半导体工艺教案第十章平坦化.docx
《半导体工艺教案第十章平坦化.docx》由会员分享,可在线阅读,更多相关《半导体工艺教案第十章平坦化.docx(20页珍藏版)》请在冰豆网上搜索。
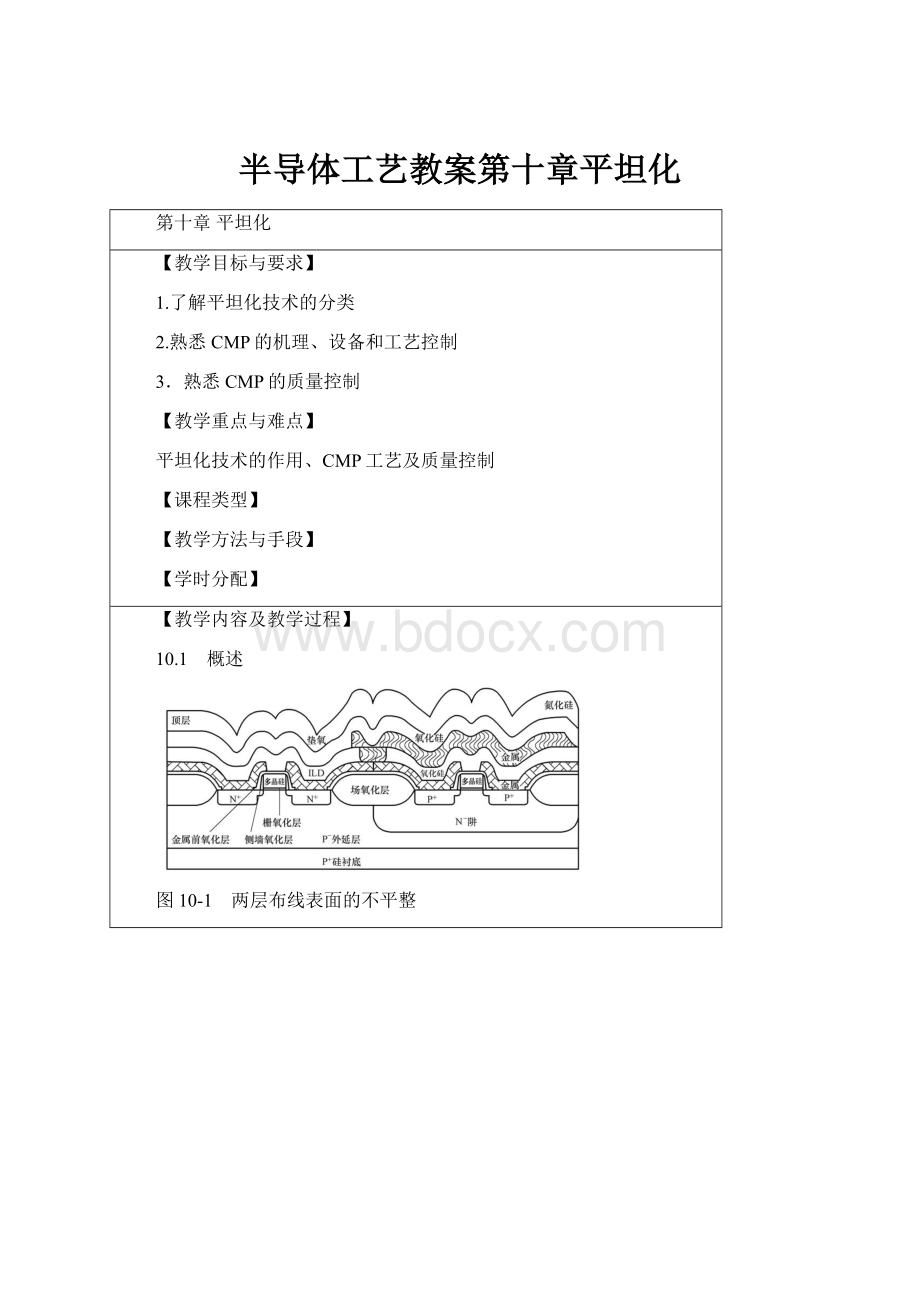
半导体工艺教案第十章平坦化
第十章平坦化
【教学目标与要求】
1.了解平坦化技术的分类
2.熟悉CMP的机理、设备和工艺控制
3.熟悉CMP的质量控制
【教学重点与难点】
平坦化技术的作用、CMP工艺及质量控制
【课程类型】
【教学方法与手段】
【学时分配】
【教学内容及教学过程】
10.1 概述
图10-1 两层布线表面的不平整
图10-2 多层布线技术
图10-3 平坦化术语
1)平滑处理:
平坦化后使台阶圆滑和侧壁倾斜,但高度没有显著减小,如图10-3b所示。
2)部分平坦化:
平坦化后使台阶圆滑,且台阶高度局部减小,如图10-3c所示。
3)局部平坦化:
使硅片上的局部区域达到平坦化。
4)全局平坦化:
使整个硅片表面总的台阶高度显著减小,使整个硅片表面平坦化,如图10-3e所示。
10.2 传统平坦化技术
10.2.1 反刻
反刻平坦化是在起伏的硅片表面旋涂一层厚的介质材料或其他材料(如光刻胶或SOG),这层材料可以填充空洞和表面的低处,将作为平坦化的牺牲层,如图10⁃4a所示。
然后用干法刻蚀技术进行刻蚀,利用高处刻蚀速率快,低处刻蚀速率慢来实现平坦化。
当被刻蚀的介质层达到希望的厚度时刻蚀停止,这样把起伏的表面变得相对平滑,实现了局部平坦化,如图10⁃4b所示。
图10-4 反刻平坦
10.2 传统平坦化技术
10.2.2 玻璃回流
玻璃回流是对作为层间介质的硼磷硅玻璃(BPSG)或其他的掺杂氧化硅膜层进行加热升温,使玻璃膜层发生流动来实现平坦化的技术,如图10⁃5所示。
一般,BPSG在氮气环境中,在850℃加热30min就发生流动,这样可使台阶处变成斜坡。
玻璃回流不能满足深亚微米IC的平坦化要求。
图10-5 玻璃回流
10.2.3 旋涂玻璃法
旋涂玻璃法(SpinOnGlass)主要是在起伏的硅片表面旋涂含有溶剂的液体材料,这样表面低处和缝隙将被填充,然后进行烘烤固化,使溶剂蒸发,即可获得表面形貌的平滑效果,如图10⁃6所示。
图10-6 旋涂玻璃
10.3化学机械平坦化
图10-7 化学机械平坦化原理图
10.3.1 CMP优点和缺点
1.优点
1)能获得全局平坦化。
2)对于各种各样的硅片表面都能平坦化。
3)可对多层材料进行平坦化。
4)减小严重的表面起伏,使层间介质和金属层平坦,可以实现更小的设计图形,更多层的金属互连,提高电路的可靠性、速度和良品率。
5)解决了铜布线难以刻蚀良好图形的问题。
6)通过减薄表层材料,可以去掉表面缺陷。
7)CMP是湿法研磨,不使用干法刻蚀中常用的危险气体。
8)CMP可以实现设备自动化、大批量生产、高可靠性和关键参数控制。
2.缺点
1)影响平坦化质量的工艺因素很多且不易控制。
2)CMP进行平坦化的同时也会引入新的缺陷。
3)需要配套的设备、材料、工艺控制技术,这是一个需要开发、提高的系统工程。
4)设备、技术、耗材、维护等十分昂贵。
10.3.2 CMP机理
CMP工作原理是将硅片固定在抛光头的最下面,将抛光垫放置在研磨盘上,抛光时,旋转的抛光头以一定的压力压在旋转的抛光垫上,由亚微米或纳米磨粒和化学溶液组成的研磨液在硅片表面和抛光垫之间流动,然后研磨液在抛光垫的传输和离心力的作用下,均匀分布其上,在硅片和抛光垫之间形成一层研磨液液体薄膜。
研磨液中的化学成分与硅片表面材料产生化学反应,将不溶的物质转化为易溶物质,或者将硬度高的物质进行软化,然后通过磨粒的微机械摩擦作用将这些化学反应物从硅片表面去除,溶入流动的液体中带走,即在化学去膜和机械去膜的交替过程中实现平坦化的目的,如图10⁃8所示。
图10-8 CMP具体步骤
1)化学过程:
研磨液中的化学品和硅片表面发生化学反应,生成比较容易去除的物质;
2)物理过程:
研磨液中的磨粒和硅片表面材料发生机械物理摩擦,去除化学反应生成的物质。
1.CMP机理模型
(1)Preston方程 从微观上来看,抛光同时是机械摩擦作用也是化学行为,理想的情况是化学作用速率和机械磨除速率相等,但这很难达到。
(2)Cook的模型 Cook模型仅适用于单纯的硅片抛光,是目前描述抛光最详细的模型。
2.CMP主要参数
(1)平均磨除率(MRR)在设定时间内磨除材料的厚度是工业生产所需要的。
(2)CMP平整度与均匀性 平整度是硅片某处CMP前后台阶高度之差占CMP之前台阶高度的百分比。
图10-9 硅片平整度的测量
(3)选择比 在CMP中,对不同材料的抛光速率是影响硅片平整性和均匀性的一个重要因素。
图10-10 CMP选择比应用
图10-11 阻挡层
(4)表面缺陷 CMP工艺造成的硅片表面缺陷一般包括擦伤或沟、凹陷、侵蚀、残留物和颗粒污染。
1)硅片表面上的擦痕或沟。
图10-12 CMP微擦痕造成的钨塞间的短路
图10-13 大图形中的CMP凹陷现象
1)侵蚀。
图10-14 高密度图形区域的CMP侵蚀
2)凹陷。
图10-15 由于侵蚀带来的不完全通孔刻蚀问题
4)残留物。
10.3.3 CMP设备
1.CMP设备组成
图10-16 CMP设备组成
(1)抛光机运动组件(常叫抛光机)包括抛光头、研磨盘,是实现CMP的关键机械装置。
1)抛光头组件。
图10-17 抛光
图10-18 CMP非均匀边沿区域
图10-19 更新的抛光头设计
2)研磨盘是CMP研磨的支撑平台,其作用是承载抛光垫并带动其转动。
(2)研磨过程的控制 它是控制抛光头压力大小、转动速度、开关动作、研磨盘动作的电路和装置。
(3)抛光垫与抛光垫修整
1)抛光垫大多是使用发泡式的多孔聚亚胺脂材料制成,是一种多孔的海绵,利用这种类似海绵的机械特性和多孔特性的材料,提高抛光的均匀性。
图10-20 抛光
2)抛光垫修整。
3)抛光垫寿命及定期更换。
(4)研磨液的供给与循环系统
1)研磨液由磨粒、酸碱剂、纯水及添加物构成,其成分见表10-1。
表10-1 研磨液成分
2)研磨液供给与输送系统。
①研磨液供给与输送系统与CMP工艺之间的关系:
研磨液中的化学品在配比混合输送过程中可能有许多变化,这一点,使输送给机台的研磨液质量与抛光工艺的成功形成了非常紧密的关系,其程度超过了与高纯化学品的联系。
尽管CMP设备是控制并影响CMP工艺结果的主要因素,但是研磨液在避免缺陷和影响CMP的平均抛光速率方面起着巨大的作用。
②研磨液供给与输送系统实现的目标:
通过恰当设计和管理研磨液供给与输送系统来保证CMP工艺的一致性。
研磨液的混合、过滤、滴定以及系统的清洗等程序会减轻很多与研磨液相关的问题。
那么就要设计一个合适的研磨液的供给与输送系统,完成研磨液的管理,控制研磨液的混合、过滤、浓度、滴定及系统的清洗,减少研磨液在供给、输送过程中可能出现的问题和缺陷,保证CMP的平坦化效果。
③研磨液混合和输送设备的设计特点:
搅动:
一般来讲,研磨液中的固体颗粒经过一段时间后会逐渐淀积,为了满足特定的工艺要求,必须保持桶中和储蓄罐中的液体均一,专业的研磨液系统制造商可以为每种研磨液设置特定的淀积率和分散率。
④各种CMP工艺的操作问题:
在处理化学品和研磨液时,一定要理解各种化学品之间的细微差别,并在系统中将这些不同点体现出来。
半导体工业使用的化学品已经超过了2000种,任何两种化学品在操作和安全方面都不同。
在处理研磨液过程中,其特性和问题基本上和工艺有关。
研磨液参数对特定CMP应用工艺的影响见表10-2。
作为成熟的工艺,氧化物和钨CMP都各自面临挑战。
作为新出现的技术,STI、铜和低k介质为业界带来新的挑战。
表10-2 研磨液参数对特定CMP应用工艺的影响
⑤抛光研磨液后处理:
作为消耗品,研磨液一般是一次性使用。
随着CMP市场的扩大,抛光研磨液的排放及后处理工作量也在增大(出于环保原因,即使研磨液不再重复利用,也必须先处理才可以排放)。
而且,抛光研磨液价格昂贵,如何对抛光研磨液进行后处理,补充必要的化学添加剂,重复利用其中的有效成分,或降级使用,不仅可以减少环境污染,而且可以大大降低加工成本。
抛光研磨液的后处理研究将是未来的新研究热点。
(5)终点检测设备 终点检测是检测CMP工艺把材料磨除到一个正确的厚度的能力。
1)电动机电流终点检测。
2)光学干涉法终点检测。
图10-21 终点检测的光学干涉
图10-22 CMP后的CMOS电路剖面图(未经过光学检测)
图10-23 经光学终点检测后的剖面图
3)先进的终点检测技术——红外终点检测技术。
(6)清洗设备与干出干进 过去CMP设备只是研磨抛光,与清洗设备是分开的。
2.CMP设备的发展
(1)单抛光头旋转式系统 CMP转动设备是用以玻璃陶瓷或其他金属的磨平抛光设备为基础的,这种设备由单个研磨盘和单个抛光头构成。
(2)多抛光头旋转式CMP系统 随着生产力需求和缺陷标准提高,出现了多研磨头的旋转体系,这类设备有很多种。
图10-24 多抛光头CMP设备
(3)多研磨盘CMP系统 由于Auriga公司和Symphony公司的设备缺乏灵活性,例如加工的硅片片数是22片而不是25片硅片,就不能发挥它们生产力高的优点。
(4)轨道式CMP系统 由于对于工艺的灵活性和生产力的需求提高,IPEC公司开发出了676轨道式CMP系统。
(5)线性CMP设备 最后,有些公司开发出能够实现高线速度的线性CMP设备。
10.3.4 CMP工艺控制
CMP工艺操作虽然简单,可是CMP效果受多方面因素的控制,所以要得到期望的效果,工艺控制就非常重要。
1.CMP工艺流程
1)前期准备:
根据研磨的材料对象(如硅、二氧化硅、铝、铜等)、工艺对象(STI、ILD、LI等)来选择合适的研磨液、抛光垫、清洗液等消耗品,并按照要求做好CMP设备、硅片、化学品(研磨液、清洗液)配置和输送系统、环境等的前期准备(例如设备和硅片清洗、检测,环境是否达到要求等)。
2)研磨抛光、清洗、甩干:
按照工艺文件的要求设置工艺参数进行CMP、清洗和甩干并监控工艺过程,做好工艺记录。
3)质量检测与评估:
按照检验工艺文件的检测方案(抽样、质量参数、检测工具和仪器、测量点等)进行测量和计算,并按照标准判断CMP工艺的合格性,做好记录。
2.影响CMP效果的主要参数
表10-3 影响CMP效果的主要参数
图10-25 单晶硅片抛光速率v与压力p的关系图
(1)抛光头压力 以对单晶硅片进行CMP为例来说明。
(2)抛光头与研磨盘间的相对速度 抛光速率随着抛光头与研磨盘间的相对速度的增大而增大。
(3)抛光垫 抛光垫是在CMP中决定抛光速率和平坦化能力的一个重要部件。
①碎片后为防止缺陷而更换抛光垫。
②优化衬垫选择以便取得好的硅片内和硬膜内的均匀性和平坦化(建议采用层叠或两层垫)。
③运用集成的闭环冷却系统进行研磨垫温度控制。
④孔型垫设计、表面纹理化、打孔和制成流动渠道等有利于研磨液的传送。
⑤CMP前对研磨垫进行修正、造型或平整。
⑥有规律地对研磨垫用刷子或金刚石修整器做临场和场外修整。
(4)研磨液 研磨液是影响CMP速率和效果的重要因素,在半导体工艺中,针对SiO2、钨栓、多晶硅和铜,需要用不同的研磨液来进行研磨,不同厂家的研磨液的特性也有所区别。
1)磨粒。
①磨粒材料:
对不同的薄膜CMP和不同工艺的CMP要精心选择磨粒材料。
即使是对同种薄膜材料进行CMP,其磨粒材料不同,抛光速率也不同。
例如对于ILD氧化硅进行CMP,采用二氧化铈(CeO2)作为磨粒的抛光速率比用气相纳米SiO2为磨粒的抛光速率大约快3倍。
ChristopherL.Borst对含碳量不同的三种PECVD的SiOC进行了抛光实验,发现SiOC在基于SiO2磨粒的碱性研磨液作用下的抛光速率明显高于基于氧化铝磨粒的酸性抛光液作用下的抛光速率,而且随着pH值的增加,抛光速率显著增大。
图10-26 磨粒含量对抛光速率的影响
②磨粒含量:
磨粒含量是指研磨液中磨粒质量的百分数。
即(磨粒质量/研磨液质量)×100%,又叫磨粒浓度。
由图10-26可知,对于硅抛光,在低磨粒含量时,在一定范围内对硅的抛光速率随着磨粒含量的增加而增加,平整度趋于更好。
这主要是由于,随着磨粒含量的提高,研磨液中参与机械研磨的有效粒子数增多,抛光液的质量传递作用提高,使平坦化速率增加,可以减小塌边情况的发生。
但并不是磨粒含量越高越好,当磨粒含量达到一定值之后,平坦化速率增加缓慢,且流动性也会受影响,成本也增加,不利于抛光。
要通过实验对确定的抛光对象找出一个最优的磨粒含量。
10.3 化学机械平坦化
③磨粒大小及硬度:
随着微粒尺寸和硬度的增加,去除速率也随之增加。
但会产生更多的凹痕和划伤。
所以要很细心地选择颗粒的大小和硬度,颗粒硬度要比去除材料的硬度小。
要不能使平坦化的表面产生凹痕和擦伤等表面缺陷。
2)研磨液的选择性:
对确定的研磨液,在同样条件下对两种不同的薄膜材料进行抛光时其抛光速率的不同,这就是研磨液的选择性。
3)研磨液中添加物的浓度与pH值:
与MRR有直接关系。
(5)温度对去除率的影响 CMP在加工过程中无论是酸性液体还是碱性液体,在与去除材料的化学反应中都是放热的反应,造成温度的上升,同时在加工过程中,由于抛光头的压力作用和抛光头及研磨盘的旋转具有做功的情况,所以有能量的释放,造成温度的上升。
(6)薄膜特性 CMP研磨薄膜材料的性质(化学成分、硬度、密度、表面状况等)也影响抛光速度和抛光效果。
3.CMP主要工艺控制
(1)研磨速率的控制 CMP的基本工艺控制主要是改变研磨盘转速、抛光头角速度和研磨压力。
(2)硅片内抛光均匀性控制 研磨均匀性是考量CMP的一个非常重要的考核指标,必须很好地优化设备、耗材和工艺。
(3)CMP后清洗 清洗液的成分、浓度和清洗设备有机地结合,可以达到清洗的最佳效果。
表10-4 CMP工艺对象与CMP后清洗
10.3.5 CMP应用
CMP技术应用的领域相当广泛,有如下几个方面:
①半导体表面的平坦化处理;②去除硅片损伤层,达成良好的表面粗度与平坦度;③CMP用在无电镀磷化镍铝镁基板的双面抛光。
此外还有一些其他应用,如镜头、薄膜液晶显示器的零组件的导电玻璃与彩色滤光片的抛光、微机电元件等制作。
CMP的应用领域见表10⁃5。
表10-5 CMP的应用领域
表10-5 CMP的应用领域
1.浅沟槽隔离平坦化(STICMP)
图10-27 STI浅槽隔离制作步骤
1)薄膜制作:
先做一层很薄的隔离氧化层(15nm)用来在后面去除氮化硅时保护有源区。
2)STI浅沟槽刻蚀:
对氮化硅、氧化硅、硅进行光刻、刻蚀、去胶,刻出STI沟槽,如图10-27c所示。
3)STI沟槽氧化硅淀积:
先在暴露的沟槽侧壁热氧化一层氧化硅(约15nm),改善硅与沟槽CVD填充氧化物之间的界面特性。
4)STICMP氧化物:
对图10-27d中的不平坦的CVD氧化硅进行CMP,如图10-27e所示。
①单液型是指在出厂前已经将研磨粒子与添加剂等混合好,可以直接使用的研磨液。
这种研磨液使用相对简单、风险小,但是工艺灵活度相对欠缺。
②双液型是指研磨粒子液体和添加剂液体分别包装,IC工厂根据自己的配方现场调配。
这种方法灵活度高,但是操作烦琐,增加了操作风险。
2.层间介质平坦化(ILDCMP)
图10-28 ILD制作及CMP
3.金属钨抛光
1)金属钛淀积(PVD工艺):
淀积一薄金属钛衬垫于介质沟道的底部和侧壁上。
2)氮化钛淀积(CVD工艺):
淀积完钛之后立即在钛金属层的表面淀积氮化钛(TiN),阻止金属钨向硅和氧化硅介质扩散,即做扩散阻挡层。
3)钨淀积:
钨填满局部互连的沟槽并覆盖硅片表面,如图10-29b所示。
4)钨CMP:
钨被CMP到局部互连介质层的上表面,如图10-29c所示。
图10-29 钨金属栓塞的制作流程
4.铜CMP
1)对层间介质层进行平坦化并蚀刻开出布线槽,如图10-30a所示。
2)利用溅射(PVD)方法形成绝缘用的阻挡层和导电用的籽铜层,如图10-30b、c所示。
3)在此基础上,采用电镀技术制成铜膜,如图10-30d所示。
4)铜CMP:
磨除掉层间介质表面以上的铜,完成布线埋入工艺,如图10-30e所示。
图10-30 铜布线的双大马士革工艺流程
10.4 CMP质量控制
10.4.1 膜厚的测量及均匀性分析
1.膜厚测量
图10-31 分光光学干涉法测量
(1)分光光学干涉法 分光光学干涉是利用光在介质上下表面反射的路程差形成干涉,测量干涉后的光强即可计算出薄膜厚度,如图10-31所示。
(2)椭圆偏振法 椭圆偏振法简称椭偏法,是一种先进的测量薄膜纳米级厚度的方法。
2.硅片表面的非均匀性分析
1)转盘上的抛光垫不平将导致中间快、中间慢或一些边缘问题。
2)磨头的压力(向下的压力)设置的不正确。
3)检查抛光垫修整臂是否调节到恰当位置,是否破旧(没有平滑面出现)。
4)磨料流量不够或粘滞度不正确(流动的能力)。
5)磨头上的垫膜破损,硅片不能保持成一个平面。
6)转盘转速的设置不对。
7)硅片的背压设置得不合适。
10.4.2 硅片表面状态的观测方法及分析
CMP后,有必要了解硅片的表面状况,观察和测量CMP后的表面缺陷。
以此来评估抛光的质量。
1.硅片表面状态的观测方法
图10-32 扫描电子显微镜
(1)扫描电子显微镜(ScanElectronMicroscope)关键尺寸测量的一个重要原因是要达到对产品所有线宽的准确控制。
图10-33 原子力显微镜示意图
(2)原子力显微镜 原子力显微镜(AFM)是一个表面形貌仪,用一个较小的平衡探针头扫描硅片表面产生的三维表面图形,使用光学技术,直接用针尖接触,并用激光器感应出其在硅片上的位置,如图10-33所示,探针和表面的距离非常小,以致原子力影响表面,针尖的几何尺寸极为关键,必须分类以便准确测量。
(3)光散射探测仪 光散射探测仪主要是根据光的散射效应,由于光的散射携带有很多丰富的信息,因此,提取这种信息将非常有助于分析其上层、下层甚至衬底的表面情况。
(4)光散射表面缺陷探测仪 可以测量CMP清洗后的颗粒污染;已在第9章中介绍,这里不再赘述。
2.硅片表面状态质量分析
(1)硅片表面上的擦痕或沟
1)外来物质碎片(如泵的软连接及垫片的碎片)。
2)磨料中的颗粒尺寸较大、分布不好或颗粒污染;磨料存储时间太长或使用不当造成磨料颗粒沉积而生成较大颗粒。
3)工艺未优化或没有进行减少微擦痕的二次缓冲抛光等。
(2)凹陷
1)抛光垫较软导致CMP过程抛光垫弯曲产生凹陷。
2)研磨液选择比选取不当,造成软材料处抛光速率过高,导致凹陷。
3)研磨液配比不当,造成CMP过程化学抛光速度和机械抛光速度的不均衡。
4)抛光速率过大,导致对硬度不同的材料带来抛光速率的差异过大。
5)研磨过程温度控制不稳,温度升高可能导致对一些材料的抛光速率提高的多。
6)抛光时间过长,导致速率高的区域过磨的量多。
(3)侵蚀
1)图形密度过高,没有采用适当的补偿措施。
2)抛光速率过大,导致对硬度不同材料带来抛光速率的差异过大。
3)过长的时间精抛(过抛情况下)及终点检测的延迟也会导致侵蚀情况的增加。
(4)残留物 对不同的材料进行CMP都会产生沿图形边沿的细长线条残留物,如钨或多晶硅细长线条。
1)研磨液的化学成分没有优化到最佳。
2)抛光垫的选取、研磨液的化学配置、被抛光材料的特性三者没有配合优化到最佳。
(5)CMP清洗后表面的颗粒
1)颗粒数过多(例如检测标准0.18μm工艺,要求颗粒直径大于8μm的颗粒数要小于20个)。
2)在深图形中残留研磨液结垢,如在光刻对准标记和压点区。
3)残留的铜在介质区域或有图形的表面的线条间移动。
①检查是否做了有图形硅片上残留铜的清洗。
对于高图形密度来说这是很难的。
②检查双面洗擦毛刷是否污染。
③确认是否用了最合适的清洗化学药品,特别是对清洗铜残留物而言。
10.4 CMP质量控制
④确认从硅片表面上不同的暴露材料和毛刷及清洗化学试剂没有产生化学药品的交叉污染。
【作业布置】
【课后分析】