超临界锅炉概况.docx
《超临界锅炉概况.docx》由会员分享,可在线阅读,更多相关《超临界锅炉概况.docx(23页珍藏版)》请在冰豆网上搜索。
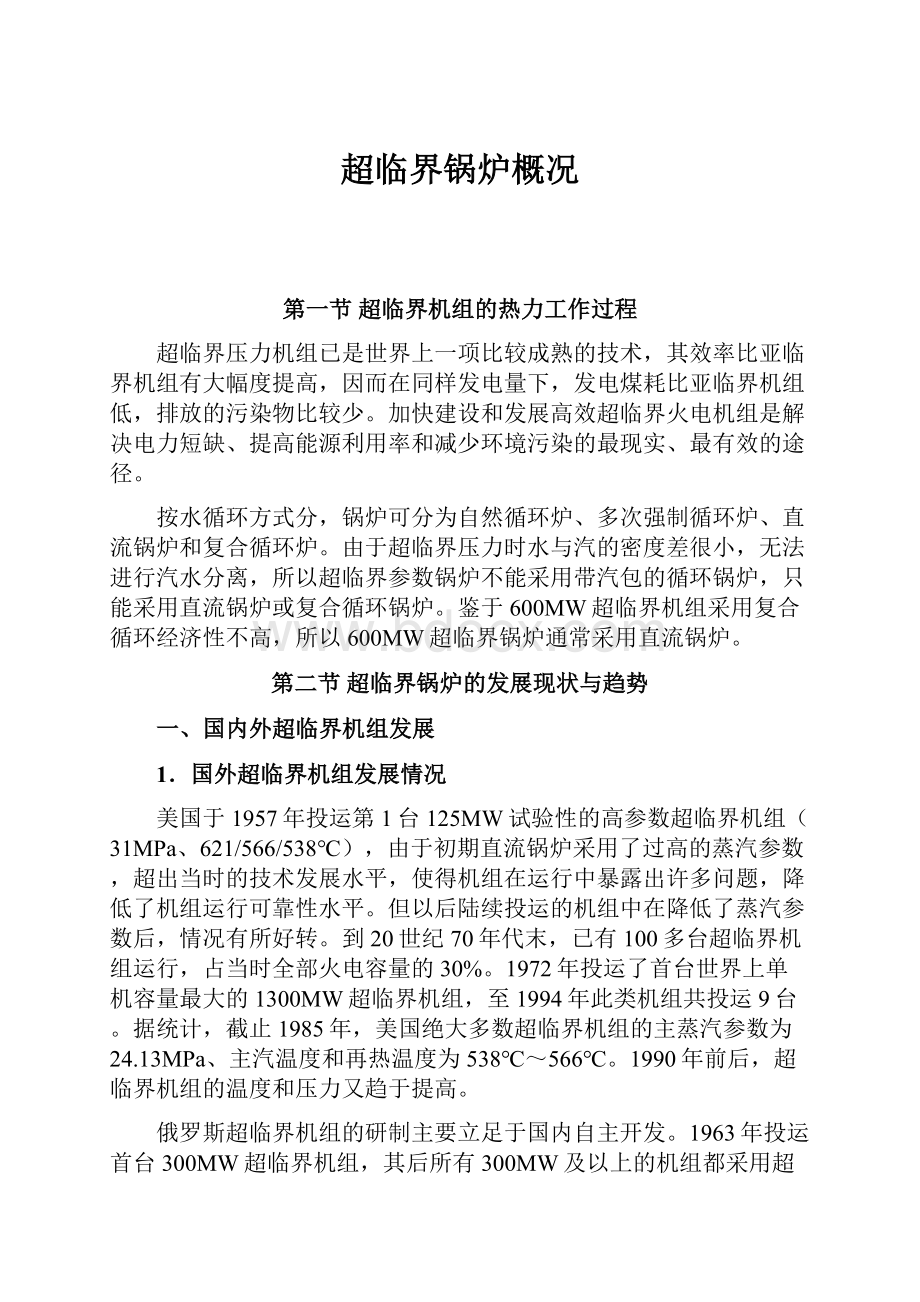
超临界锅炉概况
第一节超临界机组的热力工作过程
超临界压力机组已是世界上一项比较成熟的技术,其效率比亚临界机组有大幅度提高,因而在同样发电量下,发电煤耗比亚临界机组低,排放的污染物比较少。
加快建设和发展高效超临界火电机组是解决电力短缺、提高能源利用率和减少环境污染的最现实、最有效的途径。
按水循环方式分,锅炉可分为自然循环炉、多次强制循环炉、直流锅炉和复合循环炉。
由于超临界压力时水与汽的密度差很小,无法进行汽水分离,所以超临界参数锅炉不能采用带汽包的循环锅炉,只能采用直流锅炉或复合循环锅炉。
鉴于600MW超临界机组采用复合循环经济性不高,所以600MW超临界锅炉通常采用直流锅炉。
第二节超临界锅炉的发展现状与趋势
一、国内外超临界机组发展
1.国外超临界机组发展情况
美国于1957年投运第1台125MW试验性的高参数超临界机组(31MPa、621/566/538℃),由于初期直流锅炉采用了过高的蒸汽参数,超出当时的技术发展水平,使得机组在运行中暴露出许多问题,降低了机组运行可靠性水平。
但以后陆续投运的机组中在降低了蒸汽参数后,情况有所好转。
到20世纪70年代末,已有100多台超临界机组运行,占当时全部火电容量的30%。
1972年投运了首台世界上单机容量最大的1300MW超临界机组,至1994年此类机组共投运9台。
据统计,截止1985年,美国绝大多数超临界机组的主蒸汽参数为24.13MPa、主汽温度和再热温度为538℃~566℃。
1990年前后,超临界机组的温度和压力又趋于提高。
俄罗斯超临界机组的研制主要立足于国内自主开发。
1963年投运首台300MW超临界机组,其后所有300MW及以上的机组都采用超临界技术。
迄今,基本上形成300MW、500MW、800MW、1200MW等4个容量等级,参数基本保持在23.5MPa、540/540℃。
超临界机组占火电容量50%以上,最大单机容量为1200MW。
目前俄罗斯的列宁格勒金属工厂和莫斯科动力学院又设计了新一代高参数超临界机组,蒸汽参数为(30~32)MPa/580~600/580~600℃,给水温度300℃。
当凝汽器压力为(3.4~3.6)kPa时,预计电站的效率为44%~46%。
日本发展超临界机组虽然起步较晚(20世纪60年代中期),但发展快、收效大。
其采取引进、仿制、创新的技术路线,与俄罗斯形成鲜明的对比。
日本于1967年从美国进口首台600MW超临界机组,两年后仿制的同型机组就已投运;而1971年投运的600MW超临界机组则有效地利用了日本自己的技术。
80年代以后,日本吸取了欧洲的经验,自行开发了能带中间负荷滑压运行的超临界直流锅炉。
现在容量为450MW以上的机组均采用超临界参数,一般为24.1MPa/538/566℃,一次再热;少数机组采用24.1MPa/538/538℃或24.1MPa/538/552/566℃,二次再热。
目前,日本超临界机组已占其火电容量的50%以上,最大单机容量为1000MW。
而且开始向更高参数发展,蒸汽温度多在566℃~593℃的范围内。
1989年日本投运了世界上第1台采用超超临界参数的川越电厂1号机组,其主蒸汽压力为31MPa,温度为566/566/566℃(二次再热)。
德国也是发展超临界技术最早的国家之一,但其单机容量较小。
1956年参数为29.3MPa、600℃(无再热)的117MW超临界机组投运,1972年首台430MW(24.5MPa、535/535℃)超临界机组投运。
德国近年来很重视发展超临界机组,目前最具有代表性的是1992年投运的斯道丁格电站5号机组,该机组容量为535MW,参数为26.2MPa、545/562℃,机组净效率可达43%。
国际上通常把主蒸汽压力在28MPa以上和主蒸汽、再热蒸汽温度在580℃及其以上的机组定义为高效超临界(highefficiencysupercritical)机组或高参数超临界(advancedsupercritical)机组。
之所以这样定义是因为这个参数是锅炉、汽轮机只需使用现代超临界机组用钢上限,超过这个参数高温高压部件就必须采用改进或新开发的耐热钢种。
2.国内超临界机组发展情况
我国自80年代开始引进超临界压力机组,600MW超临界机组在上海石洞口第二发电厂于1992年投入运行以来,克服了许多技术上的难关,机组达到设计指标,经济效益良好。
前几年国内先后引进的多台300MW、500MW、600MW、800MW等超临界火电机组也投运良好,取得了一些重要的调试和运行经验。
近几年来国内三大动力集团在电站设备设计和制造方面的技术、经验、能力和技术装备水平等都有了很大的进步和发展。
所有这些,都为加速我国大型超临界火电机组的研制步伐和实现批量生产,提供了必要的条件和基础。
600MW级机组在技术上属于成熟产品,考虑到国内电网对单机容量600MW的需求和国内已有亚临界600MW火电机组产品的实际情况(有些配套可以通用),我国发展超临界火电机组的起步容量定为600MW;从技术性、经济性以及机组配用材料方面考虑,参数初步定为压力24~25MPa、温度538℃~566℃、一次再热。
超临界压力锅炉蒸发受热面(水冷壁)有垂直管屏和螺旋管圈两种形式。
我国引进的俄罗斯的超临界压力锅炉均采用垂直管屏式水冷壁,瑞士与美国引进的锅炉下部炉膛采用螺旋管圈,上部采用垂直管屏。
垂直管屏式水冷壁结构简单,螺旋管圈式水冷壁,可满足各种炉膛尺寸,适用于滑压运行。
随着电网峰谷差的加大,大型火电机组要参与电网调峰,这时,大容量超临界锅炉采用垂直管屏,对调峰的适应性要差一些。
我国现运行的俄罗斯造超临界锅炉水冷壁全部采用垂直管屏,但俄罗斯国内运行的800MW超临界锅炉水冷壁大多采用螺旋管圈式。
超临界锅炉的总体布置形式有两种,即倒U形和T形。
倒U形布置是最常见的布置形式,但随着锅炉容量的增大,炉膛宽度b增长的速度比锅炉容量D增长的慢,故b/D值随锅炉容量D增大而减少。
另一方面,锅炉的蒸汽量和燃烧形成的烟气量随锅炉容量增大而增加。
这样对于大容量的锅炉容易造成过热器中蒸汽流速和烟气流速过高。
如果把出口烟窗的高度增大来减小烟气流速,则会使烟气沿出口烟窗高度的热力和流动的不均匀性增大。
锅炉的T形布置可以解决上述问题。
它是在炉膛上部开两个出口烟窗,组成两个对流烟道。
这样就可解决对流烟道中的布置困难和降低出口烟窗高度,但T形布置的锅炉占地面积大。
俄罗斯在锅炉燃烧器的选用上,习惯于旋流燃烧器,而CE技术公司采用直流煤粉燃烧器切圆燃烧方式。
目前我国制造的国产引进型300MW、600MW亚临界压力机组绝大多数采用的是直流燃烧器切圆燃烧方式。
切圆燃烧方式存在的主要问题是残余旋转加大,从而会造成炉膛出口以后受热面的热偏差增大。
我国引进的俄罗斯造超临界锅炉,采用了多种形式的磨煤机,华能南京电厂2×300MW机组采用俄罗斯传统的球磨机、中储式热风送粉系统;伊敏发电厂500MW机组因燃用褐煤而采用了风扇式磨煤机;其它按燃用烟煤设计的锅炉均采用MPS中速磨煤机。
上海石洞口二厂采用的是HP中速磨冷一次风机正压直吹式制粉系统。
中速磨煤机的煤种适应性虽然不如低速球磨机那样广泛,但在其适用的煤种范围,却比球磨机有重量轻、占地小、投资省、耗电低、金属磨耗低和噪音小等优点。
因此,在煤种适宜的条件下,优先采用中速磨煤机是合理的。
目前我国300MW及以上机组多数采用中速磨煤机,国产引进技术制造的中速磨主要有RP型和MPS型,HP型是RP型的改进型。
随着节约能源和保护环境的要求日益迫切,在我国大力发展超临界压力机组已成为当务之急。
对超临界压力锅炉,将再热由一次转为两次可提高效率1.5%~2%。
采用两次再热的主要问题是:
系统复杂,受热面布置较困难;初投资增加;再热汽温调节复杂。
二、超临界火电技术的发展趋势
1.国外超超临界机组
为进一步降低能耗和减少CO2排放,改善环境,在材料技术发展的支持下,超临界机组正朝着更高参数的超超临界的方向发展。
目前高参数的超临界机组已达到成熟、高效和商业化程度,其最大容量已达1300MW,最高效率达49%,具有极高的推广前景。
超超临界机组技术也正趋于成熟,国外超超临界机组发展的近期目标为1000MW级机组,参数为31MPa、600/600/600℃,并正在向更高的水平发展。
一些国家和制造厂商已经公布了发展下一代高效超临界机组的计划,蒸汽初温将提高到700℃,再热汽温达720℃,相应的压力也将从目前的30MPa左右提高到35~40MPa,机组供电效率有望达到50%~55%。
在欧洲的“THERMIE”计划中目前正在支持旨在推动欧洲发展超临界火电技术的项目“ADVANCED(“700℃”)PFPPOWERPLANT”(即先进的“700℃”PF电厂),该项目主要有两个目标:
使燃烧粉煤(PF)电厂的净效率由47%提高到55%(对于低海水冷却水温度)或52%左右(对于内陆地区和冷却塔);降低燃煤电站的造价。
欧洲各国约有40个单位参加了这个项目的工作,其中有26家是设备制造商(包括汽轮机、锅炉、主要辅机和材料等制造商),其它则分别是有关的研究机构、大学、电力公司等部门。
该项目从1998年开始,分为8个阶段,预计在2014年完成。
在此还应特别说明的是,根据世界上先进的超临界电站的发展经验,机组效率的提高可能来源于许多方面的因素,如:
较低的锅炉排烟温度,高效率的主、辅机设备,煤的良好燃烧,较高的给水温度,较低的凝汽器压力,较低的系统压损,蒸汽再热级数等等。
2.国内超超临界机组
华能浙江玉环电厂一期工程建设两台100万千瓦级超超临界燃煤机组,计划于2007年下半年和2008年上半年分别投产。
超超临界燃煤发电机组煤耗低、环保性能较好、技术含量高,是国际上燃煤发电机组的重要发展方向。
锅炉由哈尔滨锅炉有限责任公司中标,技术支持方为日本三菱公司,汽轮机、发电机则分别由上海汽轮机有限公司、上海汽轮发电机有限公司供货,其技术支持方为德国西门子公司。
华能玉环电厂锅炉为超超临界参数变压垂直管圈直流炉、一次再热、平衡通风、露天布置、固态排渣、全钢构架、全悬吊结构Π型锅炉。
锅炉的最大连续蒸发量(B-MCR)2950t/h。
锅炉出口蒸汽参数27.56Mpa/605℃/603℃。
炉膛上、下部水冷壁均采用内螺纹垂直管。
上下部水冷壁之间设有混合集箱,在由各水冷壁下集箱引出的水冷壁入口管段上,按不同的回路装有不同孔径的节流孔圈。
为防止锅炉结渣,慎重地选择炉膛容积热负荷为82.7kW/m3,炉膛断面热负荷为4.59MW/m2。
锅炉采用带启动循环泵的内置式启动系统。
燃烧方式采用无分隔墙的八角双火焰切圆燃烧方式。
采用PM-MACT型八角反向双切圆布置的摆动燃烧器。
采用该燃烧器NOX的排放量低于360mg/Nm3。
过热器系统采用四级布置,以降低每级过热器焓增,沿蒸汽流程依次为水平与立式低温过热器、分隔屏过热器、屏式过热器和末级过热器。
过热器系统共有三级喷水减温。
再热器分为低温再热器和高温再热器,两级再热器之间设有事故用紧急喷水减温器。
主要使用烟气挡板调节再热汽温。
省煤器管束采用无缝光管顺列布置。
省煤器为连续管圈可疏水型。
受热面主要材料的选择是成败的关键,高温过热器、末级再热器受热面的主要材料为Super304H和HR3C,Super304H高温下许用应力较高,但在抗蒸汽氧化及抗烟气高温腐蚀上比HR3C稍差,玉环电厂锅炉采用了抗氧化性更好的成熟材料同HR3CSuper304H相结合方式,将Super304H作喷丸处理后用于金属温度较低区域,易氧化的高温区则采用HR3C。
第三节超临界锅炉机组的技术特点
一、超临界火电机组的参数、容量及效率
水的临界状态点的参数为22.115MPa、374.15℃。
理论上认为,在水的状态参数达到临界点时,水完全汽化会在一瞬间完成,即在临界点时,在饱和水和饱和蒸汽之间不再有汽、水共存的二相区存在,二者的参数不再有区别。
与较低压力下水的特性不同,在压力很高的情况下,特别在临界点附近,水的质量定压热容Cp值会有较显著的变化。
对水蒸汽动力装置循环理论分析表明,提高循环蒸汽的初参数和降低循环的终参数都可以提高循环的热效率。
除此之外,采用再热循环和回热循环也可以提高循环的热效率。
实际上,蒸汽动力装置的发展和进步一直是以提高参数为目的的。
另外,在蒸汽参数相同的情况下,机组容量增加,其热耗率会有所降低。
在机组容量一定的情况下,蒸汽参数的提高虽然会提高循环热效率,但由于这时蒸汽压力升高、质量热容减小,有可能会对汽轮机的高压缸内效率带来不利影响。
因此,在实际中或许会有一个“最小经济容量”的问题,即在机组容量小于“最小经济容量”的情况下,采用超临界参数有可能是不经济的。
事实表明,提高蒸汽参数并与发展大容量机组相结合是提高常规火电厂效率及降低单位容量造价最有效的途径。
与同容量亚临界火电机组的热效率相比,在理论上采用超临界参数可提高效率2%~2.5%,采用超超临界参数可提高4%~5%。
目前,世界上先进的超临界机组效率已达到47%~49%。
二、超临界火电机组的运行灵活性与可靠性
目前先进的大容量超临界机组具有良好的启动、运行和调峰性能,能够满足电网负荷的调峰要求,并可在较大的负荷范围(30%~90%额定负荷)内变压运行,变负荷速率多为5%/min。
美国《发电可用率数据系统》1980年的分析报告中公布了71台超临界机组和27台亚临界机组的运行统计数据,表明这两类机组的平均运行可用率、等效可用率和强迫停运率已无差别。
据美国EPRI的统计,容量为(600~835)MW、具有二次中间再热的超临界机组整机可用率已达90%,1300MW二次中间再热的燃煤超临界机组整机可用率为92.3%,有的还要高一些;有1台ABB公司制造的1300MW超临界机组甚至创造过安全运行605天的记录。
同时,从国内引进的几台超临界机组的运行情况看,也说明了这一点,即目前投运的超临界机组的运行可靠性指标已经不低于亚临界机组,有的甚至更高。
三、超临界机组的投资造价比较
提高蒸汽参数将使机组的初投资有所增加,这是因为压力提高后很多设备和主蒸汽管道的壁厚要相应增加,或者说要选用性能和价格更高一些的材料;而温度提高后则要使用更多价格昂贵的合金钢材。
一般认为超临界机组的造价比亚临界机组大约增加3%~10%。
但由于世界各国的具体情况不同,且各个电站的设计和辅机配套方案等也有所不同,因此,造价增加的幅度不同。
四、水冷壁管圈型式
传统的观念认为只有螺旋管圈水冷壁才能满足全炉膛变压运行的要求,但是目前欧洲的火电机组锅炉仍然采用下炉膛螺旋管圈,上炉膛垂直管屏的传统设计,这种水冷壁系统对于光管水冷壁为了获得足够的冷却能力是十分必要,其优点是:
可以采用较大口径的光管水冷壁管;可以有效地补偿沿炉膛断面上的热偏差;不需要根据热负荷分布进行平行管系中复杂的流量分配;在低负荷下仍能保持平行管系流动的稳定性。
螺旋管圈水冷壁的缺点是显而易见的,结构复杂、流动阻力大和现场安装工作量大。
因而日本三菱公司在亚临界控制循环锅炉设计制造经验基础上,开发出了一次上升垂直管圈水冷壁变压运行超临界锅炉,其特点是采用内螺纹管来防止变压运行至亚临界区域时,水冷壁系统中发生膜态沸腾和在水冷壁管入口处设置节流圈使其管内流量与它的吸热相适应。
至2000年,在日本已有7台垂直管圈水冷壁高效超临界锅炉在运行中。
五、承压部件材质的选择
大容量电站锅炉承压部件用钢主要有奥氏体和铁素体两类。
奥氏体钢热强性高,但导热性差,膨胀系数大,抗应力腐蚀能力低,工艺性能差,且成本高。
因此,设计时应尽量少用奥氏体钢,多用新开发的铁素体钢和改进的奥氏体钢。
由于制造,特别是安装的要求,锅炉水冷壁必须是无需焊后热处理的材料制成,现代超临界锅炉水冷壁通常采用的钢种为T22/13CrMo44。
这种材料就水冷壁而言,最高许用温度460~470℃,对于高效超临界锅炉,当主汽参数为28MPa/580℃/580℃时,水冷壁采用这种材料还是可行的。
低合金Cr-Mo钢的最大不足是其高温蠕变断裂强度低,随着参数的提高管壁厚度增加,提高了成本和工艺复杂性,也降低了运行灵活性,日本新研制的HCM2S钢不仅具有优于常规低铬铁素体钢的高温蠕变强度,而且具有优于2.25Cr-1Mo钢的可焊性,也不需要焊前预热和焊后热处理。
HCM2S钢已获得ASME规范认可,列为SA213-T23钢,可用于替代T22钢用于更高的蒸汽参数。
对于过热器、再热器出口集箱及其连接管道,当前所用的P22/X20CrMoV121钢,在技术上认为是合理的壁厚和管径范围内,其极限许用温度略高于550℃。
若采用改善的9%Cr钢P91做集箱,其极限许用温度可超过580℃。
用P91替代P22,尽管其焊接性能不及P22,但壁厚可减薄50%以上,其经济效益十分可观。
在集箱领域中,对P91的进一步改进,新一代9%~12%Cr系钢按其高温蠕变,断裂强度已经进入奥氏体钢的温度范围,在600℃的汽温条件下,其壁厚可比P91减薄40%,如E911,NF616和HCM12A等。
对于过热器、再热器管束,在600℃/600℃的汽温条件下,其最高管壁温度达到650~670℃,因此选用奥氏体是十分必要的,如TP347H,TP347HFG,Super304H等。
甚至部分高温段采用20-25Cr系的奥氏体钢,如HR3C,NF709,TempaloyA-3。
这种材料给予足够的蠕变断裂强度,且由于含Cr高能很好地抗高温腐蚀。
奥氏体钢在受到热疲劳时易出问题,但用于管束,由于口径小管壁薄,产生热疲劳的可能性不大。
六、二次中间再热的调温方式和受热面的合理配置
采用二次再热可使机组的热效率提高1%~2%,但也造成了调温方式和受热面布置上的复杂性。
二次再热锅炉同样有п型和塔式两种炉型。
对于п型布置,一、二次再热器的冷段和低温过热器分别布置在尾部3个分烟道中,热段布置在水平烟道中,通过摆动式燃烧器、烟气挡板和烟气再循环调节来达到设计汽温。
对于塔式布置的炉型,一、二次再热器上、下间隔布置,一次再热汽温可采用摆动燃烧器或少量喷水调节,使用烟气再循环来调节二次汽温。
烟气再循环有冷、热两种。
热烟气从空气预热器入口处取出,这意味着空气预热器在再循环回路之外;冷烟气则取自空气预热器出口处,那么这台空气预热器就存在空气流和烟气流之间出力的不平衡,为此,还需开发出一种再循环空气预热器。
第四节本厂国产600MW超临界锅炉技术特点
一、锅炉主要参数和性能
1.主要参数
本厂国产600MW超临界机组采用DG1900/25.4-II1型锅炉,其主要技术参数如下。
锅炉主要参数:
过热蒸汽:
最大连续蒸发量(B-MCR)1900t/h
额定蒸发量(BRL)1807.9t/h
额定蒸汽压力25.4MPa.g
额定蒸汽温度571℃
再热蒸汽:
蒸汽流量(B-MCR/BRL)1607.6/1525.5t/h
进口/出口蒸汽压力(B-MCR)4.71/4.52MPa.a
进口/出口蒸汽压力(BRL)4.47/4.29MPa.a
进口/出口蒸汽温度(B-MCR)321/569℃
进口/出口蒸汽温度(BRL)315/569℃
给水温度(B-MCR/BRL)282/280℃
本厂国产600MW超临界锅炉的效率也达到了较高的水平,本厂600MW超临界锅炉的主要热力特性计算结果如下:
锅炉热力特性(B-MCR工况):
干烟气热损失LG4.51%
氢燃烧生成水热损失LH0.38%
燃料中水份引起的热损失Lmf0.08%
空气中水份热损失LmA0.06%
未燃尽碳热损失Luc0.70%
辐射及对流热损失LR0.17%
未计入热损失LuA0.30%
计算热效率89.47%(按ASMEPTC4.1计算)
计算热效率(按低位发热量)93.8%
制造厂裕量Lmm%
保证热效率(按低位发热量)
BRL工况不低于93.49%
燃料消耗量266600kg/h
炉膛容积热负荷91kW/m3
炉膛断面热负荷4.98MW/m2
燃烧器区域壁面热负荷1.66MW/m2
空气预热器进风温度(一次/二次风)28/20℃
空气预热器出口热风温度
一次风温度324℃
二次风温度337℃
省煤器出口过剩空气系数α1.15
炉膛出口过剩空气系数α1.14
空气预热器出口烟气修正前温度124℃
空气预热器出口烟气修正后温度118℃
2.锅炉给水及蒸汽品质
补给水量:
正常时(按B-MCR的1%计)19t/h
起动时清洗用水(按B-MCR的25%计)475t/h
补给水制备方式:
一级除盐加混床系统。
锅炉给水质量标准(按CWT工况设计,即联合水处理工况设计)
总硬度~0μmol/l
溶解氧(化水处理后)30~200μg/l
铁≤10μg/l
铜≤5μg/l
二氧化硅≤15μg/l
油~0mg/l
PH值8.0~9.0
电导率25℃≤0.2μS/cm
钠≤5μg/l
3.锅炉基本性能要求
锅炉运行方式:
带基本负荷并具有良好的调峰能力。
制粉系统:
采用中速磨正压直吹冷一次风制粉系统,每炉配6台HP磨煤机(5台运行,1台备用),煤粉细度按200目筛通过量为75%。
给水调节:
机组配置2×50%B-MCR调速汽动给水泵和一台30%B-MCR容量的电动调速给水泵。
汽轮机旁路系统:
暂按采用30%容量二级串联旁路考虑。
空气预热器进风加热方式:
采用热风再循环。
锅炉在投入商业运行后,年利用小时数不小于6500小时,年可用小时数不小于7800小时。
锅炉投产第一年因产品质量和卖方原因引起的强迫停用率不大于2%。
锅炉强迫停用率计算公式如下:
强迫停运小时
强迫停用率=×100%
运行小时+强迫停运小时
机组运行模式符合以下方式
负荷每年小时数
100%4200
75%2120
50%1180
40%300
锅炉完全能适应设计煤种和校核煤种。
燃用设计煤种,在BRL工况下锅炉保证热效率为93.49%(按低位发热值)。
在全部高加停运时,锅炉的蒸汽参数保持在额定值,各受热面不超温,蒸发量满足汽轮机在此条件下达到额定出力。
锅炉在燃用设计煤种时,满足负荷在不大于锅炉的35%B-MCR时,不投油长期安全稳定运行,并在最低稳燃负荷及以上范围内满足自动化投入率100%的要求。
锅炉负荷变化率能够满足下述要求:
在50%~100%B-MCR时,不低于±5%B-MCR/分钟
在30%~50%B-MCR时,不低于±3%B-MCR/分钟
在30%B-MCR以下时,不低于±2%B-MCR/分钟
负荷阶跃:
大于10%汽机额定功率
过热器和再热器温度控制范围,过热汽温在35%~100%B-MCR、再热汽温在50%~100%B-MCR负荷范围时,保持稳定在额定值,偏差不超过±5℃。
锅炉燃烧室的设计承压能力为±5800Pa,当燃烧室突然灭火内爆,瞬时不变形承载能力为±8700Pa。
因燃烧室空气动力场分布不均或其他原因产生的烟温偏差,在炉膛出口水平烟道两侧对称点温差不超过50℃。
若实测值超过该值,保证受热面不超温,采取防止结焦的措施。
过热器和再热器两侧出口的汽温偏差小于10℃。
消除蒸汽侧热力偏差的措施:
(1)炉膛设计合理,较高的炉膛高度,前后墙均匀布置燃烧器,对冲燃烧,减少炉膛出口烟温偏差;
(2)过热器系统设置一次左右交叉,两级喷水减温装在左右侧并分别控制,系统和受热面布置合理,减少蒸汽侧的热力偏差;(3)再热器布置合理,设置一次左右交叉。
过热器蒸汽侧的压降不大于1.41MPa(按B-MCR工况计算)