制程检验操作指引.docx
《制程检验操作指引.docx》由会员分享,可在线阅读,更多相关《制程检验操作指引.docx(32页珍藏版)》请在冰豆网上搜索。
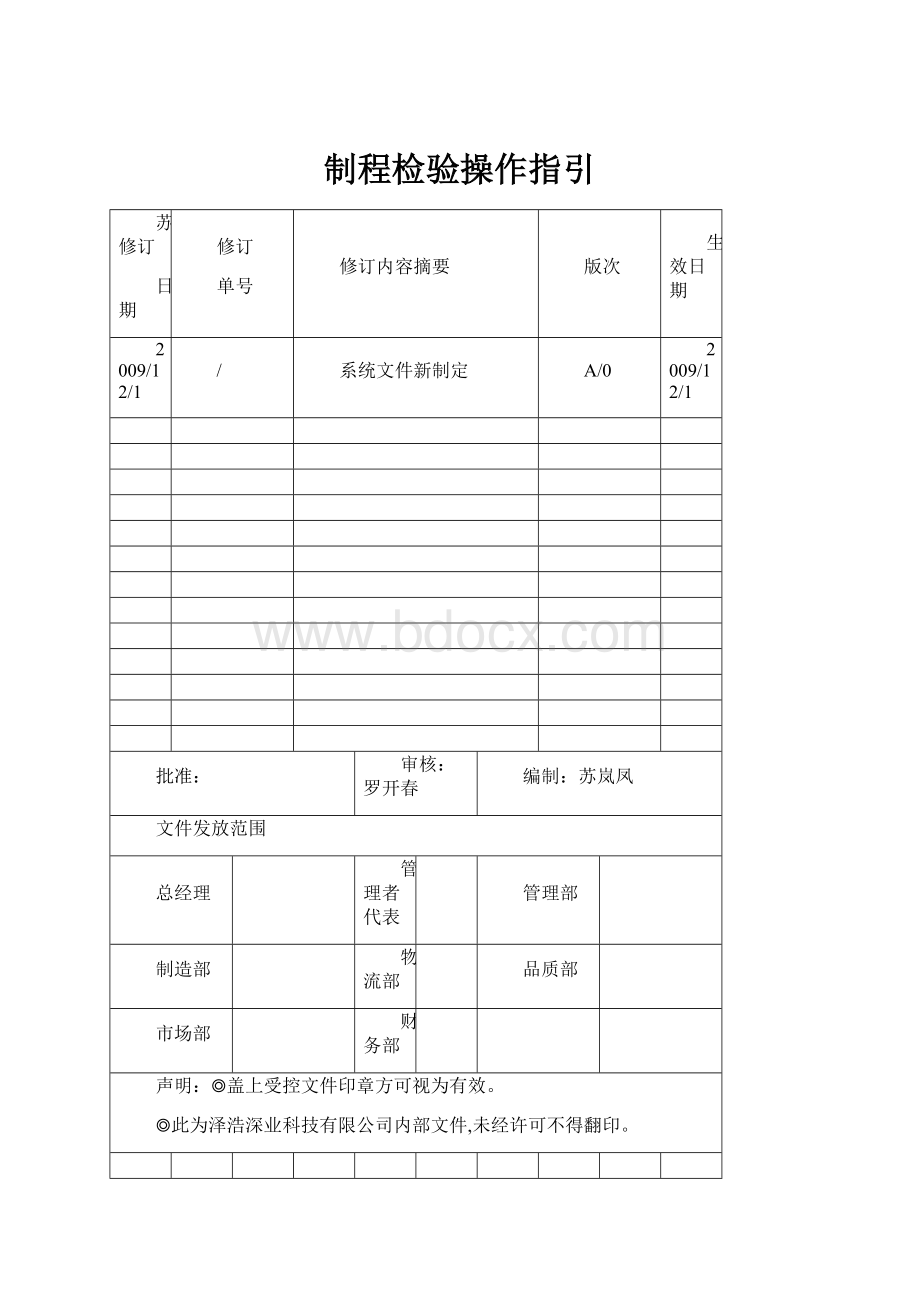
制程检验操作指引
苏修订
日期
修订
单号
修订内容摘要
版次
生效日期
2009/12/1
/
系统文件新制定
A/0
2009/12/1
批准:
审核:
罗开春
编制:
苏岚凤
文件发放范围
总经理
管理者代表
管理部
制造部
物流部
品质部
市场部
财务部
声明:
◎盖上受控文件印章方可视为有效。
◎此为泽浩深业科技有限公司内部文件,未经许可不得翻印。
目录
1.0目的--------------------------------------------------------3
2.0范围------------------------------------------------------3
3.0抽样--------------------------------------------------------3
4.0制程检验规范-------------------------------------------------3
4.1钻孔制程检验规范------------------------------------------3
4.2内层湿膜制程检验规范--------------------------------------5
4.3外层线路制程检验规范-------------------------------------7
4.4电镀制程检验规范------------------------------------------9
4.5蚀刻制程检验规范-----------------------------------------11
4.6阻焊制程检验规范-----------------------------------------14
4.7字符制符检验规范-----------------------------------------16
4.8碳油制程检验规范-----------------------------------------18
4.9喷锡制程检验规范-----------------------------------------19
4.10化Ni/Au检验规范--------------------------------------21
4.11成型制程检验规范----------------------------------------22
4.12开料检验规范--------------------------------------------23
4.13压合制程检验规范----------------------------------------24
4.14板电制程检验规范----------------------------------------25
4.15OSP检验规范---------------------------------------------26
1.0目的:
通过对各制程半成品的检验和验证,以保证各工序之半成品质量得到有效地控制,满足本公司或客户的品质要求.
2.0检验范围:
各生产制程
3.0抽样要求:
3.1在本公司生产的板各制程抽样要求参见本规范“4.0制程检验规范”中各项规定.
3.2各段制程外协加工板重缺陷按公司《抽样检查规定》中的AQL0.65进行检查(三个轻缺陷,合一个重缺陷计)。
3.3没有规定具体抽样数的IPQA检验点,进行随机抽检。
4.0制程检验规范
4.1钻孔制程检验规范:
4.1.1流程:
发料→钻孔→沉铜
4.1.2检验标准:
项目
质量要求
检验方法
缺点区分
板材厚度
符合MI要求
千分尺
MA
孔位
不允许偏孔
红片(绿片)
MA
孔数
不允许多孔、少孔
红片(绿片)
MA
孔型
不允许未钻透、孔塞、孔变形、有毛刺
目视
MA
孔壁
不允许有腻污
放大镜/九孔镜/微切片
MA
孔内粗糙度:
应≤30um(除客户要求)
孔径及槽的尺寸
符合MI要求
针规、游标卡尺
MA
板面
无污染、氧化、油污、胶渍
目视
MI
不允许有划伤、凹坑、压痕
目视
划伤在磨板后可消除
MI
划伤在磨板后不可消除
MA
内层孔偏(多层板
不充许破坏
X-RAY
MA
4.1.3检验方式:
4.1.3.1首板检验:
a.责任单位:
操作员负责检验、IPQA确认。
b.检验时机:
每连续生产批的开始;工程资料变更时;更换,维修钻机后的首次钻板;新料号。
c.检验数:
钻机各钻轴的首次钻板。
d.管制办法:
除板面以外的项目全部都以0收1退;首板检验合格后,方可进行批量生产。
e.记录:
《钻孔首板检验报告》
4.1.3.2抽检:
a.检验责任:
IPQA。
b.检验时机:
转序前。
c.检验数:
普通双面板抽样数为每2趟每轴的底板,二钻板及多层板抽样数为每趟每轴的底板。
d.管制办法:
主要缺点(MA):
采0收1退;次要缺点(MI):
三个次要缺点折合一个主要缺点;抽检合格该批转序,不合格则由该操作员(或领班)挑选、返工并上报主管,制造工序需将不合格原因查出并改善后方可继续生产。
e.记录:
《IPQA抽查记录表》
4.1.3.3巡检:
a.操作员每趟板需针对每个钻轴的底板进行检查。
b.发现问题及时修正,并对之前生产的板进行追溯直至将不合格品全部检出为止。
4.1.4记录
4.1.4.1《钻孔首板检验报告》
4.1.4.2《IPQA抽查记录表》
4.2内层湿膜制程检验规范:
4.2.1流程:
发料→内层湿膜→蚀刻。
4.2.2判定标准:
(Major--MA:
代表重缺陷,Minor--MI:
代表轻缺陷)
检验项目
检验标准
检验频率
检验方法
缺点区分
线宽
工作底片±10%
a:
首板
b:
最少3PNL/料号/班
百倍镜
MA
线距
工作底片±10%
a:
首板
b:
最少3PNL/料号/班
百倍镜
MA
缺口
≤线宽的10%
巡检
百倍锐
MA
凸位
≤线宽的10%
巡检
百倍镜
MA
对称性
两个内层线路的位置偏差
≤±0.05mm
首板
百倍镜
MA
锯齿
深度≤线宽20%、长度≤(总长度的10%;13mm取最小值)
巡检
百倍镜
MA
铜面刮伤
不露基材,不影响线宽
巡检
目视
MI
开、短路
不允许
巡检
目视
MA
露铜
不允许
巡检
目视
MA
残胶、显影不净
不允许
巡检
目视
MA
修理不良
不允许有修理不良修理符合以上各项要求
巡检
目视
MI
擦花
不允许
巡检
目视
MA
靶位
完整、清晰
巡检
目视
MA
4.2.3检验方式:
4.2.3.1首板检验:
a.检验责任:
线路QC负责检验、IPQA监控。
b.检验时机:
每一连续生产批、工程资料变更、生产设备变更,维修、新料号。
c.检验数:
开始生产前最少3片。
d.管制办法:
首板合格之后方可进行批量生产。
e.记录:
《线路首板检验报告》
4.2.3.2巡检。
a.检验责任:
线路QC。
b.检验时机、数量:
在显影口进行巡检。
4.2.4记录
4.2.4.1《线路首板检验报告》
4.3外层制程检验规范:
4.3.1流程:
全板电→外层→图形电镀
4.3.2检验标准:
(Major--MA:
代表重缺陷,Minor--MI:
代表轻缺陷)
检验项目
检验标准
检验方法
检验频率
缺点区分
开短路
不允许
目视
全检
MA
线宽
偏差小于0.01mm
百倍镜
a:
首板
b:
最少3PNL/料号/班
MA
线距
偏差小于工作底片10%
百倍镜
a:
首板
b:
最少3PNL/料号/班
MA
缺口
不允许大于线宽的20%
百倍镜
全检
MA
凸位
≤线宽的20%
百倍镜
全检
MA
焊环
≥0.1mm
百倍镜
a:
首板
b:
最少3PNL/料号/班
MA
对称性
两层线路的位置偏差≤±0.05mm
目视
百倍镜
全检
MA
残胶、垃圾
不允许
目视
全检
MA
露铜
不允许
目视
全检
MA
线面刮伤
不导致露铜
目视
全检
MA
铜面划伤
不露基材和不影响线宽
目视
全检
MI
锯齿
深度小于线宽的10%,且长度小于线宽的5倍
目视
百倍镜
全检
MA
标记
标记与MI一致;周期更改符合MI要求
目视
全检
MA
4.3.3检验方式。
4.3.3.1首板检验:
a.检验责任:
线路QC负责检验、IPQA监控。
b.检验时机:
每一连续生产批;工程资料变更;生产设备变更,维修,新料号。
c.检验数:
开始生产前最少3片
d.管制办法:
首板合格之后方可进行批量生产。
e.记录:
《线路首板检验报告》
4.3.3.2全检
a.检验责任:
线路QC。
b.检验时机,数量:
显影后的板100%检验。
c.管制办法:
检验合格以一张工作卡管制数为一批交付IPQA确认。
4.3.4记录
4.3.4.1《线路首板检验报告》
4.4电镀制程检验规范
4.4.1流程:
沉铜电镀(板电)外层线路蚀刻;阻焊表面处理
文字
4.4.2检验标准
检验项目
质量要求
检验工具
缺点区分
图形电镀后孔铜厚度(SC)
18-40um
孔内铜厚测试仪或切片
厚度小于25um,或厚度影响孔径时MA
非汽车板厚度在≥20
um,上限而未影响孔径时MI
板电铜厚
3-8um
孔内铜厚测试仪或切片
MA
注:
客户没有镀层厚度要求时,或客户要求与上述金度镀层厚度要求一致时,按本规范中规定的质量要求执行。
客户有要求时,则必须符合客户厚度要求。
4.4.3检验方式:
4.4.3.1电流与镀层厚度的确认:
a.责任单位:
物理实验室。
b.检验时机:
新料号的板正式批量电镀生产前。
c.检验数:
由制造部送交的左、中、右位置3PNL板。
d.管制办法:
对制造部提供样板进行镀层厚度测量,如果合格且确认电流合理则在经工艺签字确认的《电流指示》上签字。
不合格则通知制造部重新试做,直至确认合格,不合格试样报QA主管处理。
4.4.3.2镀层厚度的在线测量。
a.责任单位:
物理实验室。
b.检验时机:
批量生产时,每缸测试3PNL,每PNL至少测试1点。
c.管制办法:
合格则继续生产,发现不合格立即改善,必要时停工改善
4.4.4相关记录:
4.4.4.1《电镀铜厚检测报告》
4.5蚀刻制程检验规范
4.5.1流程:
图形电镀→蚀刻→阻焊
4.5.2检验标准(Major--MA:
代表重缺陷,Minor--MI:
代表轻缺陷)
项目
质量要求
检验工具
检验频率
缺点区分
开短路
不允许
目视
全检
MA
线宽
锡板偏差不超过设计线宽的20%;金板则因侧蚀而造成金镍镀层下的铜层宽度减少不超过设计线宽的20%,线宽和蚀刻系数标准两者取决于对线路影响较小者。
百倍镜
金相显微镜
a:
首板
b:
最少3PNL/料号/班
MA
侧蚀
用3M600#胶带朝着90度垂直方向拉扯线路,不允许有掉金或线路上金镍镀层起翘的现象,且做蚀刻系数切片,要求蚀刻系数在2.0以上(附图一)。
3M600#胶带
金相显微镜
a:
首板
b:
最少3PNL/料号/班
MA
线距
偏差不超过设计线宽的20%
百倍镜
a:
首板
b:
最少3PNL/料号/班
MA
线路缺口
每条线不超过3个且符合线宽要求(附图二)
目视、百倍镜
全检
MI
凸位
不超过设计线宽的20%,且符合线距要求
目视、百倍镜
全检
MI
蚀板不净
不允许在有效板内
目视
全检
MA
针孔
金手指上:
针孔小于0.1mm,不得露铜、镍,不得出现在金手指中间部位3/5的范围内.每个手指1PCS板上不得超过2个。
线路上:
针孔不影响线宽要求,同一线路上不可超过3个.
目视、百倍镜
全检
MA
线路扭曲、刮伤
不允许
目视
全检
MA
板允许有轻微刮伤,但需后工序磨板处理时去除
目视
全检
MI
金板不允许有刮伤
目视
全检
MA
环宽
环宽不小于0.1mm,与线路连接部分的环宽因偏位而减少不小于线宽80%;
目视
a:
首板
b:
最少3PNL/料号/班
MA
金属化孔
1、孔内清洁,无任何杂物。
2、孔壁不可有无铜现象
3、孔内不得有铜渣
4、不得有使孔径减少超过孔径公差的毛刺、镀瘤等,
5、不得塞孔
6、孔内空穴不能多于1个,且其任意方向尺寸≤5%孔厚或90°圆环,有空穴孔的个数≤5%总孔数。
目视\放大镜\针规
全检
MA
非金属化孔
孔内不得留有金属镀层
目视
全检
MA
铜面
不允许有退锡不净,氧化、粗糙、烧焦现象.
目视
全检
MI
基材表面
不允许有晕圈、分层、起泡现象。
目视
全检
MA
外来夹杂物
可视夹杂物为不导电体长度小于0.75mm,且夹杂物的宽度不导致线路间距超过规定的偏差。
目视、百倍镜
全检
MI
板材
LOGO与MI板材供应商要求一致;颜色(黄料或白料)相符。
目视
全检
MA
铜丝
无铜丝
目视/AOI
全检
MA
孔内铜粒
导通孔内铜粒,不可遮挡孔的三分之一面积,对于插件孔,不影响孔径可接受。
目视
全检
MA
标记不清
蚀刻标志的线条宽度不少于线宽要求的50%,但可读,允许有些线路破损,但尚可辨认。
目视
全检
MA
内层杂物
透明或半透明的外来物是允许的,其它杂物满足以下条件可接受:
a.杂物与任一导线的间距符合最小间距要求,若最小间距未作规定,最小间距应为0.13mm。
b.杂物最大尺寸<0.8mm。
目视
全检
MA
白点
受白点影响的面积不超过单元面积的5%,且线间白点不应超过间距的70%。
目视
全检
MI
露布纹
纤维显露之处与线路之距离不低于MI规定的最小间距要求。
目视
全检
MA
4.5.3检验方式
4.5.3.1首板检验
a.检验时机:
每一连续生产批;工程资料变更;生产设备更换、维修;新料号
b.检验责任:
蚀检QC、IPQA监控。
c.检验数:
开始生产前最少3片
d.管制办法:
首板合格后方可进行批量生产
e.记录:
《蚀刻首板检验报告》
4.5.3.2全检
a.检验责任:
蚀刻QC。
b.检验条件、数量:
所有蚀刻板100%全检。
c.管制办法:
检验合格以一张工作卡管制数为一批交付IPQA确认。
4.5.4记录
4.5.4.1《蚀刻首板检验报告》
4.5.5附图:
附图一:
蚀刻系数的计算方法:
照像底版上的导线宽度
附图二:
线路缺口
a≤W/S,b≥2mm,c≥2mm,d≥2mm,e≤W/S
4.6阻焊制程检验规范
检验项目
检验标准
检验方法
缺点区分
绿油上焊盘
SMD按键位阻焊上盘≤10%
目视、百倍镜
MA
露铜
不允许
目视
MA
绿油进孔
1、不允许进插件孔;
2、进非电镀孔不能影响孔径。
目视
MA
绿油底氧化
不允许
目视
MA
绿油针孔
不允许
目视
MI
绿油起泡
最大尺寸<0.25mm允许每面2个,但不能使线路或焊盘桥接。
目视
MA
显影不净
不允许
目视
MA
绿油划伤
宽度≤0.05mm长度≤10mm,每PCS不多于2条.每PNL不多于3条.
目视
MI
绿油剥离
不允许
3M600#胶带
MA
绿油上金手指
不允许
目视
MA
绿油不均
不允许
目视
MA
色泽不一致
不允许
目视
MA
塞孔不足
不允许
目视
MI
塞孔凸起
不允许
目视
MI
绿油下杂物或手指印、污点
不允许
目视
MI
显影过度
不允许
目视
MA
绿油起皱
不允许
目视
MI
绿油偏移
节距≥1.25mm只能一侧上Pad,且<0.05mm;节距<1.25mm只能一侧上Pad,且<0.025mm;BGA位不能上绿油
百倍镜
MA
塞错孔
不允许
目视
MA
绿油桥
完整,无残缺、剥离
目视
MA
漏印
不允许
目视
MA
标记
标记与MI一致;周期更改符合MI要求
目视
MA
油墨类型
颜色、油墨类型与MI要求一致
目视核对MI
MA
4.6.1流程:
蚀刻→阻焊→字符
4.6.2检验标准:
4.6.3检验方式:
4.6.3.1首板检验:
a.检验责任:
阻焊QC负责检验、IPQA监控。
b.检验时机:
每一连续生产批;工程资料变更;重要生产设备变更、维修、调整;新料号。
c.检验数:
开始生产前最少3片.
d.管制办法:
首板检合格之后方可进行批量生产。
e.记录:
《阻焊首板检验报告》
4.6.3.2全检
a.检验责任:
阻焊QC。
b.检验时机、数量:
对显影后的阻焊板进行100%全检。
c.管制办法:
检验合格品以一张工作卡管制数为一批交付IPQA确认。
4.6.4记录:
4.6.4.1《IPQA抽查记录》
4.7字符制程检验规范
4.7.1流程:
阻焊→字符→喷锡(或:
镀金手指、成型)
或:
喷锡(或化Ni/Au)→字符→成型
4.7.2检验标准:
检验项目
检验标准
检验方法
缺点区分
字符内容
完整、无误、不得印反
目视
MA
宽度不均匀
不允许
目视
MA
字符模糊
不允许
目视
MA
重影
不允许
目视
MA
偏位
不允许上焊盘的10%以上
百倍镜
MA
字符入孔
不允许
目视
MA
字符剥离
不允许
3M600#胶带
MA
油墨沾污板面
不允许
目视
MA
标记
标记与MI一致;周期更改符合MI要求
目视
MA
字符类型
颜色、油墨类型与MI要求一致
目视核对MI
MA
4.7.3检验方式:
4.7.3.1首板检验
a.检验责任:
字符员工、目检字符QC确认检查。
b.检验时机:
每一连续生产批;工程资料变更;重要生产设备变更;新料号。
c.检验数:
开始生产前最少3片;
管制办法:
首板合格之后方可进行批量生产
a.记录:
《字符首板检验报告》
4.7.3.2抽检
a.检验责任:
字符QC
b.检验时机:
转序前
c.检验数量:
随机抽样,抽样数不少于生产批的10%
d.管制办法:
主要缺陷(MA)采0收1退次要缺陷(MI)以3个次要缺陷折1个主要缺陷计;抽检合格时继续生产,不合格由相关单位挑选、改善后方可继续生产,定位缺陷还应由制造部对该抽查时段印刷的板进行全检,由制造对不合格进行返工处理。
4.7.4记录
4.7.4.1《字符首板检验报告》
4.8碳油制程检验规范
检验项目
检验标准
检验方法
缺点区分
丝印偏位
不允许
目视
MA
露铜、金
不允许
目视
MA
碳油剥离
不允许
目视、3M600#胶带
MA
碳油阻值
符合MI要求
用万用表测量
MA
碳油增宽
偏差不能超过设计间距的20%
目视、十倍镜
MA
碳油针孔
不允许
目视
MI
碳油短路
不允许
目视
MA
碳油类型
与MI要求一致
目视核对MI
MA
4.8.1流程:
字符→碳油→成型(或绿油→碳油→字符;成型→碳油→蓝胶)
4.8.2检验标准:
4.8.3检验方式:
4.8.3.1首板检验:
a.检验责任:
操作员工自检、字符QC确认检查。
b.检验时机:
每一连续生产批;工程资料变更;重要生产设备变更
c.检验数:
开始生产前最少3片。
d.管制办法:
首板合格后可进行批量生产。
e.记录:
《碳油首板检验报告》。
4.8.3.2抽检
a.检验责任:
字符QC。
b.检验时机:
转序前。
c.数量:
随机抽样,抽样数不少于生产批的10%。
d.管制方法:
主要缺陷(MA)采0收1退;次要缺陷(MI)以3个次要缺陷折一个主要缺陷计;抽检合格时继续生产,不合格由相关单位挑选、改善后方可继续生产,定位缺陷还应由制造部对该抽查时段印刷的板进行全检,由制造部对不合格进行返工处理。
4.9喷锡制程检验规范
4.9.1流程:
阻焊→喷锡→文字(或:
成型)
4.9.2检验标准:
检验项目
检验标准
检验方法
缺点区分
孔内锡厚
上限:
不影响孔径
针规
MA
锡面发黑
不允许
目视
MA
锡面发白
不允许
目视
MI
锡面粗糙
不允许
目视
MI
锡面不平整或不均匀
不允许
目视
MI
线路上锡
不允许
目视
MA
金手指上锡
不允许
目视
MA
塞孔
不允许
目视
MA
开短路
不允许
目视
MA
锡须
不允许
目视
MI
锡高
不允许
目视
MI
孔小
不允许
目视
MA
露铜
不允许
目视
MA
刮伤
不允许伤及阻焊层或线路
目视
MA
折板
不允许
目视
MA
基材分层
不允许
目视
MA
绿油起泡
不允许
3M600#胶带
MA
孔内锡渣
不允许
目视
MA
光点
不能有锡高、不圆、亚光
目视
MA
4.9.3检验方式:
抽检
4.9.3.1检验责任:
IPQA
4.9.3.2检验时机:
每一张工卡管制产品数经全检,合格需转序时.
4.9.3.3检验数:
交验批的20%。
4.9.3.4管制办法:
主要缺陷(MA)采0收1退;次要缺陷(MI)以3个次要缺陷折1个主要缺陷计,抽检合格时,该批转序,不合格则退回喷锡QC返工;
4.9.4记录:
4.9.4.1《IPQA抽查记录》
4.10化Ni/Au检验规范
4.10.1流程:
阻焊→化Ni/Au→字符。
4.10.2检验标准:
检验项目
检验标准
检验方法
缺点区分
金厚(SC)
不低于MI要求,客户无要求时必须≥0.03um
切片或X-Ray测试
MA
镍厚(SC)
不低于MI要求,客户无要求时,金手指镍厚≥5um
切片或X-Ray测试
MA