传送带PLC的设计.docx
《传送带PLC的设计.docx》由会员分享,可在线阅读,更多相关《传送带PLC的设计.docx(13页珍藏版)》请在冰豆网上搜索。
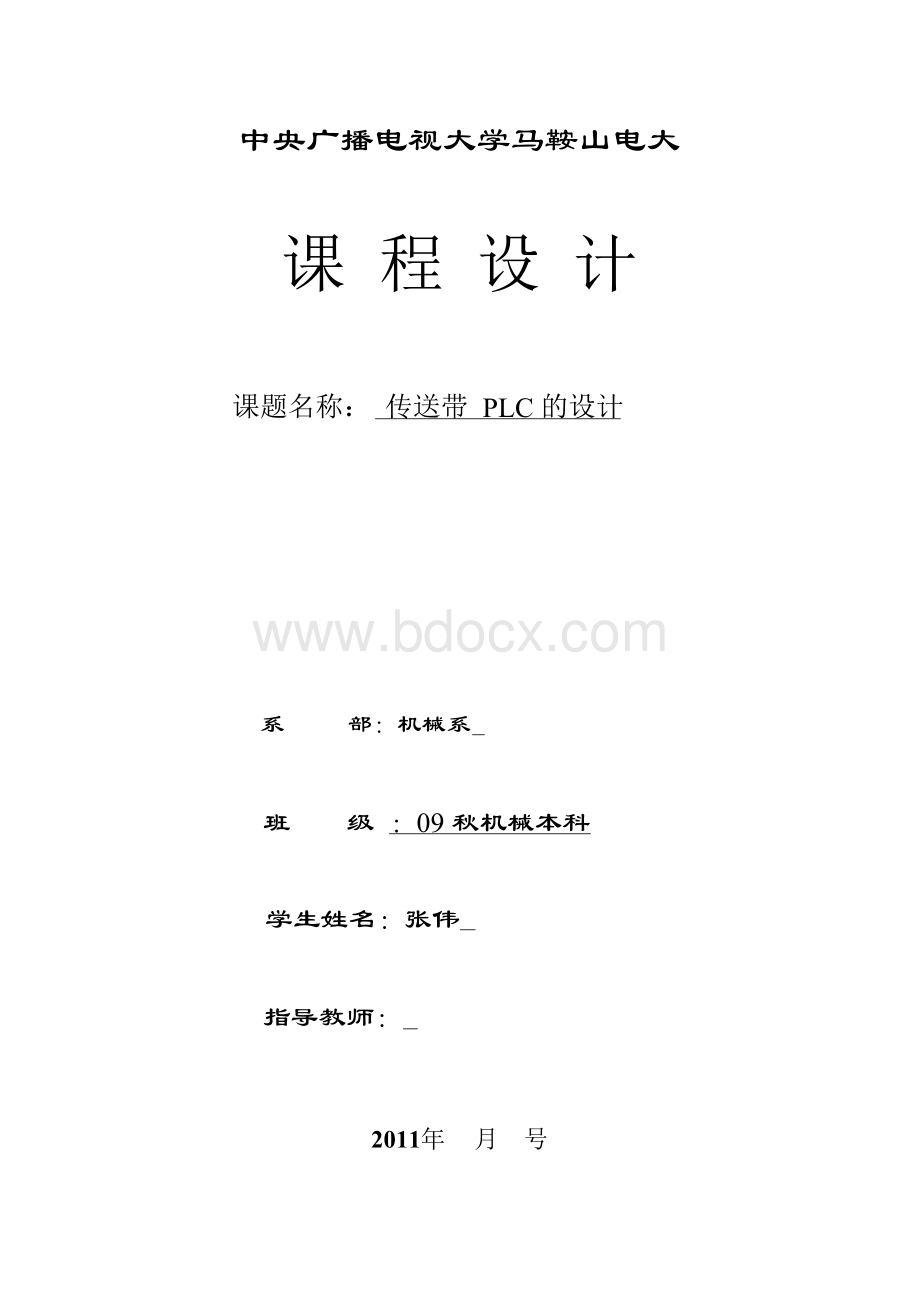
中央广播电视大学马鞍山电大
课程设计
课题名称:
传送带PLC的设计
系 部:
机械系
班 级:
09秋机械本科学生姓名:
张伟
指导教师:
2011年 月 号
设计任务书
09秋机械本科学生:
张伟
课题名称:
传送带PLC的设计要求:
在工厂自动化领域中,传送带是经常用到的。
如图所示为一输送工件的传送带,其动作过程如下:
1.按下启动按钮SB1,电机1、2运转,驱动传送带1、2
移动。
按下停止按钮SB2,电动机停止转动,输送带停止。
2.当工件到达转运点A,使输送带1停止,气缸1动作,将工件送上输送带2。
气缸采用自动归位型,当SQ2检测气缸1到达定点位置时,气缸1复位。
3.当工件到达转运点B,SQ3使输送带2停止,气缸2动作,将工件送上搬运车。
当SQ4检测气缸2到达定点位置时,气缸2复位。
根据本课题要求,用PLC实现对输送带的控制,并画出电气接口图。
指导教师:
气压缸1
电动机1
SQ2
工件A
SQ1
电动机2
搬运车
气压缸2
工件
B
SQ3
SQ4
目 录
引言 5
1.1传送带控制系统的发展概述 6
1.1.1我国传送机的发展 6
1.1.2国内传送带输送机的发展发展趋势 6
1.2总体方案说明 7
传送带控制系统设计及PLC的选取 7
2.1PLC的选取及介绍 7
2.1.1三菱FX2NPLC的主要特点 7
2.1.2PLC的性能指标和分类 7
硬件系统的设计 8
1.I/O口与内部资源的分配 8
2.PLC控制电路接线图 8
3.主电路接线图 8
软件系统的设计 11
1.控制功能的实现 11
2.梯形图语言 12
3.指令表 13
全文总结 13
参考文献 13
【引言】
随着经济的快速发展,企业竞争越来越激烈,为提高效率、降低生产成本,传送带得到了广泛的应用。
传送带广泛应用于工业生产系统。
传送带的应用不仅节约了劳动力,提高了生产效率,而且降低了生产成本,在工业生产中发挥了巨大的作用。
未来传送带设备的将向着大型化发展、扩大使用范围、物料自动分拣、降低能量消耗、减少污染等方面发展。
本设计结合传送带的实际模型,针对PLC本身具有的功能特点,成功的实现对传送带系统的控制,达到了预期的控制效果。
可编程控制器(PLC)是一种专门为在工业环境下应用而设计的数字运算和操作的电子装置。
它采用可以编制程序的存储器,用来在其内部存储执行逻辑运算、顺序运算、计时、计数和算术运算等操作的指令,并能通过数字式或模拟式的输入和输出,控制各种类型的机械或生产过程。
自从可编程控制器诞生以来,电气工程技术人员感受最深刻的也正是可编程控制器二次开发编程十分容易。
它在很大程度上使得工业自动化设计从专业设计院走进了厂矿企业,变成了普通工程技术人员甚至普通工人力所能及的工作。
再加上其体积小、可靠性高、抗干扰能力强、控制功能完善、适用性强、安装接线简单等众多优点,在问世后的短短几十年中获得了突飞猛进的发展,在工业控制中得到了非常广泛的应用。
传送带在工业生产中是必不可少的,以传统继电接触器为控制核心的传送控制系统通过接线表达各元器件之间的关系,要想改变逻辑关系就要改变接线关系,显然是比较麻烦的。
随着可编程控制器的迅猛发展,传统接触继电器控制系统已逐渐被PLC控制系统所替代。
以PLC为控制核心的传送控制系统,在它的接口上接有各种元器件,而各种元器件之间的逻辑关系是通过程序来表达的,改变这种关系只要重新编排原来的程序就行了,比较方便。
1.1传送带控制系统的发展概述
传送带的发展起源于17世纪美国架空索道传送散状物料;19世纪中叶,各种现代结构的传送带输送机相继出现。
此后,传送带又受到机械制造、电机、化
工和冶金工业技术进步的影响,不断完善,逐步由完成车间内部的传送,发展到完成在企业内部、企业之间甚至城市之间的物料搬运,成为物料搬运系统机械化和自动化不可缺少的组成部分。
1.1.1我国传送机的发展
我国早期的工业生产资源传送带输送工序主要是采用手工传送,后来随着科学技术的发展,人们逐渐采用机械化装送。
我国最早使用的传送带输送机主要是从国外进口的,20世纪70年代中期,天津力生制药厂就曾经井口过意大利生产的全传送带输送机,但由于当时我国传送材料的质量及矿产资源制作工艺等都达不到机器传送的要求,使得传送带输送机一直无法正常使用。
所以,全传送带输送机在我国的应用也一直无法得到广泛的推广,以致我国矿产资源生产、工业生产在很长的一段时间里不得不放弃传送带输送机而采用手工操作,使得生产效率极端低下。
20世纪80年代后,相关技术水平获得了飞速发展,传送材料的质量及箱子制作工艺等方面的技术有了明显的进步,全传送带输送机开始得到了应用与推广。
也是此时,我国的矿产资源传送带输送机改变了国外矿产资源一统天下的局面,国产矿产资源传送带输送机开始面市并得到了广泛的应用。
20世纪90年代末期,一些生产量大的生产企业相继开始采用国产的全传送带输送机来代替手工传送,同时国内一些相关的企业也在研制与生产功能更加全面的全自动传送带输送机。
1.1.2国内传送带输送机的发展发展趋势
目前,我国传送产业发展的正处于飞速发展的趋势中。
随着自动化生产不断发展,输送机械化得到了广泛应用。
从大型的工业生产,如矿产资源开发;到中心型的作坊工厂,如零件流水线等等,传送带输送机的应用日益重要。
带式输送机因作为一种输送量大、运行费用低、适用范围广、结构简单、便于维护、能耗较小、使用成本低的输送设备而会得到更宽广的应用范文,市场发展前景十分看好。
未来输送机将向着大型化发展,扩大适用范围,产品多元化,物料自动分拣,减低能量消耗,减少污染等方面发展。
1.2总体方案说明
如图所示,系统有两个传送带,即传送带1和传送带2。
均负责传送工件,传送
带1把工件送到传送带1的末端SQ1处,由气压缸1推至传送带2,传送带2把工件送至传送带2的末端SQ3处,由气压缸2推至搬运小车,运至车间。
2.传送带控制系统设计及PLC的选取
可编程序控制器(ProgrammableLogicalController)是20世纪70年代以来以微处理器为核心,综合计算机计术,自动控制计数和通信技术发展起来的一种新型工业自动控制装置,由于它具有功能强、可靠性高、配置灵活、使用方便及体积小、重量轻等优点,使其在自动化控制的各个领域得到了广泛的应用。
近年来由于微电子技术的发展和进步,使具有完全功能的超大规模集成电路的价格日益便宜,同样也促进可编程序控制器成本大大降低,对于采用可编程序控制器来代替传统继电器-接触器电气控制的系统来改造传统机床,无论从经济上,还是可靠性、维修性,工作寿命及功能上来说,可编程序控制器都是十分经济和划算的,也是的优选方案。
本次设计的传送带控制系统就是基于PLC控制原理而设计的。
2.1PLC的选取及介绍
本次设计采用的是日本三菱FX2N系列的PLC
2.1.1三菱FX2NPLC的主要特点:
一个程序包的单元型可编程序控制器采用装卸式端子台
内装PUN/STOP开关程序存储器
钟表功能
PUN写入
利用键盘保护程序(编程手测、外围设备手册)元件注解
丰富的输出入和特殊扩展设备用SFC表现的编程
简便的应用指令库高速处理
2.1.2PLC的性能指标和分类
1.主要性能指标
1)(I/O点数)
I/O点数是指可编程序控制器外部输入。
输出端子数的总和。
它标志着可以接开关的多少、按钮和可以控制负载的多少。
2)储存容量
存储容量是指可编程序控制器内部用于存放用户程序的存储器容量,一般以步为单位,二进制16位即以一个字为一步
3)扫描速度
一般以执行1000步指令所需要的时间来衡量,单位为ms/k步,也有以执行一步指令所需要时间来计算的,单位用μs/步。
4)功能扩展能力
可编程序控制器除了主模板之外,通常度可配置一些可扩展模板,以适应各种特殊应用的需要,如A/D模板、D/A模板、位置控制模板等。
5)指令系统
指令系统是指一台可编程序控制器指令的总和,是衡量可编程序控制器的主要指标。
硬件系统的设计
1.I/O口与内部资源的分配
本设计的I/O口与内部资源的分配如表所示:
用M1和M2分别作为电动机1
和电动机2的启停辅助继电器。
输入器件
名称
输出器件
名称
X000
启动按钮SB1
Y000
电动机1
X001
限位开关SQ1
Y001
气缸1
X002
限位开关SQ2
Y002
电动机2
X003
限位开关SQ3
Y003
气缸2
X004
限位开关SQ4
Y004
输送带1工作指示灯
X005
停止按钮SB2
Y005
输送带2工作指示灯
内部器件
功能说明
M1
M2
电动机1启停辅助继电器
电动机2启停辅助继电器
2.PLC控制电路接线图
输送带的PLC控制电气接口图如图1示:
图中KM1、KM2分别为电动机1和电动机2转动的接触器。
KM3和KM4分别为气缸1和气缸2动作与复位的接触器。
HL1、HL2分别为输送带1和输送带2的工作指示灯。
3.主电路接线图
主控制电路如图2.所示
COM
COM1
X000
COM2
X001
Y000
KM1
X002
FX2YN00-116M
KM2
X003
Y002
KM3
X004
Y003
KM4
SB1
SQ1SQ2SQ3SQ4
SB2
X005
Y004
Y005N
L
HL1
HL2
~220
2
L3
FU1
FU2
FU3
FU4
KM1
KM2
KM3
KM4
FR1
FR2
FR3
FR4
电动机1
电动机2
气缸1控
制
气缸2控
制
L1
L
软件系统的设计
1.控制功能的实现
本设计中,因为控制功能比较简单,所以采用基本指令组合实现其控制功能。
各部分功能实现如下:
电动机1和电动机2的转动与停止分别用PLC的软组件M1和M2的通与断来控制。
当按下启动按钮SB1时,M1与M2导通,将SB1的常开触与M1和M2的输出线圈串起来,因为是按钮启动,所以再将M1与M2自锁,使其保持导通;当按下停止按钮SB2时,M1和M2都断开,将SB2的常闭触点串入其中,从而实现电动机1与电动机2的停止转动。
当工件到达A点时,输送带1停止,气缸1动作,因此,将限位开关1的常闭触点串入线圈M1的前面,将限位开关1的常开触点驱动气缸1动作,并将其自锁;当到达限位开关2时,气缸1要复位,所以在气缸1线圈前串入限位开
关2的常闭触点,从而实现气缸1的动作与复位。
当工件到达B点时,输送带2停止,气缸2动作,将限位开关3的常闭触点串入线圈M2的前面,将限位开关3的常开触点驱动气缸2动作,并将其自锁;