1#机管道施工组织设计.docx
《1#机管道施工组织设计.docx》由会员分享,可在线阅读,更多相关《1#机管道施工组织设计.docx(78页珍藏版)》请在冰豆网上搜索。
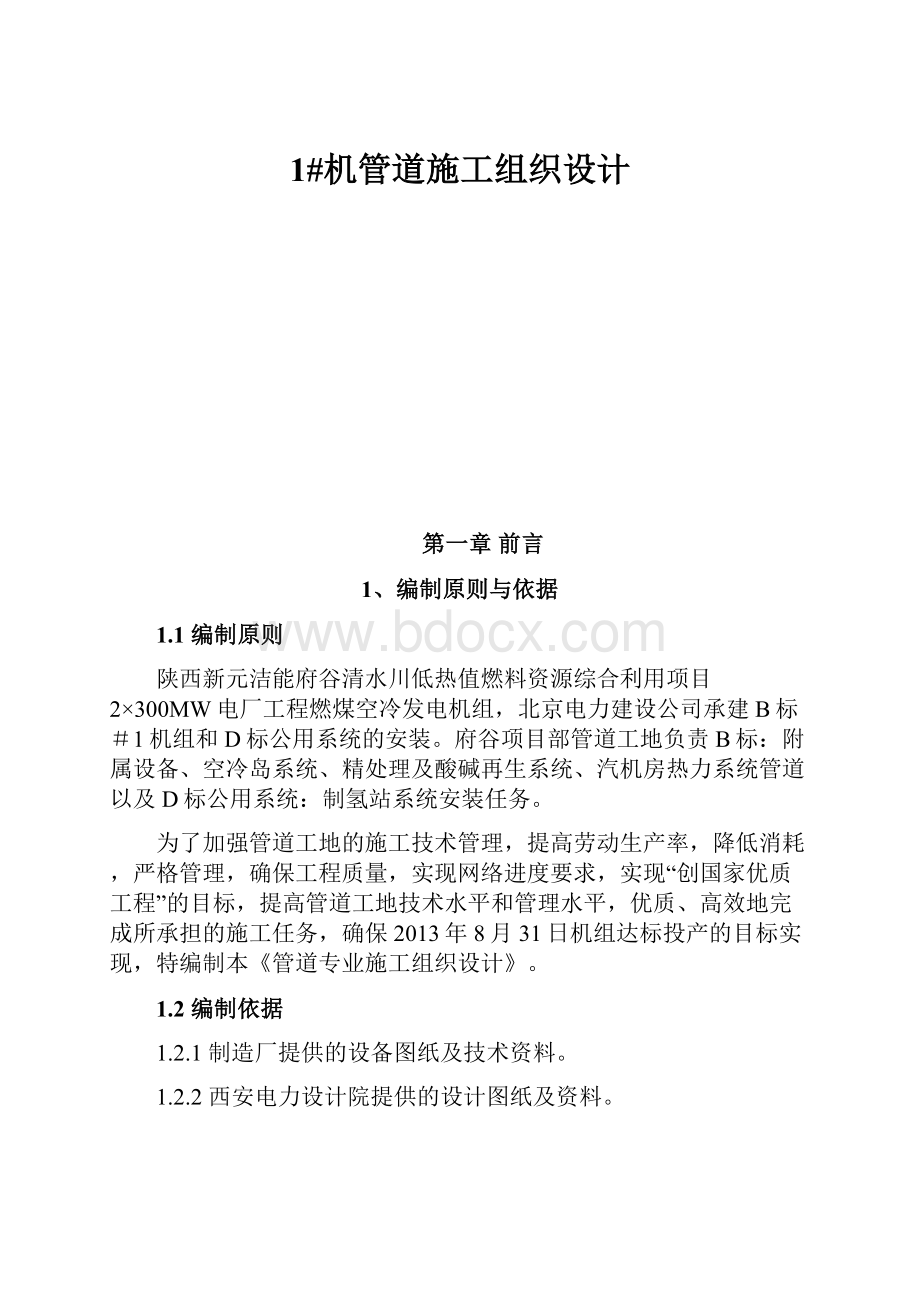
1#机管道施工组织设计
第一章前言
1、编制原则与依据
1.1编制原则
陕西新元洁能府谷清水川低热值燃料资源综合利用项目2×300MW电厂工程燃煤空冷发电机组,北京电力建设公司承建B标#1机组和D标公用系统的安装。
府谷项目部管道工地负责B标:
附属设备、空冷岛系统、精处理及酸碱再生系统、汽机房热力系统管道以及D标公用系统:
制氢站系统安装任务。
为了加强管道工地的施工技术管理,提高劳动生产率,降低消耗,严格管理,确保工程质量,实现网络进度要求,实现“创国家优质工程”的目标,提高管道工地技术水平和管理水平,优质、高效地完成所承担的施工任务,确保2013年8月31日机组达标投产的目标实现,特编制本《管道专业施工组织设计》。
1.2编制依据
1.2.1制造厂提供的设备图纸及技术资料。
1.2.2西安电力设计院提供的设计图纸及资料。
1.2.3《陕西新元洁能府谷清水川低热值燃料资源综合利用项目2×300MW电厂工程)#1机组施工组织总设计》(北京电力建设公司)。
1.2.4《电力建设施工及验收技术规范》(汽机篇1996年版,管道篇1994年版,水处理及制氢装置篇2004年版)。
1.2.5《火电施工质量检验及评定标准》(汽机篇2009年版,管道篇2009年版,水处理及制氢装置篇2009年版,土建篇DL/T5210.1-2005。
1.2.6《电力建设安全健康与环境管理工作规定》(2002-01-21实施)。
1.2.7《质量保证手册》(BPCC-QA-C-2002)。
1.2.8《工程建设标准强制性条文》(电力工程部分2011年)
1.2.9《反事故斗争二十五项措施》(国家电网安监[2006]364号)
2、工程质量目标
在府谷新元洁能#1机组管道工地任务施工中,贯彻执行公司制定的质量方针,实现如下工程质量目标,争创国优工程。
2.1全面完成分部试运和整套试运,各项技术经济指标达到验标的优良级标准,辅机试运优良率100%,机组整套试运达到优良,机组建设质量总评达到优良。
2.2热力系统、油系统等严密无渗漏。
2.3单位工程优良率100%;分部和分项工程合格品率达到100%、分部分项优良品率:
安装工程部分应达到100%,建筑工程部分应达到100%。
2.4实现汽机抽真空一次成功。
2.5汽机真空系统严密性<0.33kpa/min。
3、组织机构
根据府谷新元洁能项目部总体规划,为优质高效地完成施工任务,加强施工质量的过程控制,实现机组达标投产,管道工地组织机构设立如下:
3.1施工班组
成立辅属班、高压管道班、中低压管道班、空冷班、空冷配制班、厂区管网班六个班组,以完成管道专业各项施工工作。
第二章工程概况
1、工程规模
本工程系新建电厂,规划容量2x300MW,不再考虑扩建条件。
本期工程的建设规模为2x300MW亚临界空冷机组。
本期工程机组采用东方电气集团东方锅炉股份有限公司生产的国产亚临界循环流化床锅炉,采用上海电气集团生产的汽轮发电机组,同步建设烟气脱硫、脱硝设施。
工期要求:
于2012年3月1日浇筑第一罐混凝土,第1台机组计划于2013年8月31日投产。
质量目标:
实现高标准达标投产,确保电力行业优质工程,争创国家级优质工程。
锅炉为循环流化床、亚临界参数、一次中间再热汽包炉、紧身封闭、平衡通风、固态排渣、全钢架悬吊结构、炉顶设轻型金属屋面。
最大连续蒸发量Q=1057t/h,过热器出口压力:
17.5MPa(a);过热蒸汽出口温度/再热蒸汽出口温度:
541℃/541℃。
汽轮机为上海汽轮机有限责任公司生产的KN300-16.7/537/537型亚临界中间再热空冷汽轮机单轴双缸双排汽,铭牌出力300MW主汽压力16.7Mpa(a)设计背压13kPa(a)主汽温度537℃再热蒸汽温度537℃。
发电机为上海汽轮发电机厂有限责任公司生产的水氢氢冷却汽轮发电机静态励磁。
工程设计为西北电力设计院,工程监理为西北电力建设工程监理有限责任公司。
其中由北京电力建设公司承建B、D两个标段的施工任务。
2、主厂房结构及布置特点简介
主厂房采用现浇钢筋混凝土框排架结构,汽机房、煤仓间、锅炉房顺列布置。
2台机组间设置一道伸缩缝,伸缩缝处设双柱,柱距为1.5m。
汽机房跨度为34m,煤仓间跨度为13.5m,除氧器布置于汽机房14.70m层,锅炉采用紧身封闭岛式布置。
主厂房各层栏杆采用不锈钢管栏杆。
圆形钢煤斗采用支承式钢结构,内衬为不锈钢耐磨层。
固定端采用钢筋混凝土框架加抗风桁架结构。
扩建端在运转层以上为钢结构以下为钢筋混凝土结构。
包括#1机主厂房的建筑、结构(汽机房、除氧煤仓间、炉前通道、锅炉房、电梯井、地下设施等)及上下水、采暖通风、照明、除尘、防雷接地等。
3、管道工地所属主要设备及其系统介绍
3.1主要设备介绍
3.1.1高压加热器
该机组配置三台卧式、管壳式高压加热器。
3.1.2低压加热器
该机组配3台卧式、管壳式低压加热器,其中#7加热器布置在排汽装置喉部。
3.1.3除氧器
每台机组配置一台内置、卧式除氧器,除氧器技术参数:
水箱有效容积150m3
除氧器最大出力1118t/h
最大工作压力:
0.98MPa
最高工作温度:
353℃
3.2主要系统介绍
3.2.1主蒸汽系统
主蒸汽管道采用2-1-2连接方式,从过热器出口集箱双管接出,合成一路后在进汽机前分成两路,分别接至汽轮机左右侧高压主汽门。
主蒸汽主管管径为Di419.1×75mm,支管管径为Di298.5×54mm,材质为A335P91。
3.2.2再热蒸汽系统
再热蒸汽系统分为冷再热蒸汽管道、热再热蒸汽管道,均采用2-1-2布置,。
冷再热蒸汽管道从高压缸两个排汽口引出,在机头处汇成一根母管,到锅炉前再分成两根支管分别接至再热器入口联箱。
热再热蒸汽管道从再热器出口联箱两侧引出,合成一路后在汽机前分别进入左右侧再热联合汽阀。
热再热蒸汽主管管径为Di914.4×33mm,支管管径为Di635×24mm,材质为A335P91。
冷再热蒸汽主管管径为φ965.2×23mm,支管管径为φ660.4×16mm,材质为A672B70CL32。
3.2.3汽机旁路系统
为改善机组起停性能和回收工质,机组设有高压旁路及低压旁路两级串联旁路系统。
高压旁路从主蒸汽管道接出,经减温减压接至冷再热蒸汽管道,减温水来自给水系统。
低压旁路从热再热蒸汽侧接出后,经减温减压后接至排汽装置,减温水来自凝结水系统。
高压旁路阀前管道管径为Di215.9×40mm,材质为A335P91;阀后管道管径为ф406.4×10mm,材质为A672B70CL32。
低压旁路阀前管道管径为Di431.7×17mm材质为A335P91;阀后管道管径为φ720×11mm,材质为A672B70CL32。
3.2.4给水系统
给水系统设置3台35%BMCR容量电动调速给水泵。
采用3台卧式高压加热器,3台高压加热器设置大旁路。
每台给水泵出口设有最小流量再循环管,保证在机组启动和低负荷工况流经泵的流量大于其允许的最小流量,每根再循环管道单独接至除氧器。
给水系统为锅炉过热器的减温器、再热器减温器、高压旁路减温器提供减温水。
主给水管道管径为ф508×46mm,材质为15NiCuMoNb。
3.2.5凝结水系统
凝结水系统设2台凝结水泵,一台运行,一台备用。
本系统配置3台低压加热器,均设小旁路。
凝结水由排汽装置水箱引出,经凝结水泵升压后,经凝结水精处理装置、轴封加热器、低压加热器至除氧器。
凝结水系统设有最小流量再循环系统,自轴封加热器后的凝结水管路接出,经最小流量阀回至排汽装置。
每台机组设有一台300m3的凝结水贮水箱,在正常运行时向排汽装置热井补水和回收热井高水位时的回水,以及提供化学补充水,为机组启动间提供启动注水。
每台补充水箱配备1台凝结水输送泵,2台凝结水补充水泵。
3.2.6抽汽系统
汽轮机具有七级非调整抽汽。
一、二、三级抽汽分别向三台高压加热器供汽,四级抽汽除供除氧器外,还向高压辅助蒸汽联箱供汽。
二级抽汽还作为辅助蒸汽系统的备用汽源。
五至七级抽汽分别向三台低压加热器供汽,五级抽汽除供五号低压加热器外,还向低压辅助蒸汽联箱供汽。
3.2.7加热器疏水放气系统
三台高压加热器的正常疏水逐级自流到除氧器,事故疏水各自排入排汽装置前的疏水扩容器经扩容释压后排入排汽装置。
除氧器溢流放水到排汽装置。
低压加热器的正常疏水逐级自流到排汽装置,事故疏水排入排汽装置。
每台加热器(包括除氧器)均设有启动排气和连续排气,以排除加热器中的不凝结气体。
所有高压加热器的连续排气至除氧器,启动排汽排大气。
所有低压加热器及疏水冷却器的启动排气和运行排气接至排汽装置,除氧器放气排至大气或到排汽装置。
3.2.8辅助蒸汽系统
每台机组设低压辅助蒸汽联箱及高压辅助蒸汽联箱各一台,两台机组间设一根辅助蒸汽联络母管及一根辅助蒸汽联络母管,之间设隔离门。
1号机组启动时由厂区启动蒸汽管道供汽,启动汽源来自启动锅炉,接入高压辅汽联箱。
2号机组启动时由已运行机组辅助蒸汽经高低压联络母管供汽。
本机四段、五段抽汽作为辅助蒸汽系统的正常汽源,当本机四段抽汽参数不能满足系统要求时由备用汽源再热冷段向辅助蒸汽系统供汽,当本机五段抽汽参数不能满足系统要求时由备用汽源高压辅助蒸汽经压力调节阀向低压辅助蒸汽系统供汽,当本机冷段抽汽参数不能满足系统要求时由邻机高、低压辅助蒸汽联箱向本机辅助蒸汽系统供汽。
3.2.9闭式冷却水系统
本系统向主厂房(包括汽机房和锅炉房)的转动设备提供冷却水。
该系统主要由10m3闭式水箱、闭式循环水泵及闭式水热交换器组成。
其冷却水主要为主机冷油器、发电机氢气冷却器、定子冷却器、密封油冷却器、机械真空泵、电泵的润滑油工作油冷却器、电泵电机冷却器等设备冷却用,然后从冷却设备排出,回至闭式水回水管。
主要设备的冷却器冷却水出口管道上设有流量调节阀,用以调节冷却水量,控制冷却器内介质和出口温度。
3.2.10空冷岛
低压缸排汽经过排汽装置送至空冷岛冷却为凝结水后返回至排汽装置。
空冷系统包括空冷凝汽器平台整体结构、平台基础、支柱、平台绗架、平台板、平台步道、步梯、电梯、挡风墙及其支撑结构、分隔墙及其支撑结构、风机桥架及减震装置、风机风筒、风机护网、汽机排气管道支架、管束支架、起吊结构、其它各种设备管道支架等。
由汽轮机低压缸来的排汽,经过一根φ6000×16的排汽管道,再分成6根φ2500×12支管进入空冷凝汽器,每根支管对应一列冷却单元。
排汽经空冷凝汽器冷却后,凝结水经空冷平台上的凝结水收集母管汇合,然后自流进入主厂房内的排汽装置热井。
空冷凝汽器抽真空系统在机组启动时将空冷凝汽器及其附属管道和设备中的空气抽出以达到启动要求的真空度,正常运行时除去空冷凝汽器空气区积聚的非凝结气体,以维持真空。
每台机组安装3台50%容量水环真空泵组,机组正常运行时,2台运行,1台备用;机组启动时,3台真空泵同时运行,加快抽真空速度。
3.2.11其他系统
其他系统包括氢气系统、凝结水精处理及再生系统、主厂房仪用及厂用压缩空气系统、化学加药系统、汽水取样等。
3.2.12D标部分
管道除负责上述A标施工任务外,还承担D标部分制氢站、厂区内管网系统。
汽机房加药系统:
由加药间经加药管道分别向除氧器下降管,精处理出水母管,及闭式泵出口水母管加药。
制氢系统:
中压水电解槽电解出氢、氧气经吸附器、冷凝分离器、氢气贮存罐送至主厂房氢气管道。
4、主要设备技术规范
4.1除氧器
序号
项目
单位
除氧器
1
型号
GC-2050/GS-235
2
设计压力
Mpa
1.28
3
设计温度
OC
365
4
最高工作温度
OC
353
5
最高工作压力
Mpa
0.98
6
安全阀起跳压力
Mpa
1.23
7
安全阀排气量
KG/H
112421(两只)
8
有效容积
M3
150
9
腐蚀预量
mm
1.6
10
工作介质
汽,水
4.2高压加热器
序号
设备名称
项目
单位
管侧
壳侧
1
#1高压
加热器
型号:
JG-2520-2-3
2
设计压力
MPa
35
8.11
3
设计温度
OC
325
410/325
4
表面受热面积
m2
2520
5
工作介质
水
水和水蒸汽
7
#2高压
加热器
型号:
JG-2460-3-2
8
设计压力
MPa
35
5.55
9
设计温度
OC
300
350/300
10
表面受热面积
m2
2460
11
工作介质
水
水和水蒸汽
12
#3高压
加热器
型号:
JG-1520-3-1
13
设计压力
Mpa
35
2.8
14
设计温度
OC
258
510/258
15
表面受热面积
m2
1520
16
工作介质
水
水和水蒸汽
4.3低压加热器
序号
设备名称
项目
单位
管侧
壳侧
1
#5低压
加热器
型号:
JD-1200-1-1
2
设计压力
MPa
4.0
0.6
3
设计温度
℃
160
280/160
4
工作压力
MPa
1.7
0.47
5
加热面积
m2
1200
7
工作介质
凝结水
水蒸汽和水
8
#6低压
加热器
型号:
JD-1280-2-1
9
设计压力
MPa
4.0
0.35
10
设计温度
OC
140
200/140
11
最大工作压力
MPa
4.0
0.35
12
加热面积
m2
1280
13
工作介质
凝结水
水蒸汽和水
5、主要工程量统计表
5.1主厂房主要设备统计表
序号
设备名称
型号或规范
单位
数量
1
高压加热器
卧式、单列、管壳式
台
3
2
内置式除氧器
卧式、有效容积150m3
台
1
3
低压加热器
卧式、单列、管壳式
台
3
4
轴封冷却器
台
1
5
闭式冷却水热交换器
板式
台
3
6
闭式循环冷却水膨胀水箱
有效容积10m3
台
1
7
低压辅助蒸汽联箱
台
1
8
高压辅助蒸汽联箱
台
1
9
凝结水补充水箱
容积300m3
台
1
10
凝结水精处理装置
含体外再生系统
套
1
11
高压给水系统
W15NiCuMoNb5
套
1
12
主蒸汽系统
A335P91
套
1
13
再热热段系统
A335P91
套
1
14
再热冷段系统
A672B70CL32
套
1
15
高低压旁路系统
套
各1
16
抽汽系统
套
1
17
凝结水系统
套
1
18
辅助蒸汽系统
套
1
19
抽真空系统
套
1
20
化学加药系统
套
1
21
辅机循环冷却水系统
套
1
22
闭式循环冷却水系统
套
1
23
高低加疏水放汽系统
套
1
5.2空冷岛主要设备统计表
序号
部件名称
重量或件数
1
排汽管道(总重/最重部分)
510t
2
蒸汽分配管道(总重)
130t
3
管束和下联箱
288件
4
风机、齿轮箱、电机、变频器
30套
5
风机护网
30件
6
风筒
30件
5.3C标化学部分主要设备统计表
序号
系统名称
设备名称
单位
数量
1
制氢系统
中压水电解槽
套
1
2
氢分离器
套
1
3
氢洗涤器
套
1
4
氧分离器
套
1
5
氢气贮存罐
台
4
6
碱液箱
台
1
7
碱液循环泵
台
1
8
蒸馏水箱
台
1
第三章主要施工项目方案及措施
1、高压管道安装
1.1施工范围及工程量:
高压管道共包含主蒸汽管道、再热热段蒸汽、再热冷段蒸汽、给水、高低旁等系统。
1.2主要施工方法介绍
1.2.1施工准备:
对口凳子、对口卡子、临时抱卡及防护棚制作。
测量检验各系统管道及与其相连接的设备接口的尺寸(包括直径、厚度、坡口等)并做记录。
检查组件的外观质量、椭圆度等符合要求。
按厂家提供的配管图、零件图及原材检验记录(原材长度、编号、测厚),核对组件的规格、尺寸,检查组件编号清晰明确,并做记录。
合金件在安装或焊接前按规定前进行光谱检验,对已检验合金件做好标记。
支吊架根部、管部及连接件等均工厂化配制,现场检验零件规格、尺寸、数量是否与设计相符,并做记录。
1.2.2管道预组合:
大部分管件已在工厂内组合,现场如有条件则与起重专业协商(考虑组件重量、长度等组合后便于吊装)确定后进一步进行组合,以减少高空焊口。
管道对口时,在组合场组合管段,将管段放在对口凳子上,对口凳子下垫木板或钢板,防止地面下陷;水平方向错口用大锤敲击对口凳子底部调整;上下错口时,旋转活动式对口凳子手柄进行调整,错口量≤5㎜时用对口卡子细调错口量。
焊口检验结束后对管道内部进行清理,加封临时堵板。
1.2.3支吊架的安装:
支吊架根部安装:
先进行B列至锅炉侧支吊架根部安装,然后再进行汽机房范围内支吊架根部的安装。
支吊架应与管道安装同步进行,即先安装要吊挂管段部分的支吊架根部,待吊装管段后,立即安装支吊架管部及连接件。
安装搬运过程中注意保护连接螺纹,防止螺扣的损坏。
安装过程中严格按图施工,注意清点、核对,防止丢失、漏装、错装。
1.2.4管道吊装:
管道安装顺序:
首先安装与炉侧相连的管道,按照由炉侧至机侧的顺序依次安装。
组合好靠近炉侧的管段,用汽车运至炉左筒吊起吊范围内,利用筒吊穿装组合管段,水平管用倒链接钩,立管吊装时,在距上管口2米左右位置(若无设计抱卡,应在管道上安装临时抱卡),以悬吊钢丝绳悬挂管道;汽机侧管段(以B列为界),用汽车运至汽机房8#—9#轴吊装孔处,用行车吊至各层相应安装位置,用倒链接钩,以悬吊钢丝绳悬挂管道。
管道临时吊挂前需确认吊点、钢丝绳、倒链等吊装设施能满足所吊挂重物的载荷要求。
空中焊口过程中以焊口为中心,搭设3米见方的操作平台,对口时用2T倒链调整对口,错口量≤5㎜时以对口卡子细调错口量。
阀门安装前将阀门内部清理干净。
1.2.5支吊架调整:
支吊架调整工作在管道安装完毕后进行。
弹簧销子应在锅炉点火吹管前拆除。
拉杆端头距紧固件间的丝扣长度应一致,锁紧螺母应锁紧牢固;抱箍连接螺栓的螺母、锁紧螺母紧固后,厂家要求打毛或点焊的必须按要求实施。
1.2.6小口径管道安装应由技术员根据现场实际情况进行详细的技术交底,根据技术员现场给出的管道走向进行施工。
1.2.7安装及调整工作完成后对系统进行全面检查。
1.3施工质量标准
1.3.1施工前准备:
管材、管件、管道附件、阀门的规格、型号符合设计规定。
管材、管件、管道附件、阀门外观检查,不得有重皮、裂纹等缺陷,对于管子表面划痕、凹坑等局部缺陷做检查鉴定,椭圆度不大于5%。
拉杆平直无弯曲,螺纹部件无断齿、毛刺、伤痕等缺陷,螺杆与螺母、环形耳子配合良好。
核对技术证件中管材、管件、管道附件、阀门的化学成份、机械性能、冲击韧性等符合国家技术标准且必须按照以下要求进行金属检验:
现场用合金材料,安装前必须100%光谱检验,安装后必须做100%的光谱复查,合金材料安装前的光谱分析应做好标识,材料下料后必须移植光谱标识。
主蒸汽管道和再热蒸汽管道(包括高低旁路管减温减压阀前管道):
所有直管和弯管母材100%壁厚、硬度、金相检查。
1.3.2管道地面组合:
组件两端坡口型式符合配管图中的要求(即双“V”型),对口间隙保持一致,为2~3mm。
内壁错边量≤0.5mm;外壁错边量≤1.5mm。
管子对口平直度要求:
在距焊口中心200mm范围内测量当DN≤100时折口偏差≤0.5mm,DN>100时折口偏差≤1mm。
对接管道及设备内部清洁无杂物。
坡口表面在距管口50mm的范围内(包括内外壁)清除油漆、污锈、毛刺等杂物直至显示金属光泽,检查表面无裂纹、夹渣等缺陷。
管道对口焊接全部以氩弧焊打底,焊口焊接完成后进行100%无损探伤检查,探伤前对焊口两边各150mm左右范围内清除油污直至出现金属光泽。
1.3.3管道组件吊装、对口焊接:
管道标高偏差不得超过±7mm;水平管弯曲度:
DN≤100mm时不大于0.5/1000且≤15mm;DN>100mm时不大于1/1000且≤15mm;立管垂直度≤1‰,且≤10mm。
坡向、坡度应符合设计图纸要求;
管道对口焊接的要求与前述预组合时相同。
1.3.4支吊架安装:
吊架根部安装位置、型式、偏装方向符合设计要求,结构焊接牢固,焊缝型式、焊角高度符合设计及焊接专业要求,结构焊接厚度不得小于设计图纸中焊缝高度K值,使用J507焊条焊接,焊波均匀,无裂纹,夹渣,气孔等缺陷。
支吊架管部及连接件型式、规格、材质及安装位置符合设计要求,且不得妨碍管道自由膨胀。
弹簧吊架安装正确,弹簧指针指在冷态位置,冷态值及热态值符合设计要求。
恒力弹簧吊架规格及安装位置应符合设计要求,销轴转动灵活,冷态值及热态值符合厂家要求。
导向支架的型式、安装位置正确,预留热位移方向符合设计。
滑动支架安装位置正确,热位移偏差符合设计规定,管道能自由膨胀,滑动面接触良好无卡涩现象。
1.3.5小口径管道安装:
管道布置走向合理,并有≮5‰的坡度。
支吊架的型式、位置应符合设计要求及相关标准。
小口径管道,安装时尽量与其它系统同位置管道组合排列,以达到简洁、美观的工艺要求。
1.4应注意的质量问题
1.4.1组合件在吊装时应注意保护坡口、管座、挡块等,防止磕碰或砸伤。
1.4.2管道安装前必须检查内部清洁度,安装工作如有间断应及时封闭管口。
在安装过程中,严禁将任何物件放在管口内,保证管内始终清洁。
1.4.3管道安装时禁止强行对口,不得将外力作用在设备上。
管道焊口在热处理结束前,不得起吊、移动管道,即不得使焊口承受附加外力。
1.4.4管道表面不得引弧、试电流或焊接临时支撑物。
1.4.5安装弹簧支吊架前,除需对照图纸核对弹簧型号外,还必须核对弹簧标牌上标明的支吊架编号,经核对无误后再行安装。
依管道支吊架安装图,有偏装要求的支吊架,必须按图进行偏装。
1.4.6管道大流量冲洗、水压试验前,不得卸掉弹簧定位销;管道吹管前卸掉定位销,卸定位销时应调节花兰螺母或承载螺母,在定位销不受力状态下用手取出定位销,调节后拧紧锁紧螺母,定位销应用铅丝挂在弹簧支吊架上。
整定弹簧严格按编号及与其对应图纸使用,整定弹簧的固定销必须在保温完毕后拆除。
1.4.7支吊架调整后,各连接件的螺杆、丝扣需带满、锁紧螺母应正确锁紧,防止松动。
支吊架根部槽钢、钢板等切割后必须进行打磨处理。
1.4.
8运行前,应检查位移指示器是否在C处,如有偏差应作调整,运行时应检查位移指示器是否在H处,并作好详细记录。
1.4.9管道蠕胀测点安装,应沿圆周等距分配,其径向尺寸偏差值一般不大于0.1mm,经四级验收并作好详细记录后,再将测点头点焊住。
1.4.10小口径管道安装,应设有