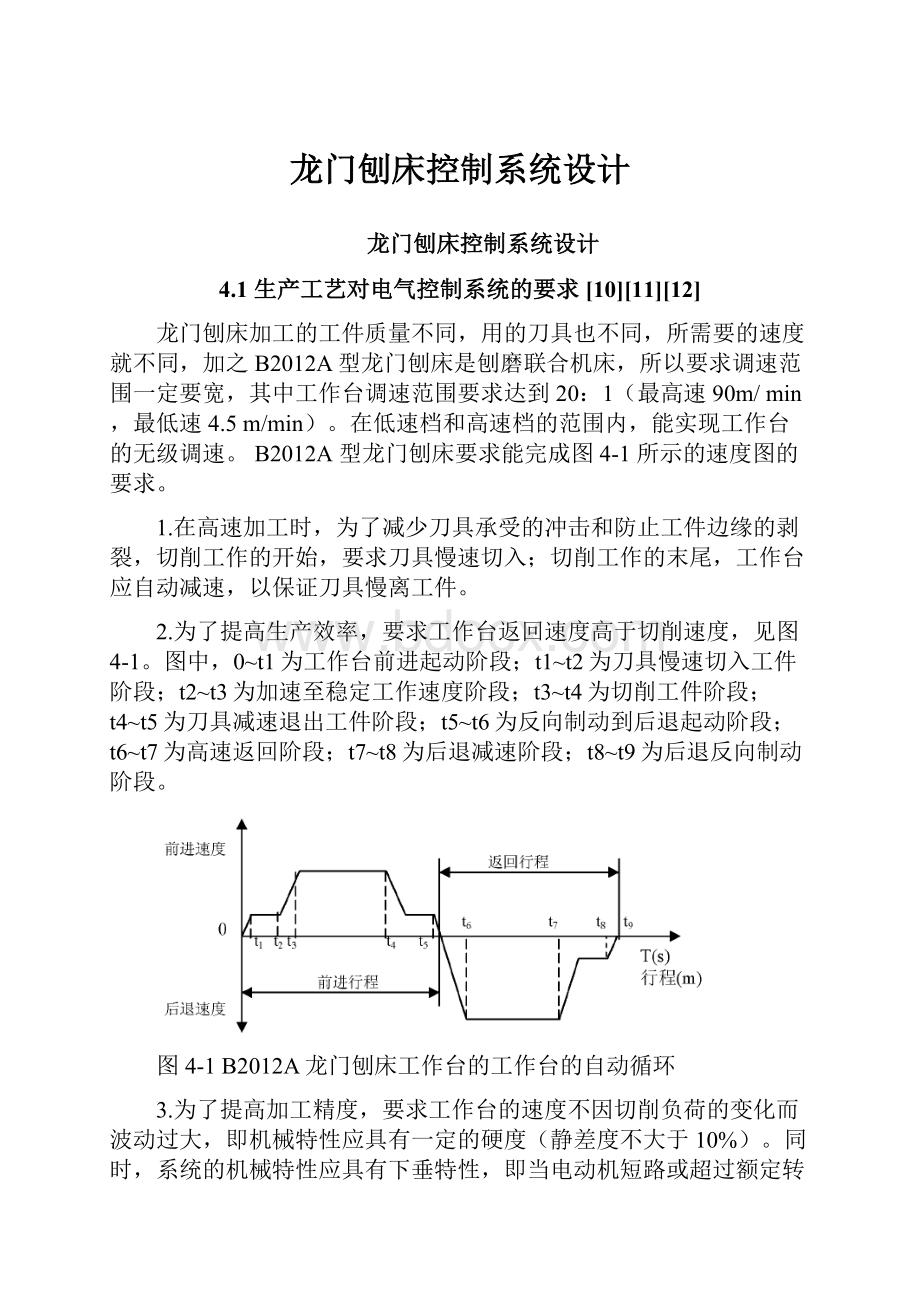
龙门刨床控制系统设计
龙门刨床控制系统设计
4.1生产工艺对电气控制系统的要求[10][11][12]
龙门刨床加工的工件质量不同,用的刀具也不同,所需要的速度就不同,加之B2012A型龙门刨床是刨磨联合机床,所以要求调速范围一定要宽,其中工作台调速范围要求达到20:
1(最高速90m/min,最低速4.5m/min)。
在低速档和高速档的范围内,能实现工作台的无级调速。
B2012A型龙门刨床要求能完成图4-1所示的速度图的要求。
1.在高速加工时,为了减少刀具承受的冲击和防止工件边缘的剥裂,切削工作的开始,要求刀具慢速切入;切削工作的末尾,工作台应自动减速,以保证刀具慢离工件。
2.为了提高生产效率,要求工作台返回速度高于切削速度,见图4-1。
图中,0~t1为工作台前进起动阶段;t1~t2为刀具慢速切入工件阶段;t2~t3为加速至稳定工作速度阶段;t3~t4为切削工件阶段;t4~t5为刀具减速退出工件阶段;t5~t6为反向制动到后退起动阶段;t6~t7为高速返回阶段;t7~t8为后退减速阶段;t8~t9为后退反向制动阶段。
图4-1B2012A龙门刨床工作台的工作台的自动循环
3.为了提高加工精度,要求工作台的速度不因切削负荷的变化而波动过大,即机械特性应具有一定的硬度(静差度不大于10%)。
同时,系统的机械特性应具有下垂特性,即当电动机短路或超过额定转矩时,工作台拖动电动机的转速应迅速下降,以致停止,从而保护电动机和机械设备不被损坏。
4.机床应能单独调整工作行程与返回速度,能作无级变速,且调速时不必停车。
要求工作台运动方向能迅速平滑地改变,冲击少。
刀架进给和抬刀能自动进行,并有快速回程。
有必要的联锁保护,通用化程度高,成本低,系统简单,易于维修。
4.2控制系统整体结构
机床电气控制系统中,主电路部分包括主传动电动机(工作台电动机,55kW)、垂直刀架电动机(1.5kW)、右侧刀架电动机(1.5kW)、左侧刀架电动机(1.5kW)、横梁升降电动机(3kW)、横梁夹紧与放松电动机(0.6kW)、通风用电动机(1.5kW)、润滑泵电动机(0.25kW)。
控制电路包括工作台控制电路、刀架控制电路、横梁控制电路以及照明、保护等辅助控制电路。
电气系统的结构框图如图4-2所示:
图4-2龙门刨床变频控制系统框图
4.3系统硬件实现
4.3.1电动机主电路设计[13][14]
控制系统设计时,只是将主拖动的直流电动机变换为输出力矩相等的变频调速电动机型号为YBP315-8,功率为55kW。
各电动机主电路如图4-3所示。
图4-3龙门刨床控制系统各电动机主电路图
4.3.2B2012A型龙门刨床主要电气部分控制分析
B2012A系列龙门刨床主要电气原理图如图4-4所示:
图4-4B2012A型龙门刨床的电气原理图
4.3.2.1刀架控制电路
B2012A系列龙门刨床采用交流电动机拖动的机械进刀方法,这种方法在电气上比较简单。
以垂直刀架控制为例。
垂直刀架有两个,每个刀架有快速移动、自动进给两种工作状态,每种工作状态有水平进刀(左右)、垂直进刀(上下)四个方向的动作,这些都由一个垂直刀架电动机来完成的。
当调整时,K4的触点是闭合的,装在进刀箱上的快速移动与自动进给转换手柄放在快速移动位置,开关SQ13的常闭触点接通,常开触点断开,选择刀架运动方向后,操纵SB3就使KM4线圈通电,垂直刀架电动机按所需的方向快速移动。
当自动工作时,快速移动与自动进给转换手柄放在自动进给位置,SQ13的常闭触点断开,常开触点接通,同时自动工作触点K4的触点也断开,保证了工作台自动工作时不能进行快速移动。
当工作台后退换向时,触点K6闭合,KM3线圈通电,电动机使刀架进刀,前进换向时,触点K7闭合,KM5线圈通电,电动机使进刀机构复位,准备下一次进刀。
左、右刀架的工作情况和垂直刀架基本相似,所不同点是左、右刀架只有上、下两个方向移动。
另一个不同点是,控制左、右刀架进给的交流接触器一端电源不是直接接在同一处,而是经过SQ8、SQ9后再接到同一根线上的。
其目的是防止刀架与横梁碰撞。
4.3.2.2横梁控制电路
横梁有放松、夹紧以及上、下移动等动作,横梁放松夹紧的动力有电动机、液压及压缩空气等几种方式,B2012A系列龙门刨床是采用电动机来实现的,横梁升降由电动机来完成的。
只有在工作台停止工作时,K4触点闭合,才能操作横梁电路。
如果需要横梁升降时,电路会自动地放松横梁。
如横梁上升,按下按钮SB7,K2线圈通电,其触点K2闭合,KM12线圈通电,使横梁夹紧放松电动机工作,横梁逐渐放松。
横梁放松时,控制位置开关SQ10的制子往横梁方向移动,移动到一定程度,使SQ10动作,SQ10-2断开,KM12线圈断电,横梁放松完毕。
此时,SQ6-1接通,由于K2已经闭合,所以,KM9线圈通电,横梁升降电动机运转,横梁上升,横梁升到所需的位置时松开SB7,K2、KM9线圈失电,横梁升降电动机停止运转,横梁停止上升。
SQ7是横梁上升到极限位置时避免与龙门顶相碰的保护开关。
这时KM11线圈通电,横梁放松夹紧电动机工作,开始横梁夹紧,到SQ10复位后,SQ10-1断开,SQ10-2闭合,为以后横梁放松做准备,此时KM11线圈经过KA1以及KM11继续供电,横梁继续夹紧,因而电动机M8中电流增大,通过KA1线圈的电流亦增大。
当电流增加到整定值时,KA1动作,触点KA1断开,KM11线圈断电。
由于KM12的存在,即使横梁没有放松完毕,松开按钮,也能保证横梁放松完毕后再自动夹紧。
当按下横梁下降按钮SB6时,也是先放松,后下降,下降到所需要的位置时,松开按钮SB6,这时除了夹紧电动机工作外,还有消除丝杠与丝母间隙的横梁稍微回升的动作,这个动作过程是由时间继电器KT3完成的。
当横梁下降时,接触器触点KM10闭合,时间继电器KT1线圈通电,其触点KT1闭合,由于接触器KM11触点断开,所以KM9线圈不通电,当横梁下降完毕,开始横梁夹紧时,接触器KM11触点闭合,而KT1的触点是延时释放,所以KT1线圈断电后,其常开触点还是接通的,这时KM9线圈通电,横梁回升,由于KT1延时很短,KT1断开,KM9线圈断电,横梁回升完毕,继续夹紧到KA1动作为止。
如果横梁回升比较多,是时间继电器KT3延时太长,可适当缩短延时时间。
4.3.2.3控制工作台的位置控制
龙门刨床的自动工作是由安装在床身侧的六个位置开关来控制的。
为了熟悉工作台的控制电路以及试车、故障检修的方便,有必要熟悉位置开关的零位以及动作情况。
位置开关零位图如图所示。
图4-5位置开关零位图
在自动控制过程中各个制子碰撞各自的位置开关,前进末了时,制子A碰撞前进减速开关SQ1,然后制子B碰撞前进换向开关SQ5,工作台经过一段越位后开始后退,后退开始时,制子B使SQ2复位,然后制子A使SQ1复位。
在后退末了时,制子C碰撞后退减速开关SQ3,然后制子D碰撞后退换向开关SQ4,亦是经过一段越位后换成前进,制子D将SQ4复位,然后制子C使SQ3复位。
位置开关SQ5、SQ6是前进以及后退终端越位保护。
由于不熟悉或不注意位置开关零位,损坏位置开关的现象比较多。
所以,在安装或故障检修完毕试车时,应先将位置开关拨在零位,制子放在位置开关两侧,然后开步进步退试验,正常后方可开启自动工作。
制子A、B、C、D间的距离是可调的,在高速档工作时间距应该大些,一般减速制子A、C的提前量为换向制子B、D的250~300毫米左右,低速档工作时间距小一些,避免低速行程太长,降低生产效率。
4.3.2.4步进、步退与润滑泵控制电路
按下步进按钮SB8时,K3线圈通电,使变频器发出相应的指令,以规定的速度步进。
按下步退按钮SB12时,K5线圈通电,使变频器发出相应的指令电动机以步退速度带动工作台后退。
在操作时,如果位置开关SQ1、SQ2没有复位,则接不通电路。
步进、步退速度是可调的,一般低速档为3~4米/分,高速档为6~8米/分。
润滑泵控制开关SA7有两个工作位置,工作台不工作而需要润滑泵时,将开关SA8拨在连续位置。
工作台自动工作时,SA8拨在自动位置。
SA8拨在任意一个工作位置上,KM2线圈通电,润滑泵电动机工作。
当润滑油达到一定压力时,压力继电器触点KP闭合,为自动工作准备条件。
4.3.2.5工作台自动工作控制电路
如果位置开关是零位,制子在位置开关两侧,按下前进按钮SB9,K4线圈通电,其触点K4闭合,K3线圈通电,工作台以调节好的前进速度前进。
前进末了时,制子A碰撞前进减速开关SQ1,触点SQ1闭合,减速继电器K8线圈通电,工作台以减速速度前进,当制子B碰撞前进换向开关SQ2后,SQ2断开,K3线圈断电,触点K3接通,由于K3是接通的,因而K5线圈通电,触点K5断开,K8线圈断电,工作台以调节好的后退速度开始后退。
制子B使SQ2复位,在没有复位前,刀架控制电路中,由于触点SQ2闭合,K7线圈通电,触点K7闭合,接触器KM4线圈通电,进刀电动机转动使进刀机构复位,SQ2复位后,SQ1断开,K7线圈断电,触点K7断开,接触器KM4线圈断电,进刀电动机停转。
SQ2复位后虽然使SQ11闭合,但是因K5断开,所以K3不会通电,工作台继续后退,制子A使SQ1复位。
后退到末了时,制子C碰撞后退减速开关SQ3,触点SQ-3闭合,减速继电器K8线圈通电,工作台以减速速度后退,当制子D碰撞后退换向开关SQ4,触点SQ4断开,K5线圈断电,触点K5接通,由于K4是接通的,因而K3线圈通电,触点K3断开,K8线圈断电,工作台以调节好的前进速度前进。
制子D使SQ4复位,在没有复位前,刀架控制电路中,由于触点SQ1闭合,K6线圈通电,触点K6闭合,接触器KM3线圈通电,进刀电动机转动使进刀机构进刀,SQ1复位后,SQ2断开,K6线圈断电,触点K6断开,接触器KM3线圈断电,进刀电动机停转。
进刀量的多少由调节进刀机构来完成的。
工作台继续前进,制子C使SQ4复位,完成控制。
4.4PLC设置
4.4.1PLC的选型
本控制系统共有输入设备34个,输出设备26个。
根据此数据,并考虑一定的余量,选择FX2N-80MR型PLC。
FX2N是三菱公司FX系列PLC中功能最强、速度最快的PLC。
其电源电压为交流220V,有开关量输入、输出点各40个。
输入回路电压为直流24V,X0~X7的输入电流为7mA,其余输入点为5mA。
电阻性负载时输出点的额定输出为2A、220V。
4.4.2PLC的主要接口I/O分配表
表4-1PLC的输入输出地址分配
代号
I/0点
功能
代号
I/O点
功能
SB1
X1
停止按钮
KM1
Y0
主电动机M1启动
SB2
X2
启动按钮
KM2
Y1
电动机M2启动
SB3
X3
垂直刀架控制按钮
KM3
Y4
电动机M3启动
SB4
X4
右侧刀架控制按钮
KM4
Y5
电动机M4正转
SB5
X5
左侧刀架控制按钮
KM5
Y6
电动机M4反转
SB6
X6
横梁上升控制按钮
KM6
Y7
电动机M5正转
SB7
X7
横梁下降控制按钮
KM7
Y10
电动机M5反转
SB8
X10
工作台步进按钮
KM8
Y11
电动机M6正转
SB9
X11
工作台前进按钮
KM9
Y12
电动机M6反转
SB10
X12
工作台停止按钮
KM10
Y13
电动机M7正转
SB11
X13
工作台向后按钮
KM11
Y14
电动机M7反转
SB12
X14
工作台步退按钮
KM12
Y15
电动机M8正转
SQ1
X15
工作台前进减速
KM13
Y16
电动机M8反转
SQ2
X16
工作台前转后
K3
Y17
工作台步进控制
SQ3
X17
工作台后退减速
K4
Y20
工作台自动循环控制
SQ4
X20
工作台退转前
K5
Y21
工作台步退控制
SQ5
X21
工作台前进极限
X1
Y22
变频器运行频率选择
SQ6
X22
工作台后退极限
X2
Y23
变频器运行频率选择
SQ7
X23
横梁上升极限
X3
Y24
变频器运行频率选择
SQ8
X24
横梁下降刀架限位
X4
Y31
变频器正转点动控制
SQ9
X25
横梁下降刀架限位
X5
Y32
变频器反转点动控制
SQ10
X26
横梁放松检测
FVD
Y27
变频器正转控制
SQ11
X27
工作台低速运行
REV
Y30
变频器反转控制
SQ12
X30
横梁加紧继电器
K9
Y25
工作台低速运行
SQ13
X31
自动进刀行程开关
K10
Y26
磨削控制
SQ14
X32
自动进刀行程开关
SQ15
X33
自动进刀行程开关
SA7-1
X34
油泵手动控制开关
SA7-2
X35
油泵自动控制开关
SA6
X36
自动/手动控制开关
SA8
X37
磨削控制开关
KP
X40
压力继电器
TA/TC
X41
变频器软故障报警
4.4.2PLC外部主要部分接线图
PLC的外部接线图如下所示:
图4-6PLC外部接线图
4.5变频器设置
4.5.1变频器选型
根据前述龙门刨床直流拖动系统工作要求,对于取代直流拖动并超越直流拖动的交流变频调速来说,选择华为TD2000系列产品。
TD2000系列通用变频器是高品质、多功能、低噪音变频器。
具有丰富的功能,可满足各种不同的需求;
变频器的控制为外部控制,而各速度段控制频率由Y22、Y23、Y24的组合来完成。
例如:
系统工作于正常切削状态,此前润滑已起动(即Y14为ON),则Y27为ON(正转)且Y30-OFF,Y22-NO,Y23-OFF(由变频器设定对应运行频率),此时工作台电动机处于切削状态。
其它控制过程与此相似。
当电动机出现过载或缺相故障时,变频器停止输出并发出报警(TA、TC为ON),同时将此信号送入PLC,PLC根据程序做出相应处理(停车)。
4.5.2变频器的外部接线图
图4-7变频器外部接线图
本系统循环工作时,要求有快速停车,所以利用变频器的特点,加装制动单元和制动电阻以吸收电动机产生的能量,实现快速安全制动停车。
4.5.3变频器系统功能设定
根据拖动系统的运行特性及系统的功能,要对变频器进行相关的系统设这里对其中的一些主要设定参数进行介绍。
F00=1;运行频率设定方式1F02=1;运行命令选择,用控制端子
F04=50;最大输出频率F05=50;基本运行频率
F07=0;通用负载选0F09=0.2;加速时间1
F10=0.2;减速时间1F11=50;上限频率
F12=0;下限频率F18=1;电机过载保护方式选择1
F19=100.0%;电机过载保护系数F20=1;功能块20-45选择
F31=2;停机直流制动起始频率F32=15%;停机直流制动电压
F33=5s;停机直流制动时间F46=1;功能块46~70显示选择
F58=5;多段频率1F59=10;多段频率2
F60=15;多段频率3F61=20;多段频率4
F62=25;多段频率5F63=30;多段频率6
F64=50;多段频率7F119=1;控制端子X1功能选择
F120=2;控制端子X2功能选择F121=3;控制端子X3功能选择
F122=12;控制端子X4功能选择,频率递增指令UP
F123=13;控制端子X5功能选择,频率递减指令DOWN
F127=0;FWD/REV运转模式设定,两线控制模式1
F165=2;参数写入保护,除本功能码外其余禁止改
4.6编程软件实现
B2012A型龙门刨床主要控制系统的PLC控制梯形图如图4-8所示(部分)。
编程软件包使用三菱的GXDeveloper8.86中文编程软件,是适用于三菱全系列PLC的编程、调试软件,它是在国际标准IECll31—3的基础上建立的,可以用LAD、CSF和STL来编程。
这是一种可以运行于通用微机中的Windows环境下进行编程的语言。
将它通过计算机的串口和一根转接电缆与PLC的接口相连,即可以进行相互间的通信。