机械手模型的PLC控制系统设计.docx
《机械手模型的PLC控制系统设计.docx》由会员分享,可在线阅读,更多相关《机械手模型的PLC控制系统设计.docx(36页珍藏版)》请在冰豆网上搜索。
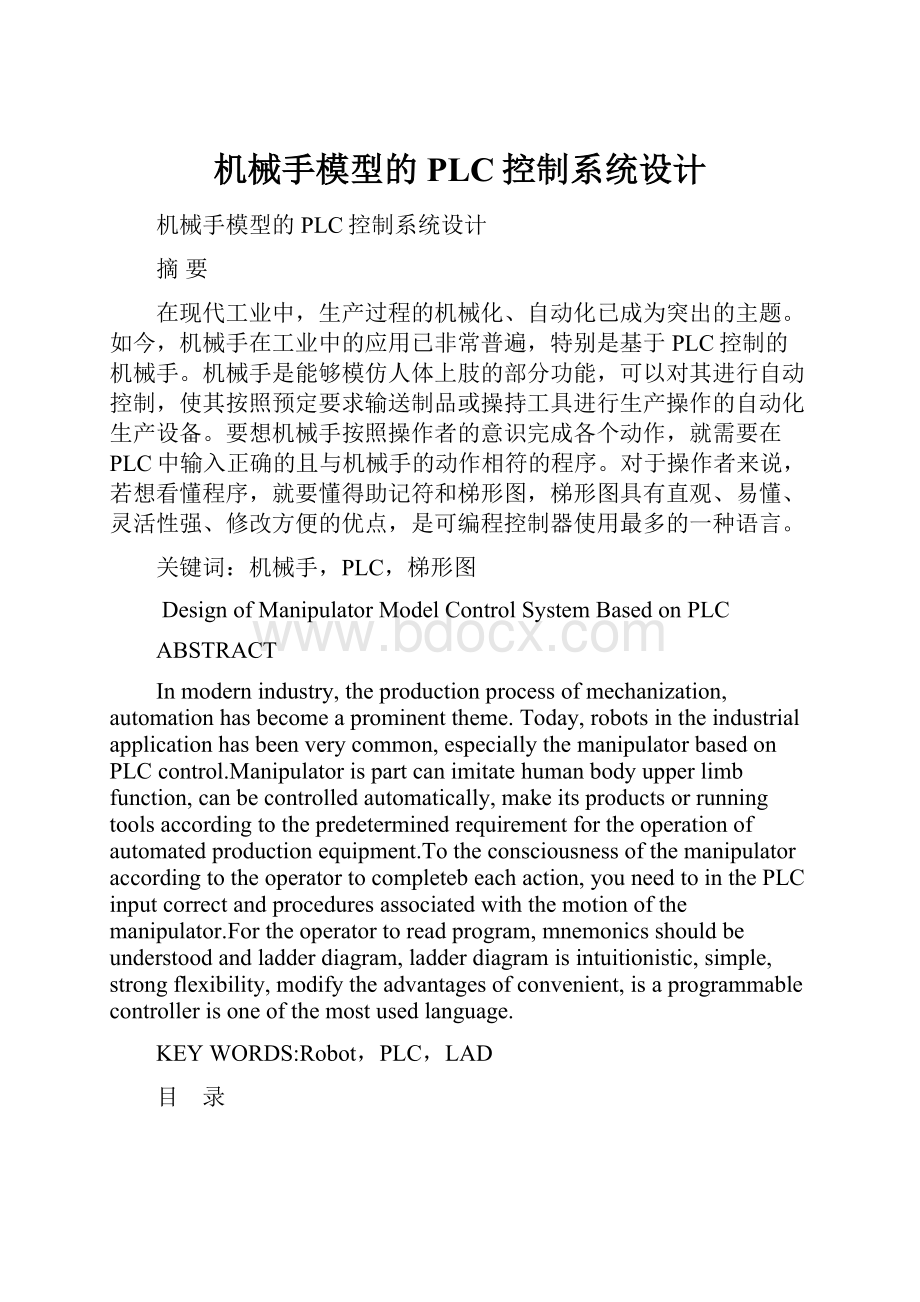
机械手模型的PLC控制系统设计
机械手模型的PLC控制系统设计
摘要
在现代工业中,生产过程的机械化、自动化已成为突出的主题。
如今,机械手在工业中的应用已非常普遍,特别是基于PLC控制的机械手。
机械手是能够模仿人体上肢的部分功能,可以对其进行自动控制,使其按照预定要求输送制品或操持工具进行生产操作的自动化生产设备。
要想机械手按照操作者的意识完成各个动作,就需要在PLC中输入正确的且与机械手的动作相符的程序。
对于操作者来说,若想看懂程序,就要懂得助记符和梯形图,梯形图具有直观、易懂、灵活性强、修改方便的优点,是可编程控制器使用最多的一种语言。
关键词:
机械手,PLC,梯形图
DesignofManipulatorModelControlSystemBasedonPLC
ABSTRACT
Inmodernindustry,theproductionprocessofmechanization,automationhasbecomeaprominenttheme.Today,robotsintheindustrialapplicationhasbeenverycommon,especiallythemanipulatorbasedonPLCcontrol.Manipulatorispartcanimitatehumanbodyupperlimbfunction,canbecontrolledautomatically,makeitsproductsorrunningtoolsaccordingtothepredeterminedrequirementfortheoperationofautomatedproductionequipment.Totheconsciousnessofthemanipulatoraccordingtotheoperatortocompletebeachaction,youneedtointhePLCinputcorrectandproceduresassociatedwiththemotionofthemanipulator.Fortheoperatortoreadprogram,mnemonicsshouldbeunderstoodandladderdiagram,ladderdiagramisintuitionistic,simple,strongflexibility,modifytheadvantagesofconvenient,isaprogrammablecontrollerisoneofthemostusedlanguage.
KEYWORDS:
Robot,PLC,LAD
目 录
前 言
在现代工业中,生产过程的机械化、自动化已成为工业发展的趋势。
但除切削加工外,还有大量的装卸、搬运、装配等作业,有待于进一步实现机械化。
据资料介绍,美国生产的全部工业零件中,有75%是小批量生产,金属加工生产批量中有四分之三是在50件以下,零件真正在机床上加工的时间仅占零件生产时间的5%。
从这里看出,装卸、搬运等工序机械化的迫切性,工业机械手就是为实现这些工序的自动化而生产的。
自上世纪六十年代,机械手被实现为一种产品后,它在减轻繁重的体力劳动、改善劳动条件和安全生产及提高注塑成型机的生产效率、稳定产品质量、降低废品率、降低生产成本和增强企业的竞争力等方面起到了极其重要的作用。
近十年来,对它的开发应用也在不断发展,最典型的发展是生产者将其大量应用于卫生行业(全自动生化分析仪),从而满足了卫生检验中需时间短、样品数据多的要求,但在卫生领域的机械手因采用样品单一酶试剂显色法,且采用滤光片结构设计,造成试剂价格昂贵,限制了产品市场的发展。
随着技术的进步,机械手的设计已经实破了单一试剂、加热及滤光片的束缚。
比如美国OI公司的产品,可针对单一工程,次序加4种试剂,加热温度也提高到50℃,检测器则采用二极管陈列技术,这些进步为新领域的应用提供了强大支持。
有专家估计未来10年,全自动流动分析仪的市场份额中,将有50%被全自动化学分析机械手取代。
通过了解上述两类产品的技术特点我们不难看出,机械手具有微试剂消耗,不受模板束缚,分析不同检测工程时可穿插完成,可完成研发性波长扫描优化检测,用户可自行设计新的检测工程,体积小,甚至可做现场快速分析等特点。
对卫生行业的快速分析中,也因新型机械手的设计特点而使其取代昂贵的试剂,降低分析成本成为可能。
机械手不能完全取代流动分析产品一个重要的原因是:
一些特殊样品处理技术不能在线实现,如萃取、高温蒸馏,需要离线进行。
相信随着技术的进步,这些方面的技术也会提高。
现代化的注塑机也常常配置有机械手,以提高生产效率。
注塑机械手是能够模仿人体上肢的部分功能,可以对其进行自动控制使其按照预定要求输送制品或操持工具进行生产操作的自动化生产设备。
随着工业机械化和自动化的发展以及气动技术自身的优点,气动机械手已经广泛应用在生产自动化的各个行业。
近20年来,气动技术的应用领域迅速拓宽,尤其是在各种自动化生产线上得到了广泛应用。
电气可编程控制技术与气动技术的结合,使整个系统自动化程度更高,控制方式更灵活,性能更加可靠;气动机械手和柔性自动化生产线的迅速发展,对气动技术提出了更多更高的要求。
气动机械手作为机械手的一种,它具有结构简单、重量轻、动作迅速、平稳、可靠、节能和不污染环境、容易实现无级调速、易实现过载保护、易实现复杂的动作等优点。
所以,气动机械手被广泛应用于汽车制造业、半导体及家电行业、化肥和化工,食品和药品的包装、精密仪器和军事工业等。
在现代汽车制造工厂的生产线上,尤其是主要工艺的焊接生产线,大多采用了气动机械手。
车身在每个工序的移动和车身外壳被真空吸盘吸起和放下,在指定工位的夹紧和定位及点焊机焊头的快速接近、减速软着陆后的变压控制点焊中,都采用了各种特殊功能的气动机械手。
高频率的点焊、力控的准确性及完成整个工序过程的高度自动化,堪称是最有代表性的气动机械手应用之一。
气动机械手还用于对食品行业的粉状、粒状、块状物料的自动计量包装和烟草工业的自动卷烟和自动包装等许多工序中。
如酒、油漆灌装气动机械手及自动加盖、安装和拧紧气动机械手和牛奶盒装箱气动机械手等。
第1章可编程控制器概述
1.1可编程控制器的产生与发展
1.1.1可编程控制器的一般概念
可编程逻辑控制器(ProgrammableLogicController)通常称为可编程控制器,英文缩写为PLC,是以微处理器为基础,综合计算机技术、自动控制技术和通信技术而发展起来的一种通用的工业自动控制装置。
它具有体积小、功能强、程序设计简单、灵活通用、维护方便等优点,特别是它的高可靠性和较强的恶劣工业环境适应能力更是得到用户的好评。
它将传统的继电接触器控制技术和现代计算机信息处理技术的优点结合起来,成为工业自动化领域中最重要、应用最多的控制设备。
目前已广泛应用于冶金、能源、化工、交通、电力等行业,并跃居现代工业控制三大支柱(PLC/机器人和CAD/CAM)的首位。
可编程控制器是在继电器控制和计算机技术的基础上开发出来的,在可编程控制器问世以前,工业控制领域中以继电接触器控制技术占主导地位。
继电器控制的系统由于结构简单、易懂,在工业控制领域中被长期广泛应用,但由于其设备体积大、耗电多、可靠性差、寿命短、运行速度不高、通用性和灵活性差,已不能满足现代化生产过程中生产工艺复杂多变的控制要求。
随着电子技术的高速发展,集计算机、仪器仪表、电器控制“三电”于一身的可编程控制器在概念、设计、性能价格以及应用领域等方面都有了全新的突破。
它将传统的“硬”接线程序控制方式改换为存储程序控制方式,即通过事先编制好并存于程序存储器中的用户程序来完成控制功能,而在控制要求改变时,只需修改存储器中的用户程序的部分语句即可。
可编程控制器自问世以来,以其可靠性高、抗干扰能力强、组合灵活、编程简单、维护方便等独特优势被日趋广泛地应用于国民经济的各个控制领域,其应用深度和广度已成为一个国家工业先进水平的重要标志。
1.1.2可编程控制器的产生和发展过程
可编程控制器产生于20世纪60年代末期,当时美国的汽车制造工业竞争十分激烈,各生产厂家为适应市场不断更新汽车型号,要求相应的加工生产线亦随之改变,整个继电接触器顺序控制系统也就要重新设计和配置。
这样不但造成设备的浪费,而且新系统的安装、调试也十分费时。
为了尽可能减少重新设计继电器控制系统和接线所需的成本和时间,1968年美国最大的汽车生产商——通用汽车公司(GM)向全球招标开发研制新型的工业控制装置取代继电控制装置,制定10项招标的技术要求,即:
(1)编程简单方便,可在现场修改程序。
(2)硬件维护方便,采用插件式结构。
(3)可靠性要高于继电器控制装置。
(4)体积小于继电器控制装置。
(5)可将数据直接送入管理计算机。
(6)成本上可与继电器控制装置竞争。
(7)输入可以是交流115V。
(8)输出为交流115V,2A以上,能直接驱动电磁阀。
(9)扩展时,原有系统只需做很小的改动。
(10)用户程序存储器容量至少可以扩展到4KB。
1969年美国数字设备公司(DEC)根据这些招标技术指标,研制了第一台可编程控制器,投入通用汽车公司的生产线过程控制系统中,取得了极佳的效果,从此开创了可编程控制器的新纪元。
1971年,日本从美国引进了这项技术,并很快研制成了日本第一台可编程控制器。
1973年,欧洲也研制出了可编程控制器并在工业领域开始使用。
我国从1974年开始研制,并于1977年开始工业应用.
由于早期的可编程控制器是用来取代继电器控制的,其控制功能主要是逻辑运算、计时、计数等顺序控制,因此人们称之为可编程控制器,简称PLC。
20世纪70年代末到80年代初,随着微电子技术的发展,微处理技术日趋成熟,使可编程控制器的处理速度大为提高,同时增加了许多特殊的功能,如数值运算、函数运算、查表等,使得可编程控制器不仅可以进行逻辑控制,而且还可以对模拟量进行控制。
因此,美国电器制造商协会NEMA(NationalElecticalManufacturersAssociation)将其正式命名为PC(ProgrammableController)。
后来,为区别个人计算机的简称,可编程控制器命名为PLC(ProgrammableLogicController)。
目前,世界著名的电气自动化企业几乎都生产可编程控制器。
可编程控制器已作为一个独立的工业设备被列入生产中,并成为当代电控装置的主导。
1.2可编程控制器的基本组成
PLC的类型繁多,功能和指令系统也存在一定程度上的差异,但就其结构和组成原理则大同小异。
PLC的实质就是一个计算机控制系统,属于过程控制计算机的一个分支,只不过它比一般的计算机具有更强的与工业过程相连接的接口和更直接的适用于控制要求的编程语言。
可编程器控制器的组成与计算机控制系统十分相似,通常由主机、输入/输出接口、电源扩展器接口和外部设备接口等几个主要部分组成。
PLC的硬件系统结构如图1-1所示:
图1-1PLC的硬件系统结构
一直到现在的现场总线控制系统,PLC更是其中的主角,其PLC的各组成元素的构成及功能:
(1)CPU的构成及功能。
CPU是PLC的核心,起神经中枢的作用,主要由运算器、控制器、寄存器及实现它们之间联系的数据、控制及状态总线构成,CPU单元还包括外围芯片、总线接口及有关电路。
每套PLC至少有一个CPU,它按PLC的系统程序赋予的功能接收并存贮用户程序和数据,用扫描的方式采集由现场输入装置送来的状态或数据,并存入规定的寄存器中,同时,诊断电源和PLC内部电路的工作状态和编程过程中的语法错误等。
进入运行后,从用户程序存储器中逐条读取指令,经分析后再按指令规定的任务产生相应的控制信号,去指挥有关的控制电路。
(2)I/O模块。
PLC与电气回路的接口,是通过输入输出部分(I/O)完成的。
I/O模块集成了PLC的I/O电路,其输入暂存器反映输入信号状态,输出点反映输出锁存器状态。
输入模块将电信号变换成数字信号进入PLC系统,输出模块相反。
I/O种类有开关量输入(DI),开关量输出(DO),模拟量输入(AI),模拟量输出(AO)等。
(3)存储器。
PLC的存储器可分为系统程序存储器和用户程序存储器,而用户程序存储器又包括用户程序存储区和用户数据存储区内存。
系统程序存储器通常采用ROM或EPROM芯片存储器,用于存放PLC生产厂商永久存储的程序和指令,称为监控程序;用户程序存储区主要存放用户已编制好的程序或正在调试的应用程序,一般采用EPROM或EEPROM存储器,用户可擦除重新编程;用户数据存储区通常采用RAM存储器,为防止掉电时信息的丢失,有后备电源作保护,用于存储PLC工作过程中经常变化,需要随机存取一些数据,数据存储区包括输入/输出数据映像区、定时器/计数器预置数和当前值数据。
(4)电源模块。
PLC电源用于为PLC各模块的集成电路提供工作电源。
同时,有的还为PLC内部提供5V直流电和为输入输出端及各种传感器提供24V直流电。
电源输入类型有:
交流电源(220VAC或110VAC),直流电源(常用的为24VAC)。
(5)底板或机架。
大多数模块式PLC使用底板或机架,其作用是:
电气上,实现各模块间的联系,使CPU能访问底板上的所有模块;机械上,实现各模块间的连接,使各模块构成一个整体。
(6)PLC系统的其它设备。
编程设备:
编程器是PLC开发应用、监测运行、检查维护不可缺少的器件,用于编写程序、对系统作一些设定、监控PLC及PLC所控制的系统的工作状况,但它不直接参与现场控制运行。
某些PLC也配有手持型编程器,目前一般由计算机(运行编程软件)充当编程器。
人机界面:
最简单的人机界面是指示灯和按钮,目前液晶屏(或触摸屏)式的一体式操作员终端应用越来越广泛,由计算机(运行组态软件)充当人机界面也非常普及。
输入输出设备:
用于永久性地存储用户数据,如EPROM、EEPROM写入器、条码阅读器,输入模拟量的电位器,打印机等。
(7)PLC的通信联网。
依靠先进的工业网络技术可以迅速有效地收集、传送生产和管理数据。
因此,网络在自动化系统集成工程中的重要性越来越显著,甚至有人提出"网络就是控制器"的观点说法。
PLC具有通信联网的功能,它使PLC与PLC之间、PLC与上位计算机以及其他智能设备之间能够交换信息,形成一个统一的整体,实现分散集中控制。
多数PLC具有RS-232接口,还有一些内置有支持各自通信协议的接口。
PLC的通信,还未实现互操作性,IEC规定了多种现场总线标准,PLC各厂家均有采用。
对于一个自动化工程(特别是中大规模控制系统)来讲,选择网络非常重要的。
首先,网络必须是开放的,以方便不同设备的集成及未来系统规模的扩展;其次,针对不同网络层次的传输性能要求,选择网络的形式,这必须在较深入地了解该网络标准的协议和机制的前提下进行;再次,综合考虑系统成本、设备兼容性、现场环境适用性等具体问题,确定不同层次所使用的网络标准。
1.3PLC工作原理及其特点
1.3.1PLC的工作原理
PLC在结构形式上虽然与微型计算机有许多相同之处,但由于PLC在工业中使用对逻辑运算及稳定性要求相应较高,所以PLC一般不采用微型计算机等待命令和中断工作方式,而是采用不断循环的顺序扫描的工作方式,即PLC工作时对用户程序反复循环扫描,逐条地解释用户程序,并加以处理。
每一次扫描所用的时间即扫描时间称为扫描周期或工作时间。
PLC的一个扫描周期必经输入采样、程序执行和输出刷新三个阶段。
顺序扫描方式简单直观,便于程序设计和PLC自身的检查。
在PLC的不断循环顺序扫描过程中,某一个输出继电器线圈被接通或断开,该线圈的所有常开和常闭触电不会像继电接触控制器控制系统中继电器那样立即动作,而必须等到扫描到该触点时才会动作。
PLC采用循环扫描工作方式的工作过程一般包括6个阶段:
以故障诊断和处理为主的公共操作、与编程器等的通信处理、输入扫描、执行用户程序、输出处理、响应外设。
1.3.2PLC的特点PLC的特点如下:
(1)抗干扰能力强、可靠性高。
(2)通用性强,使用方便。
(3)程序设计简单,易学易懂。
(4)采用模块化结构,系统组合灵活方便。
(5)设计、施工、调试的周期短。
(6)安装简便,调试方便,维护工作量小。
(7)对生产工艺改变适应性强,可进行柔性生产。
1.4PLC的应用
初期的PLC主要在以开关量居多的电气顺序控制系统中使用,但在20世纪90年代后,PLC也被广泛地在流程工业自动化系统中使用,应用面越来越广。
目前,世界上有200多厂家生产300多品种PLC产品,应用在汽车、粮食加工、化学/制药、金属/矿山、纸浆/造纸等行业。
根据PLC的特点,可以将应用形式归纳为如下几类种类型:
(1)开关逻辑控制。
(2)模拟量控制。
(3)顺序(步进)控制。
(4)定时控制。
(5)计数控制。
(6)闭环过程控制。
(7)数据处理。
(8)通信和联网。
第2章PLC设计方案分析
2.1PLC类型的选取
2.1.1西门子S7-200系列简介
S7-200系列PLC是SIEMENS公司推出的一种小型PLC。
以紧凑的结构、良好的扩展性、强大的指令功能、低廉的价格,已经成为当代各种小型控制工程的理想控制器。
S7-200PLC包含了一个单独的S7-200CPU和各种可选择的扩展模块,可以十分方便地组成不同规模的控制器。
其控制规模可以从几点到几百点。
S7-200PLC可以方便地组成PLC-PLC网络和微机-PLC网络,从而完成规模更大的工程。
S7-200的STEP7-Micor/WIN32编程软件可以方便地在Windows环境下对PLC编程、调试、监控,使得PLC的编程更加方便、快捷。
可以说,S7-200可以完美地满足各种小规模控制系统的要求。
此外,丰富的CPU类型和电压等级使其在解决用户的工业自动化问题时,具有很强的适应性。
图2-1展示了一台S7-200MicroPLC的CPU22*系列PLC的CPU外型图。
目前S7-200系列PLC主要有CPU221、CPU222、CPU224和CPU226四种CPU,其外观结构基本相同。
这四种CPU的特点如下:
(1)CPU221。
该主机集成6输入/4输出共10个数字量I/O点(无I/O扩展能力)、6KB程序和数据存储空间、4个独立的30kHz高速计数器、2路独立的20kHz高速脉冲输出、1个RS485通信/编程口(具有PPI通信协议、MPI通信协议和自由方式通信能力)。
适用于小数点控制系统。
(2)CPU222。
该主机集成8输入/6输出共14个数字量I/O点、6KB程序和数据存储空间。
与CPU221相比,增加了扩展能力,可连接2个扩展模块,可扩展最多64个数字量I/O点或8路模拟量I/O点。
(3)CPU224。
该主机集成14输入/10输出共24个数字量I/O点、13KB程序和数据存储空间、6个独立的30kHz高速计数器、2路独立的20kHz高速脉冲输出,具有PID控制器。
与CPU222相比,扩展能力大为加强,即可连接7个扩展模块,最大扩展至168个数字量I/O点或35路模拟量I/O点。
(4)CPU226。
该主机在CPU224的基础上功能进一步增强:
13KB程序和数据存储空间、40个数字量I/O点、最大扩展至248个数字量I/O点或35路模拟量I/O点;增加了一个通信口,可以分别进行设置,同时与两个设备进行通信互不干扰,,通信功能大大加强。
CPU226适用于较高要求的复杂的中小型控制系统。
S7-200PLC的I/O扩展模块有:
(1)输入扩展模块EM221:
共有3种产品,即8点和16点DC、8点AC。
(2)输出扩展模块EM222:
共有5种产品,即8点DC和4点DC、8点AC、8点继电器和4点继电器。
(3)输入/输出混合模块EM223:
共有6种产品。
其中DC输入/DC输出的有3种,DC输入/继电器输出的有三种,它们对应的输入/输出点数分别为4点、8点和16点。
(4)模拟量输入扩展模块EM231。
(5)模拟量输出扩展模块EM232。
(6)模拟量输入/输出扩展模块EM235。
S7-200CPU模块包括一个中央处理器单元(CPU)、电源以及数字量I/O点,这些都被集成在一个紧凑、独立的设备中。
图2-1S7-200CPU外型图
1.CPU负责执行程序和存储数据,以便对工业自动控制任务或过程进行控制。
2.输入和输出是系统的控制点,输入部分从现场设备(例如传感器或开关)中采集信号;输出部分则控制泵、电机以及工业过程中的其它设备。
3.电源向CPU及其所连接的各种模块提供电力。
4.通讯端口允许将S7-200CPU同编程器或一些设备连接起来。
5.状态信号灯显示了CPU的工作模式(运行或停止),本机I/O点的当前状态,以及检查出来的系统错误。
6.通过扩展模块可以增加CPU的I/O点数(CPU221不可以扩展)。
7.通过扩展模块可以提供其通讯功能。
8.一些CPU具有内置实时时钟,其它CPU需要实时时钟卡。
9.EEPROM卡可以存储CPU程序,也可以将一个CPU中的程序传送到另一个CPU中。
10.通过可选的插入式电池盒可延长RAM中的数据存储时间。
图2-2展示了一个基本的S7-200MicroPLC。
它包括一个S7-200CPU模块,一台个人计算机(PC),STEP7-Micro/win32编程软件,以及一条通讯电缆。
图2-2S7-200MicroPLC系统的组成
2.1.2西门子S7-200系列与三菱FX系列的比较
(1)三菱的编程软件从早期的FXGPWIN到近期的GX8.0,和所有的日系品牌一样,该软件的编程思路是自上而下的单一纵向结构;而西门子的MicroWIN则是纵向和横向兼备的结构,而且子程序支持局部变量,相同的功能只需要编一次程序即可,大大减少了开发难度和时间。
(2)S7-200一直以来支持强大的浮点运算,编程软件直接支持小数点输入输出;而三菱直至近年推出的FX3U系列才具有此功能,以前的FX2N系列的浮点功能都是假的。
(3)S7-200的模拟量输入输出程序非常简单方便,AD、DA值可以不需编程直接存取的;三菱的FX2N及其以前的系列都需要非常繁琐的FROMTO指令。
2.1.3PLC类型的选取
通过以上对S7-200的了解及其与三菱的比较,这次设计我选择S7-200系列的PLC。
从工艺要求中可以看出,从控制方式上需要3个起动按钮,分别完成自动方式I0.0、单动方式I0.1和手动方式I0.2的起动,还需要一个停止按钮I0.3用来处理在任何情况下的停止运行。
机械手运动的限位开关有4个,高位限位开关I0.4、低位限位开关I0.5、左位限位开关I0.6和右位限位开关I0.7。
手动控制输入信号有5个按钮组成,下降按钮I1.0、上升按钮I1.1、夹紧按钮I1.2、左移按钮I1.3和右移按钮I1.4。
工作台A上有工件检测光耦合器VLC的输入信号I1.5,共育14个输入信号。
输出信号有机械手下降驱动信号Q0.0、上升信号Q0.1、右移信号Q0.2、左移信号Q0.3和机械手夹紧驱动信号Q0.4,共有5个输出信号。
该系统需要输入14点,输出5点。
可选择S7-200系列的C