连铸基本工艺规程.docx
《连铸基本工艺规程.docx》由会员分享,可在线阅读,更多相关《连铸基本工艺规程.docx(39页珍藏版)》请在冰豆网上搜索。
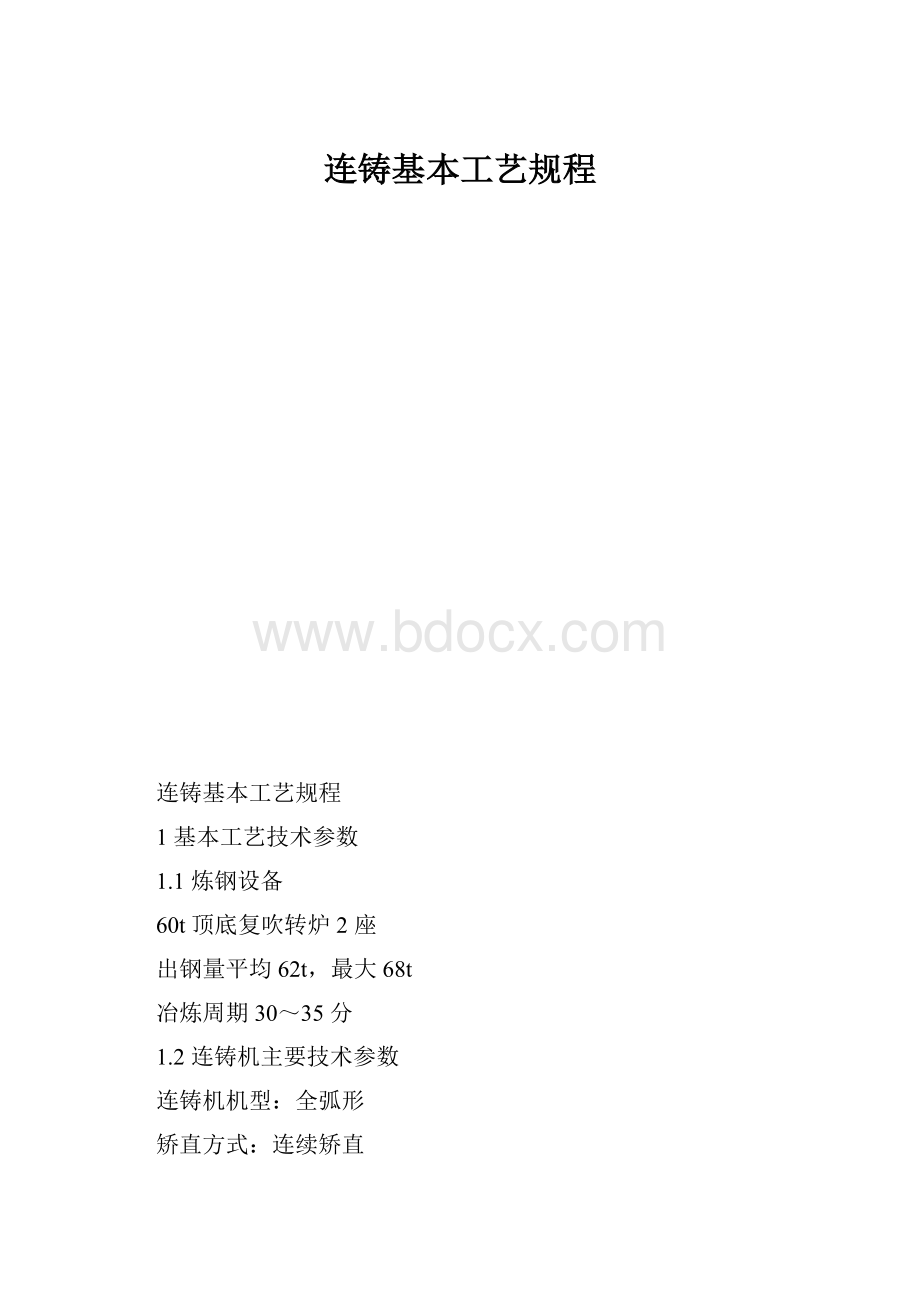
连铸基本工艺规程
连铸基本工艺规程
1基本工艺技术参数
1.1炼钢设备
60t顶底复吹转炉2座
出钢量平均62t,最大68t
冶炼周期30~35分
1.2连铸机主要技术参数
连铸机机型:
全弧形
矫直方式:
连续矫直
连铸机基本半径R=8m
连铸机冶金长度~30m
浇注断面:
方坯:
150×150mm
矩形坯:
165×225mm;165×280mm
定尺长度6000~12000mm
流间距:
1250mm
铸机拉速范围150×150mm方坯:
2.2~2.5m/min,最大3.3m/min;
165×225mm矩形坯:
1.3~1.7m/min,最大2.0m/min;
165×280mm矩形坯:
1.0~1.4m/min,最大1.8m/min;
0.3~4.5m/min。
送引锭杆速度1.0~3.8m/min
结晶器为窄缝导流水套式结晶器,铜管长度900mm
振动装置采用全板簧振动装置,并选择合适的振动参数
(振幅±3~±4,频率100~280次/min),以获得最佳的负滑脱率。
铸坯导向及拉矫装置采用连续矫直五辊拉矫机,铸坯通过矫直区时,其曲率半径由R8m连续均匀变化,应变变化均匀,变形速率低而稳定,矫直区内剪切应力接近零。
二冷系统全水冷却,喷淋管式
引锭杆装入方式下装式
引锭杆存放装置采用电机驱动、弹簧夹紧一对夹辊夹住引锭杆,锁紧销锁紧。
铸坯切割在线火焰切割机
切割辊道分流链条集中传动式辊道
出坯方式双向移坯机
出坯辊道面标高+0.00m
浇注平台标高+8.03m
1.3连铸车间工艺流程
合格钢水→
钢包回转台(钢包称重)→
(钢包保护套管氩气密封)→
中间罐车→
大容量中间罐→
(浸入式)水口→
结晶器→
结晶器振动→
二冷自动控制全水喷淋冷却
↓
连续矫直拉矫机→刚性引锭杆及引锭杆存放装置
↓
切前辊道→
火焰切割机→
输送辊道→
出坯辊道及移钢机→
翻转冷床、固定冷床
1.4钢水质量
1.4.1方(矩形)坯连铸常铸钢种及化学成份见各钢种操作要点。
1.4.2钢中的锰硫比大于25,有害元素Cu≤0.20%,Sn≤0.02%,As≤0.20。
1.4.3转炉出钢必须红包出钢。
1.4.4转炉采用挡渣出钢技术,大包渣厚小于100mm。
1.4.5所有钢种必须吹氩,需要喂线或进行LF精炼钢种,按操作要点执行。
1.4.6钢液的液相线温度按下式计算:
T(℃)=1539-(88×[%C]+8×[%Si]+5×[%Mn]+30×[%P]+25×[%S])
2.3.1.5.7方(矩形)坯连铸钢水温度参考控制参数见表1
表1:
方(矩形)坯连铸钢水温度参考控制参数
钢种
连浇中包钢水温度,℃
开浇中包钢水温度,℃
Q235,HPB235
1525~1545
1535~1555
HRB335,HRB400
1515~1535
1525~1545
1.5结晶器振动
1.5.1结晶器振幅为±3~±4mm
1.5.2振动频率:
100~280次/min(变频调速)
1.5.3振动方式:
正旋曲线
1.6拉坯速度
1.6.1起步时间与拉速
1.6.1.1起步时间(出苗时间)与铸坯断面间关系如下,铸坯宽度大时起步时间取上限,宽度小时取下限
断面规格
起步时间
150×150
30-40s
165×225
55-60s
165×280
60-70s
1.6.1.2浇注开始的初始速度及增减速设定见表2
表2:
浇注开始的初始速度及增减
铸坯断面,mm×mm
初始速度m/min
增速,m/min/min
减速,m/min/min
150×150
0.9~1.1
≤0.30
≤0.30
165×225
0.5~0.7
≤0.20
≤0.20
165×280
0.4~0.6
≤0.15
≤0.15
1.6.2工作拉速
表3:
各断面工作拉速及最大拉速见下表
铸坯断面,mm×mm
工作拉速,m/min
最大拉速,m/min
150×150
2.2~2.5
3.2
165×225
1.3~1.7
2.0
165×280
1.0~1.4
1.8
注:
拉速的设定依据:
冶炼周期按35分钟,钢坯密度按7.6吨/m3
1.7连铸机本体设备主要参数
150×150mm结晶器铜管内腔、外形尺寸见表4(单位:
mm)
表4150×150mm结晶器铜管内腔、外形尺寸见下表
弧面上口
弧面下口
侧面上口
侧面下口
内腔尺寸
154.9~155.3
153.8~154.2
154.9~155.3
153.8~154.2
外形尺寸
181.8~182
181.8~182
181.8~182
181.8~182
1.8能源介质主要参数
1.8.1连铸机冷却水系统
1.8.1.1对水量、水压、水温的要求,详见表5
表5:
供水参数
项目
用量(m3/h)
用点压力(MPa)
进水温度(℃)
温升(℃)
水质
用水制度
结晶器水
800
0.8~1.0
≤40
≤10
软水
闭路
二冷水
325
0.8~1.0
≤40
浊环水
开路
设备冷却水
300
0.4
≤40
净环水
开路
设备喷淋冷却水
125
0.4
≤45
净环水
开路
冲渣水
100
0.35
浊环水
开路
结晶器事故水
300
0.3(供水时间15min)
工业净水
1.8.1.2对水质要求,详见表6
表6:
水质要求
序号
水质要求
单位
结晶器水
二冷水及
设备喷淋冷却水
设备冷却水
1
总硬度(碳酸盐)
DH
1~2
≤12
≤6
2
杂质粒度
mm
≤0.4
≤0.4
≤0.4
3
氯化物含量
mg/l
≤100
≤300
≤300
4
硫酸盐含量
mg/l
≤200
≤500
≤500
5
悬浮物含量
mg/l
≤50
≤50
≤50
6
PH值
7~9
7~9
7~9
7
水损失
%
2
5~10
≤0.5
1.8.2连铸机用氮气(压缩空气)
1.8.2.1氮气(压缩空气)
连铸机气动设备用氮气(压缩空气)由车间管线统一供给,操作参数要求如下:
接点压力:
≥0.6Mpa
纯度:
干燥、无油
平均用量:
4.5Nm3/min
1.8.2.2主要耗气设备如下
表7:
主要耗气设备
耗气点
消耗量(最大)
(Nm3/h)
一次操作时间
(min)
平均消耗量
(Nm3/h)
切割机
3×30
10
~16
油气润滑
间断
~144
中间包修理区
1×200
间断
~40
结晶器修理区
1×20
间断
~4
精整区
1×20
间断
~4
平台用气
1×40
间断
~4
维修消耗点
10×5
间断
~5
仪表用气量
1×200
间断
~40
总量
~260Nm3/h
1.8.3氧气
氧气主要用于铸坯切割和事故处理等。
压力:
≥1.2MPa
纯度:
≥99.5%
表7:
氧气消耗
耗气点
消耗量(最大)
(Nm3/h)
一次操作时间
(min)
平均消耗量
(Nm3/h)
火焰切割机
3×60
0.5~0.9
40
大包烧氧枪
1×50
间断
5
中间包烧氧枪
2×50
间断
10
中间包维修区
1×50
间断
5
切割区事故割枪
2×50
间断
6
机旁事故割枪(浇钢平台,二冷室,拉矫机区)
3×5
间断
3
精整区割枪
3×5
间断
3
结晶器区割枪
1×5
2
维修消耗
10×5
间断
5
总量
160Nm3/h
1.8.4燃气(单台)
1.8.4.1氢氧源
表8:
氢气
耗气点
平均消耗量(Nm3/h)
切割车
~20×5
总量(Nm3/h):
~100
1.8.4.2高炉煤气
表9:
高炉煤气
耗气点
平均消耗量(Nm3/h)
中间包预热
~85×3
浸入式水口
~120×3
平台水口烘烤箱
~20×2
中间包干燥
~25×3
总量(Nm3/h):
~300×3
2连铸主控室技术操作规程
2.1浇铸前的检查与准备
2.1.1认真检查所属设备,正常后方准送引锭,同时检查风、水、电、氧、氢氧源、乙炔、液压等动力源符合工艺要求,各项必备工具和辅料准备就绪。
2.1.1.1开通结晶器冷却水,确认符合下列技术条件:
表10冷却水技术条件
项目
水量,m3/h
水压,MPa
进水温度,℃
结晶器冷却水
85~180
0.8~1.0
≤40
2.1.1.2开通二冷段冷却水,各水咀正常喷水,无缺堵现象,水条应对中,发现问题及时处理。
2.1.1.3结晶器内腔表面光洁,无划痕及损伤,不得有渗漏现象。
2.1.1.4凡连续两次发生裂纹漏钢或连续两炉铸坯有裂纹、菱变缺陷的结晶器必须更换。
2.1.1.5结晶器振动应平稳无摆动,振幅和频率符合工艺要求,对振动参数有特殊要求的钢种执行分钢种操作规程。
2.1.1.6冷却水的水位应处于正常状态,事故水塔要保证发生停电停水事故时结晶器供水压力≮0.2MPa,且不间断供水15min以上。
2.1.1.7快速更换定径水口中间包开浇前,机长必须对液压缸动作、行程和快换机构安装前后防溅板进行检查确认。
2.1.2送引锭
2.1.2.1引锭头应清洁干燥,不得潮湿或粘有废钢。
2.1.2.2送引锭前,操作工要认真检查所属机械、电气及液压设备正常,拉矫辊升降自如,工作正常。
然后,同一操工取得联系,将铸机状态选择开关拨至“送引锭”位置。
2.1.2.3送引锭时,先提升拉矫辊至最大开口度,并把拉矫液压缸压力切换到送引锭状态。
2.1.2.4将引锭杆用升降装置送至拉矫机后,放下拉矫辊,启动拉矫机。
引锭头进入二冷室后由浇钢工安装引锭钩头,以0.6m/min的速度点动进入结晶器内200mm后,再向下拉120mm,然后,再向上送至结晶器内距离下口50-100mm位置。
2.1.2.5送引锭时,操作人员应随时注意引锭杆的运动有无阻碍,要随时准备停止引锭杆行走,保证设备安全。
2.1.2.6浇钢工用石棉绳塞好引锭头与结晶器壁之间的缝隙,并在引锭头四周撒上适量的铁屑(铁屑厚度以15~20mm为宜),最后放入适量冷钢。
2.1.2.7引锭头塞好后盖好结晶器上口,以防异物落入。
拉矫机、振动电机断电,
开浇前浇钢工应检查引锭是否下滑,如果引锭下滑,需重新送引锭。
2.1.2.8浇钢工用木塞或堵锥堵好中间包水口,并在水口内放入引流砂或硅钙粉。
2.1.3连铸对钢水的基本要求
2.1.3.1钢水成分符合相关标准及作业文件要求,脱氧正常,流动性良好。
连浇炉次必须为同钢种,浇钢过程中严禁向钢包内和中间包内追加合金料调成分。
2.1.3.2连铸钢水到平台温度要求执行分钢种操作规程。
2.2浇注操作
2.2.1中间包浇注
2.2.1.1中间包车升起,开至浇注位结晶器上方,并调整中间包水口对中结
晶器上口,中间包下降将浸入式水口插入结晶器内一定深度。
2.2.1.2钢水接受跨的吊车将转炉合格钢水吊运到连铸机钢包回转台。
2.2.1.3回转台旋转180至结晶器上方的浇注位,大包工安装滑动水口液压皮管,安装钢包长水口,开启滑动水口钢水注入中间包内。
2.2.1.4中间包钢水通过定径水口(或浸入式水口)注入结晶器内,钢水液面上升到一定的高度(400mm)时,启动操作箱上的“浇注”按钮,拉矫机以给定的起步拉速开始拉坯,与此同时,结晶器振动装置,二冷室排蒸汽风机等设备自动启动;二冷水阀门打开。
起步拉速参照表2设定,遇钢水温度过高或过低时,应适当延长或缩短起步时间。
2.2.1.5带液芯的铸坯由引锭杆牵引离开结晶器下口,各区二冷水对带液
芯的铸坯直接喷淋冷却,喷水量按一定比水量随拉速变化自动调节。
2.2.1.6铸坯进入拉矫机并行进到脱坯位后,拉矫机脱坯辊压下矫直成水
平。
2.2.1.7引锭头与铸坯分离后,启动引锭杆存放装置将引锭杆收入存放位。
2.2.1.8矫直后的铸坯通过切前辊道,进入火焰切割机进行切割。
2.2.1.9切割成定尺的铸坯由切后辊道和输送辊道送至出坯辊道,碰固定
挡板后停止。
2.2.1.10铸坯由移钢机横向移送至冷床。
2.2.1.113#连铸机出坯辊道两侧分别配置有液压步进式翻转冷床和滑轨式固定冷床,150×150方坯由移坯车送至翻转冷床上,铸坯在冷床上翻转、步进冷却,进入冷床后的收集台架上收集成排,用该跨吊车卸下堆存冷却后外运。
3#连铸机在滑轨式固定冷床后设置有热送辊道,当150×150方铸坯需要热送时
由此辊道运出。
在该情况下,铸坯不再上翻转冷床冷却。
3#连铸机165×225~280矩形坯由移坯车送至滑轨式固定冷床上,用吊车卸下
堆存冷却。
2.3浇注中异常事故的处理
2.3.1结晶器冷却水入口压力低,通知浇钢工降低拉速,并告之调度室,增开备用泵。
若入口压力仍低应立即通知停浇。
2.3.2结晶器水温差△T高报警,应立即通知浇钢工降低拉速。
2.3.3结晶器水流量报警后应立即通知大包停浇,确认事故水自动投入。
通知中包浇钢工降低拉速,待结晶器冷却水正常后,通知浇钢工恢复正常拉速,如10分钟内冷却水仍不正常,应立即通知中包工停浇。
2.3.4发生漏钢事故的处理
2.3.4.1确认漏钢信息,选择“重拉坯”。
2.3.4.2将浇钢情况通知调度。
2.4停浇
2.4.1浇次结束前,监视大包内钢水重量,通知大包工准备关闭滑板,并记录钢包重量。
2.4.2监视中包钢水重量,通知浇钢工降速,并记录钢水量。
2.4.3确认铸坯位置监视,二冷水监视流量确认,确认二冷水阀门关闭顺序。
2.4.4监视夹紧辊提升顺序。
2.5停机操作
2.5.1油烟风机停止。
2.5.2二冷蒸汽排风机停止。
3.大包浇注技术操作规程
3.1检查与准备
3.1.1检查确认大包回转台正常状态下旋转定位、升降、润滑、称量、锁定、运转正常。
3.1.2检查确认大包回转台事故状态下旋转定位、升降、润滑、称量、锁定、运转正常。
3.1.3检查确认钢包加盖装置旋转、升降液压系统动作正常,停位准确。
3.1.4大包回转台A、B臂大包滑动水口液压缸驱动正常,停位准确。
3.1.5各种工器具及原辅材料准备齐全,数量满足生产需求。
3.2大包浇注操作
3.2.1大包吊座到回转台,转到浇注位,迅速安装滑动水口机构快速接头。
3.2.2中间包车开到浇注位置,大包回转台对位准确后锁定回转台。
3.2.3安装大包保护套管,降回转臂,降钢包盖。
3.2.4打开滑动水口,当中包液面上升到不小于250mm时,向中间包内加入中包覆盖剂,覆盖住整个中间包液面。
3.2.5钢包采用自动引流时,连铸第一包钢水,中间包液面达到400mm,连浇炉次中间包液面达到300mm时,钢包浇注工应及时试开关一次滑板。
3.2.6连铸第一包中间包液面低于400mm,连浇炉次液面低于300mm,钢包应保持全流浇注;正常浇注过程中,中间包液面应控制在400mm左右,在钢包浇注结束前要适当提高液面。
3.2.7连浇时,当钢包内钢水量少于5t时,要注意观察钢包钢流,发现下渣立即关闭滑动水口。
3.2.8钢包开浇后5min内天车不得离开,同一浇钢平台两台连铸机同时浇铸时必须有一部重包天车在平台值守。
3.2.9中间包的测温操作
3.2.9.1测温地点:
中间包内靠近水口的预热孔,距中间包壁距离不小于400mm。
3.2.9.2测温枪插入深度:
~200mm。
3.2.9.3正常情况下的测温:
表11中间包测温时间
测温测温时间(距大包开浇约Xmin)
测温
测温时间(距大包开浇约Xmin)
1
3
2
6
3
15
4
30
3.2.10下列异常情况下增加测温次数:
3.2.10.1中间包更换后。
3.2.10.2钢水低温时。
3.2.10.3与前次测量值相差大于8℃
3.2.11中间包钢水取样
3.2.11.1大包浇注约1/3至1/2时,在中包内取A样,浇注约4/5时取B样。
3.2.11.2取样部位:
中间包靠近水口预热孔内,取样器插入钢水深度不小于300mm。
3.2.12大包浇钢工应随时观察钢水的流动性,并与中包浇钢工取得联系调整拉速,保持中间包液面不得低于800mm,防止卷渣漏钢。
3.2.13当大包钢水接近浇完时,应保证中间包内钢液面不低850mm,以保证实现连浇,允许液面偏差±50mm内。
3.2.14钢水即将浇完时,将保护套管移开。
3.2.15大包见渣后立即关闭水口,不允许将渣放入中包。
3.2.16大包浇钢工在浇注前和浇注过程中应经常检查回转台事故操作油源的压力与供油情况,以保证电动事故状态下的液压系统正常驱动。
4.中间包浇铸工技术操作规程
4.1检查与准备
4.1.1结晶器检查
4.1.1.1大小盖板应配套、放置整齐,残钢、残渣清理干净,结晶器与盖板之间间隙要用石棉绳塞好,并用耐火泥抹平。
4.1.1.2检查结晶器,并清除其上角的残余钢渣。
4.1.1.3结晶器铜板内壁刮伤或划痕深度应小于1.0mm。
4.1.1.4每天每班测量一次结晶器倒锥度,当磨损后的锥度超过规定值时,应更换结晶器。
4.1.1.5检查结晶器(165×225、165×280)足辊转动是否灵活,发现不转或转动不灵活,应通知更换。
4.1.1.6检查工器具是否齐全,各种原辅材料是否满足生产需要。
4.1.2浇铸前送引锭
4.1.2.1将引锭杆用升降装置送至拉矫机后,放下拉矫辊,启动拉矫机。
引锭头进入二冷室后由浇钢工安装引锭钩头,以0.6m/min的速度点动进入结晶器内200mm后,再向下拉120mm,然后,再向上送至结晶器内距离下口50-100mm位置。
4.1.2.2确认引锭无下滑,进行干燥引锭头和结晶器操作,用专用工具将纸绳塞紧结晶器壁与引锭头之间的间隙,要求不留缝隙,孔洞塞后的纸绳要略高于引锭头表面,以防钢水钻入。
4.1.2.3在转炉开始吹氧时,开始送引锭。
4.1.2.4在引锭头上均匀铺撒20-30mm厚的钢屑(钉尖),冷却钢屑要求无潮湿、无油脂。
4.1.2.5为了缩短头坯凝固时间,在引锭头上加适量专用冷钢(盘条)。
4.1.2.6在结晶器钢板表面均匀涂上一层油脂。
4.1.2.7大包钢水上回转台时,通知主控将工作方式选择开关置于“浇注准备”
位。
4.2浇注操作
4.2.1中间包浇注
4.2.1.1中包开浇
4.2.1.1.1钢包吊上座架(或回转台并转到浇钢位置)后无异常,中间包停止烘烤并迅速开到浇钢位置,将中间包水口与结晶器对中。
4.2.1.1.2中间包采用带长水口开浇(钢水温度偏低时,可先开浇后上长水口)。
要保证长水口垂直且对中,长水口在使用前应预热不少于半小时,尤其是铝碳长水口。
4.2.1.1.3中间包液面达到200mm左右,加入中包覆盖剂或炭化稻壳。
4.2.1.1.4中间包液面达到400mm后,进行测温并开浇。
中间包水口未自引,可烧氧引流。
4.2.1.1.5中间包开浇前由机长通知一操工,一操工通知配水人员,各方面确认后方可开浇。
4.2.2结晶器液面及拉速控制
4.2.2.1中包温度偏低或是中包烘烤不好时,液面在300mm时开浇。
4.2.2.2采用油润滑时,起步时给油。
采用保护渣润滑时,当结晶器钢液面淹没长水口侧孔时,加入保护渣,保护渣应均匀覆盖液面,勤加少加,以液面不亮为准,渣条长大时及时捞出。
当液面距上口150mm时,启动拉矫机,并注意结晶器是否振动,是否有二冷水喷出声。
4.2.2.3结晶器液面应控制在800mm左右的高度上,即渣面距结晶器上口100mm左右,液面控制应平稳。
起步正常后,控制水口浸入深度为50~80mm。
4.2.2.4开浇初期拉速逐步提高,至铸坯出拉矫机后升到正常拉速,升速过程要平稳,要求铸坯断面≥165×165的连铸机一次变速≯0.1m/min;起步拉速控制在1.5m/min,拉速高时应使用摆槽。
4.2.2.5正常浇注过程中,钢包开浇5min时测量一次中间包钢水温度,以后间隔10~15min测量一次,一操工做好时间与温度记录。
浇注过程中钢包或中间包调温必须使用同钢种洁净废钢。
4.2.2.6浇注过程中结晶器液面控制在距上口50mm以下,禁止液面超高。
4.2.2.7浇注过程中,结晶器保护渣变得过分粘稠,铺展性下降,就应进行换渣,用捞渣棒将熔渣层从结晶器二侧捞除,边捞边添新渣。
4.2.2.8浇注中出现液面波动,应随时将“渣块”“渣条”挑出,以防卷入钢液造成事故,当液面波动大于10mm时,浇钢工应控制好液面平稳,在严重时应适当降低速予以减缓。
4.2.2.9一般情况下,一个中间包只允许浇注同一钢种,不同钢种连浇必须更换中间包。
如有特殊试验钢,同一中间包需浇注不同钢种时,须有公司技术主管部门出具的质量计划。
原则上换大包不允许降低拉速,但如遇引流时间长例外,要严防停机或中包水口下渣。
4.3浇注结束程序
4.3.1当最后一炉中包浇完前,前3-5min(以中包液面低至300mm为准)开始计划堵流,以保证尾坯质量。
停浇后仍维持尾坯拉速3~5min,再快速拉下。
同时,应停止向结晶器供油或添加保护渣。
4.3.2当铸坯末端拉出结晶器时,关闭振动装置,延时后关闭结晶器冷却水,按程序关闭二冷水,二冷风机。
4.4换中包连浇操作
4.4.1换包前的准备
4.4.1.1计划换包时,必须提前一炉通知调度按连铸第一炉供应钢水,并做好换包准备。
4.4.1.2按铸机断面准备好操作工具。
4.4.1.3中间包更换时间标准:
中间包更换时间≤3.5分钟。
4.4.1.4更换中间包时需将结晶器内残余保护渣捞净,中间包停浇至大包开浇的时间间隔不得超过10min。
4.4.2快速更换中间包操作
4.4.2.1当大包停浇后,旋转90°,此时中包操作工应停止加保护渣
4.4.2.2中包液面到150mm时,迅速堵流开走旧中包车。
4.4.2.3捞出断碎水口等杂质及结晶器内旧渣。
4.4.2.4新中包对中后,大包应立即开浇,操作按正常开浇操作。
4.4.2.5大包开浇后至中包规定液面,新中包开浇,用挡流板挡流,重新在液面上加入保护渣。
4.4.2.6起步时间和起步拉速按铸机开浇标准进行。
4.4.2.7快速更换定径水口中间包,浇注过程中钢流增大,拉速过快时必须更换新滑块。
更换新滑块前,把垫块及滑块在备用位置预热10分钟以上。
4.4.2.8更换新滑块时,首先将