干熄焦工艺概况.docx
《干熄焦工艺概况.docx》由会员分享,可在线阅读,更多相关《干熄焦工艺概况.docx(31页珍藏版)》请在冰豆网上搜索。
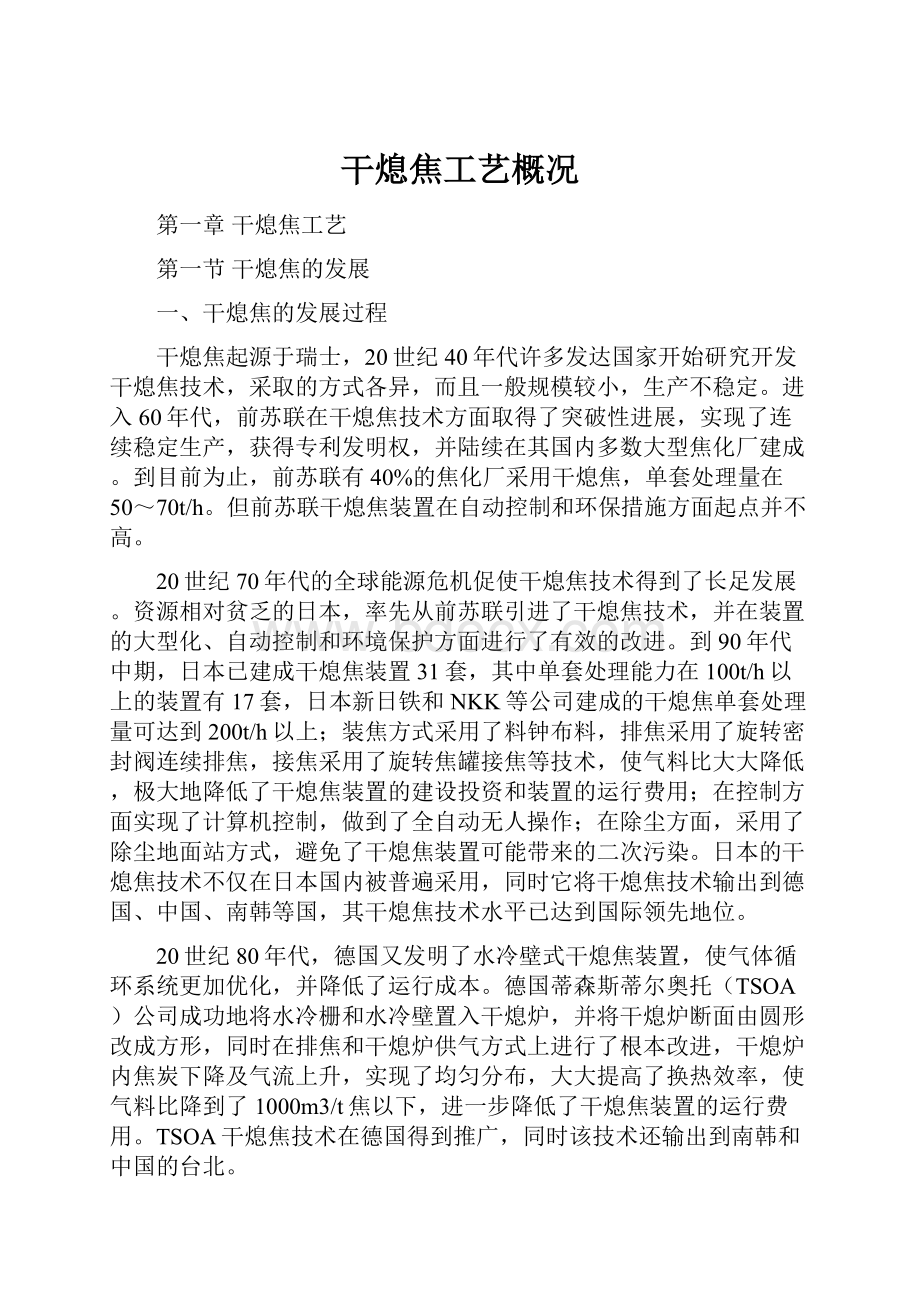
干熄焦工艺概况
第一章干熄焦工艺
第一节干熄焦的发展
一、干熄焦的发展过程
干熄焦起源于瑞士,20世纪40年代许多发达国家开始研究开发干熄焦技术,采取的方式各异,而且一般规模较小,生产不稳定。
进入60年代,前苏联在干熄焦技术方面取得了突破性进展,实现了连续稳定生产,获得专利发明权,并陆续在其国内多数大型焦化厂建成。
到目前为止,前苏联有40%的焦化厂采用干熄焦,单套处理量在50~70t/h。
但前苏联干熄焦装置在自动控制和环保措施方面起点并不高。
20世纪70年代的全球能源危机促使干熄焦技术得到了长足发展。
资源相对贫乏的日本,率先从前苏联引进了干熄焦技术,并在装置的大型化、自动控制和环境保护方面进行了有效的改进。
到90年代中期,日本已建成干熄焦装置31套,其中单套处理能力在100t/h以上的装置有17套,日本新日铁和NKK等公司建成的干熄焦单套处理量可达到200t/h以上;装焦方式采用了料钟布料,排焦采用了旋转密封阀连续排焦,接焦采用了旋转焦罐接焦等技术,使气料比大大降低,极大地降低了干熄焦装置的建设投资和装置的运行费用;在控制方面实现了计算机控制,做到了全自动无人操作;在除尘方面,采用了除尘地面站方式,避免了干熄焦装置可能带来的二次污染。
日本的干熄焦技术不仅在日本国内被普遍采用,同时它将干熄焦技术输出到德国、中国、南韩等国,其干熄焦技术水平已达到国际领先地位。
20世纪80年代,德国又发明了水冷壁式干熄焦装置,使气体循环系统更加优化,并降低了运行成本。
德国蒂森斯蒂尔奥托(TSOA)公司成功地将水冷栅和水冷壁置入干熄炉,并将干熄炉断面由圆形改成方形,同时在排焦和干熄炉供气方式上进行了根本改进,干熄炉内焦炭下降及气流上升,实现了均匀分布,大大提高了换热效率,使气料比降到了1000m3/t焦以下,进一步降低了干熄焦装置的运行费用。
TSOA干熄焦技术在德国得到推广,同时该技术还输出到南韩和中国的台北。
干熄焦工艺发展至今,虽然出现了不同的形式,但基本工艺流程大同小异,只是在装焦、排焦、循环气体除尘等方面有所区别。
具有代表性的有德国TSOA公司设计的干熄焦工艺和日本新日铁设计的干熄焦工艺,这两种典型的干熄焦工艺在消化吸收前苏联干熄焦成熟技术的基础上都有所创新,形成各自的特点,并使干熄焦技术及其应用达到了较先进的水平。
中国的鞍山焦耐院和首钢设计院,以及武钢、宝钢、首钢在吸收消化日本干熄焦技术方面作了一些有益的工作,并积累了较为丰富的经验。
目前,全世界正在生产的干熄焦装置约130套,各国和地区干熄焦装置的建设情况见表1—1。
二、国内干熄焦技术的现状
我国自20世纪80年代初,宝钢一期从日本引进干熄焦至今,现有六个厂投产了干熄焦,各厂的使用状况也存在着一定差异。
国内干熄焦装置建设情况见表1—2。
(一)各厂的干熄焦状况
1.宝钢干熄焦
宝钢为配合12×50孔(6m)焦炉,共建了12套75t/h规模的干熄焦装置,年处理焦炭510万吨,共分三期建设。
一期4×75t/h干熄焦装置于1985年5月建成设产,二期、三期分别于1991年6月和1997年12月建成设产。
一期干熄焦装置是从日本全套引进的;二期干熄焦装置是在消化吸收一期的基础上,主要由我国自己设计建成的,设备国产化率占设备总重的80%,部分关键部件从日本引进;三期除极少数关键部件从日本引进外,绝大部分设备已国产化,国产化率达到了90%以上。
宝钢只有干法熄焦,不用湿法熄焦作备用,采用“三开一备”的生产方式。
表1—1世界各国和地区干熄焦装置建设情况表
序号
设计
建设国家或地区
数量
1
新日铁
日本
16
南韩
3
中国
9
德国
1
2
NKK
日本
11
3
石川岛播磨
日本
12
南韩
2
4
蒂森斯蒂尔奥托
德国
3
南韩
2
中国台北
1
5
乌克兰
前苏联国家
27
中国
6
印度
12
罗马尼亚
5
波兰
6
芬兰
2
6
鞍山焦耐院
中国
4
7
意大利
巴西
5
8
罗德洛基
芬兰
1
合计
128
2.浦东煤气厂干熄焦
浦东煤气厂为配合年产56万吨焦炭的焦炉熄焦,1984年从前苏联(乌克兰)全套引进2×70t/h规模的干熄焦装置,由前苏联国立焦化设计院负责全套干熄焦装置核心设计,鞍山焦耐院和上海化工研究院参与了干熄焦的配套设计,并由鞍山焦耐院负责干熄焦工程的设计总承包。
工程于1991年12月开工建设,1994年12月建成设产。
该套干熄焦装置设备全套从前苏联引进,并保留了湿法熄焦作为备用。
3.济钢干熄焦
济钢为配合年产110万吨焦炭的焦炉熄焦,1994年从前苏联引进了2×70t/h规模的干熄焦装置,由前苏联国立焦化设计院与济钢设计院共同设计。
在设备方面采取部分引进,部分合作制造的方式,工程于1996年开工,1999年3月建成投产。
投产后发现苏联技术可靠性不高,达产时间较长。
该装置与浦东煤气厂的干熄焦装置一样,自动化水平并不高,也保留了湿法熄焦作为备用。
4.首钢干熄焦
首钢一期1×65t/h规模的干熄焦装置,是利用日本政府的绿色援助计划建成的一套干熄焦装置,其主体设备由日本供给,辅助设备由首钢自己采购。
该装置设计工作由新日铁与首钢设计院共同完成,工程于1999年动工,2001年1月投产。
首钢干熄焦装置投产后运行可靠,而且自动化控制水平和环保效果都比较理想。
首钢也保留了湿法熄焦作备用。
表1—2国内干熄焦装置建设情况
项目内容
宝钢一期
宝钢二期
宝钢三期
济钢
浦东煤气厂
首钢
武钢
马钢
处理能力
4×75t/h
4×75t/h
4×75t/h
2×70t/h
2×70t/h
1×65t/h
1×140t/h
1×125t/h
技术来源
新日铁
新日铁
新日铁
乌克兰
乌克兰
新日铁
新日铁
华泰
基本设计
新日铁
新日铁
焦耐院
哈尔克夫设计院
哈尔克夫设计院
新日铁
新日铁
华泰
详细设计
新日铁
焦耐院
焦耐院
济钢设计院转化设计
焦耐院转化设计
新日铁
焦耐院转化设计
华泰
气料比(m3/t焦)
1500
1500
1500
2000
1750
1500
1200
主要设备设计制造情况
提升机
引进
引进
大部分引进
买进制造图国内制造
引进
引进
引进
国产
锅炉
引进
国产
国产
国内外联合设计国内制造关键部件引进
引进
引进
国产
国产
电机车
引进
引进
引进
引进
引进
引进
引进一台国产一台
国产
鼓风机
引进
引进
引进
国产
引进
引进
引进
引进
装入装置
引进
引进
国外方案设计,焦耐院详细设计,国内制造关键部件引进
买进制造图,国内制造
引进
引进
国产
国产
排焦装置
引进
引进
国外方案设计,焦耐院详细设计,国内制造关键部件引进
引进
引进
引进
引进
引进
供气装置
引进
焦耐院设计国内制造
焦耐院设计国内制造
引进
引进
引进
国产
国产
装备水平
控制方式
PLC+DCS
PLC+DCS
三电一体化
PLC+DCS
PLC+DCS
PLC+DCS
三电一体化
三电一体化
软件编制
国外
焦耐院
焦耐院
济钢设计院
国外
国外
武钢
华泰
投产时间(年)
1985
1991
1997
1999
1994
2001
2003
2004
投资(亿元)
未单独计算
未单独计算
4.5
2.3
1.0
5.武钢干熄焦
武钢7、8号焦炉为2×55孔6m焦炉,其干熄焦装置设计能力为1×140t/h,该装置由日本作核心设计,鞍山焦耐院作转接设计。
该项目为国家经贸委的消化吸收项目,是目前国内单套处理能力最大的干熄焦装置。
干熄焦关键设备从日本引进,部分设备由日方设计和监制,国内厂家制造,其中干熄焦的自动控制部分由武钢自行设计,工程于2002年10月动工,2003年12月建成投产,2004年5月份该装置已全面达产。
武钢7、8号焦炉干熄焦仍保留了湿法熄焦作备用。
6.马钢干熄焦
马钢5、6号焦炉为2×50孔6m焦炉,所配置的干熄焦装置能力为1×125t/h,该装置由鞍山焦耐院总承包,部分关键设备从日本、德国、美国引进,其它设备由国内制造,是目前国内干熄焦装置中国产化设备最多的一套,于2004年4月建成投产,也保留湿法熄焦备用。
随着国家环保法规的不断完善和全民环保意识的提高,发展干熄焦势在必行,各大钢厂筹建6m以上焦炉都要建设与之配套的干熄焦。
(二)过去干熄焦装置推广难的原因
自上世纪80年代宝钢一期引进日本干熄焦装置至今已近20年,但这期间干熄焦技术在我国却未能大量推广,其主要原因是:
1.规格单一
各企业根据各自需要自行引进,没有进行有组织的协调和整合,造成重复引进,资金投入多,但没能解决根本问题,使我国的单套干熄焦装置处理能力一直徘徊在70t/h、75t/h的中型规模水平上,规格单一,不能按照焦化厂的生产规模经济合理地配置干熄焦装置。
以包头钢铁公司5、6号焦炉为例,其生产能力为年产干全焦100万吨,理应配置126t/h的干熄焦装置,但由于受到我国现有干熄焦装置处理能力单一的限制,又不合适地考虑了设备的热态备用,而设计采用3×75t/h干熄焦装置,其实际处理能力超过实际需要近80%,结果是投资高、效益差,导致项目夭折。
2.工程投资高
过去没有专业制造厂介入干熄焦设备的消化吸收,设备未能实现国产化。
例如提升机、循环风机、电机车、排焦及装入装置等设备,建干熄焦就要引进;再加上干熄焦,控制系统复杂,要引进大量的电气和自控设备,导致工程投资居高不下。
3.能源价格不合理
长期以来我国能源价格一直处于比较低的状态,使干熄焦节能的经济效益不明显,造成投资收益率低,回收期长。
但按照现在的能源价格,干熄焦回收能源所创造的效益是每t焦炭10元,比较可观。
4.没有考虑干熄焦的延伸效益
过去因钢铁企业内部管理问题,前后工序之间没有严格进行成本核算,未对焦炭质量对炼铁经济效益的影响进行单独考核,致使干熄焦对焦炭质量的提高未能在炼铁获得的经济效益中体现出来,这是造成干熄焦工程经济效益差的另一个原因。
实际上每t干熄焦焦炭对炼铁系统带来的效益约14元。
(三)干熄焦的发展方向
随着我国国民经济的不断发展,能源价格已逐步趋向合理,同时,目前钢铁企业内部已经实行成本核算、成本否决制度。
因此,如果能够有效地降低干熄焦装置的建设投资,这项技术就一定能够在我国得到广泛应用,并取得可观的经济效益和社会效益。
从前面的论述不难看出,降低干熄焦投资的关键,一是干熄焦装置系列化,使规模配置经济合理。
二是干熄焦技术和设备全面国产化。
1.干熄焦装置系列化,使规模配置经济合理
宝钢一期引进的干熄焦投产以后,我国曾片面地追求100%干熄,即干熄焦的备用装置也必须是干熄,结果造成基建投资大大增加,尤其是在干熄焦装置大型化后,投资增加更加惊人。
例如,100万吨焦化厂配套干熄焦装置,采用75t/h干熄焦装置,以干熄焦备用,需建3×75t/h干熄焦装置,能力将增大二分之一;采用126t/h干熄焦装置,以干熄焦备用,能力将增大一倍。
其实,干熄焦完全可以用湿熄焦备用,因为,随着对干熄焦所用耐火材料的不断开发,装置的检修时间间隔也越来越长,日本已达到每~年检修一次,一次只有20天左右,所以以干熄焦为备用的意义越来越小。
日本、德国等经济发达国家近些年在设计干熄焦装置时,也采用湿熄焦备用,以减少基建投资。
92年底投产的德国凯泽斯图尔(Kaiserstuhl)焦化厂是世界最现代化、也是环保和装备水平最高的焦化厂,该厂配备了一套世界上最大的250t/h干熄焦装置,也是采用湿熄焦作为备用(该厂现已停产)。
世界上干熄焦技术发展最快的日本,85年以后所建干熄焦均以湿熄焦作为备用。
干熄焦装置系列化是至关重要的。
规模单一,不能形成系列,就不能按照焦炉的不同规模经济合理地配置干熄焦装置。
还以100万吨焦化厂为例,如果干熄焦装置处理能力不成系列,只能配置我国当时已掌握的75t/h干熄焦装置,形成2×75t/h一组干熄焦装置,即使以湿熄焦作备用,其处理能力也将浪费约20%。
对70~80万吨焦化厂,仍配置2×75t/h一组干熄焦装置,处理能力将浪费约60%。
因此,干熄焦装置必须根据生产能力形成系列,也就是目前的75t/h处理能力是不够的,必须向大型化发展,其处理能力至少应满足110万吨焦化厂要求,即开发140t/h干熄焦装置,2003年底武钢7、8号焦炉干熄焦投产后,我国才初步形成处理能力70~140t/h系列干熄焦装置。
表1—3也反应出日本干熄焦装置配置的系列化及处理能力的大型化。
表1—3日本干熄焦装置现状表
公司名称
生产厂
所服务的焦炉
干熄焦处理能力(t/h)
投产年代(年.月)
新日本制铁
八幡
,4
1×175
室兰
,6
1×108
广田
,4
1×110
名古屋
1×129
,2
1×106
大分
,4
1×180
,2
1×190
新日铁化学
君津
—3
3×110
—
,5
1×170
NKK
京浜
5×70
—12
3×70
福山
1×125
1×200
川崎制铁
千业
3×56
水岛
,4
2×100
—9
,6
1×130
住友金属工业
鹿岛
1×130
1×150
A-D
1×195
关西热化学
加古川
,2
1×140
中山制铁所
船町
1×60
2.干熄焦技术和设备要全面国产化
我国干熄焦装置设备国产化比例较高的宝钢三期,只有提升机、循环风机、电机车、排焦装置的部分部件和电气、仪表元件从国外引进。
但是,这部分所占投资比例为总设备投资的一半左右。
这几件设备中,电机车属专用设备,其特点是起动速度快、走行速度快、对位要求准确;循环风机国内目前尚无可选产品,要求耐磨性好,并能在较高温度下长期连续稳定运行;提升机是干熄焦专用设备,其特点提升速度快、走行速度快、对位准确、自动化程度高;排焦装置的部分部件主要是由于以前没有用过,选国内设备没把握。
就我国目前的机械制造水平而言,只要国家投入一定人力、物力、财力,将有相当实力的起重机厂、风机厂、锅炉制造厂(在干熄焦装置大型化之后需要进一步消化吸收)及炼焦专用设备制造厂有效地组织起来,通过引进,进行消化吸收和创新,这些设备实现国产化不成问题。
武钢7、8号焦炉干熄焦的建设就吸收了国内一些有实力机电厂家加盟,自动控制方面由武钢自已设计,武钢7、8号焦炉干熄焦的投产成功为我国干熄焦技术和设备全面实现国产化作出了重要的贡献。
第二节干熄焦的原理
所谓干熄焦,是相对湿熄焦而言的,是指采用惰性气体将红焦降温冷却的一种熄焦方法。
在干熄焦过程中,红焦从干熄炉顶部装入,低温惰性气体由循环风机鼓入干熄炉冷却段红焦层内,吸收红焦显热,冷却后的焦炭从干熄炉底部排出,从干熄炉环形烟道出来的高温惰性气体流经干熄焦锅炉进行热交换,锅炉产生蒸汽,冷却后的惰性气体由循环风机重新鼓入干熄炉,惰性气体在封闭的系统内循环使用。
干熄焦在节能、环保和改善焦炭质量等方面优于湿熄焦。
一、湿熄焦的特点
煤在炭化室炼成焦炭后,应及时从炭化室推出,红焦推出时温度约为1000℃。
为避免焦炭燃烧并适于运输和贮存,不能直接送往高炉炼铁,必须将红焦温度降低。
一种熄焦方法是采用喷水将红焦温度降低到300℃以下,即通常所说的湿熄焦。
传统湿熄焦系统由带喷淋水装置的熄焦塔、熄焦泵房、熄焦水沉淀池以及各类配管组成,熄焦产生的蒸汽直接排放到大气中。
传统湿熄焦的优点是工艺较简单,装置占地面积小,基建投资较少,生产操作较方便。
但湿熄焦的缺点也非常明显,其一,湿熄焦浪费红焦大量显热,每炼1t焦炭消耗热量约为~,其中湿熄焦浪费的热量为,约占总消耗热量的45%;其二,湿熄焦时红焦急剧冷却会使焦炭裂纹增多,焦炭质量降低,焦炭水份波动较大,不利于高炉炼铁生产;其三,湿熄焦产生的蒸汽夹带残留在焦炭内的酚、氰、硫化物等腐蚀性介质,侵蚀周围物体,造成周围大面积空气污染,而且随着熄焦水循环次数的增加,这种侵蚀和污染会越来越严重;其四,湿熄焦产生的蒸汽夹带着大量的粉尘,通常达200~400g/t焦,既污染环境,又是一种浪费。
为解决湿熄焦存在的问题,各国焦化工作者进行了不懈的努力,对湿熄焦装置及湿熄焦工艺不断进行改进,改进的湿熄焦工艺主要有以下两种:
(一)低水份熄焦
低水份熄焦系统主要由工艺管道、水泵、高位水槽、一点定位熄焦车以及控制系统等组成。
在低水份熄焦过程中,通过专门设计的喷头以及不同的水压往一点定位熄焦车内喷水使红焦熄灭。
水流经过焦炭固体层后,再经过专门设计的凹槽或孔流出,足够大的水压使水流迅速通过焦炭层,达到熄焦车的底板,并快速流出熄焦车。
当高压水流经过焦炭层时,短期内产生大量的蒸汽,瞬间充满了整个焦炭层的上部和下部,使焦炭窒息。
低水份熄焦工艺在熄焦初期的10~20s内使用低压水,在熄焦后期的50~80s内采用高压水来代替传统湿熄焦的喷淋式分配水流。
熄焦水源由高位水槽提供,高位水槽出来的熄焦水由一台小型的PLC机控制气动阀门的开度自动控制其水压和流量。
低水份熄焦工艺可节约熄焦用水30%~40%;同时还可以降低并稳定焦炭水份,从而有利于稳定高炉的生产;此外,还可以降低熄焦过程中随蒸汽带走的粉尘排放量,传统湿熄焦粉尘排放量为200~400g/t焦,而低水份熄焦粉尘排放量可降为50g/t焦左右。
低水份熄焦工艺流程图见图1-1。
图1-1低水份熄焦工艺流程图
图1-2压力蒸汽熄焦工艺流程图
(二)压力蒸汽熄焦
压力蒸汽熄焦系统主要由工艺管道、水泵、熄焦槽、旋风分离器、余热锅炉以及控制系统等组成。
在压力蒸汽熄焦过程中,红焦由炭化室推入下部具有栅板的熄焦槽内,装满红焦的熄焦槽盖好后移至熄焦站,然后有控制地通入熄焦水,水从熄焦槽上部的盖子处通入,水压和水量由一台小型的PLC控制。
水与红焦接触产生的蒸汽强制向下流动而穿过焦炭层,使焦炭进一步冷却,同时所夹带的水滴进一步气化。
采用压力蒸汽熄焦可得到压力为的水蒸气和一定数量的水煤气,该气体由熄焦槽下部引出,经旋风分离器除去所夹带的焦粉后,可送至余热锅炉回收热量并分离出水煤气。
压力蒸汽熄焦工艺流程图见图1—2。
上述两种改进后的湿熄焦工艺,虽然在某些方面缓解了传统湿熄焦的不足,但还不能从根本上解决浪费能源、污染环境以及降低焦炭质量等方面的问题。
二、干熄焦的工艺流程
干熄焦系统主要由干熄炉、装入装置、排焦装置、提升机、电机车及焦罐台车、焦罐、一次除尘器、二次除尘器、干熄焦锅炉系统、循环风机、除尘地面站、水处理系统、自动控制系统、发电系统等部分组成。
根据设计的不同,干熄焦系统包含的主要设备也不尽相同,比如德国TSOA设计的干熄焦就没有一次除尘器,其进锅炉的循环气体中粗颗粒焦粉的去除由干熄炉本体完成;有的干熄焦直接采用外供除盐水,因此省略了干熄焦除盐水生产这一环节,只是对外供除盐水进行除氧处理即可;有的干熄焦没有设计发电系统,锅炉产生的蒸汽经减温减压后直接并网使用;等等。
武钢7、8号焦炉干熄焦工艺采用日本新日铁的干熄焦技术,并在某些工艺及设备性能上进行了改进,其工艺流程图见图1—3、工艺布置图见图1—4。
除盐水
红焦
拦焦车
环型烟道
一次除尘器
纯水槽
旋转焦罐
焦罐台车
提升机
装入装置
预存段
冷却段
平板闸门
振动给料器
旋转密封阀
双岔溜槽
皮带输送机
锅炉
二次除尘器
循环风机
链式刮板机
焦粉仓
加湿搅拌机
链式刮板机
布袋除尘器
净化气体排放
锅炉给水泵
减温减压器
除氧器
给水预热器
除氧给水泵
热力管网
汽轮发电机
蒸汽放散
电
粉焦外运
蒸汽并网
给水预热器
斗式提升机
焦炭外运
除尘风机
焦炭
循环气体
烟气和粉尘
水蒸汽
图1-3武钢7、8号焦炉干熄焦工艺流程图
一次除尘器
旋转焦罐
焦罐台车
旋转密封阀
振动给料器
吹扫风机
给水预热器
除氧器
消音器
强制循环泵
二次除尘器
锅炉给水泵
焦粉收集设备
除盐水站
焦炭仓
除氧器循环泵
循环风机
除氧给水泵
水水换热器
焦粉仓
地面除尘站
自动润滑泵
预存段
冷却段
装入装置
水冷管
提升机
锅炉
纯水槽
图1-4武钢7、8号焦炉干熄焦工艺布置图
从炭化室推出的红焦由焦罐台车上的圆形旋转焦罐(有的干熄焦设计为方形焦罐)接受,焦罐台车由电机车牵引至干熄焦提升井架底部,由提升机将焦罐提升至提升井架顶部;提升机挂着焦罐向干熄炉中心平移的过程中,与装入装置连为一体的炉盖由电动缸自动打开,装焦漏斗自动放到干熄炉上部;提升机放下的焦罐由装入装置的焦罐台接受,在提升机下降的过程中,焦罐底闸门自动打开,开始装入红焦;红焦装完后,提升机自动提起,将焦罐送往提升井架底部的空焦罐台车上,在此期间装入装置自动运行将炉盖关闭。
装入干熄炉的红焦,在预存段预存一段时间后,随着排焦的进行逐渐下降到冷却段,在冷却段通过与循环气体进行热交换而冷却,再经振动给料器、旋转密封阀、双岔溜槽排出,然后由专用皮带运输机运出。
为便于运焦皮带系统的检修,以及减小因皮带检修给干熄焦生产带来的影响,皮带运输机一般设计有两套,一开一备。
冷却焦炭的循环气体,在干熄炉冷却段与红焦进行热交换后温度升高,并经环形烟道排出干熄炉;高温循环气体经过一次除尘器分离粗颗粒焦粉后进入干熄焦锅炉进行热交换,锅炉产生蒸汽,温度降至约160℃的低温循环气体由锅炉出来,经过二次除尘器进一步分离细颗粒焦粉后,由循环风机送入给水预热器冷却至约130℃,再进入干熄炉循环使用。
经除盐、除氧后约104℃的锅炉用水由锅炉给水泵送往干熄焦锅炉,经过锅炉省煤器进入锅炉汽包,并在锅炉省煤器部位与循环气体进行热交换,吸收循环气体中的热量;锅炉汽包出来的饱和水经锅炉强制循环泵重新送往锅炉,经过锅炉鳍片管蒸发器和光管蒸发器后再次进入锅炉汽包,并在锅炉蒸发器部位与循环气体进行热交换,吸收循环气体中的热量;锅炉汽包出来的蒸汽经过一次过热器、二次过热器,进一步与循环气体进行热交换,吸收循环气体中的热量后产生过热蒸汽外送。
干熄焦锅炉产生的蒸汽,送往干熄焦汽轮发电站,利用蒸汽的热能带动汽轮机产生机械能,机械能又转化成电能。
从汽轮机出来的压力和温度都降低了的饱和蒸汽再并入蒸汽管网使用。
经一次除尘器分离出的粗颗粒焦粉进入一次除尘器底部的水冷套管冷却,水冷套管上部设有料位计,焦粉到达该料位后水冷套管下部的格式排灰阀启动将焦粉排出至灰斗,灰斗上部设有料位计,焦粉到达该料位后灰斗下的排灰格式阀启动向刮板机排出焦粉。
从一次除尘器出来的循环气体含尘量约为10~12g/m3,流经锅炉换热后,进入二次除尘器进一步除去细颗粒的焦粉。
二次除尘器为多管旋风式除尘器,由进口变径管、内套筒、外套筒、旋风子、灰斗、壳体、出口变径管、防爆装置等组成。
灰斗设有上下两个料位计,焦粉料位达到上限时,灰斗出口格式排灰阀向灰斗下面的刮板机排出焦粉,焦粉料位达到下限时停止焦粉排出,以防止从负压排灰口吸入空气,影响气体循环系统压力平衡。
从二次